机械加工质量及其检测
机械加工车间产品质量检验

机械加工车间产品质量检验机械加工车间是制造业中一个至关重要的环节,而产品质量则是确保企业竞争力和声誉的重要指标。
在这个机械加工车间中,产品质量检验是一个不可或缺的环节,它能够确保所生产的产品符合规定的标准,并达到客户的要求和期望。
本文将探讨机械加工车间产品质量检验的重要性、常用的检验方法以及如何改进和优化检验流程。
一、产品质量检验的重要性机械加工车间生产的产品涵盖了各种行业和领域,如汽车、航空航天、电子设备等。
而这些产品的质量直接关系到用户的安全、产品的可靠性以及企业的声誉。
因此,在机械加工车间进行产品质量检验是至关重要的。
1.1 确保产品符合标准产品质量检验能够确保所生产的产品符合国家和行业的标准要求。
这包括产品的外观、尺寸、材料、性能等各个方面。
通过对产品进行全面检测,可以及时发现和解决产品存在的质量问题,防止不合格产品流入市场,保障用户的权益。
1.2 提高产品可靠性产品质量检验可以帮助机械加工车间发现产品存在的潜在问题,并及时进行修复和调整,从而提高产品的可靠性和使用寿命。
只有通过对产品的全面检验,确保产品达到设计和制造要求,才能够保证产品在使用过程中不会出现故障和损坏,提高产品的可靠性和稳定性。
1.3 建立企业声誉优质的产品品质是企业赢得市场和用户信任的基础。
通过对产品进行质量检验,可以确保产品的一致性和稳定性,提升企业的声誉和形象。
而企业的声誉将直接影响到企业的竞争力和市场地位,对于机械加工车间来说,保证产品质量是维护企业良好声誉的关键。
二、常用的产品质量检验方法在机械加工车间进行产品质量检验时,常用的方法有多种,包括外观检查、尺寸检测、材料分析、性能测试等。
下面将介绍其中几种常用的检验方法。
2.1 外观检查外观检查是最基本也是最常见的一种检验方法。
通过对产品的外观进行检查,判断产品是否存在表面缺陷、划痕、氧化等问题,以及外观是否满足设计和美观要求。
外观检查可以使用人工目视和辅助设备(如显微镜、相机等)进行,通过对产品进行仔细观察和比对,以保证产品的外观质量。
机械类质量标准“三检、三按”ppt

三、主要内容
1.零部件首件检查
• • • •
• 1.1下列情况必须进行首件检查 1.1.1操作者每个生产班次加工的第一个零件。 对工艺能保证质量的,已连续生产一个班以上的 可以不必每 班做首件检查(特殊情况单位可自行规定)。 1.1.2加工过程中换工、换料、换活加工的第一个零件。 1.1.3改变工艺参数和加工方法(如更换机床,改变零件 的装卡,改变加工部位等)加工出的第一个零件。 1.1.4在调整修理后的设备上加工出的第一个零件。
•
• •
•
•
•
• 2.4 a)工序检查员或操作者发现上道工序或毛料等非本单 位责任的不合格品,由车间通知责任单位认可后,工序检查员 按《不合格品控制程序》进行处置,意见不一致时,由质检科 判决生效。 • b)若粗加工中发现毛料及热处理缺陷,操作者及工序检查员 应及时反馈,待粗加工完毕后,所暴露的问题由责任单位一并 处理。 • c)生产过程中,对上道工序发生的问题,下道工序应该发现, 但未反映继续加工的: • 1)产品本来可以采取措施挽救,因继续加工造成的不合格品, 由加工单位(或下道工序)承担50%的责任; • 2)废品发生工序以后所产生的工时无效。 • 2.5跨车间的质量问题,责任单位必须在半天之内拿出解决 方案并实施,否则,在产单位检查员开具废品票,不再冲票。 • 2.6工序检查员要随时填写工序检查记录 。
1.2 首件检查项目:
• 1.2.1加工的零件与零件生产进程单上的产品图号、名称、 材料、规格是否一致;上下工序的衔接是否符合工艺文件;代 料票是否有技术人员的签字;临时工艺有技术人员的签字认可。 • 1.2.2 加工零件的尺寸、形位公差、表面粗糙度等与产品 图纸、工艺、标准等技术文件的要求是否一致,综合检查零件 是否合格。
机械零件加工质量检验技术研究

机械零件加工质量检验技术研究摘要:在机械生产中,大部分机械零件都是批量生产的产品,在技术、环境等因素的作用下,很容易出现质量问题,所以要想进一步提升机械零件质量,就要加强机械零件加工质量检验工作。
机械零件加工质量检验内容机械零件的长度、角度及表面粗糙程度等测量,在这个过程中,需要应用专业的检测技术,同时,还需要完善相应的管理制度,以便于及时的发现零件缺陷,消除机械运行风险。
下文对此进行简要的阐述。
关键词:机械零件;质量检验;技术要点;控制策略一、机械零件加工质量检验技术要点(一)感觉检验法这种方法的一些精度较高的零件检验当中并不适用,同时对于检验人员自身也有着较高的标准和要求。
如果工作人员的经验较为丰富,那么检验结果的准确性就较高。
但如果工作人员的经验不够丰富,在运用这种方法后,检验的结果就无法得到保障。
所以这种检验的方式只能作为定性检验与鉴定的一种方法进行应用。
通常感觉检验法主要包括三种类型,第一种是目测法,就是通过肉眼或是利用放大镜对机械零件进行观察,这样就能够对零件的磨损破坏程度进行确定,如果零件有明显的变形,裂纹或是疲劳脱落则可以通过这种方法进行观察。
第二种是触觉法,即通过工作人员的手触摸零件表面一次进行判断,这种方法能够根据零件表面磨损痕迹的深浅度,对磨损的情况进行大致判断。
如果零件是刚进入工作状态,通过手就可以感受到零件的温度,这样就能对零件的具体工作情况进行评判。
第三种则是耳听法,也就是工作人员通过敲击或是零件工作过程中所发出的声音,对零件的实际运行状况进行评判。
如果对零件敲击时所发出的声音较为清脆,那么零件就不存在缺陷,如果声音较为沉闷,零件就有可能存在沙眼或是裂纹的情况。
在具体的应用中,工作人员也可凭借自身的工作经验,选择相应的感觉检验法对零件的质量进行检验及鉴定。
(二)仪器检验法在应用这种检验方法时,需要工作人员具备一定的技术操作能力,同时对于相关的检验工具也要有详细的了解,否则工作人员就无法操作相关的检验设备及器械。
机械加工质量控制

机械加工质量控制一、引言机械加工质量控制是指在机械加工过程中对产品质量进行控制和管理的一系列措施。
它涉及到材料的选择、加工工艺的确定、设备的选择和调试以及成品的检测等环节。
本文将详细介绍机械加工质量控制的标准格式,以及其中涉及的各个环节的要求和控制方法。
二、材料的选择1. 材料的性能要求根据产品的使用环境和要求,选择具有合适机械性能、化学性能和物理性能的材料。
例如,对于耐磨件,应选择具有较高硬度和耐磨性的材料;对于耐腐蚀件,应选择具有良好耐腐蚀性的材料。
2. 材料的检测方法在材料进厂时,应进行材料的检测,以确保材料的质量符合要求。
常用的检测方法包括化学成分分析、金相组织分析、机械性能测试等。
三、加工工艺的确定1. 加工工艺的选择根据产品的形状、尺寸和要求,选择合适的加工工艺。
常用的加工工艺包括车削、铣削、钻削、磨削等。
2. 加工工艺的编写编写加工工艺流程,明确每个工序的要求和参数。
流程中应包括加工顺序、刀具的选择、切削速度、进给量、切削深度等。
四、设备的选择和调试1. 设备的选择根据产品的形状、尺寸和要求,选择适合的加工设备。
设备应具备稳定性好、精度高、刚性强等特点。
2. 设备的调试设备调试是确保机械加工质量的重要环节。
调试时应检查设备的各项参数是否符合要求,如刀具的安装是否正确、切削液的供给是否稳定等。
五、成品的检测1. 检测方法的选择根据产品的要求,选择合适的检测方法。
常用的检测方法包括三坐标测量、硬度测试、表面粗糙度测试等。
2. 检测标准的制定根据产品的要求和标准,制定相应的检测标准。
标准中应包括尺寸偏差、形状偏差、表面质量等指标。
六、质量控制的记录和分析1. 质量记录的要求在机械加工过程中,应及时记录各个环节的质量参数和检测结果。
记录应包括日期、操作人员、设备参数、加工工艺、检测结果等。
2. 质量分析的方法根据质量记录,进行质量分析,找出产生质量问题的原因,并采取相应的措施进行改进。
常用的质量分析方法包括鱼骨图、因果图、直方图等。
机械加工质量控制标准

机械加工质量控制标准在机械制造领域中,机械零部件的质量是至关重要的。
为了确保机械零部件的加工质量,我们需要遵守一定的标准和规范。
本文将介绍机械加工质量控制标准。
一、加工质量要求机械零部件的加工质量要求包括尺寸精度、形位公差、表面质量等方面的要求。
在进行加工之前,需要明确零部件的加工质量要求,并在加工过程中严格控制,以保证最终产品的质量。
1. 尺寸精度尺寸精度是衡量机械零部件加工质量的重要指标之一。
尺寸精度一般分为公差等级,根据零部件的实际要求选择适当的公差等级。
加工过程中需采用合适的加工工艺和设备,保证尺寸精度的达到要求。
2. 形位公差形位公差是衡量机械零部件几何形状和位置精度的指标。
对于要求较高的零部件,需要在制定工艺方案和选择设备时考虑形位公差的控制。
在加工过程中,应严格按照设计要求进行加工,保证形位公差的控制。
3. 表面质量零部件的表面质量对于产品的整体外观和性能有较大的影响。
在机械加工过程中,应注重工艺操作的细节,控制好加工参数和刀具状况,保证零部件的表面光洁度和无明显缺陷。
二、加工工艺要求机械加工工艺是保证零部件加工质量的重要环节。
在加工过程中,应根据零部件的具体要求和材料特性,合理选择加工工艺和设备,并制定相应的操作规程。
1. 工艺路线在制定加工工艺时,需要明确每道工序的加工内容和顺序。
合理的工艺路线可以最大程度地减少加工扭曲和变形,提高零部件的加工精度。
2. 加工方法不同的零部件可能采用不同的加工方法,如车削、铣削、钻削、磨削等。
选择合适的加工方法需要考虑加工效率和加工质量的平衡,确保加工过程中的稳定性和准确性。
3. 刀具选择刀具是机械加工中不可或缺的工具,合适的刀具选择能够有效地提高加工质量。
在选择刀具时,需要考虑加工材料的硬度、表面光洁度等因素,并结合具体的加工操作进行选用。
三、设备要求机械加工设备对于加工质量的控制至关重要。
高精度、稳定性好的设备能够提供良好的加工基础,保证零部件加工质量的稳定性和可靠性。
机械加工件检测标准

机械加工件检测标准1、目的:通过严格执行三检,“首件检验”、“巡回检验”、“完工检验”将检验工件与工序控制紧密结合,对每一工序的质量问题或可能出现的质量问题不放过,不合格品不能转入下工序,从而提高产品质量。
2、适用范围:所有加工件3.检验原则3.1.检验人员必须具有一定的专业知识和实际工作经验,且能满足现行产品对检验工作的各项要求。
3.2.检验人员所用的计量器具必须是经计量部门校验合格并在规定周期内。
3.3.检验人员验收产品前应熟读相关图样和技术文件,了解零件的关键尺寸及装配关系要点。
3.4 检验人员必须严格按照图样和技术文件所规定的要求对零件进行判定。
4.检验依据检测依据按图纸及工艺卡检测5.检测种类:“工序自检”“首件检验”、“巡回检验”、“完工检验”5.1.工序自检:工件完成工序后进行自检,自检合格后在工艺卡进行签字;5.2.首件检验:批量工件必须首件检验后,才能开始加工5.2.1.对首件,根据加工工艺要求,核实首件产品或工件(毛坯)产品的质量特性是否符合要求。
对首批检查的工件,操作者必须做好自检,在操作者缺乏检测手段时,也应对工件外观质量自检,合格后送质量专员检查。
无论在任何情况下,首件检验未经检验合格,不得进行批量生产或继续加工作业。
5.2.2.工作班开始加工的第一个工件;5.2.3.调换操作者后加工的第一个工件;5.2.4. 更换(调整)工艺装备或更换模具后加工的第一个工件;5.2.5.更换材料批(炉)号后加工的第一个工件;5.2.6. 代用材料后加工的第一个工件;5.2.7.检验内容:根据检验标准的要求,核对首件产品的质量特性值是否真正符合要求;对首件检验合格,批准生产加工,首件检验不合格,进行不合格品的处理,同时分析不合格原因,采取改进措施后加工,产品继续首件检验,直至合格为止。
5.3.巡回检验:5.3.1.由检验人员在生产现场,进行日常巡回监督检查,重点监控工序质量和典型零件质量;5.3.2根据检验标准、图纸和工艺的要求、检验、核对巡检产品的质量特性值是否真正符合要求;5.3.3.若巡检某质量特性值不合格,应按《不合格品报告单》处理,同时。
机械加工质量控制与检测PPT课件
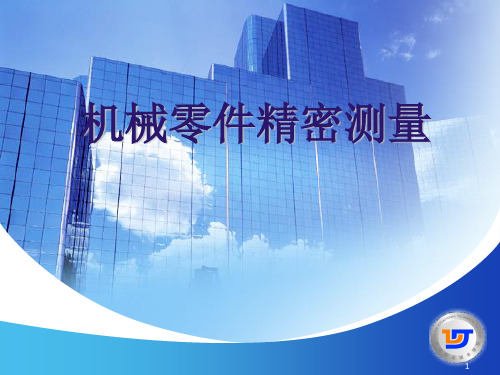
❖ 质量控制的重点:工艺过程的正确性、 操作者的技能和经验
大连职业技术学院
4
绪论
例如:加工有色金属右旋梯形 螺纹螺母时,表面粗糙度达不 到要求?
关键
学习如何在加工过程中 实施质量“控制”
大连职业技术学院
5
绪论
(二)检测 ❖目的:量具、仪器或专用检具对加工好
的零件进行检测、比较,得到误 差值或判断其是否符合质量要求 的过程
❖ 检测方法:
检测原理
复杂的计算
查表
经验公式
❖掌握各种精度指标项目的定义—获得检测原 理—确定检测方法—选取相应的量具及辅助 工具—获取正确的误差值—数据分析处理— 得出检测结论—对工艺过程进行指导
大连职业技术学院
6
目录
1
加工质量控制基础
2
检测技术基础
3
几何量误差检测
4
各类毛坯的检测
5 典型零件加工质量控制与检测
直线度 形
状 平面度
无
平行度
有
定
位
垂直度
有
无
向 倾斜度
有
公 圆度 差 圆柱度
形状 或位 置公
差
线轮廓 度
面轮廓 度
无 无 有或无 有或无
置
位置度
定 同轴度
公 位 对称度
圆跳动
差跳 动 全跳动
有或无 有 有 有 有
13
1.1 零件的使用性能与加工质量
1.1.2零件加工质量
(二)表面质量的概念 1、表面层的几何形状
表面粗糙度:表面微观几何形状误差,其波长与波高的比值在 L1/H1<40的范围内,波距<1mm。由刀刃切削后形成。 表面波度:介于加工精度(宏观几何形状误差L3/H3 = 1000)和表 面粗糙度间的一种带有周期性的几何形状误差,其波长与波高的比值 在40<L2/H2<1000的范围,波距=1~10mm。由工艺系统的振动引起。 纹理方向: 表面刀纹的方向,它取决于表面形成过程中所采用的 机械加工方法。 伤痕:加工表面上一些个别位置上出现的缺陷。例如:砂眼、气孔、 裂痕等。
机械零件的加工精度检测与控制
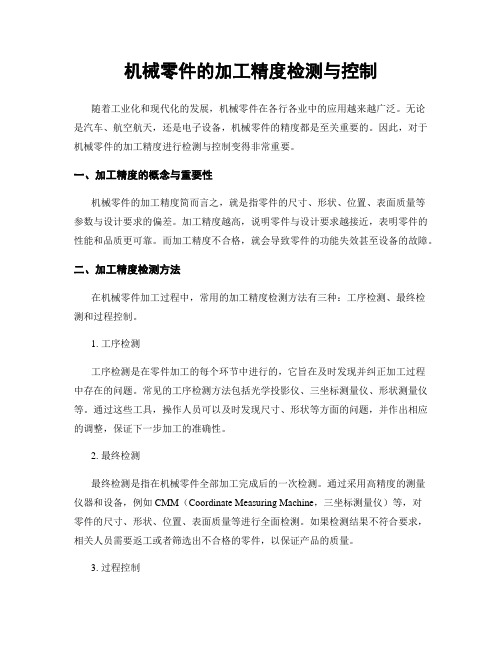
机械零件的加工精度检测与控制随着工业化和现代化的发展,机械零件在各行各业中的应用越来越广泛。
无论是汽车、航空航天,还是电子设备,机械零件的精度都是至关重要的。
因此,对于机械零件的加工精度进行检测与控制变得非常重要。
一、加工精度的概念与重要性机械零件的加工精度简而言之,就是指零件的尺寸、形状、位置、表面质量等参数与设计要求的偏差。
加工精度越高,说明零件与设计要求越接近,表明零件的性能和品质更可靠。
而加工精度不合格,就会导致零件的功能失效甚至设备的故障。
二、加工精度检测方法在机械零件加工过程中,常用的加工精度检测方法有三种:工序检测、最终检测和过程控制。
1. 工序检测工序检测是在零件加工的每个环节中进行的,它旨在及时发现并纠正加工过程中存在的问题。
常见的工序检测方法包括光学投影仪、三坐标测量仪、形状测量仪等。
通过这些工具,操作人员可以及时发现尺寸、形状等方面的问题,并作出相应的调整,保证下一步加工的准确性。
2. 最终检测最终检测是指在机械零件全部加工完成后的一次检测。
通过采用高精度的测量仪器和设备,例如CMM(Coordinate Measuring Machine,三坐标测量仪)等,对零件的尺寸、形状、位置、表面质量等进行全面检测。
如果检测结果不符合要求,相关人员需要返工或者筛选出不合格的零件,以保证产品的质量。
3. 过程控制在机械零件加工的整个过程中,通过控制加工设备的参数和监测加工过程中的数据,可以实现对加工精度的控制。
例如,通过对切削力、切削转速、进给速度等参数的实时监测和控制,可以及时调整加工过程中的问题,提高零件的加工精度。
三、加工精度控制的现状与挑战虽然加工精度检测与控制在现代工业中已经得到广泛应用,但仍面临一些挑战。
1. 多种零件加工不同的机械零件具有不同的形状、材料和制造要求,因此对于不同的零件,需要采用不同的加工精度检测与控制方法。
如何在不同的加工环境中选择合适的检测与控制方法,是一个需要技术人员深入研究的问题。
- 1、下载文档前请自行甄别文档内容的完整性,平台不提供额外的编辑、内容补充、找答案等附加服务。
- 2、"仅部分预览"的文档,不可在线预览部分如存在完整性等问题,可反馈申请退款(可完整预览的文档不适用该条件!)。
- 3、如文档侵犯您的权益,请联系客服反馈,我们会尽快为您处理(人工客服工作时间:9:00-18:30)。
3
获得加工精度的方法
获得尺寸精度的方法有4种、 试切法、调整法、定尺寸刀具法、主动测量法。 获得形状精度的方法有3种 轨迹法、成形法、展成法。 获得位置精度的方法有2种 划线找正:按照零件图在毛坯上划线。 夹具保证:夹具以正确的位置安装在机床上,工 件按照六点定位原理在夹具中定位并夹紧,工件 的位置精度完全由夹具来保证。
15
精密加工和超精密加工
精密加工和超精密加工有6个特点: 创造性原则:原有的机床已不能满足加工零件的精度要求, 需研制专门的超精密机床或通过工艺手段达到 微量切除:对机床精度有很高要求。 综合制造工艺系统:是一个系统工程,复杂且难度大。 精密特种加工和复合加工方法:例如精密电火花加工、激 光加工、电子束加工、离子束加工等。 自动化程度高。 加工检测一体化:不仅进行离线检测、而且可以采用在位 检测、在线检测和误差检测,以提高检测精度。
9
影响因素及改进措施
影响因素:
残留面积、磷刺、积屑瘤、切削过程中的变形、 刀具主刀刃磨损、刀刃与工件的位置变动 改善措施: 刀具方面、工件方面、切削条件方面。
10
机械加工质量检测
长度测量的基本原则:
在进行长度测量时,为保证测量准确,应使被测 工件的尺寸线和量仪中作为标准的刻度尺重合或 顺次排成一条直线。此原则称之为阿贝原则。 长度:包括轴径、孔径 角度:包括锥度
6
技术测量基础
测量是指以确定被测量对象量值为目的的全部操 作。一个完整的测量过程应包括被测对象、计量 定位、测量方法和测量精度4个方面要素。
测量对象:主要指几何量、包括长度、角度、表面粗糙度、 几何形状和相互位置等。 计量单位:机械制造中常用的长度单位为毫米(mm)在 精密测量中长度单位采用微米、在超精密测量中长度单位 采用纳米 测量方法:根据被测量对象确定最佳的测量方法 测量精度:是指测量结果与真值的一致程度。任何测量过 程总不可避免出现测量误差,误差小则证明精度高。
测量时体现基准的方法有模拟法、直接 Nhomakorabea、分析 法和目标法等。
14
精密加工的概念
尺度加工 根据加工零件的尺寸来分类,可分为宏尺度加工、中尺度 加工和微尺度加工 通常的机械加工大多指宏尺度加工,零件的技术性能要求 大多反映在宏观结构或表层结构上,尺寸相对较大,加工 的范畴较广。又可分为特大型、重型、一般型和小型产品 的加工。 微尺度加工是指微纳米加工,尺寸相对来说在微米、亚微 米和纳米级,主要用精密和超精密加工技术、微细加工技 术和纳米加工技术来加工。强调了微观结构,其领域相对 较窄。
机械加工精度
机械加工精度是指零件经过加工后的几何参数 (尺寸、几何要素的形状和相互位置)的实际值 与设计理想值的符合程度,而它们之间的偏离程 度称为加工误差。加工误差越小、加工精度越高。
加工精度和加工误差是零件加工后几何参数的两 种表示方法。
1
加工精度
零件的加工精度包括三个方面:
尺寸精度:限制加工表面与其基准面间尺寸误差 不超过一定的范围。尺寸精度用标准公差等级表 示,分为20级。 形状精度:限制加工表面宏观几何形状误差,如 圆度、圆柱度、平面度、直线度等。形状精度用 形状公差表示。 位置精度:限制加工表面与基准间的相互位置误 差,如平行度、垂直度、同轴度等。位置精度用 位置公差等级表示。
8
机械加工表面质量
机械加工表面质量的表示 1.表面几何学特征。它主要指零件最外层表面的 几何形状,通常用表面粗糙度、浓度和纹理表示。 2.表面层材质的变化。零件加工后在一定深度的 表面内出现与基体材料组织不同的变质层。在此 表面层内,金属的机械、物理及化学性质均发生 变化,如塑性变形、硬度变化、微观裂纹、残余 应力、晶粒变化、热损伤区、微观组织变化以及 化学性质及电特性的变化等。
4
经济加工精度
正常生产条件:设备完好、工夹量具适应、工人 技术水平相当、工时定额合理。
机械加工时,每种机床上所达到的精度越高,则 所耗费的工时越多,成本越高。 每种机床在正常条件下能经济地达到的加工精度 是有一定范围的,这个精度范围就是这种加工方 法的经济精度。
5
工艺基准
在制造工艺过程中采用的基准称为工艺基准 装配基准:是产品装配时用来确定零件或部件在 机器中的相对位置所用的基准。 测量基准:是测量时所采用的基准。 定位基准:加工中的定位基准。 工序基准:在工序图上用来确定本工序所加工表 面加工后的尺寸、形状、位置的基准。
2
加工误差产生的原因
加工前的误差
理论误差、装夹误差、机床制造、安装误差及磨损、刀具 误差、夹具误差、调整误差。
加工中的误差
工艺系统受力变形、工艺系统受热变形、刀具磨损、测量 误差、残余应力引起的变形。 控制方法与措施: 试切法、调整法、定尺寸刀具法、自动控制法、误差转移 法、误差分组法、
形状和位置误差:包括直线度、平面度、圆度、 圆柱度和表面粗糙度等的基本测量方法。
11
常用轴径测量仪器
卡尺、千分尺、指示表千分尺、杠杆千分尺、杠 杆齿轮传动测微仪、扭簧测微仪、电感测微仪、 电容测微仪、立式光学计、卧式光学计、立式测 长仪、万能测长仪、 工具显微镜:分大型、小型、万能
12
7
计量器具
量具:分为单值量具和多值量具 单值量具:量块、直角尺等 多值量具:金属直尺、卷尺、游标卡尺、游标万 能角度尺等;螺旋测微量具:内、外径千分尺和 螺纹千分尺等; 量规:专用计量器具,用于检验零件要素的实际 尺寸及形状、位置的实际情况所形成的综合结果 是否在规定的范围内,从而判断零件被测的几何 量是否合格。
常用孔径测量仪器
内径百分表 内径测微仪 万能测长仪 一米测长机 万能工具显微镜 孔径测量仪 自准直孔径测量仪 内孔比长仪 小孔显微镜
13
角度测量
两面角的测量 锥度测量 基准的建立与体现 基准是用以确定被测要素的理想方向和理想位置 的依据。根据实际零件的形体表面(有形状误差 的表面)来建立基准时应按统一的原则,这个原 则应是最小条件。