XX钢铁集团原料场堆取料机防碰撞技术方案
圆形料场堆取料机刮板机防撞装置

图1 圆形料场堆取料机悬臂式刮板机是圆形料场堆取料机的取料机构,通常安装在取料回转平台下部铰座处。
刮板机主要由悬臂、导轨、驱动链轮、改向轮、链条和刮板组成,悬臂前部安装有悬挂,悬挂上安装动滑轮组。
刮板机在不同区域进行取料作业时,取料回转平台连同刮板机必须进行一Copyright©博看网. All Rights Reserved./ 2017年第9期图2 原防撞装置安装当防撞检测板与料堆相撞时,防撞检测板23旋转,接近开关检测板11与接近开关10远离,接近开关常闭触点闭合。
PLC 的DI4输入模块相对应的输入点变成高电平24 V ,PLC 的DI4输入模块相对应通道的指示灯亮,刮板机回转保护停机。
DI4输入模块接线图所示,PLC 程序如图4所示。
图3 DI4模块接线图图4 PLC 程序图5 防撞装置安装图4.1 主要零部件介绍1)底座防撞装置底座采用Q345B 材料制作,设计时底座的末端圆弧与刮板机悬臂外径一致,便于焊接安装,底Copyright ©博看网. All Rights Reserved.底座 2. 拨杆 3. 接近开关 4. 接近开关底座 5. 筒体6. 销轴7. 圆柱螺旋压缩弹簧8. 法兰9. 检测板图6 防撞装置装配图2)法兰防撞装置法兰采用Q345B材料制作,设计时考虑合理定位,法兰外侧加装挡板,限制销轴旋转,确保销轴和检测板准确动作和可靠复位,确保拨杆与接近开关准确靠近和远离。
3)筒体筒体采用Q345B材料制作,设计时仅需考虑长度合适、刚度足够即可。
4)销轴销轴采用SUS304材料制作,其首、末端需铣制平面,装配后能周向定位,以保证其连接的拨杆能准确、可靠地与接近开关靠近或远离。
销轴零件图如图7所示。
5)圆柱螺旋压缩弹簧圆柱螺旋压缩弹簧采用50CrV A材料制作,喷丸处理,设计时主要考虑有效圈数、总圈数、自由长度、弹簧直径和屈服系数。
图7 销轴零件图4.2 安装及调试防撞装置底座与刮板机悬臂和下导轨采用焊接连接,销轴与检测板采用焊接连接,其余零部件均采用螺栓或螺钉连接。
炼钢厂物体打击事故的预防及其应急预案

炼钢厂物体打击事故的预防及其应急预案物体打击伤害是建筑行业常见事故中五大伤害的其中一种,特别在施工周期短,劳动力、施工机具、物料投入较多,交叉作业时常有出现。
这就要求在高处作业的人员对机械运行、物料传接、工具的存放过程中,都必须确保安全,防止物体坠落伤人的事故发生。
1. 常见物体打击事故主要有:(1)在高空作业中,由于工具零件、砖瓦、木块等物从高处掉落伤人;(2)人为乱扔废物、杂物伤人;(3)起重吊装、拆装、拆模时,物料掉落伤人;(4)设备带“病”运行,设备中物体飞出伤人;(5)设备运转中,违章操作,用铁棍捅卡料,铁棍飞弹出伤人;(6)压力容器爆炸的飞出物伤人;(7)放炮作业中乱石伤人等。
2.预防物体打击事故的措施(1)人员进入施工现场必须按规定配戴好安全帽。
在高处作业的人员,衣着要灵便,不准穿高跟鞋、拖鞋;不得攀爬脚手架或乘运料井架吊篮上下。
应在规定的安全通道内出入和上落,不得在非规定通道位置行走。
(2)凡4米以上的在施工程,首层要设1道的安全网,每隔4m再支一道固定安全网;同时在施工层处必须设一道安全网。
若采取立网防护,立网应高出建筑物(作业面)1米以上。
在同一垂直方向上同时进行多层交叉作业时,必须设有隔离防护棚。
(3)各种脚手架的搭设必须符合国家标准。
每层要设护身栏和挡脚板(高度在18㎝以上)以防物料从平台缝隙或栏杆底部漏下。
(4)施工层脚手板必须铺严,架子上不准留单跳板、探头板。
脚手板与建筑物之间距离得大于20厘米。
各种脚手架使用前应经过安全技术部门的验收。
(5)安全通道(施工洞口)上方应搭设双层防护棚,防护棚的长度不少于3米,同时设有安全警告标志和夜间警示红灯。
防护棚使用的材料要能防止高空坠落物穿透。
(6)施工现场的一切孔、洞,必须设置围栏、盖板、架网等防护措施。
(7)作业过程一般常用工具必须放在工具袋内,任何人都不准从高处向人抛掷物料,吊装运输零散物料时,要用吊笼或吊斗。
同时也应消除各种物品被无意碰落或被风吹落的可能因素。
堆取料机事故预案

一、总则1.1 编制目的为保障堆取料机作业过程中的安全,防止和减少事故的发生,提高事故应急处理能力,保障人员生命财产安全,特制定本预案。
1.2 适用范围本预案适用于公司堆取料机作业过程中的各类事故,包括但不限于机械故障、火灾、触电、中毒、窒息等。
1.3 工作原则(1)预防为主,安全第一;(2)统一指挥,分级负责;(3)快速反应,协同处置;(4)以人为本,减少损失。
二、组织机构及职责2.1 事故应急指挥部成立堆取料机事故应急指挥部,负责组织、协调、指挥事故应急工作。
2.1.1 指挥部组成(1)指挥长:公司总经理;(2)副指挥长:公司副总经理;(3)成员:安全总监、生产部经理、设备部经理、人力资源部经理、保卫部经理等。
2.1.2 指挥部职责(1)组织、协调、指挥事故应急工作;(2)确定事故应急响应级别;(3)发布事故应急指令;(4)组织事故调查和处理。
2.2 事故应急小组成立堆取料机事故应急小组,负责事故现场处置、人员救援、物资供应等工作。
2.2.1 小组成员(1)现场指挥员:负责现场指挥、协调;(2)救援组:负责人员救援、伤员救治;(3)警戒组:负责现场警戒、交通管制;(4)物资保障组:负责应急物资供应、调配;(5)通讯保障组:负责通讯联络、信息报送。
2.2.2 小组职责(1)现场指挥员:负责现场指挥、协调,确保事故应急工作顺利进行;(2)救援组:负责人员救援、伤员救治,确保伤员得到及时救治;(3)警戒组:负责现场警戒、交通管制,确保事故现场安全;(4)物资保障组:负责应急物资供应、调配,确保应急物资充足;(5)通讯保障组:负责通讯联络、信息报送,确保事故信息畅通。
三、事故应急响应3.1 事故报告发生事故后,现场负责人应立即向事故应急指挥部报告,报告内容包括:事故发生时间、地点、原因、人员伤亡、财产损失等情况。
3.2 事故应急响应级别根据事故情况,事故应急指挥部确定事故应急响应级别,分为四个等级:(1)一级响应:事故造成人员死亡或重伤,财产损失较大;(2)二级响应:事故造成人员轻伤,财产损失一般;(3)三级响应:事故造成轻微财产损失;(4)四级响应:一般事故。
斗轮堆取料机防碰撞保护的研究

SAFETY ∙MONITORING 安全 · 检测堆取料机和取料机之间防碰撞的基本思路是将斗轮堆取料机和取料机投影到堆场水平面上,在水平面上对其投影进行防碰撞分析。
防碰撞模型主要包括相邻轨道梁上的两台设备和同一轨道梁上的两台设备。
设备在轨道梁上的位置,设备的回转角度用光电式绝对值编码器测定,堆取料机的俯仰角度用角度仪通过4~20 mA 的模拟量信号传到大机PLC中,取料机的俯仰角度通过光电式绝对值编码器测定然后传到大机PLC中。
大机PLC再通过工业以太网把行走、回转、俯仰等编码器数值传到中控PLC系统中。
中控与大机之间的通讯用光缆作为传输介质以工业以太网的方式进行通讯。
1 防碰撞数学模型建立1.1 相同轨道梁上两台单机碰撞分析图1为两台大机处于同一条轨道梁时的状况,为保障两台设备不发生碰撞,必须使A大机的尾车H1到B 大机悬臂或配重最近点小于程序设定的最短距离。
设大机悬臂长度L1,尾车部分长度L2,配重部分长度为L3,B大机的俯仰角度为α,以臂架向左平行轨道梁为回转零点,B大机的回转角度为β,两大机的位置差为d。
B大机回转角度的绝对值≤90°时三维算法为d =L2+ L1sin α cos | β | (1)B大机回转角度的绝对值>90°时的三维算法为d =L2+ L3sin α cos(180°-| β | ) (2)1.2 相邻轨道梁上大机碰撞分析相邻轨道梁上两台大机碰撞情况分为A、B两种模式,见图2。
大机的回转角度范围为-120°~120°,以臂架向上平行轨道梁为回转零点。
A模式中C大机臂架最前端和D大机臂架最前端距离不能小于设定值;B 模式中C大机臂架最前端和D大机配重最后端距离不能小于设定值。
图2中的A模式设C大机回转角度大于等于0°,小于等于120°,D大机回转角度大于等于-120°,小于等于0°,设C大机俯仰角度为α1,回转角度为β1;D大机俯仰角度为α2,回转角度为β2,两大机的臂架长度为L1,两大机位置差值为d,算法为d = | L1sin α1 cos β1-L1sin α2 cos β2 | (3)图2中B模式设C大机俯仰角度为α1,回转角度为β1,β1为0°~120°;D大机俯仰角度为α2,回转斗轮堆取料机防碰撞保护的研究杨敏康神华粤电珠海港煤炭码头有限责任公司 珠海 519050摘 要:神华粤电珠海港煤炭码头公司现有8台斗轮堆取料机和2台取料机,由于堆场范围广,斗轮堆取料机和取料机行走距离长,大车行走编码器易出现偏差,同一轨道梁之间以及相邻的轨道梁之间容易发生斗轮堆取料机相撞事故,对司机人身安全和设备稳定运行造成很大的威胁。
XX钢铁集团原料场堆取料机防碰撞技术方案

XX钢铁集团有限公司原料场堆取料机防碰撞及定位检测技术方案目录1.项目概述 (3)2.防碰撞定位控制系统实现功能 (3)2.1绝对位置检测 (4)2.2空间防碰撞 (4)2.3安全联锁控制 (5)2.4防混料检测 (5)2.5动态显示 (5)3.防碰撞控制系统构成 (5)3.1 系统构成 (5)3.2系统信号流程 (6)4.格雷母线技术简介 (7)4.1 格雷母线检测原理 (7)4.2 检测方式 (9)4.3 格雷母线的结构 (10)4.4位置检测特点 (10)5.实现方案 (11)5.1 机车走行位置检测方案 (11)5.2 悬臂旋转位置检测方案 (11)6.基本配置清单 (13)7.项目承担企业简介与成功案例.............................................. 错误!未定义书签。
7.1企业简介...................................................................................... 错误!未定义书签。
XX钢铁集团原料场堆取料机走行及回转位置检测技术方案1.项目概述XX钢铁有限公司拟建设高炉、烧结、球团和燃煤发电厂,需提供原燃料供应系统、成套设备、配套设施提供及相关服务,先期建设综合原料场一步工程,配套有5台大型堆取料机设备,其中贮料场有堆取料机4台、混均堆场有堆料机1台和取料机1台,为实现料场机械自动运行、位置跟踪、安全防碰撞保护系统功能,要求料场同轨道的两台堆取料机必须设置可靠的防碰撞控制系统置,确保关键设备生产安全和实现设备精细化管理,提高原料场运行效益。
原料场与混均料场的堆取料机、双轮取料机是煤场重要作业设备,跨间内有两台及两台以上的大型设备工作时必须设置防碰撞装置,碰撞距离在5~20m可调、设置减速与停止功能与进行声光报警、安全运行,另外布料小车要求实现精确位置对正下料。
2024年堆料机安全技术操作规程
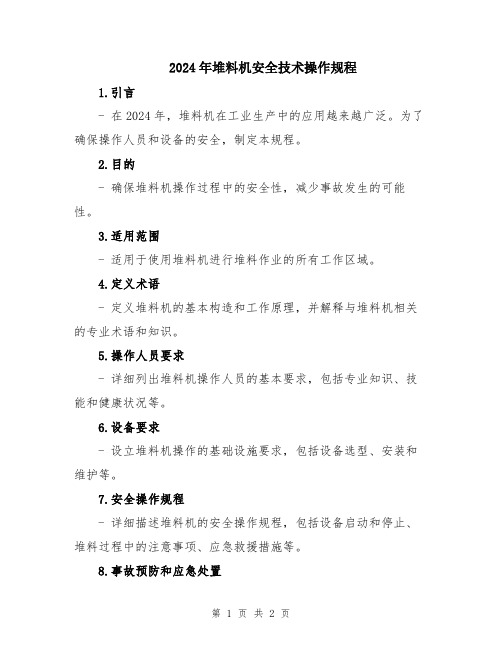
2024年堆料机安全技术操作规程
1.引言
- 在2024年,堆料机在工业生产中的应用越来越广泛。
为了确保操作人员和设备的安全,制定本规程。
2.目的
- 确保堆料机操作过程中的安全性,减少事故发生的可能性。
3.适用范围
- 适用于使用堆料机进行堆料作业的所有工作区域。
4.定义术语
- 定义堆料机的基本构造和工作原理,并解释与堆料机相关的专业术语和知识。
5.操作人员要求
- 详细列出堆料机操作人员的基本要求,包括专业知识、技能和健康状况等。
6.设备要求
- 设立堆料机操作的基础设施要求,包括设备选型、安装和维护等。
7.安全操作规程
- 详细描述堆料机的安全操作规程,包括设备启动和停止、堆料过程中的注意事项、应急救援措施等。
8.事故预防和应急处置
- 提供事故预防和应急处置的指导,包括事故预防措施的制定和应急处置步骤的详细说明。
9.培训和评估
- 说明对堆料机操作人员进行安全培训和定期评估的要求。
10.监测和改进
- 列出对堆料机操作进行监测和改进的措施,包括定期检查和评估的频率和方法。
以上是一个简要的2024年堆料机安全技术操作规程的框架。
您可以根据实际情况进行补充和修改,以确保规程的有效性和适用性。
料场堆取料机的防碰撞控制研究
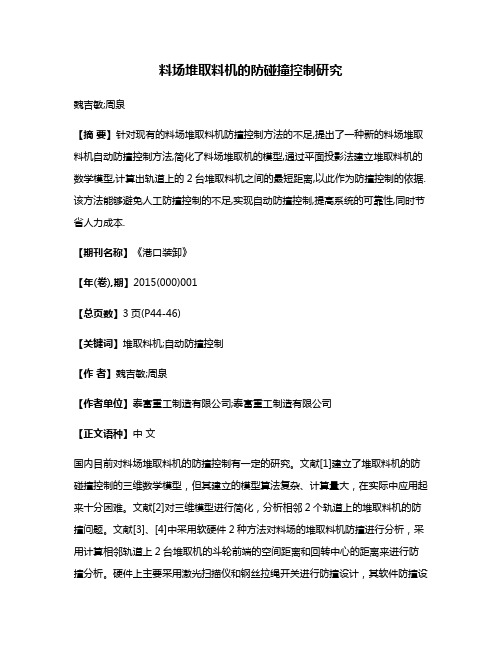
料场堆取料机的防碰撞控制研究魏吉敏;周泉【摘要】针对现有的料场堆取料机防撞控制方法的不足,提出了一种新的料场堆取料机自动防撞控制方法,简化了料场堆取机的模型,通过平面投影法建立堆取料机的数学模型,计算出轨道上的2台堆取料机之间的最短距离,以此作为防撞控制的依据.该方法能够避免人工防撞控制的不足,实现自动防撞控制,提高系统的可靠性,同时节省人力成本.【期刊名称】《港口装卸》【年(卷),期】2015(000)001【总页数】3页(P44-46)【关键词】堆取料机;自动防撞控制【作者】魏吉敏;周泉【作者单位】泰富重工制造有限公司;泰富重工制造有限公司【正文语种】中文国内目前对料场堆取料机的防撞控制有一定的研究。
文献[1]建立了堆取料机的防碰撞控制的三维数学模型,但其建立的模型算法复杂、计算量大,在实际中应用起来十分困难。
文献[2]对三维模型进行简化,分析相邻2个轨道上的堆取料机的防撞问题。
文献[3]、[4]中采用软硬件2种方法对料场的堆取料机防撞进行分析,采用计算相邻轨道上2台堆取机的斗轮前端的空间距离和回转中心的距离来进行防撞分析。
硬件上主要采用激光扫描仪和钢丝拉绳开关进行防撞设计,其软件防撞设计中将2台堆取料机斗轮之间的距离作为2台堆取料机之间的最短距离,而实际中2台堆取料机的最短距离并不是2台堆取料机斗轮与斗轮之间的距离,故该方法存在一定的缺陷。
本文对堆取料机的模型进行简化,将堆取料机投影到料场水平面,在水平面上对堆取料机的投影进行防撞分析。
本文不仅分析了相邻2个轨道上2台堆取料机的防撞,而且还对同一条轨道上相邻的2台堆取料机进行防撞分析。
对堆取料机的数学建模方法主要有三维立体模型法、平面投影法等。
下面以一个简化的料场为例,分析用平面投影法如何推导出斗轮堆取料机防撞问题的数学模型。
简化的料场中总共4条行走轨道,其示意图见图1。
以堆取料机的臂架与轨道重合方向为0度方向。
顺时针旋转的方向为正方向,逆时针旋转的方向为负方向。
悬臂式斗轮取料机臂架防碰料堆系统设计及实现

悬臂式斗轮取料机臂架防碰料堆系统设计及实现摘要:安全生产是我们国家的一项重要政策,也是社会、企业管理的重要内容之一。
秦皇岛港股份有限公司作为重要的煤炭转运枢纽,大型设备众多,危险点复杂,这就需要我们采取有效的安全保护措施,保证设备安全运行。
悬臂式斗轮取料机是秦皇岛港煤炭运输设备中重要的取料设备,其在取料作业时司机通过操控大机臂架反复回转进行扇形取料。
这种作业模式下,由于受料堆垛型和垛距的限制,取料机臂架与料堆是存在碰撞风险的。
为了避免发生此类机损事故,就需要有妥善的臂架防碰系统对臂架进行保护。
本文对悬臂式斗轮取料机臂架防碰料堆系统进行了探索设计,并进行了广泛的使用,实践证明保护效果良好。
关键词:悬臂式;斗轮取料机;臂架防碰料堆系统;悬吊钢丝绳1臂架防碰料堆系统探索设计的必要性取料机臂架碰撞检测系统通常由安装于臂架两侧下沿的防碰拉线绳、拉线绳支架和保护限位开关组成,使用拉线开关作为该保护装置的检测元件。
拉线开关动作范围较小,当臂架将要与煤垛发生接触时,虽然可以立刻检测到碰撞信号,令取料机停止动作,但由于取料机大臂旋转有一定的惯性,碰撞经常造成拉线绳被拉断或拉线绳支架变形。
原有保护形式虽然能够使取料机臂架免于碰撞发生损坏,但却难以“自保”。
防碰装置一旦在作业过程中发生损坏,维修工作会耗费大量的人力、物力和财力。
且修复前的这段时间,取料机臂架是缺乏保护的。
再者,原有保护形式在检测到碰撞时,还需要司机到臂架尾部对拉线开关进行手动复位。
基于以上原因,笔者针对悬臂式斗轮取料机的臂架防碰料堆系统进行了重新设计和改造。
2悬臂式斗轮取料机臂架防碰料堆系统设计2.1原有检测形式原取料机臂架碰撞检测系统主要由负责检测故障的拉线开关以及连接拉线开关的碰撞拉绳和支撑碰撞拉绳的支架三部分组成,通常在生产作业中会出现以下两个问题:(1)在出现臂架碰撞故障之后必需由司机到大臂上手动复位故障才能消除。
(2)碰撞经常造成拉线绳被拉断或拉线绳支架变形导致检测系统无法使用。
- 1、下载文档前请自行甄别文档内容的完整性,平台不提供额外的编辑、内容补充、找答案等附加服务。
- 2、"仅部分预览"的文档,不可在线预览部分如存在完整性等问题,可反馈申请退款(可完整预览的文档不适用该条件!)。
- 3、如文档侵犯您的权益,请联系客服反馈,我们会尽快为您处理(人工客服工作时间:9:00-18:30)。
XX钢铁集团有限公司原料场堆取料机防碰撞及定位检测技术方案目录1.项目概述 (3)2.防碰撞定位控制系统实现功能 (3)2.1绝对位置检测 (4)2.2空间防碰撞 (4)2.3安全联锁控制 (5)2.4防混料检测 (5)2.5动态显示 (5)3.防碰撞控制系统构成 (5)3.1 系统构成 (5)3.2系统信号流程 (6)4.格雷母线技术简介 (7)4.1 格雷母线检测原理 (7)4.2 检测方式 (9)4.3 格雷母线的结构 (10)4.4位置检测特点 (10)5.实现方案 (11)5.1 机车走行位置检测方案 (11)5.2 悬臂旋转位置检测方案 (11)6.基本配置清单 (13)7.项目承担企业简介与成功案例.............................................. 错误!未定义书签。
7.1企业简介...................................................................................... 错误!未定义书签。
XX钢铁集团原料场堆取料机走行及回转位置检测技术方案1.项目概述XX钢铁有限公司拟建设高炉、烧结、球团和燃煤发电厂,需提供原燃料供应系统、成套设备、配套设施提供及相关服务,先期建设综合原料场一步工程,配套有5台大型堆取料机设备,其中贮料场有堆取料机4台、混均堆场有堆料机1台和取料机1台,为实现料场机械自动运行、位置跟踪、安全防碰撞保护系统功能,要求料场同轨道的两台堆取料机必须设置可靠的防碰撞控制系统置,确保关键设备生产安全和实现设备精细化管理,提高原料场运行效益。
原料场与混均料场的堆取料机、双轮取料机是煤场重要作业设备,跨间内有两台及两台以上的大型设备工作时必须设置防碰撞装置,碰撞距离在5~20m可调、设置减速与停止功能与进行声光报警、安全运行,另外布料小车要求实现精确位置对正下料。
为此可采用基于格雷母线绝对定位检测技术,建立一套完整的防碰撞定位控制系统,实现本工程中设备防碰撞与料场设备精细管理。
2.防碰撞定位控制系统实现功能大型堆取料机定位技术是近年来自动化技术发展的一个热点,也是实现原料场的定点堆取、自动化无人操作的核心技术。
近年来定位技术和通信技术发展较快,当前定位技术主要有格雷母线位置检测技术、旋转编码器位置检测技术、定位片编码位置检测技术、条形码位置检测技术等。
在众多的定位技术中,格雷母线位置检测技术最为成熟。
武汉利德测控技术有限公司研发的格雷母线技术为非接触式连续测量,检测精度5mm,是输出信号为绝对值格雷码一种绝对位置定位技术,能与所有工业现场总线的设备实时通信,能实现堆取料机走行位置与回转位置的精确检测,特别适合应用于原料场工况高温、强腐蚀、湿度大环境。
该技术在宝钢、济钢、武钢和首钢等单位工程大量应用表明,该技术定位精度高、设备运行稳定、完全满足均匀定点堆料、混料及生产过程中对移动机车的定位管理要求,有效防止生产混料、防止设备碰撞,是实现生产设备精细化管理的的有效解决方案。
结合山钢集团日照有限公司综合原料场防碰撞定位控制系统要求,格雷母线绝对位置检测定位技术能够很好地满足控制要求,可实现如下控制功能:2.1绝对位置检测走行绝对位置检测:堆取料机和堆料机大车、双轮取料机大车走行绝对位置精确检测,检测精度5毫米。
回转绝对位置检测:回转绝对位置精确检测检测精度5毫米(回转角度±110度)。
料点绝对位置检测:走行绝对位置、回转绝对位置检测,可选结合水平位置检测旋臂端点高度,可计算出堆取料机旋臂在空间的三维位置姿态,实现堆取料点位置的检测。
2.2空间防碰撞基于格雷母线技术建立绝对位置检测防碰撞定位系统,防止前后堆取料、双轮取料机、布料小车相互间碰撞,当前后两台取料机空间位置之间距离20米报警提示,10米控制停机。
2.3安全联锁控制卸料位置联锁作业:如需将原料堆入堆场,必须待堆取料机到达指定位置区域后方能作业。
取原料位置联锁作业:单台取料机取原料作业,取原料作业必须堆取料机及取料点到达指定位置区域方可取料。
2.4防混料检测通过堆取料点空间绝对位置的检测,结合堆场计量系统、电气控制系统,保证堆取料机在指定区域内进行堆料,不与临近的堆料范围相混杂。
2.5动态显示建立绝对位置检测防碰撞定位系统建立后,可在中控室系统实时显示堆取料机及其悬臂的三维位置,建立整个堆场设备防碰撞、生产设备位置定位、安全生产管理监控系统,杜绝事故发生,提高工作效率。
3.防碰撞控制系统构成3.1 系统构成根据总体平面布局,整个堆场共有5台套料场堆取料机设备,如下图1所示。
料场:其中一步料场1#~4#堆取料机(1#、2#同一轨道长665米、3#、4#同一轨道长665米)回转堆取料,混均料场5#堆料机 (轨道650米)回转堆料、6#双轮取料机(轨道650米)取料。
本方案铺设4条格雷母线作为防碰撞控制系统绝对位置检测装置,格雷母线铺设在轨道旁,实时检测每台机车位置,同时每台机车安装回转格雷母线和选配俯仰角度传感器,可测量堆取料点的绝对位置。
图1防碰撞定位系统的布局示意图3.2系统信号流程防碰撞控制系统可以对整个堆场的堆取料机进行统一的管理及监控、数据的记录,中控室对全厂的集控系统采取统一的管理,如下达生产任务,生产报表、相关的数据记录。
它系统上下行信号说明如下:上行信号:每个料场的堆取料机PLC把采集到的堆取料机地址、I/O 信号、悬臂旋转角度、俯仰角度等数据通过无线网桥传送到机车PLC。
机车PLC把堆取料机的位置状态及相关的控制进行处理,通过堆场有线/无线系统传输到中控室上位机,中控室上位机显示各车位置及工作状态,并生成相关的数据报表。
通过悬臂旋转角度、俯仰角度、臂长可以精确测定落料点位置,完成物料位置的检测和控制,保证堆取料机在指定的区域内堆料、取料,不与临近的料堆相混杂。
图2上行信号流程图下行信号:中控上位机发布某车到某堆场堆料、取料、转料和卸料等命令到中控PLC,中控PLC根据任务再把防碰撞禁控或允控命令下传到对应的机车PLC,机车PLC根据命令控制堆取料机走行机构、俯仰机构和回转机构动作,并把位置信息机车显示屏,显示出本车所在的位置、任务等信息。
图3下行信号流程图4.格雷母线技术简介4.1 格雷母线检测原理格雷母线采用电磁感应技术判别格雷母线与天线箱相对位置进行检测,电缆芯线有两种即基准线(R线)和地址线(G0线—G10线)。
各对电缆芯线按不同步长的规律编排,每隔一定长度(步长)交叉一次,设电缆的最小步长为W,则G0、G1、G2…G8、G9、G10步长分别为1W、2W、4W、8W…256W、512W、1024W,基准线R在整个电缆段中不交叉,如6图所示。
步长W要根据定位精度来确定,芯线的数量由电缆长度和定位精度决定。
一般地,定位精度μ=W(其中W为最小电缆环路即最小步长),电缆长度为L=2n-1*μcm,(其中n为电缆地址线的数量),理论上讲,只要将W 取得很小,定位精度就可以做得很高,但在工程上是行不通的,因为根据电磁学的理论,感应电压 e=N*dΦ/dt,Φ=S*B,其中N为线圈的匝数,Φ为磁通量,S为发射线圈或接收线圈的面积,B为电磁强度。
因此当W 取得很小,S就很小,接收到的信号(感应电压)就很小,地址检测系统的信噪比低,地址检测就无法实现或地址不稳定。
根据工程经验,W=200mm 较好。
图4 格雷母线芯线展开示意图如移动机车上安装一个天线箱,一般天线箱距离扁平电缆100±10mm ,天线箱发射的高频信号通过电磁感应被地面的格雷母线接收,R线为平行敷设的一对线,接收到的信号作为基准信号,G0—G9在不同的位置有不同的交叉点,其接收到的信号在经过偶数个交叉后,相位与基准信号相同,在经过奇数个交叉点后,相位与基准信号的相位相反,若规定同相位时地址为“0”,反相位时地址为“1”,则在格雷母线的某一位置得到唯一10位的地址编码,此对应与机车的一个地址。
位置检测单元将地址格雷码转换成十进制的数,即可检测出机车离格雷母线始端的距离,从而得到机车的位置。
4.2 检测方式一般地,格雷母线定位检测分地上检测方式和车上检测方式,两种检测方式格雷母线的结构相同,但应用方式不同。
(1)地上检测方式:地址编码器和天线箱安装在移动站,通过天线箱发射地址信号,地址解码器安装在固定站(地面)上,在固定站完成地址检测。
如图5所示。
图5 地上检测方式框图(2)车上检测方式:地址编码器安装在固定站,通过格雷母线芯线发射地址信号,天线箱、地址解码器安装在移动站上,移动站(车上)直接检测到地址。
如图6所示。
图6 车上检测方式框图选择检测工作方式根据控制系统的需求来考虑决定。
如果控制系统的重心在移动站上,则采用车上检测方式较好;如果控制系统的重心在固定站,则采用地上检测方式较合适。
本项目中堆取料机走行的地址检测采用车上检测方式,回转角度地址检测采用地上检测方式。
4.3 格雷母线的结构格雷母线由电缆芯线、模芯和电缆护套构成,如图7所示。
图7 格雷母线外形图4.4位置检测特点格雷母线防碰撞定位控制系统主要由地址编码器、天线箱、格雷母线以、解码器及辅助电气组成。
格雷母线定位技术有以下特点: 非接触工作方式:非接触工作方式,位置检测精度5毫米,无滑脱和磨损等故障。
⏹绝对位置检测:能够连续地、高精度地检测绝对地址,可以实现移动机车实时绝对地址检测。
检测适应速度≤200m/Min。
⏹抗干扰能力强:使用交叉扭绞结构及相位检测技术,天线箱与格雷母线两者间隙从30毫米到300毫米均可正常工作,不受环境噪音和接收信号电平波动的影响。
⏹不受无委会管制;格雷母线工作频率为低频,所产生的电磁场只限于几米范围内,无需向无管会申请频段即可使用。
⏹可连接各种现场总线通讯接口: RS485/Controlnet /DeviceNet/Ethernet或自定协议。
⏹适用于恶劣的产业环境:安装在室外的格雷母线电缆、天线箱采用非金属材料制作而且采用密封工艺,耐酸、碱腐蚀,能在诸如铁矿石场等恶劣环境条件中长期可靠的工作。
5.实现方案5.1 机车走行位置检测方案通过安装在大车一侧的格雷母线电缆检测大车的走行位置,如图8示。
大车走行的位置即为Y轴的位置。
图8 大车位置检测示意图5.2 悬臂旋转位置检测方案旋转角度检测:通过安装在悬臂回转盘上的格雷母线电缆检测悬臂的旋转角度,格雷母线电缆随悬臂一起转动,天线安装在大车上不动,如图9所示。
格雷母线电缆安装成与回转盘一致的圆形,通过检测格雷母线电缆与天线的位置确定悬臂旋转的角度β。
图9 悬臂旋转角度检测示意图俯仰角度检测:通过安装在悬臂上的角度检测仪检测旋转角度,检测得到悬臂相对水平面俯仰的角度α,如图10所示。