表面工程
表面工程
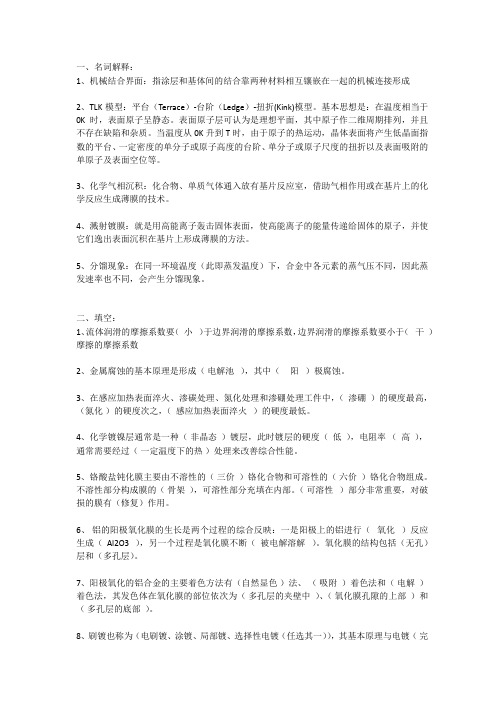
2 举例说明热喷涂和喷焊在工业上的应用? 要求写出所用材料名称 热喷涂的应用:喷涂耐腐蚀涂层,如锌、铝、不锈钢、氧化铝、氧化铬。喷涂耐磨涂层,如 铁基或镍基耐磨合金涂层、氧化铝、氧化铬,喷涂耐高温涂层,如氧化铝、氧化锆涂层。 喷焊的应用:等离子喷焊适宜对大批量零件的表面强化处理。在冶金工业中的工模具 和各 类阀门的表面强化方面,应用越来越广泛。 氧-乙炔火焰喷焊在各种工模具修复方面显示了极大的优越性 .在风机叶片等工件表面强化 方面得到了很好的应用。
2、采用表面变形原理能否获得表面纳米化组织,请举例,并画出相应试验装置图。 答:能, 例如采用表面研磨可在纯铁(或其它材料如铝,不锈钢)等表面上获得纳米化组 织,验装置图。
3、已知某种金属 A 在空气中发生氧化反应,形成 AxO 氧化物,金属的摩尔质量为 M,金属 的密度为ρ,AxO 氧化物的摩尔质量为 M’ , 氧化物的密度为 D,推导保持氧化膜完整的必 要条件,并用以上参数表示。 答:保持氧化膜完整的必要条件(或者是表面氧化膜作为保护层 的必要条件)是:形成的 氧化物的体积必须大于氧化消耗 的金属体积。
四、简答题 1、热喷涂的原理是什么?画出相应的示意图。热喷涂有哪些应用。
Hale Waihona Puke 答:原理:热喷涂是采用各种热源使涂层材料加热熔化或者半熔化,然用高速气体使涂层材 料分散细化并高速撞击到基体表面形成涂层的工艺。
应用:喷涂耐腐蚀涂层,如锌、铝、不锈钢、氧化铝、氧化铬。喷涂耐磨涂层,如铁基或镍 基耐磨合金涂层、氧化铝、氧化铬,喷涂耐高温涂层,如氧化铝、氧化锆涂层。
二、填空: 1、 流体润滑的摩擦系数要 ( 小 ) 于边界润滑的摩擦系数, 边界润滑的摩擦系数要小于 ( 干 ) 摩擦的摩擦系数 2、金属腐蚀的基本原理是形成( 电解池 ) ,其中( 阳 )极腐蚀。
表面工程技术

表面工程技术
表面工程技术是一种在材料表面上进行处理和改进的技术。
它通过改变材料表面的组成、结构和性质,以达到增加材
料表面硬度、抗磨损、抗腐蚀、提高润滑性、改善表面外
观等目的。
表面工程技术广泛应用于各个领域,包括金属加工、汽车
制造、航空航天、能源等。
常见的表面工程技术包括镀层
技术、喷涂技术、热处理技术、化学处理技术等。
镀层技术是应用最广泛的一种表面工程技术,包括电镀、
热浸镀、喷镀等方法。
它可以在材料表面形成一层具有一
定性质的金属或非金属膜,用于提高材料的耐腐蚀性、耐
磨性和美观性。
喷涂技术是通过喷涂设备将涂料或粉末涂覆在材料表面,
形成一层保护层。
这种技术可以实现材料表面的功能改善,如增加耐磨性、耐热性、耐腐蚀性等。
热处理技术是通过加热和冷却的过程改变材料的结构和性质。
热处理可以提高材料的硬度、强度和耐磨性,改善材料的机械性能。
化学处理技术是利用化学反应将溶液中的活性物质与材料表面发生反应,形成一层化合物或被改变的表面层。
这种技术可以用于清洁、除锈、改善表面润滑性等。
除了以上提到的几种常见的表面工程技术,还有其他一些特殊的技术,如氮化、氧化、表面合金化等。
这些技术能够在材料表面形成一层具有特殊性质的薄层,以满足特定的要求。
表面工程
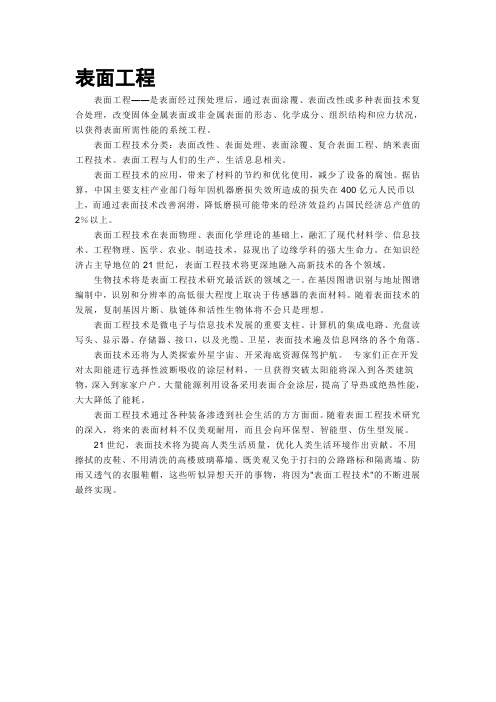
表面工程表面工程——是表面经过预处理后,通过表面涂覆、表面改性或多种表面技术复合处理,改变固体金属表面或非金属表面的形态、化学成分、组织结构和应力状况,以获得表面所需性能的系统工程。
表面工程技术分类:表面改性、表面处理、表面涂覆、复合表面工程、纳米表面工程技术。
表面工程与人们的生产、生活息息相关。
表面工程技术的应用,带来了材料的节约和优化使用,减少了设备的腐蚀。
据估算,中国主要支柱产业部门每年因机器磨损失效所造成的损失在400亿元人民币以上,而通过表面技术改善润滑,降低磨损可能带来的经济效益约占国民经济总产值的2%以上。
表面工程技术在表面物理、表面化学理论的基础上,融汇了现代材料学、信息技术、工程物理、医学、农业、制造技术,显现出了边缘学科的强大生命力。
在知识经济占主导地位的21世纪,表面工程技术将更深地融入高新技术的各个领域。
生物技术将是表面工程技术研究最活跃的领域之一。
在基因图谱识别与地址图谱编制中,识别和分辨率的高低很大程度上取决于传感器的表面材料。
随着表面技术的发展,复制基因片断、肽链体和活性生物体将不会只是理想。
表面工程技术是微电子与信息技术发展的重要支柱。
计算机的集成电路、光盘读写头、显示器、存储器、接口,以及光缆、卫星,表面技术遍及信息网络的各个角落。
表面技术还将为人类探索外星宇宙、开采海底资源保驾护航。
专家们正在开发对太阳能进行选择性波断吸收的涂层材料,一旦获得突破太阳能将深入到各类建筑物,深入到家家户户。
大量能源利用设备采用表面合金涂层,提高了导热或绝热性能,大大降低了能耗。
表面工程技术通过各种装备渗透到社会生活的方方面面。
随着表面工程技术研究的深入,将来的表面材料不仅美观耐用,而且会向环保型、智能型、仿生型发展。
21世纪,表面技术将为提高人类生活质量,优化人类生活环境作出贡献。
不用擦拭的皮鞋、不用清洗的高楼玻璃幕墙、既美观又免于打扫的公路路标和隔离墙、防雨又透气的衣服鞋帽,这些听似异想天开的事物,将因为"表面工程技术"的不断进展最终实现。
表面工程

一、名词解释(本大题共5小题,每小题4分,总计20分)1、表面工程学答:表面工程学是指为满足特定的工程需求,使材料或零部件表面具有特殊的成分、结构和性能(或功能)的化学、物理方法与工艺。
其内涵包括以下几方面:1)表面改性技术;2)表面加工技术;3)表面合成材料技术;4)表面加工三维合成技术;5)上述几个要点的组合或综合。
2、贝尔比层答:当外力作用于金属表面时,在距离表面几微米范围内,其显微组织有较大的变化。
如在抛光金属的表面组织中,在离表面约5nm的区域内,点阵发生强烈畸变,形成厚度约1~100nm的晶粒极微小的微晶层,亦称为贝尔比层。
贝尔比层具有粘性液体膜似的非晶态外观,不仅能将表面覆盖的很光滑,而且能流入裂缝或划痕等表面不规则处。
3、标准电极电位答:标准电极电位是以标准氢原子作为参比电极,即氢的标准电极电位值定位0,与氢标准电极比较,电位较高的为正,电位较低者为负。
金属浸在只含有该金属盐的电解溶液中,达到平衡时所具有的电极电位,叫做该金属的平衡电极电位。
当温度为25℃时,金属离子的有效浓度为1mol/L(及活度为1)时测得的平衡电极电位,叫做标准电极电位。
标准电极电位负值较大的金属都易失掉电子被氧化,而标准电极电位正值较大的金属都易得到电子被还原。
4、化学镀答:化学镀是指在没有外电流通过的情况下,利用化学方法使溶液中的金属离子还原为金属并沉积在基体表面,形成镀层的一种表面加工方法。
与电镀相比,化学镀的优点:1)不管零件形状如何复杂,其镀层厚度都很均匀;2)镀层外观良好,晶粒细,无孔,耐蚀性更好;3)无需电解设备及附件;4)能在非金属(塑料、玻璃、陶瓷等)以及半导体上沉积。
其缺点:溶液稳定性差,使用温度高,寿命短。
5、金属化学处理答:金属化学处理是通过化学或电化学手段,使金属表面形成稳定的化合物膜层的方法。
这种经化学处理生成的膜称之为化学转化膜。
化学成膜处理的机理是金属与特定的腐蚀液接触而在一定条件发生化学反应,由于浓度极化作用和阴极极化作用等,使金属表面生成一层附着力良好的,能保护金属不易受水和其他腐蚀介质影响的化合物膜。
表面工程技术工艺方法800种
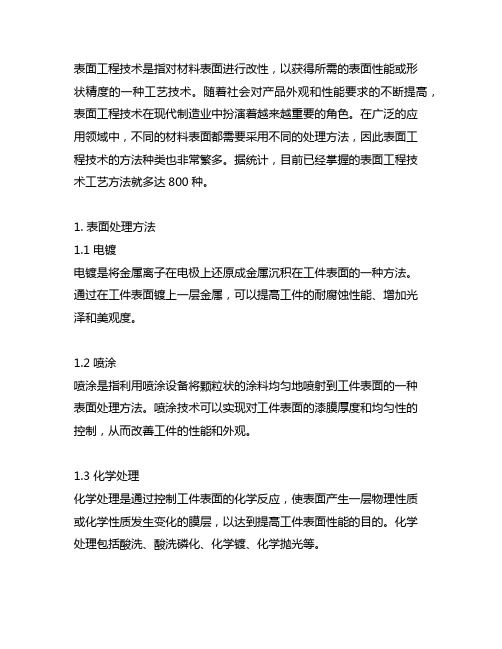
表面工程技术是指对材料表面进行改性,以获得所需的表面性能或形状精度的一种工艺技术。
随着社会对产品外观和性能要求的不断提高,表面工程技术在现代制造业中扮演着越来越重要的角色。
在广泛的应用领域中,不同的材料表面都需要采用不同的处理方法,因此表面工程技术的方法种类也非常繁多。
据统计,目前已经掌握的表面工程技术工艺方法就多达800种。
1. 表面处理方法1.1 电镀电镀是将金属离子在电极上还原成金属沉积在工件表面的一种方法。
通过在工件表面镀上一层金属,可以提高工件的耐腐蚀性能、增加光泽和美观度。
1.2 喷涂喷涂是指利用喷涂设备将颗粒状的涂料均匀地喷射到工件表面的一种表面处理方法。
喷涂技术可以实现对工件表面的漆膜厚度和均匀性的控制,从而改善工件的性能和外观。
1.3 化学处理化学处理是通过控制工件表面的化学反应,使表面产生一层物理性质或化学性质发生变化的膜层,以达到提高工件表面性能的目的。
化学处理包括酸洗、酸洗磷化、化学镀、化学抛光等。
1.4 激光处理激光处理是利用高能激光对工件表面进行熔化、氧化、磨蚀等处理的一种表面改性方法。
激光处理可以实现对工件表面微小结构的精细加工,改善工件的表面光洁度和耐磨性。
2. 表面涂层方法2.1 热喷涂热喷涂是一种利用高温或高速气流将新型材料喷射到工件表面形成涂层的方法。
热喷涂涂层具有较高的结合强度和耐磨性,可以有效地提高工件的使用寿命。
2.2 溅射溅射是利用蒸发或击打的方式将材料喷射到工件表面形成薄膜的方法。
溅射膜层具有良好的附着力和致密性,可用于提高材料的硬度和耐蚀性能。
2.3 电泳涂装电泳涂装是利用电场作用将带电涂料沉积在工件表面形成涂层的方法。
电泳涂装可以实现对工件表面涂层厚度的精准控制,使得工件表面形成均匀、光滑的涂层。
3. 表面硬化方法3.1 淬火淬火是将金属材料加热至一定温度后迅速冷却的一种表面硬化方法。
淬火可以使金属材料表面形成高硬度的马氏体组织,从而提高工件的耐磨性和抗载荷能力。
表面工程学科体系

(7)表面工程促进(cùjìn)了机械维修创新-再制造
1984年美国“技术评论”提倡旧品翻新或再生并称为“重新制 造”, 2005年美国再制造产值已超过1000亿美元,100万人 就业。
德国大众从1941年开始再制造,到2004年已再制造发动机748万 台,变速器240万台。
再制造成本节约50%,节能60%,节材70%。 再制造目前已在我国得到了广泛的重视。2009年11月,工业与信
第五页,共38页。
二.表面工程技术(jìshù)的目的及其意义 1.表面工程技术(jìshù)的 目的
第六页,共38页。
表2-1:表面(biǎomiàn)工程有关的表
第七页,共38页。
第八页,共38页。
2.表面工程技术(jìshù)的 意(义1)满足社会生产及人民生活的需要
表面工程技术应用在钟表、手饰、灯具、餐具、 家具及仿古建筑等方面。
第三页,共38页。
几种常见的金属表面处理(chǔlǐ)技 术
第四页,共38页。
2. 现代(xiàndài)表面工程的发 展历程
—1983 年英国T. Bell(英国伯明翰大学教授)在伯明翰 大学建立沃福森表面工程研究所
— Surface Engineering(1984) — 1985年,英国第一届表面工程国际会议 — 1986年,国际热处理与表面工程联合会 — 1987年,英国第二届国际会议 — 1987年12月在北京成立表面工程研究所,徐滨士
电刷镀方面,研究出摩擦电喷镀及复合 电刷镀技术
高能束应用方面,发展了激光或电子束 表面淬火、表面熔覆等技术
第二十七页,共38页。
2.发展(fāzhǎn)复合表面工程技术
单一的表面工程技术,由于(yóuyú)其固有的局限性,不能 满足日益苛刻工况条件的要求,通过最佳协同效应获得了 1+1>2 的效果,解决了一系列高新技术发展中特殊的工程技 术难题
表面工程文档

表面工程1. 简介表面工程是一种应用于工业生产中的技术,通过对材料表面进行改性或处理,可以改变材料的性质和表面特征,从而提供更好的耐磨、耐腐蚀、耐高温等性能,并增加材料的美观度和装饰性。
表面工程广泛应用于汽车工业、航空航天、电子设备制造、医疗器械、建筑等领域。
2. 表面工程的分类2.1 表面涂覆表面涂覆是将一层或多层涂料、漆膜、涂层等材料均匀地涂覆在材料表面上,形成一层保护层或功能层的处理方法。
常见的表面涂覆技术包括电镀、喷涂、浸镀等。
表面涂覆可以提高材料的耐腐蚀性能、抗磨损性能等,同时也能增加材料的装饰性。
2.2 表面喷涂表面喷涂是将材料的颗粒或粉末喷射到待处理表面上,通过热熔或化学反应使其附着在表面上形成涂层。
表面喷涂常用于金属表面的防护和保护,可以防止氧化、腐蚀和高温等影响。
2.3 表面改性表面改性是通过物理或化学方法对材料表面进行处理,从而改变其物理、化学或机械性能。
常见的表面改性方法包括阳极氧化、磨削、抛光等。
表面改性可以提高材料的硬度、耐磨性、耐腐蚀性等性能。
2.4 表面涂覆与改性的比较表面涂覆和表面改性是表面工程的两种主要方法,它们有各自的特点和适用范围。
表面涂覆主要应用于需要增加防护和装饰性的场合,例如汽车的喷漆,可以保护车身免受腐蚀和刮擦;而表面改性主要应用于需要改变材料性质和提升机械性能的场合,例如通过磨削和抛光改善金属表面的光洁度和平整度。
3. 表面工程的应用3.1 汽车工业在汽车制造过程中,表面工程技术可以使车身更加耐腐蚀、耐磨损,同时也增加了车身的装饰性。
例如,汽车车身经过喷漆和镀膜等表面涂覆技术可以防止腐蚀和刮擦,并提供车身的颜色和亮度;汽车发动机的表面经过热喷涂技术可以提高其耐磨损性和耐高温性能。
3.2 航空航天在航空航天领域,材料的轻量化和高强度是目前的发展趋势。
通过表面涂覆和改性可以增加材料的耐腐蚀性和抗磨损性,从而提高飞机和航天器材料的使用寿命和安全性。
3.3 电子设备制造表面工程在电子设备制造中起着至关重要的作用。
表面工程名词解释汇总
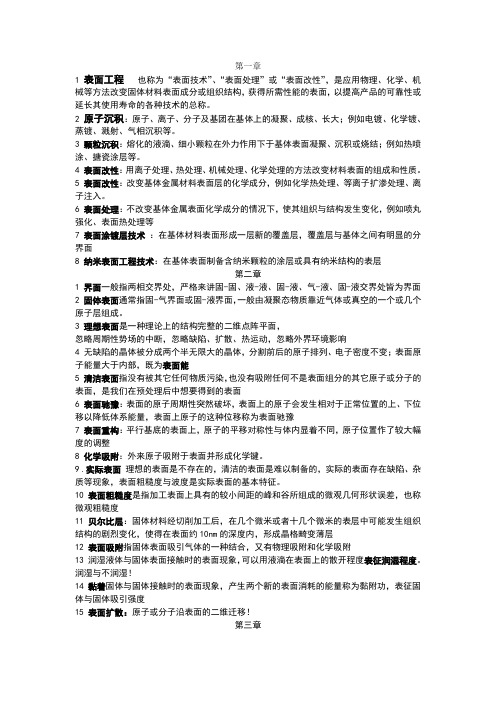
第一章1 表面工程也称为“表面技术”、“表面处理”或“表面改性”,是应用物理、化学、机械等方法改变固体材料表面成分或组织结构,获得所需性能的表面,以提高产品的可靠性或延长其使用寿命的各种技术的总称。
2 原子沉积:原子、离子、分子及基团在基体上的凝聚、成核、长大;例如电镀、化学镀、蒸镀、溅射、气相沉积等。
3 颗粒沉积:熔化的液滴、细小颗粒在外力作用下于基体表面凝聚、沉积或烧结;例如热喷涂、搪瓷涂层等。
4 表面改性:用离子处理、热处理、机械处理、化学处理的方法改变材料表面的组成和性质。
5 表面改性:改变基体金属材料表面层的化学成分,例如化学热处理、等离子扩渗处理、离子注入。
6 表面处理:不改变基体金属表面化学成分的情况下,使其组织与结构发生变化,例如喷丸强化、表面热处理等7 表面涂镀层技术:在基体材料表面形成一层新的覆盖层,覆盖层与基体之间有明显的分界面8 纳米表面工程技术:在基体表面制备含纳米颗粒的涂层或具有纳米结构的表层第二章1 界面一般指两相交界处,严格来讲固-固、液-液、固-液、气-液、固-液交界处皆为界面2 固体表面通常指固-气界面或固-液界面,一般由凝聚态物质靠近气体或真空的一个或几个原子层组成。
3理想表面是一种理论上的结构完整的二维点阵平面,忽略周期性势场的中断,忽略缺陷、扩散、热运动,忽略外界环境影响4 无缺陷的晶体被分成两个半无限大的晶体,分割前后的原子排列、电子密度不变;表面原子能量大于内部,既为表面能5 清洁表面指没有被其它任何物质污染,也没有吸附任何不是表面组分的其它原子或分子的表面,是我们在预处理后中想要得到的表面6 表面驰豫:表面的原子周期性突然破坏,表面上的原子会发生相对于正常位置的上、下位移以降低体系能量,表面上原子的这种位移称为表面驰豫7 表面重构:平行基底的表面上,原子的平移对称性与体内显着不同,原子位置作了较大幅度的调整8 化学吸附:外来原子吸附于表面并形成化学键。
- 1、下载文档前请自行甄别文档内容的完整性,平台不提供额外的编辑、内容补充、找答案等附加服务。
- 2、"仅部分预览"的文档,不可在线预览部分如存在完整性等问题,可反馈申请退款(可完整预览的文档不适用该条件!)。
- 3、如文档侵犯您的权益,请联系客服反馈,我们会尽快为您处理(人工客服工作时间:9:00-18:30)。
表面工程论文班级:金材1102班姓名:田进学号:201112030211金属搪瓷涂覆层研究摘要:概述耐磨材料的应用背景和发展现状,综述金属陶瓷和金属陶瓷涂覆层研究进展,描述了电热爆炸超高速喷涂法反应合成亚微米晶金属陶瓷涂层技术和等离子反应合成碳化物基金属陶瓷熔覆层技术的进展及其应用前景。
关键词:金属搪瓷涂覆层引言:磨损是机械零件失效的三大方式(磨损、腐蚀、断裂)之一,磨损也是工业材料和能源消耗的主要根源之一,其中麽粒磨损约占各种磨损类型的50%。
磨粒磨损通常是指处理砂土、矿石、岩石等物料时,由这类物料造成机件的磨损。
这类物料与机件表面相互作用的方式很多,有冲击、滚动、滑动和冲刷等。
关于磨粒磨损的分类,当前世界各国广泛认同的是H.S.Avery提出的分类方法,将磨粒磨损分为凿削性碰撞磨损、研碎性高应力磨损,擦伤性低应力磨损等。
对于在凿削性碰撞磨损、研碎性高应力磨损工况下工作的耐磨件,目前高铬铸铁是首选的材料。
含铬量在12%以上的高铬铸铁开发于20世纪初,1917年获得了美国专利。
随后数十年内,由于对高铬铸铁的性能了解不多而限制了其应用范围。
20世纪中期,美国国际镍公司研究开发了镍硬系列耐磨铸铁,其中,镍硬4(Ni Hard 4)于1951年获美国专利,并逐渐广泛应用于矿产品加工行业。
镍硬4的耐磨性能较好,但因其抗冲击能力欠佳而限制了其在高应力磨粒磨损条件下的应用。
20世纪60年代,美国Abex公司为改善高铬铸铁的性能进行了大量的研究工作,系统研究了Ni、Mo、Mn、Si、Cr和C等在高铬铸铁中的作用。
随后,美国ClimaxMolybdenum公司又对Mo和Cu在高铬铸铁中的作用进行了系统的研究。
20世纪80年代,美国内政部矿业局的研究中心又对高铬铸铁的热处理进行了研究,美国材料试验学会制定的“抗磨铸铁”标准ASTM A532中基本体现了上述研究成果。
我国耐磨材料每年消耗约数百万吨,并且以每年15%的速度在增长。
在水泥工业生产中,由于各种机械磨损,大量的钢材被消耗掉。
据统计,我国水泥产量约13亿吨/年,每年水泥工业消耗钢材在200万吨以上。
其中机械磨损消耗钢材占90%以上。
在电力行业,针对火电厂制粉系统中速磨煤机制造落后的情况,我国从1980年起先后从西方国家引进了RP、HP、MPS系列磨煤机制造技术,目前已有2000多台国产中速磨煤机在火电厂运行。
国内早期使用的磨煤机磨辊和磨盘采用镍硬4(含Cr 8%~9%,Ni 5.o%~6.5%,C2.6%~3.2%)制造,随后由于降低成本的需要而采用高铬铸铁替代镍硬4。
由于用高铬铸铁制造的磨辊和磨盘寿命高于镍硬4,我国已逐步将高铬铸铁取代了镍硬4。
在高铬铸铁焊接工艺获得突破后,堆焊耐磨高铬铸铁的技术在磨煤机磨辊和磨盘上得到成功应用,采用堆焊制造和修复的磨辊及磨盘的使用寿命相当于或者高于铸态的高铬铸铁磨辊(最高可达铸态高铬铸铁寿命的1.5倍)。
但由于国内煤质较差,无论是铸态还是堆焊的高铬铸铁磨辊的寿命仅为4 000~8 000 h,远达不N20 000 h以上设计寿命和磨煤机高效稳定运行的要求。
在现有耐磨合金耐磨性已接近极限的情况下,迫切需要突破现有耐磨合金材料的局限性,开发新的高耐磨复合材料技术。
综上,开发新的耐磨材料和防磨表面技术,对于减少磨损、降低钢材消耗、节约能源、促进水泥和电力等行业可持续发展,具有十分重要的意义。
一、金属陶瓷发展概述金属陶瓷是一种由金属或合金与一种或几种陶瓷相所组成的非均质复合材料。
在金属陶瓷中,陶瓷相体积分数约占15%~90%,这使得金属陶瓷既保持有陶瓷的高强度、高硬度,耐磨损,耐高温、抗氧化和化学稳定性等特性,又有较好的韧性和塑性。
金属陶瓷已成为非常重要的工具材料和结构材料,其用途极其广泛,几乎涉及到国民经济的各个部门和现代技术的各个领域,对工业的发展和生产效率的提高起着重要的推动作用。
金属陶瓷中陶瓷相通常是由高熔点氧化物(如Al2O3、ZrO2等)、碳化物(如TiC、SiC、WC等)、硼化物(如TiB2、ZrB2、CrB2等)、氮化物(如TiN、BN、Si,N等)组成。
硅化物的熔点虽高,但易与金属反应,所以在金属陶瓷的配方中较少采用。
作为金属粘结相的材料主要有Ni、Co、Fe、Mo等,它们可以单独或组合起来使用,也可以是其它金属材料,如不锈钢青铜或高温合金。
为了使金属陶瓷同时具有金属和陶瓷的优良特性,需满足以下几个主要条件:(1)金属对陶瓷相的润湿性要好。
金属与陶瓷颗粒间的润湿能力是衡量金属陶瓷组织结构与性能优劣的主要因素之一,润湿力愈强,则金属形成连续相的可能性愈大,金属陶瓷的性能愈好。
(2)金属相与陶瓷相应无剧烈的化学反应。
金属陶瓷制备时如果界面反应剧烈,形成化合物,就无法利用金属相改善陶瓷抵抗机械冲击和热震动的性能。
(3)金属相与陶瓷相的膨胀系数相差不可过大。
金属陶瓷中的金属相和陶瓷相的膨胀系数相差较大时,会造成较大的内应力而降低金属陶瓷的热稳定性。
1914年,德国人洛曼等首次将质量分数为80%~95%的难熔化合物与金属粉末混合制得了烧结金属陶瓷。
1923年,德国人施勒特尔首次制成了性能良好的烧结WC—Co材料(常称为硬质合金),WC—Co材料至今仍在国际上得到广泛应用,每年全世界市场WC—Co需求量在2万t以上。
我国2006年上半年的WC-Co产量接近8 000 t。
但钨在地壳中含量很少,只占地壳重量的0.007%。
我国钨矿储量虽为世界第一位,但总储量仅527万t(资源储量为262万t)。
在钨矿中,钨的含量通常不高(一般三氧化钨含量只有千分之几,最富的矿也不过2%~3%)。
我国钨资源中主要是白钨矿(CaWO4),其成分复杂不易开采利用;黑钨矿(Fe/MnWO4)资源由于大量开发而濒临枯竭。
我国钴矿资源十分贫乏,全国总保有储量钴约为47万t。
由于w和Co资源的短缺,促使了无钨金属陶瓷的研制与开发,迄今已历经三代。
第一代是二战期间,德国以Ni粘结TiC生产金属陶瓷;第二代是20世纪60年代美国福特汽车公司发明的添加Ni、Mo的金属陶瓷,即添加Mo到Ni粘结相中改善TiC和其它碳化物的润湿性;第三代金属陶瓷则将氮化物引入合金的硬质相,改单一相为复合相,又通过添加Co和其它元素改善了粘结相。
在碳化物陶瓷中,TiC是由c原子填充于a-Ti的密排六方八面体间隙而形成的具有面心立方结构和非化学计量比的间隙型化合物,TiC陶瓷因为具有高熔点(3 523 K),高显微硬度(28.5~32 GPa)、高强度(弹性模量350 GPa)、良好的耐磨耐蚀性和导电性而成为一种极具竞争力的材料。
近十年来,硼化物金属陶瓷的研究也得到了极大的重视。
硼化物陶瓷由于具有很高的硬度、熔点和优良的导电性、耐腐蚀性,从而使硼化物金属陶瓷成为最有发展前途的金属陶瓷。
研究表明,金属硼化物具有高的导热率和高温稳定性。
TiB2在温度超过1 100℃时其机械性能超过所有其它陶瓷材料(金刚石,立方氮化硼、碳化物,碳氮化物)。
硼化物基金属陶瓷用于需要非常耐热和耐蚀的条件下,如在与活性热气体和熔融金属接触的场合。
可用来粘结硼化物的主要金属有Fe、Ni、Co、Cr、Mo或者它们的合金。
用质量分数为0.15的SiC和ZrB2反应,这种固结的金属陶瓷可进一步增强ZrB2的抗氧化性,能经受l 900~2500℃范围内的氧化环境。
这种金属陶瓷可应用于处理熔融金属的系统,如在压铸机上压铸液态合金所用泵的叶轮和轴承、与熔融活性金属或与蒸汽接触的炉子零部件等。
金属陶瓷材料具有显著的耐高温、耐磨、耐腐蚀等优点,是当前国际上研究的热点。
为了改善陶瓷材料的强韧性,金属陶瓷材料正在由单相陶瓷向多相复合陶瓷发展、由微米级陶瓷复合材料向纳米级陶瓷复合材料发展。
二、金属陶瓷涂覆层制备工艺概述在工业磨损部件的表面上制备金属陶瓷涂覆层,可使部件既满足高耐磨损要求又具有良好的整体韧性,同时还能大幅度降低制造成本。
但是,由于金属陶瓷涂覆层的制备成本较高、工艺较复杂等原因而限制了其应用范围,水泥,火电、矿山机械中的大型磨损部件仍主要采用传统的耐磨钢铁材料。
因此,迫切需要开发低成本金属陶瓷涂覆层新产品,从而显著延长水泥、电力等行业大型磨损机械的寿命。
目前,金属陶瓷涂覆层的制备工艺主要有铸渗法,热喷涂法、粉末烧结法、熔注法、离子注渗法、堆焊法、激光熔覆法、原位合成法、电渣熔铸法等。
外加陶瓷增强体是传统金属陶瓷涂覆层的制备工艺,这类技术存在增强体易偏聚、增强体与基体之间的物理及化学性质不相容、工艺复杂,成本高等问题,从而限制了其应用范围。
与外加增强体复合工艺相比,原位反应合成具有以下优点:增强相是在基体中原位生成的热力学稳定相,与基体间相容性好,界面结合强度高;合理选择反应物的类型和配比,可有效控制原位生成增强相的种类,大小和体积分数;增强相在基体中直接生成,工艺简单,成本相对较低。
在铸渗法研究方面,20世纪90年代中期以来,国内鲍志勇,等人利用铸渗法制备出了WC颗粒增强的复合磨辊(耐磨层中WC体积分数为25%~54%),复合磨辊寿命可达高铬铸铁磨辊寿命的2倍以上。
由于磨辊尺寸大,采用该技术时需选择合理的工艺参数,以防止出现粘模、WC颗粒氧化等问题。
由于该技术的工艺较复杂(需要将对复合磨辊进行后续时效处理、退火处理、精加工等),成本较高,目前尚未得到广泛应用。
热喷涂技术可用于制备表面复合涂层,其具有生产效率高,成本低等优点,但热喷涂技术制备的涂层存在结合强度较低(涂层与基体一般为机械或半冶金结合),孔隙率较高(1%~10%)、涂层厚度一般为几百um等局限性,无法满足磨辊等大型磨损部件在严重磨损环境下长寿命工作的要求,热喷涂法制备的涂层主要用于锅炉管及叶轮的防磨防腐。
以激光为代表的高能束熔覆技术的特点是可以实现热输入的准确控制,热畸变小,成分和稀释率可控性好,可以获得组织致密、性能优越的复合材料,因而成为国内外学者的研究热点,近十几年来得到了迅速发展。
常用激光熔覆材料主要包括镍基、铁基、钴基、铜基自熔合金、以及上述合金与碳化物(WC、TiC、SiC等)颗粒组成的复合粉末以及A12o3、zro2等陶瓷材料等。
激光熔覆法主要适用于尺寸较小的部件,如缸体、阀座等。
氩弧熔覆法是近十几来较受关注的低成本焊接技术。
氩弧的能量密度介于自由电弧和压缩电弧之间,工件被氩气包围,加热、冷却过程中无氧化、烧损现象;其稀释率为5%~20%,无熔渣,一般用于焊接合金材料。
近年来,国内在将该技术拓展到制备表面复合材料的研究方面取得一定进展。
宋思利、邹增大等人将FeTi25粉末与C粉混合后预敷到金属表面,利用氩弧熔覆法制备了Fe基TiC颗粒增强的涂层,涂层中原位合成了弥散细小分布的TiC颗粒,涂层最高硬度676HV。