CO变换操作知识问答
变换操作
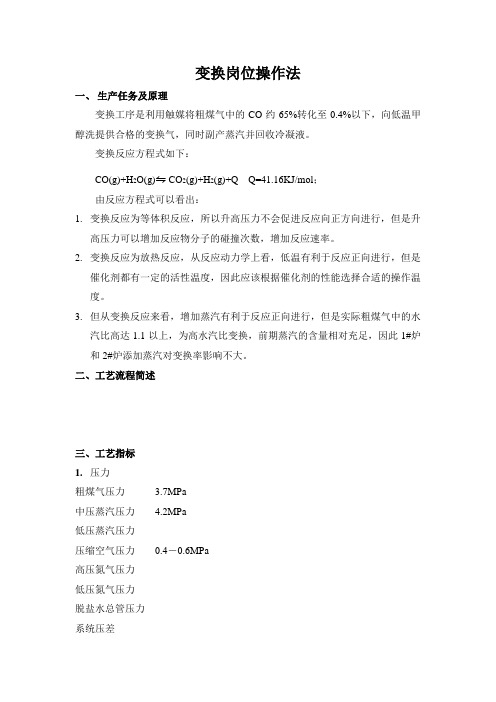
变换岗位操作法一、生产任务及原理变换工序是利用触媒将粗煤气中的CO约65%转化至0.4%以下,向低温甲醇洗提供合格的变换气,同时副产蒸汽并回收冷凝液。
变换反应方程式如下:CO(g)+H2O(g)⇋ CO2(g)+H2(g)+Q Q=41.16KJ/mol;由反应方程式可以看出:1.变换反应为等体积反应,所以升高压力不会促进反应向正方向进行,但是升高压力可以增加反应物分子的碰撞次数,增加反应速率。
2.变换反应为放热反应,从反应动力学上看,低温有利于反应正向进行,但是催化剂都有一定的活性温度,因此应该根据催化剂的性能选择合适的操作温度。
3.但从变换反应来看,增加蒸汽有利于反应正向进行,但是实际粗煤气中的水汽比高达1.1以上,为高水汽比变换,前期蒸汽的含量相对充足,因此1#炉和2#炉添加蒸汽对变换率影响不大。
二、工艺流程简述三、工艺指标1.压力粗煤气压力 3.7MPa中压蒸汽压力 4.2MPa低压蒸汽压力压缩空气压力0.4-0.6MPa高压氮气压力低压氮气压力脱盐水总管压力系统压差2、温度粗煤气温度出工段变换气温度40o C1#变换炉进口温度260±5o C 1#变换炉出口温度380±5o C2#变换炉进口温度240±5o C 2#变换炉出口温度430±5o C3#变换炉进口温度220±5o C 3#变换炉出口温度260±5o C4#变换炉进口温度200±5o C 4#变换炉出口温度200±5o C四、设备五、控制要点1.精心控制变换炉进口温度,注意床层温度变化情况,能够对异常情况作出正确的判断并及时处理;2.细心观察炉温变化,总结规律和影响因素,避免炉温波动过大,损坏催化剂;3.严格控制各工艺指标,保证系统安全、稳定生产;4.生产负荷变化时,做到及时调整,保证炉温稳定和出口达标;5.加强各处导淋排放,控制变换炉进口温度在露点温度30o C以上,防止液体水进入床层,损坏触媒;6.控制各蒸发冷凝器液位、压力正常,稳定各点温度并外送合格蒸汽,同时防止超温或蒸汽倒流现象发生;7.根据前后工段的生产情况,选择合适的调节手段,控制变换系统稳定正常运行;8.沉着冷静,针对突发情况作出正确判断并及时处理;9.遵循一定的路线按时对整个变换系统进行巡检,准确掌握各个设备的使用和运行情况;六、原始开车1、开车前应具备的条件:①各设备、管道安装到位,系统吹扫、清洗干净,气密合格氮气置换合格;②各处盲板抽堵正常;③仪表控制设施安装正确,DCS调试完毕;④安全设施全部到位,安全阀已经校检;⑤相关公用工程具备使用条件;⑥各泵盘车正常备用;⑦变换炉催化剂装填完毕,具备充压条件;2、升温硫化(厂家提供)3、开车①根据变换炉床层温度判断是否需要电炉升温;②检查升温硫化及置换管线上各盲板是否完全关闭,关闭各分离器出口阀门、导淋和放空;③往E-20108上段壳程通入溴化锂冷却水,给V-20101建立一定液位;开启P-20101、P-20102、P-20103,给E-20102、E-20104、E-20105、E-20107、E-20111建立一定液位,用管网蒸汽对各个蒸发冷凝器进行预热;开启P-20107给V-20103建立一定液位;利用脱盐水给S-20102和E-20108下段建立一定液位后,开启P-20104、P-20105往E-20103壳程通入冷却水;E-20109壳程通入循环冷却水;开启P-20101给E-20106通入冷却水;利用管网蒸汽对各个蒸汽添加管线暖管(打开导淋);④缓慢打开界区阀XV1001的旁路均压阀,对系统前后进行均压;⑤均压结束后,打开XV1001界区阀,调节PV201018开度,控制系统压力,对变换炉床层进行升温,同事注意排放各处冷凝液,调节蒸汽用量,严格控制升温速率,防止超温飞温现象发生;(接气后给S-20104通入脱盐水,同时往C-20101通入气提蒸汽)⑥根据工艺指标调节个参数,待出口变换气分析合格后想后工段送气,并关闭PV201018;七、开停车1.长期停车①通知调度变换长期停车,请相关工段做好相应的处理;②根据气量的减少,逐渐减少蒸汽和水的添加量直到完全切断蒸汽和水;③依次停下P-20104、P-20105、P-20103、P-20102、P-20101、P-20106、P-20107、P-20108八台泵并排净泵内的液体;同时关闭蒸发冷凝器的压力控制阀PV1034、PV1035、PV1036、PV1037、PV1020,排净蒸发冷凝器内的水,关闭各自的液位调节阀;④关闭粗煤气界区阀XV1001;⑤关闭变换气去低温甲醇洗界区阀HV1001;⑥将系统卸至常压,然后用干煤气或者惰性气体(N2)保压;2. 短期停车①停车前4小时适当的提高各变换炉的温度;②通知调度变换停车,请相关工段做好相应的处理;③根据气量的减少逐步减少蒸汽和水的添加量直至切断蒸汽和水的添加;④依次停下P-20104、P-20105、P-20103、P-20102、P-20101、P-20106、P-20107、P-20108八台泵;同时关闭蒸发冷凝器的压力控制阀PV1034、PV1035、PV1036、PV1037、PV1020,根据蒸发冷凝器内的液位,关闭各自的液位调节阀;⑤关闭粗煤气界区阀XV1001;⑥关闭变换气去低温甲醇洗界区阀HV1001;⑦整个系统做保温保压处理;⑧注意排净各蒸汽以及工艺气管线上各处的导淋。
一氧化碳变换反应实验报告思考题目
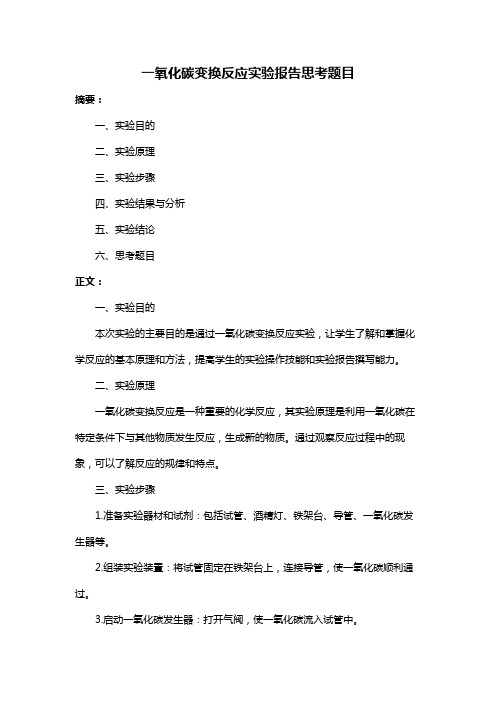
一氧化碳变换反应实验报告思考题目摘要:一、实验目的二、实验原理三、实验步骤四、实验结果与分析五、实验结论六、思考题目正文:一、实验目的本次实验的主要目的是通过一氧化碳变换反应实验,让学生了解和掌握化学反应的基本原理和方法,提高学生的实验操作技能和实验报告撰写能力。
二、实验原理一氧化碳变换反应是一种重要的化学反应,其实验原理是利用一氧化碳在特定条件下与其他物质发生反应,生成新的物质。
通过观察反应过程中的现象,可以了解反应的规律和特点。
三、实验步骤1.准备实验器材和试剂:包括试管、酒精灯、铁架台、导管、一氧化碳发生器等。
2.组装实验装置:将试管固定在铁架台上,连接导管,使一氧化碳顺利通过。
3.启动一氧化碳发生器:打开气阀,使一氧化碳流入试管中。
4.观察实验现象:在一氧化碳的作用下,试剂发生反应,观察反应过程中的现象。
5.记录实验数据:记录实验过程中各个阶段的现象和数据。
6.实验结束:关闭气阀,整理实验器材。
四、实验结果与分析实验结果显示,在特定条件下,一氧化碳与其他物质发生反应,生成了新的物质。
通过对实验数据的分析,可以得出反应的规律和特点。
五、实验结论通过本次实验,学生可以了解一氧化碳变换反应的原理和方法,掌握实验操作技能,提高实验报告撰写能力。
同时,本次实验也有助于培养学生的观察力、思维能力和实验能力。
六、思考题目在实验过程中,学生可以思考以下问题:1.一氧化碳变换反应的原理是什么?2.实验中观察到了哪些现象?这些现象说明了什么?3.如何根据实验数据分析反应的规律和特点?4.如何撰写一份完整的实验报告?。
变换,安全知识试题

变换岗位试题一、填空1.变换反应的化学反应式是:,此反应的特点是:①②③④。
2.饱和塔的作用是,热水搭的作用是,这两个设备的目的是为了维持系统的平衡及平衡。
3.饱和塔出口气体温度越高,则系统自产蒸汽越(多、少),外加蒸汽越(多、少)。
4.进系统半水煤气CO含量大约是% ,CO2含量大约是 %,O2含量大约是%,出系统变换气CO含量大约是%,CO2含量大约是% 。
5.硫化用的cs2起火时,(能、不能)用水来灭火,因为cs2的比重要比水,且cs2(溶、不溶)于水。
6.甲系变换系统进口压力表接在系统进口阀(前、后);碳系变换半水煤气进口压力表接在系统进口阀(前、后),变换气压力表接在系统出口阀(前、后),变换炉进口压力表接在。
7.启用电炉前必须经检查,并先后才能启用电炉,目前低变共有组,全低变有组。
8.硫化时遇到飞温时要及时停、停、停硫化结束标志的三到是指:。
9.本岗位的蒸气来自于。
10.甲系变换与碳系变换的进口连通副线是从接至;出口连通副线是从接至。
11.能使变换触媒中毒的物质有。
12.本岗位的电加热器为电加热器,它是根据半水煤气中的CO、CO2 以及水蒸气等能吸收的原理制成的一种的辐射加热器。
13.操作工“六严格”是指:。
14.本岗位的有毒有害物质有。
操作工的“三懂四会”是指:。
15.变换岗位的喷水器的主要作用是。
16.催化剂的主要作用是。
17.本岗位共有台热水泵,其规格型号分别是是,正常生产时电流分别是A。
18.正常生产时热水泵出口压力与饱和塔出口之间的压差为Mpa,系统进口与饱和塔出口之间的压差为Mpa,系统进出口之间的压差为Mpa。
19.机械过滤器出口没有压力的主要原因。
20.变换出口管比进口管(大、小),原因是。
21.CO升高应该通知的岗位有。
22.硫化副线是直接从接至变换岗位,共有根。
23.要提变换炉一段触媒层的温度,可(关小、开大)(1#、2#)副线。
24.室内压力表从左至右分别是。
25.室内CO压力表的量程是,目前工作档是档,其气源根部引自,目前CO指标控制在,1格=% 。
一氧化碳变换技术交流

℃
• 但实际上完全按最适宜温度曲线操作是不可能的,因 为在反应开始时,最适宜温度最高(以中温变换为例, 要达到620℃以上),大大超过催化剂的耐热温度, 而且热量的来源是个问题。随着反应的进行,要不断 地、准确地按照最适宜温度的需要移出反应热是极为 困难的,见二 段CO变换的T-x图。 图中: CD即为最适宜温度曲线,AB为平衡曲线,EF线为第 一段绝热反应线,FG线表示段间间接换热降温过程。 GH线表示第二段绝热反应线。。 • 变换过程的温度应综合各个方面因素来确定,主要原 则是: • 1)、反应开始温度应高于催化剂活性温度10~20℃ 左右。另外必须要高于气体露点温度20℃以上(防止 原料气析水,一是使催化剂粉碎结块,二是腐蚀设 备)。
CS2+4H2 2H2S+CH4+246 kJ∕mol MoO3+2H2S+H2 MoS2+3H2O+48.1 kJ∕mol CoO+H2S CoS+H2O+13.4 kJ∕mol • 升温硫化一般采用循环硫化法,升温硫化阶段所需要的热 量主要靠电加热器提供。 • 3)国内外Co-Mo系耐硫变换催化剂的发展历程 • ⑴1969年德国BASF公司开发成功的K8-11耐硫变换催化 剂(镁铝尖晶石复合材料为载体),1978年首次实现工业 化的应用,用于重油部分氧化法制合成气流程和加压煤气 化制合成氨流程的CO变换。它的主要特点是以镁铝尖晶 石为载体,硫化后活性高,耐高水蒸汽分压,可在高压下使用, 抗毒物能力强,能再生,平均寿命 3~5年。
• 由于变换反应是放热反应,降低温度有利于平衡 向右移动,因此平衡常数随温度的降低而增大。 例如:250℃时为86.51,450℃时为:7.311。 • 在工业生产中,受催化剂装填量、设备投资的经 济效益等因素影响,反应不可能也没必要达到平 衡,只能尽可能接近平衡。 • 实际生产的流程组合中,一般利用高温段之后再 进行低温变换,就是为了提高反应平衡常数,从 而提高变换率,降低变换气CO含量。
变换岗位问答

(3)活性组份流失;
(4)因毒物的带入而使触媒中毒;
(5)因杂物堵塞微孔或高温烧结等原因导致的触媒比表面积降低;
(6)因触媒长期在较高温下使用而导致的低温活性下降。
8、如何延长变换触媒的使用寿命?
答:操作中为延长触媒使用寿命,应注意以下几点:
a.水气比增大,入炉总气量增大,CO反应不完全就可能出炉;
b.增大了热量回收系统的负荷;
d.水蒸汽分压增大,露点温度升高,从而限制了低变的入口温度。
(4)空速:空速过大则气体在炉内停留时间太短,CO来不及反应即出炉,空速过小则生产能力小,形成浪费,空速的选择要考虑触媒的活性及设备的生产能力。
(5)副反应的影响:一氧化碳变换过程中,可能发生下列副反应:
(7)充压、卸压时控制好速率不要过快;
(8)接气时提温缓慢,避免触媒毒物有带入。
9、变换开车接气时,如何防止一变炉带水?
答:首先接气前需要预热外管,排放分离器、管线导淋积水,接气时采取常压接气或较低压力下接气,缓慢提压,接气过程中也要及时排放分离器,管线导淋冷凝水。
11、废锅为什么要排污?排污率为多少?水质分析指标为多少?
(1)变换炉的进口温度控制在指标之内,在触媒的使用前期尽量使用触媒温度范围的低限区;
(2)触媒在升温硫化时,应严格按照升温硫化方案执行,因升温硫化的好坏直接影响触媒的活性及使用寿命;
(3)严禁带水带氧入炉;
(4)避免长时间存在过高水气比,避免无硫操作;
(5)尽量避免负荷大幅度变动,频繁开停车;
(6)严格控制炉温,防止床层超温,避免床温大幅度波动;
(3)原料气中粉尘等杂质阻塞触媒表面;
(4)触媒分布不均匀,气流偏流;
CO shift变换
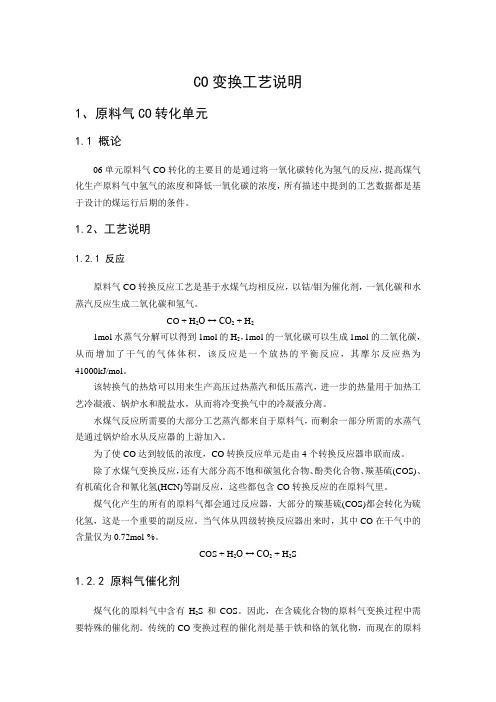
CO变换工艺说明1、原料气CO转化单元1.1 概论06单元原料气CO转化的主要目的是通过将一氧化碳转化为氢气的反应,提高煤气化生产原料气中氢气的浓度和降低一氧化碳的浓度,所有描述中提到的工艺数据都是基于设计的煤运行后期的条件。
1.2、工艺说明1.2.1 反应原料气CO转换反应工艺是基于水煤气均相反应,以钴/钼为催化剂,一氧化碳和水蒸汽反应生成二氧化碳和氢气。
CO + H2O ↔ CO2 + H21mol水蒸气分解可以得到1mol的H2,1mol的一氧化碳可以生成1mol的二氧化碳,从而增加了干气的气体体积,该反应是一个放热的平衡反应,其摩尔反应热为41000kJ/mol。
该转换气的热焓可以用来生产高压过热蒸汽和低压蒸汽,进一步的热量用于加热工艺冷凝液、锅炉水和脱盐水,从而将冷变换气中的冷凝液分离。
水煤气反应所需要的大部分工艺蒸汽都来自于原料气,而剩余一部分所需的水蒸气是通过锅炉给水从反应器的上游加入。
为了使CO达到较低的浓度,CO转换反应单元是由4个转换反应器串联而成。
除了水煤气变换反应,还有大部分高不饱和碳氢化合物、酚类化合物、羰基硫(COS)、有机硫化合和氰化氢(HCN)等副反应,这些都包含CO转换反应的在原料气里。
煤气化产生的所有的原料气都会通过反应器,大部分的羰基硫(COS)都会转化为硫化氢,这是一个重要的副反应。
当气体从四级转换反应器出来时,其中CO在干气中的含量仅为0.72mol-%。
COS + H2O ↔ CO2 + H2S1.2.2 原料气催化剂煤气化的原料气中含有H2S和COS。
因此,在含硫化合物的原料气变换过程中需要特殊的催化剂。
传统的CO变换过程的催化剂是基于铁和铬的氧化物,而现在的原料气变换中催化剂包含一个特殊的载体,钴和钼的氧化物。
对于不含硫的气体,基于铁和铬的氧化物的催化剂可以表现它最大的活性,而对于含硫酸性气体转换的催化剂则是基于钴和钼的氧化物,而且只有在硫化物存在的情况下才能表现出最大的活性。
一氧化碳变换
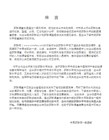
3、较好的选择性 4、催化剂对毒物灵敏性小、机械强度高、耐热性好、使用寿
命长、价格低廉及原料易得等
变换催化剂分类
催化剂 催化剂 按组成 分类
按反应 温度分 类
中 温 变 换
低 温 变 换
耐 硫 低 变
铁 铬 系
铜 锌 系
钴 钼 系
“工程实践教学观摩中心”汇集了100多种固体催化剂,包括 中低变催化剂,欢迎各位同学参观,
优点
a 设备体积小,节省投资。
b 增加空速,提高生产能力 c 有利于热能回收 热能的品位得以提高,有利于热量回收。 d 费托合成 CO+H2 →CnH2n+2nH2O 被抑制 在汽气比非常小时有费托合成, 冷激流程可抑制费托合 成反应的发生。
e 电耗降低
a 腐蚀加剧(点蚀 ),设备使用寿命缩短。 (尤其是采用耐硫变换催化剂流程) b 有机硫转化↓
摩尔分数
1
150 200 250 300 350 400 450 500 550 600 0.009538 0.016999 0.027313 0.059030 0.078495 0.099126 0.120184 0.141059 0.161286 0.180547
3
0.001757 0.002137 0.003017 0.008375 0.015234 0.024781 0.036818 0.050849 0.066249 0.082407
最佳操作温度
动力学的影响
高温加快反应速度
Te 平衡温度 Tm 最适宜操作温度 E1正反应活化能 E2逆反应活化能 平衡温度和最适宜温度的关系随温度的关系 使反应沿最适宜温度曲线进行时反应器利用率最大、 催化剂用量最少
CO变换操作知识问答
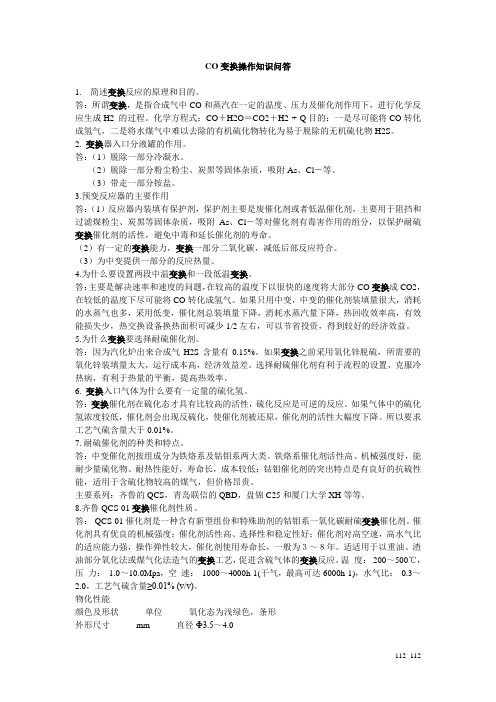
CO变换操作知识问答1. 简述变换反应的原理和目的。
答:所谓变换,是指合成气中CO和蒸汽在一定的温度、压力及催化剂作用下,进行化学反应生成H2 的过程。
化学方程式:CO+H2O=CO2+H2 + Q目的:一是尽可能将CO转化成氢气,二是将水煤气中难以去除的有机硫化物转化为易于脱除的无机硫化物H2S。
2. 变换器入口分液罐的作用。
答:(1)脱除一部分冷凝水。
(2)脱除一部分粉尘粉尘、炭黑等固体杂质,吸附As、Cl-等。
(3)带走一部分铵盐。
3.预变反应器的主要作用答:(1)反应器内装填有保护剂,保护剂主要是废催化剂或者低温催化剂,主要用于阻挡和过滤煤粉尘、炭黑等固体杂质,吸附As、Cl-等对催化剂有毒害作用的组分,以保护耐硫变换催化剂的活性,避免中毒和延长催化剂的寿命。
(2)有一定的变换能力,变换一部分二氧化碳,减低后部反应符合。
(3)为中变提供一部分的反应热量。
4.为什么要设置两段中温变换和一段低温变换。
答:主要是解决速率和速度的问题,在较高的温度下以很快的速度将大部分CO变换成CO2,在较低的温度下尽可能将CO转化成氢气。
如果只用中变,中变的催化剂装填量很大,消耗的水蒸气也多,采用低变,催化剂总装填量下降,消耗水蒸汽量下降,热回收效率高,有效能损失少,热交换设备换热面积可减少1/2左右,可以节省投资,得到较好的经济效益。
5.为什么变换要选择耐硫催化剂。
答:因为汽化炉出来合成气H2S含量有0.15%。
如果变换之前采用氧化锌脱硫,所需要的氧化锌装填量太大,运行成本高,经济效益差。
选择耐硫催化剂有利于流程的设置,克服冷热病,有利于热量的平衡,提高热效率。
6. 变换入口气体为什么要有一定量的硫化氢。
答:变换催化剂在硫化态才具有比较高的活性,硫化反应是可逆的反应。
如果气体中的硫化氢浓度较低,催化剂会出现反硫化,使催化剂被还原,催化剂的活性大幅度下降。
所以要求工艺气硫含量大于0.01%。
7. 耐硫催化剂的种类和特点。
- 1、下载文档前请自行甄别文档内容的完整性,平台不提供额外的编辑、内容补充、找答案等附加服务。
- 2、"仅部分预览"的文档,不可在线预览部分如存在完整性等问题,可反馈申请退款(可完整预览的文档不适用该条件!)。
- 3、如文档侵犯您的权益,请联系客服反馈,我们会尽快为您处理(人工客服工作时间:9:00-18:30)。
CO变换操作知识问答1. 简述变换反应的原理和目的。
答:所谓变换,是指合成气中CO和蒸汽在一定的温度、压力及催化剂作用下,进行化学反应生成H2 的过程。
化学方程式:CO+H2O=CO2+H2 + Q目的:一是尽可能将CO转化成氢气,二是将水煤气中难以去除的有机硫化物转化为易于脱除的无机硫化物H2S。
2. 变换器入口分液罐的作用。
答:(1)脱除一部分冷凝水。
(2)脱除一部分粉尘粉尘、炭黑等固体杂质,吸附As、Cl-等。
(3)带走一部分铵盐。
3.预变反应器的主要作用答:(1)反应器内装填有保护剂,保护剂主要是废催化剂或者低温催化剂,主要用于阻挡和过滤煤粉尘、炭黑等固体杂质,吸附As、Cl-等对催化剂有毒害作用的组分,以保护耐硫变换催化剂的活性,避免中毒和延长催化剂的寿命。
(2)有一定的变换能力,变换一部分二氧化碳,减低后部反应符合。
(3)为中变提供一部分的反应热量。
4.为什么要设置两段中温变换和一段低温变换。
答:主要是解决速率和速度的问题,在较高的温度下以很快的速度将大部分CO变换成CO2,在较低的温度下尽可能将CO转化成氢气。
如果只用中变,中变的催化剂装填量很大,消耗的水蒸气也多,采用低变,催化剂总装填量下降,消耗水蒸汽量下降,热回收效率高,有效能损失少,热交换设备换热面积可减少1/2左右,可以节省投资,得到较好的经济效益。
5.为什么变换要选择耐硫催化剂。
答:因为汽化炉出来合成气H2S含量有0.15%。
如果变换之前采用氧化锌脱硫,所需要的氧化锌装填量太大,运行成本高,经济效益差。
选择耐硫催化剂有利于流程的设置,克服冷热病,有利于热量的平衡,提高热效率。
6. 变换入口气体为什么要有一定量的硫化氢。
答:变换催化剂在硫化态才具有比较高的活性,硫化反应是可逆的反应。
如果气体中的硫化氢浓度较低,催化剂会出现反硫化,使催化剂被还原,催化剂的活性大幅度下降。
所以要求工艺气硫含量大于0.01%。
7. 耐硫催化剂的种类和特点。
答:中变催化剂按组成分为铁烙系及钴钼系两大类。
铁烙系催化剂活性高、机械强度好,能耐少量硫化物、耐热性能好,寿命长,成本较低;钴钼催化剂的突出特点是有良好的抗硫性能,适用于含硫化物较高的煤气,但价格昂贵。
主要系列:齐鲁的QCS,青岛联信的QBD,盘锦C25和厦门大学XH等等。
8.齐鲁QCS-01变换催化剂性质。
答:QCS-01催化剂是一种含有新型组份和特殊助剂的钴钼系一氧化碳耐硫变换催化剂。
催化剂具有优良的机械强度;催化剂活性高、选择性和稳定性好;催化剂对高空速,高水气比的适应能力强,操作弹性较大,催化剂使用寿命长,一般为3~8年。
适适用于以重油、渣油部分氧化法或煤气化法造气的变换工艺,促进含硫气体的变换反应。
温度:200~500℃,压力:1.0~10.0Mpa,空速:1000~4000h-1(干气,最高可达6000h-1),水气比:0.3~2.0,工艺气硫含量≥0.01% (v/v)。
物化性能颜色及形状单位氧化态为浅绿色,条形外形尺寸mm 直径Ф3.5~4.0堆密度kg/l 0.70~0.80抗压碎力N/cm ≥100(平均值)载体Mg--Al—Ti尖晶石活性组份Co--Mo6助剂m/m 稀土9.齐鲁QCS-03变换催化剂性质。
答:QCS-03催化剂是一种含有新型组份和特殊助剂的第二代钴钼系一氧化碳耐硫变换催化剂。
催化剂具有优良的机械强度;催化剂活性高、选择性和稳定性好;催化剂对高空速,高水气比的适应能力强,操作弹性较大,催化剂使用寿命长,一般为3~8年。
适适用于以重油、渣油部分氧化法或煤气化法造气的变换工艺,促进含硫气体的变换反应。
温度:200~500℃,压力:1.0~10.0Mpa,空速:1000~4000h-1(干气,最高可达6000h-1),水气比:0.3~2.0,工艺气硫含量≥0.01% (v/v)。
物化性能颜色及形状单位氧化态为浅绿色,条形外形尺寸mm 直径Ф3.5~4.0堆密度kg/l 0.80~0.90抗压碎力N/cm ≥140(平均值)载体Mg--Al--Ti尖晶石活性组份Co--Mo助剂m/m 稀土10.预硫化反应的原理。
答:变换催化剂QCS-01和QCS-03是钴钼系耐硫变换催化剂,新催化剂是氧化态,在使用前要先进行硫化,只有硫化过的催化剂才具有活性,硫化过程的主要反应式:CoO + H2S = CoS + H2O + 3.2KcalMoO3 + 2H2S + H2 = MoS2 + 3H2O + 11.5Kcal11.钴钼系耐硫催化剂使用前为什么要硫化?答:因为钴钼催化剂中真正的活性组份是COS和MOS2,因此,必须经过硫化才具有变换活性。
硫化的目的还在于防止钴钼氧化物被还原成金属态,而金属态钴钼可促进一氧化碳和氢气发生甲烷化反应,这一强放热反应有可能造成巨大的温升,而将催化剂烧坏。
所以使用前要硫化。
12.催化剂预硫化方法。
答:催化剂预硫化一般分为湿法预硫化和干法预硫化两种。
湿法预硫化是在氢气存在下,采用硫化剂和馏分油在液相或半液相状态下的预硫化。
干法预硫化是在氢气存在下,直接用含有一定浓度的H2S或直接向循环氢中注入有机硫化物进行的预硫化。
湿法预硫化又分为两种:一种是催化剂硫化过程所需要的硫由外部加入来进行预硫化;另一种是依靠硫化油自身的硫进行预硫化。
本装置预硫化过程所需要的硫,采用外部加入二甲基二硫化物(DMDS)或者CS2)的方法。
13. 常用的硫化剂有那几种。
答。
有硫化氢、二甲基二硫化物(DMDS)和CS2。
14.变换催化剂的主要活性组分和载体是什么?答:变换催化剂活性组分CoO3和MoO3,载体:(MgO,Al2O3,新物质为余量)。
15.变换催化剂首次接气时应注意哪些问题?答:(1)向系统内送气时,蒸汽暖管及换热器预热要合格,导淋排放要合格。
应配备足够氮气量防止接气过程中出现超温。
(2)保持催化剂的床层温度不低于270℃。
(3)增压过程要缓慢,当压力增至1.0-1.5Mpa时,最好运行3-4个小时后再逐步增压,以使催化剂在压力下继续深度硫化,从而发挥更好的催化活性。
16.变换催化剂硫化时应注意哪些事项?答:(1)原则上加硫不提温,以防止硫化过程超温。
因为补加氢气加二硫化的方法为循环硫化法,硫化过程只有少量气体排出系统,二硫化碳需在催化剂表面氢解和水解所以循环气中氢气要有一定含量,补加二硫化碳前分析循环气中氢气的含量,每次增加二硫化碳后要及时分析变换炉后即循环机入口处氢气含量,要求变换炉后氢气含量在10%-15%之间。
(2)硫化时,严格控制床层空速在400-500h-1,以使催化剂与硫化剂充分接触和反应。
(3)若床层温度增长过快并超过450℃时,要立即停加CS2,降低N2入口温度并加大循环气的流量,使床层降温。
(4)补入CS2量一定要有专人负责,CS2加入量要缓慢和稳定,防止CS2过量,使床层超温或在系统内冷凝和吸附,以出口H2S不超过15g/m3为宜。
硫化结束后用氮气将系统彻底置换合格,各道淋取样分析H2S为零,系统保正压。
17.变换催化剂装填时,应注意什么事项?答:(1)运输和装填时候意防潮措施,以免使催化剂受潮。
(2)在运输、过筛、起吊、充装过程中要轻拿轻放,不能摔打或滚动催化剂桶。
(3)装填时亦不能超过规定的下落高度,造成催化剂的粉碎。
(4)在往设备内撒放触煤时,应沿整个平面均匀分布,不允许撒在一块,堆成山形,然后耙开,以免尘集聚,阻力不均。
触媒装填量应按规定,不能少装也不要过量。
(5)在设备内工作时,要严格注意不损坏内件,热电偶管周围要装实。
18.如何延长变换催化剂寿命。
答:1)正常使用时,在满足出口CO含量的要求下,尽可能降低进口温度(高于露点30℃以上);2)防止超温超压和超负荷,防止工艺气降低至露点温度;3)控制好进口分离器液位,防止带水;4)防止有毒物质进入反应器。
5 )合适的水汽比。
6)催化剂装填硫化效果好。
19.简述停车过程中,预防催化剂损坏的措施。
答:(1)开压缩机建立循环时,应在装置负荷较低时进行,做好平稳操作;(2)停进料要及时用氮气置换;(3)控好反应器的降温速度;(4)停车过程中降压要缓慢。
(5)降温时注意防止水蒸气冷凝。
20.哪些因素对变换反应器负荷产生影响?答:(1)催化剂性能;(2)反应热量;(3)反应空速;(4)原料的预热温度;(5)原料的质量;(6)反应器的压差(7)反应器热量的分布。
21. 写出催化剂硫化反应方程式?答:(1)硫化反应CoO+H2S CoS+H2OMoO3+2H2S+H2 MoS2+3H2O(2)副反应变换反应CO+H2O(g) CO2+H2甲烷化反应CO+3H2 CH4+H2OCO2+4H2 CH4+2H2O22. 提高变换转化率有哪些措施?答:(1)提高反应器入口、出口温度;适当提高水气比;(2)减小反应器温差;(3)选用活性高的催化剂;(4)选用优质原料。
23. 影响变换效果的主要因素有哪些。
答:(1)催化剂活性,(2)温度,(3)空速,(4)水汽比(5)硫化氢浓度,(6)原料的性质,(7)床层压差。
24. 什么叫硫容?答:硫容就是每单位重量脱硫剂所能吸收硫的重量。
饱和硫容,在一定的实验条件下,单位重量脱硫剂所能吸收硫的最大重量。
换言之,即进脱硫剂和出脱硫剂的原料气中硫含量相等时,此时脱硫剂再不能吸收硫。
卸下后脱硫剂所测定的硫容量叫饱和硫容。
穿透硫容,在一定使用条件下,脱硫剂在确保工艺净化度指标时所能吸收硫的重量。
换言之,即当出口工艺气中硫含量出现大于工艺净化度指标时,立即卸下全部废脱硫剂,取平均样测定的硫容量叫穿透硫容。
一般产品说明书上将提供一定使用条件的重量穿透硫容。
理论硫容,按其化学反应方程式计算出来的硫容。
40.什么叫硫穿透?答:氧化锌在脱硫过程中,上层的饱和区不断增大;中层的吸收区基本不变但位置下移;下层的清净区逐渐减少直至最后消失;这时脱硫反应器出口硫含量迅速增高,直至超指标,即称为硫穿透。
41.简述氧化锌脱硫剂的性质。
氧化锌脱硫剂按照使用温域范围分类:高温(100-300度)氧化锌脱硫剂、常温(30-120度)氧化锌脱硫剂,其中高温氧化锌脱硫剂的氧化锌含量都大于90%,型号如:T305\T306\JX-4C 等;常温氧化锌脱硫剂的氧化锌含量70%,型号:KT310\T307\JX-4D等。
42. 影响氧化锌脱硫的主要因素有哪些。
答:(1)脱硫剂自身的特性,温度,空速,水汽比和硫化物的类型和浓度。
43. 甲烷化前为什么要设置氧化锌脱硫?答: 甲烷化催化剂主要活性组分是镍,载体是活性氧化铝氧化镁等,催化剂在使用前要经过活化,将氧化镍还原为镍才有活性.而硫化氢会和镍生产硫化镍. 甲烷化催化剂吸附0.1%的硫和0.05%的氯会丧失大部分活性而中毒.44. 氧化锌脱硫原理.答:在一定的温度和压力下, 氧化锌能与H2S反应生成难于解离的ZnS,ZnO也能吸收一般的有机硫化物.化学反应式: ZnO+H2S=ZnS+H2O45. 温度对氧化锌脱硫影响.答: 氧化锌脱硫过程是一个放热过程,但温度越高越有利于提高脱硫效果,因为有些有机硫在较高的温度下,能转化为无机硫;另外,脱硫剂的硫容与温度成正比,提高温度可以提高硫容,特别是使用后期,但温度超过420℃会造成烃类裂解而结碳.46. 空速对氧化锌脱硫影响.答:在保证有足够的线速度,不存在气膜效应的前提下,采用较低的空速对提高脱硫效率是有利的。