离心泵叶轮的设计
基于CFD分析的双吸式离心泵叶轮优化设计的开题报告

基于CFD分析的双吸式离心泵叶轮优化设计的开题报告一、研究背景和意义离心泵是流体运输和输送的主要工具之一,在各个领域都得到了广泛应用。
其中,双吸式离心泵是一种非常重要的类型,通常应用于大型工业设备中,如水处理、电力、焦化等领域。
在实际应用中,离心泵的叶轮是起主要流体力学作用的部件,其设计的优化对于泵的性能和效率具有重要影响。
目前,离心泵的叶轮设计主要依靠经验和试验室实验,虽然已有较多的先进设计方法和技术,但叶轮设计仍然存在一定的不足,如流场效果的不理想、输送流量等方面的不足等问题,这需要更为精细的设计方法和技术逐渐逐渐优化和改进。
因此,本文将尝试基于CFD(计算流体力学)分析理论,对双吸式离心泵的叶轮进行优化设计,旨在提升泵的性能和效率。
二、研究内容和方法1.研究内容1)分析双吸式离心泵的结构和工作原理。
2)运用CFD理论研究叶轮的三维流场,确定叶轮的流场特性;3)建立叶轮模型,并结合MATLAB/ANSYS等软件对模型进行模拟计算,得出不同叶片倾角下的流体力学性能并分析;4)通过实验验证分析结果,并对实验数据和模拟结果进行比较。
2.研究方法1)文献阅读和综述分析;2)利用CFD软件对叶轮流场进行计算和分析;3)采用MATLAB和ANSYS有限元分析软件建立叶轮模型,并结合CFD 流场计算得到数值模拟结果;4)设计并实施实验验证,并通过数据分析验证数值模拟结果。
三、预期成果和意义预期成果:本文将利用CFD分析,通过长期反复的计算、分析以及实验验证,得出一套完整的双吸式离心泵叶轮优化设计方案,对于相关领域的离心泵设计和工程应用具有广泛实际的参考价值。
意义:通过对双吸式离心泵叶轮的优化设计,达到提高泵的效率、降低耗能的目的,不仅为工程实践提供了参考依据,同时也对未来离心泵的设计和优化研究提供了一定的参考意义。
叶轮的设计

取:
: 8 0( n l m)
一
2 . 叶 片 螺线 平 面 图
t 一一 背 叶 片 与 涡 室 间隙 取 t = 1 mm
一
根 据 上 述 叶 轮 叶 片 曲面 螺 线 计 算 结 果 ,绘 制 叶 片 螺 线 。在
圆周 上 取 1 6 个 轴 面 ,每 两 个 轴 面 夹 角 为2 2 . 5 。 ,当 Z = O 时, 空 螺 线 在 平 面 上投 影 , 如 图 所示 :
1 9 9 7 , 2 0 ( 5 ) : 6 -1 3
3 . 叶片 厚 度 计算 确 定 叶片 厚 度 时 ,应 注 意 到 铸 造 的 可能 性 ,对 铸 铁 叶 轮 , 叶 片 最 小 厚 度 为3—4 毫 米 ,本 次 设 计 的叶 轮 材 料 选 用MT 一 4 ,叶 … 馘 拙 :
【 1 】 丁成伟 . 离心 泵 与 轴 流 泵 . 北京: 机械 工 业 出版社, 1 9 8 1
1 4 3— 1 5 8
【 2 ] A . J . 斯捷潘诺夫. 离心 泵 和 轴 流 泵 . 北京: 机 械 工 业 出 版 社
19 80: 7 4—9 3
【 3 】 劳学苏, 何希杰. 螺旋 离心泵的原理 与设计方法. 水泵技术
I
=
5. 6 8 7 (mm )
S - - 6( I T l m)
4 . 背 叶 片 的设 计
图 卜 1叶 轮 轴 面 投 影 图
背 叶片 的主 要作 用 是 减 压 ,其 减 压 程 度 决 定 了背 叶片 的 几 何 参 数 。 背 叶 片 对 于 一 般 的 泵 而 言 ,还 有 另 一 个 作 用 , 就 是 能
离心泵毕业论文

离心泵毕业论文离心泵毕业论文离心泵是一种常见的工业设备,广泛应用于水处理、石油化工、电力等行业。
它以其高效、可靠的特点,成为工业生产中不可或缺的一部分。
本文将对离心泵的工作原理、设计要点以及应用领域进行探讨,旨在为读者提供关于离心泵的全面了解。
一、离心泵的工作原理离心泵是一种利用离心力将液体输送到高处的设备。
其工作原理可以简单地描述为:泵体内的叶轮通过电机的驱动旋转,液体在叶轮的离心力作用下被抛出,形成一定的压力,从而推动液体流动。
离心泵的工作过程可以分为吸入、压缩和排出三个阶段。
1. 吸入阶段:当泵体内部的叶轮旋转时,叶轮的叶片会在离心力的作用下形成一个低压区域。
此时,液体会通过吸入管道进入泵体,填满叶轮的叶片间隙。
2. 压缩阶段:当液体进入叶轮后,叶轮的旋转速度会使液体产生离心力。
离心力的作用下,液体被抛出叶轮,并沿着泵体的流道逐渐增加压力。
3. 排出阶段:当液体压力达到一定程度后,它会被排出泵体,通过出口管道输送到目标位置。
此时,液体的动能会转化为压力能,从而实现液体的输送。
二、离心泵的设计要点离心泵的设计要点包括叶轮设计、泵体结构、轴承选型等。
下面将分别对这些要点进行详细介绍。
1. 叶轮设计:叶轮是离心泵的核心部件,其设计直接影响着泵的性能。
叶轮的设计应考虑到流体的流动特性、工作条件以及泵的效率要求。
常见的叶轮类型有前后叶片式、开式和闭式叶轮等,设计时应根据具体情况选择合适的叶轮类型。
2. 泵体结构:泵体是离心泵的外壳,承载着叶轮和轴承等关键部件。
泵体的结构应具备良好的刚性和密封性,以保证泵的正常运行。
同时,泵体的内部流道设计也要考虑到流体的流动特性,以减小能量损失和阻力。
3. 轴承选型:离心泵的轴承起到支撑叶轮和传递转矩的作用。
轴承的选型应根据泵的工作条件和负载要求进行,以确保泵的稳定性和可靠性。
常见的轴承类型有滚动轴承和滑动轴承等,选型时应综合考虑摩擦损失、寿命和维护成本等因素。
三、离心泵的应用领域离心泵具有流量大、扬程高、效率高等优点,广泛应用于各个行业。
离心泵叶轮与蜗壳设计几何参数的优化研究

离心泵叶轮与蜗壳设计几何参数的优化研究离心泵是一种常用的流体机械设备,广泛应用于工业生产和民用领域。
其工作原理是通过离心力将液体推向出口,实现流体输送的目的。
离心泵的性能直接受到叶轮和蜗壳的设计参数的影响,因此对这些几何参数进行优化研究,可以改善离心泵的工作效率和节能性能。
叶轮是离心泵的核心部件,其结构形式多样,包括正向叶轮、背靠背叶轮和双吸入流通道叶轮等。
在进行叶轮设计时,需要考虑叶轮的轴长、轴功率、进口直径和出口直径等参数。
叶轮的直径越大,对应的扬程和流量也会增加,但是叶轮过大会导致泵的体积增大,造成不必要的浪费。
轴功率则与流量和工作压力有关,合理控制轴功率可以提高泵的工作效率。
另外,在叶轮的设计中,还需要考虑叶片的形状、数量和间隙等因素。
叶片的形状通常遵循空气动力学原理,采用弯曲或弯折形式,以减小流体在泵内的速度和压力变化,并提高泵的稳定性。
蜗壳是离心泵的另一个重要部件,其作用是引导进入泵的液体流向叶轮,并将离心泵的压力能转化为流体动能。
蜗壳的几何参数包括进口直径、出口直径、蜗舌角度和蜗舌长度等。
进口直径和出口直径是决定流量和扬程的关键参数,通常根据泵的设计工况和流体性质来确定。
蜗壳的设计还需要考虑蜗舌角度和蜗舌长度,这两个参数对泵的效率和稳定性影响较大。
蜗舌角度越小,流体在蜗壳内的速度变化越小,从而减小能量损失;而蜗舌长度越长,流体在蜗壳内的速度变化越平缓,减少压力波动和振动。
离心泵叶轮与蜗壳的几何参数优化研究的目标是找到一组最佳参数组合,使得离心泵在给定的工况下能够实现最大的效率和能量转换。
该研究可以通过理论计算、数值模拟和实验测试等方法进行。
对于叶轮的优化研究,可以通过设计不同形状和数量的叶片,采用数值模拟方法进行性能评估,并通过实际测试验证。
对于蜗壳的优化研究,可以通过调整进出口直径和蜗舌角度等参数,采用CFD模拟方法进行性能预测,并通过试验验证。
在离心泵叶轮与蜗壳设计几何参数的优化研究中,需要考虑的因素很多,如流体性质、工况参数、材料选择等,且不同泵的要求和工况也存在差异。
离心泵叶轮的流场分析
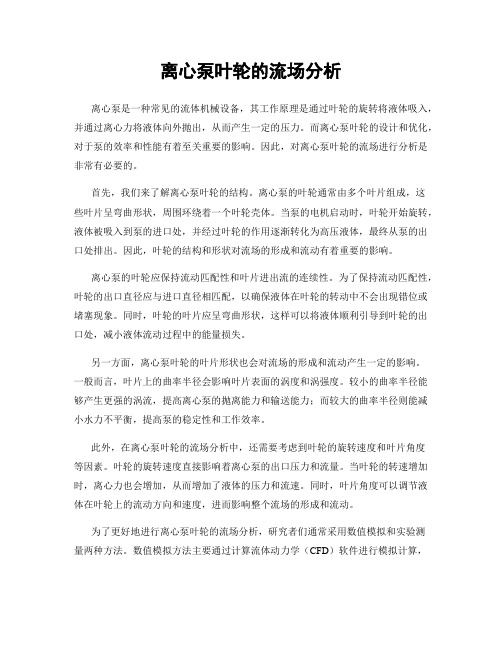
离心泵叶轮的流场分析离心泵是一种常见的流体机械设备,其工作原理是通过叶轮的旋转将液体吸入,并通过离心力将液体向外抛出,从而产生一定的压力。
而离心泵叶轮的设计和优化,对于泵的效率和性能有着至关重要的影响。
因此,对离心泵叶轮的流场进行分析是非常有必要的。
首先,我们来了解离心泵叶轮的结构。
离心泵的叶轮通常由多个叶片组成,这些叶片呈弯曲形状,周围环绕着一个叶轮壳体。
当泵的电机启动时,叶轮开始旋转,液体被吸入到泵的进口处,并经过叶轮的作用逐渐转化为高压液体,最终从泵的出口处排出。
因此,叶轮的结构和形状对流场的形成和流动有着重要的影响。
离心泵的叶轮应保持流动匹配性和叶片进出流的连续性。
为了保持流动匹配性,叶轮的出口直径应与进口直径相匹配,以确保液体在叶轮的转动中不会出现错位或堵塞现象。
同时,叶轮的叶片应呈弯曲形状,这样可以将液体顺利引导到叶轮的出口处,减小液体流动过程中的能量损失。
另一方面,离心泵叶轮的叶片形状也会对流场的形成和流动产生一定的影响。
一般而言,叶片上的曲率半径会影响叶片表面的涡度和涡强度。
较小的曲率半径能够产生更强的涡流,提高离心泵的抛离能力和输送能力;而较大的曲率半径则能减小水力不平衡,提高泵的稳定性和工作效率。
此外,在离心泵叶轮的流场分析中,还需要考虑到叶轮的旋转速度和叶片角度等因素。
叶轮的旋转速度直接影响着离心泵的出口压力和流量。
当叶轮的转速增加时,离心力也会增加,从而增加了液体的压力和流速。
同时,叶片角度可以调节液体在叶轮上的流动方向和速度,进而影响整个流场的形成和流动。
为了更好地进行离心泵叶轮的流场分析,研究者们通常采用数值模拟和实验测量两种方法。
数值模拟方法主要通过计算流体动力学(CFD)软件进行模拟计算,可以对叶轮的流动过程和特性进行全面、精确的分析。
而实验测量方法则是通过实际的泵和叶轮装置进行流体实验,通过测量数据来验证模拟结果的准确性。
总之,离心泵叶轮的流场分析是优化离心泵性能的重要环节。
离心泵叶轮轴面图的优化设计

后 盖板 型线 圆弧段日G的半 径 尺 的最小值 和最 ,
第3 2卷 第 3期
2 1 年 6月 01
化 工装 备技 术
5 3
离心泵 叶轮轴面 图的优化 设计
王敏 辉 余 猛 胡 家顺 李 翔
( 中船重 工集 团七一二研究所 ) ( 武汉工程大学机 电工程学 院)
摘 要 在 叶 轮 轴 面投 影 图绘 制 方 法 的基 础 上 ,用正 交设 计 方 法 完成 对 流道 型 线进 行 反 复 检 验一 整 、修 改 的优化 ,以取得 较 为理 想 的叶轮 轴 面投 影 图。 调
Wa gMih i n n u YuMe g n HuJah n L Xi g is u i a n
Ab t a t s r c :Th s a t l ic s e h t o f u i g r o o a d sg o c n u t i r ce d s u s s t e meh d o s o t g n l e i n t o d c mu t l n p ci n , i n h lpe is e t s i o
到 最好 ( )的试验 结果 。 优
0 引 言
当正交设 计 用于 优化 计算 时 ,以上 所说 的 “ 试 验 ”就 是访 问 目标 函数 的一次计 算 。也 即用 正 交设 计进 行 优化 计算 时 ,可用 较少 的访 问 目标 函数 的计
算 次数 得到 最优 解 。 用 正交设 计 方法 进行 优化计 算 可归 结 为如 下过
po ig to ,o c i e h t a i el i — ln rjcda ig ltn h dt ahe eo i lmpl r xa paepoet r n. t me vt pm ea l w
离心泵叶轮的参数化设计
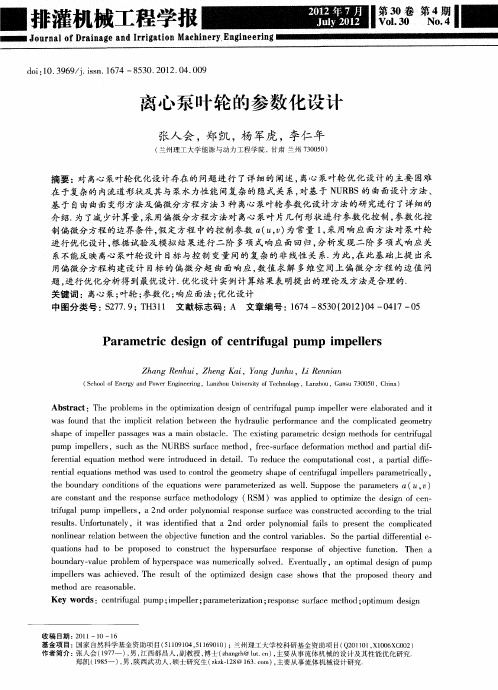
Pa a e rc d sg f c n r f g lp m p i p l r r m t i e i n o e t iu a u m e l s e
Z a g Re h i h n i h n n u ,Z e g Ka , 几 u h ,L n n gJ n u i Re n a
r n ile u to sme h d wa s d t o to he g o t h p fc n rf g li e lr a a ti al e t q ai n t o su e o c n r lt e mer s a e o e tiu a mp l sp r merc ly, a y e
在 离心 泵 的传 统 设 计 方 法 中 , 计 人 员 的 经 验 设
对 泵产 品 的设计 质量 有 很 大 的影 响 , 优 秀 的水 力 且 模 型需 要较 长 的设 计 周 期 , 化 设 计 难 以进 行 . 优 这 是 由于泵 的水 力性 能 与其 复 杂 的 内流 道 形 状 之 间 复 杂 的隐式关 系所 致 , 问题 在 形状 优 化 领 域 被称 该 为 具有 流动 约束 的功 能 曲面 的形 状 优 化 问题 , 是 也
aecnt t n erso s sr c e oooy ( S )w sa pi pi z ed s no e . r o s n dt ep ne u aem t d l a a h f h g RM a p l dt ot et ei f n e o mi h g c
p mp i elr u mp le s,s c st u h a he NURBS s ra e meho u c t d,fe —u a e d f r to t o n a t ld f f r e s r c eo main meh d a d p ri i- f a
离心泵——叶轮设计说明书

主要设计参数本设计给定的设计参数为: 流量Q=33500.01389mmhs=,扬程H=32m ,功率P=15Kw ,转速1450minrn =。
确定比转速s n根据比转速公式343.65145046.3632s n ⨯=== 叶轮主要几何参数的计算和确定1. 轴径与轮毂直径的初步计算1.1. 泵轴传递的扭矩3159.5510955098.81450t P M N m n =⨯=⨯=⋅其中P ——电机功率。
1.2泵的最小轴径对于35号调质钢,取[]5235010Nm τ=⨯,则最小轴径0.02424d m mm ==== 根据结构及工艺要求,初步确定叶轮安装处的轴径为40B d mm =,而轮毂直径为(1.2~1.4)h B d d =,取51h d mm = 2. 叶轮进口直径jD 的初步计算取叶轮进口断面当量直径系数0 4.5K =,则0 4.50.09696D K m mm ====对于开式单级泵,096j D D mm == 3. 叶片进口直径1D 的初步计算由于泵的比转速为46.36,比较小,故1k 应取较大值。
不妨取10.85k =,则110.859682j D k D mm ==⨯=4. 叶片出口直径2D 的初步计算220.50.5246.369.359.3513.7310010013.730.292292s D D n K D K m mm --⎛⎫⎛⎫==⨯= ⎪⎪⎝⎭⎝⎭====5. 叶片进口宽度1b 的初步计算()002221114/4//v vm j j hvQ Q V V D D d Q b DV ηηππηπ===-=所以 220111144j j v V D D b V D K D ==其中,10v V K V =,不妨取0.8v K =,则22118535.42440.863.75jv D b mm K D ===⨯⨯6. 叶片出口宽度2b 的初步计算225/65/6246.360.640.640.33731001000.33730.00727.2s b b n K b K m mm ⎛⎫⎛⎫==⨯= ⎪⎪⎝⎭⎝⎭====7. 叶片出口角2β的确定取2β=15°8. 叶片数Z 的计算与选择取叶片数Z=8,叶片进口角0155.8β=。
- 1、下载文档前请自行甄别文档内容的完整性,平台不提供额外的编辑、内容补充、找答案等附加服务。
- 2、"仅部分预览"的文档,不可在线预览部分如存在完整性等问题,可反馈申请退款(可完整预览的文档不适用该条件!)。
- 3、如文档侵犯您的权益,请联系客服反馈,我们会尽快为您处理(人工客服工作时间:9:00-18:30)。
离心泵叶轮的设计
离心泵的水力设计主要是设计叶轮和泵壳,下面我们了解下其中的叶轮。
离心泵产生的理论压头计算:
离心泵常被认为是一种动能机器。
叶轮的旋转使叶轮中的流体高速旋转,从而将能量传递给液体,这个概念可以用数学等式表示出来:
H i=u2x c u2/g
式中H i——离心泵产生的理论压头,ft;
u2——叶轮外直径处的旋转速度,ft/s;
c u2——液体离开叶轮的旋转速度,ft/s;
g——重力加速度,ft/s2。
下面是3种基本的叶轮设计:
1)封闭式叶轮,在叶轮的前后面都有封闭罩(旋转壳体);
2)半开放式叶轮,只在一边有封闭护罩,并且紧密地和另外一边静止壳体相连;
3)开放式叶轮,只在一边有或者没有封闭罩(如图)。
离心泵中液体的转速:
流体进入离心泵吸入管时没有旋转速度,当流体进入叶轮的旋转管路中时,它开始以叶轮的旋转速度旋转。
液体被挤出叶轮中心,并且它的旋转速度与叶轮直径成比例。
可以用下面方式算出任何直径的液体叶轮转速:
u=D X N/229
式中u——液体旋转速度,ft/s;
D——速度计算点的直径,in;
N——叶轮旋转速度,r/min;
1/229——单位换算系数。
叶轮里压头损失通常包括摩擦损失、涡流损失、流体再循环损失、入口耗损和出口损失。
在壳体会发生附加损失。
应当注意的是,离心泵产生的压头取决于流体速度而不是被泵吸入的流体。