包包生产工艺-厂家生产具体流程
包的生产工艺流程图

包的生产工艺流程图包的生产工艺流程图包是我们日常生活中必不可少的物品之一,它的生产过程经过了多个环节的精细处理。
下面将对包的生产工艺流程进行详细介绍。
1. 设计:包的生产过程首先是设计阶段。
设计师根据市场需求和时尚趋势,确定包的样式、尺寸和材质等。
设计师会绘制出包的草图和大小样,供后续生产环节参考。
2. 材料采购:生产包需要用到各种材料,如面料、拉链、皮革、配件等。
生产厂商会与供应商联系,采购所需的材料。
同时,还要对采购的材料进行质量检验,确保符合生产要求。
3. 裁剪:在材料准备好后,需要进行裁剪。
根据包的设计图纸,使用切割机器或手工切割,将面料、皮革等材料按照相应尺寸裁剪成所需的形状。
4. 缝制:裁剪好的材料进入缝制环节。
包的款式不同,缝制工艺也有所不同。
一般来说,使用缝纫机进行缝制,将各个零部件缝合在一起,形成包的基本结构。
5. 细节处理:缝制完成后,对包进行细节处理。
这包括各种辅助装饰,如用丝线装饰、安装拉链、加装金属扣等。
此外,还要进行包的整体熨烫,使其形状更加完美。
6. 质检:在包完成后,进行质量检验。
质检人员会对包的外观、线头、拉链等进行检查,确保其质量合格。
不合格的包会进行返工或拒绝销售。
7. 包装:质检通过的包进入包装环节。
包装包括包装盒、纸袋或塑料袋等。
同时,还要加入标签、说明书等必要的配件。
包装完成后,包的外观更加整齐,便于销售和运输。
8. 销售:包装完成后,包可以上市销售。
销售渠道包括线上和线下,在商场、专卖店或电商平台上进行销售。
消费者可以根据自己的喜好和需要选择合适的包。
总之,包的生产工艺流程经过了设计、材料采购、裁剪、缝制、细节处理、质检、包装和销售等多个环节。
每个环节都需要经过严格的控制和管理,确保包的质量和外观符合消费者的需求。
只有经过精心的制作,才能生产出符合市场需求的高质量包。
箱包生产工艺流程图

箱包车间生产工艺流程图
抽板
领料拌料烘料挤出/抽板切断/摆放检验/周转
成型
调模 /预热箱壳成型裁边冲孔钻孔检验/周转
铝框成型
领料调模冲孔/弯角成型
铆钉前处理喷涂检验/周转
缝纫备料
领料调试刀模冲裁内里片剪裁里布检验/周转车缝
车缝内装车缝拉链/钉扣
检验/周转
组装
组装备料成品组装全检包装入库/出货
『抽板』
领料
拌料
烘料
挤出 /抽板切断 /摆放检验 /周转
箱包生产工艺流程图
『铝材成型』『缝纫备料』
领料领料
『箱壳成型』调模调试刀模
调模 /预热冲孔 / 弯角成型冲裁内里片
箱壳成型铆钉剪裁里布『车缝内装』裁边前处理检验 /周转车缝内装冲孔钻孔喷涂车缝拉链 /钉扣检验 /周转检验 /周转检验 /周转『组装』
组装备料
成品组装
全检
包装
入库 /出货
制订:核准:。
包生产工艺流程
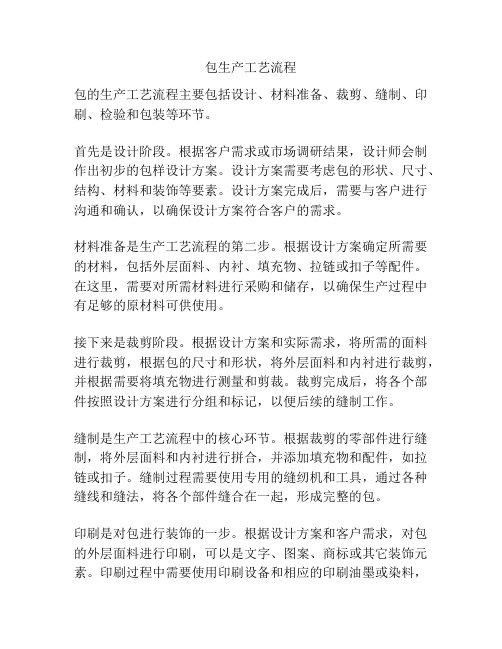
包生产工艺流程包的生产工艺流程主要包括设计、材料准备、裁剪、缝制、印刷、检验和包装等环节。
首先是设计阶段。
根据客户需求或市场调研结果,设计师会制作出初步的包样设计方案。
设计方案需要考虑包的形状、尺寸、结构、材料和装饰等要素。
设计方案完成后,需要与客户进行沟通和确认,以确保设计方案符合客户的需求。
材料准备是生产工艺流程的第二步。
根据设计方案确定所需要的材料,包括外层面料、内衬、填充物、拉链或扣子等配件。
在这里,需要对所需材料进行采购和储存,以确保生产过程中有足够的原材料可供使用。
接下来是裁剪阶段。
根据设计方案和实际需求,将所需的面料进行裁剪,根据包的尺寸和形状,将外层面料和内衬进行裁剪,并根据需要将填充物进行测量和剪裁。
裁剪完成后,将各个部件按照设计方案进行分组和标记,以便后续的缝制工作。
缝制是生产工艺流程中的核心环节。
根据裁剪的零部件进行缝制,将外层面料和内衬进行拼合,并添加填充物和配件,如拉链或扣子。
缝制过程需要使用专用的缝纫机和工具,通过各种缝线和缝法,将各个部件缝合在一起,形成完整的包。
印刷是对包进行装饰的一步。
根据设计方案和客户需求,对包的外层面料进行印刷,可以是文字、图案、商标或其它装饰元素。
印刷过程中需要使用印刷设备和相应的印刷油墨或染料,将设计好的图案或文字印刷到包的表面。
检验是保证产品质量的一步。
在缝制和印刷过程中,需要不断进行检查和测试,确保包的质量符合设计要求和客户需求。
检验包括对面料的材质和质量进行检查、对缝制工艺进行检验、对印刷效果进行测试等。
最后是包装阶段。
完成了检验的包需要进行整理和包装,以便出货和销售。
包装可以是用塑料袋、纸箱、木箱或布袋等材料进行包装,对包的外表进行保护和美化,同时也方便存储和运输。
以上就是包的生产工艺流程,通过以上的环节,可以完成包的设计、加工和包装,最终交付给客户使用。
这个生产流程需要不同的技能和设备,只有经过精细的安排和严谨的执行,才能确保包的质量和客户满意度。
箱包生产工艺流程

箱包生产工艺流程箱包是人们日常生活中常用的物品,它们不仅具有实用功能,还可以体现个人品味和时尚风格。
箱包的生产工艺流程经过多道工序,需要经过设计、材料选择、裁剪、缝制、装配等环节,才能最终成品。
下面将详细介绍箱包的生产工艺流程。
1. 设计。
箱包的生产工艺流程首先需要进行设计。
设计师根据市场需求和时尚潮流,设计出款式新颖、实用性强的箱包图稿。
设计稿需要考虑到箱包的尺寸、结构、内部隔层、拉链、扣具等细节,以及面料的选择和搭配。
设计稿完成后,需要进行样品制作和样品确认,确保设计效果符合预期。
2. 材料选择。
箱包的材料选择非常重要,它直接影响到箱包的质量和外观。
常用的箱包材料包括皮革、帆布、尼龙、PU皮等。
不同的材料有不同的特点,例如皮革具有良好的手感和耐磨性,而帆布则轻便耐用。
在选择材料时,需要考虑到箱包的用途、款式和成本等因素。
3. 裁剪。
裁剪是箱包生产的重要环节。
根据设计稿,将所需的面料进行裁剪,包括外层面料、内衬、填充物等。
裁剪需要根据不同的部位和尺寸进行,确保面料的利用率和裁剪精度。
4. 缝制。
缝制是箱包生产的核心环节。
经过裁剪的面料需要进行缝制,包括缝合外层面料、内衬、拉链、扣具等。
缝制需要使用专业的缝纫机和工艺,确保线迹平整、牢固。
对于皮革箱包,还需要进行打孔、翻边、打蜡等特殊工艺。
5. 装配。
装配是箱包生产的最后一道工序。
经过缝制的各个部件需要进行装配,包括安装拉链、扣具、肩带等配件。
装配需要注意细节,确保各个部件的位置和功能正确。
6. 质检。
质检是箱包生产的关键环节。
经过装配的箱包需要进行严格的质量检验,包括外观检查、拉链拉力测试、扣具耐久性测试等。
只有通过质检的箱包才能出厂销售。
通过以上工艺流程,箱包的生产从设计到成品经历了多道工序,需要经过精心的计划和细致的操作。
每个环节都需要严格把关,确保箱包的质量和外观达到标准。
箱包生产工艺流程的完善和严谨,是箱包制造业得以持续发展的重要保障。
包包生产工艺-厂家生产具体流程

1 目的为强化生产过程管理,规范影响生产进度和过程质量各个因素的控制,使生产在受控状态下进行,提高生产效率,提升产品质量。
2 适用范围适用于客户意向锁定后,从订单评审签订开始到成品入库/交付为止整个生产过程控制。
3 职责a) 业务部:订单产品报价成本分析,提供材料(定额)清单,样品制作和确认,签发生产通知单,协调产品发货,销售款项催收结算。
b) 生产部:参与订单评审,审核业务部提交的生产通知单、材料定额,审定工序(工步)流程和工时定额,下达采购指令、生产指令,协调督导采购、车间、设备、检验包装和仓库落实职能工作,按期保质保量完成生产任务。
c) 采购科:根据材料定额和生产部下达的采购指令组织原辅材料的采购,保证质量,按期入库,确保生产用料。
d) 品管科:根据程序执行进料检验、成品检验和出货检验,确保出货产品的品质。
e) 车间:执行生产部下达的周生产进度计划,分解工序,调配生产要素(人员、材料、机台等),组织均衡生产,督导落实制作工艺流程,按期完成生产任务。
f) 仓管组:物料的进库、保管和发放及资材帐务、票证管理。
g) 其他:办公室、财务部按照职能开展工作。
4 业务洽谈和销售合同4.1 业务部销售人员应通过原有的市场网络和电脑网络,多渠道搜集客户需求信息,主动联系,扩大业务触角,争取更多的目标客户。
4.2 客户联络应建立完整记录,对总经理室锁定的目标客户,应保持跟踪联络,及时通报洽谈的进展情况,必要时,应提报总经理室介入洽谈,形成合同意向。
4.3 业务部与客户洽谈合同,应对合同要素(如款式、单价、交货期限、付款办法及质量要等进行认真评审,财务部、生产部应配合成本分析,提供决策依据。
4.4 销售合同应按规定格式拟制,报经总经理室签发。
4.5 合同意向达成(或签订合同)后,业务部应向技术科下达样品制作,并交付客户确认。
确认的主要内容包括包袋的结构样式,布料质地和颜色,装饰件及辅料,外观视觉效果及验收标准。
包包生产工艺流程

包包生产工艺流程包包生产工艺流程一般包括设计、裁剪、缝制、加工和质检等环节。
下面将详细介绍一下包包生产的工艺流程。
首先,包包的生产从设计开始。
设计师根据市场需求和时尚潮流,进行包包款式、尺寸和材料的选择。
设计稿提供给生产部门后,生产部门进行材料采购、面料染色等准备工作。
接下来是裁剪环节。
根据设计要求,将原料进行裁剪,得到包包的各个组成部分,如正面、背面、底部和侧面等。
裁剪时要确保尺寸准确,材料利用率高。
裁剪完成后,将各个部分进行编号,以便后续缝制工序。
缝制环节是包包生产的关键环节之一。
按照编号将各个部分进行拼接缝合,使用缝纫机和特殊缝纫线进行缝制。
在缝制过程中,需要注意线迹的整齐、饰品的固定以及包包结构的稳固等问题。
不同款式的包包,缝制的工序会有所不同。
缝制完成后,进入加工环节。
加工包括压花、烫金、绣花等工艺。
通过对包包进行各种加工,可以增加包包的质感和美观度。
同时,还可以根据客户需求进行个性化定制,提高包包的附加值。
最后是质检环节。
质检员对生产出来的包包进行检验,确保其外观、尺寸和质量等符合设计要求和相关标准。
只有通过质检合格的包包才能进入下一道工序,否则需要进行返工或报废。
总结起来,包包的生产工艺流程包括设计、裁剪、缝制、加工和质检等环节。
这些环节相互配合,协同作业,确保最终生产出的包包符合市场需求和客户要求。
每一个环节都需要工人们的精细操作和扎实技术,才能制造出高品质的包包产品。
随着科技的进步和生产工艺的不断改进,包包生产工艺也会不断创新和完善,以满足消费者对包包的更高要求。
具生产前期--皮具厂生产流程
具生产前期--皮具厂生产流程一很多客户经常问我:皮具厂到底是怎样生产皮具制品的,想了解一下。
对于这个问题,很多圈内做过皮具的人都知道,但对于没进过皮具厂的人,就肯定不是太清楚了。
一直想写篇文章来和大家分享,但一直苦于没有时间。
难得今天空闲,普飞特皮具厂就在这里向有兴趣的客户朋友们解释一下。
以小皮件为例,如钱包,钥匙包,名片包,卡包,护照包等等,当订单下来以后,皮具厂主要可以分成生产前期工作,生产中期工作和后期工作。
这里先详细介绍生产前期工作。
生产前期工作包括:1.算料。
一个OEM皮具厂,是根据客人实际的订单数量来购买相对应数量的材料的,材料算得越准确,生产后所留下的余料就越少,这样工厂的库存就越少,成本浪费越小。
要购买的主要材料是皮,另外还包括里布,纸皮,胶水,线,边油,五金等一些辅料。
里布,纸皮,胶水,线一般工厂仓库都有库存,五金按照确认板的五金来买或者定做,里布如果客人要求丝印logo则也需要定做。
主要就是要算皮的用量。
皮的用量是通过纸格来计算的,任何一个皮具产品在生产前都会出一套纸格,专业的板房师傅会在纸格的每一个部件上标明这个部件的名称(如大面皮,围皮,页仔,袋皮,包边皮等等),这样测量每一块纸格部件的面积,然后将每个部件的面积相加就得到面积总和。
这个面积总和的单位是平方英尺,英文是sqft,皮具厂都简称“尺”。
但要注意的是,这个面积总和并不是实际的皮用量,原因是一张整皮在切割过程中是存在损耗的,一般真皮小皮件的的损耗在20%至30%.所以,实际需要购买的皮量=面积总和X(1+损耗比例)X订单数量。
比如,一个钥匙包的纸格经计算后面积总和是0.625平方英尺,此钥匙包需要做500个,那么要购买的皮量就是0.625X1.20X500=375SQFT.2.买料。
买料也是一门学问,一个好的皮具厂采购能够帮助皮具厂以尽量少的成本买到质量好且价格也有优势的材料。
具体的我们这里不多说,有一个“尺码”的问题需要解释一下。
箱包检测注意事项
箱包检测注意事项一、箱包生产工艺流程:拌料---->抽板---->吸壳---->切割成型---->打孔---->刷胶---->安装五金及配件---->喷胶---->粘里布及网袋---->裁剪---->缝拉链及皮条---->组合上下盖(上拉头)---->包布(拉链尾部)---->修剪内外部线头---->擦拭箱体表面---->贴标贴---->终检及挂吊牌---->包装二、各流程注意事项及控制方法⒈拌料(重要工序)所需用到的设备拌料机。
注意点:按合同规定的原回料配比进行放料操作,不得出现多放回料和少放新料的情况。
此批产品原回料详细情况如下:1包747S(25kg/包),3包275(25kg/包),3.5包回料(22~26kg),原料约占55%,回料约占45%。
控制方法:如发现拌料工人有不符合要求进行操作时,立即要求工人进行调整,然后在通知供应商相关负责人员。
例:此批产品有发现工人多放了半包回料,我们立即要求工人增加小半包新料进去。
⒉抽板所要用到的设备熔料器,挤出机,转辊机,输送机,剪板机。
注意点:定时关注板材表面,检查板材厚度及尺寸。
此批板材板材规格如下(划线尺寸为抽板时的固定宽度):18寸板材:上盖510X680X2.5下盖510X680X2.721寸板材:上盖560X720X3.0下盖560X720X3.125寸板材:上盖820X680X3.0下盖920X750X3.128寸板材:上盖930X760X3.2下盖980X810X3.4控制方法:时刻关注板材流水线,如发现板材表面有亮斑(这种情况是由于部分点供料不足),立即通知工人进行调节;定时检查板材厚度,如发现有厚度不足的情况,立即通知抽板工进行轧辊调节;检查板材的长宽,误差应在5mm以内,如发现异常尺寸,应检查机器,并将此板做废板处理。
⒊吸壳所要用到的设备吸塑机。
注意点:吸壳时注意壳体外表面有无烫伤,变形,各个定位凸点要清晰。
此批产品需将板材加热到180度才能进行吸塑,吸完固定在模具上冷却时间约在45秒左右。
箱包生产工艺流程
箱包生产工艺流程箱包生产工艺流程主要包括设计、裁剪、缝制、装配和质检等环节。
下面是一个大致的700字的箱包生产工艺流程介绍。
箱包生产是一个复杂而精细的过程,首先,设计师根据市场需求和时尚趋势进行设计,并绘制出样品图。
设计图纸确定后,将进入材料采购阶段。
箱包所需的材料包括面料、衬里、拉链、扣具等。
根据设计需求,选用合适的材料,进行采购。
接下来是裁剪环节。
工人根据设计图纸,将面料和衬里进行裁剪,确保尺寸和形状的准确性。
裁剪完毕后,开始缝制环节。
箱包的缝制一般分为内外缝。
首先,将箱包的翻边部分缝制好,然后将面料一边与衬里一边进行对接缝合。
缝制箱包时,质量控制是非常重要的。
工人需要仔细检查每个缝线的牢固性和整齐度,确保每个针脚都符合制定的标准。
缝制完成后,进行装配环节。
箱包的装配包括拉链、扣具、手柄等部件的安装。
工人需要根据设计要求和标准,细致负责地进行装配。
装配完成后,进行质检。
质检是箱包生产的重要环节。
质检员会对箱包的外观、结实度以及其他功能进行检查。
只有通过质检的箱包才能出厂销售。
质检合格的箱包将进入包装环节。
箱包包装一般使用塑料袋或纸板盒包装。
箱包的包装需要保证箱包的完整性和品质,以及方便运输和销售。
包装完成后,箱包将进行仓库储存,等待运输和销售。
以上是一个大致的箱包生产工艺流程,每个环节都需要精细操作和严格控制质量。
任何一个环节出现问题都会影响到最终产品的品质和市场竞争力。
因此,在生产过程中,箱包厂商需要严格遵守工艺流程,建立科学的质量管理体系,确保产品的品质和市场竞争力。
包的生产工艺流程
包的生产工艺流程
包的生产工艺流程通常包括以下步骤:
1. 材料采购:选择合适的包材料,如纸张、塑料、布料等,并确保材料的质量和供应。
2. 设计和样品制作:根据客户要求或市场需求,设计包的外观和结构,并制作样品以供确认。
3. 切割和裁剪:根据设计要求,将材料进行切割和裁剪,制作出包的各个部分。
4. 印刷和涂层:对包的材料进行印刷和涂层,以增加外观效果和保护功能。
5. 组装和缝制:将各个部分进行组装和缝制,制成成品包。
6. 装配和包装:将包进行装配,如添加拉链、扣子等,然后进行包装,以保护包的完整和外观。
7. 质检和验收:对成品包进行质量检查和验收,确保符合要求。
8. 包装和品牌标识:将包装成品包装好,并贴上品牌标识和价格标签等。
9. 发货和分销:将包装好的产品发货到销售渠道或分销商处,并跟踪销售和库存情况。
10. 售后服务:提供售后服务,如包修理、退换货等,以满足消费者需求。
以上是一般包的生产工艺流程的基本步骤,具体步骤和流程可能会根据不同类型的包和生产工厂的要求而有所变化。
- 1、下载文档前请自行甄别文档内容的完整性,平台不提供额外的编辑、内容补充、找答案等附加服务。
- 2、"仅部分预览"的文档,不可在线预览部分如存在完整性等问题,可反馈申请退款(可完整预览的文档不适用该条件!)。
- 3、如文档侵犯您的权益,请联系客服反馈,我们会尽快为您处理(人工客服工作时间:9:00-18:30)。
1 目的为强化生产过程管理,规范影响生产进度和过程质量各个因素的控制,使生产在受控状态下进行,提高生产效率,提升产品质量。
2 适用范围适用于客户意向锁定后,从订单评审签订开始到成品入库/交付为止整个生产过程控制。
3 职责a) 业务部:订单产品报价成本分析,提供材料(定额)清单,样品制作和确认,签发生产通知单,协调产品发货,销售款项催收结算。
b) 生产部:参与订单评审,审核业务部提交的生产通知单、材料定额,审定工序(工步)流程和工时定额,下达采购指令、生产指令,协调督导采购、车间、设备、检验包装和仓库落实职能工作,按期保质保量完成生产任务。
c) 采购科:根据材料定额和生产部下达的采购指令组织原辅材料的采购,保证质量,按期入库,确保生产用料。
d) 品管科:根据程序执行进料检验、成品检验和出货检验,确保出货产品的品质。
e) 车间:执行生产部下达的周生产进度计划,分解工序,调配生产要素(人员、材料、机台等),组织均衡生产,督导落实制作工艺流程,按期完成生产任务。
f) 仓管组:物料的进库、保管和发放及资材帐务、票证管理。
g) 其他:办公室、财务部按照职能开展工作。
4 业务洽谈和销售合同4.1 业务部销售人员应通过原有的市场网络和电脑网络,多渠道搜集客户需求信息,主动联系,扩大业务触角,争取更多的目标客户。
4.2 客户联络应建立完整记录,对总经理室锁定的目标客户,应保持跟踪联络,及时通报洽谈的进展情况,必要时,应提报总经理室介入洽谈,形成合同意向。
4.3 业务部与客户洽谈合同,应对合同要素(如款式、单价、交货期限、付款办法及质量要等进行认真评审,财务部、生产部应配合成本分析,提供决策依据。
4.4 销售合同应按规定格式拟制,报经总经理室签发。
4.5 合同意向达成(或签订合同)后,业务部应向技术科下达样品制作,并交付客户确认。
确认的主要内容包括包袋的结构样式,布料质地和颜色,装饰件及辅料,外观视觉效果及验收标准。
4.6 样品经客户确认后,业务部应提报总经理室组织合同执行评审,明确采购周期、生产周期和检验包装周期、确定计划交货期,并提供材料(定额)清单。
5 生产计划和生产准备协调工作5.1 销售合同经执行评审后,各部门应按规定期限落实生产准备工作,为车间生产创造良好条件业务部提供材料采购清单及耗用定额,经生产厂长审核,报总经理室审定,交采购科组采购。
5.2 采购科接到审定的材料采购清单后,应分解选择合格(定点)供应商,洽谈(“货比三家,选优择省”)有关采购合同要素(包括材料品种、规格型号、质量要求、单价、交货时间、付款办法等),拟定采购合同,报总经理室批准执行,在计划时间内采购到库。
5.3 业务部应在规定时间内提供指导生产的样品,交付车间生产控制参照。
对有特殊要求的产品,业务部技术科应对提供作业指导文件(或工作联络单)予以明确。
5.4 车间主管应对拟批量投产的产品进行工步分解和工序划分,编制生产工序流程,拟定计件工资工序(工步)单价,报生产部审核。
5.5 生产部在审核计件工资单价时,应控制工序之间的平衡,计件工资总额超过业务部核定的工资成本时,应及时反馈业务部,必要时,应提报总经理室审定。
5.6 车间作业人员原则实行计件工资,必要时,经厂部核定,部分勤杂辅助人员可实行计时工资,但应严格控制编制。
5.7 生产部根据定单合同和车间的实际产能,编制周生产计划,经周例会审定,下达各部门、车间执行。
5.8 因市场客户需要临时紧急插单需要调整生产计划,业务部应提报总经理室组织评审,并对订单的生产顺序提出相应调整方案。
5.9 临时插单一般会影响车间正常生产计划,给车间管理带来一些困难。
但车间管理人员要以公司全局出发,无条件的配合销售业务工作,不得以任何理由拒绝条件执行厂部的计划调整指令,以满足市场客户的需要。
5.10在订单大于产能时,业务部生产应与客户保持良好沟通,争取在交货周期取的客户的支持和谅解,为生产车间创造必要的环境。
5.11各车间根据周生产计划调配人员、材料和机台设备,仓库、机修等保障人员密切配合,保障按期投产。
5.12每天上班,车间管理人员提前10-15分钟上班,下达每个工序人员的“派工单”和加工材料、产成品。
、每天下班前,车间管理人员应根据生产计划产量指标、工序均衡的需要,合理调配作业人员,确定次日每个工序人员的定额产量,填制“派工单”。
6 生产过程控制6.1新订单投料后,车间应对每道工序进行首件确认,确认的内容包括材料质地颜色、样式结构、加工质量和外观效果(参照业务部提供的样品)。
6.2 首件确认由车间主任或组长或半道检牵头组织,本工序作业人员参加,首件确认必须要有记录。
6.3 首件确认发现重大不合格(如材料不良、色差超标、裁减尺寸超差、线的配色不符要求、款式不符及外观重大不良等),应及时纠正合格,方可批量投料生产。
6.4 车间管理人员应按规定程序手续,协调材料申领、材料发放、成品移转的交接点验,保障生产物流顺畅贯通。
6.5 车间管理人员和检验人员应做好巡检,控制过程质量,纠正违章作业和不合格,关键工序应做好转序检验。
6.6 在生产过程中,发现材料不良率或制作不良报废超过规定指标,应及时报告报告厂部组织相关人员评审,提出解决办法。
6.7 车间应把成品送至包检车间,由品管部组织检验。
成品全检必须对送检成品进行逐个、逐项检验。
发现不合格,应标识不合格项目和部位,予以剔除隔离,返回车间责任工序进行返工,并经再次检验合格。
成品必须经全检合格方可包装发货。
6.8 车间管理人员应强化督导隶属人员遵守劳动纪律,做好本岗位的整理整顿,不窜岗、不闲聊、不喧哗、不擅自离岗,自觉维护生产秩序和环境。
作业人员下班,应整理本岗位的卫生,随手关灯、关电扇,切断机台电源。
6.9 车间各工序作业人员应完成“派工单”下达的定额产量和进度,每日下班时,把经车间管理人员签证的“派工单”投进工单箱,作为工资核算的依据。
6.10车间应按厂部下达的日生产指标,未经厂长同意,车间主任不得在未完成日生产指标擅自宣布停产下班。
6.11厂部人员应深入车间,检查生产计划的落实情况,及时协调处理生产现场的出现的缺料、产成品转序堵塞、重大质量不合格及车间与车间之间、车间与部门之间的不协调等问题,控制总体生产节奏,提高效率,按时交货,减低损耗。
7 物流管理7.1 物料采购依据7.1.1 业务部业务员应根据客户提供或确认的样品,对材料厂进行分解,编制材料预算表。
7.1.2 材料预算表中的布料应提供下料的计算尺寸,供核对。
7.1.3材料预算表对应的材料名称/型号规格型号应用意规范(具有唯一识别性),必要时。
应提供材料样品。
7.1.4材料预算表应经专业审核人(暂定厂长)审核,作为采购依据。
7.1.5材料预算表经审核,由业务主管填制单价后,报总经理室备案。
7.1.6生产需要零星物料采购由生产部或车间填制申购单,经厂长审核,100元/批次可直接作为采购依据,超过100元/批次应报总经理室签批。
7.2 材料采购合同7.2.1采购科主办接到《销售合同进度计划评审》表和材料预算表后,对合格(定点)供应商搜索和市场调查,就交货期、单价等要项比较,选择相应供应商。
7.2.2 采购科主办根据材料类别,分别与供应商洽谈合同要素(材料名称、规格型号、数量、单价、交货时间、结算方式、付款办法及材料质量不合格、材料不良品的处理办法等),拟制采购合同,报总经理室批准。
7.2.3 采购合同经总经理室签发后,采购主办应把采购合同和材料清单印发相应部门:采购合同供应商(原)财务部(原)仓库组(复)总经理室(复)采购科(原)材料清单生产部财务部仓管组业务部采购科7.2.4 外购材料到库时,先放置在指定的“待检区”,通知品管科进行进料检验(大宗材料来不及检验,可以先办理入库手续)。
并通知采购组和生产部。
7.2.5 仓管员进行入库点验,应持采购合同(或请购单)与供应商客户提供的随货“发货清单”比较核对,并对实物包装标签进行逐一点收确认(必要时,应进行计量验收)。
7.2.6 采购合同、随货单及实物“三者”相印无误,可直接开具入库单,与送货人签证确认。
“三者”相印出现“不符”,若仅属数量不符,可按实填单入库。
7.2.7 属供应商发错料或重大质量缺陷,应立即通知采购员与供应商联系处理或拒收退货。
7.2.8 仓管员应认真填写“收料单”,对有关要素(如名称、规格型号、数量、单价、到库时间等)应认真审核,字迹清楚,涉及数据的不得擅自涂改。
入库收料单一式四份,分别送供应商、财务部(经采购主办签审)、总经理室和仓库存根。
7.2.9 材料入库后,应在当日进行登帐。
并标识入库单的编号。
7.2.10仓管员应保管好帐本和有关原始票证,定期缴交财务部,作为核算依据和归挡。
7.3 车间生产用料出库7.3.1生产部签发的“生产通知单”,作为仓库备料、发料的依据。
7.3.2发料时,仓管员根据车间的生产进度和“生产通知单”填写“领料单”,标明清楚订单合同编号、材料名称、规格型号、出库时间及出库数量等要素。
材料名称规格要与采购合同的(采购材料清单)对应。
7.3.3出库的材料数量累计未超过“生产通知单”的定额数量,由仓管员与车间领料员直接办理出库交接,车间领料员应在“领料单”签收。
7.3.4车间领料达到“生产通知单”的定额数量后需要“补料”,由车间主任申报,仓管员填写“领料单”,并在单上标识“补料”,交车间主任(或领料员)提报厂长审批,到仓库补料。
订单完成后,仓管员应汇总本订单发生的补料“领料单”提报厂长处理。
7.3.5“领料库”一式三份,仓库(存根)、车间和财务各一份。
7.3.6车间领料出库,仓管员必须在当日登帐。
7.4 车间成品移转检验7.4.1生产车间应完成生产部下达的日定额成品产量计划,按批次(一般装满一车为一批次)及时移转检包车间。
7.4.2生产车间成品由领料员负责移转,与检包车间指定人员点数交接。
成品移转登记表生产车间与检包车间各持一份,相互印证。
7.4.3检包车间对车间送检的成品进行全(逐一逐项)检,剔除不良品,标识不合格项的位置,作为车间返工的依据,并进行不合格品总数统计及返工工序统计。
返工不合格品一般应在该批次检验完毕,接车间新的批次时与车间领料员交接。
7.4.4返工不合格品的交接,品管科应建立“车间返工不合格品交接记录”,标明不合格品的数量、返工工序名称和数量等要素,双方签证确认,作为车间质量指标考核的依据。
车间对品管判定返工的标准有异议,依照检验标准商定,商定不一致,车间应先执行品管科意见,但可持样品提报生产部厂长申诉裁决,必要时,请业务部配合判定。
7.4.5合格成品的数量一定要满足订单的数量。
7.4.6成品必须经全检合格,方可包装装箱。
7.5 外协加工材料出库7.5.1生产部下达的“外协加工协议”和“外协生产通知单”是仓库备料、发料的依据。