大容量注射剂生产工艺灭菌前微生物污染水平测定验证研究
注射剂无菌保证工艺研究与验证及相关申报资料的原则性要求

(五)再验证(拟进行再验证的时间和内容)
无菌保证工艺研究与验证试验的过程及结果
明确剂型选择的原则 稳定性的考虑、无菌保证水平的高低 评价灭菌工艺的合理性 将F0、SAL引入工艺评价
规范申报资料要求
二、总体考虑
实施中的关注点
涉及的品种广、时间紧
技术难度大,缺少相应的经验
对临床安全有效性可能产生的影响
与药监系统相关部门的共同实施
充分认识现实性,以实践促完善
二、总体考虑
面临的主要问题
剂型选择不合理 无菌保证工艺选择不合理 无菌保证工艺研究不全面 无菌保证工艺缺乏必要的验证
GMP与发达国家要求还存在差距
认知不到位 技术要求不明确 申报资料无相应内容
二、总体考虑
拟着重解决的问题
提高无菌认知的水平
无菌检查的局限性、工艺验证的重要性等
符合注册F0值标准
注意:
同品种不同浓度 — 考察不同浓度对热穿透的影响
不同包装规格 — 进行最大和最小包装规格的试验 不同装载量 — 进行最小和最大装载量的试验 不同灭菌温度 —进行最高温度条件下的试验
微生物挑战试验
证明通过该工艺能杀灭一定污染量和D值的微生物
– 生物指示剂
– 根据D值计算接种量
水平限度标准
• 控制药液存放温度和时间
• 药液取样、污染菌的鉴别
无菌生产工艺-以防止污染为目的,消除后续
导致二次污染的各种可能性
各种容量注射液微生物灭菌验证研究

分割线------------------------------------智能小车平台前言该小车平台采用模块化设计,可根据不同的任务选配合适的传感器及硬件电路进行组装。
本课题主要从四个部分进行了探讨:第一部分为对智能小车平台的系统进行概述和对智能小车平台常用的控制算法进行分析。
第二部分为智能小车平台各个模块的选型及硬件结构的设计和控制算法的具体设计与实现,是课题智能小车平台设计的重点、难点,主要讲述具体硬件的设计第三部分是智能小车平台的软件部分和各种控制算法的实现,如路障检测、路径走向判断、加减速机构、转弯角度控制及目标搜索方式的处理等。
第四部分是我们的课题已经获得的成果及课题组学生收获感想。
分割线-----------------------------------------------大容量注射剂生产工艺灭菌前微生物污染水平测定验证研究大容量注射剂灭菌前微生物污染水平验证大容量注射剂灭菌前微生物污染水平验证,主要验证生产系统来至的污染水平,如配置系统、灌装系统、及相应的在线灭菌系统、瓶子、瓶塞等,由于最终灭菌产品所用的胶塞、玻璃瓶采用当天用合格注射用水洗、当天用的办法,在灌装前不灭菌,只检查瓶内的不溶性微粒合格,清洁过的瓶子,瓶塞仍然存在不同程度的的微生物污染,因此,取样瓶应当使用灭菌瓶,否则,监测的结果超出限度时,将无法判断污染来自生产系统、还是来自内包材(瓶子、瓶塞等),并由此可能延误采取纠正措施的时间。
生产中应当对瓶子、瓶塞的清洁效果进行微生物监控。
大容量注射剂规格xxxxxxxxxxx,批号:20100708、20100709、20100710三批生产药品。
在生产灌装开始、中间及结尾取样检测。
取样:在正常生产过程中,从每批生产灌装开始、中间及结尾各取一瓶灌封好的产品。
取样瓶应在121℃,灭菌15分钟的无菌瓶,并做好标记。
操作方法:先配制5%吐温溶液,用在121℃,灭菌15分钟,在用灭菌后的5%吐温充分润湿0.45μm滤膜,然后定量(250ml:亚叶酸钙40mg与氯化钠2.25g)过滤药液,将此滤膜移至营养琼脂平板上,在30-35℃培养3-7天,计数。
大容量注射剂-工艺验证实施方案

1、概述1.1工艺验证是指为保证某一特定工艺能持续一致地生产出符合预定标准和质量特性的产品并有文件和记录证据的相关活动。
应证明一个生产工艺按规定的工艺参数能持续生产出符合预定用途和注册要求的产品。
1.2本工艺验证为大容量注射剂氯化钠注射液软袋线生产工艺验证。
质量管理部门负责贯彻GMP的要求以确保生产工艺被验证且维护在验证状态。
生产管理部门负责完成工艺验证并且维护生产工艺在验证状态。
氯化钠为无色、透明的立方结晶或白色结晶性粉末;无臭,味咸。
在水中易溶,在乙醇中几乎不溶,本品为氯化钠的等渗灭菌水溶液,用于电解质补充药。
氯化钠注射液软袋线生产过程中涉及的空调净化系统、纯化水和注射用水系统,以及主要设备已分别进行了验证,即此验证是建立在厂房、空气净化、工艺用水及设备已验证并合格基础上,对产品生产过程中的各种工艺参数进行验证并作出评价。
作为大容量注射剂,本品对无菌、无热原、微粒控制及高纯度的质量要求使它的工艺验证成为一个复杂的课题。
作为大容量注射剂,本品对无菌、无热原、微粒控制及高纯度的质量要求使它的工艺验证成为一个复杂的课题。
按照工艺流程和SOP,分工序对氯化钠注射液生产过程的每个操作和技术参数的验证和分析,在验证分析的基础上,,进一步完善和确定生产工艺规程、岗位标准操作规程、关键技术参数, 并对岗位标准操作规程和关键技术参数提出确定或修订意见,确保产品质量的稳定和均一。
2、验证目的与适用范围2.1验证目的:通过对氯化钠注射液软袋线生产工艺的验证,确定氯化钠注射液软袋线生产过成各岗位SOP的合理性,分析影响产品质量的关键因素,纠正偏差,建立生产全过程的运行标准和监控标准,确保产品质量安全有效、稳定均一。
证明在执行《氯化钠注射液软袋线生产工艺规程》的情况下,按规定的工艺参数能持续生产出符合预定用途和注册要求的产品。
产品质量可控,工艺稳定。
2.2适用范围:本验证方案适用于氯化钠注射液软袋线生产工艺验证。
3、验证方案验证方案规定了生产条件、控制、检测及预期结果的书面方案,对于工艺验证是必不可少的,需在验证前批准3.1验证部门及职责3.1.1验证领导小组3.1.1.1组成成员:组长、副组长、成员。
大容量注射剂工艺验证方案范文

大容量注射剂工艺验证方案范文1.1工艺验证是指为保证某一特定工艺能持续一致地生产出符合预定标准和质量特性的产品并有文件和记录证据的相关活动。
应证明一个生产工艺按规定的工艺参数能持续生产出符合预定用途和注册要求的产品。
1.2本工艺验证为大容量注射剂氯化钠注射液软袋线生产工艺验证。
质量管理部门负责贯彻GMP的要求以确保生产工艺被验证且维护在验证状态。
生产管理部门负责完成工艺验证并且维护生产工艺在验证状态。
氯化钠为无色、透明的立方结晶或白色结晶性粉末;无臭,味咸。
在水中易溶,在乙醇中几乎不溶,本品为氯化钠的等渗灭菌水溶液,用于电解质补充药。
氯化钠注射液软袋线生产过程中涉及的空调净化系统、纯化水和注射用水系统,以及主要设备已分别进行了验证,即此验证是建立在厂房、空气净化、工艺用水及设备已验证并合格基础上,对产品生产过程中的各种工艺参数进行验证并作出评价。
作为大容量注射剂,本品对无菌、无热原、微粒控制及高纯度的质量要求使它的工艺验证成为一个复杂的课题。
作为大容量注射剂,本品对无菌、无热原、微粒控制及高纯度的质量要求使它的工艺验证成为一个复杂的课题。
按照工艺流程和SOP,分工序对氯化钠注射液生产过程的每个操作和技术参数的验证和分析,在验证分析的基础上,,进一步完善和确定生产工艺规程、岗位标准操作规程、关键技术参数,并对岗位标准操作规程和关键技术参数提出确定或修订意见,确保产品质量的稳定和均一。
2、验证目的与适用范围2.1验证目的:通过对氯化钠注射液软袋线生产工艺的验证,确定氯化钠注射液软袋线生产过成各岗位SOP的合理性,分析影响产品质量的关键因素,纠正偏差,建立生产全过程的运行标准和监控标准,确保产品质量安全有效、稳定均一。
证明在执行《氯化钠注射液软袋线生产工艺规程》的情况下,按规定的工艺参数能持续生产出符合预定用途和注册要求的产品。
产品质量可控,工艺稳定。
2.2适用范围:本验证方案适用于氯化钠注射液软袋线生产工艺验证。
注射剂无菌保证工艺及常见验证问题

1、按照欧盟决策树的要求,不能达到121℃,15分钟灭菌,可选择F0≥8的残存概率法。
请问,若产品能达到121℃,12分钟灭菌,是否就不能选择121℃,10分钟,同样,能达到10分钟,就不能选择8分钟,都是F0≥8的情况。
答:从微生物杀灭的数学模型可知,在初始污染相同的情况下,灭菌F0值越大,无菌保证水平越高。
因此,显然为降低产品残留微生物的风险,尽量选择高的F0值是顺理成章的。
2、在产品质量稳定的条件下,均能满足121℃,8分钟和115℃,30分钟,哪个条件应该优先选择呢?答:不考虑产品理化质量稳定性,理论上这两种条件达到的F0值几乎相等,无所谓优选哪个。
但实际生产中,还要考虑灭菌器内产品中热穿透的情况,灭菌器内不同部位的产品实际获得的F0值的差异,不同灭菌批次间产品的F0的差异等。
应该选择热分布差异小,产品F0值差异较小的灭菌工艺。
2℃,灭菌30分钟”,这种表示法是否规范?±3、申报资料中的灭菌条件为“101℃40min。
⨯15min或116℃⨯2℃,灭菌30分钟”几乎不能计算F0值。
灭菌条件的表示可以参照中国药典2005年版二部附录168灭菌法,121℃±2℃,灭菌30分钟”本身不能称为终端灭菌,因“101℃±2℃,灭菌30分钟”是否规范,“101℃±答:暂不说灭菌条件为“101℃4、同品种10ml、20ml注射剂,采取相同的灭菌方式是否合适?答:同品种10ml、20ml注射剂,可以采取相同的灭菌方式,但应进行热穿透试验,考察不同体积样品的热穿透是否有一致,同时考虑采用的灭菌方式应能保证大体积产品的无菌保证水平。
5、选择最高无菌保证水平的灭菌工艺,可能会与产品的质量,如有关物质、稳定性等方面有冲突,如何平衡这一矛盾?另外,国外上市的是粉针剂,国内申报时是否还需要进行灭菌工艺的选择研究?答:实际上,在进行灭菌工艺选择研究过程中就应该进行不同灭菌条件下样品质量变化的研究,选择灭菌工艺的过程也是平衡无菌保证水平和(样品质量)理化指标的过程,在产品有临床需求的情况下,灭菌工艺的选择应以其自身能达到的最高无菌保证水平为原则。
化学药品注射剂灭菌和灭菌工艺研究及验证指导原则

化学药品注射剂灭菌和灭菌工艺研究及验证指导原则灭菌工艺的研究与验证是确保注射剂灭菌的有效性和稳定性的关键。
下文将介绍化学药品注射剂灭菌和灭菌工艺的研究及验证指导原则。
一、灭菌方法硫酸化法是一种常见的化学药品注射剂灭菌方法,其原理是在一定的温度和时间条件下,通过硫酸的浓度和反应时间达到灭菌的目的。
硫酸化法的灭菌效果通常良好,且内部流体与过量气体都可以通过使用缓冲盐来被中和。
另一种常用的方法是辐照灭菌,其原理是利用辐射对微生物进行杀灭。
辐照灭菌要求灭菌剂的材料必须与放射物隔离,且需要进行辐射剂量的检测。
二、灭菌工艺的研究1. 灭菌剂选择灭菌剂的选择应该考虑以下因素:(1)药品的特殊性质,例如特殊化学成分、PH值、温度等。
(2)灭菌剂的生物学效应。
(3)灭菌剂的可靠性和性能。
2. 灭菌参数灭菌参数是指灭菌的具体操作条件。
在制定灭菌参数时研究人员应该考虑到一些因素,如:(1)温度。
温度是影响灭菌的主要因素之一。
一般下,灭菌温度降低时,灭菌时间会相应地延长。
(2)压力。
在高温、水蒸气和其他灭菌方法中,压力是保证灭菌效果的重要条件。
一般来说,在不同的药品生产领域中,压力的极限值是不一样的,需要根据不同药品在实践中的表现进行确定。
(3)通气量。
通气量是否合适直接关系到产品中菌落的灭亡情况。
三、灭菌工艺验证灭菌工艺的验证是指通过实验方法验证所制定的灭菌工艺是否能够达到有效的灭菌效果。
灭菌工艺验证应该包括以下步骤:1. 工艺确认工艺确认是指通过实验测试验证所制定的工艺是否能达到预期的灭菌效果,并且符合要求的工艺参数。
工艺确认还包括对制定工艺的初步调试,对灭菌剂的选择及其对生产环境的适应性的验证。
2. 确定最小灭菌剂量最小灭菌剂量是指在给定的灭菌条件下,使无菌品转化为有菌品所需的最小灭菌剂量。
灭菌剂量的确定可以通过针对特定灭菌剂,在不同条件下的生物指标进行实验来完成。
3. 灭菌验证灭菌验证是指在已确立的灭菌工艺参数下,通过实验测试验证所生产出的产品是否能够满足灭菌要求,从而评估具体灭菌方法的效果和稳定性。
注射剂无菌保证工艺研究、残氧检测与验证常见技术70问
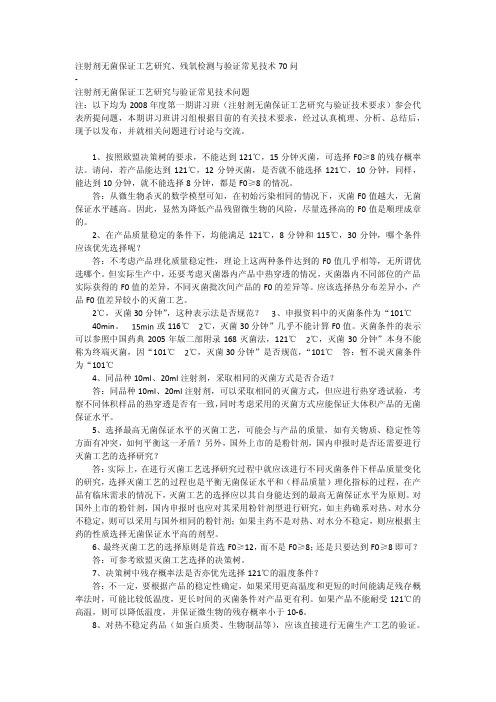
注射剂无菌保证工艺研究、残氧检测与验证常见技术70问-注射剂无菌保证工艺研究与验证常见技术问题注:以下均为2008年度第一期讲习班(注射剂无菌保证工艺研究与验证技术要求)参会代表所提问题,本期讲习班讲习组根据目前的有关技术要求,经过认真梳理、分析、总结后,现予以发布,并就相关问题进行讨论与交流。
1、按照欧盟决策树的要求,不能达到121℃,15分钟灭菌,可选择F0≥8的残存概率法。
请问,若产品能达到121℃,12分钟灭菌,是否就不能选择121℃,10分钟,同样,能达到10分钟,就不能选择8分钟,都是F0≥8的情况。
答:从微生物杀灭的数学模型可知,在初始污染相同的情况下,灭菌F0值越大,无菌保证水平越高。
因此,显然为降低产品残留微生物的风险,尽量选择高的F0值是顺理成章的。
2、在产品质量稳定的条件下,均能满足121℃,8分钟和115℃,30分钟,哪个条件应该优先选择呢?答:不考虑产品理化质量稳定性,理论上这两种条件达到的F0值几乎相等,无所谓优选哪个。
但实际生产中,还要考虑灭菌器内产品中热穿透的情况,灭菌器内不同部位的产品实际获得的F0值的差异,不同灭菌批次间产品的F0的差异等。
应该选择热分布差异小,产品F0值差异较小的灭菌工艺。
2℃,灭菌30分钟”,这种表示法是否规范?、申报资料中的灭菌条件为“101℃40min。
或116℃℃,灭菌30分钟”几乎不能计算F0值。
灭菌条件的表示可以参照中国药典2005年版二部附录168灭菌法,121℃℃,灭菌30分钟”本身不能称为终端灭菌,因“101℃℃,灭菌30分钟”是否规范,“101℃答:暂不说灭菌条件为“101℃4、同品种10ml、20ml注射剂,采取相同的灭菌方式是否合适?答:同品种10ml、20ml注射剂,可以采取相同的灭菌方式,但应进行热穿透试验,考察不同体积样品的热穿透是否有一致,同时考虑采用的灭菌方式应能保证大体积产品的无菌保证水平。
5、选择最高无菌保证水平的灭菌工艺,可能会与产品的质量,如有关物质、稳定性等方面有冲突,如何平衡这一矛盾?另外,国外上市的是粉针剂,国内申报时是否还需要进行灭菌工艺的选择研究?答:实际上,在进行灭菌工艺选择研究过程中就应该进行不同灭菌条件下样品质量变化的研究,选择灭菌工艺的过程也是平衡无菌保证水平和(样品质量)理化指标的过程,在产品有临床需求的情况下,灭菌工艺的选择应以其自身能达到的最高无菌保证水平为原则。
对大容量注射剂采用残存杀灭法进行终端灭菌工艺验证的应用

对大容量注射剂采用残存杀灭法进行终端灭菌工艺验证的应用邹伟(苏州大学,江苏苏州215000;贝朗医疗(苏州)有限公司,江苏苏州215000)引?j j。
|j’|‘。
“”j,。
睛要】本文概述了如何对使用残存杀灭法进行灭菌的大容量注射荆进行验证。
j睽蛊悯】灭菌;灭茵验证;应用评价无菌保证工艺是否有效曾一度主要通过对最终产品抽样进行无菌检验来判断:由于微生物在产品中的分布是不均匀的,且抽检样品的数量有限,故抽检的结果不能真实代表整批产品的无菌状态。
国际上更为注重无菌保证工艺的设计是否合理、所用的设备与工艺是否经过充分的验证,在此基础上,切实按照验证后的工艺进行生产,这样才能保证灭菌(无菌)工艺的可靠性。
因此,基于此要求,本文就着重针对灭菌工艺中灭菌温度小于115℃,8。
<F0<12的残存杀灭法的最终灭菌,讨论如何进行更为有效,低成本和科学性的验证。
1验证设计1.1产品特性及验汪目的验证琥珀酰明胶注射液的灭菌工艺能够满足设计要求。
琥珀酰明胶注射液是一种代血浆,其特点是密度和粘度较大,其热穿透性能较弱。
12验证方案灭菌验证包括四个部分:灭菌设备的空载热分布,装载热分布(包括满载和最小装载),产品装载下的热穿透及微生物挑战试验。
其中,产品装载下的热穿透及微生物挑战试验是验证的关键部分,该部分使用待注册产品一琥珀酰明胶注射液重复进行3次。
121灭菌前微生物污染水平测定需定期对环境中的微生物进行监控,从而对环境微生物的耐热情况进行监控。
在灭菌前,需对生产的产品确定微生物限度的标准,并进行移姓物限度分析,以确定符合该限度值。
同时,应检测产品中是否含有面j繁漕。
本公司灭菌前的2姓物限度为小于1O ocf u/m I。
122空载热分布使用15个K a ye探头进行灭菌柜的空载热分布。
1)满载热分布使用30个精度为02℃的K eya探头分别插入30个装满直立式输液袋产品中,放置可能出现温度最冷点和F O值最低点的地方。
- 1、下载文档前请自行甄别文档内容的完整性,平台不提供额外的编辑、内容补充、找答案等附加服务。
- 2、"仅部分预览"的文档,不可在线预览部分如存在完整性等问题,可反馈申请退款(可完整预览的文档不适用该条件!)。
- 3、如文档侵犯您的权益,请联系客服反馈,我们会尽快为您处理(人工客服工作时间:9:00-18:30)。
大容量注射剂生产工艺灭菌前微生物污染水平测定验证研究大容量注射剂灭菌前微生物污染水平验证
大容量注射剂灭菌前微生物污染水平验证,主要验证生产系统来至的污染水平,如配置系统、灌装系统、及相应的在线灭菌系统、瓶子、瓶塞等,由于最终灭菌产品所用的胶塞、玻璃瓶采用当天用合格注射用水洗、当天用的办法,在灌装前不灭菌,只检查瓶内的不溶性微粒合格,清洁过的瓶子,瓶塞仍然存在不同程度的的微生物污染,因此,取样瓶应当使用灭菌瓶,否则,监测的结果超出限度时,将无法判断污染来自生产系统、还是来自内包材(瓶子、瓶塞等),并由此可能延误采取纠正措施的时间。
生产中应当对瓶子、瓶塞的清洁效果进行微生物监控。
我们选择了大容量注射剂规格xxxxxxxxxxx,批号:20100708、20100709、20100710三批生产药品。
在生产灌装开始、中间及结尾取样检测。
取样:
在正常生产过程中,从每批生产灌装开始、中间及结尾各取一瓶灌封好的产品。
取样瓶应在121℃,灭菌15分钟的无菌瓶,并做好标记。
操作方法:
先配制5%吐温溶液,用在121℃,灭菌15分钟,在用灭菌后的5%吐温充分润湿0.45μm滤膜,然后定量(250ml:亚叶酸钙40mg与氯化钠2.25g)过滤药液,将此滤膜移至营养琼脂平板上,在30-35℃
培养3-7天,计数。
培养基:营养琼脂培养基
试验方法:薄膜过滤法
生产工艺灭菌前微生物污染水平控制标准:每100ml药液中污染菌不的超过100cfu。
标准依据参照欧洲。
对灭菌前微生物污染水平测定,结果如下:
表一:大容量注射剂灭菌前微生物污染水平测定情况
大容量注射剂灭菌前微生物污染水平验证评价,经对大容量注射剂,三批产品灭菌前微生物污染水平测试,结果均符合标准规定。