未来航空发动机涡轮叶片用材
新材料在航空航天中的使用

新材料在航空航天中的使用随着科技的不断发展和进步,新材料的应用越来越广泛,其中最为重要的领域之一便是航空航天。
新材料的各种优异特性和性能,不仅能够提升飞行器的飞行效率和安全性,同时也可以减轻飞机的重量和降低能耗成本。
本文将重点探讨新材料在航空航天中的应用。
1. 碳纤维复合材料碳纤维复合材料是一种高性能材料,由碳纤维和树脂等组成。
它的密度很小,而强度和刚度非常高,同时还具有极好的耐腐蚀性和抗疲劳性。
在飞机的制造中,碳纤维复合材料已经成为最常用的材料之一,尤其是在机身、机翼等大部件的制造中,起到了关键的作用。
与传统的金属材料相比,碳纤维复合材料具有更轻的重量和更好的飞行性能。
2. 稀土金属材料稀土金属材料是一种新型的金属材料,其性能非常优异。
在航空航天中,稀土金属材料可以用于制造飞机发动机的各种部件,比如涡轮叶片和燃烧室。
它具有高温抗氧化性、高强度和轻质化等特点,可以大大提高飞机的动力性能和燃油效率。
3. 高温耐腐蚀材料高温耐腐蚀材料是一种新型的材料,在航空航天领域中有着广泛的应用。
航空发动机的运行过程中,往往要承受极高的温度和腐蚀。
高温耐腐蚀材料可以在高温和腐蚀环境下保持稳定的性能,并且能够有效减少机身等重要部件的磨损和失效。
目前,高温耐腐蚀材料主要是采用钼、钨、铜等金属材料和其它合金进行制造。
4. 轻质化材料轻质化材料是指在保证足够强度的前提下,将材料的密度降低,从而实现降低飞机重量的目标。
在航空航天领域中,轻质化材料的应用非常广泛,比如高分子复合材料、铝合金、镁合金等。
这些材料不仅具有轻质化的特点,而且还具有优异的强度和刚度,可以大大提高飞机的综合性能和安全性。
5. 智能材料智能材料是一种新型的材料,在航空航天领域中也已经得到了广泛的应用。
智能材料具有响应外部刺激的特性,比如形状记忆材料、压电材料等。
在航空航天中,智能材料可以用于制造自适应控制系统、智能传感器、无人机等高科技装备,可以有效提高飞行器的智能化水平和性能。
特种金属材料

特种金属材料
特种金属材料是指一类具有特殊性能和特殊用途的金属材料。
这些金属材料具有很高的强度、硬度、耐腐蚀性、耐高温性、耐磨性等特点,常常被用于高端领域,如航空航天、船舶制造、电子器件、医疗器械等。
一种常见的特种金属材料是高温合金。
高温合金具有高强度、耐高温、耐氧化的特点,可以在高温环境下保持稳定的性能。
因此,高温合金广泛应用于航空航天、石油化工、冶金等领域。
航空发动机的涡轮叶片、燃烧室、燃气轴承等关键零部件都采用高温合金制成,以保证其在高温高压环境下的可靠性和安全性。
另一种常见的特种金属材料是钛合金。
钛合金具有优异的机械性能和耐腐蚀性,比重轻,强度高,在航空航天、船舶制造、汽车制造、医疗器械等领域有广泛应用。
航空航天领域常用的钛合金有TC4、Ti-6Al-4V等,它们具有高的强度、低的密度
和良好的耐腐蚀性,适用于制造飞机结构件、发动机零部件,如机翼、外壳、支撑架等。
此外,镍基高温合金、钼合金、锆合金等也是常见的特种金属材料。
镍基高温合金在高温环境下具有优异的耐热性能和抗蠕变性能,常用于航空发动机、石油化工设备等;钼合金具有优异的机械性能和耐热耐腐蚀性,在航空航天、船舶、电子器件中得到广泛应用;锆合金具有低密度、高强度和良好的耐腐蚀性,主要应用于核工业、化工设备等领域。
特种金属材料的发展对于推动先进制造技术和高端产业的发展具有重要意义。
随着科技的不断进步和需求的不断增加,特种金属材料的研发和应用将越来越广泛。
在未来,随着材料科学和工艺技术的发展,特种金属材料将不断创新和突破,为各个领域带来更多的可能性和机遇。
未来航空发动机材料面临的挑战与发展趋向

未来航空发动机材料面临的挑战与发展趋向摘要:航空发动机是进行航空的重要动力,对航空领域今后的发展有着非常关键的作用,为此必须要对其予以重视。
本篇文章简要介绍了未来航空器对航空发动机材料的需求,分析了航空发动机材料相关技术,并研究了材料今后的发展趋向,希望能够增强航空发动机的性能。
关键词:未来;航空发动机;材料;挑战;发展;趋向基金项目:陕西省自然科学基础研究计划资助项目(项目批准号:2020JQ-477,2018JQ5175)随着我国经济水平的提升,科技实力增强,航空行业得到了一定的发展,航空飞行器出现了变化,作为飞行器主要动力来源的航空发动机有着越发重要的作用。
从某种角度来说,发动机的材料能够决定其性能,为此,必须要对其予以重视。
一、未来航空发动机材料面临的挑战无论是用于军事的飞机还是民航飞行器,性能都会受到发动机的影响。
近些年来,发动机的研究取得了一定的成果。
但是随着发动机的发展,叶片等原本的构造越发复杂,原本的材料已经无法满足发动机正常运转的需要,为此,必须要对材料进行创新,找出适宜的材料,并合理的选择工艺,确保发动机能够为飞行器的正常使用提供充足的动力[1]。
根据目前时代发展情况来进行分析,在今后航空飞行器的主要发展趋势是在保护环境的同时降低对能源的消耗,并且性能有所增强。
随着现在可以借助于技术来减少发动机需要消耗的能源,但是,如果对发动机的材料进行改善,就能够较为有效的达成各个目标,为此,必须要重视未来发动机材料的选择。
二、航空发动机关键零件材料所运用的技术(一)压气机从当前的情况来进行分析,压气机盘和叶片材料的钛合金最高能够在600摄氏度的环境下进行工作。
随着压气机的压力增加,压气机出口的温度也会有所提升。
在这一情况下,压气机后几级会选择使用钛合金等材料,但是这一类材料随着压气机总压比的进一步提升,已经无法满足现实需要,如果发动机的推重比到达20,出口温度就会到达800摄氏度。
为了对这一问题进行解决,国外通过改变难溶金属的比例和晶粒大小,研究了新型材料,这种材料对高温的承受能力比较强。
航空发动机的新材料

航空制造是制造业中高新技术最集中的领域,属于先进制造技术。
美国惠普公司研制的F119发动机,通用电气公司的F120发动机,法国的SNECMA公司的M88-2发动机,英国、德国、意大利和西班牙四国联合研制的EJ200发动机。
这些代表世界先进水平的高性能航空发动机,它们的共同特点是普遍采用了新材料、新工艺和新技术。
今天就来看看那些高性能航空发动机上的新材料。
高温合金高温合金是为了满足喷气发动机对材料的苛刻要求而研制的,至今已成为军用和民用燃气涡轮发动机热端部件不可替代的一类关键材料。
目前,在先进的航空发动机中,高温合金用量所占比例已高达50%以上。
高温合金的发展与航空发动机的技术进步密切相关,尤其是发动机热端部件涡轮盘、涡轮叶片材料和制造工艺是发动机发展的重要标志。
由于对材料的耐高温性能和应力承受能力提出很高要求,早期英国研制了Ni3(Al、Ti)强化的Nimonic80合金,用作涡轮喷气发动机涡轮叶片材料,同时,又相继发展了 Nimonic系列合金。
美国开发了含铝、钛的弥散强化型镍基合金,如普惠公司、GE公司和特殊金属公司分别开发出的Inconel、Mar-M和 Udmit等合金系列。
在高温合金发展过程中,制造工艺对合金的发展起着极大的推进作用。
由于真空熔炼技术的出现,合金中有害杂质和气体的去除,特别是合金成分的精确控制,使高温合金性能不断提高。
随后,定向凝固、单晶生长、粉末冶金、机械合金化、陶瓷型芯、陶瓷过滤、等温锻造等新型工艺的研究成功,推动了高温合金的迅猛发展。
其中定向凝固技术最为突出,采用定向凝固工艺制出的定向、单晶合金,其使用温度接近初熔点的90%。
因此,目前各国先进航空发动机叶片都采用定向、单晶合金制造涡轮叶片。
从国际范围来看,镍基铸造高温合金已形成等轴晶、定向凝固柱晶和单晶合金体系。
粉末高温合金也由第一代650℃发展到750℃、850℃粉末涡轮盘和双性能粉末盘,用于先进高性能发动机。
航空发动机涡轮叶片的研究与设计

航空发动机涡轮叶片的研究与设计随着现代航空事业的快速发展,航空发动机作为航空工业的核心技术之一也迎来了飞速的发展。
航空发动机主要由压气机、燃烧室和涡轮三部分组成。
其中,涡轮是发动机最核心的组成部分之一,而涡轮叶片则是涡轮中最重要的组成部分。
涡轮叶片的主要作用是将高速气流转化为机械能,驱动整个发动机运转。
同时,涡轮叶片的材质、设计和制造工艺等方面也会直接影响到发动机的运转效率、寿命和可靠性等方面。
因此,涡轮叶片的研究与设计一直是航空工业的研究热点之一。
涡轮叶片的材质涡轮叶片的材质是涡轮叶片设计的首要问题之一。
目前,航空发动机涡轮叶片常用的材料为镍基高温合金和钛合金等。
镍基高温合金具有高的热强度、抗氧化性和抗腐蚀性,是制造高温部件的主要材料;而钛合金则具有良好的强度、韧性和疲劳寿命等特点,是制造低温部件的优选材料之一。
为了满足不同使用环境下的涡轮叶片设计需求,研究人员也在不断探索新的涡轮叶片材料。
近年来,一些新型的高强度、高温度抗氧化性能良好的材料,如SiC、C/C复合材料、La2O3等,也被广泛应用于航空发动机涡轮叶片的研究和设计中。
涡轮叶片的设计涡轮叶片的设计需要考虑很多因素,如叶片的长度、宽度、厚度、倾角、弯曲角度、扭转角度和叶片数量等,以及叶片与叶片之间的间隙和位移等因素。
不同类型的发动机和使用环境,对涡轮叶片的设计也有着不同的要求。
例如,民用飞机的涡轮叶片通常要求具备较高的运转效率和低的噪音、振动等特性,设计时需要将各种因素进行权衡,力求寻求最佳的设计方案。
而在军用飞机和直升机等特殊用途飞行器上,涡轮叶片的设计往往更加考虑高强度、高温度、高抗氧化性、低可检测性等特点。
涡轮叶片的制造工艺涡轮叶片的制造工艺与材料和设计方案一样,也需要考虑到不同的使用环境和要求。
目前,涡轮叶片的制造工艺主要包括:传统的铸造、锻造、粉末冶金和激光熔覆等工艺,以及新兴的快速成型、3D打印和表面喷涂等技术。
其中,传统的铸造和锻造工艺是涡轮叶片生产中最主要的工艺方法之一,这些方法可以制造较大尺寸和复杂形状的叶片,但同时也有一定的缺点,如叶片内部可能产生气孔、夹杂等缺陷,影响叶片的强度和寿命。
航空发动机涡轮叶片材料的应用与发展
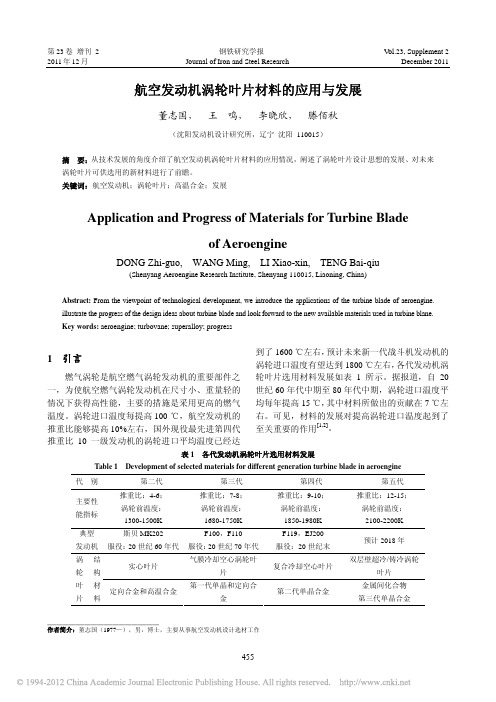
第23卷 增刊 2 钢铁研究学报 V ol.23, Supplement 2 2011年12月 Journal of Iron and Steel Research December 2011____________________________________作者简介:董志国(1977—),男,博士,主要从事航空发动机设计选材工作航空发动机涡轮叶片材料的应用与发展董志国, 王 鸣, 李晓欣, 滕佰秋(沈阳发动机设计研究所,辽宁 沈阳 110015)摘 要:从技术发展的角度介绍了航空发动机涡轮叶片材料的应用情况,阐述了涡轮叶片设计思想的发展、对未来涡轮叶片可供选用的新材料进行了前瞻。
关键词:航空发动机;涡轮叶片;高温合金;发展Application and Progress of Materials for Turbine Bladeof AeroengineDONG Zhi-guo, WANG Ming, LI Xiao-xin, TENG Bai-qiu(Shenyang Aeroengine Research Institute, Shenyang 110015, Liaoning, China)Abstract: From the viewpoint of technological development, we introduce the applications of the turbine blade of aeroengine. illustrate the progress of the design ideas about turbine blade and look forward to the new available materials used in turbine blane. Key words: aeroengine; turbovane; superalloy; progress1 引言燃气涡轮是航空燃气涡轮发动机的重要部件之一,为使航空燃气涡轮发动机在尺寸小、重量轻的情况下获得高性能,主要的措施是采用更高的燃气温度。
航空发动机叶片材料及制造技术现状

航空发动机叶片资料及制造技术现状在航空发动机中,涡轮叶片由于处于温度最高、应力最复杂、环境最恶劣的部位而被列为第一要点件,并被誉为“王冠上的明珠”。
涡轮叶片的性能水平,特别是承温能力,成为一种型号发动机先进度度的重要标志,在必然意义上,也是一个国家航空工业水平的显然标志【 007】。
航空发动机不断追求高推重比,使得变形高温合金和铸造高温合金难以满足其越来越高的温度及性能要求,因其他国自7O年代以来纷纷开始研制新式高温合金,先后研制了定向凝固高温合金、单晶高温合金等拥有优异高温性能的新资料;单晶高温合金已经发展到了第3代。
8O年代,又开始研制了陶瓷叶片资料,在叶片上开始采用防腐、隔热涂层等技术。
1航空发动机原理简介航空发动机主要分民用和军用两种。
图 1是普惠公司民用涡轮发动机主要构件;图2是军用发动机的工作原理表示图;图 3是飞机涡轮发动机内的温度、气流速度和压力分布;图 4是罗尔斯 -罗伊斯喷气发动机内温度和资料分布;图 5为航空发动机用不同样资料用量的发展变化情况。
图 1普惠公司民用涡轮发动机主要构件图2 EJ200 军用飞机涡轮发动机的工作原理图3商用涡轮发动机内的温度、气流速度和压力分布图4罗尔斯-罗伊斯喷气发动机内温度和资料分布图5航空发动机用不同样资料用量的变化情况1变形高温合金叶片1.1 叶片资料变形高温合金发展有 50多年的历史,国内飞机发动机叶片常用变形高温合金如表 1所示。
高温合金中随着铝、钛和钨、钼含量增加,资料性能连续提高,但热加工性能下降;加入昂贵的合金元素钴此后,能够改进资料的综合性能和提高升温组织的牢固性。
表1国内飞机叶片用高温合金牌号及其工作温度合金牌号合金系统GH4169Cr-Ni GH4033Cr-NiGH4080A Cr-Ni GH4037Cr-Ni GH4049Cr-Ni-Co GH4105Cr-Ni-Co GH4220Cr-Ni-Co 使用温度 /℃特点及应用650 热加工性能好,热变形和模锻叶片成形不困难,叶身变形80%也不开裂。
航空发动机涡轮叶片材料研究

航空发动机涡轮叶片材料研究航空发动机的性能对于航空产业的发展起着至关重要的作用,而其中涡轮叶片是飞机发动机中非常重要的组成部分。
涡轮叶片的材料研究一直以来都是一个热门的研究领域,其材料的选择与性能直接关系到飞机的可靠性和安全性。
因此,对于航空发动机涡轮叶片材料的研究一直以来都备受关注。
1. 涡轮叶片材料研究的历史沿革早在20世纪初期,英国的战斗机大战时期,涡轮叶片的材料就成为了一个重要的问题。
当时的涡轮叶片材料是由铁、铬、钴合金制成,这种材料的性能稳定,但是其密度很大,对于飞机的轻量化有很大的制约,同时其强度也比较低,无法满足高速飞行和高温环境的要求。
随着科技的不断进步,人们开始研究新的材料并探索新的工艺,逐渐从金属材料向复合材料、陶瓷材料和高温合金材料转变。
2. 现有涡轮叶片材料的特点与不足目前,航空发动机涡轮叶片材料主要包括高温合金材料、陶瓷基复合材料和单晶超合金材料等。
高温合金材料的主要特点是具有很高的耐高温性能和抗氧化能力,符合飞行器大气层的高温、高压和高速环境的要求,但是其强度和硬度较低,带有一定的脆性,耐蚀性和耐疲劳性能也有待提高。
陶瓷基复合材料的优点在于具有很高的强度和硬度、低密度、高温稳定性和抗腐蚀性等特点,但是其耐疲劳性和韧性还需要进一步加强。
单晶超合金材料(SCM)是最典型的高性能涡轮叶片材料,具有高强度、高温稳定性、良好的耐蠕变性能和良好的耐腐蚀性能。
但是,其制造工艺较为复杂,生产成本较高,同时该材料的脆性也难以完全避免,使用寿命可能受到一定影响。
3. 涡轮叶片材料未来发展趋势在涡轮叶片材料的研究中,材料的性质和制造工艺都是研究的重点。
在未来的研究中,涡轮叶片材料将更加注重材料的性能和成本,同时更加注重环保和可持续发展。
其中,复合材料和纳米材料可能会成为涡轮叶片材料的发展方向。
复合材料因其轻量化和强度优势,在涡轮叶片材料的研究中已经被广泛应用;而纳米材料则因其纳米级尺度下的特殊性能,被认为是涡轮叶片材料未来的发展趋势。
- 1、下载文档前请自行甄别文档内容的完整性,平台不提供额外的编辑、内容补充、找答案等附加服务。
- 2、"仅部分预览"的文档,不可在线预览部分如存在完整性等问题,可反馈申请退款(可完整预览的文档不适用该条件!)。
- 3、如文档侵犯您的权益,请联系客服反馈,我们会尽快为您处理(人工客服工作时间:9:00-18:30)。
L A - 攀 4V 熬燕 1 t : 沉积通常用于制备非 薰黔薰 u1 〕 鬓 0 常薄的 (Om) In 的微 L 羹C-b叠 . J 2 . }1 鳞 7 〕 I -N 7 1
( 护 ) 创 照 民
合材料.而物理气相
明 喇
复护 \ 合、 材
/
/ 体料 材
1 ‘ 月 卫 .月 卫 土
近年来,美国G P公司 在美国空军 二 进 冷 却 实验室材料指导部资助下,开展了将金 划 招 属间化合物与韧性金属组成微叠层复合 各 材料这一新方案的研究工作,从事这一 ‘ ‘向 翎径对 研究的还有洛克希德・ 马丁公司、 橡树岭 、流冷 却 国家实验室、 加州大学等, 加拿大和欧洲 高压涡轮叶片冷却气流减少 也已着手从事该方面的研究工作。因此 图1 高压涡轮叶片冷却设计和材料的演进过程 这种材料已成为目前的 一 个研究热点。 该项研究旨在依靠耐高温金属间化 持其原有强度,且在某些条件 「 能保持 到 1 ) 但经研究发现 作为一种单体 合物提供高温强度和蠕变抗力,而利用 4℃ 0 材料, 金属间化合物非常脆. 成形工艺性 高温金属作韧化元素,从而很好地克服 了金属间化合物脆性这一缺点,使航空 差, 难以在发动机上获得实际应用 洲 K 发动机祸轮叶片材料这一航空领域最关 ( 尸 R' N4 键的材料展示出光明前景 )侧 CM S X-1 0 H 阳 图3 所示为合金使用温度与使用温 担 盗 度占其熔点百分比的函数关系图。从图 澎 州 月 弓 中可看出,与镍基合金及其复合材料相 卜 吠 xJ 比,以锭基合金韧化的金属间化合物复 奎 }一 合材料具有明显的优势, 它的工作温度 己 仪 月 芝 占熔点的百分率较低.因此工作温度较 0 分 高 - 7( 犯
叭i r t y 1 & f t - l 9
1 0
2体材科
" N基 溢合 / O 高 金 i
I 霏G " }e n Y O ( N l i j } 1 * 4
化合物笨/ } )创 』履 一次 引 }
}" 夕
朋 绷
N 基高温合金 i
及复合材科
(5卜 微叠层复 >( m) )
能 实现的 :
通过对上述 bC2 系统的一系 N - r b N 列分析,可以预期制备叶片的第一步是 在高韧性的金属梁上做 一 个微叠层金属 间化合物复合材料外壳( 目前定义的微
化 合物墓
基 金且 间
系统只能部分满足上述 需求. 缺乏综合性能良好 的材料系统。 抗氧化性是 . r 述综 合要求中最关键的性能
优点是可以制备出各种层厚、 体积百分 比以及层组分的金属间化合物复合材 料, 且间隙元素污染程度低, 并具备良好
舫 空工 怪 与组 价 2 0 1 0 15
1 1
万方数据
( 吕 ・日 )、 沙
2. 42 2. 1 7
纳米层状热障涂层
单层 T C B
梢 嵘 臻 叶
热障涂层 T C) ( 已有多年 B 1. 77 的发展历史, 近年随着纳米技术 1名 3 的发展, 有可能将其用于镍基高 1. 04 温合金的涂层, 将来还有可能用 69 . 纳米层状 T C B 35 . 其直接制备出叶片 图 6所 示为传统的单层 t0 3 4 5 7 10 02 0 0 5 0 0 0 0 0 0 0 0 0 T C材料与纳米层状 T C材料 B B 温度 ( ) ℃
4 厕 藩 r" 巨 蘸 薰 C4 料 3 - 2 互2 r b 曦- C鼠鑫 L 浑C菊 N 7 2 7 b9 r
招
叠层材料
物理气相沉积的
片
阴
的结构完整性。 1表2 表 、 所示分别为在 不同的实验中 C,h N r - b和 N - b i N b N,, S -I a ,/ } r } 一 0p 动 9 . 0 即 0 I0 0 之一。事实上, 所有在高 复合材料的层厚 使用昌 1度占材料I点百分比 S 温下长期使用的复合材 C 公司重点进行了C2b N 微叠 E r -b N 圈 3合金使用温度与使用沮度占熔点百分比的关 系 料系统 为防止氧化 都需 层复合材料的研究, 其结论是; 要涂层,但金属间化合物复合材料系统 () I 较薄层厚材料的室温断裂强度 还必须具备足够的固有的抗氧化能力, 优于较厚的层, 但韧性稍差, 因而选择层 以防止当涂层发生破坏时出现灾难性氧 厚需要在断裂强度和韧性之间求得平 化 这里的问题是, 尽管优基合金较之镍 衡 基合金的使用温度更高,但其致命的抗 () 2 由于金属间化合物层的显微组 氧化能力差却一直是限制其用于航空发 织为超细晶粒组织, 因而高温强度较低, 动机的主要原因‘图 S 是各类高温合金 但在其他定向非连续复合材料系统中可 在1h 0 高温下失重的比较 从该图可看 以观察到很高的强度和蠕变抗力,这表 0 图4 V 法生 用P D 产涡轮叶片的示 宜圈 出,锭基合金伉氧化性明显劣于镍基合 明如果金属间化合物的晶粒可以粗化 , () 1由于梁内部不需要铸出冷却 孔, 金 近期开发的以钦、 铝、 铅、 铬合金化的 可采用 较低成本的方案加工梁 妮合金与 普通市售锭合金相比,抗氧化 黔 { () 2 通过壳型铸造或机加工方法加 性 得显 改 获 著 进, 并在1010 及 薰 蒸 羹 1 - 0℃ 5 2 O ( i 鹅蘸 鹦 U 工出高塑性金属梁中的冷却通孔。 1 其以上温度下的氧化行为接近镍基合 ; 薰 } I 寒3 蒸 D, 麟 羹1 7 k () 3 在加工出孔的梁表面上填充以 金 此外, X , 在同样的温度范围内, N 一 高温 b N h 临时的填充物, 然后对表面进行修橄、 研 (iN ,: N (r C,b S - bS 和 b ) r 复合材料 ) i C- N v } I L N I 靡 a 瞬I h, 羹w S 磨 〕薰 0 的抗氧化行为也接近镍基合金 因此可 麟 黝 蘸7 蒸 N b ( V 4 采用P D法沉积出金属间化 以预期 、具有较 高抗氧 ) 、 () 沮度 ' C 合物复合材料的外壳 化能力的金属间化合物 30 0 ( 通过化学浸析, 洲 将冷却通孔中 复合材料将得到发展。 10 0 的临时填充物析出 2韧性金属间化合 !( 〔幻 ( 口日 采用这种制备方案生产高压祸轮叶 物基复合材料的合成 3 0 巴 )东 目前已制备出的几 片, 可使涡轮进口 温度提高30. 0T, 同时 1 0 10 〔日二 军 保持涡轮叶片的高塑性.并可减少冷却 种微叠层复合材料有具 遥 )水 . 娜 30 卑 气流的用量 有不同组分和层I f的 卫完 1 . 0 10 咚叫 下 叶片材料性能 N - r bN - b i以 b , ,bN ,, C N S 1 03 . 月8 高压涡轮叶片材料需要满足多种要 及 N - oi等体系 采 bM S , 叫 01 . 求, 即强度、 高温抗蠕变能力、 低温断裂 用的方法有真空热H : . 1 00 .3 强度及断裂韧性、 抗氧化性、 抗热振能 箔、 物理气相沉积、 铸造 力、 高温下的显微组织稳定性, 此外还应 和固态反应等方法。研 0m 1 00 10 1 0 2 0 2 0 . 0 3 6 0 9 0 2 0 5 0 具备价格优势 在金属间化合物复合材 究表明,真空热压和铸 温度( ) ( } F 料旱期研发阶段 所制备出的复合材料 造 法 适 干 制 备 厚 的 图5各类高温合金在 10 高温下失1的比较 0h
侧 洲
‘ 产 、 产 先 闷 多 层
微叠层体型复合材料
t f 成果使得 2 世纪 1 及 9 年 代航空 0 1 0 0
发动机的涡轮进口温度提高了30:图 09 】 展示出高压涡轮叶片冷却设计和材料 的演进过程 图2 所不为高温合金的最高使用温 度与其使用年代的关系一从图中可明显 看出. 近年来高温合金的发展速度放慢 其中最卞要的原因是,虽然单晶工艺可 使合金 熔点得以部分提高,但其提高的 幅度相当有限 高温金属(化合物的出现为解决上 a l 屯子束物理气相沉积‘V 工艺 P D, 1 4 1 6 1 8 2 9 0 9 0 9 0 仆X 是生产这种多层冷却结构的一种经济上 述问题提供了希望, 0 在2 世纪八九十年 使用年代 是用P D法生产涡 V 代得到广泛重视和迅速发展。如C,b 圈2离温合金的最高使用温度与其使用年代 可承受的方案 图4 r , N 轮叶片的示意图。其基本过程是: N ;3 A 或 C. 在 10℃下能保 的关系 bS , I r i 20 iW , S
专粗 S E IL E O T P CA R P R
微叠层复合材料技术将是未来航空发动机涡轮叶片用材 料的最新材料形式技术。本文对该技术进行了综合论述, 包括 微叠层体型复合材料技术及纳米层状热障涂层技术两个方面。
未来航空发动机涡轮叶片用材的 最新形式— 微叠层复合材料
Mi oa n td mp s e: e x c l r miae C o oi s T N t t h e
导 热率的比较 从图中可看出_
涂覆方案, 如浸涂 、 喷涂 旋涂、 辊涂以及 刷涂等: 采用激光检测技术, 探索将 r , i o 用于热障涂层 并着手进入商业化 种种迹象表明, 在微米层次上, 界面 作用增加,薄层的性质已开始偏离体材 料性质. 从而在热胀、 变形、 应力传递、 以 及压敏、 压电、 热敏等方面出现新性质 作为一项新兴技术。它在航空领域蕴藏 着巨大应用潜力,潜伏着大好的创新机
的基本途径 同时, 必须充分了 解穿透形
者的明显差异,纳米层状 T C B 涂层的导热系数远低于单层的 T C 因 B, 而国外预测采用纳米层状热障涂层可将
尧成扳 娜% 驴 0 . 公a W A 诊I 的P ( 0 日 7 i 0 0
成的机理, 以预测穿透现象出现的条件 ( )镍基金属韧化层和复合材料 4 系统二者的抗氧化性能得以改善的事 实表明, 耐高温、 抗氧化这一目标是可
遇. 口
圈 6单层 〕 BC材料与纳米层状 T C材料导热率的比较 B
则高温强度可获改善 目 前这种晶粒粗 化技术可以通过提高沉积温度。 或通过 选择适宜的金属间化合物复合材料系统 来实现,这种金属间化合物复合材料在 晶界迁移起点和金属间化合物稳定性上 限之间具有较宽温度窗口 () 3 微叠层复合材料在 10℃下的 40 稳定性受金属间化合物相向金属f深度 L 穿透这一非平衡态变化过程的影响, 穿 透形成的机理可能与晶界扩散有关, 因 此获得一种在整个工作温度范围内处于 平衡态的金属和金属间化合物组分很少 变化的复合材料系统,是消除这一问题