开式液压系统与闭式液压系统区别及优缺点(转载)
开式液压泵与闭式液压泵

液压系统根据系统中液体的循环方式,一般可分为闭式液压系统和开式液压系统两种类型。
闭式液压系统是指系统中的液体在循环时是闭合的,即液体从液压泵进入液压缸(或液压马达)后,再通过液压阀回到液压泵,形成一个闭合的液路。
在闭式液压系统中,系统的压力和流量可以通过液压泵和液压阀来控制和调节,系统的动作比较平稳,具有较高的控制精度和能量利用率。
闭式液压系统的缺点是系统的设计和维护较为复杂,成本也比开式液压系统高。
开式液压系统是指系统中的液体循环是开放的,即系统中的液体从液压泵进入液压缸(或液压马达)后,流回油箱而不是回到液压泵。
在开式液压系统中,系统的压力和流量受到液压泵的输出和负载的影响,控制精度和能量利用率较低,但系统的设计和维护较为简单,成本较低,因此在一些较为简单的机械设备中,开式液压系统比较常见。
总的来说,闭式液压系统具有高效、精确的控制特性,适用于高性能、高精度的液压控制系统;开式液压系统则更为简单、经济,适用于一些不要求过高控制精度的场合。
开中心和闭中心液压系统工作特点和优缺点分析
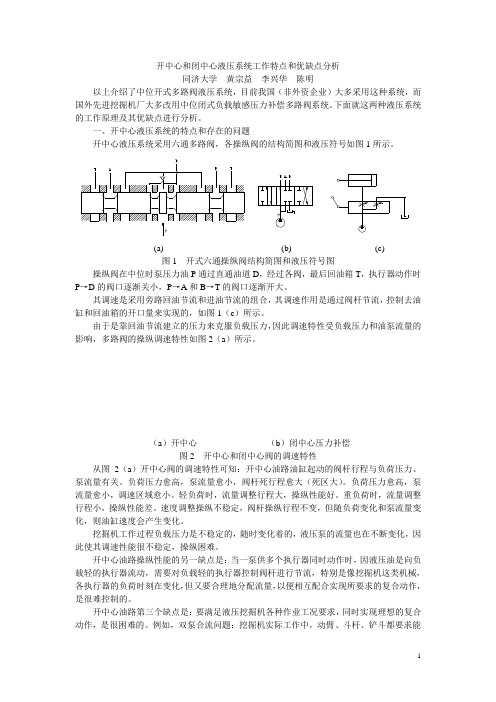
开中心和闭中心液压系统工作特点和优缺点分析同济大学黄宗益李兴华陈明以上介绍了中位开式多路阀液压系统,目前我国(非外资企业)大多采用这种系统,而国外先进挖掘机厂大多改用中位闭式负载敏感压力补偿多路阀系统。
下面就这两种液压系统操纵阀在中位时泵压力油P通过直通油道D,经过各阀,最后回油箱T,执行器动作时P→D的阀口逐渐关小,P→A和B→T的阀口逐渐开大。
其调速是采用旁路回油节流和进油节流的组合,其调速作用是通过阀杆节流,控制去油缸和回油箱的开口量来实现的,如图1(c)所示。
由于是靠回油节流建立的压力来克服负载压力,因此调速特性受负载压力和油泵流量的影响,多路阀的操纵调速特性如图2(a)所示。
(a)开中心(b)闭中心压力补偿图2 开中心和闭中心阀的调速特性从图2(a)开中心阀的调速特性可知:开中心油路油缸起动的阀杆行程与负荷压力、泵流量有关。
负荷压力愈高,泵流量愈小,阀杆死行程愈大(死区大)。
负荷压力愈高,泵流量愈小,调速区域愈小。
轻负荷时,流量调整行程大,操纵性能好。
重负荷时,流量调整行程小,操纵性能差。
速度调整操纵不稳定,阀杆操纵行程不变,但随负荷变化和泵流量变化,则油缸速度会产生变化。
挖掘机工作过程负载压力是不稳定的,随时变化着的,液压泵的流量也在不断变化,因此使其调速性能很不稳定,操纵困难。
开中心油路操纵性能的另一缺点是:当一泵供多个执行器同时动作时,因液压油是向负载轻的执行器流动,需要对负载轻的执行器控制阀杆进行节流,特别是像挖掘机这类机械,各执行器的负荷时刻在变化,但又要合理地分配流量,以便相互配合实现所要求的复合动作,是很难控制的。
开中心油路第三个缺点是:要满足液压挖掘机各种作业工况要求,同时实现理想的复合动作,是很困难的。
例如,双泵合流问题:挖掘机实际工作中,动臂、斗杆、铲斗都要求能合流,但有时却不要求合流,但对开中心油路来说,要实现有时合流,有时不合流是很困难的。
各种作业工况复合动作问题:例如:掘削装载工况,平整地面工况,沟槽侧边掘削工况等,如何向各执行器供油,向那个执行器优先供油,如何按操作者的愿望实现理想的配油关系也是很困难的。
浅谈挖掘机液压系统

浅谈挖掘机液压系统挖掘机液压系统挖掘机,又称挖掘机械,是用铲斗挖掘高于或低于承机面的物料,并装入运输车或卸至堆料场的土方机械。
挖掘机的液压系统形式和种类很多,我们可以从不同的角度进行分类,那么都可以分为哪几类呢?挖掘机液压系统分类l 按油液的循环形式可分为开式系统和闭式系统;l 从多路阀的形式可分开中心系统和闭中心系统;l 从泵的形式来看有定量泵系统和变量泵系统。
系统类型存在的不同优劣油液的循环形式开式系统是指液压泵从油箱吸油,油经各种控制阀后,驱动液压执行元件,回油再经过换向阀回油箱。
●优点:1) 液压系统结构较为简单;2) 可以发挥油箱的散热、沉淀杂质作用。
●缺点:1) 油液常与空气接触,使空气易于渗入系统,导致机构运动不平稳;2) 吸油管路管径大而短;3) 转速受吸油压力限制;4) 方向阀通径的大小由系统流量决定;5) 过滤器/冷却器的尺寸大小由系统流量决定(对于较大功率的系统采用单独旁路节流过滤/冷却的形式);6) 系统油箱大;7) 泵的安装位置需要考虑其对吸油压力的影响;8) 负载的平衡靠回油路上的背压或平衡阀来实现。
闭式系统是指液压泵的进油管直接与执行元件的回油管相连,工作液体在系统的管路中进行封闭循环。
●优点:1) 结构紧凑,油箱小;2) 油液与空气接触机会少,空气不易渗入系统,传动较平稳;3) 可采用高转速泵,故可相对减小泵体积;4) 没有控制阀,由泵确定流量和流向;5) 没有制动阀;6) 工作机构的变速和换向靠调节泵或马达的变量机构实现,避免了开式系统换向过程中所出现的液压冲击和能量损失。
●缺点:1) 较开式系统复杂,因无油箱,油液的散热和过滤条件较差;2) 为补偿系统中的泄漏,通常需要一个小流量的补油泵和油箱;3) 只能同时实现与安装油泵数量一样多的动作;4) 空行程速度只能通过使用较大排量的油泵或变量马达来提高。
多路阀的形式开中心系统是指当换向阀阀杆在中位时,液压泵排出的液压油通过换向阀的中位油道直接流回油箱。
开式液压系统和闭式液压系统各有什么特点

开式液压系统的特点(1)一般采用双泵或三本供油,先导油由单独的先导泵提供。
有些液压执行元件所需功率大需要合流供油,合流有两种方式:①阀内合流。
一般有双泵合流供给一个阀杆,在由该阀一般杆控制供油给所需合流的液压执行元件。
该合流方式的阀杆的孔径设计需要考虑多泵供油所虚的流通面积。
②阀外合流。
双泵分别通过各自阀杆,通过两阀泛联动操纵,在阀杆外合流供油给所需合流的液压执行元件。
虽然操纵结构相对复杂、体积较大,但由于流经阀杆的饿是单泵流量,阀杆孔径相对较小,而且有可能与其他阀杆通用。
(2)多路阀常进行分块且分泵供油,每一阀组根据实际需要可利用直通供油道和并联供油道两种油道。
前者可实现优先供油,既上游阀杆动作时,压力油就供给该阀杆操纵的液压元件,而下游阀杆操纵的液压元件就不能动作。
后者可实现并供油。
(3)为满足多种作业工况及复合动作要求,一般采用简单的通断型二位二痛阀和插装阀,把油从某一油路直接引到另一油路,并往往采用单向阀防止油回流,构成单向通道。
通断阀操纵有以下3种方式:①采用先导操纵油联动操纵,先导操纵油在控制操纵阀杆移动的同时,联动操纵通断阀。
②采用操纵阀中增加一条油道作为控制通断阀的油道,这样在操纵操纵阀的同时,也操纵了通断阀的开闭。
开式油路的另一缺点是:当一个泵供多个执行器同时动作时,因液压油首先向负载轻的执行器流动,导致高负载的执行器动作困难,因此,需要对负载轻的执行器控制阀杆进行节流。
闭式液压系统具有以下优点:(1)目前闭式系统变量泵均为集成式结构,补油泵及补油、溢流、控制等功能阀组集成于液压泵上,使管路连接变得简单,不仅缩小了安装空间,而且减少了由管路连接造成的泄漏和管道振动,提高了系统的可靠性,简化了操作过程。
(2)补油系统不仅能在主泵的排量发生变化时保证容积式传动的响应,提高系统的动作频率,还能增加主泵进油口处压力,防止大流量时产生气蚀,可有效提高泵的转速和防止泵吸空,提高工作寿命;补油系统中装有过滤器,提高传动装置的可靠性和使用寿命;另外,补油泵还能方便的为一些低压辅助机构提供动力。
开式压力机和闭式压力机的异同点
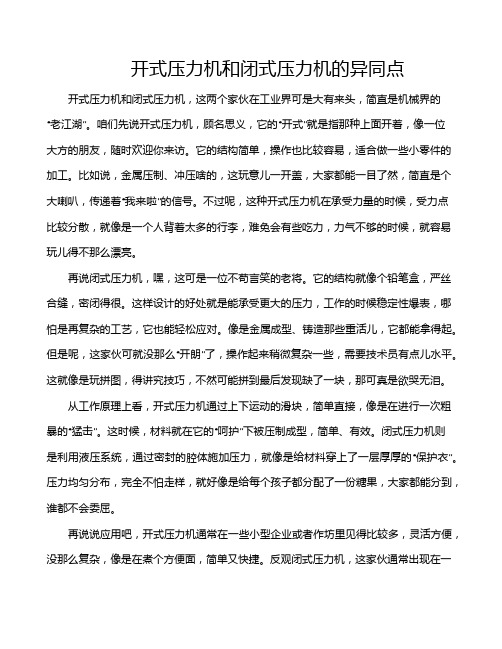
开式压力机和闭式压力机的异同点开式压力机和闭式压力机,这两个家伙在工业界可是大有来头,简直是机械界的“老江湖”。
咱们先说开式压力机,顾名思义,它的“开式”就是指那种上面开着,像一位大方的朋友,随时欢迎你来访。
它的结构简单,操作也比较容易,适合做一些小零件的加工。
比如说,金属压制、冲压啥的,这玩意儿一开盖,大家都能一目了然,简直是个大喇叭,传递着“我来啦”的信号。
不过呢,这种开式压力机在承受力量的时候,受力点比较分散,就像是一个人背着太多的行李,难免会有些吃力,力气不够的时候,就容易玩儿得不那么漂亮。
再说闭式压力机,嘿,这可是一位不苟言笑的老将。
它的结构就像个铅笔盒,严丝合缝,密闭得很。
这样设计的好处就是能承受更大的压力,工作的时候稳定性爆表,哪怕是再复杂的工艺,它也能轻松应对。
像是金属成型、铸造那些重活儿,它都能拿得起。
但是呢,这家伙可就没那么“开朗”了,操作起来稍微复杂一些,需要技术员有点儿水平。
这就像是玩拼图,得讲究技巧,不然可能拼到最后发现缺了一块,那可真是欲哭无泪。
从工作原理上看,开式压力机通过上下运动的滑块,简单直接,像是在进行一次粗暴的“猛击”。
这时候,材料就在它的“呵护”下被压制成型,简单、有效。
闭式压力机则是利用液压系统,通过密封的腔体施加压力,就像是给材料穿上了一层厚厚的“保护衣”。
压力均匀分布,完全不怕走样,就好像是给每个孩子都分配了一份糖果,大家都能分到,谁都不会委屈。
再说说应用吧,开式压力机通常在一些小型企业或者作坊里见得比较多,灵活方便,没那么复杂,像是在煮个方便面,简单又快捷。
反观闭式压力机,这家伙通常出现在一些大型制造企业,工业气息十足,干起活儿来就像是个身手不凡的武林高手,干脆利落。
它们的用途虽然不同,但目标一致,都是为了把材料变成想要的形状,满足生产需求。
不过,虽然它们各有千秋,开式压力机和闭式压力机也不是没得比的,彼此之间总有些小争斗。
开式压力机总是说自己灵活机动,适应性强,而闭式压力机则以稳定见长,总是低调地展示自己的强大。
开式系统与闭式系统的区别和特性

1. 开式系统与闭式系统严格来讲,开式系统与闭式系统并不以系统内水是否和空气接触区分,比如膨胀水箱定压的冷冻水系统,膨胀水箱内的水是和空气接触的,再如冷却水系统,冷却塔内的水是和空气接触的,但冷却水系统更加接近一个闭式系统,详见下文。
个人以为开式系统与闭式系统的严格区分应该以系统水泵运行过程中是否需要克服水的势能做功。
如图1,为一水池蓄冷系统简图,在利用水池冷水供冷时,水泵要克服从水池吸入点到系统最高点的水柱压力,此外还要克服左侧部分水路的管件、管路、冷水机组以及末端设备阻力。
这样泵的扬程为上述阻力与水柱压力之和。
如图2,为典型膨胀水箱定压空调冷冻水系统简图,水在膨胀水箱处是与空气接触的,对系统腐蚀是不利的。
但该系统是一个闭式系统。
因为右侧水柱压力与左侧水柱压力互相抵消,水泵运行时不需要克服水柱的势能,只要克服系统(左侧部分与右侧部分)水路的管件、管路、冷水机组以及末端设备阻力,所以楼高、楼正、楼歪影响不大。
这样泵的扬程为上述阻力之和。
如图3,为空调冷却水系统简图,如果安装系统是否与空气接触判断,这一系统应该时开式系统。
然而,右侧冷却管内的水柱静压可以和左侧部分抵消,水泵不需要克服这部分阻力。
但是从冷却塔接水盘到系统最高点这部分的高差形成的水压,需要水泵克服。
此外,冷却塔喷嘴也需要一定的水压进行喷水,所以水泵的扬程应该为系统(左侧部分与右侧部分)水路的管件、管路、冷水机组的阻力加上高差h 以及喷嘴前的必要压头之和。
图3. 接近闭式系统对开式系统,管路水力曲线如图4 中1 所示,其表达式如下:H = h + SQ2h 即为泵要求克服的系统静水压力。
对闭式系统,管路水力曲线如图4 中2 所示,其表达式如下:H = SQ2图4. 管路阻力曲线对上述开式系统和闭式系统,利用水泵变频进行节能计算时,区别很大,因为在曲线2 上各点为相似工况点,遵循水泵功率与转速3 次方成正比的关系,但是对曲线1,水泵变频调速后与1 的新交点与原来的工作点不是相似工况点,3次方关系不成立,常常见到需要商家不论系统情况上来就以三次方关系计算节能量,夸大了水泵调速的节能效果。
矿山机械典型液压系统的分类
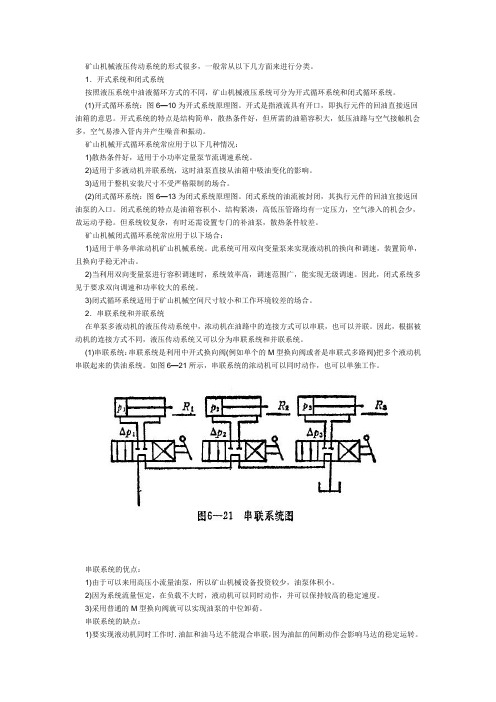
矿山机械液压传动系统的形式很多,一般常从以下几方面来进行分类。
1.开式系统和闭式系统按照液压系统中油液循环方式的不同,矿山机械液压系统可分为开式循环系统和闭式循环系统。
(1)开式循环系统:图6—10为开式系统原理图。
开式是指液流具有开口,即执行元件的回油直接返回油箱的意思。
开式系统的特点是结构简单,散热条件好,但所需的油箱容积大,低压油路与空气接触机会多,空气易渗入管内并产生噪音和振动。
矿山机械开式循环系统常应用于以下几种情况:1)散热条件好,适用于小功率定量泵节流调速系统。
2)适用于多液动机并联系统,这时油泵直接从油箱中吸油变化的影响。
3)适用于整机安装尺寸不受严格限制的场合。
(2)闭式循环系统:图6—13为闭式系统原理图。
闭式系统的油流被封闭,其执行元件的回油宜接返回油泵的入口。
闭式系统的特点是油箱容积小、结构紧凑,高低压管路均有一定压力,空气渗入的机会少,故运动乎稳。
但系统较复杂,有时还需设置专门的补油泵,散热条件较差。
矿山机械闭式循环系统常应用于以下场合:1)适用于单务单浓动机矿山机械系统。
此系统可用双向变量泵来实现液动机的换向和调速,装置简单,且换向乎稳无冲击。
2)当利用双向变量泵进行容积调速时,系统效率高,调速范围广,能实现无级调速。
因此,闭式系统多见于要求双向调速和功率较大的系统。
3)闭式循环系统适用于矿山机械空间尺寸较小和工作环境较差的场合。
2.串联系统和并联系统在单泵多液动机的液压传动系统中,浓动机在油路中的连接方式可以串联,也可以并联。
因此,根据被动机的连接方式不同,液压传动系统又可以分为串联系统和并联系统。
(1)串联系统:串联系统是利用中开式换向阀(例如单个的M型换向阀或者是串联式多路阀)把多个液动机串联起来的供油系统。
如图6—21所示,串联系统的浓动机可以同时动作,也可以单独工作。
串联系统的优点:1)由于可以来用高压小流量油泵,所以矿山机械设备投资较少,油泵体积小。
2)因为系统流量恒定,在负载不大时,液动机可以同时动作,并可以保持较高的稳定速度。
开中心和闭中心液压系统工作特点和优缺点分析

添加标题
闭中心液压系统:适用于需要大流 量、低压差的场合,如挖掘机、起 重机等
闭中心液压系统:适用于需要大流 量、低压差的场合,如挖掘机、起 重机等
优缺点比较
开中心液压系统:优点是结构简单,易于维护;缺点是泄漏风险高,效率较低。 闭中心液压系统:优点是泄漏风险低,效率较高;缺点是结构复杂,维护难度大。 开中心液压系统:优点是价格较低;缺点是使用寿命较短。 闭中心液压系统:优点是使用寿命较长;缺点是价格较高。
缺点
泄漏风险:开中心液压系统容易发生泄漏,导致液压油损失和系统效率降低 压力损失:由于开中心液压系统的结构特点,容易产生压力损失,影响系统效率 控制精度低:开中心液压系统的控制精度相对较低,难以满足高精度控制需求 维护成本高:由于开中心液压系统的结构复杂,维护成本相对较高
闭中心液压系统
工作特点
添加 标题
优缺点:开中心液压系统结构简单、易于维护,但体积 较大;闭中心液压系统结构紧凑、体积小,但维护相对 复杂。
应用场合比较
开中心液压系统:适用于需要快速 响应、高精度控制的场合,如机床、 机器人等
开中心液压系统:适用于需要高精 度、高响应速度的场合,如数控机 床、机器人等
添加标题
添加标题
添加标题
THANK YOU
汇报人:
开中心和闭中心液压系统工作 特点和优缺点分析
汇报人:
开中心液压系统 闭中心液压系统 开中心和闭中心液压系统的比较
开中心液压系统
工作特点
结构简单,易于维 护
压力损失小,效率 高
流量大,适用于大 流量场合
控制精度高,适用 于精密控制场合
优点
结构简单,易于维护 压力损失小,效率高 流量大,适用于大流量场合 易于实现多路控制,适应性强
- 1、下载文档前请自行甄别文档内容的完整性,平台不提供额外的编辑、内容补充、找答案等附加服务。
- 2、"仅部分预览"的文档,不可在线预览部分如存在完整性等问题,可反馈申请退款(可完整预览的文档不适用该条件!)。
- 3、如文档侵犯您的权益,请联系客服反馈,我们会尽快为您处理(人工客服工作时间:9:00-18:30)。
开式液压系统与闭式液压系统区别及优缺点
开式系统
开式系统是指液压泵1从油箱5吸油,通过换向阀2给液压缸3(或液压马达)供油以驱动工作机构,液压缸3(或液压马达)的回油再经换向阀回油箱。
在泵出口处装溢流阀4。
这种系统结构较为简单。
由于系统工作完的油液回油箱,因此可以发挥油箱的散热、沉淀杂质的作用。
但因油液常与空气接触,使空气易于渗入系统,导致路上需设置背压阀,这将引起附加的能量损失,使油温升高。
在开式系统中,采用的液压泵为定量泵或单向变量泵,考虑到泵的自吸能力和避免产生吸空现象,对自吸能力差的液压泵,通常将其工作转速限制在额定转速的75%以内,或增设一个辅助泵进行灌注。
工作机构的换向则借助于换向阀。
换向阀换向时,除了产生液压冲击外,运动部件的惯性能将转变为热能,而使液压油的温度升高。
但由于开式系统结构简单,仍被大多数起重机所采用。
闭式系统
在闭式系统中,液压泵的进油管直接与执行元件的回油管相连,工作液体在系统的管路中进行封闭循环。
闭式系统结构较为紧凑,不口空气接触机会较少,空气不易渗入系统,故传动的平稳性好。
工作机构的变速和换向靠调节泵或马达的变量机构实现,避免了在开式系统换向过程中所出现的液压冲击和能量损失。
但闭式系统较开式系统复杂,由于闭式系统工作完的油液不回油箱,油液的散热和过滤的条件较开式系统差。
为了补偿系统中的泄漏,通常需要一个小容量的补液泵进行补油和散热,因此这种系统实际上是一个半闭式系统。
一般情况下,闭式系统中的执行元件若采用双作用单活塞杆液压缸时,由于大小腔流量不等,在工作过程中,会使功率利用率下降。
所以闭式系统中的执行元件一般为液压马达。
工程机械液压传动系统,有开式系统和闭式系统,国内小吨位汽车起重机通常采取具有换向阀把持的开式系统,实现履行机构正、反方向活动及制动的请求。
中、大吨位起重机大多采用闭式系统,闭式系统采取双向变量液压泵,通过泵的变量转变主油路中液压油的流量和方向,来实现履行机构的变速和换向,这种节
制方法,可以充足体现液压传动的长处。
重型机械厂中、大吨位起重机液压工作装置,通常采取斜盘式轴向柱塞变量泵和定量马达组成的闭式系统。
斜盘式变量柱塞泵的流量与驱动转速及排量成正比,并且可无级变量。
闭式回路中变量泵的出油口和马达的进油口相连,马达的出油口和泵的进油口相连,组成一个封闭的液压油路,无需换向阀,通过调节变量泵斜盘的角度来转变泵的流量及压力油的方向,从而改变马达的转速和旋转方向。
变量泵的流量随斜盘摆角变更可从零增添到最大值。
当斜盘摆过中位,可以安稳转变液体流动方向,因此微动性好,且工作安稳。
闭式液压驱动系统在工作中不断有油液泄露(连续的高压油内泄是元件设计的固有产物),为了弥补这些泄漏和耗费,保持闭式系统正常工作,必需给闭式体系及时弥补油液。
闭式系统主泵上通轴附设一个小排量补油泵,由于补油泵的排量和压力相对主泵均很小,所以其附加功率丧失通常仅为传动装置总功率的1%~2%,可以忽咯不计。
在闭式系统液压工作装置中设有补油溢流阀和补油单向阀,补油溢流阀限制最高补油压力,补油单向阀依据两侧管路液压油压力的高下,选择补油方向,向主油路低压侧补油,以补偿由于泵、马达容积丧失所泄露的流量;主泵的两侧设有两个高压溢流阀,斜盘快速摆动时呈现的压力峰值及最大压力由高压溢流阀维护,防止泵和马达超载;该液压装置中还设有压力切断阀,压力切断阀相当于一种压力调节,当到达设定的压力时,将油泵的排量回调到为零的状况。
另外,在补油泵出口处还设有过滤器,对液压系统工作介质进行过滤,进步了液压油的干净度。
闭式体系具有以下优点:
(1)目前闭式系统变量泵均为集成式构造,补油泵及补油、溢流、把持等功效阀组集成于液压泵上,使管路衔接变得简略,不仅缩小了安装空间,而且减少了由管路衔接造成的泄露和管道振动,进步了体系的可靠性,简化了操作进程。
(2)补油系统不仅能在主泵的排量产生变更时保证容积式传动的响应,进步系统的动作频率,还能增添主泵进油口处压力,防止大流量时产赌气蚀,可有效提高泵的转速和防止泵吸空,提高工作寿命;补油系统中装有过滤器,提高传动装置的可靠性和应用寿命;另外,补油泵还能便利的为一些低压帮助机构供给动
力。
(3)由于仅有少量油液从油箱中汲取,减少了油箱的损耗。
开式液压系统的特点:
(1)一般采用双泵或三本供油,先导油由单独的先导泵提供。
有些液压执行元件所需功率大需要合流供油,合流有两种方式:①阀内合流。
一般有双泵合流供给一个阀杆,在由该阀一般杆控制供油给所需合流的液压执行元件。
该合流方式的阀杆的孔径设计需要考虑多泵供油所虚的流通面积。
②阀外合流。
双泵分别通过各自阀杆,通过两阀泛联动操纵,在阀杆外合流供油给所需合流的液压执行元件。
虽然操纵结构相对复杂、体积较大,但由于流经阀杆的饿是单泵流量,阀杆孔径相对较小,而且有可能与其他阀杆通用。
(2)多路阀常进行分块且分泵供油,每一阀组根据实际需要可利用直通供油道和并联供油道两种油道。
前者可实现优先供油,既上游阀杆动作时,压力油就供给该阀杆操纵的液压元件,而下游阀杆操纵的液压元件就不能动作。
后者可实现并供油。
(3)为满足多种作业工况及复合动作要求,一般采用简单的通断型二位二痛阀和插装阀,把油从某一油路直接引到另一油路,并往往采用单向阀防止油回流,构成单向通道。
通断阀操纵有以下3种方式:①采用先导操纵油联动操纵,先导操纵油在控制操纵阀杆移动的同时,联动操纵通断阀。
②采用操纵阀中增加一条油道作为控制通断阀的油道,这样在操纵操纵阀的同时,也操纵了通断阀的开闭。
开式油路的另一缺点是:当一个泵供多个执行器同时动作时,因液压油首先向负载轻的执行器流动,导致高负载的执行器动作困难,因此,需要对负载轻的执行器控制阀杆进行节流。
闭式液压系统具有以下优点:
(1)目前闭式系统变量泵均为集成式结构,补油泵及补油、溢流、控制等功能阀组集成于液压泵上,使管路连接变得简单,不仅缩小了安装空间,而且减少了由管路连接造成的泄漏和管道振动,提高了系统的可靠性,简化了操作过程。
(2)补油系统不仅能在主泵的排量发生变化时保证容积式传动的响应,提高
系统的动作频率,还能增加主泵进油口处压力,防止大流量时产生气蚀,可有效提高泵的转速和防止泵吸空,提高工作寿命;补油系统中装有过滤器,提高传动装置的可靠性和使用寿命;另外,补油泵还能方便的为一些低压辅助机构提供动力。
(3)由于仅有少量油液从油箱中吸取,减少了油箱的损耗。