最新机械加工质量分析与控制
机械装配中的质量保证与质量控制的工艺改进案例分析
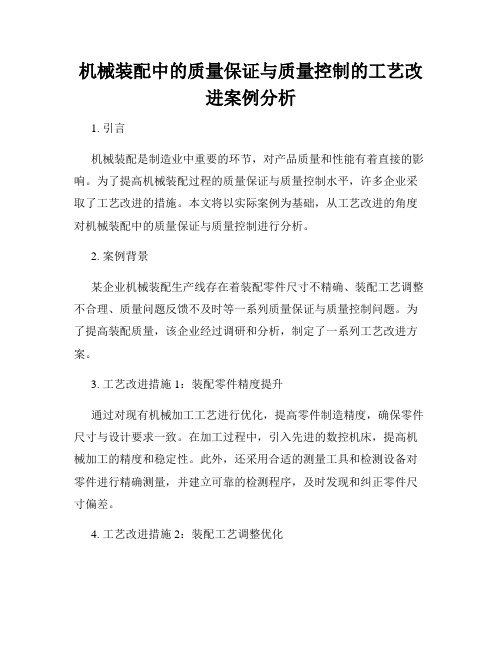
机械装配中的质量保证与质量控制的工艺改进案例分析1. 引言机械装配是制造业中重要的环节,对产品质量和性能有着直接的影响。
为了提高机械装配过程的质量保证与质量控制水平,许多企业采取了工艺改进的措施。
本文将以实际案例为基础,从工艺改进的角度对机械装配中的质量保证与质量控制进行分析。
2. 案例背景某企业机械装配生产线存在着装配零件尺寸不精确、装配工艺调整不合理、质量问题反馈不及时等一系列质量保证与质量控制问题。
为了提高装配质量,该企业经过调研和分析,制定了一系列工艺改进方案。
3. 工艺改进措施1:装配零件精度提升通过对现有机械加工工艺进行优化,提高零件制造精度,确保零件尺寸与设计要求一致。
在加工过程中,引入先进的数控机床,提高机械加工的精度和稳定性。
此外,还采用合适的测量工具和检测设备对零件进行精确测量,并建立可靠的检测程序,及时发现和纠正零件尺寸偏差。
4. 工艺改进措施2:装配工艺调整优化针对装配过程中的问题,通过优化工艺调整方法,提高装配效率和精确度。
首先,对装配顺序进行调整,合理安排零部件的装配顺序,减少装配过程中出现的问题。
其次,采用合适的装配工具和夹具,提高装配的精度和稳定性。
最后,建立标准化的装配操作规范,对装配人员进行培训,确保每个环节的执行符合要求。
5. 工艺改进措施3:质量问题反馈机制改进为了及时掌握装配过程中的质量问题,该企业建立了完善的质量问题反馈机制。
装配人员在发现问题后,立即向质量管理部门报告,并提供详细的问题描述和相关数据。
质量管理部门根据反馈的问题,分析原因并采取相应的纠正措施。
同时,对发现的问题进行记录和分析,为后续的质量改进提供参考。
6. 案例分析与效果评估通过对上述工艺改进措施的实施,该企业在机械装配中的质量保证与质量控制水平得到了显著提升。
首先,装配零件的精度得到了有效提升,减少了因零件尺寸偏差引起的装配问题。
其次,装配工艺调整的优化使得装配过程更加顺畅,提高了装配效率和质量稳定性。
机械加工质量控制

机械加工质量控制标题:机械加工质量控制引言概述:机械加工质量控制是一个关键的环节,直接影响到产品的质量和性能。
通过合理的质量控制措施,可以提高机械加工的精度和效率,降低产品的缺陷率和不合格率。
本文将从五个方面介绍机械加工质量控制的重要性和具体措施。
一、材料选择1.1 选择合适的材料:根据产品的要求和使用环境,选择适合的材料。
考虑材料的强度、硬度、耐磨性等特性,以确保产品的使用寿命和性能。
1.2 检查材料质量:对进货的材料进行严格的质量检查,包括外观、尺寸、化学成分等方面。
确保材料的质量符合标准要求,避免因材料质量问题导致的加工缺陷。
1.3 控制材料变形:在机械加工过程中,材料的变形会直接影响产品的尺寸精度和形状。
通过合理的加工工艺和工装设计,控制材料的变形,保证加工精度。
二、加工工艺控制2.1 设计合理的加工工艺:根据产品的要求和材料的特性,设计合理的加工工艺流程。
考虑加工顺序、切削参数、刀具选择等因素,以确保加工的精度和效率。
2.2 严格的加工过程控制:在加工过程中,严格执行加工工艺要求,控制各个环节的加工参数。
包括切削速度、进给量、刀具磨损等方面的控制,以保证加工的一致性和稳定性。
2.3 定期检查和维护设备:定期对加工设备进行检查和维护,确保设备的正常运行。
包括设备的润滑、刀具的更换、机床的校准等方面,以保证加工的稳定性和精度。
三、质量检验与控制3.1 制定合理的检验标准:根据产品的要求和行业标准,制定合理的质量检验标准。
包括尺寸精度、表面质量、材料成分等方面的要求,以确保产品的质量符合要求。
3.2 使用合适的检测设备:选择适合的检测设备和方法,对产品进行全面的质量检测。
包括三坐标测量机、硬度计、显微镜等设备的使用,以保证检测的准确性和可靠性。
3.3 建立完善的质量控制体系:建立完善的质量控制体系,包括质量记录、异常处理、追溯体系等方面。
通过对质量数据的分析和整理,及时发现和解决质量问题,提高产品的质量稳定性。
机械工程加工质量控制措施
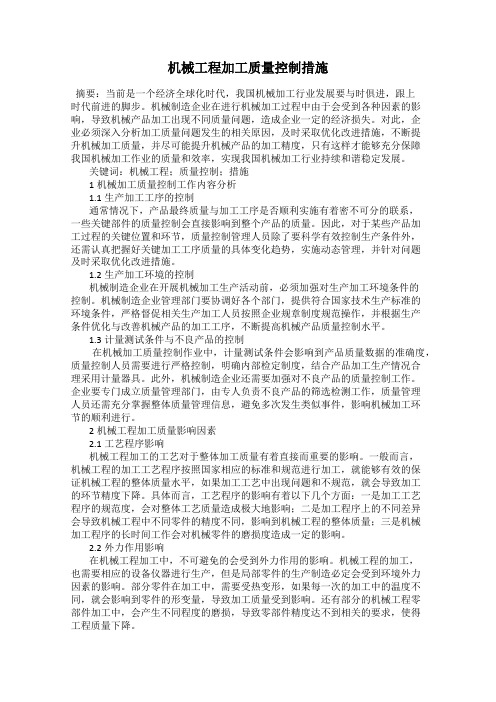
机械工程加工质量控制措施摘要:当前是一个经济全球化时代,我国机械加工行业发展要与时俱进,跟上时代前进的脚步。
机械制造企业在进行机械加工过程中由于会受到各种因素的影响,导致机械产品加工出现不同质量问题,造成企业一定的经济损失。
对此,企业必须深入分析加工质量问题发生的相关原因,及时采取优化改进措施,不断提升机械加工质量,并尽可能提升机械产品的加工精度,只有这样才能够充分保障我国机械加工作业的质量和效率,实现我国机械加工行业持续和谐稳定发展。
关键词:机械工程;质量控制;措施1机械加工质量控制工作内容分析1.1生产加工工序的控制通常情况下,产品最终质量与加工工序是否顺利实施有着密不可分的联系,一些关键部件的质量控制会直接影响到整个产品的质量。
因此,对于某些产品加工过程的关键位置和环节,质量控制管理人员除了要科学有效控制生产条件外,还需认真把握好关键加工工序质量的具体变化趋势,实施动态管理,并针对问题及时采取优化改进措施。
1.2生产加工环境的控制机械制造企业在开展机械加工生产活动前,必须加强对生产加工环境条件的控制。
机械制造企业管理部门要协调好各个部门,提供符合国家技术生产标准的环境条件,严格督促相关生产加工人员按照企业规章制度规范操作,并根据生产条件优化与改善机械产品的加工工序,不断提高机械产品质量控制水平。
1.3计量测试条件与不良产品的控制在机械加工质量控制作业中,计量测试条件会影响到产品质量数据的准确度,质量控制人员需要进行严格控制,明确内部检定制度,结合产品加工生产情况合理采用计量器具。
此外,机械制造企业还需要加强对不良产品的质量控制工作。
企业要专门成立质量管理部门,由专人负责不良产品的筛选检测工作,质量管理人员还需充分掌握整体质量管理信息,避免多次发生类似事件,影响机械加工环节的顺利进行。
2机械工程加工质量影响因素2.1工艺程序影响机械工程加工的工艺对于整体加工质量有着直接而重要的影响。
一般而言,机械工程的加工工艺程序按照国家相应的标准和规范进行加工,就能够有效的保证机械工程的整体质量水平,如果加工工艺中出现问题和不规范,就会导致加工的环节精度下降。
机械加工质量分析及控制精简版范文
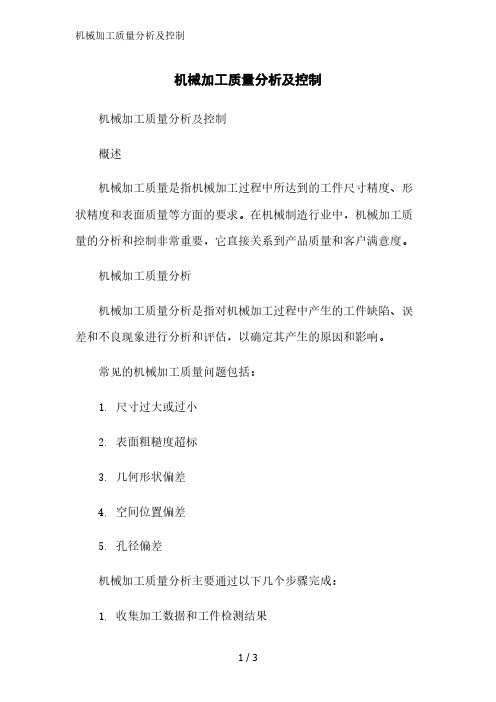
机械加工质量分析及控制
机械加工质量分析及控制
概述
机械加工质量是指机械加工过程中所达到的工件尺寸精度、形状精度和表面质量等方面的要求。
在机械制造行业中,机械加工质量的分析和控制非常重要,它直接关系到产品质量和客户满意度。
机械加工质量分析
机械加工质量分析是指对机械加工过程中产生的工件缺陷、误差和不良现象进行分析和评估,以确定其产生的原因和影响。
常见的机械加工质量问题包括:
1. 尺寸过大或过小
2. 表面粗糙度超标
3. 几何形状偏差
4. 空间位置偏差
5. 孔径偏差
机械加工质量分析主要通过以下几个步骤完成:
1. 收集加工数据和工件检测结果
2. 对数据进行统计分析和图像处理
3. 利用统计分析结果,确定质量问题的原因和影响因素
4. 提出相关改善措施和加工优化建议
机械加工质量控制
机械加工质量控制是指通过控制加工参数和采用合理的加工工艺,确保机械加工过程中所达到的工件质量能够满足设计要求和客户需求。
常见的机械加工质量控制方法包括:
1. 控制加工参数,如刀具刃口半径、加工速度、进给量等
2. 采用合适的加工工艺,如铣削、车削、钻削等
3. 使用高精度的测量设备进行质量检测和纠正
4. 实施质量管理体系和质量控制标准
机械加工质量控制的关键在于不断优化和改进加工工艺、设备和管理体系,以提高加工稳定性和质量可靠性。
结论
机械加工质量分析和控制是机械制造过程中必不可少的环节,它直接关系到产品的质量和市场竞争力。
通过科学的分析和有效的
控制措施,能够提高机械加工的质量稳定性和可靠性,满足客户的需求。
机械加工质量分析及控制

机械加工质量分析及控制机械加工质量分析及控制一、引言二、机械加工质量分析机械加工质量的分析主要包括以下几个方面:1.表面粗糙度分析机械加工的表面粗糙度对于产品的外观和性能有着重要影响。
通过使用表面粗糙度测量仪器,可以对机械加工的表面粗糙度进行评估。
常用的表面粗糙度参数包括Ra、Rz等。
2.尺寸精度分析机械加工的尺寸精度是指产品的实际尺寸和设计图纸上的尺寸之间的偏差。
通过使用测量工具和仪器,可以对机械加工的尺寸精度进行评估。
常用的尺寸精度参数包括公差、尺寸偏差等。
3.形状偏差分析机械加工的形状偏差是指产品的实际形状和设计图纸上的形状之间的偏差。
通过使用形状测量仪器,可以对机械加工的形状偏差进行评估。
常用的形状偏差参数包括圆度误差、平面度误差等。
三、机械加工质量控制为了确保机械加工的质量,需要进行相应的控制措施。
以下是几个常用的机械加工质量控制方法:1.工艺参数控制调整机械加工的工艺参数,可以对机械加工的质量进行控制。
例如,通过调整切削速度、进给速度和切削深度等参数,可以控制机械加工的表面粗糙度和尺寸精度。
2.设备状态监控对机械加工设备的状态进行监控,可以及时发现并修复设备故障,避免对产品质量的影响。
常用的设备状态监控方法包括振动监测、温度监测等。
3.质量检验与统计分析对机械加工的产品进行质量检验,并进行统计分析,可以及时发现并纠正加工过程中的问题。
常用的质量检验方法包括外观检查、尺寸测量等。
四、机械加工质量的分析和控制是确保产品质量的重要手段。
通过对表面粗糙度、尺寸精度和形状偏差等进行分析,可以找出问题所在。
通过工艺参数控制、设备状态监控和质量检验与统计分析等控制措施,可以提高机械加工的质量水平。
机械加工行业中的质量控制方法
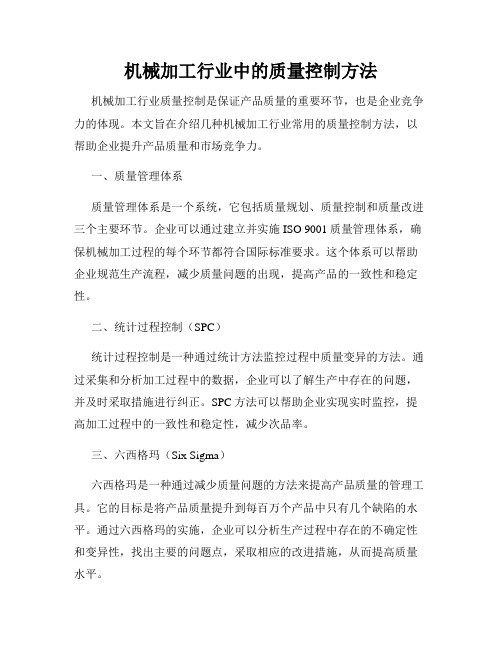
机械加工行业中的质量控制方法机械加工行业质量控制是保证产品质量的重要环节,也是企业竞争力的体现。
本文旨在介绍几种机械加工行业常用的质量控制方法,以帮助企业提升产品质量和市场竞争力。
一、质量管理体系质量管理体系是一个系统,它包括质量规划、质量控制和质量改进三个主要环节。
企业可以通过建立并实施ISO 9001质量管理体系,确保机械加工过程的每个环节都符合国际标准要求。
这个体系可以帮助企业规范生产流程,减少质量问题的出现,提高产品的一致性和稳定性。
二、统计过程控制(SPC)统计过程控制是一种通过统计方法监控过程中质量变异的方法。
通过采集和分析加工过程中的数据,企业可以了解生产中存在的问题,并及时采取措施进行纠正。
SPC方法可以帮助企业实现实时监控,提高加工过程中的一致性和稳定性,减少次品率。
三、六西格玛(Six Sigma)六西格玛是一种通过减少质量问题的方法来提高产品质量的管理工具。
它的目标是将产品质量提升到每百万个产品中只有几个缺陷的水平。
通过六西格玛的实施,企业可以分析生产过程中存在的不确定性和变异性,找出主要的问题点,采取相应的改进措施,从而提高质量水平。
四、故障模式与影响分析(FMEA)故障模式与影响分析是一种通过分析潜在故障引发的影响来预防和控制质量问题的方法。
通过对加工过程中可能出现的故障模式进行识别、评估和控制,企业可以采取相应的措施,降低质量风险,提高加工过程中的可靠性和稳定性。
五、品质功能展开(QFD)品质功能展开是一种通过转化顾客需求为产品设计要求的方法,以确保产品质量的客户满意度。
通过分析客户需求,将其转化为清晰的设计指标,企业可以针对客户需求进行加工和设计,从而提高产品的质量,并满足市场需求。
六、持续改进持续改进是质量控制的核心,也是实现质量卓越的关键。
企业应该建立和执行一个持续改进计划,不断分析和改进加工过程中存在的问题,寻求优化和提升的机会。
定期组织质量会议和培训,提升员工的质量意识和能力,推动质量文化在企业内部深入落地。
机械加工质量分析报告
现以卧式车床为例,说明导轨误差是怎样影响工件 的加工精度的。
(1)导轨在水平面内直线度误差的影响
当导轨在水平面内的直线度误差为△y时,引起工件在 半径方向的误差为(图4-9):
△R=△y
由此可见:床身导轨在水平面内如果有直线度误差,使工件 在纵向截面和横向截面内分别产生形状误差和尺寸误差。
第四章 机械加工质量分析与控制
第一节 机械加工精度概 述
优质、高产、低消耗是企业发展的必由之路。 优质就是高的产品质量。 高产就是生产效率高。 低消耗就是成本低。 产品的质量与零件的加工质量、产品的装配质 量密切相关,而零件的加工质量是保证产品质量的 基础。它包括零件的加工精度和表面质量两方面。 零件的加工精度包括尺寸精度、形状精度和相 互位置精度。
•轴向窜动 •径向跳动 •角度摆动
机床几何误差
机床导轨误差
•水平面内直线度 •垂直面内直线度 •前后导轨的平行度
机床传动链误差
•内联传动链始末两 端传动元件间相对 运动误差
1、机床导轨误差
机床导轨是机床中确定某些主要部件相对位置的 基准,也是某些主要部件的运动基准。
机床导轨误差的基本形式
•水平面内的直线度 •垂直面内的直线度 •前后导轨的平行度
Z1 δ1 δ1n=i1nδ1
Z2 δ2 δ2n=i2nδ2
………………
Zn δn δnn=innδn 在任一时刻,各齿轮的转角误差反映到丝杠的总误差为:
n
Σ 1n 2n nn ji jn j 1
(3)减少传动链误差的措施
1)尽量缩短传动链。 2)提高传动件的制造和安装精度,尤其是末端 零件的精度。 3)尽可能采用降速运动,且传动比最小的一级 传动件应在最后。 4)消除传动链中齿轮副的间隙。 5)采用误差校正机构
机械加工过程中的质量控制与检测技术
机械加工过程中的质量控制与检测技术在现代制造业中,机械加工是一个至关重要的环节,其质量直接影响到最终产品的性能、可靠性和使用寿命。
为了确保机械加工产品的质量符合设计要求和客户期望,质量控制与检测技术的应用不可或缺。
机械加工过程中的质量控制是一个系统性的工作,涵盖了从原材料采购到成品交付的整个生产流程。
在原材料阶段,就需要严格筛选,确保其性能和质量符合加工要求。
例如,钢材的硬度、韧性等指标必须经过精确检测,以避免在后续加工中出现裂纹、变形等问题。
加工设备的精度和稳定性对产品质量有着决定性的影响。
定期对机床进行维护保养,校准精度,能够有效地减少加工误差。
同时,操作人员的技能水平和工作态度也不容忽视。
熟练的操作人员能够根据加工材料的特性和工艺要求,合理调整加工参数,从而提高加工质量。
在工艺规划方面,科学合理的工艺路线和工艺参数是保证质量的关键。
通过对加工过程进行详细的分析和优化,能够降低废品率,提高生产效率。
例如,在切削加工中,选择合适的刀具、切削速度和进给量,可以减少刀具磨损,提高零件的表面质量和尺寸精度。
质量控制还包括对加工环境的管理。
温度、湿度、粉尘等环境因素都可能对加工精度产生影响。
因此,保持良好的加工环境,对于提高产品质量具有重要意义。
检测技术则是质量控制的重要手段。
常见的检测方法包括尺寸测量、形位公差检测、表面粗糙度检测等。
尺寸测量是最基本的检测项目之一。
常用的测量工具如卡尺、千分尺、量规等,能够精确测量零件的长度、直径、厚度等尺寸参数。
对于高精度的尺寸测量,还可以采用三坐标测量机等先进设备,它能够实现对复杂零件的三维测量,获取更加全面和精确的尺寸信息。
形位公差检测用于评估零件的形状和位置精度。
例如,圆度、圆柱度、平行度、垂直度等。
这些公差的检测通常需要使用专门的量具和仪器,如圆度仪、垂直度检测仪等。
表面粗糙度检测对于零件的耐磨性、密封性等性能有着重要影响。
常用的检测方法有比较法、触针法和光切法等。
机械加工质量分析与控制
机械加⼯质量分析与控制第四模块机械加⼯质量分析与控制⼀、填空题1.⼯件表⾯的加⼯质量指标分为:()和()。
2.()是指零件在加⼯后的⼏何参数的实际值与理想值相偏离的程度3.机械加⼯中,由机床、夹具、⼑具、⼯件组成的统⼀体,称为();4.加⼯原理误差是指采⽤了近似的()或()进⾏加⼯时产⽣的误差;5.加⼯细长轴时,通常后顶尖采⽤弹性顶尖,⽬的是为了消除()的影响。
6.加⼯经济精度是指在正常⽣产条件下,符合()、(),(),所能达到的加⼯精度等级。
7.在普通铣床上,采⽤成型法加⼯齿形时,存在由⼑具近似形状引起的()。
8.在普通外圆车床上车削外圆时,如果导轨在⽔平⾯内存在直线度误差(向前凸),则加⼯出来的零件会产⽣()。
9.原始误差所引起的切削刃与⼯件间的相对位移,如果产⽣在加⼯表⾯的法线⽅向,则对加⼯误差有直接的影响,所以把加⼯表⾯的法向称为()。
10.⼯艺系统受⼒变形的程度主要与系统的()有关。
11.由于部件是有许多零件组成,其中存在很多( ) ,所以在受⼒变形时不能和整体零件相⽐,部件的刚度要⽐我们想象的( )的多。
12.⼀般情况下,复映系数远( ),在2~3次⾛⼑之后,⽑坯误差下降很快,所以⼀般只有在( ) 时⽤误差复映规律估算加⼯误差才有实际意义。
13.⼤批量⽣产时,采⽤调整法加⼯,⼀批⽑坯余量都不⼀样,由于( )的结果,造成⼀批零件的“尺⼨分散”。
14.磨削薄⽚零件时,在零件下⾯垫橡胶的⽬的是消除( )造成的⼯件变形。
15.不同加⼯⽅法,切削热传⼊⼯件的( )不同,有时相差很⼤,所以⼯件的热变形程度不同;16.⼯件受热⽐较均匀,主要影响⼯件的( )精度;⼯件受热不均,主要影响( ) 。
17.按误差在⼀批零件出现的规律,分两类:( )、()。
18.加⼯⼀批零件时,如果是在机床⼀次调整中完成的,则机床的调整误差引起( )误差;如果是经过若⼲次调整完成的,则调整误差就引起( )误差。
19.⼯艺系统热平衡之前的变形造成的雾差是( )误差;之后是( )误差。
机械加工质量分析及控制
单击此处添加副标题
演讲人姓名
第一节 概 述
添加标题
添加标题
添加标题
添加标题
零件的加工质量是保证机械产品工作性能和产品寿命的基础。
加工精度 表面质量
本章的任务是讨论零件的机械加工精度问题。
衡量进行加工质量的指标有两方面
一、加工精度和表面质量的概念
在机械加工过程中,由于各种因素的影响,使刀具和工件间的正确位置发生偏移,因而加工出来的零件不可能与理想的要求完全符合,两者的符合程度可用机械加工精度和加工误差来表示。
距表层深度
加工后
0
-σ
距表层深度
+σ
0
-σ
+σ
加工时
金相组织变化的影响 切削时产生的高温会引起表面层的相变。由于不同的金相组织有不同的比重,表面层金相组织变化的结果造成了体积的变化。表面层体积膨胀时,因为受到基体的限制,产生压应力;反之表面层体积缩小,则产生拉应力。各种金相组织中,马氏体比重最小,奥氏体比重最大。
0
-σ
距表层深度
+σ
加工时
0
-σ
距表层深度
+σ
加工后
(1)冷塑性变形的影响 当切削加工完成后,切削力已去除,里层金属趋向复原(弹性恢复),但受到已产生塑性变形的表面层限制,回复不到原状,因而在表面层产生残余压应力,里层则为拉应力与之相平衡。
0
-σ
距表层深度
+σ
(2)热塑性变形的影响 表面层在切削热的作用下产生热膨胀,此时基体温度较低,因此表面热膨胀受到基体的限制而产生热压缩应力。当表面层的温度超过材料的弹性变形的温度范围时,就会产生热塑性变形(在压力作用下材料相对缩短)。当切削过程结束,温度下降至与基体温度一致时,因为表面层已产生热塑性变形,但受到基体的限制产生拉应力,里层则为残余压应力。
- 1、下载文档前请自行甄别文档内容的完整性,平台不提供额外的编辑、内容补充、找答案等附加服务。
- 2、"仅部分预览"的文档,不可在线预览部分如存在完整性等问题,可反馈申请退款(可完整预览的文档不适用该条件!)。
- 3、如文档侵犯您的权益,请联系客服反馈,我们会尽快为您处理(人工客服工作时间:9:00-18:30)。
l y尾-
y主
=
x yx- y主
yx =
y主
l-x l
+
y尾
x l
y系= y刀架+ yx=Fy
k刀1 架+
1 k主
l-x l
2
+
1 k尾xຫໍສະໝຸດ l2当x = 0时, y系= ?;当 x = l 时, y系= ?
当 x = k尾l /(k主+ k尾)时,y系min= Fy
① 定尺寸刀具 刀具尺寸精度直接影响工件尺寸精度 ② 成形刀具 刀具形状精度直接影响工件形状精度 ③ 展成刀具 刀刃形状精度会影响工件加工精度 ④ 一般刀具 制造精度对工件加工精度无直接影响
(4)夹具的几何误差
包括夹具制造误差、安装误差及磨损 对工件尺寸精度和位置精度影响很大
(5)定位误差
包括基准不重合误差、定位副制造不准确误差 直接影响工件的尺寸精度和位置精度
(6)调整误差
在工序的调整工作中所存在的误差即调整误差
一次调整后存在的误差对这一批零件的影响是不变的。 但大批量加工中存在多次调 整,不可能每次完全相同。 对全部零件来说,每次调整 误差为偶然性误差。机床调 整误差可理解为零件尺寸分 布曲线中心的最大偏移量。
加工中不产生废品的
条件:Δfb+Δt≤T
4)自动控制法
切削测量补偿调整
滚动轴承结构复杂,影响主轴精度因素也较复杂
除轴承本身精度外,与配合件精度有很大关系如主轴轴 颈、支承座孔等精度
产生轴向窜动主要原因是主轴轴肩端面和轴承承载端面 对主轴回转轴线有垂直度误差。
主轴不同形式的回转误差引起的加工误差不同
车床上加工外圆内孔时,主轴径向跳动引起工件圆度和 圆柱度误差,对工件端面无影响;
机械加工质量分析与控制
常用加工误差的大小来评价加工精度的高低 加工误差越小,加工精度越高
➢ 零件的加工精度包括 尺寸精度、形状精度、位置精度
通常尺寸精度要求高,形位精度要求也越高
➢ 获得加工精度的方法
(1)获得尺寸精度的方法
1)试切法
用于单件小批生产
2)调整法
用于成批大量生产
3)定尺寸刀具法
生产率高,刀具制造复杂
轴向窜动对圆柱表面影响不大,对端面垂直度平面度影 响大,车削螺纹时会造成导程的周期性误差;
纯角度摆动会造成车削外圆或内孔的锥度误差; 在镗孔 时,会镗出的孔为椭圆形。
纯角度摆动会造成车削外圆或内孔的锥度误差;在镗孔 时,若工件进给会使镗出的孔为椭圆形。
提高主轴及支承座孔的加工精度,选用高精度轴承,提高 主轴部件装配精度、预紧和平衡等,提高主轴回转精度。
Δφ∑= ∑Δφwi= ∑Ki Δφi
减少传动链误差的措施:
① 尽可能缩短传动链,减少传动元件数目; ② 尽量采用降速传动,误差被缩小; ③ 提高传动元件、特别是末端元件的制造和
装配精度; ④ 消除传动间隙; ⑤采用误差补偿机构或自动补偿装置。
(3)刀具的几何误差
包括刀具切削部、装夹部的制造误差及刀具安装误差
3)机床传动链误差
指机床内传动链始末两端的传动元件间相对运动的误差, 一般用传动链末端元件的转角误差来衡量。产生的原因 是传动链中各传动元件的制造误差、装配误差及磨损等。
若传动齿轮 i 在某一时刻产生转角误差为Δφi,则它所
造成传动链末端元件的转角误差:Δφwi =Ki Δφi
Ki 为该轴到末端元件的总传动比,称为误差传递系数, 若Ki大于1则误差被扩大;反之,若Ki小于1误差被缩小。 各传动件对工件精度影响的总和为:
(5)工艺系统受力变形及其对加工精度的影响 1)工艺系统的变形
总变形 y系 = y机+ y夹+ y刀+ y工 k系= Fy / y系,k机= Fy / y机 , k夹= Fy / y夹 ,
k刀= Fy / y刀 , k工= Fy / y工 所以, k系= 1/(1/ k机+ 1/ k夹+ 1/ k刀+ 1/ k工)
2)机床导轨误差
导轨精度要求主要有以下三方面:
① 在水平面内的直线度(以卧式车床为例)
Δ1将直接反映在工件加工表面法线方向(误差敏感方向) 上,误差ΔR =Δ1 ,对加工精度影响最大。
刀尖在水平面内的运动轨迹造成工件轴向形状误差。
② 在垂直面内的直线度 Δ2对工件的尺寸和形状误差影响比Δ1小得多
若扭曲误差为Δ3,工件误差ΔR≈(H/B)Δ3 ,一般车床
H/B≈2/3,外圆磨床H/B≈1,误差对加工精度影响很大
除导轨制造误差外,导轨的不均匀磨损和安装质量,也 是造成导轨误差的重要因素。导轨磨损是机床精度下降 的主要原因之一。可采用耐磨合金铸铁、镶钢导轨、贴 塑导轨、滚动导轨导轨表面淬火等措施。
对卧式车床ΔR ≈Δ22/D 若设Δ2= 0.1mm,D=40mm,则 ΔR =0.00025mm,影响可忽略不计。 而对平面磨床、龙
门刨床误差将直接反映在工件上。
导轨在垂直面内的直线度的特殊情况为斜坡状, 加工的工件轴向形状为鞍形。
③ 前后导轨的平行度(扭曲)
卧式车床或外圆磨床若前后导轨存在平行度误差时, 刀具和工件之间相对位置发生变化,刀尖运动轨迹是一 条空间曲线,使工件产生形状误差。
(3)刀具刚度
外圆刀具在加工表面法线方向上的刚度很大变形可忽略; 镗小孔刀杆刚度很差,变形对加工精度影响很大,刀杆变 形按材料力学公式估算。
(4)机床部件刚度 机床部件刚度
机床结构形状复杂,刚度计算主要通过实验方法来测定。 变形与载荷不成线性关系; 加载与卸载曲线不重合; 有残余变形存在;实际刚度比估算的小
3.工艺系统的受力变形
(1)基本概念
(1)工艺系统刚度 工艺系统抵抗变形的能力可用工艺系统刚度 k系来描述。 垂直作用于工件加工表面的径向切削分力Fy与工艺系统在 该方向上的变形y之间的比值,称为工艺系统刚度 k系
k系= Fy / y 柔度 w= 1/ k
(2)零件刚度
若零件刚度相对于机床、刀具、夹具来说比较低,其变形 对加工精度影响比较大,最大变形量按材料力学公式估算。 长轴两顶尖装夹按简支梁计算,三爪卡盘装夹按悬臂梁计算
工艺系统刚度比刚度最小环节的刚度还要差
2)工艺系统受力变形对加工精度的影响 ①切削力位置的变化对加工精度的影响
设刀具工件刚度很大 总变形 y系= y刀架+ yx
设刀具工件刚度很大 总变形 y系= y刀架+ yx
y主=FA/k主=Fy(l-x) /(l k主),y尾=FB /k尾=Fyx /(l k尾)