飞机装配自动钻孔技术
面向飞机装配自动制孔系统研究现状分析

产品与技术面向飞机装配自动制孔系统研究现状分析成都航空职业技术学院机电工程学院 唐 越 郑金辉 张 冒飞机结构件机械连接主要采用机械连接方式,机械连接处质量对整个飞机的使用寿命有重要影响。
面向飞机装配的自动制孔系统应用于航空制造工程中的飞机数字化装配中,可以极大提高装配质量和效率。
对国外EI公司和宝捷公司,以及国内北航、南航、成飞、沈飞和上海交大等高校和科研院所制造的典型制孔系统的特点进行介绍,对制孔系统关键技术和发展趋势进行简要介绍,为自动制孔系统的研究提供参考。
飞机结构件的连接是飞机装配中重要的一环,目前主要以机械连接为主,最常用的形式为铆钉连接和螺纹连接。
飞机上有多达数百万连接处,而75%~80%的机体疲劳破坏发生在机身连接处,可见连接质量对飞机整体质量影响之大。
飞机零部件具有大尺寸、高精度、形状复杂等特点,传统飞机装配中的制孔以手工制孔为主,受到人工作业水平的限制,制孔精度差、效率低,难以满足飞机装配质量和效率要求。
以工业机器人技术为基础,加装制孔末端执行器,配合高精度在线检测设备组成的自动制孔系统越来越多地应用到飞机装配中。
制孔系统不仅工作空间大,操作灵活,制孔精度高,且大大提高了装配效率,降低了人工操作强度,是今后飞机装配的发展方向之一。
1.面向飞机装配的自动制孔系统研究现状近年来,航空制造业竞争愈演愈烈,尤其是在大飞机的制造装配行业中。
以波音、空客为代表的航空制造企业越来越多地将自动化和数字化技术应用到了飞机制造和装配中,进一步提高了产品质量,降低了生产成本,缩短了制造装配时间,国外飞机装配已基本实现自动化和数字化。
对传统飞机装配生产线进行改造,增强国家制造业核心竞争力,自动制孔系统有较大的研究价值和良好的应用前景。
(1)国外研究现状早在2001年,美国EI公司与空客公司联合设计了一套工业机器人制孔系统ONCE(one-sided end effector),该系统主要应用于波音公司超级大黄蜂机翼后缘襟翼的钻孔及锪窝工作,如图1所示,该系统可加工直径范围3.73~9.525mm,孔位精度±1.5mm,锪孔深度精度可达0.0635mm,空间绝对定位精度±0.508mm,制孔精度可以达到H8。
飞机装配中自动制孔技术的应用与研究
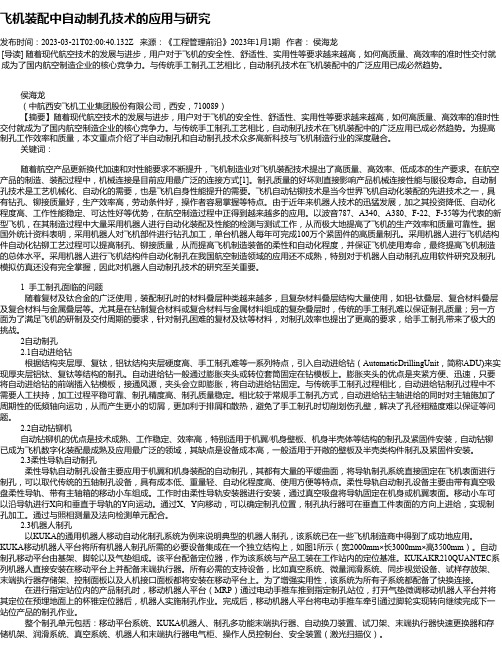
飞机装配中自动制孔技术的应用与研究发布时间:2023-03-21T02:00:40.132Z 来源:《工程管理前沿》2023年1月1期作者:侯海龙[导读] 随着现代航空技术的发展与进步,用户对于飞机的安全性、舒适性、实用性等要求越来越高,如何高质量、高效率的准时性交付就成为了国内航空制造企业的核心竞争力。
与传统手工制孔工艺相比,自动制孔技术在飞机装配中的广泛应用已成必然趋势。
侯海龙(中航西安飞机工业集团股份有限公司,西安,710089)【摘要】随着现代航空技术的发展与进步,用户对于飞机的安全性、舒适性、实用性等要求越来越高,如何高质量、高效率的准时性交付就成为了国内航空制造企业的核心竞争力。
与传统手工制孔工艺相比,自动制孔技术在飞机装配中的广泛应用已成必然趋势。
为提高制孔工作效率和质量,本文重点介绍了半自动制孔和自动制孔技术众多高新科技与飞机制造行业的深度融合。
关键词:随着航空产品更新换代加速和对性能要求不断提升,飞机制造业对飞机装配技术提出了高质量、高效率、低成本的生产要求。
在航空产品的制造、装配过程中,机械连接是目前应用最广泛的连接方式[1]。
制孔质量的好坏则直接影响产品机械连接性能与服役寿命。
自动制孔技术是工艺机械化、自动化的需要,也是飞机自身性能提升的需要。
飞机自动钻铆技术是当今世界飞机自动化装配的先进技术之一,具有钻孔、铆接质量好,生产效率高,劳动条件好,操作者容易掌握等特点。
由于近年来机器人技术的迅猛发展,加之其投资降低、自动化程度高、工作性能稳定、可达性好等优势,在航空制造过程中正得到越来越多的应用。
以波音787、A340、A380、F-22、F-35等为代表的新型飞机,在其制造过程中大量采用机器人进行自动化装配及性能的检测与测试工作,从而极大地提高了飞机的生产效率和质量可靠性。
据国外统计资料表明,采用机器人对飞机部件进行钻孔加工,单台机器人每年可完成100万个紧固件的高质量制孔。
飞机装配制孔技术的研究与展望
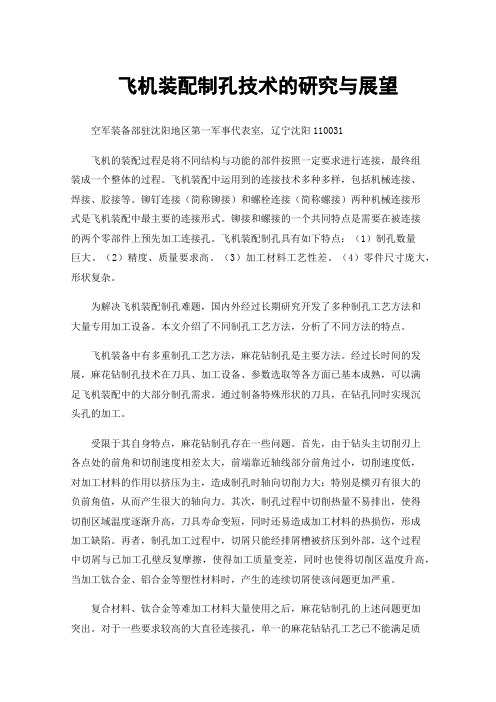
飞机装配制孔技术的研究与展望空军装备部驻沈阳地区第一军事代表室, 辽宁沈阳110031飞机的装配过程是将不同结构与功能的部件按照一定要求进行连接,最终组装成一个整体的过程。
飞机装配中运用到的连接技术多种多样,包括机械连接、焊接、胶接等。
铆钉连接(简称铆接)和螺栓连接(简称螺接)两种机械连接形式是飞机装配中最主要的连接形式。
铆接和螺接的一个共同特点是需要在被连接的两个零部件上预先加工连接孔。
飞机装配制孔具有如下特点:(1)制孔数量巨大。
(2)精度、质量要求高。
(3)加工材料工艺性差。
(4)零件尺寸庞大,形状复杂。
为解决飞机装配制孔难题,国内外经过长期研究开发了多种制孔工艺方法和大量专用加工设备。
本文介绍了不同制孔工艺方法,分析了不同方法的特点。
飞机装备中有多重制孔工艺方法,麻花钻制孔是主要方法。
经过长时间的发展,麻花钻制孔技术在刀具、加工设备、参数选取等各方面已基本成熟,可以满足飞机装配中的大部分制孔需求。
通过制备特殊形状的刀具,在钻孔同时实现沉头孔的加工。
受限于其自身特点,麻花钻制孔存在一些问题。
首先,由于钻头主切削刃上各点处的前角和切削速度相差太大,前端靠近轴线部分前角过小,切削速度低,对加工材料的作用以挤压为主,造成制孔时轴向切削力大;特别是横刃有很大的负前角值,从而产生很大的轴向力。
其次,制孔过程中切削热量不易排出,使得切削区域温度逐渐升高,刀具寿命变短,同时还易造成加工材料的热损伤,形成加工缺陷。
再者,制孔加工过程中,切屑只能经排屑槽被挤压到外部,这个过程中切屑与已加工孔壁反复摩擦,使得加工质量变差,同时也使得切削区温度升高,当加工钛合金、铝合金等塑性材料时,产生的连续切屑使该问题更加严重。
复合材料、钛合金等难加工材料大量使用之后,麻花钻制孔的上述问题更加突出。
对于一些要求较高的大直径连接孔,单一的麻花钻钻孔工艺已不能满足质量与精度要求,生产中需要采用“钻—扩—铰”的多工序方案,某些制孔加工中甚至需要多达十几道工序,生产效率低,生产成本也随之增加。
飞机制造中的装配连接技术
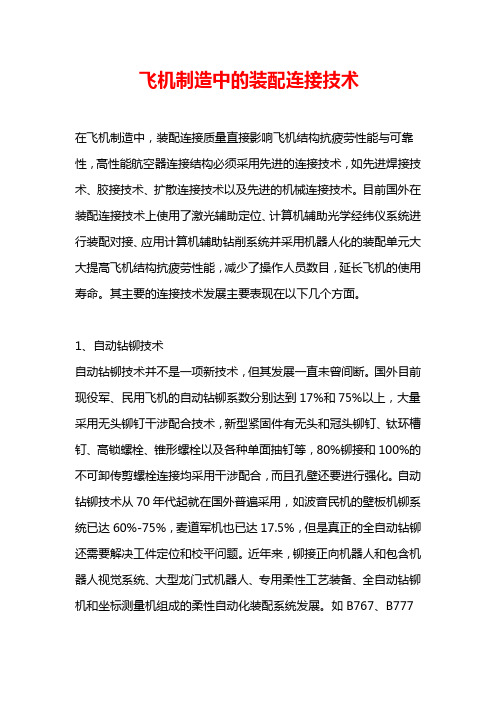
飞机制造中的装配连接技术在飞机制造中,装配连接质量直接影响飞机结构抗疲劳性能与可靠性,高性能航空器连接结构必须采用先进的连接技术,如先进焊接技术、胶接技术、扩散连接技术以及先进的机械连接技术。
目前国外在装配连接技术上使用了激光辅助定位、计算机辅助光学经纬仪系统进行装配对接、应用计算机辅助钻削系统并采用机器人化的装配单元大大提高飞机结构抗疲劳性能,减少了操作人员数目,延长飞机的使用寿命。
其主要的连接技术发展主要表现在以下几个方面。
1、自动钻铆技术自动钻铆技术并不是一项新技术,但其发展一直未曾间断。
国外目前现役军、民用飞机的自动钻铆系数分别达到17%和75%以上,大量采用无头铆钉干涉配合技术,新型紧固件有无头和冠头铆钉、钛环槽钉、高锁螺栓、锥形螺栓以及各种单面抽钉等,80%铆接和100%的不可卸传剪螺栓连接均采用干涉配合,而且孔壁还要进行强化。
自动钻铆技术从70年代起就在国外普遍采用,如波音民机的壁板机铆系统已达60%-75%,麦道军机也已达17.5%,但是真正的全自动钻铆还需要解决工件定位和校平问题。
近年来,铆接正向机器人和包含机器人视觉系统、大型龙门式机器人、专用柔性工艺装备、全自动钻铆机和坐标测量机组成的柔性自动化装配系统发展。
如B767、B777采用了翼梁自动装配系统,提高效率14倍,费用降低90%,废品率降低50%。
而且由于进一步的改进使钻铆工具能够到达以前难以达到的部位。
如通过采用特制的紧固件,只在部件的单边需要工具,与通常的C型机在部件两边进行连接有所不同,克服了工具难以到达部位所产生的问题。
另外,军用飞机和民用飞机在自动连接方面有所不同,民用飞机由于部件大、紧固件种类少较易实现自动化,而军用飞机由于部件尺寸小且复杂、紧固件种类多而较难实现自动化装配,如麦道军用飞机公司的紧固件自动化装配程度只有大约17.5%,他们的努力的目标是达到20%。
以F-18为例,把一纵梁连接到四分之一板上需要三种铆钉,每一种铆钉都需要重新安装工具,这样在安装工具上要花费很多时间,而且大多数自动化装配设备都是固定在车间内的,不仅大且不具备柔性,鉴于这种原因,促进了手动钻孔、手动铆接机等工具的使用范围。
飞机装配自动进给钻应用及精度控制
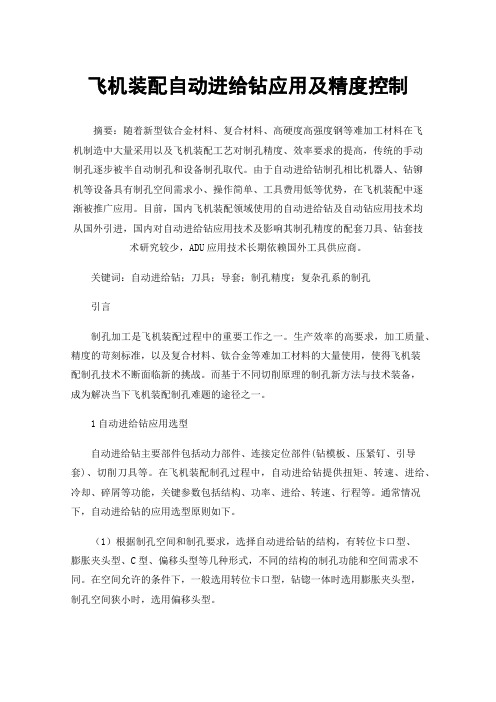
飞机装配自动进给钻应用及精度控制摘要:随着新型钛合金材料、复合材料、高硬度高强度钢等难加工材料在飞机制造中大量采用以及飞机装配工艺对制孔精度、效率要求的提高,传统的手动制孔逐步被半自动制孔和设备制孔取代。
由于自动进给钻制孔相比机器人、钻铆机等设备具有制孔空间需求小、操作简单、工具费用低等优势,在飞机装配中逐渐被推广应用。
目前,国内飞机装配领域使用的自动进给钻及自动钻应用技术均从国外引进,国内对自动进给钻应用技术及影响其制孔精度的配套刀具、钻套技术研究较少,ADU应用技术长期依赖国外工具供应商。
关键词:自动进给钻;刀具;导套;制孔精度;复杂孔系的制孔引言制孔加工是飞机装配过程中的重要工作之一。
生产效率的高要求,加工质量、精度的苛刻标准,以及复合材料、钛合金等难加工材料的大量使用,使得飞机装配制孔技术不断面临新的挑战。
而基于不同切削原理的制孔新方法与技术装备,成为解决当下飞机装配制孔难题的途径之一。
1自动进给钻应用选型自动进给钻主要部件包括动力部件、连接定位部件(钻模板、压紧钉、引导套)、切削刀具等。
在飞机装配制孔过程中,自动进给钻提供扭矩、转速、进给、冷却、碎屑等功能,关键参数包括结构、功率、进给、转速、行程等。
通常情况下,自动进给钻的应用选型原则如下。
(1)根据制孔空间和制孔要求,选择自动进给钻的结构,有转位卡口型、膨胀夹头型、C型、偏移头型等几种形式,不同的结构的制孔功能和空间需求不同。
在空间允许的条件下,一般选用转位卡口型,钻锪一体时选用膨胀夹头型,制孔空间狭小时,选用偏移头型。
(2)根据被加工材料及孔径大小确定自动进给钻的转速、进给。
在多种叠层材料制孔时,自动进给钻参数选用采用“就难”原则(如钛合金和铝合金叠层制孔,转速、进给以钛合金加工参数为准)。
(3)自动进给钻功率与制孔孔径大小、材料加工难易程度相关,通常选用涡轮马达且主轴输出功率大于1.3kW。
(4)根据材料厚度、钻模厚度、排屑空间、钻套系列及刀具结构,确定自动进给钻的加工行程。
看了国外的飞机自动钻铆技术,才知道什么是差距!

看了国外的飞机自动钻铆技术,才知道什么是差距!飞机壁板的连接质量对飞机的气动外形及其疲劳寿命有至关重要的影响,铆接作为一种传统的机械连接技术,由于其连接可靠、质量轻、成本低等特点被广泛用于航空航天领域,因此铆接质量对飞机的安全性能有重要的影响。
采用自动钻铆技术实现飞机壁板的制孔和铆接是提高飞机装配质量与效率的有效途径。
资料显示,手工钻铆效率平均为15s/ 钉,自动钻铆效率最快能达到3s/ 钉,效率提高5 倍;手工铆接镦头高度公差为±0.5mm,自动钻铆所形成镦头高度公差能达到±0.05mm,精度提高10倍。
自动钻铆设备按结构形式可分为龙门式自动钻铆系统、C 型架式自动钻铆系统以及机器人自动钻铆系统。
前两种设备刚性好,精度高,提供的铆接力大,可用于开敞性好的大型结构件的自动钻铆;机器人自动钻铆系统成本低,运动灵活,空间利用率高,可达性高,适用于开敞性差的壁板的自动钻铆装配。
自动钻铆设备按铆接驱动方式又可分为气动锤铆、伺服压铆和电磁铆接。
气动锤铆结构简单,体积小,铆接力小,易于集成,与工业机器人构成机器人自动钻铆系统已成为发展趋势。
伺服压铆采用伺服电机驱动,行星滚珠丝杠传动,可实现高精度、大负载的伺服压铆,较传统的气动铆接具备更高的控制精度与柔性化的速度调节能力,能够按照设定的位移曲线或力曲线进行加载,目前已成功取代液压铆接广泛运用在飞机装配中。
电磁铆接是在电磁成形工艺的基础上发展起来的一种新型铆接工艺,能够实现钛合金和复合材料的连接,以及大直径和难成形材料铆钉成形。
国外自动钻铆技术研究应用现状自动钻铆技术起源于20 世纪50 年代,经过几十年的发展,已成为能够自动完成定位、制孔、送钉、铆接及检测功能的先进制造技术。
国外自动钻铆设备主要供应商以美国捷姆科(GEMCOR)、EI (Electroimpact)、德国宝捷(BROETJE)、意大利B&C (BISUACH & CARRU)为代表,各公司的典型产品型号及其应用情况如表1 所示。
飞机装配制孔装备的探究与分析
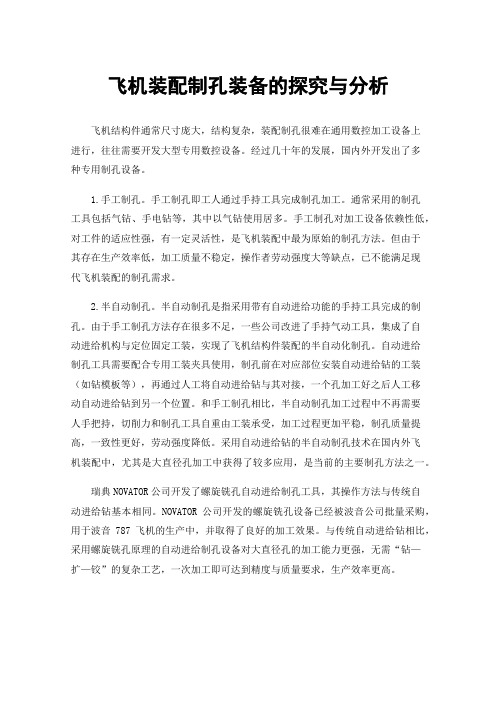
飞机装配制孔装备的探究与分析飞机结构件通常尺寸庞大,结构复杂,装配制孔很难在通用数控加工设备上进行,往往需要开发大型专用数控设备。
经过几十年的发展,国内外开发出了多种专用制孔设备。
1.手工制孔。
手工制孔即工人通过手持工具完成制孔加工。
通常采用的制孔工具包括气钻、手电钻等,其中以气钻使用居多。
手工制孔对加工设备依赖性低,对工件的适应性强,有一定灵活性,是飞机装配中最为原始的制孔方法。
但由于其存在生产效率低,加工质量不稳定,操作者劳动强度大等缺点,已不能满足现代飞机装配的制孔需求。
2.半自动制孔。
半自动制孔是指采用带有自动进给功能的手持工具完成的制孔。
由于手工制孔方法存在很多不足,一些公司改进了手持气动工具,集成了自动进给机构与定位固定工装,实现了飞机结构件装配的半自动化制孔。
自动进给制孔工具需要配合专用工装夹具使用,制孔前在对应部位安装自动进给钻的工装(如钻模板等),再通过人工将自动进给钻与其对接,一个孔加工好之后人工移动自动进给钻到另一个位置。
和手工制孔相比,半自动制孔加工过程中不再需要人手把持,切削力和制孔工具自重由工装承受,加工过程更加平稳,制孔质量提高,一致性更好,劳动强度降低。
采用自动进给钻的半自动制孔技术在国内外飞机装配中,尤其是大直径孔加工中获得了较多应用,是当前的主要制孔方法之一。
瑞典NOVATOR公司开发了螺旋铣孔自动进给制孔工具,其操作方法与传统自动进给钻基本相同。
NOVATOR公司开发的螺旋铣孔设备已经被波音公司批量采购,用于波音787飞机的生产中,并取得了良好的加工效果。
与传统自动进给钻相比,采用螺旋铣孔原理的自动进给制孔设备对大直径孔的加工能力更强,无需“钻—扩—铰”的复杂工艺,一次加工即可达到精度与质量要求,生产效率更高。
半自动制孔方式自动化程度低限制了生产效率;但由于这种制孔装置相对简单、成本低、技术成熟,在今后相当长的时间内仍将是飞机装配中有推广应用价值的重要制孔方法。
飞机装配自动进给钻应用及精度控制

飞机装配自动进给钻应用及精度控制摘要基于国内飞机装配自动进给钻的技术发展还不完善的情况,需要对其的技术应用及精度进行控制,以便寻求出更好的发展方向,掌握更好的技术。
飞机制造技术的创新与发展,能够促进和保障我国飞机航空事业的顺利发展,从而推动我国经济进一步的发展。
关键词:自动进给钻刀具导套制孔精度复杂孔系的制孔中图分类号:V262.4文献标识码:A1 飞机装配的相关概述飞机各项部件之间的连接属于一种高科技的范畴,由于飞机各个部件的精密性要求非常高,所以对于其装配工作就要做到百分百的严谨。
就当前的飞机结构件之间的连接方式来说,主要以机械型的连接为主。
其中比较常见的形式为铆钉连接和螺栓连接。
鉴于飞机对于各项部件的高要求,因此该项连接技术在不断地发展进步当中。
该技术应用对于飞机来说,是直接影响到飞机的使用质量,甚至直接与人们的生命安全相关联。
对飞机上四分之三的机体疲劳破坏情况进行分析,发现疲劳主要产生的位置就在机身的连接处。
在传统的飞机部件制作中,大部分的装配件是通过手工制孔来进行连接。
因为个体技能及素质差异,人工进行操作,就会存有一定程度上的误差,毕竟人工的作业水平和精准度是有限制性的,即会产生制孔的精度差、质量低等问题,难以达到飞机装配质量和效率的标准。
飞机的制孔方式目前主要存在手工、半自动和自动等方式[1]。
随着科学技术的不断发展,对于一些新型材料如新型钛合金材料、复合材料、高硬度高强度钢等被开始逐渐使用在飞机的制造中,对于飞机制造的相关工艺和技术要求也日益提高,传统的手动制孔技术已经不能再适应时代的发展,在逐渐被淘汰的同时也被设备制孔方法所取代。
目前就我国飞机制造行业的发展现状来看,飞机的装配领域已经在逐渐地使用自动进给钻技术。
这些技术由于大部分是从国外引进的,所以国内对其精髓掌握的还不全面。
除此之外,国内对于与该技术相关的符合标准的制孔精度配套的刀具、钻套技术研究较少,所需要的一系列技术几乎全部依赖国外的供应。