氢腐蚀
氢腐蚀
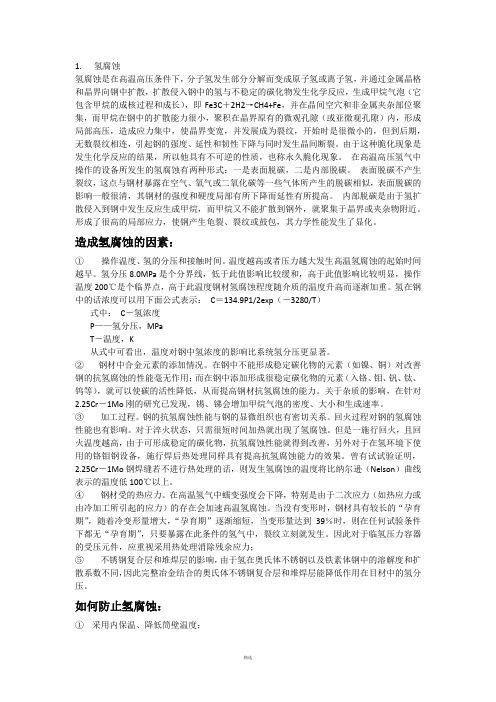
1. 氢腐蚀氢腐蚀是在高温高压条件下,分子氢发生部分分解而变成原子氢或离子氢,并通过金属晶格和晶界向钢中扩散,扩散侵入钢中的氢与不稳定的碳化物发生化学反应,生成甲烷气泡(它包含甲烷的成核过程和成长),即Fe3C+2H2→CH4+Fe,并在晶间空穴和非金属夹杂部位聚集,而甲烷在钢中的扩散能力很小,聚积在晶界原有的微观孔隙(或亚微观孔隙)内,形成局部高压,造成应力集中,使晶界变宽,并发展成为裂纹,开始时是很微小的,但到后期,无数裂纹相连,引起钢的强度、延性和韧性下降与同时发生晶间断裂。
由于这种脆化现象是发生化学反应的结果,所以他具有不可逆的性质,也称永久脆化现象。
在高温高压氢气中操作的设备所发生的氢腐蚀有两种形式:一是表面脱碳,二是内部脱碳。
表面脱碳不产生裂纹,这点与钢材暴露在空气、氧气或二氧化碳等一些气体所产生的脱碳相似,表面脱碳的影响一般很清,其钢材的强度和硬度局部有所下降而延性有所提高。
内部脱碳是由于氢扩散侵入到钢中发生反应生成甲烷,而甲烷又不能扩散到钢外,就聚集于晶界或夹杂物附近。
形成了很高的局部应力,使钢产生龟裂、裂纹或鼓包,其力学性能发生了显化。
造成氢腐蚀的因素:①操作温度、氢的分压和接触时间。
温度越高或者压力越大发生高温氢腐蚀的起始时间越早。
氢分压8.0MPa是个分界线,低于此值影响比较缓和,高于此值影响比较明显,操作温度200℃是个临界点,高于此温度钢材氢腐蚀程度随介质的温度升高而逐渐加重。
氢在钢中的话浓度可以用下面公式表示:C=134.9P1/2exp(-3280/T)式中:C-氢浓度P——氢分压,MPaT-温度,K从式中可看出,温度对钢中氢浓度的影响比系统氢分压更显著。
②钢材中合金元素的添加情况。
在钢中不能形成稳定碳化物的元素(如镍、铜)对改善钢的抗氢腐蚀的性能毫无作用;而在钢中添加形成很稳定碳化物的元素(入铬、钼、钒、钛、钨等),就可以使碳的活性降低,从而提高钢材抗氢腐蚀的能力。
钢铁发生析氢腐蚀的条件

钢铁发生析氢腐蚀的条件析氢腐蚀,又称为氢腐蚀,是指氢原子穿透金属物质结构,在内部氧化形成氢氧化物的一种化学反应。
它是一种逆转的化学反应,金属由其原子的小分子及晶体形态转变为由有机分子组成的非结晶型的弱的、非晶质状的陶粒状结构。
析氢腐蚀是一种把钢铁变脆的事情,在特定条件下,析氢腐蚀可以来做一些特定事情,如增加金属口感或形状。
钢铁析氢腐蚀发生的条件:水与空气中的温度,pH值,氧含量,pH和水活度是析氢腐蚀发生的重要因素,pH值低于7时,酸性条件下更易发生析氢腐蚀。
此外,还有一些金属有抗空气性的这一性质,它会抗拒氧化,光照,空气中的有害气体的蔓延,所以它的析氢腐蚀性质也较小。
析氢腐蚀过程存在“负反馈”,当氢氧化物在氢渗纳过程中析出时,它会以析出更多的氢将触媒作用降低;而氢氧化物不能完全氢渗纳时,氢氧化物就会析出更多的氢,从而维持平衡。
钢铁在析氢腐蚀发生时,金属发生变脆,金属口感或形状会发生
变化,这时内部钢铁结构就发生了改变,最终钢铁会发生裂缝,造成
钢铁损坏。
为了避免钢铁发生析氢腐蚀,采取的最有效的措施是改变环境条件,增加钢铁的耐腐蚀性,比如减少温度、湿度,改变pH值,维护湿度、湿度等,使得环境条件有利于钢铁抗腐蚀。
另外,金属表面也可
以采取有机氧化物、金属盐涂层等抗腐蚀措施,增加金属表面对腐蚀
的抵抗能力。
另外,采取有效的油脂润滑添加剂,如润滑滴剂、抗磨
润滑剂等,以增加金属的耐腐蚀性,使金属表面结构稳定。
从上面可以看出,想要避免钢铁发生析氢腐蚀,就要改变周围环
境条件,增强钢铁表面对抗腐蚀的能力,采取正确的油脂润滑添加剂,这样才能够有效地防止钢铁发生析氢腐蚀。
析氢腐蚀的实例

析氢腐蚀的实例
氢腐蚀是一种金属腐蚀现象,主要是由于金属表面与氢气发生反应产生氢化物或氢离子,导致金属内部发生损伤。
以下是几个氢腐蚀的实例:
1. 石油钻井管道:石油中含有大量的氢化物,当石油通过钻井管道时,其中的氢化物会与管道金属发生反应,生成氢离子并引起金属的氢腐蚀。
2. 锅炉和蒸汽发生器:在高温高压的蒸汽环境中,金属表面会受到腐蚀,氢离子会渗入金属内部,导致金属的氢腐蚀。
3. 高强度钢材:一些高强度钢材在应力环境下容易发生氢腐蚀。
例如,当高强度钢材处于腐蚀性介质中,并承受着应力时,金属表面会产生氢离子,并在应力作用下渗入金属内部,导致氢脆和氢腐蚀的发生。
4. 镀锌钢材:在某些环境条件下,如酸性环境或高温环境,锌会与酸中的氢离子反应生成氢气,从而引起锌的氢腐蚀。
这些都是氢腐蚀的实例,氢腐蚀会导致金属的强度和耐久性下降,甚至引起严重的结构破坏,因此需要采取适当的防护措施来减少氢腐蚀的发生。
发生析氢腐蚀的条件

发生析氢腐蚀的条件
析氢腐蚀是指金属在氢气环境下发生的腐蚀过程。
析氢腐蚀本质上是金属与氢
气发生化学反应,金属溶解中被氢气所腐蚀,而金属上形成一层薄膜,严重时直接穿透金属,形成一种称为析氢点的痕迹或裂纹。
关于析氢腐蚀发生的条件,首先要考虑的是氢气的作用。
氢气既是最重要的气
体之一,也是一种有活性的气体,它能够与金属发生化学反应,考虑到析氢腐蚀的发生,有必要说明氢气的浓度和温度的水平。
一般来说,当氢气浓度超过一定比例或在高温条件下时,析氢腐蚀将会发生。
另外,金属材质也会影响析氢腐蚀的发生。
析氢腐蚀的发生取决于金属的化学
成分、组织结构和形态,还可能受到介质中的微量元素的影响。
由于不同的金属有不同的塑性、热力学性质和电化学性质,所以金属对氢气的腐蚀率也有所不同。
一般来说,金属铁和钢的析氢腐蚀程度较高,而镍和钴的析氢腐蚀程度却较低。
此外,析氢腐蚀还受到环境条件的影响。
当环境中的氧气含量为0%时,金属
更容易受到析氢腐蚀的影响,因为氧气和氧气之间会酸化,而金属与氢气则会形成反应,从而加速金属的腐蚀速度。
另外,环境中的空气湿度也会影响析氢腐蚀过程,当湿度较高时,金属腐蚀会变得更加严重。
总之,析氢腐蚀是一种金属在高氢气浓度、高温和无氧条件下发生的腐蚀过程,受金属材质,空气湿度及外界环境条件的影响,对于金属妆件的腐蚀会对金属结构造成很大的破坏,因此在使用时必须加以警惕。
炼油装置设备的氢腐蚀、氢鼓包、氢脆和氢蚀
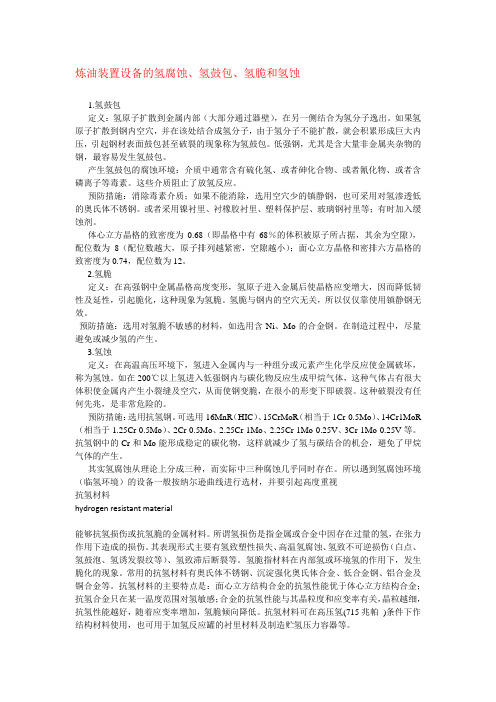
炼油装置设备的氢腐蚀、氢鼓包、氢脆和氢蚀1.氢鼓包定义:氢原子扩散到金属内部(大部分通过器壁),在另一侧结合为氢分子逸出。
如果氢原子扩散到钢内空穴,并在该处结合成氢分子,由于氢分子不能扩散,就会积累形成巨大内压,引起钢材表面鼓包甚至破裂的现象称为氢鼓包。
低强钢,尤其是含大量非金属夹杂物的钢,最容易发生氢鼓包。
产生氢鼓包的腐蚀环境:介质中通常含有硫化氢、或者砷化合物、或者氰化物、或者含磷离子等毒素。
这些介质阻止了放氢反应。
预防措施:消除毒素介质;如果不能消除,选用空穴少的镇静钢,也可采用对氢渗透低的奥氏体不锈钢。
或者采用镍衬里、衬橡胶衬里、塑料保护层、玻璃钢衬里等;有时加入缓蚀剂。
体心立方晶格的致密度为0.68(即晶格中有68%的体积被原子所占据,其余为空隙),配位数为8(配位数越大,原子排列越紧密,空隙越小);面心立方晶格和密排六方晶格的致密度为0.74,配位数为12。
2.氢脆定义:在高强钢中金属晶格高度变形,氢原子进入金属后使晶格应变增大,因而降低韧性及延性,引起脆化,这种现象为氢脆。
氢脆与钢内的空穴无关,所以仅仅靠使用镇静钢无效。
预防措施:选用对氢脆不敏感的材料,如选用含Ni、Mo的合金钢。
在制造过程中,尽量避免或减少氢的产生。
3.氢蚀定义:在高温高压环境下,氢进入金属内与一种组分或元素产生化学反应使金属破坏,称为氢蚀。
如在200℃以上氢进入低强钢内与碳化物反应生成甲烷气体,这种气体占有很大体积使金属内产生小裂缝及空穴,从而使钢变脆,在很小的形变下即破裂。
这种破裂没有任何先兆,是非常危险的。
预防措施:选用抗氢钢。
可选用16MnR(HIC)、15CrMoR(相当于1Cr-0.5Mo)、14Cr1MoR (相当于1.25Cr-0.5Mo)、2Cr-0.5Mo、2.25Cr-1Mo、2.25Cr-1Mo-0.25V、3Cr-1Mo-0.25V等。
抗氢钢中的Cr和Mo能形成稳定的碳化物,这样就减少了氢与碳结合的机会,避免了甲烷气体的产生。
氢腐蚀
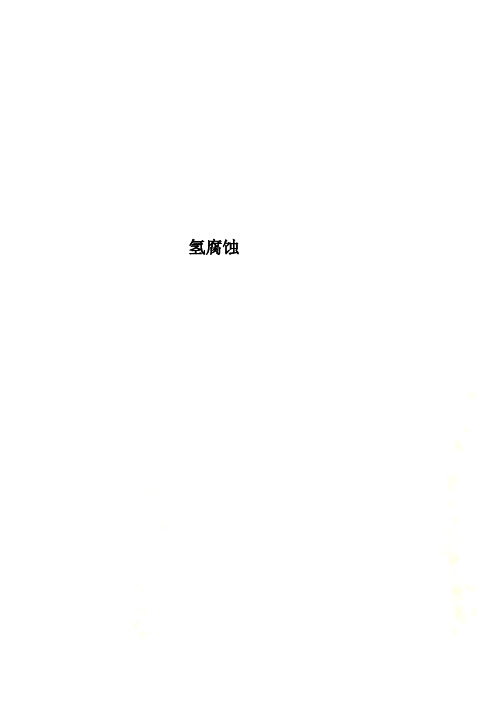
氢腐蚀1. 氢腐蚀氢腐蚀是在高温高压条件下,分子氢发生部分分解而变成原子氢或离子氢,并通过金属晶格和晶界向钢中扩散,扩散侵入钢中的氢与不稳定的碳化物发生化学反应,生成甲烷气泡(它包含甲烷的成核过程和成长),即Fe3C+2H2→CH4+Fe,并在晶间空穴和非金属夹杂部位聚集,而甲烷在钢中的扩散能力很小,聚积在晶界原有的微观孔隙(或亚微观孔隙)内,形成局部高压,造成应力集中,使晶界变宽,并发展成为裂纹,开始时是很微小的,但到后期,无数裂纹相连,引起钢的强度、延性和韧性下降与同时发生晶间断裂。
由于这种脆化现象是发生化学反应的结果,所以他具有不可逆的性质,也称永久脆化现象。
在高温高压氢气中操作的设备所发生的氢腐蚀有两种形式:一是表面脱碳,二是内部脱碳。
表面脱碳不产生裂纹,这点与钢材暴露在空气、氧气或二氧化碳等一些气体所产生的脱碳相似,表面脱碳的影响一般很清,其钢材的强度和硬度局部有所下降而延性有所提高。
内部脱碳是由于氢扩散侵入到钢中发生反应生成甲烷,而甲烷又不能扩散到钢外,就聚集于晶界或夹杂物附近。
形成了很高的局部应力,使钢产生龟裂、裂纹或鼓包,其力学性能发生了显化。
造成氢腐蚀的因素:①操作温度、氢的分压和接触时间。
温度越高或者压力越大发生高温氢腐蚀的起始时间越早。
氢分压8.0MPa是个分界线,低于此值影响比较缓和,高于此值影响比较明显,操作温度200℃是个临界点,高于此温度钢材氢腐蚀程度随介质的温度升高而逐渐加重。
氢在钢中的话浓度可以用下面公式表示: C=134.9P1/2exp(-3280/T)式中: C-氢浓度P——氢分压,MPaT-温度,K从式中可看出,温度对钢中氢浓度的影响比系统氢分压更显著。
②钢材中合金元素的添加情况。
在钢中不能形成稳定碳化物的元素(如镍、铜)对改善钢的抗氢腐蚀的性能毫无作用;而在钢中添加形成很稳定碳化物的元素(入铬、钼、钒、钛、钨等),就可以使碳的活性降低,从而提高钢材抗氢腐蚀的能力。
氢气对铝合金的腐蚀条件

氢气对铝合金的腐蚀条件
氢气对铝合金的腐蚀主要与氢气的吸附和渗透有关。
氢气可以在铝合金表面吸附并渗透到金属晶体内部,导致铝合金发生氢脆和氢腐蚀。
以下是氢气对铝合金腐蚀的一些条件:
1.应力环境:氢脆通常在应力环境下发生,这意味着在受到应力的情况下,铝合金更容易吸附和渗透氢气。
例如,当铝合金处于拉伸或扭曲等应力状态下,氢脆的风险会增加。
2.氢气浓度:氢气的浓度是影响铝合金腐蚀的关键因素。
高浓度的氢气更容易引起铝合金的氢脆和氢腐蚀。
3.温度:温度对氢气在金属中的扩散速率起着重要作用。
较高的温度有助于氢气的渗透,增加了铝合金发生氢脆和氢腐蚀的风险。
4.含氧环境:在含氧环境中,氢气腐蚀可能更为显著。
氧气与氢气共同作用,加剧了铝合金的腐蚀过程。
5.金属结构:不同类型的铝合金对氢气的敏感性也有所不同。
某些铝合金可能对氢气更为敏感,容易发生氢脆和氢腐蚀。
为了减轻氢气对铝合金的腐蚀,可以采取一些措施,例如使用耐腐蚀的涂层来保护表面、避免应力环境、控制氢气浓度、降低温度等。
第三章 析氢腐蚀和吸氧腐蚀(09.3修改)
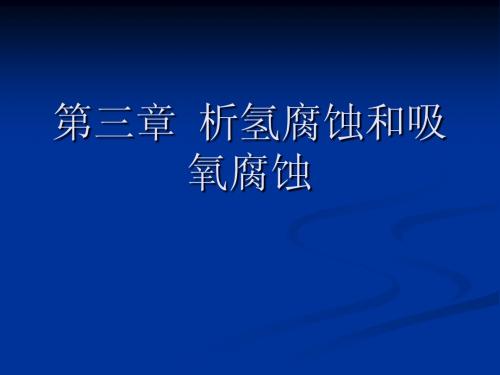
O ao bo lg ic
ao:与电极材料、表面状态、溶液组成和温度有关; bo:与电极材料无关。 • 氧离子化过电位越小,氧与电子结合越容易,腐蚀速率越大; 一般金属上氧离子化过电位都较高,多在1V以上。 当电流密度较小时,氧过电位与电流密度呈直线关系
ηO=ω i = RFi
在一定的阴极电流密度下氧还原反应的实际电位与该溶液中 氧电极的平衡电位间的差值,称为该电流密度下氧离子化过 电位,简称氧过电位,以ηO表示。
•与氢离子还原反应相比,氧还原反 应可在正得多的电位下进行,因此 氧去极化腐蚀比氢去极化腐蚀更为 普遍。 •大多数金属在中性和碱性溶液中以 及少数正电性金属在含有溶解氧的 弱酸性溶液中的腐蚀都属于氧去极 化腐蚀。
吸氧腐蚀发生的场合:
海水、大气和土壤——自然环境介质中普遍存在
碱类、盐类介质 酸性介质:析氢+吸氧
(3)
析氢腐蚀的基本原理
金属发生析氢腐蚀时,阴极上将进行如下反应:
由反应式可知,其最终产物是氢分子。当电极电 位比氢的平衡电位负时,上式的平衡就向右移动, 发生氢离子放电,溢出氢气;若电极电位比氢的 平衡电位略正时,平衡将向左移动,氢气转变为 氢离子。
发生析H2腐蚀的必要条件: EH>EM 对于 2H++2e H2 25℃时 E2 H / H 2 0.059 pH (V , 相对于SHE)
(i)如果腐蚀金属在溶液中的电 位较正,腐蚀过程中氧的传递 速度又很大,则金属腐蚀速度 主要由氧在电极上的放电速度 决定。这时阳极极化曲线与阴 极极化曲线相交于氧还原反应 的活化极化区(上图中的 Ee,OBC段)。
此时腐蚀电流密度小于极限扩 散电流密度,过程的控制步骤 是氧的离子化反应。 例如,铜在强烈搅拌的敞口溶 液中的腐蚀。
- 1、下载文档前请自行甄别文档内容的完整性,平台不提供额外的编辑、内容补充、找答案等附加服务。
- 2、"仅部分预览"的文档,不可在线预览部分如存在完整性等问题,可反馈申请退款(可完整预览的文档不适用该条件!)。
- 3、如文档侵犯您的权益,请联系客服反馈,我们会尽快为您处理(人工客服工作时间:9:00-18:30)。
combination of batch and continous inhibitors. Key words: Elemental Sulfur; corrosion; pitting corrosion; galvanic corrosion; inhibitor
0 引言:
元素硫沉积在高酸性气田普遍存在,危害巨大,是高酸性气藏开发中存在的棘手问题之一。 元素硫在地层、采气管和地面设施中沉积不仅可能造成硫堵塞或关井停产,还可能带来灾难性的 设备腐蚀问题。随着高含硫气藏的开发,目前国内外对元素硫腐蚀问题的研究逐渐引起重视。 元素硫的腐蚀性在 1953 年被初次发现, Farrer 和 Wormwell[1]将硫的悬浊液作为钢和铁的浸蚀 剂,发现 30℃时含 20%悬浮硫的溶液与含 3%盐酸溶液具有相同的腐蚀性,并且金属的腐蚀速率 随悬浮的硫含量增加而增加。直到 1978 年,MacDonald 等[2]进一步对湿硫条件下碳钢的腐蚀行为 开展了系统研究,发现灾难性的元素硫腐蚀需要一定的孕育期,其腐蚀行为受元素硫的粒径和溶 液的初始 pH 值的影响。 加注缓蚀剂作为一种高效、经济的腐蚀控制方法被石油、天然气工业广泛采用。 Bruckhoff 等[3]对缓蚀剂控制硫腐蚀进行了研究,发现在元素硫存在环境,被研究的常用成膜型缓蚀剂的缓 蚀效率都不佳或需要在很高的浓度下才发挥缓蚀效果,一些石油、天然气工业常用的商业吸附型 缓蚀剂对于控制元素硫腐蚀无效(如咪唑啉基)或者不能过量使用。 根据中国石油化工集团公司企业标准Q/SH 0247-2009(川东北高含硫化氢气田集输管道腐蚀 监测与控制设计技术要求)的规定, 缓蚀剂在生产现场使用以前应根据材料的材质并模拟工况条件 进行缓蚀剂性能评价。当有元素硫存在时,缓蚀剂的评价应该包括元素硫的影响。 根据分析,某气田集输管道存在元素硫沉积的可能性。本文以某气田集输管道为研究背景, 研究 L360 抗硫钢在含元素硫的环境的腐蚀行为,评价缓蚀剂性能,为其它类似天然气集输管道 的元素硫腐蚀与缓蚀剂控制提供参考。
1. 实验方法
实验材料为 L360 抗硫钢,表 1 是采用 X-MET3000 快速 X 射线合金成份仪测得的 L360 钢的 化学成份。图 1 是对 L360 钢机械磨抛至 1m 后用 10%硝酸酒精溶液擦蚀 10s,采用 STM6 显微 镜观察的金相照片。L360 的组织结构为珠光体和铁素体,其中亮白色部分为铁素体,蓝色部分为 珠光体。实验温度为 35℃,压力为常压,溶液为 3.5%NaCl l 溶液。按照 GB 10124-88 要求,所有 腐蚀实验试样均加工成表面积大于 10cm2 的块状试样。在试样边缘部分钻一直径为 3mm 的小孔, 便于悬挂试样。由于升华硫粉 S8 不溶于水,实验前将升华硫粉在压片机上压片成形。在 150mL 的锥形瓶中加入实验溶液和 45g 升华硫 S8, 通 1 小时 CO2 排出实验溶液中的 O2 并使其被 CO2 饱和, 采用 HCl 溶液或 NaOH 溶液调节实验溶液的 pH 值为 5。所有试样工作表面依次经 150#,400#和 600#水磨砂纸打磨,丙酮超声清洗,干燥,然后用感量为 0.1mg 的电子天平称重。锥形瓶中放入 三个称重后的试样,并使其表面完全被升华硫覆盖。实验周期为 1~6 天。实验后金属表面的腐蚀
(1. SINOPEC Qingdao Research Institute of Safety Engineering;2. China University of Petroleum, Qingdao 266071)
Abstract: Corrosion, galvanic corrosion and inhibition for L360 steel in the presence of elemental sulfur was studied in the laboratary to simulate the condition of a natural gas gathering line. It was found that elemental sulfur can cause severe general corrosion and pitting corrosion, and the general corrosion was increased by about 50 times. The corrosion behavior between the metal surface directly contacted with elemental sulfur and the metal surface not directly contacted with elemental sulfur were different, an obvious corrosion potential difference was observed, which indicated that the deposition of elemental sulfur in the gathering line can cause galvanic corrosion. The corrosion of L360 steel in the presence of elemental sulfur can be inhibited by the batch inhibitor alone, and possibly controlled by the
(a)
(b) 图 3 3.5%NaCl 溶液中未添加元素硫条件下腐蚀产物清除后金属 表面形貌(a)和厚度图(b) Fig.3 The surface morphology(a)and the thickness change (b) in the absence of elemental sulfur in 3.5% NaCl solution after film removal
图 4 为 3.5%NaCl 溶液中添加元素硫条件下清洗掉腐蚀产物膜后的金属表面形貌(a)和侧面厚 度(b)照片。从表面形貌可以看出:1~6 天内,金属表面都出现了肉眼可见的小孔腐蚀,小孔腐蚀 随浸泡时间增加变得更加严重。这说明元素硫腐蚀主要表现为小孔腐蚀;从侧面厚度可以看出:3 天后试片的厚度明显减薄,并且随浸泡时间的增加试片变得越来越薄。 综上所述,在 3.5%NaCl 溶液中,元素硫的腐蚀性很强,添加元素硫后金属的均匀腐蚀速率
在天然气工业,批处理缓蚀剂膜的厚度和均匀性受很多因素的影响,很难在实验室准确模拟这些 因素的影响。因此,在实验室对缓蚀剂膜的评估通常采用浸和滴(dip and drip)的方法,这个方 法比较简单,方便。
本文的批处理缓蚀剂成膜采用浸和滴(dip and drip)的方法,将打磨后的金属试样在缓蚀剂溶液 中浸泡 10s,在空气中悬挂 1 小时晾干形成缓蚀剂膜,用棉球将金属蚀速率为实测腐蚀速率除以某一相同系数,但这不影响比较金属腐蚀 速率的变化趋势。
2. 实验结果
2.1 3.5%NaCl 溶液中添加元素硫条件下金属的腐蚀行为
图 2 为 3.5%NaCl 溶液中添加和未添加元素硫条件下金属均匀腐蚀速率随时间的变化。 从图 中可以看出:1~6 天内,未添加元素硫条件下,金属的均匀腐蚀速率很低,但元素硫的添加加速 了金属的腐蚀,使均匀腐蚀速率增加至未添加元素硫条件下的约 50 倍。
图 3 为 3.5%NaCl 溶液中未添加元素硫条件下清洗掉腐蚀产物膜后的金属表面形貌(a)和厚度 照片(b)。1~6 天内,金属表面没有小孔腐蚀,试片的厚度随时间基本上保持不变,这主要是因为 均匀腐蚀速率(图 2)很低。
(a)
(b) 图 4 3.5%NaCl 溶液中添加元素硫条件下腐蚀产物清除后金属 表面形貌(a)和厚度图(b) Fig.4 The surface morphology(a)and the thickness change (b) in the presence of elemental sulfur in 3.5% NaCl solution after film removal
增加约 50 倍,元素硫腐蚀主要表现为均匀腐蚀和小孔腐蚀。
2.2 元素硫存在环境的电化学腐蚀研究
图 5 和图 6 分别为存在及不存在元素硫条件下金属的腐蚀速率及腐蚀电位随浸泡时间的变化 图。从腐蚀速率变化可以看出:在不含元素硫的环境,金属的腐蚀速率很低;在含元素硫的环境, 与元素硫直接接触的金属腐蚀速率很高,这与图 2 的结果一致;但未与元素硫直接接触的金属腐 蚀速率比不含元素硫环境的金属腐蚀速率更低,这可能是因为在元素硫存在环境,在金属表面形 成了保护性的 FeS 膜。从腐蚀电位可以看出:存在元素硫环境下的金属腐蚀电位比不含元素硫条 件下高,并且在元素硫存在环境,直接与元素硫接触的金属的腐蚀电位明显高于未与元素硫直接 接触的腐蚀电位;综合图 5 和图 6 的结果说明:在元素硫存在环境,元素硫沉积部位的金属与未 沉积元素硫部位的金属之间可能形成电偶腐蚀。
Paper No.
11010
元素硫存在条件下 L360 钢的腐蚀行为及缓蚀剂性能研究
蒋秀 1,张艳玲 1,左甜 2,宫庆想 2,黄玉萍 2,刘小辉 1
(1. 中国石油化工股份有限公司青岛安全工程研究院;2.中国石油大学(华东),青岛 266071)
摘要:本文以某气田集输管道工况为研究背景,通过实验室模拟研究 L360 抗硫钢在元素硫条件下的腐蚀行为、 电偶腐蚀行为及缓蚀剂性能。研究结果表明:元素硫的腐蚀性很强,使金属的均匀腐蚀速率增加约 50 倍,腐蚀 形式主要表现为严重的均匀腐蚀和小孔腐蚀;在含元素硫的环境中,元素硫直接接触的金属与未和元素硫直接 接触的金属的腐蚀行为不同,存在明显的腐蚀电位差,元素硫的沉积可能导致电偶腐蚀;批处理缓蚀剂对元素 硫腐蚀有一定的抑制作用;在批处理和连续加注缓蚀剂的共同作用下,元素硫腐蚀可以得到有效控制。 关键词: 元素硫;腐蚀;小孔腐蚀;电偶腐蚀;缓蚀剂
产物膜清洗液配置及使用方法参照 GB/T 16545-1996,即:500 mL 浓度为 36%的盐酸加 3.5 g 六 次甲基四胺,加蒸馏水配制成 1000 mL 溶液,在 20~25℃下清洗试样 10min。实验前,取 5 个空 白试样,按上述方法清洗,并称量清洗前后的失重,其平均失重小于 0.1 mg。说明此清洗方法是 可靠的。 腐蚀速度按下式计算: w V 24 365 st 其中 ρ:材料密度(g/mm3); s:试样表面积(mm2); t:实验周期(h); ∆w:实验前后试样失重(g)。 采用日立公司带有 EDX 功能的 S3400N 型扫描电镜(SEM)对试样表面做形貌观察和元素分 析。