焦炉的热平衡及热工评定
焦炉热平衡测定及节能实践

焦炉热平衡测定及节能实践
焦炉热平衡测定是一种检测燃烧过程中焦炉的热量平衡状况的方法。
它的主要目的是通过改变燃烧条件和结构,确保焦炉的最佳热量利用率,减少燃料的消耗,节约能源。
实施焦炉热平衡测定包括以下几步:首先,对焦炉进行盘算计算,计算出热量损失和热量收益,并计算出全焦炉的能量平衡;然后,根据计算结果,控制焦炉条件,及时调整燃烧条件和结构等因素;最后,减少燃料消耗,增加焦炉热效率,达到节能的目的。
此外,焦炉的热量利用率可以通过定期检查炉缸内部受热情况,检查山灰层的厚度、减少空气流量,采用特殊膨胀材料,改变炉门结构等方法来提高。
总之,焦炉热平衡测试是一种支持能源节约的有效方法,可以有效减少焦炉热量损失,提高热量利用率,达到节能实践的目的。
焦炉的热平衡与热工评定

焦炉的热平衡与热工评定焦炉是一种燃煤设备,用于将硬煤转化为焦炭。
在整个焦化过程中,焦炉的热平衡和热工评定是非常重要的,因为热平衡和热工评定的正确性会直接影响到炉子的稳定运行、能源消耗和产品质量。
热平衡是指炉内各部分的热量输入和产出达到平衡状态的情况。
焦炉的热平衡是指炉内热量的产出和输入量达到平衡状态。
在炉内,燃料在高温下燃烧产生热能,同时也向外界散发热量,炉内还有焦炭的放热和化学反应的吸放热,因此要求在炉内各个部位热量输入和产出之间达到平衡。
对于焦炉,热平衡主要包括两个方面:一是炉内各部分气体的温度分布,二是炉墙的温度分布。
炉内各部分气体的温度分布是影响炉内反应过程的关键因素,也是为保证炉内的稳定运行必须要控制的因素。
炉墙的温度分布则是保证炉子的安全运行、延长炉墙使用寿命和减少炉墙腐蚀的重要因素。
在炉子运行的过程中,热工评定也是必不可少的,它是指对炉子热工参数进行分析和评估,以确定炉子的运行效果和评估炉子的性能指标。
其中最重要的参数是焦温、炉顶温度、炉底温度、高炉炼铁比和热风温度等等。
焦温是指焦炭的温度,是衡量焦炭品质的重要指标之一。
炉顶温度是指炉子顶部的温度,该指标可以反映炉子内部的热平衡状态。
炉底温度是指炉子底部的温度,因为底部温度过高会导致煤气中的其他物质产生变化,影响炼焦的质量。
高炉炼铁比是指高炉进料铁矿石与焦炭的比例,该指标主要关系到高炉出铁质量和能耗。
热风温度则是高炉热风的温度,对炉内反应关键参数有很大的影响。
需要注意的是,热平衡和热工评定的正确性是“关键的”有时可能会影响到炉子的稳定运行以及产品质量的稳定性。
因此,炉子企业必须确保其评价系统的有效性,以便以最低的维护和控制成本来确保其能够满足生产需求和质量要求。
总之,焦炉热平衡和热工评定是炼焦过程中十分重要的两个方面。
对于炼焦企业来说,它们的准确性直接关系到生产质量和能源消耗。
只有满足了这两个方面的要求,才能有效地确保炼焦过程的可持续性和稳定性。
炼焦炉的加热与调节
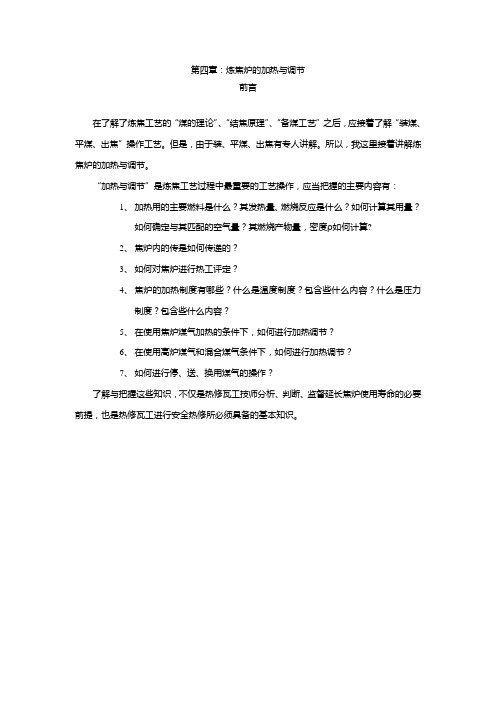
第四章:炼焦炉的加热与调节前言在了解了炼焦工艺的“煤的理论”、“结焦原理”、“备煤工艺”之后,应接着了解“装煤、平煤、出焦”操作工艺。
但是,由于装、平煤、出焦有专人讲解。
所以,我这里接着讲解炼焦炉的加热与调节。
“加热与调节”是炼焦工艺过程中最重要的工艺操作,应当把握的主要内容有:1、加热用的主要燃料是什么?其发热量、燃烧反应是什么?如何计算其用量?如何确定与其匹配的空气量?其燃烧产物量,密度ρ如何计算?2、焦炉内的传是如何传递的?3、如何对焦炉进行热工评定?4、焦炉的加热制度有哪些?什么是温度制度?包含些什么内容?什么是压力制度?包含些什么内容?5、在使用焦炉煤气加热的条件下,如何进行加热调节?6、在使用高炉煤气和混合煤气条件下,如何进行加热调节?7、如何进行停、送、换用煤气的操作?了解与把握这些知识,不仅是热修瓦工技师分析、判断、监督延长焦炉使用寿命的必要前提,也是热修瓦工进行安全热修所必须具备的基本知识。
第一节:焦炉加热用燃料——煤气以及助燃空气的计算一、焦炉加热常用燃料有两种:焦炉煤气和高炉煤气。
为提高高炉煤气的热值,常在高炉煤气中掺烧焦炉煤气。
二、热工计算用煤气的组成:①名称:组成(体积%)低发热量焦炉煤气H2CH4CO CmHnCO2N2 O2KJ/Nm359.2 25.5 6.0 2.2 2.4 4.0 0.4 17890高炉煤气 1.5 0.2 26.8 13.6 57.2 0.4 3637②煤气的湿组成表示及换算煤气中常含有饱和水蒸汽。
湿煤气的组成,可按干煤气组成和各个温度在煤气中饱和水蒸汽的含量进计算。
一般是给出1立方米干煤气所能吸收的水蒸汽的质量(g常数)来表示:g干干H2O 因此,必须先把g干H2O变成H2O湿。
在标准状态下(0℃760mmHg)条件下:1Kg水蒸汽的体积为:22.14= 1.24 m3 /Kg181m3干煤气吸收的水份为g干干H2O100 m3干煤气吸收的水份为:g干干H2O×100×1.24 = 0。
6米焦炉热工参数分析

6m焦炉热工参数的分析及节能措施汪洋(攀钢煤化工厂,攀枝花617022)根据国家“十一五”钢铁企业发展纲要中节能减排的要求,我厂对新1、2号焦炉的热工参数进行了测量与计算,在此基础上研究了6m焦炉的节能降耗方案,以实现符合国家节能减排要求的焦炉最佳经济运行模式。
1 物料平衡物料平衡计算中取1000kg干煤为基准。
物料平衡参数见表1。
物料平衡G入= GM+GS= 1130.58 kgG出= GJ+GV+GB+GA+GZ+GK+GS+GL= 1120.981 kg物料误差η = (G入-G出)/G入×100% = 0.85%计算误差为0.85%<5%,符合行业标准。
2 能量平衡对炼焦炉的热平衡,一般应以焦炉本体为测定体系。
热量平衡参数见表2,根据表2数据计算得出本次标定的2号焦炉的热平衡误差为1.71%<5%, 符合行业标准。
2.1 效率计算1)热效率:η热 = (Q供-Q废-Q不)Q供= 81.31%2)热工效率::η热工 = (Q供-Q废-Q损-Q散)Q供=68.16%3)窑炉统一效率:η统=(Q有-Q原)/(Q供-Q原)=67.82%2.2 炼焦耗热量计算1) 相当耗热量。
用湿煤炼焦,以l kg干煤为计算标准,需供给焦炉的热量:q相=Q1/1000 = 2847 kJ/kg干煤2) 湿煤耗热量。
1 kg湿煤炼成焦炭需供给焦炉的热量:q湿=q相×(100-Mt)/100 = 2518.2 kJ/kg表1 物料平衡参数表2 热量平衡参数3) 干煤耗热量。
1 kg水蒸汽出炭化室所需热量:qs1=[ (2500+2.06×755) + (2500+748×2.056)]/ 2×0.6782 = 5966.7 kJ/kg由q湿=q干×(100-Mt)/100-qs1(Mt/100)得q干=[q湿-qs1(Mt/100)]/(100-Mt)×100 = 2067.7 kJ/kg4)相当(换算)耗热量。
焦炉热工制度规定

焦炉热⼯制度规定焦炉热⼯制度规定:3、编排推焦计划时,最短结焦时间不得短于周转时间15分钟,烧空炉时,不得短于周转时间25分钟。
4、每昼夜允许最⼤升温速度不得超过60℃,当焦侧温度在1360℃以上时,不得超过20℃.5、⽴⽕道温度在交换后20秒时,不得超过1450℃,不得低于1100℃.6、硅砖蓄热室顶部温度不得超过1320℃.7、⼩烟道温度不得超过450℃,不得低于250℃,分烟道温度不得超过400℃.8、焦饼中⼼温度保持在950~1050℃.9、集⽓管温度应保持在80~100℃.10、炉顶空间温度要低于850℃.11、焦炉煤⽓加热时,煤⽓预热后温度为40~50℃.12、发⽣炉煤⽓加热时,煤⽓温度不得⾼于35℃.13、炭化室底部压⼒在结焦末期时应⼤于5Pa.14、集⽓管压⼒以吸⽓管下⽅炭化室底部压⼒在结焦末期⼤于5Pa来决定、保持。
15、加热煤⽓总管压⼒不得低于450Pa。
16、看⽕眼压⼒不得低于5Pa。
17、机、焦侧烟道⾛廊,地下室空⽓中CO含量不得超过30mg/m3。
18、⽤焦炉⽓加热时,相当耗热量不得超过2460~2700KJ/Kg装炉煤,⽤发⽣炉煤⽓加热时,相当耗热量不得超过2633.4~2900KJ/Kg装炉煤.19、炉体伸长量每年不应超过0.035%。
20、空⽓过剩系数保持1.15—1.35.焦炉损坏的原因⼀、⾼温、机械⼒作⽤及物理化学反应作⽤,表现在墙⾯剥落、炉顶过顶砖断裂、炉长增长、炉宽变窄、边炉炉墙外倾、炉底砖龟裂、磨损、斜道烧熔、窜透。
1、SIO2升华,荒煤⽓裂解,碳氨、CO还原温度⾼于1300度SIO2--------->1300---CO+SIO是逐步进⾏的,从⽽降低硅砖的性能。
2、SIO2溶蚀、煤料中碱性物质,Fe2O3,FeO、AL2O3与SIO2结合,使硅砖形成低熔点共熔物,从⽽降低硅砖的耐热性能和抗机械磨损能⼒,墙⾯结渣,剥蚀脱离。
3、压⼒作⽤,焦炉温度周⽽复始冷热交替,机械碰撞。
焦炉等级评定实施方案

焦炉等级评定实施方案一、背景介绍焦炉是炼钢过程中不可或缺的设备,其性能和等级直接影响着钢铁生产的质量和效率。
为了科学评定焦炉的等级,制定实施相应的方案,本文旨在规范焦炉等级评定的相关内容。
二、评定范围焦炉等级评定的范围主要包括焦炉的设备状况、运行情况、能耗情况等方面,具体包括但不限于以下内容:1. 焦炉设备的完好情况,包括炉体、煤气管道、冷却系统等;2. 焦炉的运行情况,包括操作稳定性、生产效率等;3. 焦炉的能耗情况,包括燃料利用率、能源消耗等。
三、评定标准为了科学、客观地评定焦炉的等级,我们制定了一套严格的评定标准,主要包括以下几个方面:1. 设备状况评定:根据焦炉设备的完好程度、维护情况等进行评定,分为优、良、中、差四个等级;2. 运行情况评定:根据焦炉的操作稳定性、生产效率等进行评定,分为优、良、中、差四个等级;3. 能耗情况评定:根据焦炉的燃料利用率、能源消耗等进行评定,分为优、良、中、差四个等级。
四、评定流程焦炉等级评定的流程主要包括以下几个步骤:1. 调查准备:组织评定人员,准备评定所需的相关资料和工具;2. 现场调查:对焦炉设备进行现场检查,了解其运行情况和能耗情况;3. 数据分析:对所获得的数据进行分析,综合考虑设备状况、运行情况和能耗情况;4. 等级评定:根据评定标准,对焦炉进行等级评定,并形成评定报告。
五、评定结果运用焦炉等级评定的结果将直接影响钢铁生产的质量和效率,具体运用包括但不限于以下几个方面:1. 优化管理:根据评定结果,对焦炉进行管理优化,提高设备状况和运行效率;2. 能效改进:根据评定结果,对焦炉的能耗情况进行改进,降低能源消耗;3. 安全生产:根据评定结果,加强焦炉设备的维护和保养,确保安全生产。
六、总结焦炉等级评定实施方案的制定,对于提高焦炉设备的管理水平、降低能源消耗、确保安全生产具有重要意义。
希望各相关单位能够严格按照本方案进行实施,不断提升焦炉设备的等级,为钢铁生产提供更好的保障。
焦炉的热平衡与热工评定

焦炉的热平衡及热工评定一、焦炉的物料平衡及热平衡焦炉的物料平衡计算是设计焦化厂最基本的依据,也是确定各种设备操作负荷和经济估算的基础。
而焦炉的热平衡是在物料平衡和燃烧计算的基础上进行的。
通过热平衡计算,可具体了解焦炉热量的分配情况,从理论上求出炼焦耗热量,并得出焦炉的热效率和热工效率,因此对于评定焦炉热工操作和焦炉炉体设计的是否合理都有一定的实际意义。
为了进行物料衡算,必须取得如下的原始数据:(1)精确称量装入每个炭化室的原料煤量,取3~5昼夜的平均值,同时在煤塔取样测定平均配煤水分。
干煤和配煤水分为焦炉物料衡算的入方。
以下为焦炉物料平衡的出方:(2)各级焦炭产量。
标定前要放空焦台和所有焦槽的焦炭,标定期间应准确计量冶金焦、块焦和粉焦(要计入粉焦沉淀池内的粉焦量)的产量。
并对各级焦炭每班取平均试样以测定焦炭的水分,并考虑到水分蒸发的损失量,然后计算干焦产量。
(3)无水焦油、粗苯、氨的产量,通常按季度或年的平均值确定,不需标定。
(4)水汽量按季或年的多余氨水量的平均值确定。
(5)干煤气产量由洗苯塔后(全负压操作流程为鼓风机后)的流量表读数确定,并进行温度压力校正。
在计算时,一般以1000kg干煤或湿煤为基准。
以下列出某厂焦炉炭化室物料平衡的实际数据。
如表8—9所示。
根据物料平衡和温度制度,计算出各种物料带入焦炉和带出焦炉的显热和潜热,然后作出焦炉的热平衡计算。
具体计算方法可参考有关资料。
现列出根据表8-9的物料平衡所作的热平衡计算,如表8-10的数据,并加以分析。
由热平衡可知,供给焦炉的热量有98%来自煤气的燃烧热,故在近似计算中可认为煤气的燃烧热为热量的惟一来源,这样可简化计算过程。
在热量出方中,传入炭化室的有效热1~4项占70%,而其中焦炭带走的热量占37.6%,换算到每吨赤热焦炭带走的热量为:kJ/t焦。
此值相当可观。
采用干法熄焦此热量可大部分回收。
降低焦饼中心温度和提高焦饼加热均匀性可降低此热量。
焦炉热工制度规定

焦炉热工制度规定:3、编排推焦计划时,最短结焦时间不得短于周转时间15分钟,烧空炉时,不得短于周转时间25分钟。
4、每昼夜允许最大升温速度不得超过60℃,当焦侧温度在1360℃以上时,不得超过20℃.5、立火道温度在交换后20秒时,不得超过1450℃,不得低于1100℃.6、硅砖蓄热室顶部温度不得超过1320℃.7、小烟道温度不得超过450℃,不得低于250℃,分烟道温度不得超过400℃.8、焦饼中心温度保持在950~1050℃.9、集气管温度应保持在80~100℃.10、炉顶空间温度要低于850℃.11、焦炉煤气加热时,煤气预热后温度为40~50℃.12、发生炉煤气加热时,煤气温度不得高于35℃.13、炭化室底部压力在结焦末期时应大于5Pa.14、集气管压力以吸气管下方炭化室底部压力在结焦末期大于5Pa来决定、保持。
15、加热煤气总管压力不得低于450Pa。
16、看火眼压力不得低于5Pa。
17、机、焦侧烟道走廊,地下室空气中CO含量不得超过30mg/m3。
18、用焦炉气加热时,相当耗热量不得超过2460~2700KJ/Kg装炉煤,用发生炉煤气加热时,相当耗热量不得超过2633.4~2900KJ/Kg装炉煤.19、炉体伸长量每年不应超过0.035%。
20、空气过剩系数保持1.15—1.35.焦炉损坏的原因一、高温、机械力作用及物理化学反应作用,表现在墙面剥落、炉顶过顶砖断裂、炉长增长、炉宽变窄、边炉炉墙外倾、炉底砖龟裂、磨损、斜道烧熔、窜透。
1、SIO2升华,荒煤气裂解,碳氨、CO还原温度高于1300度SIO2--------->1300---CO+SIO是逐步进行的,从而降低硅砖的性能。
2、SIO2溶蚀、煤料中碱性物质,Fe2O3,FeO、AL2O3与SIO2结合,使硅砖形成低熔点共熔物,从而降低硅砖的耐热性能和抗机械磨损能力,墙面结渣,剥蚀脱离。
3、压力作用,焦炉温度周而复始冷热交替,机械碰撞。
- 1、下载文档前请自行甄别文档内容的完整性,平台不提供额外的编辑、内容补充、找答案等附加服务。
- 2、"仅部分预览"的文档,不可在线预览部分如存在完整性等问题,可反馈申请退款(可完整预览的文档不适用该条件!)。
- 3、如文档侵犯您的权益,请联系客服反馈,我们会尽快为您处理(人工客服工作时间:9:00-18:30)。
一、焦炉的物料平衡及热平衡焦炉的物料平衡计算是设计焦化厂最基本的依据,也是确定各种设备操作负荷和经济估算的基础。
而焦炉的热平衡是在物料平衡和燃烧计算的基础上进行的。
通过热平衡计算,可具体了解焦炉热量的分配情况,从理论上求出炼焦耗热量,并得出焦炉的热效率和热工效率,因此对于评定焦炉热工操作和焦炉炉体设计的是否合理都有一定的实际意义。
为了进行物料衡算,必须取得如下的原始数据:(1)精确称量装入每个炭化室的原料煤量,取3~5昼夜的平均值,同时在煤塔取样测定平均配煤水分。
干煤和配煤水分为焦炉物料衡算的入方。
以下为焦炉物料平衡的出方:(2)各级焦炭产量。
标定前要放空焦台和所有焦槽的焦炭,标定期间应准确计量冶金焦、块焦和粉焦(要计入粉焦沉淀池内的粉焦量)的产量。
并对各级焦炭每班取平均试样以测定焦炭的水分,并考虑到水分蒸发的损失量,然后计算干焦产量。
(3)无水焦油、粗苯、氨的产量,通常按季度或年的平均值确定,不需标定。
(4)水汽量按季或年的多余氨水量的平均值确定。
(5)干煤气产量由洗苯塔后(全负压操作流程为鼓风机后)的流量表读数确定,并进行温度压力校正。
在计算时,一般以1000kg干煤或湿煤为基准。
以下列出某厂焦炉炭化室物料平衡的实际数据。
如表8—9所示。
根据物料平衡和温度制度,计算出各种物料带入焦炉和带出焦炉的显热和潜热,然后作出焦炉的热平衡计算。
具体计算方法可参考有关资料。
现列出根据表8-9的物料平衡所作的热平衡计算,如表8-10的数据,并加以分析。
由热平衡可知,供给焦炉的热量有98%来自煤气的燃烧热,故在近似计算中可认为煤气的燃烧热为热量的惟一来源,这样可简化计算过程。
在热量出方中,传入炭化室的有效热1~4项占70%,而其中焦炭带走的热量占%,换算到每吨赤热焦炭带走的热量为:kJ/t焦。
此值相当可观。
采用干法熄焦此热量可大部分回收。
降低焦饼中心温度和提高焦饼加热均匀性可降低此热量。
由水蒸汽带走的热量占16%,故降低配煤水分可以降低此热量。
此外,采取降低炉顶空间温度、上升管加水夹套回收余热等方法可以减少或部分回收煤气、化学产品和水汽带走的热量。
由废气带走的热量也很大,约占%,因此改善蓄热室的操作条件,提高蓄热效率,是降低热量消耗的重要途径之一。
一般散失于周围空间的热量,对于大焦炉约为10%,小焦炉由于表面积大,故散热损失大于10%。
二、焦炉的热效率和热工效率根据焦炉的热平衡,可进行焦炉的热工评定。
由表8-10可见,只有传入炭化室的热量(出方1~4项)是有效的,称为有效热。
为了评定焦炉的热量利用程度,以有效热(Q效)占供入总热量(Q总)的百分比称为焦炉的热工效率(η热工)即:η热工= ×100% (8-15) 因Q效等于供入焦炉总热量减去废气带走的热量Q废和散失周围空间的热量Q散,所以:η热工= ×100% (8-16)由于计算Q散比较困难,也可以采用热效率(η热)的方式来评定焦炉的热量利用情况。
η热= ×100% (8-17)它表示理论上可被利用的热量占供入总热量的百分比。
通常对现代大型焦炉η热工约为70~75%,η热为80~85%。
η热工与η热可从焦炉热平衡中求得。
由表8-10可得:η热工= ×100%=%η热= ×100%=%但由于进行热量算衡需要做大量的繁琐的测量、统计和计算工作,通常生产上不进行,而是根据燃烧计算来估算η热工和η热,方法如下:①计算以1标m3加热煤气为基准。
②在热量入方中,由于煤气的燃烧热(低发热值)和煤气、空气的显热已占总热量99%以上,因此可以近似看作为Q总。
煤气低发热值按其组成计算,煤气和空气的显热则根据燃烧计算所得的L实和烟道走廊的温度计算。
③由蓄热室进入废气盘的废气所带出的热量Q废和废气中不完全燃烧产物的燃烧热Q不,可通过取样分析得出的废气组成和测定的废气温度来求得。
焦炉的散热损失一般按供入总热量的10%计。
则:η热= ×100%η热工= ×100%[例8-3] 某焦炉以Q低=3643kJ/m3的高炉煤气加热,由燃烧计算得,L实= m3/(m3煤气),产生的废气量V废=/(m3煤气),煤气温度30oC,烟道走廊的空气温度为35oC,空气的相对湿度为,废气中含CO为%,废气的平均温度为280oC,计算焦炉的η热和η热工。
解 (1) 煤气的燃烧热Q低=3643kJ/(m3煤气)。
(2)煤气带入的显热煤气温度30oC,查图8-4得c煤=/(m3·℃),30℃时煤气带入的饱和水汽量为干煤气的%(查表8-3),30℃时水汽的比热容 = /(m3·℃)。
Q煤=+ (3)空气带入的显热 35℃时空气的比热容c空=/(m3·℃),35℃时饱和水汽量为干空气的%,当相对湿度为时,空气中所含水汽量为干空气的。
Q空=废气带走的热量废气在280℃时的比热容查图8-4得c废=/(m3·℃)。
Q废=。
(5)不完全燃烧的热损失 CO的发热值为12728kJ/m3。
Q不=则η热 ===%若Q效为供入总热量的10%,则η热工==%三、炼焦耗热量由焦炉热平衡作热工评定方法比较麻烦,因此生产上广泛采用炼焦耗热量对焦炉进行热工评定。
炼焦耗热量是表示焦炉结构的完善程度、焦炉热工操作及管理水平和炼焦消耗定额的重要指标,也是确定焦炉加热用煤气量的依据。
炼焦耗热量是将1kg煤在炼焦炉内炼成焦炭所需供给焦炉的热量。
由于采用的计算基准不同,故有下列表示方法。
1.湿煤耗热量1kg湿煤炼成焦炭应供给焦炉的热量,用q湿来表示,显然湿煤耗热量随煤中水分变化而变化,水分越多,q湿越大。
q湿= ,kJ/(kg湿煤) (8-18)式中V0——标准状态下加热煤气的耗量,m3/h;Q湿——焦炉的湿煤装入量,kg;Q低——加热用煤气的低发热值,kJ/m3。
2.干煤耗热量lkg干煤炼成焦炭所消耗的热量。
干煤耗热量不包括煤中水分的加热和蒸发所需要的热量,以q干来表示。
每kg水汽从焦炉炭化室带走的热量为:l00%=51000kJ/(kg水)式中 2491——lkg水在OoC时的蒸发潜热,kJ/kg;——为水汽在0~600oC时的平均比热容,kJ/(kg·oC);600——从炭化室导出的荒煤气的平均温度,℃;%——焦炉的平均热工效率,%。
如配煤水分为M t%(湿基),则q湿=q干 +5100=q干 +51M tq干= l00, kJ/(kg干煤) (8-19)3.相当耗热量为统一基准,便于比较,提出了相当耗热量这一概念。
它是在湿煤炼焦时,以lkg干煤为基准时,需供给焦炉的热量(包括水分加热和蒸发所需热量),以q相来表示。
,kJ/(kg干煤)(8-20)式中G干——焦炉干煤装入量,kg/h我国焦炉相当耗热量指标见表8-11。
表8-11数据按每kg捣固煤料,配煤水分7%计。
计算加热系统时,考虑使生产留有余地,故规定值较高。
由表可见,焦炉用高炉煤气加热时,相当耗热量高于用焦炉煤气加热。
这是因为高炉煤气与焦炉煤气相比,热辐射强度低,废气量大,废气密度高,故废气带走的热量多,通过炉墙和设备的漏损量也大。
由于煤料水分常有波动,各厂煤料水分也不相同,故耗热量也不相同。
为便于比较,必须将炼焦耗热量换算为同一基准。
水分每变化1%时,相当于湿煤中1%的干煤为1%的水分所取代,故q湿的变化值为。
因q 干一般约为2094kJ/kg,q水为5100 kJ/kg,则q湿的变化值为29~33 kJ/kg。
该值的换算方法如下:当用焦炉煤气加热时,配煤水分7%的q相取大中型焦炉的平均值:(2345+2596)=2470kJ/kg按式8-20得:q湿=q相==2303kJ/kg配煤水分增加1%时,该湿煤的耗热量增加29kJ,则折算到q相的增加为:=67kJ对于高炉煤气,配煤水分取7%时:q相= (2638+2931)=2785kJ/kg则 q湿=2785 =2596kJ/kg故配煤水分增加1%时,q相的增加值为:=67kJ我国焦化厂的配煤水分一般为9~10%,由测得的耗热量换算为9%配煤水分的耗热量q换时,可按下列公式计算:焦炉煤气:q相换=q相-59(M t-9) (8-21)q湿换=q湿-29(M t-9) (8-22)高炉煤气:q相换=q相-67(M t-9) (8-23)q湿换=q湿-33(M t-9) (8-24)炼焦耗热量可由焦炉的热平衡得到(按表8-9和8-10):q湿= = 2663kJ/(kg湿煤)q干= 100=2458kJ/(kg干煤)q相=2663 =2897kJ/[kg干煤(水)]用焦炉煤气加热时,换算为水分9%时耗热量为:q湿换=2663-29(8-9)=2692kJ/(kg湿煤)q相换=2897-59(8-9)=2956kJ/[kg干煤(水)]由物料平衡和热平衡作炼焦耗热量计算,生产上不可能随时进行,因此可用下式直接作近似计算:q相= K T·K P·K换(8-25)式中τ——炭化室周转时间,h;V0——煤气流量表数值,m3/h;Q低——加热煤气的低发热值,kJ/m3;G——炭化室平均装干煤量,kg/孔;n——一座焦炉的炭化室孔数;K T、K P、K换——分别为温度、压力和换向校正系数。
需要进行上述校正的原因是,煤气流量表的刻度是按煤气在某一固定操作条件下(温度、压力、含水量等)由实际煤气流量换算来的,但实际操作时,煤气的温度、压力和含水量不同于流量表刻度时规定的数值,因此需校正。
孔板流量计的计算公式如下:V0= (8-26)式中 a——标准孔板的消耗系数;d——孔板流通孔直径,cm;ρ0——标准状态下煤气密度,kg/m3;f——煤气中水汽含量 (按入炉前煤气温度定) ,kg/m3;P——煤气的绝对压力,Pa;T——煤气的绝对温度,K;h——流量孔板前后的压差,Pa;V0——煤气流量,m3/h。
对固定的流量孔板a、d的值是一定的,对一定组成的煤气,ρ0也不变。
如果实际操作条件和流量表刻度规定的条件一致为P、T和f时,表上的读数是正确的。
当实际操作条件为p′、T′和f′时,则对同一压差h,其标准流量将不是V0而是V0′,即:V0′= ·ad2 m3/h因此,应按流量表读数V o校正到实际操作条件下的标准流量Vo′,其关系为:因f、f′分别由T、T′决定,故令:所以V o′=V o·K T·K P故只要把K T、K P制成图表,按煤气的实际温度、压力查取即可。
K换是考虑到由于换向时,有一段时间不向焦炉送煤气,则每小时实际进入焦炉的煤气量将小于流量表的读数,因此乘以K换。
K换=式中 m——一小时内的换向次数;τ——每次换向焦炉不进煤气的时间,min;60——每小时60分钟。