塑胶模具开模流程图完整版
塑胶模具组立工程图的画法2

图(十二)前模2D图
图(十三)后模2D图
图(十四)横向剖视2D图
略。
图(十五)纵向剖视2D图通过组立图可拆出零件图:
图(十五)零件2D图
d、3D模具图的绘制
此模采用PRO-E 2001版进行分模,以下图片供参考!
图(十六)模具3D分解图
3D图纸绘好,提供给CNC编程员,即可开始编制NC程式,安排锣模胚、
钢料、铜公等。
模具机加工正式展开。
八、结束语
本文为作者利用业余时间写成的,主要谈了本人从事塑胶模具行业这几年的一些经验。
塑胶模具设计涉及方方面面的知识,短短篇幅无法全部讲完,还有重要的部分如CNC编程、模具制造加工工艺等没有详细介绍。
待后续……。
塑胶模具生产过程控制程序(含流程图)

文件制修订记录1.0目的:对影响塑胶模具生产品质的各个环节进行控制,确保生产作业在规定的方法和程序在受控状态下进行。
2.0适用范围:塑胶模具的生产和管理过程的控制。
3.0相关文件3.1文件资料和记录管制程序3.2采购管理程序3.3设计开发管制程序3.4工程变更作业管理程序3.5模具易损耗件更换及研磨标准4.0职责4.1研发部:负责开立(工作执行单)及样品确认。
4.2塑模课:负责模具之设计制作、组装、维修、二、三级保养及零配件生产,管理,自制零件与委外加工零件验收及数量核对。
4.3品保课:负责模具之零件配件及委外加工零件的检验,及试模产品之检验。
4.4采购课:负责模具材料购买,及零件委外加工。
4.5射出课:负责塑胶模具试模及模具验收。
5.0作业内容5.1塑胶模具作业流程:5.2生产计划:5.2.1塑模课依据“研发部”开立的<工作执行单>作<模具开发进度表>。
5.2.2申购、领料过程控制:依据模具设计之图面填写<请购单>申购符合HSF要求之材料,经主管核准后,交至采购办理。
5.3模具生产作业过程的控制:5.3.1生产工艺制程的控制:由模具主管负责其生产流程,各工序技术员依据图面进行作业,当相关资料需更改时,依据<<工程变更作业管理程序>>之相关设计变更进行更改。
5.3.2品质控制:各工序按<模具课制令单>生产完成后,交模具品管进行检验及HSF符合性的测试,并把所测量尺寸及HSF测试记录于<模(治)具检验记录表>及登录于<模具零件加工统计表>,判定允收后,方可交由下一道工序生产◦如判定不符合要求则退回生产单位(含分包商),并开立<模(治)具异常不良处理单>,作相关处理。
5.3.3设备品质及符合HSF的控制:设备品质\符合HSF的控制是依据<仪器、设备每日保养记录表>以及定期清洗相应设备执行。
图解说明塑胶模具的结构组成完整版

图解说明塑胶模具的结构组成HEN system office room 【HEN16H-HENS2AHENS8Q8-HENH1688】模具采购必备基础知识之二:塑胶模具的结构组成图解说明:模具注塑成型是批量生产某些形状复杂部件时用到的一种加工方法。
具体原理指:将受热融化的塑胶原材料由注塑机螺杆推进高压射入塑胶模具的模腔,经冷却固化后,得到塑胶成形产品。
塑胶模具由动模和定模两部分组成,动模安装在注射成型机的移动模板上,定模安装在注射成型机的固定模板上。
在注射成型时动模与定模闭合构成浇注系统和型腔,开模时动模和定模分离以便取出塑料制品。
塑胶模具的结构虽然由于塑胶品种和性能、塑胶制品的形状和结构以及注射机的类型等不同而可能千变万化,但是基本结构是一致的。
一、塑胶模具结构按功能分,主要由:浇注系统、调温系统、成型零件系统、排气系统、导向系统、顶出系统等组成。
其中浇注系统和成型零件是与塑料直接接触部分,并随塑料和制品而变化,是塑模中最复杂,变化最大,要求加工光洁度和精度最高的部分。
1.浇注系统:是指塑料从射嘴进入型腔前的流道部分,包括主流道、冷料穴、分流道和浇口等。
2.成型零件系统:是指构成制品形状的各种零件组合,包括动模、定模和型腔(凹模)、型芯(凸模)、成型杆等组成。
型芯形成制品的内表面,型腔(凹模)形成制品的外表面形状。
合模后型芯和型腔便构成了模具的型腔。
按工艺和制造要求,有时型芯和凹模由若干拼块组合而成,有时做成整体,仅在易损坏、难加工的部位采用镶件。
3.调温系统:为了满足注射工艺对模具温度的要求,需要有调温系统对模具的温度进行调节。
对于热塑性塑料用注塑模,主要是设计冷却系统使模具冷却(也可对模具进行加热)。
模具冷却的常用办法是在模具内开设冷却水通道,利用循环流动的冷却水带走模具的热量;模具的加热除可利用冷却水通热水或热油外,还可在模具内部和周围安装电加热元件。
4.排气系统:是为了将注射成型过程中型腔内的空气及塑胶融化所产生的气体排除到模具外而设立,排气不畅时制品表面会形成气痕(气纹)、烧焦等不良;塑胶模具的排气系统通常是在模具中开设的一种槽形出气口,用以排出原有型腔空气的及熔料带入的气体。
塑料模具操作方法
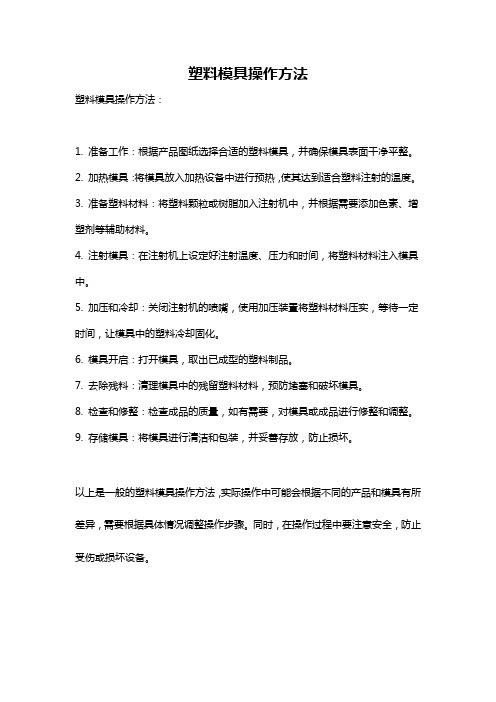
塑料模具操作方法
塑料模具操作方法:
1. 准备工作:根据产品图纸选择合适的塑料模具,并确保模具表面干净平整。
2. 加热模具:将模具放入加热设备中进行预热,使其达到适合塑料注射的温度。
3. 准备塑料材料:将塑料颗粒或树脂加入注射机中,并根据需要添加色素、增塑剂等辅助材料。
4. 注射模具:在注射机上设定好注射温度、压力和时间,将塑料材料注入模具中。
5. 加压和冷却:关闭注射机的喷嘴,使用加压装置将塑料材料压实,等待一定时间,让模具中的塑料冷却固化。
6. 模具开启:打开模具,取出已成型的塑料制品。
7. 去除残料:清理模具中的残留塑料材料,预防堵塞和破坏模具。
8. 检查和修整:检查成品的质量,如有需要,对模具或成品进行修整和调整。
9. 存储模具:将模具进行清洁和包装,并妥善存放,防止损坏。
以上是一般的塑料模具操作方法,实际操作中可能会根据不同的产品和模具有所差异,需要根据具体情况调整操作步骤。
同时,在操作过程中要注意安全,防止受伤或损坏设备。
塑胶模具排组立图步骤及注意事项_内部资料

2D排組立步驟及注意事項排組立圖的步驟:1. 把產品的3D圖檔轉到2D圖檔上,需將倒勾或有機構處做剖面,要注意比例問題。
(1:1比例)2. 轉到2D圖檔上的產品圖要加縮水和鏡像。
注意:完成以上兩步驟后必須檢查,可以測量產品在加縮水前后的同一地方,來檢查縮水加的是否正確。
3. 排組立前要定成品基准線。
即把產品上boss或大平面等易找到的特征定X,Y,Z三軸,特征的尋找需盡量接近于成品中心,若是兩上下蓋相配合,基准則盡量為同一點。
成品基准線相對模具中心要為整數。
4. 依照成品基准線把模仁排出來。
步驟輿表示重點:A 刪除成品上的虛線。
B 如側視圖為剖面要將側視圖的實線改為虛線,僅留剖面處為實線。
C 要把成品的分型面表示出來,重點表示主分型面,斜銷,滑塊處分型面。
分型面上的插破,靠破也需表示。
D 還需把模仁拆入子處表示清楚,正視圖入子遍界用黃色線表示,且入子沉頭也需表示。
入子輿入子間要避免有薄鐵現象,一般不可小于1mm。
(模仁需拆入子部位一般為整體不好加工處或肋較深處及一些boss處)。
5. 排頂針,水路,最后排模仁螺絲。
要注意三者不能干涉,三者間距不小于3mm,拆入子時也要一同考慮.以下為頂針,水路,螺絲的排列重點:a 頂針要排在成品不易脫模處,如成品的邊緣,肋,及塑膠較深處。
頂針的尺寸要盡量選擇大的,以增加強度。
頂針輿成品形狀間距應不小于0.6-1mm,以避免薄鐵現象。
b排水路的宗旨是可以盡快的帶走模溫,以達到冷卻效果。
直通的水路效果最好。
C模仁螺絲一般排四個,位置要盡量對稱。
6. 排模仁要注意強度問題,產品邊緣距模仁邊緣應不小于20mm,模仁邊緣距模架邊緣的距離要按模具大小而定,大模具要50mm以上,小模具為30-50mm(天地側350mm以下視為小模具).有特殊要求的要個別對待。
模板厚度的選擇如圖1-1母模板公模板a一般為20-30mm b=2c+20mm1- 1畫模架時的注意事項:A. KO孔一般放在模具的正中,當有多個時,它們之間的間距一般為100mm。
模具开发流程图
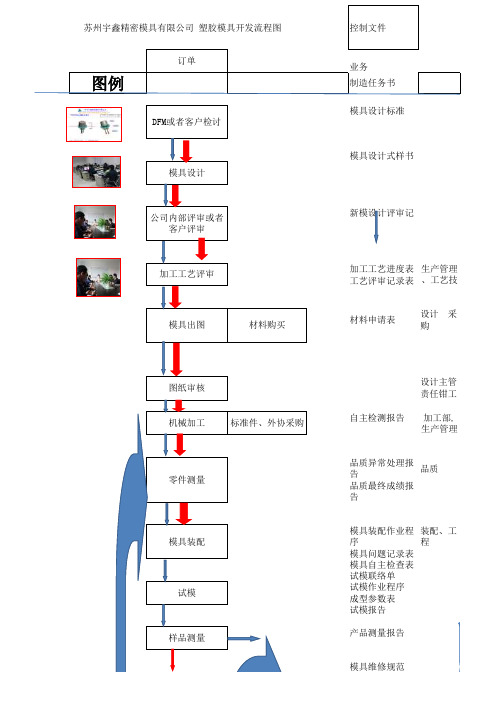
产品测量报告
加工、生 产管理
模具出货检测表 送货单
Ⅰ
ⅠⅡⅢⅣ ⅤⅥⅦ 采购
Ⅱ
Ⅲ
苏州宇鑫精密模具有限公司 塑胶模具开发流具设计
公司内部评审或者 客户评审
加工工艺评审
模具出图
材料购买
控制文件
业务 制造任务书 模具设计标准
模具设计式样书
新模设计评审记
加工工艺进度表 生产管理 工艺评审记录表 、工艺技
材料申请表
设计 采 购
图纸审核
机械加工
标准件、外协采购
零件测量
模具装配 试模
样品测量
设计主管 责任钳工
自主检测报告 加工部, 生产管理
品质异常处理报 告
品质
品质最终成绩报
告
模具装配作业程 装配、工
序
程
模具问题记录表
模具自主检查表
试模联络单
试模作业程序
成型参数表
试模报告
产品测量报告
模具维修规范
模具维修检讨 样品送客户确认
模具出货
试模、装 模具维修报告 配、工程
注塑模具开发流程及加工工艺ppt课件

六、改模及修模
模具在试模后,根据试模的情况做出相应的更改,另外在工程师确认胶件后,胶件的结构也要做 相应的更改。由于模具已经制作完成,故所有的更改都比较麻烦,甚至有时比重做更困难,必须根据具 体情况,找到最好的更改办法。对于结构设计来说,结构的更改必须尽量了解模具情况,是否碰运水、 顶针,怎样更改最容易等,可在结合相关信息的情况下再作出相关的改模,必要时可咨询模具组同事。 冷却系统的加工: 冷却系统的加工(钻运水),产品一般要求前模运水在发第一次改模资料时需加工,后模运水在发第二次 改模资料后需加工,但对于运水开启与否对生产影响较大的情况,如PC料的生产(需打热油成型情况), 尽量在第一次试模前开启。 故结构设计图纸阶段考虑好各种情况,尽量减少改模的工作量,使得运水的开启能正常运行,生产尺寸 尽快确定。 产品结构的改模: 加筋条,加柱子,结构大改重做镶件。 原生筋条加减胶,柱子移位,螺丝柱加大减小,高度加高降低,批锋修整等等。
能加工
能保证光洁度,平 面度,圆度要求
磁盘,批士
铣床,车床 钻孔,CNC,铣床
A5
ZN01
钻孔
台式铣床,立 式钻床
钻床
0.05
0.02
钻攻螺丝孔,穿丝孔,钻铰 各类针孔,司筒孔,钻铰入 水孔,精镗直身唧嘴孔或
开粗唧嘴孔
模具长度不能超过1米, 钻孔深度不能超过150, 模具材料是非淬火料
塑胶模具开模的相关介绍
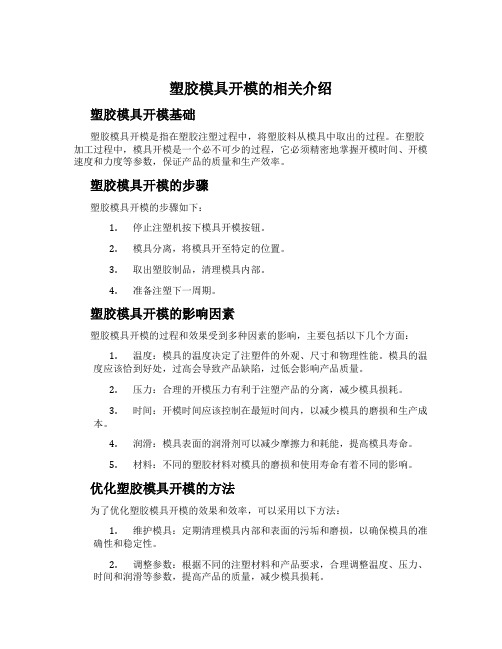
塑胶模具开模的相关介绍塑胶模具开模基础塑胶模具开模是指在塑胶注塑过程中,将塑胶料从模具中取出的过程。
在塑胶加工过程中,模具开模是一个必不可少的过程,它必须精密地掌握开模时间、开模速度和力度等参数,保证产品的质量和生产效率。
塑胶模具开模的步骤塑胶模具开模的步骤如下:1.停止注塑机按下模具开模按钮。
2.模具分离,将模具开至特定的位置。
3.取出塑胶制品,清理模具内部。
4.准备注塑下一周期。
塑胶模具开模的影响因素塑胶模具开模的过程和效果受到多种因素的影响,主要包括以下几个方面:1.温度:模具的温度决定了注塑件的外观、尺寸和物理性能。
模具的温度应该恰到好处,过高会导致产品缺陷,过低会影响产品质量。
2.压力:合理的开模压力有利于注塑产品的分离,减少模具损耗。
3.时间:开模时间应该控制在最短时间内,以减少模具的磨损和生产成本。
4.润滑:模具表面的润滑剂可以减少摩擦力和耗能,提高模具寿命。
5.材料:不同的塑胶材料对模具的磨损和使用寿命有着不同的影响。
优化塑胶模具开模的方法为了优化塑胶模具开模的效果和效率,可以采用以下方法:1.维护模具:定期清理模具内部和表面的污垢和磨损,以确保模具的准确性和稳定性。
2.调整参数:根据不同的注塑材料和产品要求,合理调整温度、压力、时间和润滑等参数,提高产品的质量,减少模具损耗。
3.采用高品质材料:选择质量优良的塑胶材料和模具材料,可以提高产品性能和模具寿命。
4.操作规范:培训操作人员,确保开模过程严格按照规范进行,以避免人为失误导致的损失。
结论塑胶模具开模是注塑过程中最为重要的步骤之一,它关系到产品的质量和生产效率。
优化塑胶模具开模的过程可以大幅提高产品的质量和生产效率,减少工厂的成本和模具的损耗,同时保障操作人员的人身安全。