压力容器封头成型工艺规程
封头制造工艺

编码:JYL技-01/11 版次:A 修改:1 页码:24/40封头压制工艺守则1 主题内容与适用范围本规程规定了受压封头冲压的技术要求和操作方法。
并适用于材质为碳钢、低合金钢的翻边、平拆管板、椭圆封头及碟形封头拱形管板的加热压制和修复。
2 引用标准GB/T25198-2010 《钢制压力容器用封头》GB/T25198-2010 《锅壳式锅炉受压元件制造技术条件》3 对操作人员的技术要求3.1 操作人员应熟悉图样、技术要求及工艺规范。
3.2 操作人员应熟悉所用设备、模具、工具的性能、结构及必要的维修知识,严格遵守操作规程。
加热炉和压力机的操作人员须持有操作许可证,方能上岗操作。
3.3 操作人员要认真做好现场管理工作,对工件、模具、工具应具有相应的工位器具,整齐放置在指定地点,防止碰损、锈蚀。
4 设备及工装4.1 各种油压机、加热炉、送料小车等设备的性能应符合设备说明书中的规定。
4.2 工装模具、工具、量具有成形模、复合模具、脱件装置、支脚、紧固扳手、手锤、大锤、风动砂轮、风铲、钢卷尺、盒尺、钢板尺、弯尺、卡尺、内外卡钳、测温仪等,模具应经检查合格方可使用。
量具与仪表应按规定经周期检定合格。
5 对封头毛坯的制作5.1封头毛坯尺寸(计算公式)P=1.2(PN+δ+2h)5.2划下料线时,先划十字中心线,再划坯料线及人孔开孔线,人孔之长短轴要与十字中心线重合且长轴必须与钢板轧制方向垂直(轧制方向通常为钢板长度方向)。
5.3下料时,封头毛坯外圆可用手工切割,易采用定心切割,推荐采用仿形切割。
5.4 封头毛坯的拼接5.4.1 封头毛坯应尽量采用整块钢板制成。
若需拼接时,允许由两块钢板按GB/T25198-2010标准和GB/T25198-2010标准、施工图样进行。
5.4.2 焊接后,内表面拼接焊缝以及影响成形质量的外表面拼接焊缝,在成形前应将焊缝余高打磨至与母材齐平,铲平长度为离圆坯外边缘300~350mm。
封头工艺规程
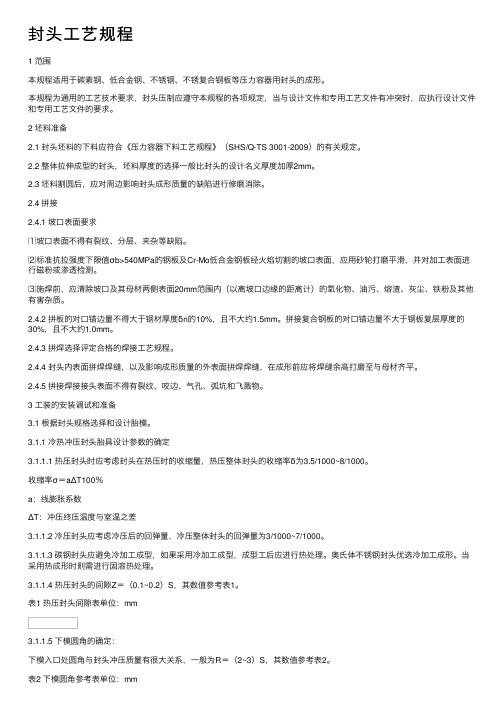
封头⼯艺规程1 范围本规程适⽤于碳素钢、低合⾦钢、不锈钢、不锈复合钢板等压⼒容器⽤封头的成形。
本规程为通⽤的⼯艺技术要求,封头压制应遵守本规程的各项规定,当与设计⽂件和专⽤⼯艺⽂件有冲突时,应执⾏设计⽂件和专⽤⼯艺⽂件的要求。
2 坯料准备2.1 封头坯料的下料应符合《压⼒容器下料⼯艺规程》(SHS/Q-TS 3001-2009)的有关规定。
2.2 整体拉伸成型的封头,坯料厚度的选择⼀般⽐封头的设计名义厚度加厚2mm。
2.3 坯料割圆后,应对周边影响封头成形质量的缺陷进⾏修磨消除。
2.4 拼接2.4.1 坡⼝表⾯要求⑴坡⼝表⾯不得有裂纹、分层、夹杂等缺陷。
⑵标准抗拉强度下限值σb>540MPa的钢板及Cr-Mo低合⾦钢板经⽕焰切割的坡⼝表⾯,应⽤砂轮打磨平滑,并对加⼯表⾯进⾏磁粉或渗透检测。
⑶施焊前,应清除坡⼝及其母材两侧表⾯20mm范围内(以离坡⼝边缘的距离计)的氧化物、油污、熔渣、灰尘、铁粉及其他有害杂质。
2.4.2 拼板的对⼝错边量不得⼤于钢材厚度δn的10%,且不⼤约1.5mm。
拼接复合钢板的对⼝错边量不⼤于钢板复层厚度的30%,且不⼤约1.0mm。
2.4.3 拼焊选择评定合格的焊接⼯艺规程。
2.4.4 封头内表⾯拼焊焊缝,以及影响成形质量的外表⾯拼焊焊缝,在成形前应将焊缝余⾼打磨⾄与母材齐平。
2.4.5 拼接焊接接头表⾯不得有裂纹、咬边、⽓孔、弧坑和飞溅物。
3 ⼯装的安装调试和准备3.1 根据封头规格选择和设计胎模。
3.1.1 冷热冲压封头胎具设计参数的确定3.1.1.1 热压封头时应考虑封头在热压时的收缩量,热压整体封头的收缩率δ为3.5/1000~8/1000。
收缩率σ=aΔT100%a:线膨胀系数ΔT:冲压终压温度与室温之差3.1.1.2 冷压封头应考虑冷压后的回弹量,冷压整体封头的回弹量为3/1000~7/1000。
3.1.1.3 碳钢封头应避免冷加⼯成型,如果采⽤冷加⼯成型,成型⼯后应进⾏热处理。
超级双相不锈钢S32750_压力容器封头成形工艺
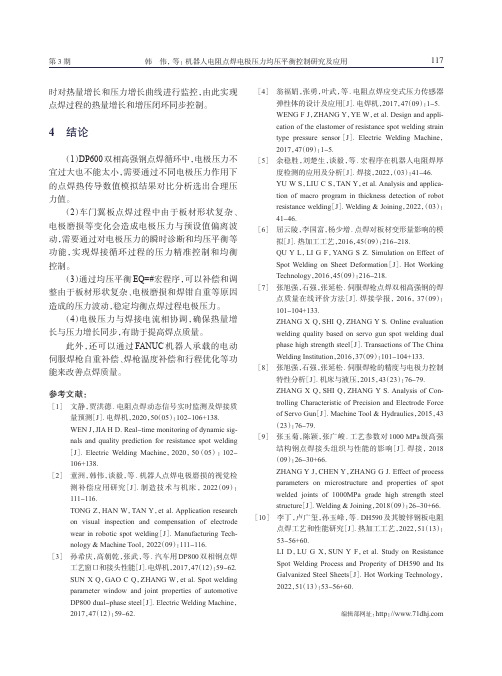
第3期韩伟,等:机器人电阻点焊电极压力均压平衡控制研究及应用时对热量增长和压力增长曲线进行监控,由此实现点焊过程的热量增长和增压闭环同步控制。
4 结论(1)DP600双相高强钢点焊循环中,电极压力不宜过大也不能太小,需要通过不同电极压力作用下的点焊热传导数值模拟结果对比分析选出合理压力值。
(2)车门翼板点焊过程中由于板材形状复杂、电极磨损等变化会造成电极压力与预设值偏离波动,需要通过对电极压力的瞬时诊断和均压平衡等功能,实现焊接循环过程的压力精准控制和均衡控制。
(3)通过均压平衡EQ=#宏程序,可以补偿和调整由于板材形状复杂、电极磨损和焊钳自重等原因造成的压力波动,稳定均衡点焊过程电极压力。
(4)电极压力与焊接电流相协调,确保热量增长与压力增长同步,有助于提高焊点质量。
此外,还可以通过FANUC机器人承载的电动伺服焊枪自重补偿、焊枪温度补偿和行程优化等功能来改善点焊质量。
参考文献:[1] 文静,贾洪德. 电阻点焊动态信号实时监测及焊接质量预测[J]. 电焊机,2020,50(05):102-106+138.WEN J,JIA H D. Real-time monitoring of dynamic sig‐nals and quality prediction for resistance spot welding[J]. Electric Welding Machine,2020,50(05):102-106+138.[2] 童洲,韩伟,谈毅,等. 机器人点焊电极磨损的视觉检测补偿应用研究[J]. 制造技术与机床, 2022(09):111-116.TONG Z,HAN W,TAN Y,et al. Application researchon visual inspection and compensation of electrodewear in robotic spot welding[J]. Manufacturing Tech‐nology & Machine Tool, 2022(09):111-116.[3] 孙希庆,高朝乾,张武,等. 汽车用DP800双相钢点焊工艺窗口和接头性能[J].电焊机,2017,47(12):59-62.SUN X Q,GAO C Q,ZHANG W,et al. Spot weldingparameter window and joint properties of automotiveDP800 dual-phase steel[J]. Electric Welding Machine,2017,47(12):59-62.[4] 翁福娟,张勇,叶武,等. 电阻点焊应变式压力传感器弹性体的设计及应用[J]. 电焊机,2017,47(09):1-5.WENG F J,ZHANG Y,YE W,et al. Design and appli‐cation of the elastomer of resistance spot welding straintype pressure sensor[J]. Electric Welding Machine,2017,47(09):1-5.[5] 余稳胜,刘楚生,谈毅,等. 宏程序在机器人电阻焊厚度检测的应用及分析[J]. 焊接,2022,(03):41-46.YU W S,LIU C S,TAN Y,et al. Analysis and applica‐tion of macro program in thickness detection of robotresistance welding[J]. Welding & Joining,2022,(03):41-46.[6] 屈云陵,李国富,杨少增. 点焊对板材变形量影响的模拟[J]. 热加工工艺,2016,45(09):216-218.QU Y L,LI G F,YANG S Z. Simulation on Effect ofSpot Welding on Sheet Deformation[J]. Hot WorkingTechnology,2016,45(09):216-218.[7] 张旭强,石强,张延松. 伺服焊枪点焊双相高强钢的焊点质量在线评价方法[J]. 焊接学报, 2016, 37(09):101-104+133.ZHANG X Q,SHI Q,ZHANG Y S. Online evaluationwelding quality based on servo gun spot welding dualphase high strength steel[J]. Transactions of The ChinaWelding Institution,2016,37(09):101-104+133.[8] 张旭强,石强,张延松. 伺服焊枪的精度与电极力控制特性分析[J]. 机床与液压,2015,43(23):76-79.ZHANG X Q,SHI Q,ZHANG Y S. Analysis of Con‐trolling Characteristic of Precision and Electrode Forceof Servo Gun[J]. Machine Tool & Hydraulics,2015,43(23):76-79.[9] 张玉菊,陈颖,张广峻. 工艺参数对1000 MPa级高强结构钢点焊接头组织与性能的影响[J]. 焊接, 2018(09):26-30+66.ZHANG Y J,CHEN Y,ZHANG G J. Effect of processparameters on microstructure and properties of spotwelded joints of 1000MPa grade high strength steelstructure[J]. Welding & Joining,2018(09):26-30+66.[10] 李丁,卢广玺,孙玉峰,等. DH590及其镀锌钢板电阻点焊工艺和性能研究[J]. 热加工工艺,2022,51(13):53-56+60.LI D,LU G X,SUN Y F,et al. Study on ResistanceSpot Welding Process and Properity of DH590 and ItsGalvanized Steel Sheets[J]. Hot Working Technology,2022,51(13):53-56+60.编辑部网址:http://117Electric Welding MachineVol.54 No.3Mar. 2024第 54 卷 第 3 期2024 年3 月超级双相不锈钢S32750压力容器封头成形工艺卜繁煜, 刘宇飞, 刘玉婷, 黄思琪, 刘成洋大连金重机器集团有限公司,辽宁 大连 116100摘 要:系统探讨了S32750超级双相不锈钢压力容器封头的成形工艺。
压力容器用封头

压力容器用封头Formed heads for pressure vessels(送审稿)200X-XX-XX发布200X-XX-XX实施目次前言………………………………………………………………………………………………1 范围………………………………………………………………………………………………2 规范性引用文件…………………………………………………………………………………3 符号………………………………………………………………………………………………4 型式参数及标记……………………………………………………………………………………5 材料…………………………………………………………………………………………………6 制造、检验与验收………………………………………………………………………………7 出厂质量证明文件…………………………………………………………………………………8 油漆、包装与运输…………………………………………………………………………………附录A(资料性附录)HHA球形封头型式参数……………………………………………………附录B(资料性附录)EHA椭圆形封头型式参数…………………………………………………附录C(资料性附录)EHB椭圆形封头型式参数…………………………………………………附录D(资料性附录)THA碟形封头型式参数…………………………………………………附录E(资料性附录)THB碟形封头型式参数…………………………………………………附录F(资料性附录)SDH球冠形封头型式参数…………………………………………………附录G(资料性附录)常见材料密度表……………………………………………………………附录H(资料性附录)封头内表面积、容积、质量以及总高度(总深度)的计算公式………附录I(资料性附录)封头合格证及质量证明书………………………………………………前言本标准自颁布之日起代替JB/T 4746-2002“钢制压力容器用封头”。
压力容器制造通用工艺规程(DOC)
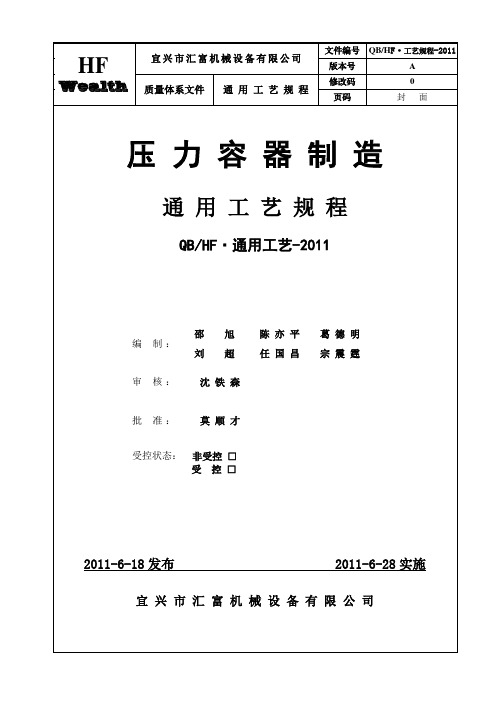
1300
8.7
17.5
1600
9
20
1800
10.2
22.5
2000
12.5
25
2200
12.7
27.5
40
-2.0~4.0
2400
15
30
2600
16.2
32.5
2800
17.5
35
3000
18.7
37.5
3200
20
40
3400
21.2
42.5
3600
22.5
45
3800
2ቤተ መጻሕፍቲ ባይዱ.7
47.5
4000
(1)封头坯料宜采用整板,如需拼接,宜取同一炉批号板料,并尽可能选用同一张板料。
(2)板料拼接时,其最小一条焊接接头距中心距离a≤0、4Di,且最小板宽b不小于300mm。
3.2椭圆型封头下料毛体板计算公式:
DM=1、2Dg+2h+s(碳钢)
DM=1、2Dg+2h+s+50(不锈钢)
注:具体尺寸以封头压制方提供的下料尺寸为准。
式中:DM—毛体板直径Dg—封头内径S—封头毛体板厚度
h—封头直边高度
3.3成型后的封头最小厚度&不小于该部位的名义厚度-钢板负偏差。当钢板负偏差≤0.25m时可忽略不计。钢板负偏差均为0.25mm。
一般钢材标准规定的负偏差如表
表2-1
公称
直径
外圆周长允差△L
最大间隙C
直边高度
△允差h2
总高度
△允差h1
直边高度
倾斜度
最小厚度
成形后δ
直边纵向
封头制造工艺规程
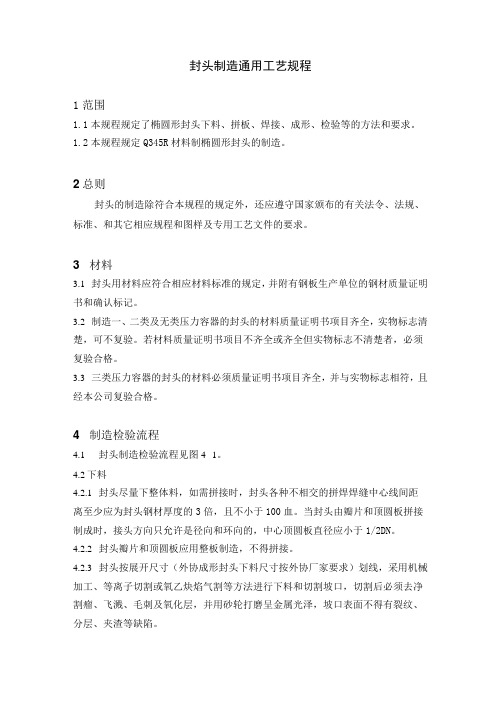
封头制造通用工艺规程1范围1.1本规程规定了椭圆形封头下料、拼板、焊接、成形、检验等的方法和要求。
1.2本规程规定Q345R材料制椭圆形封头的制造。
2总则封头的制造除符合本规程的规定外,还应遵守国家颁布的有关法令、法规、标准、和其它相应规程和图样及专用工艺文件的要求。
3 材料3.1封头用材料应符合相应材料标准的规定,并附有钢板生产单位的钢材质量证明书和确认标记。
3.2制造一、二类及无类压力容器的封头的材料质量证明书项目齐全,实物标志清楚,可不复验。
若材料质量证明书项目不齐全或齐全但实物标志不清楚者,必须复验合格。
3.3三类压力容器的封头的材料必须质量证明书项目齐全,并与实物标志相符,且经本公司复验合格。
4 制造检验流程4.1封头制造检验流程见图4--1。
4.2下料4.2.1封头尽量下整体料,如需拼接时,封头各种不相交的拼焊焊缝中心线间距离至少应为封头钢材厚度的3倍,且不小于100血。
当封头由瓣片和顶圆板拼接制成时,接头方向只允许是径向和环向的,中心顶圆板直径应小于1/2DN。
4.2.2封头瓣片和顶圆板应用整板制造,不得拼接。
4.2.3封头按展开尺寸(外协成形封头下料尺寸按外协厂家要求)划线,采用机械加工、等离子切割或氧乙炔焰气割等方法进行下料和切割坡口,切割后必须去净割瘤、飞溅、毛刺及氧化层,并用砂轮打磨呈金属光泽,坡口表面不得有裂纹、分层、夹渣等缺陷。
K 川Q345R 钢材经火焰气割的坡口表面,应进行磁粉或渗透检测。
图4-14.3拼接4.3.1封头拼接坡口型式及尺寸按专用焊接工艺,坡口表面应平整、光滑。
4.3.2封头拼接时,对口错边量不得大于钢板厚度的10%,且不大于1mm,复合钢板的对口错边量不得大于钢板复层厚度的30%,且不大于1mm ,棱角度应不大于O.1J+1且不大于2mm (5为名义厚度)。
n n4.3.3封头拼焊前,须将焊缝两侧各30mm 范围内的氧化物、油污、锈蚀等杂物彻底清除干净。
《压力容器下料工艺规程》2010.12
压力容器下料工艺规程1.本规程适用于压力容器筒体、封头的号料划线、切割下料、边缘加工和封头拼版等工序。
2.压力容器用料应符合《固定式压力容器安全技术检查规程》、GB150-1998和GB151-1999中有关规定,压力容器筒体及封头的下料除应符合上述规程及标准的有关规定,还应符合本工艺规程的规定。
3.严禁将未经检验合格和检验不合格的材料、有探伤要求还没有完成的材料及无材料标记或标记不清楚的材料用于下料。
4.号料前准备4.1工艺排版图必须执行GB150、GB151和《固容规》等有关规定,合理安排焊缝和开孔位置,便于组对焊接等工序要求,提高工作效率,确保产品质量。
4.2 号料者认真审查核算下料尺寸是否正确。
4.3 仔细查看压力容器主要受压元件制造工艺过程流转卡有无特殊规定;4.4 检查材料是否与图纸要求一致,材料标记是否清晰准确,代用材料的变更单是否齐全有效。
4.5详细检查排版图、零部件下料单,检查来料尺寸,合理进行安排。
注意节约用料,提高材料利用率。
4.6 根据加工工艺的需要及下料方法留出相应的加工余量和切割间隙。
4.7 坯料尺寸应考虑现有设备的加工能力及吊运能力。
4.8 在号料时应按规定做好标记移植,材料标记在零件外表面上。
5. 拼版5.1 封头坯料的拼接5.1.1封头坯料的下料尺寸应在制造工艺过程卡中加以注明,并应符合外协厂家的要求。
5.1.2封头下料的拼接应符JB/T4746-2002和GB150-1998的有关规定。
5.1.3封头坯料拼接需符合图纸要求,车间规定小于1400mm的封头不准拼接。
5.2 筒体料的拼接5.2.1筒体坯料的拼接应符合图纸和制造工艺过程卡上规定。
若图纸上及工艺过程卡无规定,应符合GB150的有关规定。
5.2.2 公称直径小于或等于900mm的筒体不准拼接焊缝。
5.2.3公称直径大于900mm,若拼接纵缝但长度等于或小于2000mm时不准拼接环缝。
5.2.4筒体的拼接长度不应小于300mm,最大长度不超过2000mm。
关于压力容器用封头成形质量及成形厚度减薄量的技术要求
关于压力容器用封头成形质量及成形厚度减薄量的技术要求从本月开始公司为进一步提高产品质量,对筒体的卷制偏差、焊接坡口加工等各方面作出了严格控制,但压力容器用封头属于外协件,其成形偏差及成形厚度减薄量直接影响到产品质量和使用安全。
因此必须进行严格控制与验收。
根据各标准和各封头厂家设备能力特作出如下规定,望各部门及外协单位严格执行。
1、封头有拼缝时,在冲压成形前,除去圆片内表面全部焊缝及外表面直边部和过渡区焊缝余高后再进行加工;在旋压成形前,则焊缝内外表面的余高都要去除。
2、公称直径D N≤1000mm的封头尽量不拼接。
3、在提料时,一般封头采用冲压成形,如采用旋压成形时应特殊提出。
4、冷成形封头的热处理:当加工度的最大纤维伸长率超过5%,同时属于5个条件任意一项时,碳素钢及低合金钢冷成形封头要做热处理。
●计算公式:最大纤维伸长率=75×δs(r+0.5δs)(%)δs:钢材厚度(mm)r:封头折边部的内半径。
● 5个条件:1)使用介质为极度或高度危害者;2)材料要求进行冲击试验者(可按ASMEVIII-1UCS-66判定);3)冷成形后钢板厚度大于15.9mm者;4)冷成形后板厚减薄率大于10%者;5)成形温度处于120-48℃范围内者。
●热处理条件:1)退火(SR)时,温度:625℃±25℃保温时间:δs≤25.4mm 60分钟其他一般按60分钟/25.4mm适用材料:碳素钢、低合金钢2)正火(N)时温度:900℃±25℃保温时间:30分钟/25.4mm,但不少于30分钟适用材料:碳素钢、低合金钢注:《容规》管辖范围内的产品按相应规定执行。
5、封头的成形加工方法有热冲压和冷冲压、冷旋压和热旋压等,不同尺寸、不同加工方法有不同的减薄量,只要提供设计厚度(δ+C2)加上封头制造厂的实际减薄量并圆整至钢板标准规格的厚度,即可避免设计、制造二次圆整(δ1+δ2)造成的浪费,从而得到安全经济合理的封头成形厚度,这也是当今国内外同行之所以采用的最小保证厚度(即δ+C2的设计厚度)的原因。
压力容器产品组装工艺规程
压力容器产品组装工艺规程(QB/SAR0303-2005)1.0总则1.1编制依据1.1.1《压力容器安全技术监察规程》;1.1.2《钢制压力容器》(GB150-1998);1.1.3《钢制卧式容器》(JB4731-2000);1.1.4《钢制塔式容器》(JB4710-2000);1.1.5《锅炉压力容器产品安全性能监督检验规则》;1.1.6本公司原有工艺方法。
1.2适用范围本规程适用于压力容器产品的壳体和其他零部件的组装过程。
1.3一般规定1.3.1产品组装前的零、部件均已完成规定的检验、试验项目并合格。
1.3.2压力容器必须按设计图纸进行加工制造,任何原因造成的需对原设计进行的变更,应取得原设计单位的认可。
1.3.3组装过程中各质量控制点必须按规定的控制类别,由相应级别的监检人员检验确认后,方可进行后续作业。
1.3.4压力容器产品质量应符合设计图纸和相关标准规定要求,须经授权的检验机构实施监检。
2.0壳体组装:2.1组对:2.1.1筒节加工完成并经检验合格后,即可进行壳体组装,组装前,应对各部件的标识和制作序号及组装中心线进行校核。
2.1.2相邻的筒节以及筒节与封头对接前,应对对接端的周长进行测量,换算成对接端的平均直径,以保证对接使的错边量均匀地分布在筒节或封头直边的全周上,避免对接端的直径差集中表现在局部圆弧上,而造成错边量超差。
2.1.3单层管钢板壳体环向对接焊缝的对口错边量b(见图2-1)应符合(表2-1)的允许值。
图2-1 图2-2表2-1 单层管钢板筒体环向对接错边允许偏差单位:mm 钢板厚度(δs) 对口错边允许偏差(b)δs≤12 ≤1/4δs12<δs≤20 ≤1/4δs20<δs≤40 ≤5.040<δs≤50 ≤1/8δsδs>50 ≤1/16δs.且不大于102.1.4复合钢板壳体的环向对接焊缝的对口错边量b(见图2-2)不得大于钢板复合层厚度5%,且不得大于2mm.2.1.5壳体组对时,要对壳体的直线度不断的进行测量和控制,以保证壳体组装完成后的直线度符合设计要求。
压力容器装配通用工艺规程
压力容器装配通用工艺规程1范围本规程规定了公司压力容器产品装配焊缝布置、装配错边量棱角度不等厚度对接、装配尺寸公差、热处理、无损检测和管箱装配的要求;本规程适用于本公司压力容器产品的装配;非压力容器产品可参照本标准执行;本规程不适用于按ASM规范制造生产的压力容器的装配;2规范性引用文件下列文件中的条款通过本标准的引用而成为本标准的条款;凡是注日期的引用文件, 其随后所有的修改单(不包括勘误的内容)或修订版均不适用于本标准,然而,鼓励根据本标准达成协议的各方研究是否可使用这些文件的最新版本;凡是不注日期的引用文件, 其最新版本适用于本标准;G150 《压力容器》GB151 《管壳式换热器》HG20584 《钢制化工容器制造技术要求》JB4730 《压力容器无损检测》JB/T4750 《制冷装置用压力容器》3总则3.1 当本标准与图纸或专用工艺的规定不一致或图纸另有规定时,应以图纸或专用工艺文件规定为准;3.2 操作工在操作前应先看图纸和专用工艺文件, 熟悉装配方法、顺序和装配要求;3.3装配时应核对装配零件的P/N号是否与BO一致;受压元件是否有材料标记;上道工序的加工是否合格;是否已经过必要的检验;3.4操作工在本工序完工后应首先自检, 合格后再转下道工序;3.5 需经相关检验人员(以下简称检验员)检验的控制点在自检合格后交相关检验员检验;停止点必须经检验员和压力容器体系相关责任人检验确认;3.6 不准强力装配;3.7 装配时使用的临时拉筋、吊耳等应采用与容器焊接性能相似的材料、焊材及焊接工艺;装配后留下的焊疤应磨平, 打磨后的厚度不应小于设计母材厚度;3.8 制造中应避免钢板表面的机械损伤;对尖锐伤痕以及不锈钢容器防腐蚀表面的局部伤痕、刻槽等缺陷应予修磨, 修磨范围的斜度至少为1:3;修磨的深度应不大于该部位钢材厚度的5%S n,且不大于2mm否则应予补焊;对于复合钢板,其修磨深度不得大于复层厚度的3%且不大于1mm否则应予补焊;钢板的补焊按Q/YWT0204的规定3.9凡被支座、腹板、垫板、补强圈等覆盖的焊缝,均应打磨至母材平齐; 3.10壳体内凡妨碍管束顺利装入或抽出的焊接接头均应打磨至与母材平齐;3.11 容器封闭前(装配封头、管板等)均应对容器内进行清洁检查, 并检查是否有工具或杂物遗留在容器内;3.12容器在生产过程中应对暂时不加工的管口进行封闭, 防止杂物进入容器内;有螺纹的接管在焊接过程中应用闷盖保护, 防止飞溅进入容器或损坏螺纹; 3.13加工过程中如发现标记会被覆盖或加工掉, 则应事先进行标记移植;4焊缝布置4.1筒节长度一般应不小于300mm相邻筒节间纵缝及筒节纵缝与封头拼缝应错开,焊缝中心错开间距(外圆弧长)应大于名义厚度S n的三倍、且不小于100mm图1);4.2设备内外装配件与壳体相焊接的焊缝,其焊缝边缘应尽量避开筒体焊缝;4.3当装配件与壳体主焊缝交叉时,应在附件上开一槽口,以使连接焊缝跨越主焊缝(图1);4.4筒体或封头上开孔,以开孔中心为圆心,1.5倍开孔直径为半径的范围内不要布置焊缝(图1)若不能避开,则在此范围内的A B类焊缝应全部进行无损检测; 4.5筒体焊缝布置时应尽量不被支座、垫板等覆盖;如被覆盖则按3.9条执行外,还应对被覆盖部分的焊缝全部进行无损检测;5装配错边量b、棱角度E、不等厚对接的要求5.1A、B类焊接接头对口错边量b按表1和图2规定;5.1.1用焊接检验尺检验,当壳体为不等厚钢板时,按薄板计算,且测量时不计入钢板的厚度差;5.1.2对于封头压制后接头部分的增厚情况,装配应以外表对齐为准,测量时不计入增厚因素5.1.3装配时先测量两零件的外周长,计算差值,确定错边量值,以便装配时保证错边量在圆周方向均匀分布;b图2:错边量示意图表1 A 、 B 类焊接接头的错边量单位:mm对口处钢材厚度S s A 类焊接接头对口错边量b B 类焊接接头对口错边量b < 12 b < 1/4 S s b < 1/4 S s >12~20 b < 3 b < 1/4 S s >20~40 b < 3 b < 5.0 >40~50b < 3b < 1/8 S s> 50b < 1/16,且w 10b < 1/8 S s,且 w 205.2B 类焊接接头在轴向形成的棱角度 E W (0.1 S n+2.0)mm 且不大于5mm 用长度不小于300mm 的直尺或样板测量(图3);图3:棱角度示意图5.3当对接壳体两侧钢板厚度不等时,当薄板厚度大于10mm 两板厚度差超过3mr 时,或当薄板 厚度大于10mm 两板厚度差大于薄板厚度的30%或超过5mr 时,均应按下图4所示的要求单面或 双面削薄厚板边缘,或按同样要求采用堆焊方法将薄板边缘焊成斜面 ;EDdL24 - |r(L1,L2) > 3( S 1—S 2)图4不等厚对接5.4最大最小直径差,壳体上同一截面上最大最小直径差应该不大于该截面内径的 1%;如果为 换热容器,则壳体上同一截面上最大最小直径差应该不大于该截面内径的 0.5 %;当被检断面 位于开孔中心一倍开孔内径范围内时,则该断面最大内径与最小内径应不大于该断面内径的1%Eb住J=2ES 2S 2”与开孔内径的2%之和;5.5当筒体由几节拼接而成时,拼接后的筒体直线度△ L W L%。
- 1、下载文档前请自行甄别文档内容的完整性,平台不提供额外的编辑、内容补充、找答案等附加服务。
- 2、"仅部分预览"的文档,不可在线预览部分如存在完整性等问题,可反馈申请退款(可完整预览的文档不适用该条件!)。
- 3、如文档侵犯您的权益,请联系客服反馈,我们会尽快为您处理(人工客服工作时间:9:00-18:30)。
压力容器封头成型工艺规程
1. 主题内容与适用范围
本规程规定了压制封头时胎具的选择、封头成形及检验等内容。
适用于碳素钢、普通低合金钢、不锈钢等材质的压力容器封头制造。
2. 引用标准
GB150-1998《钢制压力容器》
《钢制压力容器用封头》
《压力容器安全技术监察规程》
3. 胎具选择
3.1 封头尺寸应符合JB/T4746-2002《钢制压力容器用封头》的规定。
公称直径DN=400~3000的椭圆形、碟形封头为整体冲压成型;球形、锥形封头及DN>3000mm的椭圆形、碟形封头为分片压制成型。
3.2 热压封头应考虑热压后的收缩量。
整体热压封头的收缩率δ一般为δ=3.5~8%,它与钢板的材质和线膨胀系数有关,可用下式进行计算:
δ=a×△t×100%
式中:δ收缩率,mm/mm
a 线膨胀系数,10-6 mm/mm℃
△终压温度与室温之差。
℃
3.3 冷压封头应考虑冷压后的回弹量。
回弹量与钢板的材质、厚度及封头尺寸等因素有关。
冷压整体封头的回弹量同般为3/1000~7/1000。
碳钢、低合金钢封头应避免冷压成形。
如必须冷成形时,成形后应进行热处理。
3.4 热压封头与封头模具之间的间隙Z=(0.1~0.2)δn, 其数值可参考表3.4。
表3.4 单位: mm
3.5 下模圆角R的确定
下模入口处圆角与封头冲压质量关系很大,一般取R=(2~3)δn(其数值可参考表3.5)。
表3.5 单位:mm
3.6 热压椭圆形封头的压边范围:
当D i=400~1200, D w-D i=20δn时,必须压边。
当D i=1200~1900, D w-D i=19δn时,必须压边。
当D i=2000~2800, D w-D i=18δn时,必须压边。
注:D i------------封头内径,mm;
D w-----------------封头开展直径,mm;
δn-------钢板厚度,mm;
4. 封头压制
4.1 封头的下料和拼接执行《压力容器产品下料工艺规程》和其他有关标准。
4.2 封头成形前应将毛坯边缘的气割熔渣或剪切毛刺清除干净
4.3 整体压制的封头如果需要拼接,其拼接焊缝必须是全焊透结构。
冲压成型后对焊缝进行100%射线或超声检测,合格标准与容器主体A 类焊缝相同。
4.4 封头冲压前将拼接焊缝打磨至与母材表面齐平。
4.5 毛坯料进炉前必须把毛坯料上的杂物清理干净。
4.6 毛坯料在加热炉中摆放时应均匀地加放支垫。
多块毛坯料同时加热时,毛坯与毛坯之间要加放50~100mm厚的支垫,不得将毛坯料重叠,并注意防止过烧或加热不均匀现象。
4.7 加热应采用中性火焰,加热温度的控制应符合工艺要求,且加热温度要均匀,炉内温度采用热电偶来测试。
4.8 毛坯料加热温度可参照表4.8的规定。
表4.8 单位: mm
4.9 封头模具安装时应调整模具在水压机动上的中心位置以防偏心,使上胎与压力圈及下胎的间隙均匀,上胎与下胎间隙的差值应≤1mm。
4.10 封头冲压前和冲压过程中,应检查拉环和压边圈。
如发现拉毛时应及时用砂轮修磨光滑。
4.11 封头冲压前在上下模具上必须涂以润滑剂,其润滑剂的配比如下:
(1)碳钢、低合金钢:40%的石墨粉加60%的机油调制成糊状。
(2)不锈钢:55%的石墨粉加45%的机油调制成糊状。
4.12 毛坯料放在下模上后,必须迅速准确地将毛坯料摆正。
4.13 热压封头连续冲压前应及时清除模具及加热后毛坯上的氧化皮等杂物,以防损伤封头。
4.14 热压封头终压温度计应大于700℃(如有特殊要求时按专门的工艺执行)。
4.15 热压好的封头必须冷却到暗褐色(500℃左右)才能吊运走,以防产生变形。
4.16 封头压完后,进行标记移植。
4.17 分瓣压制的封头,其焊缝布置应符合GB150-1998《钢制压力容器》中的有关规定。
冲压成形的瓣片必须用立体样板进行检查,瓣片表面任意部位间隙不得大于3mm。
4.18 修整不锈钢封头时,不得用铁锤直接敲击。
应垫以平锤或垫板(允许用铜锤或木锤直接敲击)。
4.19 对于有晶间腐蚀要求的热压不锈钢封头,应进行固熔处理。
为防止热处理变形过大,对于δn≤10mm的封头,可加热到1050℃~1100℃后空冷;对于δn>10mm的封头,可加热到1050℃~1100℃后放入水中急冷或用水喷射冷却。
4.20 热压不锈钢封头经酸洗钝化处理后方能与筒体进行组焊。
4.21 压制批量较大的封头应先试冲压成形2~3个,进行全面的检验,合格后再批量进行冲压。
5、封头检验
5.1 成形后封头最小厚度不得小于其名义厚δn减去钢反厚度负偏差C1。
5.2 用弦长相当于封头内直径的间隙样板,检查封头内表面的形状公差。
如图5.2所示。
检查时应使样板垂直于待测表面,允许避开焊缝进行测量。
椭圆形、碟圆形、球罐形封头内表面的形状公差应符合以下要求:
a)样板与封头内表面间的最大间隙:外凸不得大于 1.25%D i;内
凹不得大于
0.625%D ic
b)样板轮廓曲线线性尺寸的极限偏差:按GB/T1804-2000中m
级的规定。
图5.2
5.2.1 碟形封头、折边锥形封头过渡段转角内半径不得小于表1或图样规定值。
5.2.2 椭圆形、碟形与折边锥形封头的直边部分不得存在纵向皱折。
封头切边后,用直尺测量椭圆形、碟形与折边锥形封头的直边高度,当封头公称直径DN≤2000mm时,直边高度h宜为25mm; 当封头公称直径DN>2000mm时,直边高度h宜为40mm。
直边高度公差为(-5~10)%h。
5.2.3 对于按规则设计的封头,成形封头实测的最小厚,不得小于封头名义厚度减去钢板厚度负偏差C1,但当设计图样标注了封头成形后的最小厚度,可按实测的最小厚度不小于图样标注的最小厚度验收。
对于按分析设计的封头,实测的最小厚度不得小于封头设计厚度。
5.2.4 沿封头端面圆周0°、90°、180°、270°四个方位,用超声波测厚仪、卡钳或千分卡尺,在厚度的必测部位检测成形封头的厚度。
5.3热压封头齐边后的几何尺寸公差,应符合JB/4746表2-表4的有关规定.
5.4 球形封头分辨冲压的瓣片尺寸允差按GB12337-1998《,钢制球形储罐》的规定执行。
5.5 检验材质标记、冲压开始和终了温度,进行详细记录并妥善保管。
5.6 外供封头产品的质量证明文件按《压力容器安全技术监察规程》规定的内容及格式提供。
(注:可编辑下载,若有不当之处,请指正,谢谢!)。