机械加工质量及其控制
机械加工质量及控制

机械加工质量及控制机械加工质量及控制1. 引言1. 背景介绍:说明为什么需要进行机械加工质量的控制。
2. 目的和范围:明确本文档旨在提供关于机械加工质量及其控制方面的详尽信息,并限定了讨论内容。
2. 基础知识1. 定义与术语解释:列出相关定义并对其中涉及到法律名词进行注释。
- 法律名词A: 解释A.- 法律名词B: 解释B.3. 加工过程流程图示例:描述一个典型的机械加工过程,包括各个环节以及可能存在问题点。
附上相应图片或图表。
4.常见材料特性分析对不同类型材料(如金属、塑料等)在机械加工中所具有的特性进行分析,例如强度、韧性等因素对最终产品品质影响情况。
5.主要设备选择与使用指南提供针对不同种类零件生产时合适设备选用建议, 并给予操作规范化指导手册参考资料。
(可根据实际情况细化)6.加工质量控制方法1. 测量与检验:介绍常用的测量和检验方法,如尺寸、表面粗糙度等。
2. 数据分析与统计:说明数据收集及其分析对于机械加工质量控制的重要性,并提供相应的统计学原理。
7.问题解决方案提供一些可能出现在机械加工过程中遇到问题时所采取的解决方案。
例如,处理材料变形或刀具损坏等情况。
8.实施建议根据前述内容给予针对企业生产环境下合适改进策略, 并附上相关操作指南。
(可根据实际情况进行详细拓展)9. 结论10. 参考文献11. 附件:本文档涉及到并有助于读者更好理解主题内容而需要参阅或使用之文件列表.12 . 法律名词注释:- 法律名词A: 解释A.- 法律名词B: 解释B.。
第四章 机械加工质量及其控制
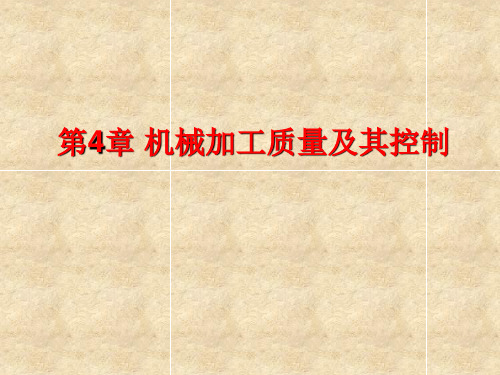
工艺系统刚度主要取决于薄弱环节的刚度。
2)机床刚度
y机床 y主轴 y刀架 y尾座
k主轴= k尾架= k刀架= Fp 2 y主轴 Fp 2 y尾架 Fp y刀架
机床的刚度取决于部件的刚度。
(2)工艺系统刚度对加工精度的影响
常见的几种工艺系统中其低刚度环节所在位置:
镗孔:工件进给孔为椭圆形。
避免措施
提高主轴及箱体的制造精度、选用高精度的轴承、提高主轴 部件的装配精度、对高速主轴部件进行平衡、对滚动轴承进 行预紧等,均可提高机床主轴的回转精度。
2)导轨误差
(a) 在水平面 内的直线度误 差 误差敏感方向
(b) 在垂直平面 内的直线度
ΔR ≈Δ22/D 设Δ2=
工艺系统的刚度在不同的加工位置上是各不相同的,当主轴箱 刚度与尾座刚度相等时,工艺系统刚度在工件全长上的差别最 小,工件在轴截面内几何形状误差最小。
在车床上加工短而粗的光轴(工件刚度相对于机床刚度大 得多),已知径向切削分力
Fp
=1000N,主轴刚度
k主轴
=100000N/mm,尾座刚度
k尾座
=50000N/mm,
正确地选用刀具材料和选用新型耐磨的刀具材料,合理地选 用刀具几何参数和切削用量,正确地刃磨刀具,正确地采用冷 却润滑液等,均可有效地减少刀具的尺寸磨损。必要时还可采 用补偿装置对刀具尺寸磨损进行自动补偿。
10000.054 mm, 加工一合金钢管,其外径为
工件长度
l =2100mm,圆柱度公差在全长范围内
c)采用合理的装夹方式和加工方式
2)减小切削力及其变化 合理地选择刀具材料、 增大前角和主偏角、对 工件材料进行合理的热 处理以改善材料的加工 性能等,都可使切削力 减小。
机械加工质量控制
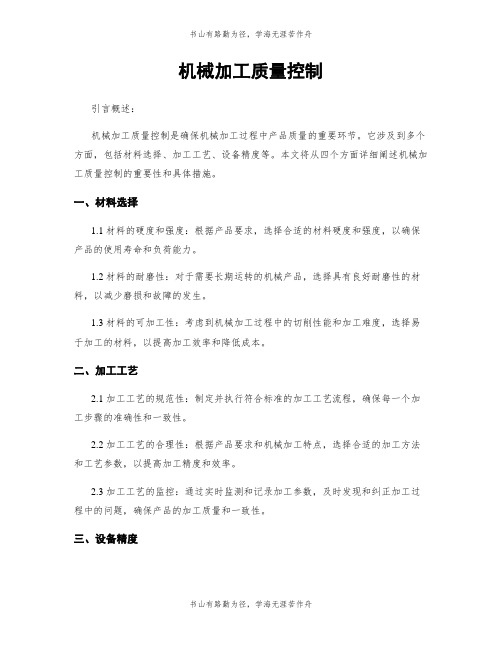
机械加工质量控制引言概述:机械加工质量控制是确保机械加工过程中产品质量的重要环节。
它涉及到多个方面,包括材料选择、加工工艺、设备精度等。
本文将从四个方面详细阐述机械加工质量控制的重要性和具体措施。
一、材料选择1.1 材料的硬度和强度:根据产品要求,选择合适的材料硬度和强度,以确保产品的使用寿命和负荷能力。
1.2 材料的耐磨性:对于需要长期运转的机械产品,选择具有良好耐磨性的材料,以减少磨损和故障的发生。
1.3 材料的可加工性:考虑到机械加工过程中的切削性能和加工难度,选择易于加工的材料,以提高加工效率和降低成本。
二、加工工艺2.1 加工工艺的规范性:制定并执行符合标准的加工工艺流程,确保每一个加工步骤的准确性和一致性。
2.2 加工工艺的合理性:根据产品要求和机械加工特点,选择合适的加工方法和工艺参数,以提高加工精度和效率。
2.3 加工工艺的监控:通过实时监测和记录加工参数,及时发现和纠正加工过程中的问题,确保产品的加工质量和一致性。
三、设备精度3.1 设备的选型和调试:根据产品要求和加工工艺的特点,选择适合的机床和刀具,并进行调试和校准,以确保设备的准确性和稳定性。
3.2 设备的维护和保养:定期对设备进行维护和保养,包括清洁、润滑和紧固等,以保持设备的正常运转和精度。
3.3 设备的监控和改进:通过设备的监控和数据分析,及时发现设备故障和性能下降的问题,并采取相应的改进措施,以提高设备的可靠性和加工精度。
四、质量检验4.1 检验方法的选择:根据产品特点和加工要求,选择合适的检验方法,包括尺寸测量、表面质量检查等,以确保产品的准确性和一致性。
4.2 检验设备的校准:定期对检验设备进行校准和验证,以确保检验结果的准确性和可靠性。
4.3 检验结果的记录和分析:对检验结果进行记录和分析,及时发现和解决质量问题,并采取相应的改进措施,以提高产品的质量和客户满意度。
结论:机械加工质量控制是确保产品质量的关键环节。
机械加工质量及其控制概述ppt68页课件

二、机械加工表面质量
(一)表面质量的概念
粗糙度太大、太小都不耐磨
适度冷硬能提高耐磨性
对疲劳强度的影响
对耐腐蚀性能的影响
对工作精度的影响
粗糙度越大,疲劳强度越差
适度冷硬、残余压应力能提高疲劳强度
粗糙度越大、工作精度降低
残余应力越大,工作精度降低
粗糙度越大,耐腐蚀性越差
压应力提高耐腐蚀性,拉应力反之则降低耐腐蚀性
本章提要
机械产品质量取决于零件的加工质量和产品的装配质量,机器零件的加工质量是整台机器质量的基础。 机器零件的加工质量一般用机械加工精度和加工表面质量两个重要指标表示,它的高低将直接影响整台机器的使用性能和寿命。 机械产品加工的首要任务,就是保证零件的机械加工质量要求。 本章重点讨论影响机械加工精度和表面质量的因素及其控制方法。
(1)主轴回转误差
第二节 机械加工精度的影响因素及控制
一、工艺系统几何误差对加工精度的影响
(一)机床的几何误差
(1)主轴回转误差
第二节 机械加工精度的影响因素及控制
一、工艺系统几何误差对加工精度的影响
(一)机床的几何误差
主轴回转误差的基本形式
车床上车削
镗床上镗削
内、外圆
端面
螺纹
孔
端面
纯径向跳动
机械加工中,采用近似的成形运动或近似的刀刃形状进行加工,虽然会由此产生一定的原理误差,但却可以简化机床结构和减少刀具数,只要加工误差能够控制在允许的制造公差范围内,就可采用近似加工方法。
原始误差
工艺系统动误差
工艺系统受力变形
刀具磨损
残余应力引起变形
测量误差
工艺系统热变形
第二节 机械加工精度的影响因素及控制
机械加工质量及控制
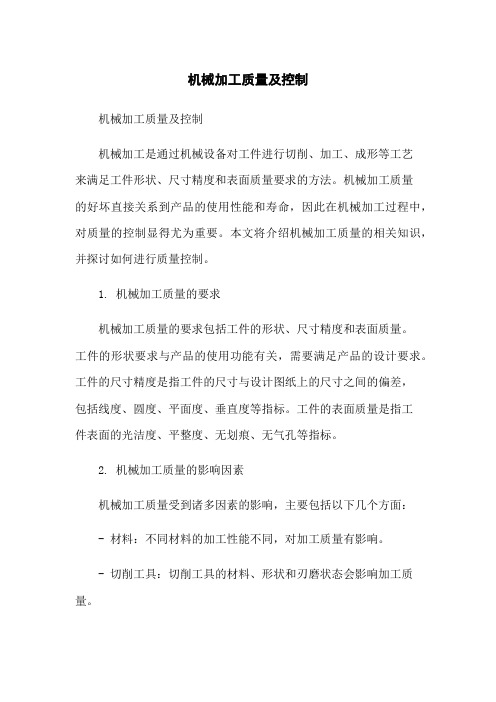
机械加工质量及控制机械加工质量及控制机械加工是通过机械设备对工件进行切削、加工、成形等工艺来满足工件形状、尺寸精度和表面质量要求的方法。
机械加工质量的好坏直接关系到产品的使用性能和寿命,因此在机械加工过程中,对质量的控制显得尤为重要。
本文将介绍机械加工质量的相关知识,并探讨如何进行质量控制。
1. 机械加工质量的要求机械加工质量的要求包括工件的形状、尺寸精度和表面质量。
工件的形状要求与产品的使用功能有关,需要满足产品的设计要求。
工件的尺寸精度是指工件的尺寸与设计图纸上的尺寸之间的偏差,包括线度、圆度、平面度、垂直度等指标。
工件的表面质量是指工件表面的光洁度、平整度、无划痕、无气孔等指标。
2. 机械加工质量的影响因素机械加工质量受到诸多因素的影响,主要包括以下几个方面:- 材料:不同材料的加工性能不同,对加工质量有影响。
- 切削工具:切削工具的材料、形状和刃磨状态会影响加工质量。
- 加工工艺:包括切削速度、进给量、切屑清除等,对加工质量有重要影响。
- 加工设备:加工设备的精度、刚性和稳定性对加工质量有直接影响。
- 操作技术:操作人员的技术水平和经验对加工质量有很大的影响。
3. 机械加工质量的控制方法为了保证机械加工质量,需要采取一系列的控制方法。
3.1 设计合理性控制这是机械加工质量控制的首要环节。
设计时需要考虑工件的功能和使用要求,并根据不同材料的加工性能确定合适的工艺参数。
3.2 切削工具的选择和维护切削工具的选择应根据加工工件的材料和形状来确定,同时需要定期进行刃磨和维护,确保切削工具的良好状态。
3.3 加工工艺的控制合理的加工工艺参数包括切削速度、进给量、冷却液的使用等。
在加工过程中需要严格控制这些参数,以保证工件的尺寸精度和表面质量。
3.4 加工设备的维护和调整加工设备的精度、刚性和稳定性对加工质量有直接影响。
定期对设备进行维护和调整,保持其良好状态。
3.5 操作人员的培训和管理操作人员的技术水平和经验对加工质量至关重要。
第五六章 机械加工质量及其控制

避免措施
提高主轴及箱体的制造精度,选用高精度的轴承,提高主轴 提高主轴及箱体的制造精度,选用高精度的轴承, 部件的装配精度,对高速主轴部件进行平衡, 部件的装配精度,对高速主轴部件进行平衡,对滚动轴承进 行预紧等,均可提高机床主轴的回转精度. 行预紧等,均可提高机床主轴的回转精度.
2)导轨误差
(a) 在水平面 内的直线度误 差 误差敏感方向 (b) 在垂直平面 内的直线度
加工误差的分类
变值系统误差:在连续加工一批工件中,其中加工 变值系统误差:在连续加工一批工件中, 误差的大小方向按一定规律变化的系统误差 例如:刀具磨损 例如: 特点: 特点: 与加时间有关 预先可以估计 较难完全消除 会造成尺寸改变,但按一定规律依次变化 会造成尺寸改变, 影响尺寸分布曲线形状 再 例:工艺系统受热变形 升温过程中-- --变值 热平衡后-- --常值 升温过程中--变值 热平衡后--常值
3 工艺系统受力变形引起的误差
工件受力变形
机床受力变形
(1)工艺系统刚度 1)工艺系统刚度
在加工误差敏感方向上工艺系统所受 在加工误差敏感方向上工艺系统所受的径向切削分力与其 上工艺系统所受的径向切削分力与其 在该方向上的变形量之比
k系=Fp / y
y系 = y机床 + y刀具 + y夹具 + y工件
(2)刀具的几何误差
包括刀具切削部, 包括刀具切削部,装夹部的制造误差及刀具安装误差 ① 定尺寸刀具 刀具尺寸精度直接影响工件尺寸精度 ② 成形刀具 ③ 展成刀具 ④ 一般刀具 刀具形状精度直接影响工件形状精度 刀刃形状精度会影响工件加工精度 制造精度对工件加工精度无直接影响
(3)夹具的几何误差
加工前:原理误差,调整误差, 加工前:原理误差,调整误差,工艺系统的几何误差和定 位误差等. 位误差等. 加工中:工艺系统受热,受力变形引起的加工误差. 加工中:工艺系统受热,受力变形引起的加工误差. 加工后:工件内应力重新分布引起的变形及测量误差. 加工后:工件内应力重新分布引起的变形及测量误差.
机械加工质量分析及控制精简版范文
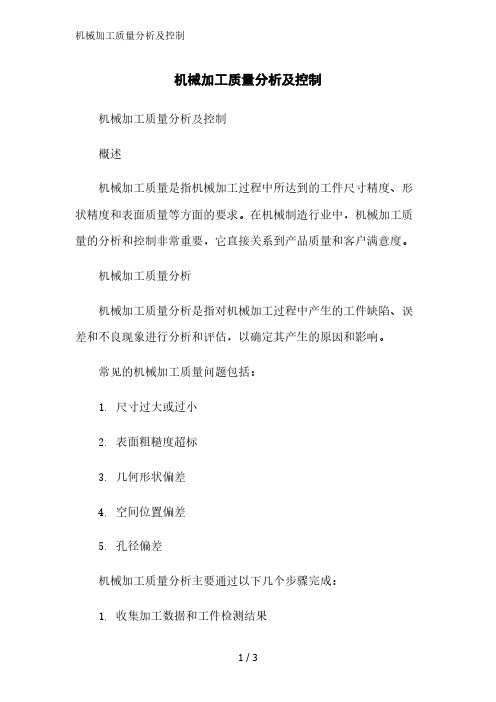
机械加工质量分析及控制
机械加工质量分析及控制
概述
机械加工质量是指机械加工过程中所达到的工件尺寸精度、形状精度和表面质量等方面的要求。
在机械制造行业中,机械加工质量的分析和控制非常重要,它直接关系到产品质量和客户满意度。
机械加工质量分析
机械加工质量分析是指对机械加工过程中产生的工件缺陷、误差和不良现象进行分析和评估,以确定其产生的原因和影响。
常见的机械加工质量问题包括:
1. 尺寸过大或过小
2. 表面粗糙度超标
3. 几何形状偏差
4. 空间位置偏差
5. 孔径偏差
机械加工质量分析主要通过以下几个步骤完成:
1. 收集加工数据和工件检测结果
2. 对数据进行统计分析和图像处理
3. 利用统计分析结果,确定质量问题的原因和影响因素
4. 提出相关改善措施和加工优化建议
机械加工质量控制
机械加工质量控制是指通过控制加工参数和采用合理的加工工艺,确保机械加工过程中所达到的工件质量能够满足设计要求和客户需求。
常见的机械加工质量控制方法包括:
1. 控制加工参数,如刀具刃口半径、加工速度、进给量等
2. 采用合适的加工工艺,如铣削、车削、钻削等
3. 使用高精度的测量设备进行质量检测和纠正
4. 实施质量管理体系和质量控制标准
机械加工质量控制的关键在于不断优化和改进加工工艺、设备和管理体系,以提高加工稳定性和质量可靠性。
结论
机械加工质量分析和控制是机械制造过程中必不可少的环节,它直接关系到产品的质量和市场竞争力。
通过科学的分析和有效的
控制措施,能够提高机械加工的质量稳定性和可靠性,满足客户的需求。
机械加工质量分析及控制

机械加工质量分析及控制机械加工质量分析及控制一、引言二、机械加工质量分析机械加工质量的分析主要包括以下几个方面:1.表面粗糙度分析机械加工的表面粗糙度对于产品的外观和性能有着重要影响。
通过使用表面粗糙度测量仪器,可以对机械加工的表面粗糙度进行评估。
常用的表面粗糙度参数包括Ra、Rz等。
2.尺寸精度分析机械加工的尺寸精度是指产品的实际尺寸和设计图纸上的尺寸之间的偏差。
通过使用测量工具和仪器,可以对机械加工的尺寸精度进行评估。
常用的尺寸精度参数包括公差、尺寸偏差等。
3.形状偏差分析机械加工的形状偏差是指产品的实际形状和设计图纸上的形状之间的偏差。
通过使用形状测量仪器,可以对机械加工的形状偏差进行评估。
常用的形状偏差参数包括圆度误差、平面度误差等。
三、机械加工质量控制为了确保机械加工的质量,需要进行相应的控制措施。
以下是几个常用的机械加工质量控制方法:1.工艺参数控制调整机械加工的工艺参数,可以对机械加工的质量进行控制。
例如,通过调整切削速度、进给速度和切削深度等参数,可以控制机械加工的表面粗糙度和尺寸精度。
2.设备状态监控对机械加工设备的状态进行监控,可以及时发现并修复设备故障,避免对产品质量的影响。
常用的设备状态监控方法包括振动监测、温度监测等。
3.质量检验与统计分析对机械加工的产品进行质量检验,并进行统计分析,可以及时发现并纠正加工过程中的问题。
常用的质量检验方法包括外观检查、尺寸测量等。
四、机械加工质量的分析和控制是确保产品质量的重要手段。
通过对表面粗糙度、尺寸精度和形状偏差等进行分析,可以找出问题所在。
通过工艺参数控制、设备状态监控和质量检验与统计分析等控制措施,可以提高机械加工的质量水平。
- 1、下载文档前请自行甄别文档内容的完整性,平台不提供额外的编辑、内容补充、找答案等附加服务。
- 2、"仅部分预览"的文档,不可在线预览部分如存在完整性等问题,可反馈申请退款(可完整预览的文档不适用该条件!)。
- 3、如文档侵犯您的权益,请联系客服反馈,我们会尽快为您处理(人工客服工作时间:9:00-18:30)。
第四章 机械加工质量及其控制例1:在车床上用两顶尖定位车削刚性轴(y 工件≈0,y 夹具≈0,y 刀具≈0),k 床头=300000N /mm ,k 尾座=56600 N /mm ,k 刀架=30000 N /mm ,F p=4000 N ,计算由于切削力作用点位置变化引起的工件形状误差,并画出加工后工件纵向截面示意图。
解:y 系(0)=F p (主轴k 1+1k 刀架)=400(3000013000001+)=0.0147 y 系(2l)=F p (主轴k 41+14k 尾座+1k 刀架)=0.0154y 系(l )=F p (1k 尾座+1k 刀架)=0.0204y 系(x 0)=y 系min = F p (尾座主轴+k k 1+1k 刀架)=0.0144x 0=尾座主轴尾座+k k k l =0.16 l其圆柱度误差为: Δ=y 系 max -y 系 min =0.0204-0.0144=0.006 其直径误差为: Δd =2(y 系 max -y 系 min )=0.012例2:在车床上车削短轴(k 系=C ),已知:a p1=2.5mm ,a p2=1.8mm ,C =2000N /mm ,k 系=2×104 N /mm 。
求工件加工后的圆柱度误差。
解:Δ工件=εΔ毛坯=(a p1-a p2)Ck 系=0.07 mm 例3:在车床上镗一短套筒工件孔,毛坯孔的圆柱度误差Δ毛坯=1.2mm ,系数C =2×103N/mm ,且只考虑切削力大小变化之影响,试求:(1)若k 系=2×104N/mm ,镗一次后,工件孔的圆柱度误差Δ工件; (2)若镗孔后使Δ工件≤0.05mm ,则需镗几次? (3)若镗一次后使Δ工件≤0.1mm ,则k 系应为多高? 解:(1)ε=工件毛坯ΔΔ=Ck 系 Δ工=C k ∆毛坯系=0.12(mm )(2)Δ毛坯·εn ≤Δg εn =工件毛坯ΔΔn lg ε = lgΔ工件-lgΔ毛坯n =(lgΔ工件-lgΔ毛坯)/lg ε=(-3+0.18)/(-2.3)=1.23 取:n =2 即需镗2次。
(3)k 系≥C∆∆毛坯工件=2.4×104(N /mm ) 例4:磨削长度为2m 的丝杠,每磨—次其温度相对于机床母丝杠升高约3℃,则丝杠的伸长量。
ΔL =2000×1.17×10-5×3=0.07(mm )而6级丝杠的螺距累积误差在全长上不允许超过0.02mm ,由此可见热变形的严重性例5:车一批轴,设计要求直径φ 00.125 -mm,已知加工尺寸正态分布,且计算得x =24.96,σ=0.02。
试计算这批工件的合格率、废品率,其废品可否修复? 解:z 1=σxx -1=-3φ(3)=0.49865≈0.50 z 2=σxx -2=2φ(2)=0.4772则:合格率=0.49865+0.4772=97.585%废品率=1-97.585%=2.415% 其中: 0.135% 偏小,不可修复;2.28% 偏大,可修复。
第五章 工艺规程设计例1:图示零件,2面设计尺寸为 2522.00+mm ,尺寸 60012.0-mm 已经保证,现以1面定位用调整法 精铣2面,试计算工序尺寸。
解:(1)建立尺寸链设计尺寸2522.00 +mm 是间接保证的,是封 闭环,A 1(600 12.0-mm )和A 2为组成环。
(2)计算根据 A 0=∑=mi i A 1-∑-+=11n m i iAA 2 = A 1-A 0=35ES 0=∑=mi i ES 1-∑-+=11n m i iEIEI 2=ES 1-ES 0=-0.22EI 0=∑=mi i EI 1-∑-+=11n m i iES 2=EI 1-EI 0=-0.12则:工序尺寸A 2=3512.022.0--=34.880 10.0-mm 。
例2:下图所示工件外圆、内孔及端面均已加工完毕,本序加工A 面,保证设计尺寸8±0.1 mm 。
由于不便测量,现已B 面作为测量基准,试求测量尺寸及其偏差。
解:(1)建立尺寸链设计尺寸8±0.1是 mm 是封闭环,A 1、 A 2、A 3是组成环。
(2)计算 根据 A 0=∑=mi i A 1-∑-+=11n m i iA 1 = A 0-A 2+A 3=18 ES 0=∑=mi i ES 1-∑-+=11n m i iEIES 1=ES 0-ES 2+EI 3=0EI 0=∑=mi i EI 1-∑-+=11n m i iEI 1=EI 0-EI 2+ES 3=-0.05则:测量尺寸A 1=180 05.0-=17.9505.00 + mm 。
例3:一带有键槽的内孔要淬火及磨削,其设计尺寸如图所示。
保证键槽尺寸034436..+ mm 的有关工艺过程如下: 1)镗内孔至中01 0396..ϕ+(005198.R .+)mm ; 2)插键槽至尺寸A 1; 3)淬火(变形忽略不计);4)磨内孔,同时保证内孔直径005 040.ϕ+(0025 020.R +)mm 和键槽深度 034 0436..+mm 两个设计尺寸的要求。
要求确定工序尺寸A 1及其公差。
解:(1)建立尺寸链键槽深度034 0436..+mm 是间接保证的,是封闭环。
005 040.ϕ+(002520.R +)mm 是本序直接保证的,是组成环,还有插键槽尺寸A 1和镗内孔01 0396..ϕ+(005198.R .+)mm 是组成环。
(2)计算根据A 0=∑=mi i A 1-∑-+=11n m i iA 1 = A 0-A 3+A 2=43.4ES 0=∑=mi i ES 1-∑-+=11n m i iEIES 1=ES 0-ES 3+EI 2=0.315EI 0=∑=mi i EI 1-∑-+=11n m i iEI 1=EI 0-EI 3+ES 2=0.05则:插键槽工序尺寸A 1=03150050434...++=026 04345..+mm 。
例4:一个齿轮装配结构如图。
为保证齿轮3在轴1上转动灵活,要求齿轮左、右端面与轴套4和档圈2之间应留有间隙0.10~0.35(0350100..++)mm 。
已知A l=35mm ,A 2=14mm ,A 3=49mm 。
试用完全互换 装配法解算各组成环尺寸及其极限偏差。
解:(1)建立装配尺寸链图,校验各环基本尺寸A 0=A 3-(A 1+A 2)=49-(35+14)=0各环基本尺寸正确 (2)求各组成环的平均公差T av =T 0/(n -1)=0.25/3≈0.083(mm )(3)确定各组成环公差取: T 1=T 3=0.10(IT10) T 2=T 0-T 1-T 3=0.05(IT 9~IT10) (4)确定各组成环公差分布(标注形式) 本例选A 2为协调环。
则:A l = 00.1035 -mm A 3=0.1049+mm 由 ES 0=∑=mi i ES 1-∑-+=11n m i iEIEI 0=∑=mi i EI 1-∑-+=11n m i iESEI 2=ES 3-ES 0-EI 1=0.10-0.35+0.10=-0.15 ES 2=EI 3 -EI 0-ES 1=0-0.10-0=-0.10即 A 2=0.100.1514--(5)验算A 0max =A 3max -A 1min - A 2min =49.10-34.90-13.85=0.35 A 0min =A 3min -A 1max -A 2max =49-35-13.90=0.10故计算结果正确。
例5:用统计互换装配法求解例4。
设各尺寸均正态分布(k 1=k 2=k 3=1) 解:(1)建立装配尺寸链图,校验各环基本尺寸 A 0=A 3-(A 1+A 2)=49-(35+14)=0各环基本尺寸正确 (2)求各组成环的平均公差T avi=0.253≈0.144(mm )(3)确定各组成环公差 取: T 1=T 3=0.160(IT11)T 2≈0.106(IT11) (4)确定各组成环公差分布(标注形式)A 1= 00.1635-=34.92±0.08(mm )A 3=0.1649+=49.08±0.08(mm ) A 0=0.350.100++=0.225±0.125(mm )选A 2为协调环A 2=A 3-A 0-A 1=13.935则:A 2=13.935±0.053=0.0120.020.1180.111414----=(mm )例6:汽车发动机活塞销与活塞销孔装配。
技术要求:销轴直径d与销孔直径D 冷态过盈量为:0.0025mm ~0.0075mm ,试确 定销轴与销孔的公差及其分布(基本尺寸D =d =28 mm )。
解:1)建立尺寸链2)计算组成环平均公差,确定装配方法 T avi =T 0/(n-1)=0.0050/2=0.0025(mm )选基轴制 d =A 1= 00.002528- mmD =A 2=0.00500.007528-- mm经分析,采用分组装配法 3)分组装配将销轴与销孔的公差在相同方向上放大4倍(采取上偏差不动,变动下偏差),即A 1= 00.010028- mmA 2=0.00500.015028-- mm测量、分组(4组),对应组完全互换装配。
IT2IT10~IT11例7:机床托板和导轨装配如图,要求保证装配间隙0~0.06mm ,现采用修配法装配(分别修配件1M 面和N 面)。
已知:A 2=0.25 020 mm ,A 3= 00.1530- mm ,取T 1=0.1mm 。
试计算:(1)A 1及其偏差;(2)最大修配量K max 和最小修配量K min 。
解:(1)修配件1M 面 1)建立装配尺寸链 2)计算① A 0=0.060+ ② 计算修配环基本尺寸 A 1=A 0+A 3-A 2=10 ③ 确定修配环尺寸∵修M 面 A 0∴首先确定修配环最大尺寸A 1max 由 A 0max =A 1max +A 2max -A 3min则 A 1max =A 0max -A 2max +A 3min =9.66(mm ) A 1min =A 1max -T 1=9.55(mm )即 A 1=0.340.4410--(mm )④计算修配量 K min =0K max =A 3max -A 1min -A 2min +A 0min =0.44(mm )(2)修配件1N 面 1)建立装配尺寸链 2)计算① A 0=0.060+ ② 计算修配环基本尺寸 A 1=A 0+A 3-A 2=10 ③ 确定修配环尺寸 ∵修N 面 A 0 ∴首先确定修配环最小尺寸A 1min 由 A 0min =A 1min +A 2min -A 3max则 A 1min =A 0min -A 2min +A 3max =10(mm ) A 1max =A 1min +T 1=10.1(mm )即 A 1=0.10 010+ (mm )④计算修配量 K min =0K max =A 1max +A 2max -A 3min -A 0max =0.44(mm )例8:图示双联齿轮装配后要求轴向具有间隙A 0=0200050..++mm ,已知:A 1=115mm ,A 2=8.5mm ,A 3=95mm ,A 4=2.5mm , A 5=9mm ,试用固定调整装配法解算各组成环的极限 偏差,并确定调整环的分组数和尺寸系列。