航空发动机叶片CAD技术综述
航空发动机涡轮叶片冷却技术综述

航空发动机涡轮叶片冷却技术一、引言航空发动机自诞生以来,对它的基本发展要求就是推力更大、推重比更高、耗油率更低、质量更轻、耐久性更好和费用更低等。
因此,航空发动机涡轮的发展趋势主要在以下两个方面:其一是不断提高涡轮前温度;其二就是不断增加涡轮气动负荷,采用跨音速涡轮设计方案,减少涡轮级数和叶片排数。
在现有技术条件下,并在保证尺寸小、质量轻的情况下,提高涡轮前温度,是获得大推力和高推重比的主要措施之一。
从理论上讲,涡轮进口温度每提高100℃,航空发动机的推重比能够提高10%左右。
当前,先进航空发动机涡轮前温度已经达到1900K 左右,这远远超过了涡轮叶片所用的高温合金材料的熔点温度。
为了保证涡轮叶片在高温燃气环境下安全可靠地工作,就必须对叶片采取冷却和热防护措施。
对于高温所带来的一系列问题,解决的办法主要有两个:一是提高材料的耐热性,发展高性能耐热合金,制造单晶叶片;二是采用先进的冷却技术,以少量的冷却空气获得更高的降温效果。
其中材料的改善占40%,冷却技术占60%。
对于军用航空发动机,第3代的涡轮进口温度为1680~1750K,涡轮叶片耐温能力主要通过第1代单晶合金或定向合金和气膜冷却技术保证;第4代的涡轮进口温度达到1850~1980K,涡轮叶片耐温能力主要通过第2代单晶合金和对流-冲击-气膜复合冷却技术来保证;未来一代的涡轮进口温度将高达2200K,预计涡轮叶片耐温能力通过第3代单晶合金或陶瓷基复合材料等耐高温材料和包括层板发散冷却在内的更加高效的冷却技术来保证。
二、航空发动机涡轮叶片冷却技术概述涡轮冷却技术研究始于上个世纪40年代,大约在1960年,气冷涡轮首次应用于商业航空发动机上。
经过多年的发展,目前基本上形成了由内部冷却和外部冷却构成的涡轮叶片冷却方案。
1.内部冷却其基本原理是冷气从叶片下部进入叶片内部,通过带肋壁的内流冷却通道,对叶片的内表面实施有效的冷却,一部分冷气通过冲击孔,以冲击冷却的形式对叶片前缘内表面进行冷却,剩下的一部分气体经过叶片尾部的扰流柱,被扰动强化换热以后从尾缘排出。
航空发动机叶片CAD、CAPP、CAM的思考
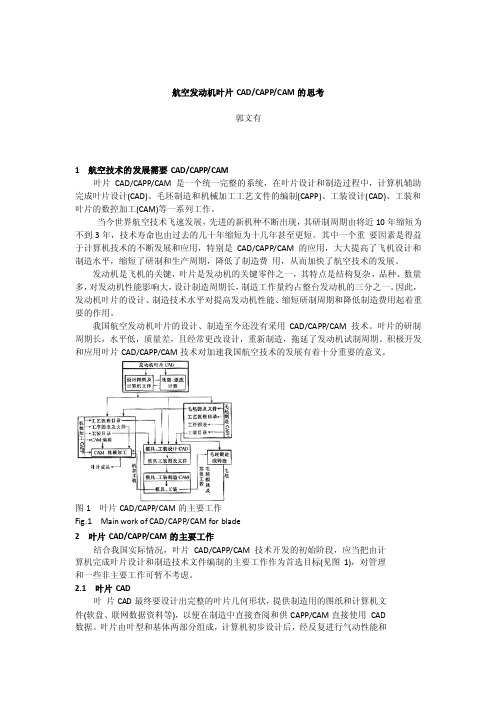
航空发动机叶片CAD/CAPP/CAM的思考郭文有1航空技术的发展需要CAD/CAPP/CAM叶片CAD/CAPP/CAM是一个统一完整的系统,在叶片设计和制造过程中,计算机辅助完成叶片设计(CAD)、毛坯制造和机械加工工艺文件的编制(CAPP)、工装设计(CAD)、工装和叶片的数控加工(CAM)等一系列工作。
当今世界航空技术飞速发展,先进的新机种不断出现,其研制周期由将近10年缩短为不到3年,技术寿命也由过去的几十年缩短为十几年甚至更短。
其中一个重要因素是得益于计算机技术的不断发展和应用,特别是CAD/CAPP/CAM的应用,大大提高了飞机设计和制造水平,缩短了研制和生产周期,降低了制造费用,从而加快了航空技术的发展。
发动机是飞机的关键,叶片是发动机的关键零件之一,其特点是结构复杂,品种、数量多,对发动机性能影响大,设计制造周期长,制造工作量约占整台发动机的三分之一。
因此,发动机叶片的设计、制造技术水平对提高发动机性能、缩短研制周期和降低制造费用起着重要的作用。
我国航空发动机叶片的设计、制造至今还没有采用CAD/CAPP/CAM技术。
叶片的研制周期长,水平低,质量差,且经常更改设计,重新制造,拖延了发动机试制周期。
积极开发和应用叶片CAD/CAPP/CAM技术对加速我国航空技术的发展有着十分重要的意义。
图1叶片CAD/CAPP/CAM的主要工作Fig.1Main work of CAD/CAPP/CAM for blade2叶片CAD/CAPP/CAM的主要工作结合我国实际情况,叶片CAD/CAPP/CAM技术开发的初始阶段,应当把由计算机完成叶片设计和制造技术文件编制的主要工作作为首选目标(见图1),对管理和一些非主要工作可暂不考虑。
2.1叶片CAD叶片CAD最终要设计出完整的叶片几何形状,提供制造用的图纸和计算机文件(软盘、联网数据资料等),以便在制造中直接查阅和供CAPP/CAM直接使用CAD数据。
CG与CAD_CAM技术在压气机叶片中的应用研究

1 CG、 CAD /CAM 技术概述
CG 技术是研究通过计算机将数据 转换为图形 , 并 在专用 显示设备上显 示的原 理、 方法 和技术 的一门 学科。计算机 图 形学包括图形数据结构、 图形算法与计 算机语言 , 图形 就是对 象的形象化表示。 CAD 技术采用计算机系统 完成资料整理分 析、 工程计算、 结 构模型 分析、 设 计优化、 经费 预决算、 绘制 图 形 , 它能提高产品的设 计质量 , 发挥 设计人 员的创 造性 , 缩 短 产品的设计周期 , 提高产品的 竞争能力。 CAM 是通过计 算机 直接控制加工 设备 , 使 它能够 自动地 加工产 品。它 的加工 过 程是由 CAD 技术和计算机图形软件产生一个完整的并符合加 工要求的数控语言 , 然后通过数控语言去控制加工设备。 CG 作为可视化图像表达的基础 , 为 CAD 的产生创造了条 件 ; 而 CAM 技术又是在 CAD 基础上产生的直接应用于生产的 技术 , 其加工过程 仿真中 的图形 又是 直接应 用 CG 的图像 表 达。在飞机制造工业中 , 美国波音公司已用有关的 CA D /CAM 技术实现了波音 777 飞机的整体设计和模拟 , 其中包括飞机外 形的曲线、 曲面拟合和建立外形数学模型等过程。
图 1 叶片截面图 利用 CG 技术改进设计方 案 , 可采 用反求 设计 对叶 片进 行数模建立。 反求 工程 ( R everse Eng ineering , R E) 也 称逆 向 工程、 反向工程等 , 是 指用一 定的 测量 手段 对实 物或 模型 进 行测量 , 根据测量 数据通 过三 维几 何建 模方 法 , 重构 实物 的 CAD 模型 , 从而实 现产品设计与制造的 过程。采用反 求工程 技术开发的产品往 往比较 复杂 , 通 常由 一些 复杂 曲面 构 成 , 精度要求也较高的产品 , 高压压 气机的叶 片设计 属于零 件反 求 , 实质上是零 件复制 [ 3] 。一 般针 对外 形设 计复 杂 , 无需 内 部结构的零件可采用最为简单易行的坐标测量 机 ( Coord inate M easuring M ach ine , CMM ) 的接触式 测量 , 该方 法采 用触 发探 头 , 当侧头的探针 接触到 样件 的表 面时 , 由 于探 针尖 受力 变 形触发采样器的开关 , 这样通过 数据采集 系统记 下探针 尖的
航空发动机涡轮叶片精密成型技术分析

航空发动机涡轮叶片精密成型技术分析摘要:航空发动机技术复杂且难以制造。
世界上只有几个国家可以完成航空发动机的设计和制造。
中国不断发展航空发动机的设计和制造,以提高自身的制造水平。
空心涡轮叶片是高性能航空发动机的主要部件之一,制造困难长期以来一直给中国的制造公司带来麻烦。
通过分析空心涡轮叶片的结构特性,分析和解释空心涡轮叶片的精密成型技术。
关键词:空心涡轮叶片;精密成型技术;精密铸造前言空心涡轮叶片是高性能航空发动机的关键组件,由于对精度的要求和制造困难,我们无法批量生产空心涡轮叶片。
为了提高空心涡轮叶片的制造合格率,我们将从叶片精密铸造的“形状控制”和“可控制性”两个方面出发分析空心涡轮叶片的精密铸造工艺,以提高叶片精密铸造的质量。
需要1空心涡轮叶片的精密铸造技术现代飞机发动机正朝着高推进力和低油耗的方向发展。
为了实现这一目标,当今世界上的主流方法是提高航空发动机涡轮的进气温度。
发动机涡轮的当前入口温度已经很高。
随着温度的不断升高,发动机涡轮叶片的温度达到1880℃±50℃,为了解决这个问题,目前的涡轮叶片主要用于复合膜冷却的单晶空心涡轮叶片(称为空心涡轮叶片)。
由于结构的复杂性和材料的特殊性,熔模铸造工艺主要用于制造空心涡轮叶片,但由于精度低,产量低,该工艺存在使空心涡轮叶片具有高性能的问题。
有。
通常,当今的空心涡轮叶片精密铸造的产率约为10%,其中约90%的废叶片的形状和尺寸偏差约为50%,而重结晶缺陷约占25%。
主要原因是铸造缺陷。
为了提高空心涡轮叶片的制造成品率,有必要解决“形状控制”和“铸造控制”两个问题:精密铸造后的尺寸精度和复合材料性能。
空心涡轮叶片的工艺复杂且难以制造:粗略的制造过程如下:首先,使用模芯来完成空心涡轮叶片精密铸造所需的陶瓷芯,并且陶瓷芯是空心的填充零件。
用来。
随后,使用蜡模工艺在芯的外层上制备涡轮叶片蜡模,然后通过烧结注射成型和其他工艺来制造空心涡轮叶片粗糙毛坯。
CG与CAD/CAM技术在压气机叶片中的应用研究

程是由 C D技术和计算机图形 软件产生一个完整的并符合加 A
工要 求 的数 控 语 言 , 通 过 数 控语 言 去 控 制加 工 设备 。 然后
C G作为可视化图像表达的基础 , C DD基础上产生 的直接应用于生产 的 而 A A 技术 , 其加工过程仿真 中的 图形 又是 直接应 用 C 的图像表 G 达 。在飞机制造工业 中, 美国波音公司已用有关的 C D C M A /A
的设 计 水 平 和 制 造 精 度 。
关键词 : 算机 图形 学; 算机辅助设计 ; 算机辅助制造 ; 计 计 计 压气机 叶片
中图 分 类 号 :P 9 . T 3 17 文 献标 识码 : A 文章 编 号 : 7 — 6 4 2 1 )2 0 8— 2 1 1 44 (0 10 —0 3 0 6 等一系列过程。 2 1 C 在 压气 机 叶 片设 计 中 的应 用 . G
每个 截面增 加 1 0个节 点 , 总数就 增加 大约 10个左 右 的节 5
点 , 4 0个坐标值 , 合 5 工作量较 大。在常规设 计条件 下 , 使用
1 CG、 A C M 技 术概 述 C D/ A
C G技术是研究通过计算机将数据转换 为图形 , 并在专用 显示设备上显示 的原 理 、 法和技术 的一 门学科 。计算 机图 方 形学包括图形数据结构、 图形算法与计算机语言 , 图形就是对 象的形象化表示 。C D技术采用计算机系统完成资料整理分 A
技 术 开 发 的产 品 往 往 比较 复 杂 , 常 由 一 些 复 杂 曲 面 构 成 , 通 精 度 要 求 也 较 高 的产 品 , 压压 气 机 的 叶 片 设 计 属 于 零 件 反 高 求 , 质 上是 零 件 复 制 。一 般 针 对 外 形 设 计 复 杂 , 需 内 实 无 部 结 构 的 零 件 可 采 用 最 为 简 单 易 行 的 坐标 测 量 机 ( oria C odnt e
航空发动机精锻叶片数字化数控加工技术
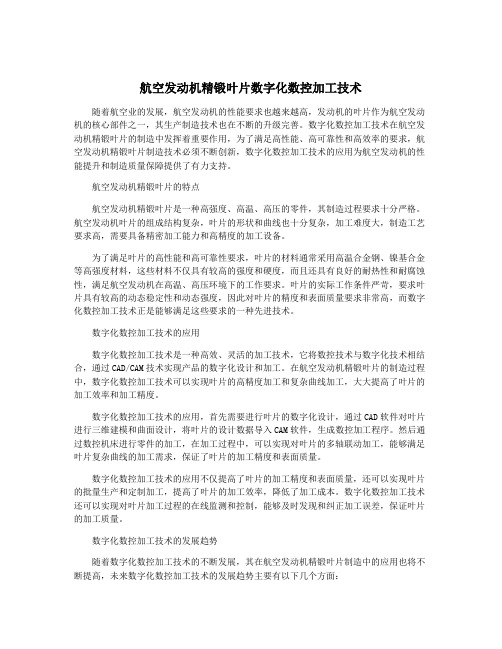
航空发动机精锻叶片数字化数控加工技术随着航空业的发展,航空发动机的性能要求也越来越高,发动机的叶片作为航空发动机的核心部件之一,其生产制造技术也在不断的升级完善。
数字化数控加工技术在航空发动机精锻叶片的制造中发挥着重要作用,为了满足高性能、高可靠性和高效率的要求,航空发动机精锻叶片制造技术必须不断创新,数字化数控加工技术的应用为航空发动机的性能提升和制造质量保障提供了有力支持。
航空发动机精锻叶片的特点航空发动机精锻叶片是一种高强度、高温、高压的零件,其制造过程要求十分严格。
航空发动机叶片的组成结构复杂,叶片的形状和曲线也十分复杂,加工难度大,制造工艺要求高,需要具备精密加工能力和高精度的加工设备。
为了满足叶片的高性能和高可靠性要求,叶片的材料通常采用高温合金钢、镍基合金等高强度材料,这些材料不仅具有较高的强度和硬度,而且还具有良好的耐热性和耐腐蚀性,满足航空发动机在高温、高压环境下的工作要求。
叶片的实际工作条件严苛,要求叶片具有较高的动态稳定性和动态强度,因此对叶片的精度和表面质量要求非常高,而数字化数控加工技术正是能够满足这些要求的一种先进技术。
数字化数控加工技术的应用数字化数控加工技术是一种高效、灵活的加工技术,它将数控技术与数字化技术相结合,通过CAD/CAM技术实现产品的数字化设计和加工。
在航空发动机精锻叶片的制造过程中,数字化数控加工技术可以实现叶片的高精度加工和复杂曲线加工,大大提高了叶片的加工效率和加工精度。
数字化数控加工技术的应用,首先需要进行叶片的数字化设计,通过CAD软件对叶片进行三维建模和曲面设计,将叶片的设计数据导入CAM软件,生成数控加工程序。
然后通过数控机床进行零件的加工,在加工过程中,可以实现对叶片的多轴联动加工,能够满足叶片复杂曲线的加工需求,保证了叶片的加工精度和表面质量。
数字化数控加工技术的应用不仅提高了叶片的加工精度和表面质量,还可以实现叶片的批量生产和定制加工,提高了叶片的加工效率,降低了加工成本。
航空发动机涡轮叶片精密成形技术分析

航空发动机涡轮叶片精密成形技术分析【摘要】航空发动机涡轮叶片是航空发动机中至关重要的部件,对发动机的性能和效率起着关键作用。
涡轮叶片精密成形技术是一项关键技术,经历了多年的发展历程,逐步完善并应用于实际生产中。
本文从涡轮叶片的重要性入手,阐述了涡轮叶片精密成形技术的发展历程及关键步骤,探讨了该技术在航空领域的应用,并展望了未来的发展趋势。
通过本文的研究,有助于更深入地了解航空发动机涡轮叶片精密成形技术的重要性和发展现状,为相关领域的研究和应用提供参考和借鉴。
【关键词】航空发动机、涡轮叶片、精密成形技术、研究背景、研究意义、发展历程、关键步骤、应用、发展趋势、未来展望、总结1. 引言1.1 研究背景航空发动机涡轮叶片是航空发动机中的重要部件,直接影响着发动机的性能和效率。
随着航空业的发展和需求的提高,对于发动机的要求也越来越高,涡轮叶片的精密成形技术显得尤为重要。
在过去的几十年里,涡轮叶片的制造技术已经取得了长足的进步,包括材料的优化和加工工艺的改进。
随着飞行速度的提高和环保要求的增加,传统的涡轮叶片制造技术已经难以满足对高性能和高精度的要求。
研究涡轮叶片精密成形技术成为当前航空发动机领域的热点之一。
通过精密成形技术,可以实现涡轮叶片的高精度、高效率的制造,提高发动机的性能和可靠性。
涡轮叶片精密成形技术还可以减少材料浪费和能耗,降低制造成本,符合航空工业的可持续发展要求。
深入研究航空发动机涡轮叶片精密成形技术的背景意义重大,能够为航空领域的技术进步和发展提供重要支持和保障。
1.2 研究意义航空发动机涡轮叶片精密成形技术的研究意义在于提高航空发动机的性能和效率,进一步推动航空工业的发展。
随着航空业的快速发展,对涡轮叶片精密成形技术的要求也越来越高。
研究该技术能够提高航空发动机的性能和可靠性,减少能源消耗和碳排放,从而符合节能减排的国际趋势。
涡轮叶片是航空发动机的关键部件之一,其质量和制造工艺直接影响整个发动机的工作效率和安全性。
航空发动机涡轮叶片精密成形技术分析
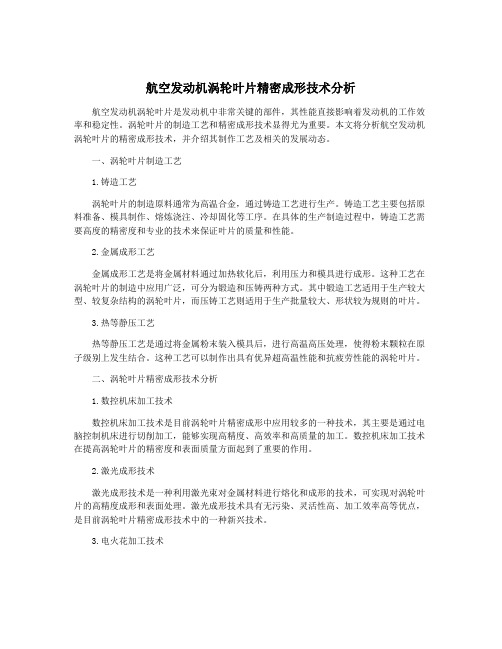
航空发动机涡轮叶片精密成形技术分析航空发动机涡轮叶片是发动机中非常关键的部件,其性能直接影响着发动机的工作效率和稳定性。
涡轮叶片的制造工艺和精密成形技术显得尤为重要。
本文将分析航空发动机涡轮叶片的精密成形技术,并介绍其制作工艺及相关的发展动态。
一、涡轮叶片制造工艺1.铸造工艺涡轮叶片的制造原料通常为高温合金,通过铸造工艺进行生产。
铸造工艺主要包括原料准备、模具制作、熔炼浇注、冷却固化等工序。
在具体的生产制造过程中,铸造工艺需要高度的精密度和专业的技术来保证叶片的质量和性能。
2.金属成形工艺金属成形工艺是将金属材料通过加热软化后,利用压力和模具进行成形。
这种工艺在涡轮叶片的制造中应用广泛,可分为锻造和压铸两种方式。
其中锻造工艺适用于生产较大型、较复杂结构的涡轮叶片,而压铸工艺则适用于生产批量较大、形状较为规则的叶片。
3.热等静压工艺热等静压工艺是通过将金属粉末装入模具后,进行高温高压处理,使得粉末颗粒在原子级别上发生结合。
这种工艺可以制作出具有优异超高温性能和抗疲劳性能的涡轮叶片。
二、涡轮叶片精密成形技术分析1.数控机床加工技术数控机床加工技术是目前涡轮叶片精密成形中应用较多的一种技术,其主要是通过电脑控制机床进行切削加工,能够实现高精度、高效率和高质量的加工。
数控机床加工技术在提高涡轮叶片的精密度和表面质量方面起到了重要的作用。
2.激光成形技术激光成形技术是一种利用激光束对金属材料进行熔化和成形的技术,可实现对涡轮叶片的高精度成形和表面处理。
激光成形技术具有无污染、灵活性高、加工效率高等优点,是目前涡轮叶片精密成形技术中的一种新兴技术。
3.电火花加工技术电火花加工技术是利用电脉冲放电的原理,通过在工件表面产生高温高压的等离子体进行加工,可以实现对涡轮叶片的微细加工和表面处理。
电火花加工技术具有高精度、高表面质量和加工难度低的特点,适用于对涡轮叶片的精密加工。
以上介绍的技术只是涡轮叶片精密成形技术中的一部分,随着科技的不断发展,会有更多更先进的技术不断涌现,为涡轮叶片的精密成形提供更多可能。
- 1、下载文档前请自行甄别文档内容的完整性,平台不提供额外的编辑、内容补充、找答案等附加服务。
- 2、"仅部分预览"的文档,不可在线预览部分如存在完整性等问题,可反馈申请退款(可完整预览的文档不适用该条件!)。
- 3、如文档侵犯您的权益,请联系客服反馈,我们会尽快为您处理(人工客服工作时间:9:00-18:30)。
早在1965年即着手研究将CAD/CAM技术应用于航空燃气涡轮发动机的设计/制造中。1968年开发涡轮叶型设计系统TADSYS,使工程分析时间缩短了5/6,提高了设计质量,增强了工程师的判断能力。1974年进一步发展为包括气动设计在内的交互式涡轮设计系统。陆续开发出压气机设计系统CAMD,发动机结构处理系统STAEBC,后来又启动了以用户满意度为核心的Q+(Qulity Plus)工程,并开始采用团队(Team)的形式来管理发动机全生命周期内的一切经济技术活动,目前已经发展成为以并行工程为核心的集成产品开发(Integrated Product Development,IPD),即运用并行工程思想,以信息集成为基础,把设计制造、用户支持等产品开发的各个环节集成到一个团队中,通过不同专业间持续不断的交流来减少重复设计,提高设计质量。
2.2 RR公司
20世纪60年代中期,开始在叶片的设计中应用CAD技术,完成了气动分析、应力分析、振动分析和造型设计,并将几何模型存储在数据库中用于加工检验。80年代中期,建成了关键零件的设计计算系统,将CAD技术扩展到了详细设计部门和制造部门,以CADDS为CAD三维建模软件,开发了RADIAL数据库作为CAD/CAM和技术系统的中心几何图档系统。80年代末期,实施发动机的并行工程,基于产品定义、设计过程定义和产品信息支持,建立了协同的计算机工作环境,具体进行了3-D离心压缩机叶轮优化。
航空发动叶片CAD技术综述
pressure and high load conditions, but also with high efficiency, small size and low weight characteristics.
This paper introduces the major aero-engine blades CAD technology.
的产品,既要工作在高温、高压和高负荷的条件下,又要具有高效率、小体积和低重量的特点。因此,航空发动机叶片设计问题受到行业内的重点关注。
2.国外航空发动机CAD技术简介
2.1 GE公司
20世纪60年代后期开始了CAD技术在航空发动机研发中的应用,1980年建立了飞机发动机部门的CIMS,使生产率提高、成本降低。1985年,在发动机设计优化技术基础上,着手开发了一个用于设计优化、自动化集成优化的软件平台Engineous,将Engineous与自主研发的涡轮设计软件和非设计状态分析系统TDOD、压气机设计软件CUS等集成,在压气机和涡轮的国内已开始有关这方面的研究开发工作,但没形成系列化产品。2000年海尔集团与哈尔滨工业大学,共同组建机器人技术有限公司。2002年哈尔滨工业大学机器人研究所成功研制出智能吸尘机器人。浙江大学早在1996年之前就开始了智能吸尘机器人的研究,在路径规划算法、多传感器信息融合等技术领域取得了一定的成果。其他一些国内知名大学和自动化研究所等科研单位也陆续涉足吸尘机器人领域并先后制造出了自己的试验样机。
3.2 我国的APTD计划
在吸取美国IHPTET计划的成功经验的基础上,我国推出了APTD(Advanced Propulsion Technologies Demonstration,航空推进技术验证)计划。APTD是国家为发展先进航空发动机而推动的一项综合的系统性工程,是一项不针对具体型号的发动机技术推进计划。希望通过APTD计划能形成一套完整的以现代信息化手段作为平台的体系标准,然后在整个航空发动机设计发展过程中不断地运用。在APTD计划中,将航空发动机看作整个飞机的子系统,即将其作为飞机的部件来综合考虑,进行发动机先进航空推进技术的研究。
3.航空发动机叶片CAD技术发展及问题分析
我国的航空发动机研制能力亟需提高。当前,我国航空发动机在研制水平上与国外发达国家尚有明显差距。西方国家的公司3年就可以研制出发动机,即从确定一个型号立项到发动机整机出来,而国内搞的两型发动机都是用时18年,花了西方国家6倍的时间,差距巨大。美国在涡轮发动机的CAD技术研究方面走在了世界前列。
3.3 航发叶片CAD技术问题分析
我国航空发动机叶片的设计,在产品结构建模方面经历了从二维手工制图到二维计算机制图,再到三维实体建模的转变;在性能分析和验证上经历了从物理样机验证分析到与计算机辅助工程相结合的数字样机的转变。航空发动机叶片的设计,是航空发动机的虚拟样机的关键部分之一,是典型的多环节、多学科、多部门协作的功能和结构都比较复杂的产品。以涡轮叶片为例,其结构的方案设计流程如图1所示。
Key Words:Aero-engine, Blades, CAD
1.引言
航空发动机是飞机的“心脏”。航空发动机研制技术复杂,投资巨大,周期长。各国航空发动机行业在突破航空发动机设计技术、材料科学技术和制造技术的同时,广泛采用CAD技术,大力推进产品的信息化。航空发动机叶片是航空燃气涡轮发动机中的关键零件,其中的高压涡轮叶片更是被誉为“现代制造业皇冠上的明珠”,不仅因为其单个产品上万美元的价值,更因其集中体现了各项性能设计要求之间的矛盾。航空发动机叶片属于功能和结构都比较复杂
3.1 美国的IHPTET计划
1988年美国制定并实施了IHPTET(The Integrated HighPerformance Turbine EngineTechnology,综合高性能涡轮发动机技术)计划,其中一个很重要的任务就是开展推进系统数值仿真计划(Numerical Propulsion System Simulation, NPSS),该计划的主要目标是通过高度可靠的多学科综合计算机仿真达到高度的系统分析能力,以提高发动机设计质量,降低研制成本。该计划在1997年实现了发动机的一维仿真,1999年实现发动机的二维仿真,计划在2010年实现三维动态多学科仿真,并最终实现飞机/发动机综合仿真。据称,这一计划一旦实现,美国航空发动机的设计水平将实现一个新的飞跃,预计可使发动机的研制成本再降低40%。