1-旋流板塔脱硫除尘系统结构性能的中试研究
旋流板脱硫塔调试说明书

****市发电综合处理厂100t/d锅炉烟气净化系统使用说明书2005-04-01发布2005-05-01实施****##环保设备工程有限公司编制前言随着工业的发展、社会的进步、人民生活水平的不断提高,城市、农村各种垃圾越来越困绕我们着我们的生活,简单的垃圾处理方法已经越来越不能适应社会、经济的发展。
垃圾焚烧技术的发展有效的解决了城市、农村生活垃圾的治理难题,同时副产大量的热能资源用以供热或发电,越来越受到人们的关注,但是垃圾焚烧也会产生大量有毒、有害的气体污染着我们的大气环境。
为治理垃圾焚烧产生的环境污染问题,我国出台了严格的环保标准《生活垃圾焚烧污染控制标准》(GB18485—2001)。
****##环保设备工程有限公司开发的半干法循环悬浮式流化床烟气净化技术由于其一次性投资小、脱硫除尘效率高、干灰利于处理、运行费用低等优点在环保领域得到了广泛的应用。
本项目是****市3×225t/d垃圾焚烧热电工程烟气净化系统工程,由****##环保设备工程有限公司承建,设计中采用了半干法循环悬浮式流化床烟气处理技术。
为使业主更加了解和使用本系统,我们编写了这本使用手册,着重介绍了本装置的设计依据、工艺原理、各子系统的使用方法及工艺指标等内容,可作为业主编写操作规程的依据。
目录第一章环境条件 (1)1.1 地震烈度及气象资料: (1)1.2 公用工程条件: (1)第二章设计范围及条件 (3)2.1 设计范围: (3)2.2 设计条件: (3)2.3性能参数: (4)第三章生产工艺原理 (4)3.1 工艺说明: (5)3.2 脱硫工艺原理: (5)3.3 除尘工艺原理: (7)第四章分系统的使用方法 (9)4.1 净化脱硫系统: (9)4.2 布袋除尘器系统: (11)4.3 石灰输送系统: (13)4.4 石灰给料系统: (14)4.5 流化风系统: (15)4.6 循环灰系统: (17)4.7 外排灰系统: (18)第五章开停车程序 (21)5.1 正常开车步骤: (21)5.2 临时停车: (21)5.3紧急停车: (21)5.4 长期停车: (22)5.5 原始开车操作: (22)第六章工艺指标一览 (24)6.1 压力 (24)6.2温度 (24)6.3其他 (24)第七章异常情况及处理 (25)附录一:工艺流程图附录二:设备一览表第一章环境条件本章内容依据****当地气象局气象资料。
脱硫塔内旋流板流场数值模拟研究

NO.01 2020
节能基础科学
节能 ENERGY CONSERVATION
脱硫塔内旋流板流场数值模拟研究
王耀萱 牛苗任 鞠付栋 聂会建 孙永斌 (中国电力工程顾问集团华北电力设计院有限公司,北京 100120)
摘 要 :对应用于脱硫塔内的标准旋流板进行建模,使用离散相模型对烟气和浆液液滴的气液两相流动进行 数值模拟。研究旋流板的直径、叶片数、重叠率等几何参数和塔内喷淋量等对塔内烟气流动的影响。结果表明, 烟气流过旋流板的压降随叶片数增加而降低,随叶片投影重叠率增加而增大,但增加叶片投影重叠率可避免浆液 过快流过旋流板,增加浆液与烟气的反应面积。旋流板直径对烟气压降影响较小。烟气流动阻力随浆液喷淋层数 增大而显著增大,空塔内烟气以旋转的方式上升至烟气出口,增加喷淋后,浆液液滴阻碍了烟气的横向流动,使 烟气旋转上升的高度降低,最后烟气以竖直向上的方式流动至烟气出口。
限于结构方面的原因,单块旋流板的直径不宜做得
作者简介:王耀萱,博士,工程师,研究方向为火力发电厂 设计。 收稿日期:219-11-19
太大,由于旋流塔板放大后,旋流板开缝增大,离心 力变弱,塔体流态、传热传质规律性变化较大。对于 300 MW等级电厂的脱硫塔,直径一般都在10 m以上。因 此,有必要开发一种大型化旋流板塔,克服旋流塔板放 大后气液接触吸收、传热等效果变差的问题。可将多个 标准型旋流板按矩形或三角形有规律地排列,构成一个 大型化旋流塔板装置,如图1所示。
学 者 们 对 脱 硫 塔 的 空 塔 内 的 数 值 计 算 研 究 较 多, 2007年,过小玲等[3]对600 MW机组装有多孔板的脱硫塔 内空塔和喷淋状态的流场进行了数值模拟,结果表明喷 淋液滴对塔内流场有强烈的整流作用,流场趋于均匀。 2016年,林瑜和陈德珍[4]对4层喷淋层的脱硫塔内烟气流 动进行了数值计算,2018年,马如等[5]以300 MW机组脱 硫塔内流场进行模拟,研究了喷淋塔塔身结构及运行参 数对塔内流场的影响。塔内阻力随着锅炉负荷、喷淋层 数增大而增大。但是对旋流塔板应用于脱硫塔的研究较 少。文中对应用于脱硫塔内的旋流板进行数值模拟,研 究其结构参数对烟气流动的影响。
旋流雾化脱硫塔除尘效果试验

旋流雾化脱硫塔除尘效果试验汇报人:2024-01-10•试验目的•试验设备与方法•试验数据收集与分析目录•结果讨论与优化建议•结论与展望01试验目的分析旋流雾化脱硫塔的除尘原理,探讨其除尘机制和影响因素。
对比旋流雾化脱硫塔与其他脱硫技术的除尘效果,评估其在工业应用中的优势和局限性。
测试旋流雾化脱硫塔在不同工况下的除尘效率,包括入口烟尘浓度、入口烟气流量、液气比等因素对除尘效果的影响。
了解旋流雾化脱硫塔的除尘效果比较不同工况下的除尘效率测试不同入口烟尘浓度下的除尘效率,分析烟尘浓度对除尘效果的影响,为实际应用中控制入口烟尘浓度提供依据。
测试不同入口烟气流量下的除尘效率,分析烟气流量对除尘效果的影响,为实际应用中优化烟气流量提供参考。
测试不同液气比下的除尘效率,分析液气比对除尘效果的影响,为实际应用中选择合适的液气比提供指导。
通过试验数据,评估旋流雾化脱硫塔在各种工况下的性能表现,为实际应用中的选型和优化提供依据。
分析旋流雾化脱硫塔在各种烟气条件下的适应性,为实际应用中处理不同烟气提供参考。
总结试验结果,形成技术报告,为推广和应用旋流雾化脱硫塔提供数据支持和技术参考。
为实际应用提供数据支持02试验设备与方法旋流雾化脱硫塔由塔体、雾化器、喷嘴、除雾器等组成,采用高效旋流雾化技术,使烟气与脱硫浆液充分接触,提高脱硫效率。
通过旋流雾化器将脱硫浆液雾化成微小液滴,与烟气中的SO2发生化学反应,生成硫酸盐,从而达到脱硫目的。
旋流雾化脱硫塔装置介绍工作原理结构特点根据试验需求,搭建适合的试验台架,包括烟气发生装置、旋流雾化脱硫塔、气体流量计、压力计、温度计等。
台架搭建对试验台架进行调试,确保各设备运行正常,数据采集准确可靠。
调试过程试验台架搭建与调试操作流程1. 启动烟气发生装置,调整烟气流量、温度和压力至设定值。
2. 开启旋流雾化脱硫塔,调整雾化器的工作参数。
试验操作流程与注意事项01024. 试验结束后,关闭所有设备,进行数据整理与分析。
一塔脱硫除尘技术方案

1. 引言随着工业化的快速发展,大量的工业废气不仅给环境带来了严重的污染,也对人们的健康造成了威胁。
其中,硫化氢(H2S)和粉尘是一种常见的工业废气污染物。
本文将介绍一种名为“一塔脱硫除尘技术”的方案,该方案能够高效地处理工业废气中的硫化氢和粉尘,从而降低环境污染、保护人们的健康。
2. 工艺原理一塔脱硫除尘技术方案基于湿式废气处理技术,主要包括四个步骤:预处理、脱硫、除尘和废水处理。
2.1 预处理在废气进入处理塔之前,需要进行预处理步骤。
首先,通过一个过滤装置将大颗粒粉尘和杂质从废气中去除。
然后,废气会被加热至一定温度(通常在70-120℃之间),以增加污染物的蒸发速率。
2.2 脱硫进入处理塔的废气首先会与一种被称为“脱硫剂”的化学物质接触。
脱硫剂主要是一种能够与硫化氢发生化学反应的物质,例如氢氧化钠或氢氧化钙。
在脱硫剂的作用下,硫化氢被转化为硫化钠或硫化钙。
脱硫过程中,废气会频繁地与脱硫液体接触,以保证废气中的硫化氢得到彻底的去除。
2.3 除尘一旦废气中的硫化氢被去除,接下来进行的是除尘步骤。
此时,废气通过一个除尘器,其中设有一系列过滤器和除尘器。
这些过滤器和除尘器通过层层过滤机制来去除废气中的微小颗粒和细粉尘。
通常,过滤器和除尘器分别采用不同的材料制成,以满足不同大小颗粒的去除要求。
2.4 废水处理在脱硫和除尘过程中,产生的废水需要经过处理才能排放。
废水处理主要包括固液分离、沉淀和中和等步骤。
在固液分离过程中,废水被过滤以去除废水中的固体颗粒。
然后,将废水与中和剂混合,使其达到酸碱中和,以确保废水的中和度满足排放标准。
最后,通过沉淀步骤将废水中的沉淀物从水中分离出来,使废水得到处理后的净化。
3. 技术优势相比于传统的废气处理技术,一塔脱硫除尘技术具有以下几个优势:•一体化设计:整个处理过程在一个处理塔中完成,占用空间小,简化了处理系统结构。
•高效性能:采用湿式废气处理技术,能够高效地去除废气中的硫化氢和粉尘。
脱硫除尘一体化介绍

脱硫除尘一体化介绍(高效旋流板塔)旋流板塔旋流板塔技术可以实现脱硫、除尘一体化。
塔内的工作机理是针对烟尘成份组成的特征,采用成功的碱液吸收法,经过旋流、喷淋、吸收、吸附、氧化、中和、还原等物理、化学过程,以及脱水、除雾,达到脱硫、除尘、除湿、净化烟气的目的。
1、脱硫原理一般情况下,脱硫是利用二氧化硫的特性,即酸性、氧化性、还原性。
氧化性与还原性是在强氧化剂强还原剂与催化剂的作用下氧化成酸性更强的SO3与还原成原素硫。
一般情况下,利用碱液脱硫时关键应考虑溶解性:SO2溶解于水,但溶解度不大,那么当碱液量一定时,只能靠增大碱液与SO2的接触面积,使SO2溶于水后与碱快速反应生成盐再次溶解SO2,或直接SO2与H2O、碱同时接触反应。
或碱液对SO2进行包溶,那么,在其它条件相同时(如PH值为定值、碱液量相同时)碱液的雾化质量越好、脱硫效率越高。
旋流板塔独特的设计能使高速运动的气流对碱液作激烈的搅拌,产生涡流内循环,重复雾化,使碱液完全雾化,液滴粒径基本在0.2mm以下,达到最佳雾化质量,液雾与SO2充分搅拌在一起,达到最佳的接触方法与接触面积,从而达到理想的脱硫效果。
2、除尘原理烟气自脱硫除尘塔底部切向进入后,绕着底部的稳流柱旋转上升,利用离心力作用除去70%的较大尘粒,然后变速通过三层涡流旋流板。
在这三次大的变速运动中,高速气流对碱液做激烈搅拌使水达到最佳的雾化质量(液滴直径0.2mm),从而使得烟气与碱液达到最大的接触面积(是水膜除尘器中的水与烟气接触面积的200倍以上)。
这样,较大的尘粒在离心力作用下被除去,较小的尘粒受到液滴的碰撞与拦截,受到粒子上的冷凝,受到多次的布朗扩散等作用而凝并成较大的尘粒而被除去,此外,还有部分微小尘粒通过絮流、吸附、聚凝、催化传质后被捕集,最后都流至塔底部再排至沉灰池。
3、原理的独特设计1)旋流板上的碱液基本不下落,在板上做抛物运动;2)该技术能使气液接触面积至最大化,又使气相紊动剧烈,增强了碱性液体对酸性气体的吸收作用;3)独特的用水量设计是利用雾化水量、阻力、烟气温降、三方互益的坐标极限来设计的,使得阻力、温降、用水量都最为合理;4)有效的利用碱液的结垢周期,控制碱液在除尘器内的停留时间,使碱液在除尘器内不结垢。
本文介绍旋流板除尘器

本文介绍旋流板除尘器旋流板塔除尘脱硫一体化装置,简称旋流板除尘器,是一种喷射型塔板洗涤器,关键部件为图1所示旋流塔板。
塔板叶片如固定的风车叶片,气流通过叶片时产生旋转和离心运动,吸收液通过中间盲板均匀分配到个叶片,形成薄液层,与旋转向上的气流形成旋转和离心的效果,喷成细小液滴,甩向塔壁后。
液滴受重力作用集流到集液槽,并通过降液管流到下一塔板的盲板区。
具有一定风压、风速的待处理气流从塔的底部进,上部出。
吸收液从塔的上部进,下部出。
气流与吸收液在塔内作相对运动,并在旋流塔板的构造部位形成很大表面积的水膜,从而大大提高了吸收作用。
每一层的吸收液经旋流离心作用掉入边缘的收集槽,再经导流管进入下一层塔板,开展下一层的吸收作用。
主要机制是尘粒与液滴的惯性碰撞,离心分离和液膜粘附等。
这种塔板由于开孔率较大,允许高速气流通过,因此负荷较高,处理能力较大,压降较低,操作弹性较大。
其气液接触时间较短,适合于气相扩散控制的过程,如气液直接接触传热、快速反应吸收等。
因此脱硫过程中所用的脱硫剂应该是快速反应吸收型的,不适合用碳酸钙等反应速度较慢的脱硫剂。
在烟道入口处设计初级喷淋装置,当烟气经进口烟道,与布置在进口烟道段的喷淋形成的水雾开展传质换热,得到初步降温和去除部分二氧化硫,切向进入吸收塔。
烟气在吸收塔内通过旋流气动装置的加速和旋流,烟尘与经过雾化的吸收液发生碰撞、附着、凝聚、离心分离等综合性的作用,被甩到塔壁,随塔壁水膜流向塔底。
旋流板喷淋塔除尘效率可以到达98.5%以上。
通过旋流气动装置的设置,使烟气在同样高度的筒体内旋转次数增加、通过的路径增长,气相紊动剧烈,烟气与吸收液在时间和空间上得到充分的碰撞、接触、溶解、吸收。
旋流板湿式除尘器工作原理除尘器为圆柱形本体,内装有旋流板。
本除尘器共有4种除尘原理。
一、自激除尘。
当烟气进入除尘器口腔后,冲击水的表面,从而使一些水被分散开,随着水被分散开的过程,开始用水收集粉尘。
北京理工大学科技成果——旋流板湿钙法烟气脱硫除尘技术
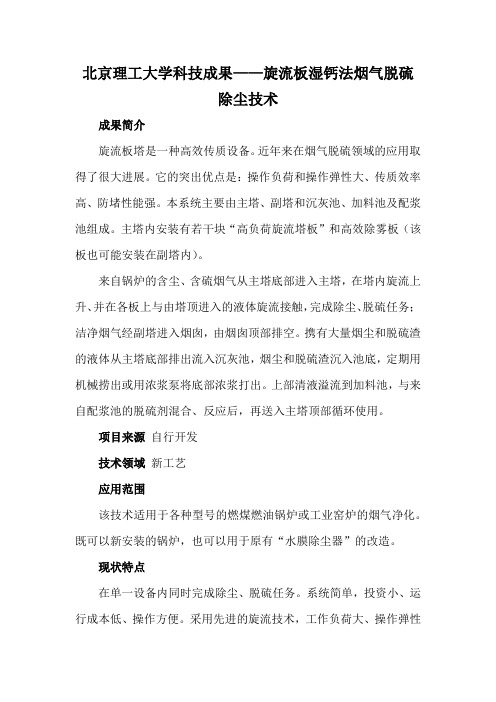
北京理工大学科技成果——旋流板湿钙法烟气脱硫除尘技术成果简介旋流板塔是一种高效传质设备。
近年来在烟气脱硫领域的应用取得了很大进展。
它的突出优点是:操作负荷和操作弹性大、传质效率高、防堵性能强。
本系统主要由主塔、副塔和沉灰池、加料池及配浆池组成。
主塔内安装有若干块“高负荷旋流塔板”和高效除雾板(该板也可能安装在副塔内)。
来自锅炉的含尘、含硫烟气从主塔底部进入主塔,在塔内旋流上升、并在各板上与由塔顶进入的液体旋流接触,完成除尘、脱硫任务;洁净烟气经副塔进入烟囱,由烟囱顶部排空。
携有大量烟尘和脱硫渣的液体从主塔底部排出流入沉灰池,烟尘和脱硫渣沉入池底,定期用机械捞出或用浓浆泵将底部浓浆打出。
上部清液溢流到加料池,与来自配浆池的脱硫剂混合、反应后,再送入主塔顶部循环使用。
项目来源自行开发技术领域新工艺应用范围该技术适用于各种型号的燃煤燃油锅炉或工业窑炉的烟气净化。
既可以新安装的锅炉,也可以用于原有“水膜除尘器”的改造。
现状特点在单一设备内同时完成除尘、脱硫任务。
系统简单,投资小、运行成本低、操作方便。
采用先进的旋流技术,工作负荷大、操作弹性高、防堵防垢性能好、气体阻力小、脱硫效率高。
根据烟气中烟尘和二氧化硫的初始含量,可调整板数,保证达到排放要求。
装配有先进的除雾装置,使洁净烟气带水量小。
可以使用石灰、石灰石和某些工业废料作脱硫剂。
因地制易、就地取材,系统运行费用低。
根据不同的脱硫要求,脱硫除尘塔内流动的液体既可以是溶液、也可以是浆液。
入塔液体由管道直接送入(不需喷头),无喷头堵塞问题,且液体输送阻力小,功耗低。
采用液体全部循环的封闭式操作,无水污染问题。
对“水膜除尘器”改造工程,可完全利用原来的麻石水膜除尘塔、部分利用原来的沉灰池,使改造工程的成本大大下降。
在塔内安装旋流板后,气液接触更充分,除尘效率比原水膜除尘器有明显提高。
所在阶段小规模生产,已在4吨/小时、10吨/小时和130吨/小时锅炉的烟气脱硫除尘中有成功的应用实例,取得了很好的效果。
旋流板塔说明知识讲解

旋流板塔说明旋流板除尘脱硫设备设计说明书一、旋流板塔旋流板塔1974年首次用于碳铵干燥尾气回收以来,已广泛用于中小氮肥厂的半水煤气脱硫(H2S)塔,饱和热水塔,除尘、冷却、冷凝塔等,也用于环保行业脱除烟气和废气中的飞灰、NO x、SO2、H2S及铅汞蒸汽等,取得了很大的经济效益和社会效益,获得1978年全国科学大会奖和1984年国家发明奖。
至90年代,在国家自然科学基金和省自然科学基金的资助下,对旋流塔板上的气液运动,传质效率进行了深入的研究,又获得了化工部1983年科技进步二等奖,国家教委1996年科技进步三等奖。
自80年代后期开始,旋流板塔开始用于烟气的脱硫除尘研究,在实验室和小型锅炉的工业化实验中,重点在除尘,脱硫,除雾和脱硫剂及工程性问题进行了研究。
旋流板塔脱硫技术作为一种实用可靠的脱硫除尘技术,具有投资和运行费用低,占地面积小,管理和维护方便等特点,现已推广用于火电,热电,冶金等行业的烟气脱硫除尘和其他工业废气治理。
我公司选用运用湿法一体化脱硫除尘的旋流板麻石除尘器,依据多年生产经验进行的多次技术改进,不断改善其脱硫除尘效率,解决多个湿式脱硫除尘常见技术难题,在高效性、经济性、实用性等方面有显著突破,我厂生产的旋流板除尘器脱硫效率可达90%以上,除尘效率在98%以上,其中高配置不锈钢旋流板麻石除尘器除尘效率可达99.5%以上,在大型锅炉及煤窑等工业废气的处理上、在0.1µm到300µm粒径范围内能有效除尘,效率接近电除尘、布袋除尘等传统高效除尘器。
在设计上突出旋流塔板脱硫除尘技术高效、低阻的传质特性,结合最成熟的湿法脱硫工艺,大大提高脱硫效率,已成功应用于120t/h燃煤大中型锅炉脱硫除尘项目。
二、主要工作原理及技术特点旋流板塔通常为圆柱塔体,塔内装有旋流塔板。
工作时,烟气由塔底向上流动,由于切向进塔,尤其是塔板叶片的导向作用而使烟气旋转上升,使在塔板上将逐板下流的液体喷成雾滴,使气液间有很大的接触面积;液滴被气流带动旋转,产生的离心力强化气夜间的接触,最后甩到塔壁上沿壁下流到下一层塔板上,再次被气流雾化而进行气液接触。
- 1、下载文档前请自行甄别文档内容的完整性,平台不提供额外的编辑、内容补充、找答案等附加服务。
- 2、"仅部分预览"的文档,不可在线预览部分如存在完整性等问题,可反馈申请退款(可完整预览的文档不适用该条件!)。
- 3、如文档侵犯您的权益,请联系客服反馈,我们会尽快为您处理(人工客服工作时间:9:00-18:30)。
旋流板塔脱硫除尘系统结构性能的中试研究Experimental research on swirl board scrubber of an integrated system of desulfurization and precipitation饶应福,陈云,白冰(中国矿业大学环境与测绘学院,江苏徐州 221008)摘要:利用实验室建立的旋流板塔脱硫除尘中试系统开展了各种结构参数对系统阻力损失的影响研究,为系统的放大设计提供了实验依据。
关键词:脱硫除尘;旋流板塔;阻力损失Abstract :The influence of various construction parameters on system re sistance is studied in a model swirl board scrub 2ber.I t can be served a s a fundation for a prototype scale de sign.K ey words :de sulfurization and precipitation integration ;swirl board scrubber ;re sistance lo ss中图分类号:X 701.3 文献标识码:B 文章编号:1009-4032(2003)03-0024-03 浙江大学发明的旋流板塔除尘脱硫系统具有负荷高、压降低、不易堵、弹性宽等优点,综合性能优于国内外普遍使用的湿法脱硫除尘器。
为此,我们建立了旋流板塔除尘脱硫工艺模型,并进行了研究。
1 实验装置脱硫除尘实验装置见图1。
1-集气罩;2-粉尘添加机构;3-S O 2供气系统;4-进风管;5-脱硫塔体;6-塔体支撑结构;7-引风管;8-引风机;9-烟囱;10-氧化池;11-调节池;12-加药箱;13-污泥泵;14-供水流量计;15-调节阀;16-塔板测试孔;17-旋流板;18-除雾板;19-进风管测试孔;20-引风管测试孔图1 脱硫除尘实验装置工艺流程实验工艺系统主要由以下几部分组成:(1)S O 2配制系统。
包括S O 2钢瓶、不锈钢减压阀、空气流量计、气体连通管;(2)气路系统。
包括气体进风管、脱硫塔体(旋流板塔体和湍球塔体)、气体引风管、风机、烟囱;(3)水系统。
由调节池、氧化池、污泥泵、塔体供水管、控制阀门、加药箱组成。
(4)其他附属结构。
包括电路系统、支撑结构和测试系统。
该工艺主体设备是直径300mm 的旋流板吸收塔,内装3块旋流塔板和1块除雾板。
烟气从集气罩通过进风管进入塔体,在塔内旋转上升,并与自上而下的浆液逆流接触,脱硫后的气体由引风机从引风管抽出,并沿烟囱排出;调节池中的脱硫剂液体被泵送入塔内,与烟气逆流接触后从塔底排入氧化池,再循环利用。
在旋流板塔内,气体通过塔板螺旋上升,液体沿盲板流动到叶片上形成液层,之后被气体旋转喷洒成液滴,摔到塔壁形成沿壁旋转的液环,从降流装置流到下块板。
高速旋转的液滴与气流接触充分,传质效率高,从而达到提高除尘效率的目的。
2 实验结果与讨论2.1 干态、湿态实验条件下系统阻力损失分析用微压计和皮托管压力计分别测量了实验系统干、湿态运行时各测点动压和静压,结果见表1。
表1数据表明:脱硫除尘系统的阻力损失主要分布在3个部分:进口烟道、塔体和出口烟道。
进、出口烟道的阻力损失是烟道内壁产生的摩擦阻力损失和渐扩、渐缩、变道等产生的阻力损失之和。
这些阻力损失基本上不会随操作条件的改变有大的变化。
干态比湿态时的阻力损失高,主要是因为在湿态操作条件下,烟气的含湿量大,对管壁具有润湿作422003年9月 电 力 环 境 保 护 第19卷 第3期用,使管壁的阻力损失系数减小,导致进、出口烟道的摩擦阻力减小;实际值比理论值大,这是由于施工过程中,烟道没有按设计要求选材而产生的,但是不会对系统的运行产生影响。
系统的主要阻力损失在塔体部分;3块捕集板上的阻力损失比设计值小,而除雾板上的阻力损失出现突变现象。
系统设计过程中,为了研究除雾板的除雾效果和阻力损失,设计了不同的除雾板,当捕集板采用外向型塔板而除雾板采用内向型塔板时,烟气的流态在除雾板上发生突变,造成塔板阻力损失骤然增大。
因此,在设计过程中,除了要考虑除雾板的除雾效果外,还要考虑捕集板上的烟气流态与除雾板之间的匹配。
否则易出现风机抽力不足的问题。
表1 干、湿态运行状况下各结构的阻力损失Pa项 目进口总阻力损失第1块塔板阻力损失第2块塔板阻力损失第3块塔板阻力损失除雾板阻力损失出口总阻力损失实际值(干态)1404575100250285理论值(干态)106.5728012774237.9实际值(湿态)11592172185250232理论值(湿态)106.516817922574237.92.2 塔板叶片倾斜角对塔板阻力损失的影响从上面的分析可知:系统的主要阻力损失在塔板上,而且可以通过设计和操作进行控制。
因此,制作了4种倾斜角(15°、20°、25°、30°)的塔板,塔板叶片数为12。
将4种塔板分别安装在系统上,测试塔板上的阻力损失,计算塔板的理论阻力损失。
干板阻力系数和湿板阻力系数分别取ζ干=1.0、ζ湿=1.5。
测试结果如图2所示。
图2 倾斜角对塔板阻力损失影响叶片倾斜角主要影响到塔板的穿孔面积,倾斜角增大,穿孔面积相应增大,而动能因子和穿孔气速相应减小。
在系统烟气量和塔板结构尺寸一定的情况下,塔板的空隙率决定了塔板的穿孔气速,塔板上的阻力损失主要是烟气通过塔板时机械运动所造成的压力损失,因此,阻力损失由塔板穿孔气速决定。
我们利用动能穿孔因子来表示穿孔气速,采用半经验公式计算塔板阻力损失。
ΔP 干=ζ干F 0212g(1)ΔP 湿=ζ湿F 0212g+3.6F 0V +4(2)F 0=v 0γ(3)v =2.78L A y(4)式中F 0为动能穿孔因子,v 0为塔板穿孔气速,v 为溢流孔的溢流速度,L 为水系统供液量,A y 为溢流孔面积,γ为烟气重度,ζ干为干板时塔板阻力系数,ζ干=0.8~1.2,ζ湿为湿板时塔板阻力系数,ζ湿=1.4~1.7。
图2体现了干板和湿板条件下,塔板阻力损失的实测值和理论值之间的关系。
从图中我们可以发现:实测值与理论值符合较好,理论值比实测值稍大,误差在10%之内,说明理论计算的半经验公式能比较好地反映塔板阻力损失。
从塔板结构来分析:影响干板阻力的因素主要是塔板的穿孔面积,我们探讨的主要目标是如何控制塔板穿孔面积,在满足脱硫除尘的同时,尽可能减少阻力损失。
测试结果为:叶片倾斜角为15°时,干板阻力损失为225Pa ,522003年 饶应福等:旋流板塔脱硫除尘系统结构性能的中试研究 第3期湿板为333Pa ,这说明塔板倾斜角小,塔板的穿孔面积也小,塔板的穿孔气速迅速增大,塔板的穿孔动能因子达19。
塔板的阻力损失主要为干板阻力损失,设计时应优化塔板倾斜角以控制塔板上的干板阻力损失(塔板结构阻力损失)。
脱硫除尘过程要求塔板上必须保持一定的液体负荷,气体通过液层形成气泡和液体雾滴,有利于气液交换和粉尘的捕集。
因此,塔板上必须保证一定的穿孔气速,穿孔气速太小,液体受重力作用容易从塔板叶片间漏出,不能形成液层,对脱硫除尘极为不利。
我们在试验中发现,当塔板倾斜角大于30°时,塔板的穿孔动能因子小于9,塔板出现漏液现象,塔板上的湿板阻力损失几乎与干板阻力损失相等。
此现象说明塔板基本上没有液体负荷,塔板对气液交换没有起到什么作用,这是在设计中应该避免的。
从试验情况来看,塔板设计的叶片倾斜角应控制在20°~25°较合适,确定值可以根据系统风压进行调节。
2.3 叶片数对塔板阻力损失的影响分析本研究设计制作了3种叶片数塔板,叶片数分别为8、12、16,叶片的倾斜角为25°,测试这3种塔板的干板、湿板阻力损失,结果见图3。
图3 叶片数与阻力损失的关系 从图3可以看出:叶片数的增加对塔板的穿孔面积、穿孔动能因子和穿孔气速影响不大,干板的阻力损失实测值都小于理论值,其中叶片数为8时,塔板的干板阻力损失仅为45Pa ,说明当叶片数偏少时,对塔板中气体的运动状态有较大影响,原因在于塔板间叶片太少时,气体不能完全旋转起来,部分气流不受塔板结构的作用,阻力系数比旋转气流阻力系数小,因此塔板上的阻力损失比理论计算值小。
同时,湿板的阻力损失仅为理论值的1/2,表明由于叶片数少,叶片之间的间距太大,在叶片间出现漏液现象,造成塔板上的液体负荷减小,从而出现塔板上的阻力损失锐减的现象。
叶片数为16时,湿板的阻力损失高达315Pa ,几乎是理论值的2倍。
这是由于湿板阻力损失主要是液体负荷造成的,叶片数增加对穿孔气速影响不大,使得液体容易在叶片表面大量积存,造成穿孔面积减小,增大塔板的阻力损失。
叶片数多,塔板上的液体负荷大,但是大量的液体在塔板表面积存,并不能起到气液交换和对固体颗粒的捕集作用,对塔设备的脱硫除尘效率影响不大。
所以,旋流板叶片数并不是越多越好。
尽管对塔板的穿孔面积影响不大,理论计算的塔板阻力损失看似合理,其实,运行的实际阻力损失要远大于设计值,因此,在设计时,要慎重选取叶片数。
2.4 液体负荷对阻力损失的影响在试验过程中,我们通过调节水系统的供水量来控制液气比,并观察塔板上液气比对塔板阻力损失的影响。
图4反映了叶片数为12,倾斜角为25°的塔板阻力损失。
图4 液气比对塔板阻力损失的影响塔板上的液体负荷主要是通过塔板溢流口来控制。
从式(2)可知:湿板阻力损失是由干板阻力损失和液体负荷造成的阻力损失两部分组成,其中液体负荷部分的阻力损失与溢流口液速成正比。
从图4可以看到:塔板阻力损失的理论值基本上是一条直线,但实际值与它并不完全符合,在液气比较小时,两者基本一致,但当液气比增大到1.5以上时,塔板上的阻力损失实际上没有什么增加。
这是因为液气比增大,塔板上的液体负荷也相应增大,溢流口降液可以减少液体负荷,但当塔板上的液体负荷增加到一定量后,液体不仅从溢流口漏出,同时由于重力作用,部分液体从塔板的叶片间降落,而出现液气比增大,而塔板阻力损失并没有相应增大的(下转第30页)为1.5%时,假设其他运行工况保持不变,煤燃烧后烟道中S O 3体积分数为26.3×10-6,分别对应于H 2O -H 2S O 4两相状态图(如图2所示)中S O 3冷凝露点线的A 、B 两点,其差值为17.5×10-6,与H 2S O 4溶液沸腾曲线分别交于C 、D 两点,即为冷凝后硫酸溶液的浓度。
从图2可以看出,煤的硫分越高,烟气中S O 3浓度越高,则酸露点温度越高,越容易造成腐蚀。