机械加工质量概述
机械加工质量及其控制概述ppt68页课件

二、机械加工表面质量
(一)表面质量的概念
粗糙度太大、太小都不耐磨
适度冷硬能提高耐磨性
对疲劳强度的影响
对耐腐蚀性能的影响
对工作精度的影响
粗糙度越大,疲劳强度越差
适度冷硬、残余压应力能提高疲劳强度
粗糙度越大、工作精度降低
残余应力越大,工作精度降低
粗糙度越大,耐腐蚀性越差
压应力提高耐腐蚀性,拉应力反之则降低耐腐蚀性
本章提要
机械产品质量取决于零件的加工质量和产品的装配质量,机器零件的加工质量是整台机器质量的基础。 机器零件的加工质量一般用机械加工精度和加工表面质量两个重要指标表示,它的高低将直接影响整台机器的使用性能和寿命。 机械产品加工的首要任务,就是保证零件的机械加工质量要求。 本章重点讨论影响机械加工精度和表面质量的因素及其控制方法。
(1)主轴回转误差
第二节 机械加工精度的影响因素及控制
一、工艺系统几何误差对加工精度的影响
(一)机床的几何误差
(1)主轴回转误差
第二节 机械加工精度的影响因素及控制
一、工艺系统几何误差对加工精度的影响
(一)机床的几何误差
主轴回转误差的基本形式
车床上车削
镗床上镗削
内、外圆
端面
螺纹
孔
端面
纯径向跳动
机械加工中,采用近似的成形运动或近似的刀刃形状进行加工,虽然会由此产生一定的原理误差,但却可以简化机床结构和减少刀具数,只要加工误差能够控制在允许的制造公差范围内,就可采用近似加工方法。
原始误差
工艺系统动误差
工艺系统受力变形
刀具磨损
残余应力引起变形
测量误差
工艺系统热变形
第二节 机械加工精度的影响因素及控制
机械加工质量及控制
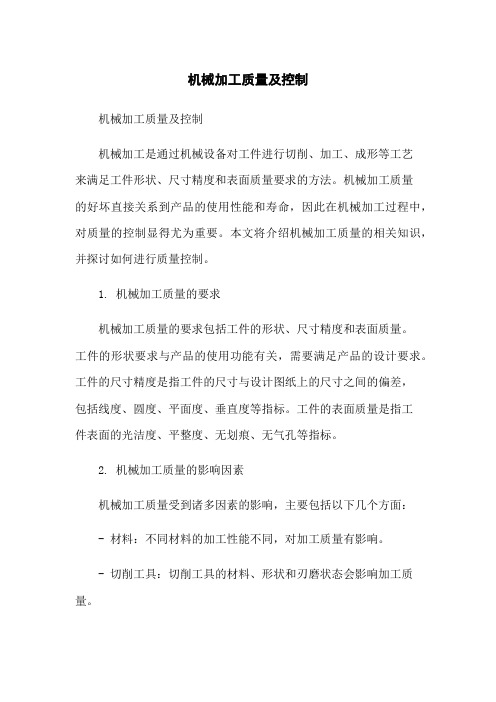
机械加工质量及控制机械加工质量及控制机械加工是通过机械设备对工件进行切削、加工、成形等工艺来满足工件形状、尺寸精度和表面质量要求的方法。
机械加工质量的好坏直接关系到产品的使用性能和寿命,因此在机械加工过程中,对质量的控制显得尤为重要。
本文将介绍机械加工质量的相关知识,并探讨如何进行质量控制。
1. 机械加工质量的要求机械加工质量的要求包括工件的形状、尺寸精度和表面质量。
工件的形状要求与产品的使用功能有关,需要满足产品的设计要求。
工件的尺寸精度是指工件的尺寸与设计图纸上的尺寸之间的偏差,包括线度、圆度、平面度、垂直度等指标。
工件的表面质量是指工件表面的光洁度、平整度、无划痕、无气孔等指标。
2. 机械加工质量的影响因素机械加工质量受到诸多因素的影响,主要包括以下几个方面:- 材料:不同材料的加工性能不同,对加工质量有影响。
- 切削工具:切削工具的材料、形状和刃磨状态会影响加工质量。
- 加工工艺:包括切削速度、进给量、切屑清除等,对加工质量有重要影响。
- 加工设备:加工设备的精度、刚性和稳定性对加工质量有直接影响。
- 操作技术:操作人员的技术水平和经验对加工质量有很大的影响。
3. 机械加工质量的控制方法为了保证机械加工质量,需要采取一系列的控制方法。
3.1 设计合理性控制这是机械加工质量控制的首要环节。
设计时需要考虑工件的功能和使用要求,并根据不同材料的加工性能确定合适的工艺参数。
3.2 切削工具的选择和维护切削工具的选择应根据加工工件的材料和形状来确定,同时需要定期进行刃磨和维护,确保切削工具的良好状态。
3.3 加工工艺的控制合理的加工工艺参数包括切削速度、进给量、冷却液的使用等。
在加工过程中需要严格控制这些参数,以保证工件的尺寸精度和表面质量。
3.4 加工设备的维护和调整加工设备的精度、刚性和稳定性对加工质量有直接影响。
定期对设备进行维护和调整,保持其良好状态。
3.5 操作人员的培训和管理操作人员的技术水平和经验对加工质量至关重要。
机械加工质量
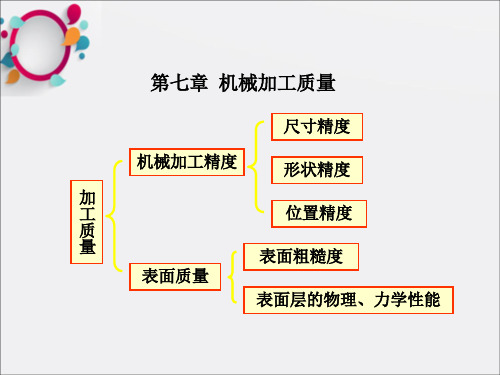
(4)调整误差 机械加工过程中的每一道工序都要进行各种各样 的调整工作,由于调整不可能绝对准确,因此必 然会产生误差,这些误差称为调整误差。
2、工艺系统的受力变形 (1)工艺系统的刚度 机械加工过程中,工艺系统在切削力、传动力、惯
性力、夹紧力、重力等外力的作用下,各环节将 产生相应的变形,使刀具和工件间已调整好的正 确位置关系遭到破坏而造成加工误差。例如,在 车床上车削细长轴时,工件在切削力的作用下会 发生变形,使加工出的工件出现两头细中间粗的 腰鼓形
第七章 机械加工质量
尺寸精度
机械加工精度
形状精度
加 工 质 量
表面质量
位置精度 表面粗糙度
表面层的物理、力学性能
第一节 概述 一、机械加工精度 1、机械加工精度的概念
所谓机械加工精度,是指零件在加工后的几何 参数(尺寸大小、几何形状、表面间的相互位 置)的实际值与理论值相符合的程度。符合程 度高,加工精度也高;反之则加工精度低。机 械加工精度包括尺寸精度、形状精度、位置精 度三项内容,三者有联系,也有区别。
3)定尺寸刀具法 用具有一定形状和尺寸精度的刀 具进行加工,使加工表面达到要求的形状和尺寸的 加工方法。如用钻头、铰刀、键槽铣刀等刀具的加 工即为定尺寸刀具法。定尺寸刀具法生产率较高, 加工精度较稳定,广泛的应用于各种生产类型。 4)自动控制法 把测量装置、进给装置和控制机构 组成一个自动加工系统,使加工过程中的尺寸测量、 刀具的补偿和切削加工一系列工作自动完成,从而 自动获得所要求的尺寸精度的加工方法。该方法生 产率高,加工精度稳定,劳动强度低,适应于批量 生产。
原始误差主要来自两方面:一方面是在加工前就存 在的工艺系统本身的误差(几何误差),包括加 工原理误差,机床、夹具、刀具的制造误差,工 件的安装误差,工艺系统的调整误差等;另一方 面是加工过程中工艺系统的受力变形、受热变形、 工件残余应力引起的变形和刀具的磨损等引起的 误差,以及加工后因内应力引起的变形和测量引 起的误差等。
《机械加工质量》课件
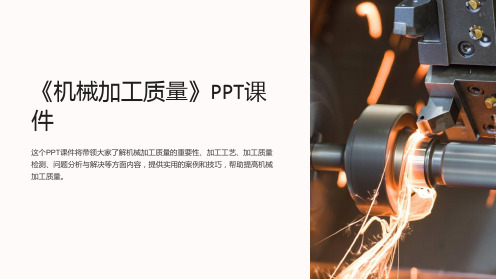
加工质量问题的预防措施
提出预防加工质量问题的措施, 如工艺参数优化、设备维护等。
总结
机械加工质量对产品的性能和外观等方面具有重要意义,通过合理的加工工艺和质量控制手段,能够提 高加工质量并增强市场竞争力。 感谢大家的聆听,希望这份课件对您在机械加工质量方面的学习和工作有所助益。
参考文献
• 加工质量检测技术手册 • 机械加工质量分析与解决实例集锦 • 机械加工质量问题预防手册
加工质量检测的方法
包括外观检测、测量检测、性能测试等多种方法。
加工质量检测的技术手段
如先进的精密测量仪器、非接触式见加工质量问题及其 原因
如尺寸偏差、表面质量不佳等 问题的常见原因分析。
加工质量问题解决的方 法与技巧
谈论如何排除加工过程中的质 量问题,提出解决方法和应对 策略。
《机械加工质量》PPT课 件
这个PPT课件将带领大家了解机械加工质量的重要性、加工工艺、加工质量 检测、问题分析与解决等方面内容,提供实用的案例和技巧,帮助提高机械 加工质量。
机械加工质量
机械加工质量是指在加工过程中所要求的工件尺寸、形状、表面质量等能够达到预定要求的程度。 机械加工质量的重要性体现在产品的性能、寿命、外观等各个方面,直接影响产品质量的好坏和市场竞 争力。
加工工艺
1
加工工艺流程介绍
从原材料准备、工艺规划、加工设备选择到加工操作流程和工艺参数设定等。
2
加工工艺参数影响
如切削速度、进给量、切削深度等参数如何影响加工质量的好坏。
3
加工前的准备工作
包括材料检查、设备准备、刀具选择、辅助装置安装等。
加工质量检测
加工质量检测的目的
通过检测,及时发现加工质量问题,确保产品符合要求。
机械加工质量分析及控制精简版范文
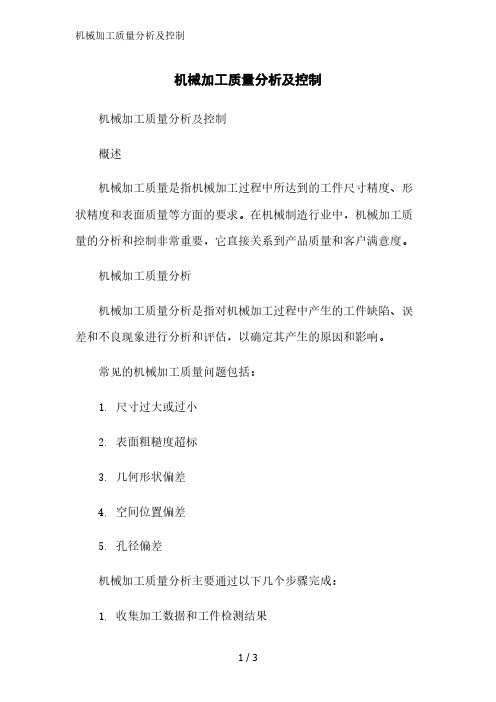
机械加工质量分析及控制
机械加工质量分析及控制
概述
机械加工质量是指机械加工过程中所达到的工件尺寸精度、形状精度和表面质量等方面的要求。
在机械制造行业中,机械加工质量的分析和控制非常重要,它直接关系到产品质量和客户满意度。
机械加工质量分析
机械加工质量分析是指对机械加工过程中产生的工件缺陷、误差和不良现象进行分析和评估,以确定其产生的原因和影响。
常见的机械加工质量问题包括:
1. 尺寸过大或过小
2. 表面粗糙度超标
3. 几何形状偏差
4. 空间位置偏差
5. 孔径偏差
机械加工质量分析主要通过以下几个步骤完成:
1. 收集加工数据和工件检测结果
2. 对数据进行统计分析和图像处理
3. 利用统计分析结果,确定质量问题的原因和影响因素
4. 提出相关改善措施和加工优化建议
机械加工质量控制
机械加工质量控制是指通过控制加工参数和采用合理的加工工艺,确保机械加工过程中所达到的工件质量能够满足设计要求和客户需求。
常见的机械加工质量控制方法包括:
1. 控制加工参数,如刀具刃口半径、加工速度、进给量等
2. 采用合适的加工工艺,如铣削、车削、钻削等
3. 使用高精度的测量设备进行质量检测和纠正
4. 实施质量管理体系和质量控制标准
机械加工质量控制的关键在于不断优化和改进加工工艺、设备和管理体系,以提高加工稳定性和质量可靠性。
结论
机械加工质量分析和控制是机械制造过程中必不可少的环节,它直接关系到产品的质量和市场竞争力。
通过科学的分析和有效的
控制措施,能够提高机械加工的质量稳定性和可靠性,满足客户的需求。
机械加工质量分析及控制

机械加工质量分析及控制机械加工质量分析及控制一、引言二、机械加工质量分析机械加工质量的分析主要包括以下几个方面:1.表面粗糙度分析机械加工的表面粗糙度对于产品的外观和性能有着重要影响。
通过使用表面粗糙度测量仪器,可以对机械加工的表面粗糙度进行评估。
常用的表面粗糙度参数包括Ra、Rz等。
2.尺寸精度分析机械加工的尺寸精度是指产品的实际尺寸和设计图纸上的尺寸之间的偏差。
通过使用测量工具和仪器,可以对机械加工的尺寸精度进行评估。
常用的尺寸精度参数包括公差、尺寸偏差等。
3.形状偏差分析机械加工的形状偏差是指产品的实际形状和设计图纸上的形状之间的偏差。
通过使用形状测量仪器,可以对机械加工的形状偏差进行评估。
常用的形状偏差参数包括圆度误差、平面度误差等。
三、机械加工质量控制为了确保机械加工的质量,需要进行相应的控制措施。
以下是几个常用的机械加工质量控制方法:1.工艺参数控制调整机械加工的工艺参数,可以对机械加工的质量进行控制。
例如,通过调整切削速度、进给速度和切削深度等参数,可以控制机械加工的表面粗糙度和尺寸精度。
2.设备状态监控对机械加工设备的状态进行监控,可以及时发现并修复设备故障,避免对产品质量的影响。
常用的设备状态监控方法包括振动监测、温度监测等。
3.质量检验与统计分析对机械加工的产品进行质量检验,并进行统计分析,可以及时发现并纠正加工过程中的问题。
常用的质量检验方法包括外观检查、尺寸测量等。
四、机械加工质量的分析和控制是确保产品质量的重要手段。
通过对表面粗糙度、尺寸精度和形状偏差等进行分析,可以找出问题所在。
通过工艺参数控制、设备状态监控和质量检验与统计分析等控制措施,可以提高机械加工的质量水平。
机械加工质量控制措施
工艺系统—机械加工时,机床、夹具、
刀具和工件构成一个相互联系的统一系统。 原始误差—工艺系统中存在的各种误差。
原始误差(原因)— 加工误差(结果)
返回本章目 录
例:滚齿时的加工误差形成
2 1 原 始 误 差
原理误差 工件装夹误差 机床误差 夹具误差 刀具误差 度量误差 工艺系统受力变形 工艺系统热变形
(2)调整法: 预先调整好刀具和工件在机床上的相对置, 并在一批零件的加工过程中始终保持这个位置不 变,以保证被加工零件尺寸的方法。 特点: ①尺寸稳定 ; ②生产率高 ; ③加工精度与操作工人的水平关系不大,主要 决定于调整精度。 应用:广泛于成批及大量生产。
(4)自动控制法: 这种方法是把测量装置,进 给装置和控制系统等组成一 个自动控制的加工系统。 特点: ①自动化程度高,精度高; ②适用于批量或大量生产。
磨 损 量 2 Ⅲ 工作时间 O O1
1-轻载荷
Ⅰ Ⅱ
1
Ra
Ⅰ—初期磨损 Ⅱ—正常磨损 Ⅲ—急剧磨损
O2
2-重载荷
图6-2 初期磨损量△与粗糙度Ra的关系
② 表面物理机械性能对耐磨性的影响 ⅰ.冷作硬化N ↑(适度)→ 耐磨性 ↑ (表面强度提高) 冷作硬化N ↑(过度)→ 耐磨性 ↓(表 面金相组织疏松,甚至出现裂纹和剥落) ⅱ.金相组织变化→耐磨性 ↓(改变表 面硬度)
返回本章目
3) 表面质量对配合精度的影响 表面粗糙度Ra大 ①间隙配合初期磨损量大,间隙值增大 ②过盈配合部分凸峰被挤平,过盈量减小 4) 表面质量对耐腐蚀性的确影响 表面粗糙度Ra↑— 耐腐蚀性↓ (由于电化学腐蚀作用) 5) 其它影响
返回本章目 录
6.2
机械加工精度
6.2.1 原始误差与加工误差
第七节 机械加工表面质量
3 表面层的残余应力
• 由于切削力和热的综合作用,表面层金属晶格 会发生不同程度的塑性变形或产生金相组织变 化,使表面层产生残余应力。
(三)表面质量的内容
表面粗糙度 表面微观几何 形状特征 表面波度
零件表面质量
表面物理力学 性能的变化 表面层冷作硬化 表面层残余应力 表面层金相组织的变化
二、表面质量对零件使用性能的影响
1.影响切削加工后表面粗糙度的因素
(c)刀尖圆弧半径
• 刀尖圆弧半径增加,从几何因素来看会减小表 面粗糙度值。但会增加切削过程中的挤压,塑 性变形增大,使表面粗糙度值增加。 •
(d)刃倾角
• 增大刃倾角,对降低表面粗糙度有利。因为刃 倾角增大,实际工作前角也随之增大,切削过 程中的金属塑性变形程度随之下降,这会显著 地减轻工艺系统的振动,从而使加工表面的粗 糙度下降。
2.影响磨削加工后表面粗糙度的因素
(4)砂轮材料
• 砂轮材料可分为氧化物系(刚玉)、碳 化物系(碳化硅、碳化硼)和高硬磨料 系(人造金刚石、立方氮化硼)。 • 氧化物系:适于磨削钢类零件 • 碳化物系:磨削铸铁、硬质合金等材料
• 高硬磨料:可获得极小的表面粗糙度值, 但加工成本很高。
2.影响磨削加工后表面粗糙度的因素
(5)砂轮的修整
• 修整工具有单颗粒金刚石笔和金刚石滚轮,也 可用白口铸铁或砂轮来修整,以单颗粒金刚石 笔修整的质量为最好。 • 修整砂轮的纵向进给量愈小,磨削的表面粗糙 度值愈小。
2.影响磨削加工后表面粗糙度的因素
(6)砂轮速度
• 砂轮速度越高,就有可能使表层金属塑性变形 的传播速度大于切削速度,工件材料来不及变 形,致使表层金属的塑性变形减小,磨削表面 的粗糙度值将明显减小。
机械加工质量及其控制培训课件
机械加工质量的控制是提高产品质量的关键环节。
质量标准
机械加工质量的定义:指机械加工产品满足设计要求、技术标准和客户需求的程度
质量标准分类:国家标准、行业标准、企业标准、客户标准等
质量标准制定依据:产品设计要求、技术标准、客户需求、生产工艺等
质量标准评价方法:检验、测量、试验、分析等方法,对机械加工产品进行质量评价和检验
03
培训效果评估:考核、反馈、改进等
04
检测方法
01
目视检测:通过肉眼观察零件表面,判断是否存在缺陷
03
仪器检测:使用光学显微镜、电子显微镜等仪器观察零件表面,判断是否存在缺陷
02
量具检测:使用卡尺、千分尺等量具测量零件尺寸,判断是否合格
04
试验检测:通过模拟实际使用环境,测试零件的性能和可靠性,判断是否合格
行业标准:机械加工行业相关标准
企业标准:企业内部制定的质量检测标准
问题分析
B
D
AБайду номын сангаас
C
加工精度问题:加工精度不足,导致产品不合格
加工成本问题:加工成本过高,影响企业效益
加工效率问题:加工效率低下,影响生产进度
加工环境问题:加工环境恶劣,影响员工健康和安全
改进措施
01
优化工艺流程:合理规划加工步骤,提高效率
02
提高设备精度:定期维护和保养设备,确保加工精度
03
加强人员培训:提高员工技能水平,减少人为误差
04
引入质量管理体系:建立完善的质量管理体系,确保质量控制有效进行
持续改进
持续改进的概念:持续改进是一种持续、系统地改进产品质量、工艺和生产效率的方法。
01
持续改进的方法:包括PDCA循环、六西格玛管理、精益生产等。
机械加工质量
提高劳动生产率的措施
缩减时间定额 采用先进工艺方法
工艺过程的技术经济性
强调的是经济性
不同的方案,经济性不同
获得加工精度 的方法 ①相关表面在一次安装中加工,由机床和夹具的精度来保证工件位置精度。
加工误差:两者间的偏差程度称加工误差。
(2)获得形状精度的方法。 保证和提高加工精度的方法
是指工人在单位时间内制造合格品的数量,或者指制造单件产品所消耗的劳动时间。
(1)获得零件尺寸精度的方法。 主(要1)包获括得表零面件层尺的寸加精工度硬的化方、法表。面层的金相组织变化和表面层的残余应力。
表面层的物理、力②学性有能的关变表化 面互为定位基准进行加工,可以保证这些表面之间有较 (2)获得形状精度高的的方法位。 置精度。
是指工人在单位时间内制造合格品的数量,或者指制造单件产品所消耗的劳动时间。
工艺过程的技术经济性
影响加工精度的因素
原理误差 机床的几何误差 工艺系统其它几何误差 工艺系统受力变形 工艺系统热变形 内应力引起的变形
①试切法 (①2相)关获表得面形在状一精次度安的装方中法加。工,由机床和夹具的精度来保证工件位置精度。 ②调整法 ①相关表面在一次安装中加工,由机床和夹具的精度来保证工件位置精度。 ③定尺寸刀具法 ①相关表面在一次安装中加工,由机床和夹具的精度来保证工件位置精度。
①相关表面在一次安装中加工,由机床和夹具的精度来保证工件位置精度。
③成形法 工表艺面过 层程的的物技理术、经力济学性性能的变化
(3)保证位(置精3度)的方保法 证位置精度的方法
劳动生产率一般通过时间定额来衡量
影响表面物理、力①学性相能的关因表素及面其控在制一次安装中加工,由机床和夹具的精度来保证工件 机械加工质量、生位产率置和经精、生产率和经济性
- 1、下载文档前请自行甄别文档内容的完整性,平台不提供额外的编辑、内容补充、找答案等附加服务。
- 2、"仅部分预览"的文档,不可在线预览部分如存在完整性等问题,可反馈申请退款(可完整预览的文档不适用该条件!)。
- 3、如文档侵犯您的权益,请联系客服反馈,我们会尽快为您处理(人工客服工作时间:9:00-18:30)。
影响加工精度的因素及其分析
在机械加工中,零件的尺寸、几何形状和表面间相对位 置的形成,取决于工件和刀具在切削运动过程中相互位置的 关系。零件的机械加工是在由机床、夹具、刀具和工件组成 的系统中进行的。该系统即为工艺系统。
工艺系统存在的误差称之为原始误差;原始误差是造成 加工误差的根源。
原始误差的存在,使工艺系统各组成部分之间的位置关 系或速度关系偏离了理想状态,致使加工后的零件产生了加 工误差。
产生径向圆跳动误差的主要原因有:主轴支承轴颈的圆度 误差、轴承工作表面的圆度误差等。
车削或镗削圆柱面时将会造成圆柱度误差,但对加工精度 的影响不同。
4.1 机床误差
对于刀具回转类机床,如钻床、铣 镗床等,切削力的方向随旋转方向改变 ,此时,主轴的支承轴颈的圆度误差影 响较小,而轴承孔圆度误差影响较大。
第四章 机械加工质量
§1机械加工质量概述 §2产生加工误差的主要因素 §3表面质量的形成及影响因素 §4加工质量对机器零件使用性能的影响
本章提要
机器零件的加工质量是整台机器质量的基础。机器零件 的加工质量一般用机械加工精度和加工表面质量两个重要 指标表示,它的高低将直接影响整台机器的使用性能和寿 命。本章研究机械加工精度的问题。
三、获得工件形状精度的方法 获得工件形状精度的方法有:轨迹法、成形法、展成法
加工精度和加工误差
加工误差:实际加工不可能做得与理想零件完全一致, 总会有大小不同的偏差,零件加工后的实际几何参数对理 想几何参数的偏离程度,称为加工误差。
加工误差的大小表示了加工精度的高低。生产实际中 用控制加工误差的方法来保证加工精度。
1.2 零件加工质量的构成
• 1) 加工精度: • 尺寸精度, • 形状精度, • 位置精度; • 2) 表面质量: • 表面粗糙度及波度,
表层物理机械性能。 见零件加工质量列表来自二 产生加工误差的主要因素
• 由机床-夹具-刀具-工件构成一个完整的加工系 统,称为工艺系统。工艺系统的各因素,加工 过程中可能会以不同的形式、程度反映在工件 上,形成加工误差,称为原始误差。
加工精度和加工误差是从两种观点来评定零件几何参 数,所谓保证和提高加工精度问题就是限制和降低加工误 差问题。
研究机械加工精度的方法
因素分析法:通过分析、计算或实验、测试等方法,研究 某一确定因素对加工精度的影响。一般不考虑其它因素的同时 作用,主要是分析各项误差单独的变化规律。
统计分析法:运用数理统计方法对生产中一批工件的实测 结果进行数据处理,用以控制工艺过程的正常进行。主要是研 究各项误差综合的变化规律,只适合于大批、大量的生产条件
本章讨论的内容有机械加工精度的基本概念、影响加工 精度的因素、加工误差的综合分析及提高加工精度的途 径四个方面。
一 机械加工质量概述
1.1 产品质量的概念 ➢ 产品质量,通常是指产品功能及其可靠性的
优劣程度。是人们对产品满意程度的总体评价。 ➢ 机械产品质量,实质上是指机械产品在其全
寿命周期表现出的优劣程度。也就是说,机械 产品质量本身,已经涵盖了产品的设计、制造、 销售、使用、服务、报废全过程。而机械加工 质量,则是指零件机械加工的优劣程度。
影响加工精度的因素及其分析
加工原理误差
机床误差
工艺系统静误差 夹具误差
工件装夹误差
刀具制造误差
原
始 调整误差 误 差
工艺系统受力变形
工艺系统动误差
工艺系统热变形
刀具磨损
测量误差
残余应力引起变形
加工前
加工中 加工后
影响加工精度的因素及其分析
4.1 机床误差
(一)机床刀轨的直线度 1)车床导轨在水平面内直线度误差
影响较小
y z2 d
4.1 机床误差
(二)机床主轴轴线与导轨平行度 (1)水平面内不平行,引起加工误差大,工件呈
锥体,锥度误差为 K=2a/L
例如,平行度误差a=0.03/300 mm 长度L=50mm的零件,产生直径误差
d 2 0.03 50 0.01mm 300
4.1 机床误差
(二)机床主轴轴线与导轨平行度 (2)垂直面内不平行,引起加工误差小,工件呈
影响加工精度的因素及其分析
若原始误差是在加工前已存在,即在无切削负荷的情况 下检验的,称为工艺系统静误差;若在有切削负荷情况下产 生的则称为工艺系统动误差。 原理误差:是指由于采用了近似的成形运动、近似的刀刃形 状等原因而产生的加工误差。 测量误差:是工件的测量尺寸与实际尺寸的差值。加工一般 精度的零件时,可占工序尺寸公差的1/5~1/10;加工精密零 件时,可占工序尺寸公差的1/3左右。
2)零件的形状精度:加工后零件的实际形状与零件理 想形状相符的程度。
3)零件的位置精度:加工后零件的实际位置与零件理 想位置相符的程度。
工件的装夹与获得加工精度的方法
一、位置精度的获得方法——装夹 装夹有三种主要的方法:直接装夹、找正装夹、夹具装夹 二、获得工件尺寸精度的方法
获得工件尺寸精度的方法有:试切法、调整法、定 尺寸刀具法、自动控制法
1:1反映到工件圆柱度误差上; 1:2反映到直径误差 2)车床导轨在垂直面内直线度误差 影响较小
y z2 d
4.1 机床误差
(一)机床刀轨的直线度 1)车床导轨在水平面内直线度误差
1:1反映到工件圆柱度误差上; 1:2反映到直径误差
4.1 机床误差
(一)机床刀轨的直线度 2)车床导轨在垂直面内直线度误差
• 产生加工误差的工艺因素可概括为七个方面, 即:工艺系统的制造精度与磨损、原理误差、 安装误差、工艺系统的受力变形、工艺系统的 受热变形、调整误差和度量误差。
加工精度和加工误差
加工精度是指零件加工后的实际几何参数(尺寸、形状 和位置)与理想几何参数的符合程度。
1)零件的尺寸精度:加工后零件的实际尺寸与零件理 想尺寸相符的程度。
双曲面回转体, 半径方向的误差为
r
r02
x2b2 L2
r0
4.1 机床误差
(三)机床主轴旋转时轴线位置的变化
• 主轴回转轴线的运动误差
可以分解为三种形式: 径向圆跳动;
a)径向圆跳动
端面圆跳动; 倾角摆动。
b)端面圆跳动
c)倾角摆动 主轴回转误差基本形式
4.1 机床误差
主轴径向跳动
径向跳动:主轴回转轴线相对于平均回转轴线在径向的变 动量。车外圆时它使加工面产生圆度和圆柱度误差 。