电液伺服阀性能测试系统设计方法
刹车电液压力伺服阀测试系统的设计与实现

阀激励信号频率范 围 输入 电流信 噪比
Hz
l~ 4 0 ≤0 . 1 %
参 数 的测试 。系统测 试项 目包 括伺 服 阀静态 性能 测试 和其动 态性 能测 试 , 以及 液压锁 性 能测试 , 伺 服 阀静态
8 . 压力表线 1 7 . 蓄能器 l 8 . 电磁球 阀
1 3 . 低压溢流阀
1 4 . 2 m液柱
1 5 . 油箱
图 1 试 验 台 液压 系统 原 理 图
位油路 的通 断 , 完 成锁 单 独i 贝 0 试 试 验 和 阀锁 联 试测 试
试验 。
试验台
压力传感器 1
I源模块 l
ZHAO Xu. c h a ng ,ZHANG Zh e 。 HUANG J i n g ,L I C h a n g . c h u n
,
( 1 . 北京交通大学 机械与电子控制工程学院 , 北京
1 0 0 0 4 4;
2 . 中国航天科技集 团公 司第一研究 院十八所 , 北京
关键 词 : 液压 ; 测控 系统 ; 二分 法 ; 巴特 沃斯 滤波 器 中 图分类 号 : T H1 3 7 。 T P 2 7 3 文 献标 志码 : B 文章 编 号 : 1 0 0 0 - 4 8 5 8 ( 2 0 1 3 ) 1 1 - 0 0 7 1 05 -
引 言
表 1 试 验 台技 术指 标 项目 额定 工作 压力 单 位 MP a 指 标 2 1
标 如 表 1所示 。
7 2
液压 与 气动
高频响电液伺服阀的控制系统设计与优化

高频响电液伺服阀的控制系统设计与优化摘要:高频响电液伺服阀是一种能够快速、准确地控制液压系统流量和压力的关键元件。
本文主要探讨了高频响电液伺服阀的控制系统设计与优化方法。
首先,介绍了高频响电液伺服阀的工作原理和特点。
然后,详细阐述了控制系统设计的关键问题,包括传感器的选择、控制器的设计、反馈控制算法的优化等。
最后,结合实际案例,展示了控制系统设计与优化在高频响电液伺服阀中的应用效果。
1. 引言高频响电液伺服阀是液压系统中重要的执行元件,广泛应用于工业设备和机械控制领域。
它具有快速响应、高精度和较大流量控制范围等特点,对于机械系统的稳定性和性能至关重要。
因此,控制系统设计与优化对于高频响电液伺服阀的使用和应用至关重要。
2. 高频响电液伺服阀的工作原理和特点高频响电液伺服阀的工作原理是通过电磁力控制和调节液阻,实现液压系统的流量和压力的控制。
它采用高灵敏度电磁阀芯和动态稳压机构,能够快速响应输入信号并精确控制液压系统的参数。
高频响电液伺服阀的特点包括响应时间短、流量控制精度高、可靠性好等。
3. 高频响电液伺服阀控制系统设计的关键问题3.1 传感器的选择传感器的选择对控制系统的准确性和可靠性具有重要影响。
在高频响电液伺服阀控制系统设计中,常用的传感器包括位移传感器、速度传感器和压力传感器。
根据具体的应用需求和系统要求,选择合适的传感器进行测量和反馈。
3.2 控制器的设计控制器是控制系统的核心部分。
在高频响电液伺服阀中,通常采用PID控制器来实现稳定的控制。
PID控制器通过计算误差、积分和微分来调节和修正输出信号,从而实现对液压系统的控制。
在控制器设计中,需要考虑控制系统的动态响应特性和稳定性,选择合适的参数进行调节和优化。
3.3 反馈控制算法的优化反馈控制算法对于高频响电液伺服阀的性能至关重要。
常用的反馈控制算法包括位置控制、速度控制和压力控制等。
在优化反馈控制算法时,需要考虑实际的控制需求、系统动态特性和系统稳定性等因素,并结合实际的试验数据进行参数调整和优化。
高频响电液伺服阀的静态与动态特性测试方法

高频响电液伺服阀的静态与动态特性测试方法引言:高频响电液伺服阀是一种广泛应用于工业自动化系统中的重要元件。
为了确保其正常运行和稳定性,需要对其静态与动态特性进行测试。
本文将介绍高频响电液伺服阀的静态与动态特性测试的具体方法。
第一部分:高频响电液伺服阀的静态特性测试方法静态特性测试是评估伺服阀性能的重要手段之一。
以下是高频响电液伺服阀静态特性测试的步骤和方法:步骤一:准备测试装置与仪器a. 确保测试装置能够提供足够的压力和流量,并且具备快速响应的能力。
b. 安装测试仪器,包括流量计、压力计和温度计等。
步骤二:测试前的准备工作a. 检查伺服阀的连接是否牢固,并进行必要的润滑和清洁。
b. 确定测试所需的工作条件,包括压力、温度和流量等。
步骤三:进行静态特性测试a. 断电,确保伺服阀处于关闭状态。
b. 通过调节控制仪对伺服阀进行一定的输入信号。
c. 测量伺服阀的流量、压力和阀芯位置等数据。
d. 循环进行不同输入信号的测试,记录测试数据。
步骤四:数据处理与分析a. 对测试得到的数据进行整理和处理。
b. 绘制流量-压力曲线和流量-阀芯位置曲线等图形。
c. 分析测试结果,评估伺服阀的静态特性表现。
第二部分:高频响电液伺服阀的动态特性测试方法动态特性测试能够评估伺服阀的响应速度和稳定性。
以下是高频响电液伺服阀动态特性测试的步骤和方法:步骤一:准备测试装置与仪器a. 确保测试装置能够提供足够的压力和流量,并具备高频响应的能力。
b. 安装测试仪器,包括快速采集系统、压力计和位移传感器等。
步骤二:测试前的准备工作a. 检查伺服阀的连接是否牢固,并进行必要的润滑和清洁。
b. 确定测试所需的工作条件,包括压力、温度和流量等。
步骤三:进行动态特性测试a. 通过控制系统向伺服阀输入一系列具有不同频率和振幅的信号。
b. 使用快速采集系统记录伺服阀的输出压力和阀芯位置等数据。
c. 观察测试数据,评估伺服阀的响应速度和稳定性。
步骤四:数据处理与分析a. 对测试得到的数据进行整理和处理。
哈工大机电液系统测试技术大作业 电液伺服阀性能测试

H a r b i n I n s t i t u t e o f T e c h n o l o g y机电液系统实验测试技术大作业(二)设计方案:电液伺服阀性能测试系统学院:机电工程学院专业:机械设计制造及其自动化班级:学号:姓名:指导老师:时间:哈尔滨工业大学目录前言 (2)系统组成及功能 (2)电液伺服阀测试系统原理 (2)电液伺服阀特性测试 (3)静态测试 (3)动态测试 (9)传感器选型 (10)体会与心得 (10)参考文献 (11)1.前言电液控制伺服阀简称伺服阀,相对于普通液压系统中的常规阀来说,伺服阀是一种高级的、精密的液压元件。
伺服阀既是信号转换元件,又是功率放大元件。
在电液伺服控制系统中,伺服阀将系统的电气部分与液压部分连接起来,实现电液信号的转换与放大,对液压执行元件进行控制,具有控制精度高、响应速度快、信号处理灵活、输出功率大和结构紧凑等优点。
为了更好地利用电液伺服阀,必须对它进行充分的实验。
2.系统组成及功能电液伺服阀测试系统主要由泵站系统、测试台、计算机测控系统等组成。
小泵额定压力为21 MPa,流量10 L/min;大泵额定压力为7 MPa,流量90 L/min。
测试台设计成两个工位,即电液伺服阀静态测试工位和动态测试工位。
测控系统主要包括:电源开关电路、信号调理器、Avant测试分析仪、控制软件(液压CAT控制测试软件)和计算机系统。
测控系统实施对液压能源、液压测试台的控制,实现对电液伺服阀某项或多项液压参数测试的油路转换,同时采集各项所需的液压参数,经软件处理获得符合电液伺服阀试验规范要求的曲线、数据、报表等。
实现了对电液伺服阀的动、静态特性的实时显示及描绘,并自动进行相关数据分析和处理。
3.电液伺服阀测试系统原理电液伺服阀测试系统原理图如图1所示。
4.电液伺服阀特性测试4.1静态测试测试系统示意图如图2:图2 静态实验装置典型回路(1)空载流量特性测试用下列实验步骤测出输入电流与负载压降的变化关系,从而绘制空载流量特性曲线。
电液伺服阀测试系统研究
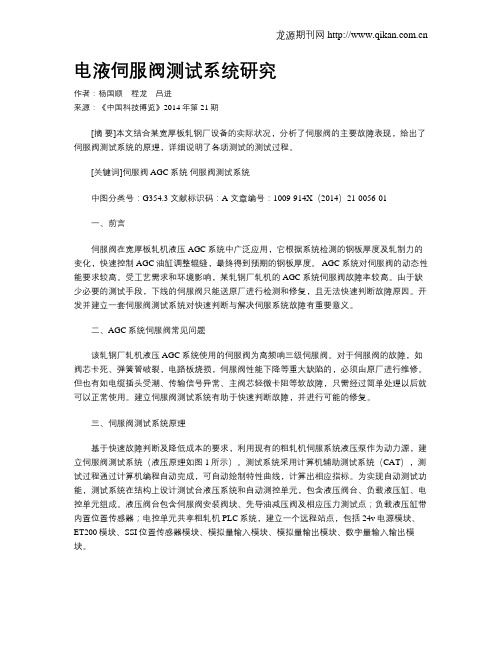
电液伺服阀测试系统研究作者:杨国顺程龙吕进来源:《中国科技博览》2014年第21期[摘要]本文结合某宽厚板轧钢厂设备的实际状况,分析了伺服阀的主要故障表现,给出了伺服阀测试系统的原理,详细说明了各项测试的测试过程。
[关键词]伺服阀 AGC系统伺服阀测试系统中图分类号:G354.3 文献标识码:A 文章编号:1009-914X(2014)21-0056-01一、前言伺服阀在宽厚板轧机液压AGC系统中广泛应用,它根据系统检测的钢板厚度及轧制力的变化,快速控制AGC油缸调整辊缝,最终得到预期的钢板厚度。
AGC系统对伺服阀的动态性能要求较高。
受工艺需求和环境影响,某轧钢厂轧机的AGC系统伺服阀故障率较高。
由于缺少必要的测试手段,下线的伺服阀只能送原厂进行检测和修复,且无法快速判断故障原因。
开发并建立一套伺服阀测试系统对快速判断与解决伺服系统故障有重要意义。
二、AGC系统伺服阀常见问题该轧钢厂轧机液压AGC系统使用的伺服阀为高频响三级伺服阀。
对于伺服阀的故障,如阀芯卡死、弹簧管破裂,电路板烧损,伺服阀性能下降等重大缺陷的,必须由原厂进行维修。
但也有如电缆插头受潮、传输信号异常、主阀芯轻微卡阻等软故障,只需经过简单处理以后就可以正常使用。
建立伺服阀测试系统有助于快速判断故障,并进行可能的修复。
三、伺服阀测试系统原理基于快速故障判断及降低成本的要求,利用现有的粗轧机伺服系统液压泵作为动力源,建立伺服阀测试系统(液压原理如图1所示)。
测试系统采用计算机辅助测试系统(CAT),测试过程通过计算机编程自动完成,可自动绘制特性曲线,计算出相应指标。
为实现自动测试功能,测试系统在结构上设计测试台液压系统和自动测控单元,包含液压阀台、负载液压缸、电控单元组成。
液压阀台包含伺服阀安装阀块、先导油减压阀及相应压力测试点;负载液压缸带内置位置传感器;电控单元共享粗轧机PLC系统,建立一个远程站点,包括24v电源模块、ET200模块、SSI位置传感器模块、模拟量输入模块、模拟量输出模块、数字量输入输出模块。
电液伺服阀静动态性能测试系统的研制

!!!!!!!!!!!!!!!!!!!!!!!!!!!!!!!!!!!!!!!!!!!!!!!! 流均为 DCC )Q。 而现有的用手动阀控制的试验 S BT 的试验精度要求, 图 L 中的节流阀 F 用于调整液压缸的空行程速 机的精度仅为 S LT 。这种电液比例控制的试验机不 度, 换向阀 BB 的 R 型中位机能用于动载试验, 其回油 口上设置单向阀 BC 是为了防止在承载试验时液压缸 的有杆腔泄空。 $ 结束语 采用电液比例控制技术实现的闭环压力控制, 完 成了手动控制无法胜任的功能, 其可靠性比电液伺服 控制高, 维 比 较 容 易, 在长时间保压时能够满足 万护 方数据
BD
液压与气动
ACCL 年第 A 期
" " " " " " " " " " " " " " " " " " " " " " " " " " " " " " " " " " " " " " " " " " " " " " " " " " " " " " " " " " " " " " " " " "
电液伺服阀试验系统设计与仿真
图5.8仿真结果
由仿真结果可以看出液压缸的位移、速度、伺服阀的流量、比较电压信号随着输入信号的输出变化。
电液伺服阀试验系统设计与仿真
55.Haykin S Communication System 1994
56.Controller Realization of a Teleoperated Dual-Wrist Assemblu System With Finite Word length Considerations 2001
42.Muneeb Khalid Data Acquisition Gains New High With PCI 1997
43.Tamra Kerns The Advantages of Multithreads Applications 1998
44.ISO 6404-1995(E).Hydraulic fluid power Servovalves Test method
52.范逸之2
53.范逸之Visual Basic与输入输出适配卡控制 2003
54.Oliver James H.Huang H-T Automatched path planning for integrated assembly design 1994(09)
论文从电液伺服阀静、动态特性的性能指标和测试原理出发,提出在静态测量中主要测量电液伺服阀的空载流量特性曲线、压力增益特性曲线、泄漏特性曲线;在动态测量中采用扫频法进行频率响应测试的理念。论文进行了测试系统的硬件设计和软件编程,主要完成了系统中各种硬件的配置以及测试系统结构的分析与设计。论文还针对测试系统的外围问题作了研究,如:电液伺服阀测试系统液压部分组成及其控制,测试系统的抗干扰设计等,为测试系统的可靠运行提供保证。最后使用本测试系统对某型电液伺服阀进行了静、动态特性测试,对所测得的结果进行了分析,找到了误差产生的原因。实验证明,本测试系统快速、简捷、精确地完成了电液伺服阀静、动态特性的测试。
电液伺服阀测试方法
电液伺服阀自动测试方法的研究广州博玮伺服科技有限公司•摘要:研究了电液伺服阀自动测试的方法。
给出了液压系统的工作原理,介绍了自动测控单元的硬件构成,详细论述了软件设计的核心算法和自动功能的实现。
1 前言电液伺服控制系统在控制领域中占有重要的地位,特别是在大功率、快速、精确的控制系统中起到重要作用。
电液伺服阀是其中的主要执行机构。
在阀出厂前和维修后进行性能测试是必不可少的环节。
传统的测试系统大都由分立的模拟仪表组成,在测试过程中,一般由模拟仪器在纸上记录模拟试验曲线或由试验人员记录试验数据,然后把数据进行手工处理得到性能指标。
显然,该方法工作量大、速度慢、效率低、精度差。
随着微电子技术和计算机技术的飞速发展,计算机辅助测试(CAT)技术在液压系统测试中得到了广泛的应用。
它具有测试精度高、速度快、性价比高、测试的重复性和可靠性高等优点,有着很好的应用前景。
因此,本文基于CAT技术,研究了实现电液伺服阀自动测试的方法。
2 自动测试系统工作原理根据GB/T15623—1995B标准,电液伺服阀的自动测试需要完成静态性能测试(空载特性、压力增益特性、负载特性)和动态性能测试(幅频特性、相频特性),在性能曲线上直接读出性能指标,并可以把曲线保存成可以随时调用的数据文件。
液压测试原理和国标相同。
自动测试就是利用现代的传感器技术、电子技术和计算机技术,原来由试验人员手工单点测试、读取模拟仪表、记录数据、描绘曲线的过程用自动测试系统迅速地自动连续地对各点进行测试、保存数据文件并自动生成性能曲线,从而得出电液伺服阀的各个性能指标。
其中,空载特性、负载特性、动态特性的测试最具代表性。
为实现自动测试功能,测试系统在结构上分为测试台液压系统和自动测控单元。
图1 测试台液压系统原理图测试台液压系统结构原理如图1所示。
在对电液伺服阀进行不同的特性测试时闸阀的开关状态如表1所示。
闸阀采用手动开关阀可以很好地密封液压回路,避免电磁开关阀有时出现行程不到位的缺点,减少测试误差。
电液伺服阀测试系统研究
卜 h ) ( 一 4  ̄ t o
得解 : h t 0= (9 1)
[ ] 朱新才 . 压 与气动 技术 [ .重庆 : 庆大 学 出版社 , 1 液 M] 重
2 000. ’
[ ] 何存兴 .液压元件[ . 2 M] 北京 : 机械工业 出版社 ,9 2 18 .
要从事流体传动与控制方面 的研究工作 。
即为 齿顶 与泵 体 间间隙 的功率 损失 。
或者 , 由压力 流 量 的乘 积 加 上 齿 顶 与 泵体 间 的粘
性摩擦 损 失功率 , 如式 1 所 示 , 6 亦得 同样 结果 。
:
z
- 一 础。 l : 【 6 ^ 考
图 功损与隙系 3 率失间关图
1 前 言
速 度快 、 号 处 理 灵 活 、 出 功 率 大 和 结 构 紧凑 等 优 信 输 点 。为 了更 好地 利用 电液伺 服 阀 , 须 对 它进 行充 分 必
的 实验 。
电液控 制伺 服 阀简称 伺 服 阀 , 对 于普 通 液压 系 相 统 中 的常规 阀 来 说 , 服 阀 是 一 种 高 级 的 、 密 的液 伺 精
一
厶
3
压测 试台 的控制 , 现对 电液伺服 阀某项 或多项 液压参 实 数测试 的油路转 换 , 同时采 集 各项 所需 的液 压参 数 , 经 软件 处理获得符合 电液伺服 阀试验 规 范要 求 的 曲线 、 数 据、 报表等 。实 现 了对 电液伺 服 阀 的动 、 态 特性 的 实 静
线 , 图 3所示 。该 曲线 表示 了损 失 功 率 与 间 隙 之 间 如 的关 系 。
与泵 体 间间 隙的最 佳 值 , 泵 的总 效 率 最佳 。对齿 轮 使
电液比例阀性能测试实验指导书
电液比例阀性能测试实验指导书实验项目1. 电液比例方向阀性能实验2. 电液比例溢流阀性能实验3. 电液比例调速阀性能实验唐山学院机电工程系实验一电液比例溢流阀性能测试一、实验液压原理图二、液压元件配置1-变量叶片泵2-先导式溢流阀3-电磁阀4-电液流量伺服阀2FRE6~20/10QM5-蓄能器6-被试阀电液比例溢流阀DBETR-10B/80M7、8-压力传感器9-加载用节流截止阀10-流量传感器11、12-截止阀13-压力表三、实验内容1、稳态压力控制特性测试测试阀控制电流与阀输出压力之间关系,画特性曲线,计算死区、滞环、非线性度。
2、稳态负载特性(压力-流量特性)测试控制输入电流、输出压力、负载干扰(流量)之间关系。
3、输入信号阶跃响应测试(选做)测试阀输出压力相对一定幅值输入电信号阶跃变化的过渡过程响应特性,画特性曲线,计算滞后时间、上升时间、过渡过程时间等。
4、频率响应特性测试测试阀对一组不同频率的等幅正弦输入信号的响应特性,画频响特性曲线(博德图),算幅频宽、相频宽。
四、实验方法●测试电回路接线操作:1)压力传感器-把P A、P B压力传感器信号线分别扦入控制面板上的模拟信号输入口1、2口。
2)电液比例溢流阀-把比例溢流阀电磁铁A线圈扦入比例溢流阀放大器电磁铁A扦座上,位移传感器信号线扦入放大器的阀蕊反馈扦座。
比例溢流阀放大器输入测试信号、输出测试信号用四蕊测试线分别扦入控制面板上的模拟信号输入口5、6口上,差动信号输入信号用二蕊测试线扦入控制面板上的模拟信号输出口1口上。
转换开关转入自动位置。
3)电液比例流量阀-把比例流量阀电磁铁A线圈扦入比例流量阀放大器电磁铁A扦座上,位移传感器信号线扦入放大器的阀蕊反馈扦座。
电液比例流量阀放大器差动输入信号号用二蕊测试线分别扦入控制面板上的模拟信号输出口2口上。
转换开关转入自动位置。
4)流量传感器-把大流量传感器、小流量传感器信号线分别扦入控制面板上的脉冲信号输入口1、2口上(模拟输入信号分别9、10通道)。
- 1、下载文档前请自行甄别文档内容的完整性,平台不提供额外的编辑、内容补充、找答案等附加服务。
- 2、"仅部分预览"的文档,不可在线预览部分如存在完整性等问题,可反馈申请退款(可完整预览的文档不适用该条件!)。
- 3、如文档侵犯您的权益,请联系客服反馈,我们会尽快为您处理(人工客服工作时间:9:00-18:30)。
( 上接第 36页 )
图 8 办公桌 成本屋 ( 产品概念 1)
图 2 自动测控单元硬件构 成
2 2 软件设计 实现电液 伺 服阀 自动 测试 的 核心 部分 是 软 件设 计。软件是实现产生自动控制信号和自动采集稳定数 据的主要部分。 如何自动产生控制被测阀和背压阀的电信号和自 动准确地采 集 各传 感器 的稳 定 数据 是软 件的 核 心功 能。在自动变换电液伺服阀的测试点时, 液压系统的 稳定正常情况下需 2~ 5 s , 当 电液伺服 阀因质 量问题 不能稳定时, 软件系统应能根据传感器的数据自动识 别并提示。软件设计部分的核心算法如图 3和图 4所 示。 图 3 是实 现 产生 自 动 控制信 号和 自动 准确 采 集 稳定数 据并 保存 的程 序 设 计流程。 U 1、 U 2 设定控 制 液 压 阀 电 压 信 号 上、 下 限, n 设定 曲 线 的 测 试 点 数。 U 是 自 动 产 生 控 制 电压信 号 的变 化 步长, 大 小由 ( U 1 - U 2 ) /n 决 定。 U 是控 制 液压 阀的 电 压 信 号, 按 U = U 2 + i U 的 递 增规律 自动 输出 以控 制 液 压 阀的 测 试 点 变 化。 q 是 根据静 态缸 和位 移传 感 器 计算所 得的 被测 阀工 作 流 量。 在 控 制 信 号 U 输 出 后, 程序 内设 定 了延 时 环 节, 其大 小可 根 据正 常 液 压阀测 试点 变换 时稳 定 时 间 来 经 验设 定, 一般 为 2 图 3 自动测控程序流程图 ~ 5s 。当 系 统 稳定 时, 系 统能从数据采集卡读取相应的传感器的稳定数据, 并 自动保存成数据表文件, 同时自动生成相应的性能曲 线。 图 4是根据传感器数据自动判断液压系统是否稳 定的程序设计流程。判断的依据是流量的变化和程序 | b- a | 的运 行时 间, 算 法上 通 过 实 现。 a、 b 是 t 程序运行的中 间变 量, t 是计 时器, n 设定 判断 稳定 时对数据进行比较的点数, 设定判断 稳定时 程序的 最大运行时 间, 设 定稳定 信号允 许的 误差, q 是静
ห้องสมุดไป่ตู้
0 前言 电液伺服 控制 系统 在 控制 领域 中 占有 重 要的 地 位, 特别是在大功率、快速、精确的控制系统中起到 重要作用。电液伺服阀是其中的主要执行机构。在阀 出厂前和维修后进行性能测试是必不可少的环节。传 统的测试系统大都由分立的模拟仪表组成, 在测试过 程中, 一般由模拟仪器在纸上记录模拟试验曲线或由 试验人员记录试验数据, 然后把数据进行手工处理得 到性能指标。显然, 该方法工作量大、速度慢、效率 低、精度差。 随着微电子技术和计算机技术的飞速发展, 计算 机辅助测试 ( CAT ) 技术在液压系统测试中得到了广 泛的应用。它具有测 试精 度高、速 度快、 性价比 高、 测试的重复性和可靠性高等优点, 有着很好的应用前 景。 因此, 本文 基于 CAT 技 术, 研究 了 实现 电液 伺 服阀自动测试的方法。 1 自动测试系统工作原理 根据 GB /T 15623 - 1995B 标 准, 电液伺 服阀 的自 动测试需 要完 成静 态性 能 测试 ( 空载 特性、 压力 增 益 特性、 负 载特 性 ) 和 动 态性 能 测 试 (幅 频 特 性、 相频特性 ), 在性能 曲线上直 接读出 性能指标, 并可 以把曲线保存成可以随时调用的数据文件。液压测试 [ 1] 原理和国标相同 。 自动测试就是利用现代的传感器技术、电子技术 和计算机技术, 原来由试验人员手工单点测试、读取 模拟仪表、记录数据、描绘曲线的过程用自动测试系 统迅速地自动连续地对各点进行测试、保存数据文件 并自动生成性能曲线, 从而得出电液伺服阀的各个性 能指标。其中, 空载特性、负载特性、动态特性的测 试最具代表性。 为实现自动测试功能, 测试系统在结构上分为测 试台液压系统和自动测控单元。
Abstrac t : T he m ethod of auto m atic testing servo - v alve w as stud ied T he hydrau lic syste m w as estab lished and the hardw are structure o f the auto m atic testing & contro lling un itw as introduced T he ar ithm etic of the softw are design and ho w to realize the autom at ic function w ere d iscussed K eyword s : A utoma tic test ; M e thod ; Servo - va lve ; A rithm etic
测试台液压系统结构原理如图 1所示。在对电液 伺服阀进行不同的特性测试 时闸阀的开 关状态如 表 1 所示。闸阀 采用 手动 开 关阀 可以 很 好地 密封 液 压回 路, 避免电磁开关阀有时出现行程不到位的缺点, 减 少测试误差。 电液伺服阀 8的各个测试点的自动变换由自动测 控单元控制, 完成空载特性测试和负载特性测试时被 测阀开口度变换的自动化过程。 为实现系统的自动加载, 采用比例溢流阀 5做背 压阀, 自动调节系统负载压力, 完成压力增益特性和 负载特性测试的自动化过程, 克服了手动加载的随机 干扰和量化不准确、耗时长等缺点。
文章编号 : 1001- 3881 ( 2005) 11- 114- 3
S tudy on the M ethod of A u tomatic Testin g Servo - valve
LI U Z i le,i WU Ba i ha,i ZOU D a peng ( Guangdong Un iv ersity of T echno lo gy, Guangzhou 510090 , China)
【1】 王占 林 社, 液压 伺 服控 制 北 京 : 航 空 航天 大 学出 版 1987 : 387~ 390
3 实验 图 4 判断液压系统稳 LabV IE W 作为 一种 定的程序 流程图 比较 规范、成 熟的 图形 化编程语言, 可以方便地开发出虚拟面板、自动控制 信号的产生和实现数据的采集、分析、处理和存储等 功能。 为了对所 作 的研 究做 进 一步 的 验证, 作 者基 于 LabV IE W 软件平 台, 按 照以 上的 测 试方 法, 对电 液 伺服阀自动测试系统做了部分开发。在搭建的简易试
本系统采用液压缸和位移传感器的方式计算电液 伺服阀的工作流量, 计算的流量不仅精确, 而且克服 了大流量流量计误 差偏大、有 最小 流量限 制的 缺点。 静态缸 23在限 位开关 22、 24和 电磁 换向 阀 21的 控 制下, 在静态性能测 试时相当 于缸 有无限 长的 行程。 对位移传感器 25 的位移信号进行微分与静态缸 23 的 有效面积的积即得电液伺服阀的工作流量, 流量的正 负由控制被测阀的电信号的正负决定。 动态性能 的 自动 测试 采 用频 域 扫频 法。 动态 缸 12的工作频率为 400H z , 满足被测电液伺服阀的动态 性能 测 试 要 求。 自 动 测 控 单 元 给 电 液 伺 服 阀 0 ~ 200H z的正弦激 励信 号, 根据 位移 传感 器 20 记录 的 动态缸的 位移 规 律, 从而 得 出电 液伺 服阀 的 动态 特 性。
《 机床与液 压 》 2005 N o 11
验台上用型号为 34B- H 10 /25B 电液比例换 向阀代替 电液伺服阀做了部分性能测试, 所测的性能曲线如图 5 和图 6所示。
4 结论 通过实验研究表明, 本文所述的电液伺服阀自动 测试的方法是完全可行的, 开发的系统是稳定的, 大 大提高了测试精度和测试速度。另外, 该方法还可以 灵活地应用于其它一些液压元件及系统的自动测试。 参考文献
116
态缸的流量。程序中的延时环节 决定了所要 判断的 n 个点 的时 差性, 进 一步 保证了 流量 q 的稳 定性 判断。从 自动 测试 系统 的 实 际 工 作 情 况 来 看, 若 n 取 10, 延 时 40 ~ 60m s效果较好。取值太 小, 不 能 准 确 判 断 稳 定, 取值 太 大, 则 浪费 系统的运行时间。 从以 上的 程序 设计 核心 算法 可以 看出, 该 算法 通用 性强, 适 用面 广, 可以 用不 同的 计算 机语言 来开发 电液 伺服 阀自 动 测试 的 软 件系 统。
2 基于 CAT 技术的自动测控单元 采 用 ∀ 工 控 机 + DA /AD 采 集 卡 # 及 相 应 的 传 感、变换电路组成信 号发生和 采集 的典型 硬件 系统, 结合编制的 专用 软件 组 成电 液伺 服阀 的 自动 测控 单 元。 自动测控单元可以自动控制 被测阀 8和 背压阀 5 的开口度按测试要求减小或增大, 并记录保存每个测 试点的压力、 流量、 电 流等 数 据, 自 动 生 成性 能 曲 线。 2 1 硬件构成 电液伺服 阀自 动测 控 单元 的硬 件 采用 ∀ 传感 器 + 数 据 采集 卡 + 工 控机 + 电 控器 # 的结 构, 如 图 2 所示。其中的压力传感器采用压阻式传感器, 位移传 感器采用 差动 变压 器 式传 感器。 A /D 数 据采 集卡 采 用研 华 的 PCL - 818L, 其 采 样 速 度 每 通 道 可 达
《 机床与液压 》 2005 N o 11 表 1 闸阀开关状态 特 闸 阀 4 11 13 15 19 开 ! 关 ! ! ! ! ! ! ! 性 空载特性 负载特性 动态特性
115
40kH z , 采用差 分输入 接线法, 有 8 个输入 通道, D / A 数据采集卡采用研华的 PCL - 726 , 可 以输出 DC ∃ 10V, 有 6个输出通 道, 输入输 出通道 的盈余可 以用 来检测其它液压系统时扩展之用。该测试结构的优点 是方便灵活, 通用性强。