粉末注射成形计算机模拟技术及其应用
注射成型过程计算机模拟---实验指导书
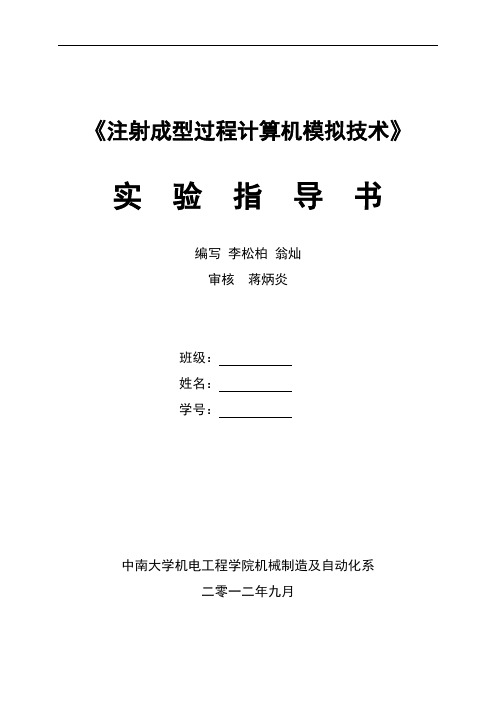
《注射成型过程计算机模拟技术》实验指导书编写李松柏翁灿审核蒋炳炎班级:姓名:学号:中南大学机电工程学院机械制造及自动化系二零一二年九月目录实验一MoldFlow软件流动分析及应用 (1)【实验目的】 (1)【实验器具】 (1)【实验原理】 (1)【实验步骤】 (1)【实验报告】 (5)实验二MoldFlow软件翘曲分析及应用 (6)【实验目的】 (6)【实验器具】 (6)【实验原理】 (6)【实验步骤】 (7)【实验报告】 (10)附录 MoldFlow软件介绍 (11)【应用领域】 (11)【软件组成及作用】 (11)【主要模块】 (12)实验一注射过程流动(Flow)分析实验【实验目的】●掌握MoldFlow软件的网格划分、网格诊断、网格修复等前处理操作技术;●了解塑料材料在模具内流动中注射工艺参数对注射制品缺陷的影响,预测注射成型制品的缺陷,控制塑料材料在模具中的流动方式,掌握保压工艺曲线的优化方法,改善成型制品的缺陷,提高一次试模的成功率。
【实验器具】●微型计算机(台/人);●MoldFlow软件。
【实验原理】塑料在不同形状的模具流道和模具型腔中流动时,由于塑料本身特有的粘滞特性,塑料熔体内部具有粘滞力,管壁存在摩擦力,塑料熔体沿管道流动和在模具型腔中流动时会引起压力降和流速的变化,模具流道和模具型腔本身截面形状和尺寸的变化,也会引起流体压力、流速分布和流量的变化,将对塑料制品的性能产生重要的影响。
研究不同塑料材料的流动特性,涉及到流体力学、材料流变学、计算数学等知识,通过对塑料熔体在流动过程中建立相应的控制方程,根据对应的边界条件,对塑料熔体流动过程中的速度场、温度场以及剪切应力、剪切速率、体积流量、粘度等参数变化进行求解,从而预测注射成型制品的缺陷,改变注射工艺参数,改善成型制品的缺陷,提高一次试模的成功率。
Moldflow软件中MPI/Flow模块能够对注塑成型工艺过程提供全面的解决方案,主要体现在以下几个方面:(1) 制品能否充满,特别是对于大型制品;(2) 最佳的浇口位置与数量、类型;(3) 流道系统的优化设计。
注射模成型计算机模拟技术实验报告一
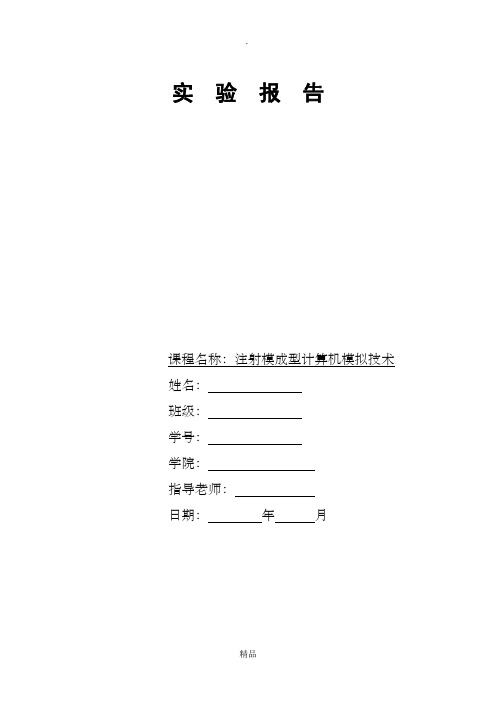
实验报告课程名称:注射模成型计算机模拟技术姓名:班级:学号:学院:指导老师:日期:年月实验一:注射过程流动分析实验1、实验目的:②掌握MoldFlow软件的网格划分、网格诊断、网格修复等前处理操作技术;②了解塑料材料在模具内流动中注射工艺参数对注射制品缺陷的影响,预测注射成型制品的缺陷,控制塑料材料在模具中的流动方式,掌握保压工艺曲线的优化方法,改善成型制品的缺陷,提高一次试模的成功率。
2、实验内容(原始方案):用Pro/E创建一个三维制品模型,通过STL格式导入到MoldFlow软件中,再根据制品材料选择相应的成型工艺参数,设置好合理的工艺参数。
接下来对制品进行网格划分,网格诊断和网格修复等前处理操作技术,然后进行模拟填充过程和保压过程,通过填充过程得到填充时间、填充压力、熔体前沿的温度在制件厚度方向的分布、熔体的流动速度、分子趋向、剪切速率及剪切应力、气穴及熔接痕位置等,并可以在电脑屏幕上直观的显示出来,通过保压过程可以得到保压时间。
在得到相应的工艺参数之后,再对相应的制品缺陷进行分析,优化工艺参数和保压工艺曲线,从而改善制品缺陷,提高一次试模的成功率。
3、实验数据:(1)、工艺参数为:熔体温度260o C,型腔温度60o C,注射时间为1.25s。
得出制件的结果:(2、)采用二级保压压力(70Mpa 3.5s,50 Mpa 3.5s)得到的制件情况(3)、工艺参数为:熔体温度260o C,型腔温度60o C,注射时间为2.25s。
并采用二级保压压力(70Mpa 3.5s,50 Mpa 3.5s)得到的制件情况4、原因分析:在对结果进行分析时,发现有较多的气穴,原因可能在于注射压力太低、注射时间太短、注射速度太高等;还有较大的收缩率,形成较大收缩率的原因可能物料温度太高、注射速度太高、注射压力太小等;5、改善措施(提出两到三种方案进行方案对比):针对出现的问题,我对方案进行了改善,先是增高了注射压力,保持注射时间不变,降低了注射速度,再次进行分析后发现气穴少了一点,方案得到了进一步改善,但收缩率的情况并没有较大的改善;然后我又增长了注射时间,再次分析后发现气穴和收缩率均得到了更好的改善6、结论:对制件工艺的分析过程,之间网格的划分是很重要的一步,不正确的网格划分将会导致MoldFlow软件对制件分析产生错误而分析不了;另外注射时间、注射压力、注射速度等对制件成型质量有着直接而重大的影响,对各项工艺参数的制定不可能一次到位,而运用MoldFlow软件进行分析后可以极大的优化工艺设计,从而得到更加稳定的成型工艺条件,改善成型制品的缺陷,提高一次试模的成功率。
PIM粉末注射成形概述(可打印修改)(2)

PIM粉末注射成形概述(可打印修改)(2)PIM粉末注射成形概述:注射成型车间连续烧结炉设备结构图真空烧结炉粉末注射成形(Powder Injection Molding,PIM)由⾦属粉末注射成形(Metal Injection Molding,MIM)与陶瓷粉末注射成形(Ceramics Injection Molding,CIM)两部分组成,它是⼀种新的⾦属、陶瓷零部件制备技术,它是将塑料注射成形技术引⼊到粉末冶⾦领域⽽形成的⼀种全新的零部件加⼯技术。
MIM的基本⼯艺步骤是:⾸先选取符合MIM要求的⾦属粉末和黏结剂,然后在⼀定温度下采⽤适当的⽅法将粉末和黏结剂混合成均匀的喂料,经制粒后再注射成形,获得成形坯(Green Part),再经过脱脂处理后烧结致密化成为最终成品(White Part)。
粉末注射成形技术的特点:粉末注射成形能像⽣产塑料制品⼀样,⼀次成形⽣产形状复杂的⾦属、陶瓷零部件。
该⼯艺技术利⽤注射⽅法,保证物料充满模具型腔,也就保证了零件⾼复杂结构的实现。
以往在传统加⼯技术中,对于复杂的零件,通常是先分别制作出单个零件,然后再组装;⽽在使⽤PIM技术时,可以考虑整合成完整的单⼀零件,这样⼤⼤减少了⽣产步骤,简化了加⼯程序。
1、与传统的机械加⼯、精密铸造相⽐,制品内部组织结构更均匀;与传统粉末冶⾦压制⁄烧结相⽐,产品性能更优异,产品尺⼨精度⾼,表⾯光洁度好,不必进⾏再加⼯或只需少量精加⼯。
⾦属注射成形⼯艺可直接成形薄壁结构件,制品形状已能接近或达到最终产品要求,零件尺⼨公差⼀般保持在±0.10%~±0.30%⽔平,特别对于降低难以进⾏机械加⼯的硬质合⾦的加⼯成本、减少贵重⾦属的加⼯损失尤其具有重要意义。
2、零部件⼏何形状的⾃由度⾼,制件各部分密度均匀、尺⼨精度⾼,适于制造⼏何形状复杂、精度密⾼及具有特殊要求的⼩型零件(0.2~200g)。
3、合⾦化灵活性好,对于过硬、过脆、难以切削的材料或原料铸造时有偏析或污染的零件,可降低制造成本。
金属粉末注射成形计算机充模模拟两相理论和颗粒模型的应用

而可以模 拟远离 平衡态 的系统[ 。这类模 型对流
体、 颗粒的运动都是采用拉格 朗日坐标描述。
单相流动一样服从流体力学 的所有基本定律 。不过
控制方程 比单相流动更复杂一些和更多一些。 目 前有关两相流动 的模型 已有大量报道 , 刻 从 划的尺度及属性上区分 , 主要有 3 大类模型 :
3 2
湖 南有 色金 属
第2 3卷
特性使得 这一 现象尤 为突出。这就带来 了一些 问 题, 比如: 流体是否均匀 , 流体是否是多相的且 每个 组分是否都起着独立 的作用 来影响整个流体 的流 动性。 通过观察流道横截面上的流体可 以发现许多有 趣的现象 。图 1 8 和图 2 中显示 的是横截面的放大 图, 出了相的分离 以及年轮一样 的结构。上面 显示 图片中的 白色条纹是相分离的一种表征 , 那里是一 些粘结剂中的低熔点组分 。在这样的地方很容易产 生裂纹。这种结构明显表明流体是多相 的, 甚至可 能是类固体的。所 以实际上 的 MI 喂料熔体是非 M
维普资讯
第2 卷第 1 3 期
20 0 7牟 2月
HUNAN NONF ERROUS METAL S
湖 南有 色金 属
31
金属粉末注射成形计算机充模模拟 两相理论和颗粒模 型的应用
刘友 良 , 高建祥 曲选辉2 ,
(. 1 湖南工业大学 , 南 株洲 4 20 ; . 湖 10 0 2 北京科技 大学, 北京 摘 10 8 ) 00 3
2 混合物 的扩展颗粒化模拟
在这种模拟 中, 出了多层次数值模 型来考察 提 粉末注射 成形过程 中粉末 一粘结剂体 系的复杂行 为。把粉末颗粒 当做是一个个单元 , 然后从颗粒和 颗粒 、 颗粒和粘结剂的相互作用中导 出其动量输运 方程。通过这种方法可以直接考察粉末特性( 粒度 、 粒径分布 、 密度和形状等) 对流动过程的影 响。从而
粉末成型机技术及应用

粉末成型机技术及应用粉末成型机(又称伺服粉末成型机)采用鑫台铭机、电、液、气、仪一体化控制、驱动技术,面向粉末冶金、陶瓷、硬质合金、磁性材料及邻近粉末行业研发的专用机型。
采用好的、特有的电气控制技术,能按照产品成型要求,在触摸屏上灵活设定各产品台阶驱动部件的动作程序,无需改动内部程序,符合了粉末冶金行业产品形状复杂,多品种台阶零件的压制成型要求,通用性强。
粉末成型机是液压机常见用途之一,粉末成型压力机顾名思义就是不同材质的粉末状物质,在模具的配合作用下,通过伺服液压机对其施加一定的压力,达成需要的产品。
常见的有金属粉末、陶瓷粉末、粉末冶金,磁性材料等。
1、按浮动凹模压制系统和脱模位置恒定原理,不管零件的高度,脱模均都在同一位置。
2、使用凹模控制系统实现凹模定位运动,可靠的平面凹模止挡设计,确保了成型件尺寸的精度控制,使密度均匀,产品坚固可靠。
3、伺服丝杆驱动系统中的上下滑块运动,使用压机有优越的粉末压制特性。
4、采用模具更换及模架安装系统,更换模架更便利。
5、压机结构简单直接,使得压机运行可靠,并减少了在压制复杂零件时的机器故障。
6、设备操作采用人机对话操作模式,结构简单,操作方便,保养容易。
1、适合任何异型产品,超小产品成型。
2、防止过充,填充稳定,粉料无外泄,漏料。
3、伺机系统调速调整方便且静音传动。
4、伺服异常对应方法明确化,简易化。
5、成型产品效率高,精度高,密度均匀,高度稳定。
6、节省模具,模具磨损小。
7、维护,保养,操作及更换模具更简便。
8、节能,能耗低,平均节能一倍以上。
9、伺服加螺杆的传动机构机台无振动,使产品单重变化小并保证品质及提升。
触摸屏功能:1.运行界面;显示当前数据显示,当日产量,显示设备的当前工作状态、显示当前各种参数设定值等、以及各种故障报警。
2.参数设定;保压时间角度设定、滑块上下限位置、工进位置、设备最大出力,光栅状态, 设备运行速度,压装力检测设定,空久停机机时间等设定。
粉末注射成型技术的研究与应用
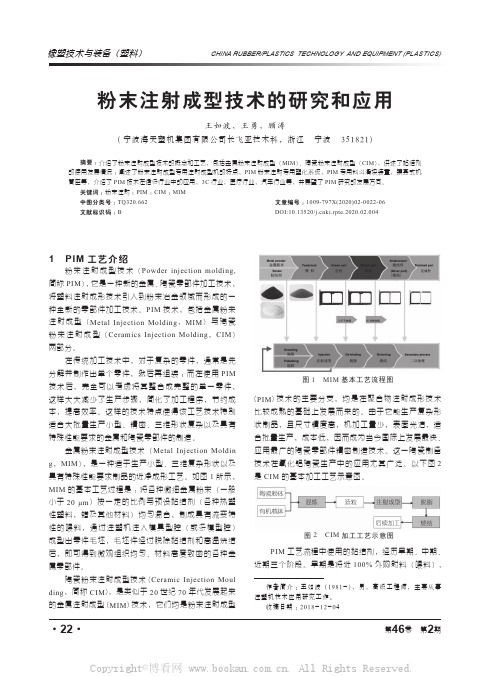
第46卷 第2期·22·作者简介:王如波(1981-),男,高级工程师,主要从事注塑机技术应用研究工作。
收稿日期:2018-12-041 PIM 工艺介绍粉末注射成型技术(Powder injection molding,简称PIM ),它是一种新的金属、陶瓷零部件加工技术,将塑料注射成形技术引入到粉末冶金领域而形成的一种全新的零部件加工技术。
PIM 技术,包括金属粉未注射成型(Metal Injection Molding ,MIM )与陶瓷粉未注射成型(Ceramics Injection Molding ,CIM )两部分。
在传统加工技术中,对于复杂的零件,通常是先分解并制作出单个零件,然后再组装;而在使用PIM 技术后,完全可以考虑将其整合成完整的单一零件,这样大大减少了生产步骤,简化了加工程序,节约成本,提高效率。
这样的技术特点使得该工艺技术特别适合大批量生产小型、精密、三维形状复杂以及具有特殊性能要求的金属和陶瓷零部件的制造。
金属粉末注射成型技术(Metal Injection Moldin g ,MIM ),是一种适于生产小型、三维复杂形状以及具有特殊性能要求制品的近净成形工艺。
如图1所示,MIM 的基本工艺过程是:将各种微细金属粉末(一般小于20 μm )按一定的比例与预设黏结剂(各种热塑性塑料,蜡及其他材料)均匀混合,制成具有流变特性的喂料,通过注塑机注入模具型腔(或多模型腔)成型出零件毛坯,毛坯件经过脱除黏结剂和高温烧结后,即可得到微观组织均匀、材料高度致密的各种金属零部件。
陶瓷粉末注射成型技术(Ceramic Injection Moul ding ,简称CIM ),是类似于20世纪70年代发展起来的金属注射成型(MIM )技术,它们均是粉末注射成型(PIM )技术的主要分支,均是在聚合物注射成形技术比较成熟的基础上发展而来的。
由于它能生产复杂形状制品,且尺寸精度高,机加工量少,表面光洁,适合批量生产,成本低,因而成为当今国际上发展最快、应用最广的陶瓷零部件精密制造技术。
文献综述--计算机辅助技术在注射成型中的应用及发展

计算机辅助技术在注射成型中的应用及发展一.前言1.课题研究背景随着塑料工业的发展,塑料模具也蓬勃发展。
近年来。
人们对各种设备和用品轻量化及美观和手感的要求越来越高,这就为塑料制品提供了更广泛的市场。
塑料制品的发展必然带动塑料模具产业的发展,塑料模具占模具总量比例越来越大。
由于人们的消费水平提高,对产品质量美观的要求也不断提高,短生命周期产品的开发,产品多样化的增加,高要求质量产品的出现,这也就意味着对塑料模具的精度以及模具的设计都需要很大的提高和改善。
由于塑料产品的模塑成型是一个十分复杂的过程,传统的设计方法经验性强,不可能综合权衡所有因素,很难确定能否生产出完全合格的产品,一般需要反复试模与修模,导致模具设计制造周期长和成本偏高。
传统的方法根本满足不了现代化模具制造的需求,这就要求必须有更加先进的技术来替代。
现在计算机技术发展迅猛,其中计算机辅助技术在模具设计制造也变得越来越重要,信息与网络技术、CAD/CAE/CAM 集成技术、并行工程,人工智能等技术来有效地解决了传统模具设计制造的困难。
2.课题研究与意义早在20世纪80年代,我国就对CAD软件技术的发展高度重视并给予重点资助。
随着注塑模具CAD的发展,大部分的商业软件已不仅仅是CAD,而是CAD/CAM/CAE/CAPP的集成,从而形成了真正意义上的无纸化设计、制造环境。
近些年来,随着信息网络的普及,一种新型的模具设计系统应运而生,一个以互联网为基础的注塑模具智能设计系统,它作为协同产品开发系统的一个模块,能够提供一种有效的和切实可行的工具来促进中小企业之间注塑模具设计的合作发展,进而满足当今全球市场对于模具设计的苛刻要求。
由于大部分人只是软件的初级用户,需要对软件进行更进一步的学习和应用。
本课题研究的是箱包锁具锁孔配件注射模设计,基于对箱包锁具锁孔配件注射模具的设计,应用CAD/CAE/CAM集成技术等一系列软件,以及所学模具设计专业知识来完成任务。
计算机技术在粉末冶金生产中的应用

计算机技术在粉末冶金零件生产中的应用姓名:段智勇学号:GC432014305随着计算机技术的普及和发展,计算机在粉末冶金零件生产中的设备、技术、管理等方面已经广泛应用,单片机、智能工业调节器已广泛应用于粉末冶金生产设备(压机、烧结炉等)的自动控制,工业用控制计算机也已经广泛应用于粉末冶金零件生产线的自动化及电子化的企业管理控制一体化。
一、计算机技术在压机设备上的应用压制成形是粉末冶金零件生产中最重要和最基本的工序之一,实现将粉末压制成压坯的设备成为粉末成形压机。
形状复杂、精度高的粉末冶金结构件压制生产用的全自动粉末成型机,通常采用可编程控制器系统控制,操作者可以按照菜单提示方式进行操作和编程,连接现场总线后,与工业控制计算机通信,可以实现远程编程、诊断和监控。
粉末成形压机的主压油缸和阴模油缸以及液压动作装粉靴均为CNC(计算机数字控制)轴,这些轴的动作相互之间可以完全联动,并在安装多层模架时,也可以同模架内的多个模冲进行联动。
主压油缸和阴模油缸配备有辅助的由闭环控制或开环控制的压轴芯杆的活塞。
可编程控制器系统采用模块化设计,用于可配置的各附加轴的控制,进行闭环或开环控制。
压制周期分为三个部分:装粉、压制和脱模三个阶段,每个阶段包括不同的组成区。
压坯的密度很大程度上取决于装粉高度,所以压制过程中对装粉高度的控制尤为重要,标准偏差可进行称重限制定义,并据此进行装粉高度自动修正。
修正方式可选择根据偏离趋势或定义一定偏差值两种方式。
装粉高度的修正由阴模装粉高度的调整完成,各模冲独立地自动按一定比例调整,因此保证压坯不同台阶的密度均匀分布。
为压制复杂形状压坯专门设计多层模架,模架的整体控制通过在压机控制板上进行简单数据输入完成,各模冲动作均为闭环CNC控制。
上模冲同样采取闭环CNC数控控制,这样可以与模架的下模冲动作以及压机的主压轴动作一起联动。
压制成形位置为牢固的机械制动,并可通过楔块式结构进行调整。
液压伺服系统控制的各模板由模架底板内相应的活塞驱动逸动。
- 1、下载文档前请自行甄别文档内容的完整性,平台不提供额外的编辑、内容补充、找答案等附加服务。
- 2、"仅部分预览"的文档,不可在线预览部分如存在完整性等问题,可反馈申请退款(可完整预览的文档不适用该条件!)。
- 3、如文档侵犯您的权益,请联系客服反馈,我们会尽快为您处理(人工客服工作时间:9:00-18:30)。
*重庆市教委科学技术研究项目(K J050603)代兵:男,硕士,现从事材料成形CA D/CA E/CA M 软件的研究与开发 E mail:daibing @粉末注射成形计算机模拟技术及其应用*代 兵,胡红军,张 驰,曾 英(重庆工学院材料科学与工程学院,重庆400050)摘要 介绍了计算机模拟软件在粉末注射成形工艺中的应用,并对注射成形软件的模拟过程进行了描述。
举例说明了计算机模拟软件在金属粉末注射成形工艺模拟实际生产中的意义。
关键词 金属粉末成形 PIM solver 软件 模拟The Application of the Simulation S oftware in Metal Power Injection MoldingDAI Bing ,HU Hong jun,ZHANG Chi,ZENG Ying(Depar tment o f M ater ial Science and Eng ineering,Cho ng qing Inst itute of T echno lo gy ,Chongqing 400050)Abstract T he applicat ion and necessity of the simulat ion so ftwa re ar e int roduced in this paper,and the simulatio ns pro cesses abo ut meta l po wer inject ion mo lding are descr ibed.T he sig nificance of simulatio n softw are in t he actu al product ion of metal po wer injectio n mo lding is illustr ated by ex amples.Key words metal injectio n mo lding,PIM so lv er softw are,simulatio n0 前言金属粉末注射成形(M etal Injection M o lding M IM )是一种源于传统塑料注射成形的新型粉末冶金近净形成形技术,由于其在制作几何形状复杂、组织结构均匀、高性能近净形产品方面具有独特的技术和经济优势而备受瞩目,被誉为 当今最热门的零部件成形技术 。
该技术所能选用的材料体系十分广泛,包括普通钢(低碳钢、低合金钢)、不锈钢、工具钢、硬质合金、高密度合金、陶瓷材料、复合材料等,其应用领域涉及到航空航天、汽车、电子、军械、医疗、日用品及机械等行业[1~3]。
但是在金属注射成形中,由于工艺参数的选择不当,往往容易产生缺陷,从而影响注射坯件的最终质量。
表1示出了粉末注射成形坯件在注射过程中常见的缺陷及产生的原因。
如何避免甚至防止这些缺陷的产生是急需解决的问题,制订合理的注射工艺参数是关系注射成形产品质量的重要因素,合理的工艺参数必须同时考虑特定的模具结构和所采用的材料。
国内已有少数工厂安装、建立了金属粉末注射成形生产线,并生产出了粉末注射成形的产品,但都存在尺寸波动较大、产品性能不稳定等问题,造成金属粉末注射成形产品的应用市场开发迟缓[4~6]。
表1 粉末注射成形坯件的常见缺陷及产生原因缺陷种类产生缺陷的原因欠注注射压力小,喂料粘度大,模具温度低,流动距离太长表面蛇形纹喷射熔接线模具温度低浇口处波纹粘结剂与粉末两相分离飞边注射压力太大气孔注射压力太小,模具温度低,注射温度太高裂纹注射压力太小,冷却收缩不均匀传统的PIM 工艺的主要过程是(见图1):首先将金属粉末与 (有机物)为35%~55%的有机黏结剂均匀混炼,并制成粒状喂料;在加热状态下(100~180 )用注射成形机将熔融状喂料注入冷模腔内成形,然后用化学或热分解的方法将成形坯中的黏结剂完全脱除,最后经烧结致密化得到最终产品[7~9]。
图1 传统的PIM 工艺流程其中注射成形阶段最为重要,因为制品的缺陷基本上是在这一步引入的,如表面塌陷、内部缩孔、开裂、两相分离、变形翘曲、分层、欠注等。
而且,这些缺陷不能在脱脂和烧结阶段得到弥补。
此外,生坯内部的残余应力还会在脱脂或烧结阶段得到松弛,从而可能导致制品的变形或开裂。
因此有必要研究成形工艺参数和模具设计对缺陷生成的影响,以获得质量合格的坯件。
对于模具设计者来说,如果能在设计方案构思阶段预测出喂料熔体在型腔内的流动情况,尽早发现问题,修改设计图样,就能大大提高模具的设计水平和一次试模成功率。
因此流动过程CA E 软件的出现,不仅是模具设计和制造上的一次变革,而且对减少模具返修率、提高模具设计水平和注射坯件的质量都具有重要的意义。
计算机辅助设计和模拟下的P IM 工艺流程见图2,通过对金属粉末注射成形过程进行计算机模拟,可从理论上弄清金属粉末注射成形喂料的各个组分所起的作用及其具体数值的大小,以准确的数值来优化喂料的粉末装载量及黏结剂的配方,优化注射成形的工艺参数,正确设计出模具的型腔尺寸,减少盲目的实验探索过程和实验消耗,缩短产品试制周期,为金属粉末注射成形真正走向实用化打下基础。
同时这种研究可促使粉末冶金的工艺研究走向数字化和计算机化,提高研究水平及准确性。
运用CA E 技术,能使设计师在模具制造之前预测所设计模具在采用某种材料、某种注射成形机注射成形时的结果,从中发现问题并作出修改,同时还可以获得上述条件下可采用的优化的工艺参数,对注射工艺提供指导性意见[10~12]。
图2 计算机辅助设计和模拟下的PIM 工艺流程在粉末注射成形过程中,由于注射喂料的黏度大、导热率较大、凝固较快等特性导致喂料的流动性较差,使粉末注射成形生坯的成形缺陷比塑料注射成形更容易形成,对压力、模具浇口的形状和位置等的要求更高。
采用实验手段分析注射过程所产生的缺陷固然可以得到一些有用的信息,但却是一项费时耗材的工作,需要投入大量的实验经费。
而通过充模流动模拟,不仅可以直观地看到充模流动过程中流动前沿的发展、压力场、温度场和速度场的分布,还可以预测是否产生气孔、熔接线和裂纹等缺陷,比较浇口设置在不同位置时对成形批质量的影响情况,以优化浇口位置和数量的设计[13~15]。
1 粉末注射成形计算机模拟的发展及现状近年来,喂料熔体在注射成形充模过程中的模拟受到了极大的关注,尽管是非等温、非牛顿流体及不稳定流动使模拟计算存在困难,但在非弹性流体模型范围内,已取得了一些成就,粉末注射成形源于塑料注塑成形,其充模流动中的许多概念也源于注塑成形。
它们之间最大的区别在于喂料流变行为的不同,致使流变本构方程不同。
PIM 喂料由于粉末的加入占了很大的含量,使其流变行为要复杂得多,而且,喂料中粉末的存在使其热物性参数与塑料相比相差较大,这就使得P IM 喂料熔体的压力梯度和温度梯度远大于塑料熔体。
在PIM 工艺中,喂料性质的微小变化也会改变其流动行为和产品最终性能。
尽管如此,人们还是主要在注塑充模流动模拟的基础上来开展PIM 喂料充模流动模拟的研究工作[16~18]。
粉末注射成形计算机模拟是一项全新的技术,在国外,虽然在理论上和技术上都取得了较大的进展,正处于蓬勃发展的时期,但仍不太成熟,如没有研究喂料充模过程中凝固层的生长(这对具有较高热导率的P IM 喂料来说是很重要的),将喂料的流变本构方程简单地视为幂率模型(喂料中由于粉末的存在,其流变行为比聚合物复杂得多)等。
由于问题的复杂性,国外的研究成果对外都是保密的,商业化的软件不但少见而且价格昂贵。
此外,由于P IM 喂料和工艺的特殊性,已经商业化的有限元分析软件和塑料注射成形模拟软件在大部分场合并不适用。
目前,我国对P IM 的研究尚处于起步阶段,而P IM 计算机模拟技术的研究仍在摸索之中。
在国内,注塑模CA D/CA E/CA M 系统的研究起步较晚,但经过几年的不懈努力,以及对国外软件开发经验与技术的吸收和研究,发展很快,并取得了一定成果。
华中理工大学模具技术国家重点实验室自行开发了注塑模CAD/CA E/CA M 集成系统H SC2.0,现已在一批工厂中推广使用。
在粉末注射成形模拟软件方面,有韩国Pohang 科技大学开发的PIM F LO W 软件。
该软件可以建立有关喂料和粘结剂密度、比热、热导率性能等参数的数据库,优化工艺条件,指导流道系统、浇口,位置、冷却系统等的设计。
2 粉末注射成形计算机模拟的理论基础粉末注射成形喂料的充模过程与热塑性塑料的充模过程相似,但由于它们的性能不同,其充模过程也不同,只有对其注射成形过程进行深入的研究,才能掌握其填充规律,分析出注射成形过程中可能产生的缺陷和区域,得到喂料在模具型腔中的流动情况,以及其流动过程的温度场和速度场的数值解,从而为模具设计和金属粉末注射成形的工艺参数的选定提供依据。
在粉末注射成形充模过程中,喂料熔体首先充入浇注系统,而后呈泉状进入型腔。
熔体的前端表面与冷空气接触,形成一个黏度较高的前沿膜。
由于前沿膜的存在,使熔体交替发生以下两个过程:一是受前沿膜的阻止,不能直线向前推进,使熔体转向模腔壁方向,当与模腔壁接触时,熔体将很快冻结,形成冷凝层;二是中心热核冲破前沿膜形成新的前沿膜。
这种材料替换的流动是一种向前并向外的合成流动,向外流动的熔体与模壁接触、凝固而形成表皮;向前流动的熔体形成新的熔芯,后面再进入模具的熔体则沿着附有已凝固的冷凝层的流道流动,这种流动称为喷泉流动[19~21]。
粉末注射成形过程的流动分析是建立在计算机被广泛应用的基础上的,其目的是预测喂料熔体注入模腔时的流动情况,从而判断熔体流动给注射件质量带来的影响。
流动分析包括两个方面:第一是利用计算机程序预计型腔中的压力和温度分布,第二是利用预计的压力和温度的分布来改善模具和制品的设计。
3 粉末注射成形计算机模拟软件的应用从20世纪80年代开始,粉末注射成形CA E 技术就已从实验室阶段进入实用化阶段,目前国际市场上相应推出了包括注射、冷却模拟的许多商业化软件,了解它们对开发专门适用于粉末注射成形充模流动模拟的软件有一定的指导作用。
PIM so lver 是一个粉末注射成形的专业CA E 分析软件,它可以模拟喂料的填充过程,促使在PIM 工艺制订阶段PIM 零件的设计、模具的设计以及最后的机加工处理等都在PIM 工艺实施以前得到优化,从而节省时间和控制成本。
在实际生产之前,可通过对注射坯件的充模流动模拟计算出温度场、压力场、速度场、应力场的分布,预测在某种工艺条件下部分常见缺陷可能产生的部位,从而更好地指导模具设计和工艺参数的选择[22~24]。
PIM so lver 可以应用到所有的P IM 喂料,包括金属、陶瓷、碳化物和复合材料等。