机械加工质量技术控制
机械加工过程中的质量控制与检测技术

机械加工过程中的质量控制与检测技术随着科技的不断进步,机械工程在制造领域发挥着重要的作用。
机械加工是制造过程中不可或缺的环节,而质量控制与检测技术则是确保机械制造的关键。
本文将探讨机械加工过程中的质量控制与检测技术,并介绍其中一些常用的方法。
一、质量控制的重要性在机械加工过程中,质量控制是确保产品符合设计要求的关键。
一旦产品质量出现问题,不仅会影响到产品的性能和可靠性,还可能导致安全隐患和经济损失。
因此,质量控制在机械工程中具有重要意义。
二、质量控制方法1. 设计阶段的质量控制:在机械加工之前,设计阶段的质量控制非常关键。
通过合理的设计和工艺规划,可以减少制造过程中的错误和缺陷,提高产品的质量和可靠性。
2. 加工参数的控制:在机械加工过程中,控制加工参数是确保产品质量的重要手段。
例如,对于数控加工,控制切削速度、进给速度和切削深度等参数,可以保证加工精度和表面质量。
3. 检测与测量:质量控制离不开检测与测量。
通过使用各种测量工具和设备,如千分尺、游标卡尺和高度规等,可以对产品的尺寸和形状进行测量,以确保其符合设计要求。
三、常用的检测技术1. 硬度检测:硬度是材料抵抗外力的能力,对于机械加工来说非常关键。
硬度检测可以通过硬度计等设备进行,以评估材料的硬度是否符合要求。
2. 表面粗糙度检测:表面粗糙度对于机械零件的功能和耐久性有着重要影响。
通过使用表面粗糙度仪等设备,可以对零件表面的光洁度进行检测,以确保其满足设计要求。
3. 尺寸测量:尺寸测量是机械加工中最常见的检测技术之一。
通过使用精密测量工具,如三坐标测量机和光学投影仪,可以对零件的尺寸进行精确测量,以确保其符合设计要求。
四、质量控制与检测技术的挑战在机械加工领域,质量控制与检测技术面临着一些挑战。
首先,随着制造工艺的不断发展,产品的复杂性和精度要求不断提高,对质量控制和检测技术提出了更高的要求。
其次,制造过程中的变异性和误差也会对质量控制造成挑战,需要采取措施来减少其影响。
浅析现代机械加工质量技术控制

刀具 误差对 加工精 度的 影响随 刀具种 类的不 同而不 同。 采用 定尺寸 刀具成 形刀具 展 成刀具 加 工时 , 刀 具的制 造误 差会 直接 影响 工件 的加 工精度 ; 而对一 般刀具 , 其制 造 误差对工 件加 工精度无 直接 影响 。 夹具 的几何误 差 : 夹 具 的作 用
内应力 引起 的变 形误差 , 尽 可能 减小测量 误差 等均 属于直 接减 少原始 误差 为 了提 高机 加工精 度 , 需对产 生加 工误差 的各 项原始 误差进 行分 析 , 根 据 不同情 况对造 成加工误 差的主要 原始误 差采取相 应的解 决措施 。 对于精 密零件 的加工 应尽 可能提 高所 使用精 密机 床的几 何精 度 、 剐度和 控制 加工热 变形 , 对具 有成 形表 面的零件 加 工 , 则 主要 是如何 减少 成形 刀具形 状误差 和刀具 的安 装误 差 3 . 2误差 补偿法 。 对 工艺 系统 的一些 原始误 差 , 可采取 误差 补偿 的方法 以 控制 其对 零件加 工误 差 的影 响。 3 . 2 . 1误差 补偿 法 : 该方法 是人 为地造 出一种新 的原始 误差 , 从 而补偿 或 抵消原 来工 艺系统 中固有 的原 始误 差 , 达到 减少加 工误差 , 提 高加工 精度 的 目
工 业技 术
C h i n a s ci e n ce a n d T e c h n o l o g y R ev i e w
啊
l
浅 析 现 代 机 械 加工 质 量 技 术 控制
张学 忠
( 哈药集 团三精 制 药股 份有 限公司 哈尔 滨市 1 5 0 0 1 8 )
[ 摘 要】 本文介绍了机械加工精度的概念及 内容 , 分析了机械加工产生误差的原因, 最后提出提高机械加工精度的工艺措施。
机械加工中的表面质量与精度控制技术

机械加工中的表面质量与精度控制技术质量和精度的控制是机械加工中的重要环节,主要从当前机械加工精度的概念和内容出发,分析机械加工过程中产生误差的原因,力图探索在机械加工的过程中如何才能提高加工的质量,并且加强对加工过程的精度控制,从而提高整体加工水平。
标签:机械加工;表面质量;精度控制中图分类号:TB 文献标识码:A 文章编号:16723198(2012)180174011 机械加工精度概述机械加工精度是指工件在机械加工后的实际几何参数与零件图纸所规定的理想值之间的符合程度,如果它们之间存在不相符的程度则就称为加工误差。
机械的加工精度包括了三方面因素:首先是尺度因素,尺度因素限制加工表面和基准间尺寸的误差;其次是几何形状精度,主要是指限制加工表面的宏观性状的误差,从而达到提高机械加工表面质量的目的;最后是相互位置的精度,主要是指限制加工表面和其基准间的相互位置误差。
机械加工误差的大小反映了机械加工的精度高低。
2 影响机械加工质量和精度的因素及对策2.1 机床的几何误差在机械加工的过程中对工件的成形操作加工一般都是在机床上完成的,因此,机械加工品的机床几何误差直接会影响最终的加工质量和精度。
直接影响机械加工质量和精度的因素主要是主轴回转误差以及传动链误差。
从主轴回转误差来看,轴承本身的是指主轴在各个瞬间的实际回转轴线相对于其平均回转轴线的误差。
从传动链误差来看,主要是指传动链的始末两端传动元件之间相互运动产生的误差。
2.2 定位误差定位误差包括了两方面内容,分别是基准不重合誤差和定位副制造不准确误差。
在机床上对工件进行加工的过程中,需要将几何要素作为定位标准,当选择的定位基准和设计基准之间存在误差时就会产生基准不重合的误差。
另外夹具上的定位元件不可能完全准确,其实际尺寸都在允许范围内变动,当超过允许范围时就会造成较大的定位误差。
2.3 刀具的几何误差刀具在使用的过程中难免会产生磨损,从而在机械加工的过程中造成工件的尺寸以及形状的误差,最终影响了加工的质量和精度。
机械制造过程中的质量控制与改进措施
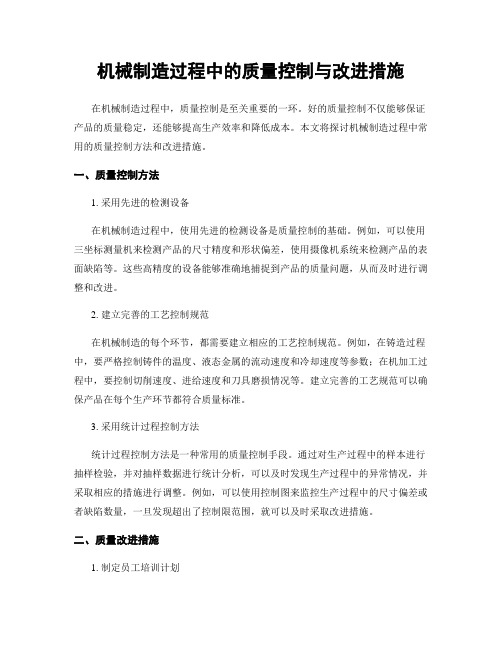
机械制造过程中的质量控制与改进措施在机械制造过程中,质量控制是至关重要的一环。
好的质量控制不仅能够保证产品的质量稳定,还能够提高生产效率和降低成本。
本文将探讨机械制造过程中常用的质量控制方法和改进措施。
一、质量控制方法1. 采用先进的检测设备在机械制造过程中,使用先进的检测设备是质量控制的基础。
例如,可以使用三坐标测量机来检测产品的尺寸精度和形状偏差,使用摄像机系统来检测产品的表面缺陷等。
这些高精度的设备能够准确地捕捉到产品的质量问题,从而及时进行调整和改进。
2. 建立完善的工艺控制规范在机械制造的每个环节,都需要建立相应的工艺控制规范。
例如,在铸造过程中,要严格控制铸件的温度、液态金属的流动速度和冷却速度等参数;在机加工过程中,要控制切削速度、进给速度和刀具磨损情况等。
建立完善的工艺规范可以确保产品在每个生产环节都符合质量标准。
3. 采用统计过程控制方法统计过程控制方法是一种常用的质量控制手段。
通过对生产过程中的样本进行抽样检验,并对抽样数据进行统计分析,可以及时发现生产过程中的异常情况,并采取相应的措施进行调整。
例如,可以使用控制图来监控生产过程中的尺寸偏差或者缺陷数量,一旦发现超出了控制限范围,就可以及时采取改进措施。
二、质量改进措施1. 制定员工培训计划质量控制和改进离不开员工的积极参与和培训。
因此,制造企业应制定员工培训计划,不断提升员工的技术能力和品质意识。
培训内容可以包括质量管理知识、工艺操作技能以及质量检测方法等。
通过培训,可以增强员工的责任心和主动性,从而有效改善产品的质量。
2. 引入先进的工艺技术和设备随着科技的不断进步,新的工艺技术和设备不断涌现。
制造企业应及时引入先进的工艺技术和设备,并与现有技术进行整合和改进。
例如,可以引入自动化设备来替代人工操作,提高生产效率和质量稳定性;还可以使用先进的模拟软件来进行工艺仿真和改进,降低生产过程中的风险。
3. 建立良好的供应链管理体系在机械制造过程中,供应链管理是一个关键环节。
机械加工过程中的质量控制简版
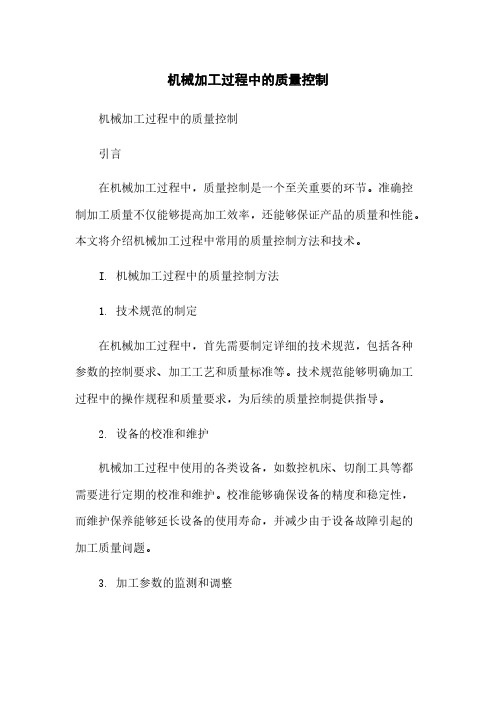
机械加工过程中的质量控制机械加工过程中的质量控制引言在机械加工过程中,质量控制是一个至关重要的环节。
准确控制加工质量不仅能够提高加工效率,还能够保证产品的质量和性能。
本文将介绍机械加工过程中常用的质量控制方法和技术。
I. 机械加工过程中的质量控制方法1. 技术规范的制定在机械加工过程中,首先需要制定详细的技术规范,包括各种参数的控制要求、加工工艺和质量标准等。
技术规范能够明确加工过程中的操作规程和质量要求,为后续的质量控制提供指导。
2. 设备的校准和维护机械加工过程中使用的各类设备,如数控机床、切削工具等都需要进行定期的校准和维护。
校准能够确保设备的精度和稳定性,而维护保养能够延长设备的使用寿命,并减少由于设备故障引起的加工质量问题。
3. 加工参数的监测和调整机械加工过程中的加工参数包括切削速度、进给速度、切削深度等。
通过实时监测和调整这些加工参数,可以保证加工过程中的稳定性和一致性,并避免加工中出现质量问题。
4. 质量检测和控制质量检测和控制是机械加工过程中最基础的质量控制环节。
通过使用各种检测设备和方法,如测量仪器、显微镜等,对加工过程中的尺寸、形状、表面质量等进行检测和判定。
对于不符合要求的产品,需要及时采取纠正措施,以保证产品达到质量标准。
II. 常用的质量控制技术1. 先进的数控技术随着科技的进步,先进的数控技术在机械加工过程中得到了广泛应用。
数控技术通过预先设定的程序来控制加工过程,实现高精度、高效率的加工作业。
同时,数控技术还能够监测加工过程中的各种参数,并根据实际情况进行自动调整,保证加工质量的稳定性。
2. 光学成像技术光学成像技术通过显微镜或相机等设备,对制件表面的质量进行实时观测和检测。
这种技术可以快速获得制件的表面形状、表面光滑度等质量指标,从而实现对加工质量的实时监控和控制。
3. 技术技术在机械加工过程中的质量控制中正发挥着越来越重要的作用。
通过对大量的数据进行分析和学习,技术能够自动识别和判断加工过程中的质量问题,并作出相应的调整和反馈。
机械加工质量技术控制[方案]
![机械加工质量技术控制[方案]](https://img.taocdn.com/s3/m/5b6b9735492fb4daa58da0116c175f0e7cd11916.png)
机械加工质量技术控制摘要:本文介绍了机械加工精度的概念及内容,分析了机械加工产生误差的原因,最后提出提高机械加工精度的工艺措施。
关键词:机械加工精度;几何误差;定位误差;工艺1机械加工精度的概念及内容机械加工精度是指零件加工后的实际几何参数(尺寸、形状和位置)与理想几何参数相符合的程度。
它们之间的差异称为加工误差。
加工误差的大小反映了加工精度的高低。
误差越大加工精度越低,误差越小加工精度越高。
加工精度包括三个方面内容:尺寸精度指加工后零件的实际尺寸与零件尺寸的公差带中心的相符合程度;形状精度指加工后的零件表面的实际几何形状与理想的几何形状的相符合程度;位置精度指加工后零件有关表面之间的实际位置与理想。
在相同中的各种因对准确和完足产品的工加工方法,的生产条件下所加工出来的一批零件,由于加工素的影响,其尺寸、形状和表面相互位置不会绝全一致,总是存在一定的加工误差。
同时,从满作要求的公差范围的前提下,要采取合理的经济以提高机械加工的生产率和经济性。
2机械加工产生误差主要原因2.1机床的几何误差加工中刀具相对于工件的成形运动一般都是通过机床完成的,因此,工件的加工精度在很大程度上取决于机床的精度。
机床制造误差对工件加工精度影响较大的有:主轴回转误差、导轨误差和传动链误差。
机床的磨损将使机床工作精度下降。
(1)主轴回转误差,机床主轴是装夹工件或刀具的基准,并将运动和动力传给工件或刀具,主轴回转误差将直接影响被加工工件的精度。
(2)导轨误差,导轨是机床上确定各机床部件相对位置关系的基准,也是机床运动的基准。
除了导轨本身的制造误差外,导轨的不均匀磨损和安装质量,也使造成导轨误差的重要因素。
导轨磨损是机床精度下降的主要原因之一。
(3)传动链误差,传动链误差是指传动链始末两端传动元件间相对运动的误差。
一般用传动链末端元件的转角误差来衡量。
2.2 刀具的几何误差刀具误差对加工精度的影响随刀具种类的不同而不同。
采用定尺寸刀具成形刀具展成刀具加工时,刀具的制造误差会直接影响工件的加工精度;而对一般刀具,其制造误差对工件加工精度无直接影响。
机械加工过程中的质量控制与检测技术
机械加工过程中的质量控制与检测技术在现代制造业中,机械加工是一个至关重要的环节,其质量直接影响到最终产品的性能、可靠性和使用寿命。
为了确保机械加工产品的质量符合设计要求和客户期望,质量控制与检测技术的应用不可或缺。
机械加工过程中的质量控制是一个系统性的工作,涵盖了从原材料采购到成品交付的整个生产流程。
在原材料阶段,就需要严格筛选,确保其性能和质量符合加工要求。
例如,钢材的硬度、韧性等指标必须经过精确检测,以避免在后续加工中出现裂纹、变形等问题。
加工设备的精度和稳定性对产品质量有着决定性的影响。
定期对机床进行维护保养,校准精度,能够有效地减少加工误差。
同时,操作人员的技能水平和工作态度也不容忽视。
熟练的操作人员能够根据加工材料的特性和工艺要求,合理调整加工参数,从而提高加工质量。
在工艺规划方面,科学合理的工艺路线和工艺参数是保证质量的关键。
通过对加工过程进行详细的分析和优化,能够降低废品率,提高生产效率。
例如,在切削加工中,选择合适的刀具、切削速度和进给量,可以减少刀具磨损,提高零件的表面质量和尺寸精度。
质量控制还包括对加工环境的管理。
温度、湿度、粉尘等环境因素都可能对加工精度产生影响。
因此,保持良好的加工环境,对于提高产品质量具有重要意义。
检测技术则是质量控制的重要手段。
常见的检测方法包括尺寸测量、形位公差检测、表面粗糙度检测等。
尺寸测量是最基本的检测项目之一。
常用的测量工具如卡尺、千分尺、量规等,能够精确测量零件的长度、直径、厚度等尺寸参数。
对于高精度的尺寸测量,还可以采用三坐标测量机等先进设备,它能够实现对复杂零件的三维测量,获取更加全面和精确的尺寸信息。
形位公差检测用于评估零件的形状和位置精度。
例如,圆度、圆柱度、平行度、垂直度等。
这些公差的检测通常需要使用专门的量具和仪器,如圆度仪、垂直度检测仪等。
表面粗糙度检测对于零件的耐磨性、密封性等性能有着重要影响。
常用的检测方法有比较法、触针法和光切法等。
试论机械加工质量技术控制
1 . 机械加 工产 生误 差主要原 因
一
一
是定位副制造不 准确误差 夹具 上的定 位元件 不可能按基 本尺寸制造 得绝对准确 .它们 的实 际尺寸都允许在分别 规定 的公差范 围内变动 。 工件定位 面与夹具定位元件共 同构成定位 副 , 由于定位副制造得不 准 确和定位副间 的配合 间隙引起 的工件最大位 置变 动量 , 称为定位 副制 造不准确误差 1 . 4 工艺系统受力变形产生 的误差 是工件刚度 。 工艺 系统 中如果工 件刚度相对 于机床 、 刀具 、 夹具 来说 比较低 . 在切削力 的作用下 . 工件 由于 刚度不足 而引起的变形对 加工精度 的影响就 比较 大。二是刀具刚度 。 外 圆车刀在加工 表面法 线 ( y ) 方向上 的刚度很 大 。 其变形可以忽略不计 。镗直径较小的 内孔 , 刀 杆刚度很差 . 刀杆受力变形对: f L  ̄ I 工精度就有很 大影响 。三是机床部
一
法 对加工精度要求高的零 件表 面 , 还可 以采取在不 断试 切加工过程 中. 逐步均化原始误差 的方法 2 . 3 . 1 分化原始误差 ( 分组1 法 根据误 差反映规律 . 将 毛坯或工序 的工件尺寸经测量按 大小 分为 n 组. 每组工件的尺寸范围就缩减 为原来 的 1 n 然后按各 组的误 差范 围分别调整刀具相对 工件 的准确位置 . 使各组工件 的尺寸分 散范围中 心基本一致 , 以使整批 工件的尺 寸分散范 围大大缩小 。 2 _ 3 . 2均化原始 误差 这种方法 的过程是通过加工 使被加工表 面原有误差不断缩小 和 平均化的过程 均化的原理就是通过有密切联系的工件或工具表面的 相互 比较和检查 . 从中找 出它们之 间的差异 . 然 后再 进行相互修 正加
Hale Waihona Puke 差 。加工误差 的大小反 映了加 工精度 的高低 。误 差越 大加 工精度越低 , 误 差越 小加 工精度越 高。
有关机械加工的质量控制技术的探讨
有关机械加工的质量控制技术的探讨摘要:自从工业技术革命之后,工业得到了快速的发展。
影响机械加工表面质量的因素有很多,我们必须掌握整个机械加工的各个环节,进而保证机械加工质量,提高产品的使用性能。
本文主要从两个方面阐述了机械加工质量的基本含义,进而阐述了影响机械加工质量的因素,供大家参考。
关键词:机械加工;精度质量;控制1 关于实际加工过程中出现的机械加工精度和误差机械加工精度主要是指设计零件时的实际的几何参数和理想中的几何参数之间的符合程度,在实际的加工过程中应该尽量保证二者是符合的,但是往往会出现偏差,我们称之为加工误差,这种误差是不可避免的,但是我们应该尽量的减少这种加工误差,进一步提高加工精度。
加工精度中主要有尺寸精度,位置精度,形状精度,这三者之间是相互联系的。
2 关于我们实践中的机械加工表面质量我们总是对事物追求完美,在实际的加工过程中也希望能够保证零件表面的质量达到完美,但是当前使用机械设备进行加工的现实是不能够实现这一点的,而且重视出现零件表面粗糙、波度等的形状上的误差,这不仅会影响到零件的使用性能,而且还影响到零件的可靠性和耐久性,所以我们必须加强对零件加工的重视程度,特别是表面质量,尽可能地达到标准。
3 机械加工表面质量对零件使用性能的影响3.1 影响耐磨性零件表面的粗糙程度直接影响零件的整体使用性能,具体的说当零件的表面粗糙度达到最大值时,零件和物体的实际接触面积就会越小,这样接触的应力就会变大就容易导致零件的磨损,但是如果零件表面的粗糙程度太小的话,就会导致零件和物体之间出现粘结,导致润滑油膜被破坏,进而导致干摩擦出现很大程度的磨损。
3.2 影响疲劳强度零件加工质量的好坏也直接影响到疲劳强度。
因为在产生交变荷载时,就会导致零件的表面粗糙程度等问题出现应力集中的现象,进而直接影响零件的疲劳强度,此外,零件加工的表面纹路也会影响到疲劳强度,如果零件表面的纹路方向和受力方向是平行的情况,就会导致疲劳强度明显的提高;而且如果零件加工中的硬化过度也会造成疲劳强度的下降。
机械加工成品质量技术指标或者标准
机械加工成品质量技术指标或者标准机械加工成品的质量技术指标或标准是指用于评估和衡量机械加工成品质量的各种要素和要求。
这些指标或标准可以帮助制造商和用户确定成品是否符合预期的要求,并确保其质量以满足用户需求。
以下是一些常见的机械加工成品质量技术指标或标准。
1.尺寸精度:尺寸精度是机械加工成品中最重要的指标之一。
它指的是成品与设计尺寸之间的差异。
常见的尺寸精度标准包括公差和尺寸偏差。
对于某些关键零部件,如发动机配件或航空航天部件,尺寸精度可能非常高,因为它们的功能和性能可能受到微小尺寸差异的影响。
2.表面粗糙度:表面粗糙度是指机械加工成品表面的纹理和光洁度。
高品质的机械加工成品应具有平滑、均匀的表面,以确保其与其他部件的贴合和运动的顺畅。
表面粗糙度可以通过测量平均粗糙度、峰值高度等参数来评估。
3.功能性能:机械加工成品的功能性能指其在特定工作条件下执行所需功能的能力。
这取决于成品的材料、设计和加工质量等因素。
功能性能测试可能包括强度测试、疲劳寿命测试、耐腐蚀性测试等,以确保成品能够在预期的使用环境下可靠地工作。
4.材料性能:材料性能是机械加工成品质量的关键要素之一。
它指的是成品所使用材料的物理、化学和力学性能。
常见的材料性能指标包括强度、硬度、韧性、耐磨性、耐腐蚀性等。
制造商必须选择具有适当材料性能的材料以满足成品的需求,并确保最终产品的质量。
5.安全性能:对于某些机械加工成品,如汽车零部件或医疗设备,安全性能是至关重要的。
安全性能指成品在使用时对人、设备或环境造成的潜在危险程度。
制造商必须遵守相关的安全标准和法规,以确保成品的安全性能达到要求。
6.可靠性:可靠性是指机械加工成品在一定时间内保持稳定和无故障运行的能力。
可靠性工程是通过使用可靠性分析和测试方法来评估和改进成品的可靠性。
对于一些关键应用领域,如航空航天、医疗和能源等,可靠性要求非常高,因为成品的故障可能导致严重的后果。
综上所述,机械加工成品的质量技术指标或标准涉及尺寸精度、表面粗糙度、功能性能、材料性能、安全性能和可靠性等多个方面。
- 1、下载文档前请自行甄别文档内容的完整性,平台不提供额外的编辑、内容补充、找答案等附加服务。
- 2、"仅部分预览"的文档,不可在线预览部分如存在完整性等问题,可反馈申请退款(可完整预览的文档不适用该条件!)。
- 3、如文档侵犯您的权益,请联系客服反馈,我们会尽快为您处理(人工客服工作时间:9:00-18:30)。
试论机械加工质量技术控制
【摘要】本文介绍了机械加工精度的概念及内容,分析了机械加工产生误差的原因,最后提出提高机械加工精度的工艺措施。
【关键词】机械加工精度;几何误差;定位误差;工艺
1 机械加工精度的概念及内容
机械加工精度是指零件加工后的实际几何参数(尺寸、形状和位置)与理想几何参数相符合的程度。
它们之间的差异称为加工误差。
加工误差的大小反映了加工精度的高低。
误差越大加工精度越低,误差越小加工精度越高。
加工精度包括三个方面内容:尺寸精度指加工后零件的实际尺寸与零件尺寸的公差带中心的相符合程度;形状精度指加工后的零件表面的实际几何形状与理想的几何形状的相符合程度;位置精度指加工后零件有关表面之间的实际位置与理想。
2 机械加工产生误差主要原因
2.1机床的几何误差
加工中刀具相对于工件的成形运动一般都是通过机床完成的,因此,工件的加工精度在很大程度上取决于机床的精度。
机床制造误差对工件加工精度影响较大的有:主轴回转误差、导轨误差和传动链误差。
机床的磨损将使机床工作精度下降。
(1)主轴回转误差,机床主轴是装夹工件或刀具的基准,并将运动和动力传给工件或刀具,主轴回转误差将直接影响被加工工件的精度。
(2)导轨误差,导轨是机床上确定各机床部件相对位置关系的基准,也是机床运动
的基准。
除了导轨本身的制造误差外,导轨的不均匀磨损和安装质量,也使造成导轨误差的重要因素。
导轨磨损是机床精度下降的主要原因之一。
(3)传动链误差,传动链误差是指传动链始末两端传动元件间相对运动的误差。
一般用传动链末端元件的转角误差来衡量。
2.2 刀具的几何误差
刀具误差对加工精度的影响随刀具种类的不同而不同。
采用定尺寸刀具成形刀具展成刀具加工时,刀具的制造误差会直接影响工件的加工精度;而对一般刀具,其制造误差对工件加工精度无直接影响。
夹具的几何误差:夹具的作用时使工件相当于刀具和机床具有正确的位置,因此夹具的制造误差对工件的加工精度有很大影响。
2.3 定位误差
一是基准不重合误差。
在零件图上用来确定某一表面尺寸、位置所依据的基准称为设计基准。
在工序图上用来确定本工序被加工表面加工后的尺寸、位置所依据的基准称为工序基准。
在机床上对工件进行加工时,须选择工件上若干几何要素作为加工时的定位基准,如果所选用的定位基准与设计基准不重合,就会产生基准不重合误差。
二是定位副制造不准确误差。
夹具上的定位元件不可能按基本尺寸制造得绝对准确,它们的实际尺寸都允许在分别规定的公差范围内变动。
2.4 工艺系统受力变形产生的误差
一是工件刚度。
工艺系统中如果工件刚度相对于机床、刀具、夹具来说比较低,在切削力的作用下,工件由于刚度不足而引起的变形对加工精度的影响就比较大。
二是刀具刚度。
外圆车刀在加工表面法线(y)方向上的刚度很大,其变形可以忽略不计。
镗直径较小的内孔,刀杆刚度很差,刀杆受力变形对孔加工精度就有很大影响。
三是机床部件刚度。
机床部件由许多零件组成,机床部件刚度迄今尚无合适的简易计算方法,目前主要还是用实验方法来测定机床部件刚度。
2.5 工艺系统受热变形引起的误差
工艺系统热变形对加工精度的影响比较大,特别是在精密加工和大件加工中,由热变形所引起的加工误差有时可占工件总误差的50%。
机床、刀具和工件受到各种热源的作用,温度会逐渐升高,同时它们也通过各种传热方式向周围的物质和空间散发热量。
2.6 调整误差
在机械加工的每一工序中,总要对工艺系统进行这样或那样的调整工作。
由于调整不可能绝对地准确,因而产生调整误差。
在工艺系统中,工件、刀具在机床上的互相位置精度,是通过调整机床、刀具、夹具或工件等来保证的。
当机床、刀具、夹具和工件毛坯等的原始精度都达到工艺要求而又不考虑动态因素时,调整误差的影响,对加工精度起到决定性的作用。
3 提高加工精度的工艺措施
3.1 减少原始误差
提高加工零件所使用机床的几何精度,提高夹具、量具及工具本身精度,控制工艺系统受力、受热变形产生的误差,减少刀具磨损、内应力引起的变形误差,尽可能减小测量误差等均属于直接减少原始误差。
为了提高机加工精度,需对产生加工误差的各项原始误差进行分析,根据不同情况对造成加工误差的主要原始误差采取相应的解决措施。
对于精密零件的加工应尽可能提高所使用精密机床的几何精度、刚度和控制加工热变形;对具有成形表面的零件加工,则主要是如何减少成形刀具形状误差和刀具的安装误差。
3.2 误差补偿法
对工艺系统的一些原始误差,可采取误差补偿的方法以控制其对零件加工误差的影响。
3.2.1 误差补偿法:该方法是人为地造出一种新的原始误差,从而补偿或抵消原来工艺系统中固有的原始误差,达到减少加工误差,提高加工精度的目的。
3.2.2 误差抵消法:利用原有的一种原始误差去部分或全部地抵消原有原始误差或另一种原始误差。
4 结语
总之,在机加工过程中,产生误差是不可避免的。
只有对误差产生的原因进行详细的分析,才能采取相应的预防措施以尽可能地减少加工误差,从而有效提高机加工的精度。
参考文献
1 郑渝.机械结构损伤检测方法研究[d];太原理工大学; 2004
年
2 杨春雷等.浅谈机械加工影响配合表面的原因及对策[n].中华建筑报; 2005年。