年产70万吨焦炭焦化厂蒸氨工段的设计
年产70万吨焦炭焦化厂毕业设计汇总

河北联合大学本科毕业设计开题报告题目:年产70万吨焦炭焦化厂鼓冷工段初步设计学院:化学工程学院专业:化学工程与工艺班级:10化工(2)班姓名:********学号:***************指导教师:樊丽华老师2014年 3 月20 日回焦炉,要通过很长的管道及各种设备,为了克服这些设备和管道阻力及保持足够的煤气剩余压力,还要对煤气进行加压[14]。
1.2.3鼓风冷凝工艺流程被冷却的煤气与冷却介质直接接触的冷却器,称为直接混合式冷却器,简称为直接冷却器或直接冷却;被冷却的煤气与冷却介质分别从固体壁面的两侧流过,煤气将热量传给壁面,再由壁面传给冷却介质的冷却器,称为间壁式冷却器,简称为间接冷却或间接冷却器。
根据采用的初冷主体设备型式的不同,初冷的方法有间接初冷法、直接初冷法和间接—直接初冷法之分。
上述三种各有缺点,可根据生产规模,工艺要求几其他条件因地制宜地选择采用。
(1)煤气的间接冷却工艺煤气间接工艺流程图如下:图1 煤气间接初冷工艺流程1—气液分离器2—煤气初冷器3—煤气鼓风机4—电捕焦油器5—冷凝液槽;6—冷凝液液下泵7—鼓风机水封槽8—电捕焦油器水封槽9—机械化氨水澄清槽10—氨水中间槽11—事故氨水槽12—循环氨水泵13—焦油泵14—焦油贮槽15—焦油中间槽16—初冷冷凝液中间槽17—冷凝液泵焦炉煤气与喷洒氨水、冷凝焦油等沿吸煤气主管首先进入气液分离器,煤气与焦油、氨水、焦油渣等再次分离。
分离下来的焦油、氨水和焦油渣一起进入焦油氨水澄清槽,经过澄清分成三层:上层为氨水,中层为焦油,下层为焦油渣。
沉淀下来的焦油渣由刮板输送机连续刮送到漏斗处排出槽外,焦油则通过液面调节器流至焦油中间槽,由此泵往焦油贮槽,经初步脱水后泵往焦油车间。
经气液分离后的煤气进入数台并联立管式间接冷却器内用水间接冷却,煤气走管间,冷却水走管内。
从各台初冷器出来的煤气温度是有差别的,汇集在一起后的煤气温度称为集合温度。
年产70万吨焦炭焦化厂毕业设计

焦化厂是炼焦行业的主要生产设施,主要用于将煤炭加热至高温下进行热解,产生焦炭、焦炉煤气和焦油等副产品。
本文将对一个年产70万吨焦炭的焦化厂进行毕业设计,包括以下内容:厂区设计、工艺流程、设备选型、环境保护等。
1.厂区设计:焦化厂的厂区面积应足够大,以容纳煤炭储存、炼焦、气体处理和产品运输等各个生产区域。
厂区应具有良好的硬质道路、供水、供电和卫生设施等基础设施,以确保生产的正常进行。
2.工艺流程:焦化厂的工艺流程主要包括煤炭破碎、除尘、焦炉炼焦、气体处理和产品收集等环节。
(1)煤炭破碎:使用煤炭破碎机将大块煤炭破碎成适合炼焦的小颗粒。
(2)除尘:煤炭破碎和炼焦过程中会产生大量的粉尘,需要通过除尘设备进行处理,以减少对环境的影响。
(3)焦炉炼焦:将破碎后的煤炭投入焦炉进行热解,同时通过燃烧热能产生焦炉煤气。
(4)气体处理:将焦炉煤气进行脱硫、脱氰等处理,以减少对环境和人体的污染。
(5)产品收集:从焦炉煤气中提取焦油和其他有价值的副产品。
3.设备选型:对于年产70万吨焦炭的焦化厂,需要选择适合规模的设备。
(1)煤炭破碎机:根据煤炭的硬度和颗粒度要求,选择适合的煤炭破碎机。
(2)除尘设备:根据排放标准,选择适合的除尘设备,如电除尘器或袋式除尘器。
(3)焦炉:选择适宜规模和效率的焦炉,以提高焦炉产出和降低能耗。
(4)气体处理设备:选择适合的脱硫、脱氰设备,如干法处理或湿法处理等。
(5)产品收集设备:选择适宜的焦油分离装置和其他副产品的收集设备。
4.环境保护:焦化厂是重要的污染源之一,为了减少环境污染,需要采取相应的措施。
(1)安装除尘设备和脱硫设备,减少粉尘和气体污染物的排放。
(2)合理规划厂区,将生产区域与居民区、水源保护区等分开,降低对周边环境的影响。
(3)定期进行环境监测,确保排放符合国家标准。
(4)建立完善的废物处理体系,对废弃物进行合理处置,避免对土壤和水体的污染。
综上所述,本文对年产70万吨焦炭的焦化厂进行了毕业设计,包括厂区设计、工艺流程、设备选型和环境保护等方面。
焦化厂AO2工艺

AOO工艺在焦化废水处理中的应用陈平高加荣王会彬(贵州盘县天能焦化有限公司,盘县553531)我公司的污水处理工段于2006年5月建成投产,其污水处理工艺采用AOO法,主要处理化产各工序产生的废水和厂区生活污水。
经过近两年的调整,目前出水指标均达到或优于国家三级综合排放标准(GB8978-88)的要求,且完成了采用生化出水作稀释水的试验,真正达到了焦化废水零排放的目的。
1 废水的来源、水量及水质我公司是年产70万吨冶金焦,污水中来自蒸氨工段的蒸氨废水量约18m3/h,生活污水约2m3/h,场地冲洗水和溢流水等约2. 3m3/h。
综合水质如下:酚-N≤200mg/L 、氰化物≤8mg/L、油≤10mg/L。
≤250mg/L、COD≤ 1000mg/L、NH32 废水生物处理的工艺流程我公司污水处理工段的设计能力为50m3/h,根据污水处理装置各构筑物的功能,可分为预处理、生化处理和污泥处理等3部分。
2.1 预处理工艺废水先后进入斜管除油池、气浮池后,除去废水中的大部分油和氰化物,使废水中的油浓度控制在10mg/L以下,氰浓度在8mg/L以下,以保证生化对污水水质的要求。
斜管除油池沉积下来的重油和气浮池出来的油泡沫,经管道送鼓冷工段回收处理。
气浮池处理后的废水进入调节池,在调节池中用新鲜水稀释,将氨氮浓度调节在要求范围内。
进入调节池的废水温度,可通过蒸汽加热或调整蒸氨废水换热器加以保证,其工艺流程示于图1。
图1 原焦化废水生化处理工艺流程图2.2 生化处理(1)污泥的接种及驯养。
我公司接种报污泥来自邻近焦化厂,在运输过程中,由于没采取供氧措施,导致好氧菌多数死亡,接种污泥量共计60m3。
事先在好氧池中存有少量原水(蒸氨废水加稀释水),液位大致为lm,原水中的氨氮≤50mg/L 、pH = 77. 5、磷2~4mg/L、COD 250~500mg/L、DO 2~4mg/L、温度28~35℃。
将接种污泥抽送到好氧池中进行闷曝,每隔2h取样观察污泥的沉降性能和菌种的复活情况,当大量的菌种出现后,废水中的氨氮、COD、磷含量等指标将会下降,此时用潜泵将调节池中的废水定量连续送入好氧池。
焦化厂硫铵蒸氨工段操作规程

焦化厂硫铵工段平安技术操作规程一、工艺流程1、硫铵工序由冷鼓送来的煤气,经蒸汽预热后,进入喷淋式饱和器的上段喷淋室,在此分两股沿饱和器内壁与内除器的环形空间流动,并循环的母液充分接触,氨被吸收后煤气合并成一股,沿切线方向进入饱和器内除酸器,别离煤气中夹带的酸雾,后送往粗笨工段。
在饱和器下端结晶室上部的母液,用循环泵连续抽出送至上段喷淋室进展喷洒,吸收煤气中的氨,并循环搅动母液以改善硫铵结晶过程。
饱和器在生产时母液中不断有硫铵结晶生产,由上段喷淋室内的降液管流至下段结晶室的底部,用结晶泵将其连同一局部母液送至结晶沉降,然后排放至离心机内进展离心别离,滤除母液并用热水洗涤结晶,离心滤除的母液与结晶槽满流出来的母液一同自流同饱和器下段的母液中。
从饱和器满流口溢流出的母液,通过插入液封内的满流管流入满流槽,满流槽内的母液用小母液泵送至饱和器顶部用于二次喷洒洗铵之用。
买来的硫酸、放入硫酸地下槽后,用液下泵打往硫酸贮槽,在通过硫酸泵打往高位槽,然后自流参加满流槽,当硫酸高位槽的液位高时,可满流回硫酸贮槽,在定期用泵打往高位槽以作补充之用。
饱和器定期补水,并用水冲洗饱和器,所形成的大量母液即由满流槽至母液贮槽,用于给饱和器补液用。
带入母液中的焦油,在饱和器上段喷淋室内由满流口满流至满流槽,在饱和器下段结晶上部由焦油排出口排出至满流槽,满流至母液贮槽,定期捞出。
当硫酸高位槽的液位高时,可满流硫酸贮槽,再定期用泵送回高位槽以作补充。
从离心机卸出的硫铵产品,由螺旋输送机送至沸腾式枯燥器,进展枯燥后进入储料斗,,然后称量,推包,封袋,送入成品库,枯燥冷却器顶部排出的尾气,经旋风别离,再经过水浴器过滤洗涤尾气中夹铵颗粒,由排风机排至大气。
2、蒸铵工序从萃取脱酚工段来的剩余氨水首先进入氨水贮槽,然后由氨水泵送入换热器预热至约90℃在进蒸氨塔顶,氨水在塔内逐级而下与蒸汽反复接触使NH3转移到汽相中,最后从塔底排入废水槽再次别离重油,废水泵从废水槽中把温度较高的废水送入换热器与氨水进展热交换,温度降低后的废水通过管道送往生化站作进一步的处理后排放,或送往熄焦池熄焦。
焦化厂剩余氨水蒸氨新工艺的应用

焦化厂剩余氨水蒸氨新工艺的应用刘俊仓刘运龙(安阳市恒威石化设备有限责任公司)1剩余氨水蒸氨新工艺焦化厂的剩余氨水经原料氨水槽静止分离和陶瓷过滤等方式脱除焦汕后;与蒸氨塔塔底部分蒸氨废水进行换热后,送入蒸氨塔上段;用废水循环泵将蒸氨塔底部分废水,送入废水加热装置,将废水加热到125〜130°C后,返回蒸氨塔代替蒸汽。
流程示意见图(1)。
图1煤气直接加热蒸氨工艺流程示总图碱液经流量计送入原料氨水泵压出管中,以分解剩余氨水中的固左彼。
蒸氨塔底的蒸氨废水与原料氨水换热,再经冷却器冷却至40°C后,送至酚魚污水处理站。
蒸氨塔顶的氨汽经氨分缩器冷凝冷却后,送入硫彼饱和器或煤气脱硫装宜。
表1列出了各种蒸氨工艺的指标对比结果(以60万t/a)o农1各种蒸氨工艺的指标对比结果(以60万吨焦炭/年)项目蒸汽直接蒸氨蒸汽间接蒸氨煤气加热蒸氨导热油加热蒸氨剩余氨水量,t/h15151515蒸汽耗量,t/h3 3.800废水增加量,3000注:1)电力:0. 6元/kWh; 2)蒸汽:120元/m3⑶煤气:0. 4元/m3; 4)导热油:4万元/t;5) 各种蒸氨工艺的循环冷却水消耗量相同,未计入动力消耗中;6)蒸汽间接蒸氨工艺未计冷凝水回收效益。
2四种蒸氨工艺的特点(1)蒸汽直接蒸氨工艺。
蒸汽直接进入蒸氨塔作为蒸懈介质加热废水的工艺简单,投资费用少,但蒸汽用量大,造成生产成本髙,并会增加蒸氨废水量,增加了生化处理装置的废水负荷。
(2)蒸汽间接蒸氨工艺。
蒸汽通过再沸器和废水进行热量互换来加热废水,比蒸汽直接蒸氨工艺复杂,蒸汽消耗大,运行费用髙,但其优点是投资费用较低,不会增加蒸氨废水量。
(3)煤气加热装垃蒸氨工艺。
用煤气加热装置宜接加热废水蒸氨的工艺流程短,生产稳定,运行费用低,不会增加蒸氨废水量。
我公司在2008年10月为河南利源焦化公司(年产焦炭60万吨)建设了一套的焦炉煤气直接加热废水的蒸氨装宜,各项操作指标均达到了设计要求:运行效果一直良好,用户非常满意,见图2。
万吨焦化厂硫铵工段设计毕业设计.doc
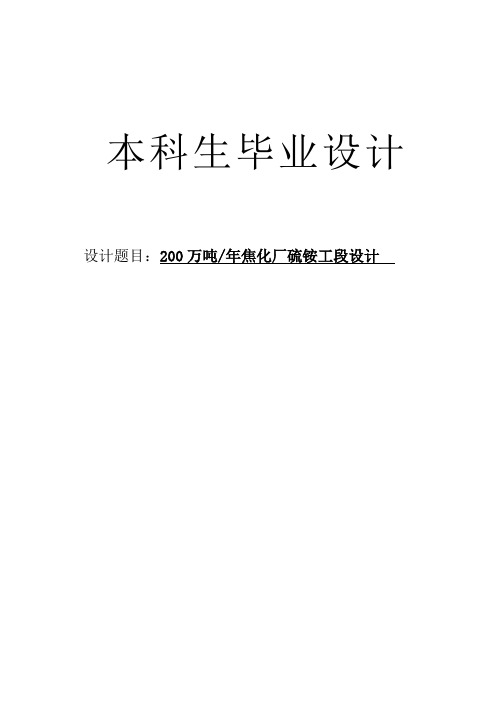
本科生毕业设计设计题目:200万吨/年焦化厂硫铵工段设计中国矿业大学毕业设计任务书学院专业年级学生姓名任务下达日期:毕业设计日期:毕业设计题目:200万吨焦化厂硫铵工段设计毕业设计专题题目:毕业设计主要内容和要求:对200万吨/年焦化厂进行主要物料计算,确定配套的氨回收工段的主要设计依据。
确定氨回收的工艺流程,并根据硫铵生产的工艺,进行设计的工艺计算、设备的选型计算、进行工艺布置,并绘制工艺流程、工艺布置和主要非标设备的图纸,对整个工段的建设进行投资估算和效益分析院长签字:指导教师签字:中国矿业大学毕业设计指导教师评阅书指导教师评语(①基础理论及基本技能的掌握;②独立解决实际问题的能力;③研究内容的理论依据和技术方法;④取得的主要成果及创新点;⑤工作态度及工作量;⑥总体评价及建议成绩;⑦存在问题;⑧是否同意答辩等):成绩:指导教师签字:年月日中国矿业大学毕业设计评阅教师评阅书评阅教师评语(①选题的意义;②基础理论及基本技能的掌握;③综合运用所学知识解决实际问题的能力;③工作量的大小;④取得的主要成果及创新点;⑤写作的规范程度;⑥总体评价及建议成绩;⑦存在问题;⑧是否同意答辩等):成绩:评阅教师签字:年月日中国矿业大学毕业设计答辩及综合成绩摘要本设计为年产焦炭200万吨焦化厂回收车间硫铵工段的工艺设计,该焦化厂拟建于徐州市西北郊区。
本设计内容包括:生产原理、工艺流程、计算及设备的选型、工艺布置、操作规程、成本估算、经济分析等。
本设计采用技术较成熟的饱和器法中的半直接法来回收煤气中的氨,工艺流程如下:从冷凝工段来的煤气首先进入煤气预热器,然后进入饱和器,在饱和器内,煤气中的氨与硫酸反应生成硫铵,硫铵经后续操作分离,从饱和器出来的煤气送往粗苯工段。
计算部分包括物料衡算和热量衡算,通过对主要设备如饱和器、煤气预热器、沸腾干燥器等的计算来确定适宜的母液温度和煤气预热温度,同样可以确定本设计所需的三台饱和器及其它设备。
浅析焦化厂蒸氨改造的工艺选择

热后 ,进入蒸氨塔上部。塔底的部器内与导热油进行换热 ,用导热 油加热
发电站的减温减压蒸汽提供生产蒸汽 ,蒸汽供应不 后的水蒸汽返 回蒸氨塔底作 为热源 其余废水送 至
太稳定 ,特别是冬天和干熄焦有故障时。水蒸汽蒸 酚氰废水处理站。该流程不使用直接蒸汽利用导热
蒸氨废水从塔下部流出和来至冷凝鼓风工段 的剩余. 耗高的问题 。
氨水换热后泵送至污水处理。塔顶温度控制在 100 2 对 比分 析
收稿 日期 :2013—09—24 作者简介 :熊曙光 (1979一 ),江西石城人 ,工程师 ,从事焦化厂生产管理工作。
第 l2期
熊 曙光 ,等 :浅析焦化厂蒸氨改造 的工艺选择
概 每小 时 处 理 量 55t。新 系 统 蒸 氨 是 和 2座 63孔 质 。从 而实 现蒸 氨 目的 。
6m焦炉配套 ,无需处理焦油精制工序产生的酚水 , 1.2 导热油 蒸氨 工艺
大概每小时处理量 25t。经过处理 的蒸氨废水全部
冷凝鼓风工段送来的剩余氨水与废水换热器换
进 生化污 水处理 。
机减温减压消耗的除盐水量。这和节能减排的环保 1.3 负压蒸氨
要求不 相符 。
塔顶 由真空系统抽 真空产 生负压蒸馏操作条
新钢焦化厂蒸氨工艺是这样 的:来至冷凝鼓风 件。通过联合 控制塔顶压 力和温度。调节蒸馏效
工段的剩余氨水经过废水换热器与废水换热后进人 果 ,多余的尾气经尾气管进入负压煤气管道中,成品
新钢焦化厂化产车间蒸氨工艺 目前采用 的是水 与废水换热 后进人蒸氨塔上部 ,部分氨水从塔底经
蒸汽直接蒸氨,老系统蒸氨是和 4座共 192孔 4.3m 泵抽出送到管式炉加热 ,加热后的氨水回到塔底 的
年产70万吨焦炭焦化厂设计—毕业设计

的氨,60%以上的萘,以及约 50%的硫化氢、氰化氢。这对后面洗氨、洗 苯过程及减少设备腐蚀,都是有益的。它与煤气间接初冷工艺相比,直 接初冷工艺有冷却效率高、煤气压力损失小、不易堵塞以及基建投资和 钢材用量少等优点。但其工艺流程较复杂、动力消耗较大、循环氨水冷 却器易堵塞等缺点。所以,大型焦化厂已很少单独采用煤气直接初冷流 程。 (3)煤气的间-直冷却工艺
煤气的初冷,输送及初步净化,是炼焦化学产品回收工艺过程的基 础。其操作运行的好坏,不仅对回收工段的操作有影响,而且对焦油蒸 馏工段及炼焦炉的操作也有影响。因此,对这部分工艺及设备的研究都 很重视[13]。
煤气初冷的目的一是冷却煤气,二是使焦油和氨水分离,并脱除焦 油渣。
在炼焦过程中,从焦炉炭化室经上升管逸出的粗煤气温度为
经气液分离后的煤气进入数台并联立管式间接冷却器内用水间接冷 却,煤气走管间,冷却后的煤气温度称为集合温度。
随着煤气的冷却,煤气中绝大部分焦油气、大部分蒸气和萘在初冷 器中被冷凝下来,萘溶解于焦油中。煤气中一定数量的氨、二氧化碳、
硫化氢、氰化氢和其他组分溶解于冷凝水中,形成了冷凝氨水。焦油和 冷凝氨水的混合液称为冷凝液。如上图所示,冷凝液自流入冷凝液槽, 再用泵送入机械化氨水澄清槽,与循环氨水混合澄清分离,分离后所得 剩余氨水送去脱酚和蒸氨。
为防止初冷器清扫时流出的萘油遇同一系统运行的初冷器水封流出的低温冷凝液而析出结块而使满流总管堵塞须在清扫前将运行初冷器的煤气出口温度控制在28以上同时打开水封系统加热器保证冷凝液温度不会偏低并且为防止初冷器清扫时流出的大量萘油带入喷洒泵送入同系运行的初冷器内造成挂萘堵塞须先关小喷洒泵入口阀门并打开出口管旁通不能含萘冷凝液进入运行的初冷器
- 1、下载文档前请自行甄别文档内容的完整性,平台不提供额外的编辑、内容补充、找答案等附加服务。
- 2、"仅部分预览"的文档,不可在线预览部分如存在完整性等问题,可反馈申请退款(可完整预览的文档不适用该条件!)。
- 3、如文档侵犯您的权益,请联系客服反馈,我们会尽快为您处理(人工客服工作时间:9:00-18:30)。
1 设 计 任 务 书1.1设计任务年产70万吨焦碳的焦化厂蒸氨工段的设计。
1.2设计的基础资料1.2.1 工艺计算主要依据煤气产率 340Nm 3/t 干煤氨产率(挥发氨) 0.3%初冷器后煤气温度 30℃剩余氨水中氨含量 3.5g/l2 概述剩余氨水是煤焦化工业中焦化废水的主要来源,其中含有大量的挥发氨和固定胺盐,严重影响了生化工段的废水处理结果,因此蒸氨工艺是焦化废水处理工艺的第一环节,同时还在为脱硫工段提供碱源的过程中起重要作用,因此蒸氨系统的稳定运行直接影响到生化工段出水指标及脱硫工段的脱硫效果。
鼓冷工段昌盛的大量剩余氨水与蒸氨塔底废水换热后,进入到蒸氨塔中开始蒸馏,蒸氨塔底部通入饱和水蒸汽,以提供蒸氨所需热量及氨气载体,蒸出的大量氨气与水蒸气混合气体从塔顶分缩器出来后,去往脱硫工段,塔底废水在与剩余氨水、冷却水连续换热后,去往盛化工段进行水处理,同时在蒸氨过程中,需要在剩余氨水中加入一定量的液体氢氧化钠,以促进剩余氨水中固定铵盐的分解,保证蒸氨效果。
3蒸氨工段设备的计算3.1 蒸氨塔的计算3.1.1 基本数据的确定①原始数据:煤气总量 35000Nm 3 进料温度 50℃分凝器后产品浓度 10%塔顶温度 102℃ 塔顶压力 14.7MPa 塔底温度 105℃ 塔底压力 34.3MPa 回流温度 90℃ 进料浓度 3.5 g/h经计算得 进料量F 及浓度X FF = 12.63 t/h%35.0%10063.12105.363.123=⨯⨯⨯=-F X 参考《炼焦化学品回收与加工》附表5,得氨水在水溶液里及液面上蒸汽内的含量为Y 1 = 3.5%② 氨分缩器后成品氨气浓度的确定X D = 10%,设在蒸氨塔里的氨回收率99%,则氨为: 99%×12.63×3.5×103-/1000≈43.75kg/h 或54.51h Nm /3氨气混合物 D = 43.75÷10% = 437.5 kg/h水蒸汽的量 437.5×(1-10%) = 393.75kg/h 或 490.61 h Nm /3考虑到氨气中H 2S 和CO 2,设占氨气体积的5%,则82.573%5161.49051.54=-+h Nm /3 取分缩器后氨气操作压力为850mmH 2O,则氨气在气体混合物中的分压为:P S = 850×490.61/573.82= 726.148 mmH 2O③分缩器后回流液含氨浓度的确定出成品氨的浓度为10% 即X D = 10% 查《炼焦化学品回收与加工》中附表5得,回流液浓度为X R = 1.2%。
则进料热状况:q = 将1Kmol 进料变为饱和蒸汽所需的热量/原料液的Kmol 汽化热,查物性手册得1097.12250184018618)50102(225018≈=⨯⨯⨯-+⨯即:q F Y Y = Xq X F = ∴Rmin=F F F D X -Y Y -X =5.05.35.310--=2.06 一般取R=(1.1~2) Rmin 现取 R=1.5Rmin=3.093.2 物料恒算(1)输入物料进料量 F = 12.63t/h含氨量 = 12.63×103×0.35% = 44.19 kg/h设蒸氨塔中氨的回收率为99%则:D=44.19×99%/10%=437.47kg/h回流量 L = RD = 3.09×437.47= 1351.79 kg/h(2)输出物料塔顶蒸汽量 V = (R+1)D = 4.09×437.47= 1789.26kg/h废水量 W = F-D+G = 12630– 437.47 +G = 12192.53+ G kg/h(3)热量恒算—确定直接蒸汽量G①输入热量进料带入热量 q 1 = 12630×50×1.0074×4.187= 2662698.14 kJ/h回流带入热量 q 2=1351.79×90×1.005×4.187= 511941.66kJ/h直接蒸汽带入热量q 3 = 2738G kJ/h式中 G — 蒸气量2738—4Kg/cm 3(绝压)时水蒸气热焓,2741 — 表压为0.3时,水蒸汽热焓 kJ/Kg1Q = q 1+ q 2+ q 3 = 2662698.14+ 511941.66 + 2738G= 3174639.8+ 2738G kJ/h②输出热量塔顶蒸汽带出热量q 4 = 2811.7×3.5%×102×2.131 + 2811.7×(1-3.5%)×2678.84= 7507857.8 kJ/h式中 2.131—— 氨的比热 KJ/(Kg ·℃)3.5% —— 含氨量2678.84—— 102℃时水的热焓 kJ/kg氨解析吸收的热量 q 5 = 2811.695×3.5%×491×4.187= 20231.16 kJ/h废水带出的热量 q 6 = (12192.53+G)×105×1.0089×4.187= 5407969.27+443.5G kJ/h散热损失 q 7 = q 3×2% = 2738G ×0.02 = 57.46G kJ/h2Q = q 4 + q 5 + q 6+ q 7=7507857.8+20231.16+5407969.27+443.5G +54.76G=12936058.23+488.26G kJ/h由 1Q =2Q 得:3174639.8+ 2738G =12936058.23+488.26G直接蒸汽量G =4338.91kg/h1吨氨水所用蒸汽量 g = G/F = 4338.91/12.63 = 343.54kg/t废水量 W = 12192.53+ G = 12536.07kg/h = 16531.44 t/h3.3蒸氨塔设备的计算(1) 塔板层数的确定作全塔的物料平衡:∵废水量W = 12192.53+ G = 16531.44kg/h = 16.531 t/h∴废水含氨量X W =%005.016531.441000%212192.535.3=⨯⨯⨯直接蒸汽加热时,提镏段的操作线方程为Y W m m X GW X G W +=-1 式中:W —废水量,16531.44 kg/hG —直接蒸汽耗量,4338.91kg/h即Y 000191.081.34338.9116531.444338.9116531.4411-=-=--m W m m X X X 以进料含氨量浓度 XF=0.35% 按《炼焦化学品回收与加工》附表5中数据采用逐板计算法计算提馏段理论板数.X % 0.35 0.17 0.0811 0.0374 0.0159 0.00536 0.000176Y % 1.70 0.811 0.374 0.159 0.0536 0.00176∴提馏段需理论板数为5对于精馏段由于塔顶气相浓度不高于和进料平衡的气相浓度,所以只 需要一块理论板,则全塔理论板数为6块.本设计采用浮阀塔,总板效率取0.5,则实际板数为6/0.5=12块(2) 塔径的计算 ∵V <V S ∴用塔底气体积确定塔径Vs =3.343.1013.1012731022734.2218%)5.31(7.281117%5.37.2811+⨯+⨯⨯⎥⎦⎤⎢⎣⎡-⨯+⨯ =3601.2h m /3原料汽化热取水的热量为 1500kJ/kg 平均温度(98+50)/2 = 74℃ρl = 974.8 ㎏/m3 ρV =0.661 ㎏/m3 查《化工原理》(天大版) 附表7 水的比热为4.2 kJ/(㎏·℃)q = 1500)5098(2.41500-⨯+=1.13 L ' = L+QF = 1351.79+1.13×20890 =24957.49㎏/hV ' = V+(q-1)F = 1351.79+0.13×20890 =4067.49㎏/h21)(Pv Pl Vh Lh =1)(661.08.974661.0/56768.974/2.25842⨯= 00.119塔板间距取45㎜,板上液层高度取0.07m 则: H T -H l = 0.38 m 查《化工原理》(天大版)下册P160, 史密斯关系图得C 20 = 0.0062校正 C = C 20×2.020)(δ = 0.062×2.0206345.0)(=0.031∴Umax=C ×Pv PvPl -=0.031×661.0661.08.974-= 1.19 m/s 通常取 U = 0.6~0.8Umax 现取安全系数 0.7则U = 0.65×1.19 = 0.774 m/s 则D =U Vs14.34=774.014.336002.36014⨯⨯⨯= 1.283m 圆整取D = 1400 mm 塔截面面积 AT =2414.3D =24.1414.3= 1.538㎡ (3) 塔高的计算1)该塔有效高度Z=(N-1)×HT=(12-1)×0.45=4.95m2)塔顶辅助高度取1m3)塔底辅助高度取1.5m(塔底最后一块塔板到塔底封头切线的距离)4)塔底裙座高度取2 m5)人孔,人孔的设计应便于进入任何一层塔板,但设置过多会使制造时塔体弯曲度难以达到要求,所以本塔设置一个人孔,位置在自上面算起第8块塔板处,此处塔板间距设计为600㎜,另外,塔裙处应设计两个人孔直径为450㎜.综上该塔实际高度H=4.95+1+1.5+2+(0.6-0.45)=9.6m参考文献[1] 朱世勇.环境与工业气体净化技术[M].北京:化学工业出版社.2001.31-36.[2] 库咸熙.炼焦化学产品的回收与加工.冶金工业出版社,1985[3] Berkowitz N.焦炉煤气脱硫工艺的选择[J].高彬升译.国外炼焦化学[J].1990(5):57[4] 王睿,石冈等.工业气体中H2S的脱除方法.天然气工业[J].1999(5):84~90.[5] 张巨水.焦化厂焦炉煤气脱硫脱氰工艺的选择[J].煤化工,1999(4):21[6] 张炳玉,金蝶翔.焦炉煤气净化工艺评述[J].包钢科技,2001(2):15[7] 杨建华,王永林.焦炉煤气净化.北京:化学工业出版社,2005[8] 张双全,吴国光.煤化学.中国矿业大学出版社,2004[9] 肖瑞华, 白金锋.煤化学产品工艺学[M].北京: 冶金工业出版社,2003[10] 夏清,陈常贵.化工原理(上下册).天津:天津大学出版社,2006[11] 姚玉英.化工原理(上册).天津:天津大学出版社,1999[12] 陈钟秀,顾飞燕等.化工热力学.化学工业出版社,2003[13] 柴诚敬,刘国维等.化工原理课程设计.天津科学技术出版社,1995[14] 倪进方.化工设计.化学工业出版社,1999[15] 汪寿建.化工厂工艺系统设计指南. 化学工业出版社,1996[16] 陈声宗.化工设计.化学工业出版社,2001[17] 王同章.煤炭汽化原理与设备.机械工业出版社,2001[18] 国家医药管理局上海医药设计院.化工工艺设计手册(上下册),1985[19] 侯文顺.化工设计概论.化学工业出版社,1999[20] 黄璐,王保国.化工设计.北京:化学工业出版社,2001[21] 历玉鸣.化工仪表及自动化.北京:化学工业出版社.2005[22] 董大勤.化工设备机械基础.化学工业出版社,2003[23] 大连理工大学.青岛化工学院.南京化工学院.化工容器及设备简明设计手册.化学工业出版社,1989[24] 范德明.工业泵选用手册[M].北京: 化学工业出版社, 1998[25] 李尚文,鲁国良.实用管路手册.化学工业出版社,1999[26] 刘相臣,张秉淑.化工设备事故分析与预防.化学工业出版社,2003。