开口裂纹检测
铸件的五种测量方法

铸件的五种测量方法对于铸件的内部缺陷,常用无损检测方法是射线检测和超声检测。
其中射线检测效果最好,它能够得到反映内部缺陷种类、形状、大小和分布情况的直观图像,但对于大厚度的大型铸件,超声检测是很有效的,可以比较精确地测出内部缺陷的位置、当量大小和分布情况。
1、射线检测射线检测,一般用X射线或γ射线作为射线源,因此需要产生射线的设备和其他附属设施,当工件置于射线场照射时,射线的辐射强度就会受到铸件内部缺陷的影响。
穿过铸件射出的辐射强度随着缺陷大小、性质的不同而有局部的变化,形成缺陷的射线图像,通过射线胶片予以显像记录,或者通过荧光屏予以实时检测观察,或者通过辐射计数仪检测。
其中通过射线胶片显像记录的方法是最常用的方法,也就是通常所说的射线照相检测,射线照相所反映出来的缺陷图像是直观的,缺陷形状、大小、数量、平面位置和分布范围都能呈现出来,只是缺陷深度一般不能反映出来,需要采取特殊措施和计算才能确定。
现在出现应用射线计算机层析照相方法,由于设备比较昂贵,使用成本高,目前还无法普及,但这种新技术代表了高清晰度射线检测技术未来发展的方向。
此外,使用近似点源的微焦点X射线系统实际上也可消除较大焦点设备产生的模糊边缘,使图像轮廓清晰。
使用数字图像系统可提高图像的信噪比,进一步提高图像清晰度。
2、超声检测超声检测也可用于检查内部缺陷,它是利用具有高频声能的声束在铸件内部的传播中,碰到内部表面或缺陷时产生反射而发现缺陷。
反射声能的大小是内表面或缺陷的指向性和性质以及这种反射体的声阻抗的函数,因此可以应用各种缺陷或内表面反射的声能来检测缺陷的存在位置、壁厚或者表面下缺陷的深度。
超声检测作为一种应用比较广泛的无损检测手段,其主要优势表现在:检测灵敏度高,可以探测细小的裂纹;具有大的穿透能力,可以探测厚截面铸件。
其主要局限性在于:对于轮廓尺寸复杂和指向性不好的断开性缺陷的反射波形解释困难;对于不合意的内部结构,例如晶粒大小、组织结构、多孔性、夹杂含量或细小的分散析出物等,同样妨碍波形解释;另外,检测时需要参考标准试块。
五大常规无损检测技术之一:渗透检测(PT)的原理和特点

五大常规无损检测技术之(PT)的原理和特点渗透检测(Penetrant Testing ),业内人士简称PT,是工业无损检测Nondestructive Testing )应用最早的无损检测方法,由于渗透检测简单易操作,其在现代工业的各个领域都有广泛的应用。
渗透检测主要的应用是检查金属(钢、铝合金、镁合金、铜合金、耐热合金等) 和非金属(塑料、陶瓷等)工件的表面开口缺陷,例如表面裂纹等。
工业产品在制造和运行过程中,可能在表面产生宽度零点几微米的表面裂纹,断裂力学研究表明,在恶劣的工作条件下,这些微细裂纹都会是导致设备破坏的裂纹源。
渗透检测是五大常规无损检测技术之一,其他四种是: 超声检测( UltrasonicTesting ): A型显示的超声波脉冲反射法、射线检测(Radiographic Testing ): 射线照相法、磁粉检测( Magnetic Particle Testing ) 、涡流检测( EddyCurrent Testing ) 。
按照不同特征,可将渗透检测分为多种不同的方法:按显示材料,分为荧光法(Fluoresce nt)和非荧光法(Non-Fluoresce nt)。
前者称为“荧光渗透检测”,后者称为“着色渗透检测”。
典型的荧光渗透检测缺陷示意图。
(图片来源于网络) 肉眼无法察觉的微裂纹,经荧光渗透检,在紫外线灯的照射下,黄绿色荧光格外渗透检测原理渗透检测,本质上是利用液体的表面能。
(a)全鮒煤(a ) 0 =0°全部润湿;(b ) 0<90°,部分润湿;(c ) 0>90°,不润湿。
对某一液体而言,表面张力越小,当液体在界面铺展时克服这个力做功越少, 则 润湿效果越好。
醒目,如下图所示: "—二"■/■ n" ■厂■> -r --- V.当液体和固体界面接触时会出现以下三种现象,B 称为接触角。
利用激光超声纵波的衍射信号测量开口裂纹

第51卷 第1期 激光与红外Vol.51,No.1 2021年1月 LASER & INFRAREDJanuary,2021 文章编号:1001 5078(2021)01 0009 06·激光应用技术·利用激光超声纵波的衍射信号测量开口裂纹宋 艳1,马世榜2(1.郑州信息科技职业学院,河南郑州450001;2.南阳师范学院机电工程学院,河南南阳473061)摘 要:激光超声的纵波声场在工件内部各个方向均有分布,相比于横波和表面波,纵波最先到达开口裂纹处,随后发生衍射以及产生波型转换现象。
若提取相应含有开口裂纹信息的超声波信号,便能够达到缺陷识别的目的。
基于烧蚀机制下激光超声纵波声场的分布特点,分析了衍射纵波信号的时间及相位特征,并给出了裂纹参数的表达式。
建立了含开口裂纹工件的二维有限元模型,根据衍射纵波的渡越时间计算了开口裂纹的深度并进行了对比。
同时还探讨了衍射纵波的相位反转现象,为检测过程中衍射纵波的识别提供了依据。
最后对开口裂纹进行了激光超声测量实验,验证了利用激光超声纵波的衍射信号测量开口裂纹的可行性。
关键词:激光超声;纵波;衍射信号;开口裂纹中图分类号:TN247 文献标识码:A DOI:10.3969/j.issn.1001 5078.2021.01.002MeasurementofopeningcracksusingdiffractionsignaloflaserultrasoniclongitudinalwaveSONGYan1,MAShi bang2(1 ZhengzhouVocationalCollegeofInformationTechnology,Zhengzhou450001,China;2 SchoolofMechanicandElectronicEngineering,NanyangNormalUniversity,Nanyang473061,China)Abstract:Laserultrasoniclongitudinalwavesoundfieldisdistributedinalldirectionsinsidetheworkpiece Comparedtoshearwaveandsurfacewave,longitudinalwavereachestheopeningcrackfirst,followedbydiffractionandwavemodeconversion Ifthecorrespondingultrasonicsignalwhichcontainsthecrackinformationoftheopeningcrackisextracted,thepurposeofdefectidentificationcanbeachieved Basedonthedistributioncharacteristicsoftheultrasoniclongitudinalwavesoundfieldgeneratedbylaserablation,thetimeandphasecharacteristicsofthediffractedlongitudinalwaveareanalyzed,andtheexpressionofthecrackdepthisgiven Atwo dimensionalfiniteelementmodelforthesamplewithanopencrackisestablished,andthedepthoftheopencrackiscalculatedbasedonthetimeofflightofthediffractivelongitudinalwave Atthesametime,thephenomenonofphaseinversionofdiffractivelongitudinalwaveisdiscussed,whichcanprovideabasisfortheidentificationofdiffractivelongitudinalwaveduringthedetectionprocess Finally,alaserultrasonicmeasurementexperimentisperformed;thetestresultsshowthatitisfeasibletousethediffractionsignaltomeasuretheopencrackKeywords:laserultrasound;longitudinalwave;diffractionsignal;opencrack基金项目:河南省科技攻关项目(No 192102110200);河南省高校重点科研基金项目(No 18B460012)资助。
HXD3型车轴压装状态裂纹检测方法

HXD3型车轴压装状态裂纹检测方法发布时间:2022-12-01T09:30:56.788Z 来源:《中国科技信息》2022年第33卷第15期作者:李忠[导读] 本文通过对HXD3型车轴卸荷槽磁痕分析,利用超声检测对压装状态下的车轴卸荷槽处进行无损检测。
作者姓名:李忠成文时间:二○二一年九月九日HXD3型车轴压装状态裂纹检测方法李忠中车大连机车车辆有限公司辽宁大连 116022摘要本文通过对HXD3型车轴卸荷槽磁痕分析,利用超声检测对压装状态下的车轴卸荷槽处进行无损检测。
采用超声小角度探头配合直探头的方法最终实现在不拆解车轮情况下裂纹检出。
关键词磁粉检测超声检测卸荷槽磁痕1 前言2020年3月,某配属检修段在对HXD3型机车开展2C4修程时,发现HXD3型机车第1位驱动装置车轴轮座存在裂纹问题。
针对驱动装置车轴轮座存在裂纹问题进行深入分析,经机车驱动装置车轴拆解研究,磁粉检测确认该车轴轮座部位存在磁痕显示,磁痕位置处于轮座卸荷槽边缘位置。
经核查发现车轴卸荷槽内两侧存在带状条纹,如图1-图4所示。
经干法连续法磁粉检测发现非齿侧轮座卸荷槽位置存在微弱聚磁现象。
后对其他车轴进行磁粉检测发现磁痕特征基本符合:距离齿侧、非齿侧卸荷槽边缘,磁痕显示圆周条状断续存在,,缺陷深度0.1-0.5mm,如图5-图6所示。
针对车轴磁痕显示的原因从HXD3型机车运行条件、牵引吨位、转向架结构形式、驱动装置悬挂方式、轮轴受力状态等方面进行了多次研究论证,结合前期HXD3/HXD3C型机车车轴轮座裂纹的磁痕显示特征,上述车轴磁痕特征与其具有高度相似性,因此初步判定磁痕显示为裂纹引起。
同时将判定存在裂纹的车轴进行宏观金相检验,检验结果显示:疲劳裂纹(穿晶裂纹),其缺陷形态如图7所示。
其余裂纹均为表面开口较大,向轮座内侧延伸,顶端细而尖,有进一步延伸趋势。
图7磁痕显示部位宏观金相检验为确保机车运用安全,需研究在段运用机车的普查方案。
裂纹柔度法 测残余应力

裂纹柔度法测残余应力
裂纹柔度法是一种测量材料中的残余应力的方法。
它基于材料在应力作用下发生线性弹性变形的原理。
在实验中,通过在材料上加工一个裂纹,并施加一定的载荷来引起该裂纹的微小开口,然后测量该开口随载荷的变化。
根据弹性力学理论,载荷与裂纹的开口之间存在一定的线性关系。
通过对该关系进行分析,可以计算出材料中的残余应力。
具体的测量步骤如下:
1. 准备样品:选择一块符合要求的材料样品,并在其上加工一个裂纹。
裂纹的形状和尺寸需要根据具体的应用要求进行确定。
2. 施加载荷:使用适当的夹具将样品放置在测试机上,并施加一定大小的载荷。
载荷的大小应该使得裂纹的开口能够被测量,但要避免超过材料的弹性限度引起塑性变形。
3. 测量裂纹开口:使用光学测量仪器(如显微镜或光栅测量仪)来测量裂纹开口的大小。
通常会采用多次测量,以获得准确的开口数据。
4. 计算残余应力:根据裂纹开口与载荷之间的线性关系,使用弹性力学理论中的裂纹柔度公式计算出材料中的残余应力。
需要注意的是,在计算过程中要考虑材料的几何形状和弹性特性。
裂纹柔度法可以应用于不同类型的材料,包括金属、复合材料、陶瓷等。
它的优点是可以非破坏性地测量材料的残余应力,并且对样品的表面形貌没有特殊要求。
然而,该方法也有一定的局限性,例如对材料的线性弹性行为有一定的要求,不适用于有明显非线性行为的材料。
此外,由于裂纹开口的测量需要高精度的仪器,因此具备一定的技术难度。
航空器荧光渗透原理

航空器制造中使用的荧光渗透检测(Fluorescent Penetrant Inspection, FPI)是一种无损检测(Non-Destructive Testing, NDT)方法,用于检测材料表面的细微裂纹、开口缺陷等。
其基本原理包括以下几个步骤:
1.渗透阶段:
o首先,将待检测的航空器部件表面彻底清洗和除脂,然后涂抹含有荧光染料的渗透剂。
荧光渗透剂是一种能渗入表面开口裂纹和不连续处
的液体。
2.渗透时间:
o渗透剂在部件表面停留一段时间(通常是几分钟到几小时,视具体情况而定),以确保渗透剂有足够的时间进入所有可能存在的表面裂纹
和缺陷中。
3.清洗阶段:
o清洗掉部件表面多余的渗透剂,但保持裂纹或缺陷内的渗透剂。
4.显影阶段:
o在清洗过的部件表面涂上一层薄薄的荧光显影剂(开发者),显影剂能吸附并浓缩从裂纹中渗出来的渗透剂,使得裂纹在紫外灯下发出明
亮的荧光。
5.观察和检测:
o使用黑光灯(UV-A光源)照射部件表面,荧光染料在紫外线激发下会发出可见的荧光,从而使得表面的裂纹和缺陷变得非常明显和突
出,便于检测人员识别和记录。
通过荧光渗透检测,技术人员可以非常敏感地检测出航空器部件表面极其微小的裂纹和缺陷,这对于确保飞行安全和设备可靠性至关重要。
铝合金渗透探伤

铝合金渗透探伤
铝合金渗透探伤是一种无损检测方法,可以检测铝合金表面开口缺陷,如裂纹、疏松、气孔、夹渣、冷隔、折叠和氧化斑疤等,其操作步骤如下:
1.预处理:对待检测铝合金表面进行清洗,以去除表面的污垢、油脂和氧化物等杂质。
2.渗透处理:将铝合金表面涂覆上一层渗透剂,以使表面的微小缺陷能够被充分填充。
3.去除多余的渗透剂:在渗透剂渗透到表面开口缺陷中后,通过擦拭或冲洗等方法,去除铝合金表面多余的渗透剂。
4.干燥处理:将铝合金表面擦干或烘干,以避免残留的渗透剂对检测结果产生干扰。
5.显像处理:在铝合金表面涂覆一层显像剂,使渗透到表面开口缺陷中的渗透剂在毛细作用下重新被吸附到铝合金表面上来而形成放大了的缺陷图像显示。
6.结果观察:在黑光灯(荧光检验法)或白光灯(着色检验法)下观察缺陷显示,从而判断出铝合金表面是否存在开口缺陷。
陶瓷材料断裂韧性的测量标准刍议
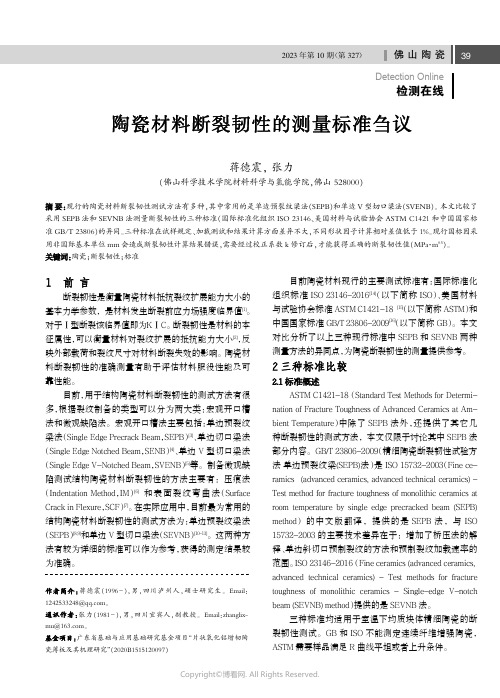
断裂韧性是衡量陶瓷材料抵抗裂纹扩展能力大小的基本力学参数,是材料发生断裂前应力场强度临界值[1]。
对于Ⅰ型断裂该临界值即为KⅠC。
断裂韧性是材料的本征属性,可以衡量材料对裂纹扩展的抵抗能力大小[2],反映外部载荷和裂纹尺寸对材料断裂失效的影响。
陶瓷材料断裂韧性的准确测量有助于评估材料服役性能及可靠性能。
目前,用于结构陶瓷材料断裂韧性的测试方法有很多,根据裂纹制备的类型可以分为两大类:宏观开口槽法和微观缺陷法。
宏观开口槽法主要包括:单边预裂纹梁法(Single Edge Precrack Beam,SEPB)[3]、单边切口梁法(Single Edge Notched Beam,SENB)[4]、单边V型切口梁法(Single Edge V-Notched Beam,SVENB)[5]等。
制备微观缺陷测试结构陶瓷材料断裂韧性的方法主要有:压痕法(Indentation Method,IM)[6]和表面裂纹弯曲法(SurfaceCrack in Flexure,SCF)[7]。
在实际应用中,目前最为常用的结构陶瓷材料断裂韧性的测试方法为:单边预裂纹梁法(SEPB)[8,9]和单边V型切口梁法(SEVNB)[10-13]。
这两种方法有较为详细的标准可以作为参考,获得的测定结果较为准确。
目前陶瓷材料现行的主要测试标准有:国际标准化组织标准ISO23146-2016[14](以下简称ISO)、美国材料与试验协会标准ASTM C1421-18[15](以下简称ASTM)和中国国家标准GB/T23806-2009[16](以下简称GB)。
本文对比分析了以上三种现行标准中SEPB和SEVNB两种测量方法的异同点,为陶瓷断裂韧性的测量提供参考。
ASTM C1421-18(Standard Test Methods for Determi-nation of Fracture Toughness of Advanced Ceramics at Am-bient Temperature)中除了SEPB法外,还提供了其它几种断裂韧性的测试方法,本文仅限于讨论其中SEPB法部分内容。
- 1、下载文档前请自行甄别文档内容的完整性,平台不提供额外的编辑、内容补充、找答案等附加服务。
- 2、"仅部分预览"的文档,不可在线预览部分如存在完整性等问题,可反馈申请退款(可完整预览的文档不适用该条件!)。
- 3、如文档侵犯您的权益,请联系客服反馈,我们会尽快为您处理(人工客服工作时间:9:00-18:30)。
开口裂纹检测
在生产过程中,由于加工不当,角钢产生裂纹,按标准规定用设备对其检测超声波检测:声源产生超声波,采用一定的方式使超声波进入工件。
超声波在工件中传播并与工件材料以及其中的缺陷相互作用,使其传播方向或特征被改变。
改变后的超声波通过检测设备被接收,并可对其进行处理和分析。
根据接收的超声波的特征,评估工件本身及其内部是否存在缺陷及缺陷的特征。
磁粉检测:铁磁材料或工件被适当磁化后,在表面或近表面缺陷处磁力线发生局部畸变,逸出工件表面形成磁极,产生漏磁场,吸附施加在工件表面上的磁粉,形成了在合适的观察条件下目视可见的缺陷磁粉图像。
磁力线与缺陷垂直时,漏磁场强,也有利于缺陷的检出,而若与缺陷平行,则无漏磁场产生,缺陷不可能被检出,故在做磁粉检测时。
工件要做整体检测,找出磁力线与缺陷垂直方向,然后对缺陷判定。
涡流检测:已知法拉第电磁感应定律,在检测线圈上接通交流电,产生垂直于工件的交变磁场。
检测线圈靠近被检工件时,该工件表面感应出涡流同时产生与原磁场方向相反的磁场,部分抵消原磁场,导致检测线圈电阻和电感变化。
若金属工件存在缺陷,将改变涡流场的强度及分布,使线圈阻抗发生变化,检测该变化可判断有无缺陷。
南京博克纳自动化系统有限公司总部位于美丽的中国古都南京,是国内专业研制无损检测仪器及设备的高科技企业。
公司致力于涡流、漏磁及各种非标设备的研制,已拥有自主研发的多项国家专利。
产品被广泛应用于航天航空、军工、
汽车、电力、铁路、冶金机械等行业。
产品出口:美国、俄罗斯、德国、新加坡、泰国、印度、香港、南非、台湾、越南、哈萨克斯坦、伊朗、日本、韩国、巴西。
BKN公司追求精益求精,坚持科技创新、坚持持续改进。
以高品质、高技术的产品和贴心服务为广大用户提供完善的产品和服务;回馈客户和社会。
BKN科技作为无损检测仪器及设备、传感器开发的公司,一直是研发和制造高质量、高性能无损检测仪器及设备的创新厂家。
我们以客户为中心提供设计服务,以满足用户的不同应用需求。
BKN公司与国内知名的院校、科研所组成了社会化科研协作网络,具有强大的研发、生产能力。
保证了BKN公司的工业无损检测技术国内、国际过硬的技术地位。
BKN将与您携手,与时俱进,为中国工业无损检测仪器及设备走向世界、走向未来而不懈奋斗!。