机械零件加工工艺的制定
机械加工工艺规程
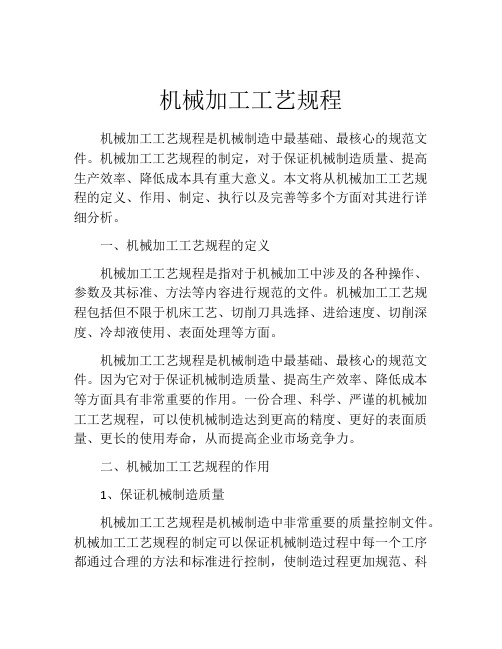
机械加工工艺规程机械加工工艺规程是机械制造中最基础、最核心的规范文件。
机械加工工艺规程的制定,对于保证机械制造质量、提高生产效率、降低成本具有重大意义。
本文将从机械加工工艺规程的定义、作用、制定、执行以及完善等多个方面对其进行详细分析。
一、机械加工工艺规程的定义机械加工工艺规程是指对于机械加工中涉及的各种操作、参数及其标准、方法等内容进行规范的文件。
机械加工工艺规程包括但不限于机床工艺、切削刀具选择、进给速度、切削深度、冷却液使用、表面处理等方面。
机械加工工艺规程是机械制造中最基础、最核心的规范文件。
因为它对于保证机械制造质量、提高生产效率、降低成本等方面具有非常重要的作用。
一份合理、科学、严谨的机械加工工艺规程,可以使机械制造达到更高的精度、更好的表面质量、更长的使用寿命,从而提高企业市场竞争力。
二、机械加工工艺规程的作用1、保证机械制造质量机械加工工艺规程是机械制造中非常重要的质量控制文件。
机械加工工艺规程的制定可以保证机械制造过程中每一个工序都通过合理的方法和标准进行控制,使制造过程更加规范、科学。
同时,机械加工工艺规程还可以限定加工参数,使得机械零件的尺寸和形状误差控制在一定的范围内,保证机械零件的质量,提高制造效率。
2、提高生产效率机械加工工艺规程对于生产效率的提升也具有非常重要的作用。
一份完整、清晰的机械加工工艺规程,可以让操作者更加容易地把握加工流程,减少操作失误和重复性工作,提高生产效率。
同时,通过对机械加工过程的规范,可以合理利用机床及切削刀具,降低能耗、物料损耗等成本。
3、降低成本机械加工工艺规程对于成本的控制也是具有重要作用的。
通过合理规划加工流程和工艺参数,可以减少物料损耗、降低能耗、扩大生产规模、提高生产效率等措施,逐步降低企业的生产成本,提高企业市场竞争力。
三、机械加工工艺规程的制定1、收集资料机械加工工艺规程的制定,首先需要收集各类资料,包括机械加工基础知识、机床参数、切削加工刀具、模具、材料性能、机械零件的图纸和加工要求等。
机械加工工艺规程的制定
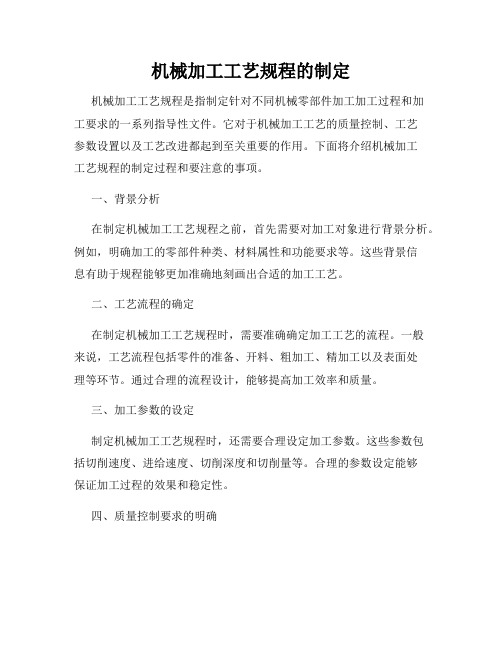
机械加工工艺规程的制定机械加工工艺规程是指制定针对不同机械零部件加工加工过程和加工要求的一系列指导性文件。
它对于机械加工工艺的质量控制、工艺参数设置以及工艺改进都起到至关重要的作用。
下面将介绍机械加工工艺规程的制定过程和要注意的事项。
一、背景分析在制定机械加工工艺规程之前,首先需要对加工对象进行背景分析。
例如,明确加工的零部件种类、材料属性和功能要求等。
这些背景信息有助于规程能够更加准确地刻画出合适的加工工艺。
二、工艺流程的确定在制定机械加工工艺规程时,需要准确确定加工工艺的流程。
一般来说,工艺流程包括零件的准备、开料、粗加工、精加工以及表面处理等环节。
通过合理的流程设计,能够提高加工效率和质量。
三、加工参数的设定制定机械加工工艺规程时,还需要合理设定加工参数。
这些参数包括切削速度、进给速度、切削深度和切削量等。
合理的参数设定能够保证加工过程的效果和稳定性。
四、质量控制要求的明确机械加工工艺规程的制定还需要明确质量控制要求。
这包括对加工零部件的尺寸、形状、表面粗糙度以及加工精度等方面的要求。
通过设定合理的质量控制要求,可以有效保证加工产品的质量。
五、工艺改进和优化一套优秀的机械加工工艺规程应该是不断改进和优化的产物。
在规程的制定过程中,需要定期对工艺进行评估和改进,以满足不同加工需求和提高加工效率。
六、培训和执行制定机械加工工艺规程后,需要进行培训和执行。
员工需要掌握规程中各项加工要求和工艺参数,并在实际操作中加以执行。
定期的培训和评估能够很好地保证规程的实施效果。
总结:机械加工工艺规程的制定是确保加工质量和效率的关键措施。
通过背景分析、工艺流程的确定、加工参数的设定、质量控制要求的明确、工艺改进和培训与执行等多个环节的合理安排,能够制定出一套完善的规程,为机械加工提供指导和保障。
在实际操作中,不断完善与优化工艺规程,不断提高员工的技能水平,才能更好地满足客户需求,推动企业的发展。
机械加工工艺路线的拟定

机械加工工艺路线的拟定1. 引言机械加工工艺路线是指在制造过程中,针对特定零件的加工工艺步骤的拟定和安排。
它是实现零件加工的关键,直接影响到产品质量和生产效率。
本文将介绍机械加工工艺路线的拟定过程及其重要性,并提出一些方法和技巧,以帮助制造企业制定高效的工艺路线。
2. 机械加工工艺路线的拟定过程机械加工工艺路线的拟定是一个复杂的过程,需要考虑多种因素,包括材料特性、工艺装备条件、工艺控制要求等。
以下是机械加工工艺路线的拟定过程的主要步骤:2.1 确定零件的加工难度首先需要对零件的几何形状、尺寸和材料进行分析,确定零件的加工难度。
加工难度包括工艺性能、切削性能和热处理性能等因素。
根据这些因素,可以初步确定合适的加工方法和工艺路线。
2.2 选择合适的工艺装备根据零件加工的特点和要求,选择合适的加工设备和工艺装备。
这些设备包括机床、刀具、夹具等。
选择合适的设备对于提高加工效率和保证加工质量非常重要。
2.3 制定切削参数根据选择的加工方法和设备,制定合适的切削参数,包括切削速度、进给量和切削深度等。
切削参数的选取将直接影响到加工过程的效率和质量。
2.4 确定工装方案根据零件的形状和特点,确定合适的工装方案。
工装的设计和使用对于提高加工精度和保证零件一致性非常重要。
2.5 设计工艺文件根据前面的步骤,编制详细的工艺文件,包括加工顺序、工艺参数、工装设计、设备要求等。
工艺文件将作为实际加工的依据,对于保证产品质量和提高生产效率非常重要。
3. 机械加工工艺路线的重要性机械加工工艺路线的拟定对于制造企业来说具有重要的意义。
以下是几个方面的重要性:3.1 提高生产效率合理的工艺路线可以最大限度地利用设备和资源,提高生产效率。
通过合理的工艺路线规划,可以最大限度地减少加工次数和加工时间,实现生产的高效率。
3.2 保证产品质量合理的工艺路线可以确保产品在加工过程中的质量。
通过精确的工艺参数和工装设计,可以保证产品的尺寸精度和表面质量。
零件工艺路线的制定

零件工艺路线的制定
§1 粗基准的选择 §2 精基准的选择 §3 工件的定位及装夹 §4 工艺路线的制定
§1 粗基准的选择
在机械制造中加工零件和装配机器所采用的各种基准,总称为工艺基准。 按其功用的不同,可分为定位基准,测量基准及装配基准三种。
以毛坯上未经加工过表面做基准,这种定位基准称为粗基准。粗基准 的选择原则如下:
一、 各表面不需要全部加工时,应以不加工的面做粗基准。
二、 所有表面都要加工的工件,应以加工余量较小的表面作为 粗基准。
三、 尽量选择光洁、平整和幅度大的表面做粗基准。
四、 粗基准只能使用一次,尽量避免重复使用。因粗基准的表面粗糙度 值大,精度又低,不能保证两次装夹的位置相同。
§2 精基准的选择
以已加工表面作为定位基准,称为精基准。精基准选择的原则如下:
(二) 最终热处理
最终热处理包括淬火、渗碳淬火和渗氮处理等。
1.淬火 目的是提高材料的硬度、强度和耐磨性。用于中碳结构钢和工具钢,当工件淬
火后,表面硬度高,除磨削外,一般不能进行切削加工,因此淬火一般安排在半精 加工之后,磨削加工之前。
2.渗碳淬火 低碳钢(15钢、15Cr、20钢、20Cr)经渗碳后,表层碳的质量分数增加到0.85
来找正工件在机床上的位置,然后将工件夹紧。
如上图所示为在车床上加工法兰盘时,用直接找正法进行装夹的情况, 先用划针检查法兰盘的端面1和外圆2,使之分别与主轴旋转中心垂直和同心。 若位置不正,则可用木锤或铜锤敲正,找正之后将法兰盘夹紧。
直接找正装夹的精度完全取决于工人的经验、技术水平及所用的工具, 此外,找正工件所费时间很长,有时甚至比用于加工的时间还多,因此这种 方法一般只适用于单件小批生产中形状简单的零件。
(机械制造行业)第三章机械加工工艺规程的制定

第三章机械加工工艺规程的制定§3-1基本概念一.生产过程与工艺过程(一)生产过程从原材料到机械产品出厂的全部劳动过程。
包括:1)生产技术准备过程2)毛坯的制造3)零件的机械加工及热处理4)产品的装配、检验、试车、油漆、包装等。
5)产品的辅助劳动过程直接生产过程被加工对象的尺寸、形状或性能、位置产生一定的变化。
如:零件的机械加工、热处理、装配等。
间接生产过程:不使加工对象产生直接变化。
如:工装夹具的制造、工件的运输、设备的维护等。
(二)机械加工工艺过程是生产过程的一部分,是对零件采用各种加工方法,直接用于改变毛坯的形状、尺寸、表面粗糙度以及力学物理性能,使之成为合格零件的全部劳动过程。
工艺:使各种原材料、半成品成为成品的方法和过程工艺过程:在生产过程中,凡是改变生产对象的形状、尺寸、相对位置和性质等,使其成为成品和半成品的过程。
二.机械加工工艺过程的组成1.工序一个或一组工人,在一台机床或一个工作地点对一个或同时对几个工件所连续完成的那一部分工艺过程。
划分工序的主要依据:工作地点是否改变和加工是否连续完成。
同一零件,同样的加工内容可以有不同的工序安排。
如图所示的阶梯轴的加工:加工内容:1.加工小端面 2.小端面钻中心孔3.加工大端面 4.大端面钻中心孔5.车大端外圆 6.对大端倒角7.车小端外圆8.对小端倒角9.精车外圆10.铣键槽11.去毛刺工序1:加工内容1到9——车床工序2:加工内容10、11——铣床(手工去毛刺)工序1:加工内容1、2、7、8—加工小端工序2:加工内容3、4、5、6—加工大端工序3:加工内容9工序4:加工内容10、11 第三种工序安排:工序1:加工内容:1、2、3、4—铣两端面打中心孔工序2:加工内容:5、6、7、8—仿形车外圆、倒角工序3:加工内容:9—精车外圆工序4:加工内容:1—铣键槽工序5:加工内容:11—去毛刺2、安装如果在一个工序中要对工件进行几次装夹,则每次装夹下完成的那部分加工内容称为一个安装。
课程设计-零件的机械加工工艺规程的编制及工装设计

课程设计-零件的机械加工工艺规程的编制及工装设计摘要本文旨在介绍零件机械加工工艺规程的编制方法和工装设计要点,为机械加工领域的学生和工程师提供参考。
引言机械加工工艺规程的编制是确保加工质量、提高生产效率的关键环节。
合理的工艺规程和工装设计能够显著提升加工精度和生产效率。
第一章:零件加工工艺规程编制1.1 零件分析对零件的几何形状、尺寸、材料等进行详细分析。
1.2 加工工艺路线确定根据零件特点确定加工顺序和加工方法。
1.3 工艺参数选择选择合适的切削参数,如切削速度、进给速度、切削深度等。
1.4 工艺文件编制编制工艺卡片、工艺流程图等工艺文件。
第二章:工装设计2.1 工装设计原则介绍工装设计的基本原则,如定位精度、夹紧稳定性等。
2.2 夹具设计根据加工工艺要求设计夹具,确保零件的定位和夹紧。
2.3 刀具选择选择合适的刀具,考虑刀具材料、类型、尺寸等因素。
2.4 量具与检测选择合适的量具,制定检测方案,确保加工质量。
第三章:工艺规程编制实例3.1 零件选择选择一个具体的零件作为工艺规程编制的实例。
3.2 工艺路线分析对选定零件的加工工艺路线进行详细分析。
3.3 工艺参数确定确定加工过程中的工艺参数。
3.4 工艺文件编制编制该零件的工艺卡片和工艺流程图。
第四章:工装设计实例4.1 夹具设计针对选定零件的加工特点,设计相应的夹具。
4.2 刀具选择与设计选择和设计适合该零件加工的刀具。
4.3 量具选择与检测方案选择适合的量具,并制定检测方案。
第五章:质量控制与优化5.1 加工质量控制制定加工过程中的质量控制措施。
5.2 工艺优化分析工艺过程中的瓶颈,提出优化建议。
5.3 成本控制考虑加工成本,提出成本控制措施。
结论机械加工工艺规程的编制和工装设计是确保加工质量和效率的重要环节。
通过合理的工艺设计和精确的工装配合,可以有效提升零件加工的精度和生产效率,为企业创造更大的价值。
机械零件加工工艺
机械零件加工工艺机械零件加工工艺机械是我们生活中不可或缺的一部分,在现代工业中,机械零件的加工也是十分重要的一环。
机械零件加工工艺是指将原材料加工成为特定形状、尺寸和精度的零件的技术过程。
机械零件加工工艺包含着多个环节,这些环节的顺序和安排对于成功的加工具有至关重要的影响。
本文旨在介绍机械零件加工工艺的流程及常用工具设备的基本原理。
一、机械零件加工工艺的流程1.零件设计与制图:在机械零件的加工工艺中,首先需要进行零件的设计与制图。
设计师需要根据机械的功能需求来制定零件设计,同时要考虑到材料、尺寸、工艺可行性以及制造成本等方面的因素。
完成零件设计之后,需要进行制图操作。
制图操作的目的是把设计好的零件展开成为一组平面图,以便进行加工时的参考使用。
2.原材料准备:机械零件加工工艺的第二步就是原材料的准备。
原材料的准备包括选材、锯切、刨削等操作。
对于不同种类的原材料,需要采取不同的处理方法。
例如,对于金属材料,需要采用对应的锯切刀具和刨削设备来进行处理。
3.粗加工:完成原材料的准备之后,需要进行粗加工。
粗加工是指将原材料进行初步形状加工,主要是为了方便后续加工操作。
在粗加工环节中,需要采用铣床、车床等设备来进行操作,以使得原材料得到相应的切削、钻孔、成型等处理。
4.精加工:在完成粗加工后,需要进行精加工的环节。
精加工是指将原材料进行精细加工,使得零件的尺寸、形状和表面精度得到保证。
在精加工环节中,通常需要采用磨床、钻床等高精度设备进行操作,以保证机械零件的高精度要求。
5.热处理与表面处理:完成精加工之后,需要进行热处理和表面处理,以保证机械零件的质量和使用寿命。
热处理是指对机械零件进行热处理,使其具有适当的硬度和强度。
表面处理是指对机械零件进行表面处理,以提高零件的耐磨性和抗腐蚀性。
常见的表面处理包括电镀、喷涂和阳极氧化等。
6.检验与组装:最后环节就是对机械零件进行检验和组装。
检验的目的是为了验证机械零件的尺寸精度和表面质量是否符合要求。
机械零件的加工工艺
机械零件的加工工艺机械零件的加工工艺是指将原材料通过一系列的工艺过程,进行切削、成形、联接等操作,最终得到符合设计要求的零件。
机械零件的加工工艺涉及到材料选择、工艺规程、加工工艺参数的确定等方面。
下面将从机械零件加工的基本步骤、常用加工方法和工艺参数的选择等方面进行详细介绍。
1. 机械零件加工的基本步骤:机械零件加工的基本步骤包括工艺准备、加工操作和工艺检验三个方面。
(1)工艺准备:包括依据设计图纸和工艺要求,选择合适的材料、设备和工具,制定加工工艺规程,并依据工艺规程制作工艺文件,如加工工序卡和工艺路线。
(2)加工操作:按照工艺文件的要求,进行机械零件的加工操作。
具体包括切削加工、成形加工、联接加工等过程。
在加工操作过程中,需要根据工艺文件和现场实际情况,灵活控制机床和工艺参数,保证加工质量和工艺效率。
(3)工艺检验:通过对加工过程和加工结果的检验,验证加工质量是否符合要求。
主要包括工艺过程中的工件检测、工艺参数记录、加工精度检验等。
通过工艺检验,及时发现问题和改进不足,提高加工质量。
2. 常用加工方法(1)切削加工:包括车削、铣削、钻削、磨削等。
切削加工是利用刀具对工件进行材料的切削,达到工件形状和精度要求的加工方法。
(2)成形加工:包括冲压、锻造、拉伸等。
成形加工是通过对工件施加压力,使其发生塑性变形,从而得到所需形状的加工方法。
(3)联接加工:包括焊接、铆接、螺纹连接等。
联接加工是将多个零件通过一定的方式连接在一起,形成一个整体的加工方法。
3. 工艺参数的选择在机械零件加工中,选取合适的工艺参数对于加工质量和效率有着重要影响。
影响工艺参数的因素包括材料的物理性质、切削刃具的材料和形状、机床类型和切削速度等。
(1)刀具材料选择:合理选择刀具材料能够提高切削刃具的硬度、耐磨性和耐冲击性。
常用的刀具材料有高速钢、硬质合金和陶瓷等。
(2)刀具形状选择:合理选择刀具的形状和刃角能够适应不同加工工艺的要求。
机械加工工艺规程的制订
机械加工工艺规程的制订1.工艺规程的作用①工艺规程是指导生产的主要技术条件;②工艺规程是生产组织和生产管理工作的依据;③工艺规程是新建或扩建工厂及车间的基本资料。
2.工艺规程的设计原则①技术上的先进性②经济上的合理性③良好的劳动条件3.制订工艺规程所需的原始资料①产品的全套装配图和零件工作图②产品验收的质量标准③产品的生产纲领④毛坯资料⑤现场生产条件⑥工艺规程设计时应尽可能多了解新工艺、新方法4.工艺规程的制订步骤4.1零件的工艺分析1)零件技术要求分析①加工表面的尺寸精度②主要加工表面的形状精度③主要表面之间的相互位置精度④各加工表面粗糙度以及表面质量方面的其它要求⑤热处理及其它技术要求2)对零件图具体技术分析:①零件的视图、尺寸、公差和技术要求是否齐全②零件图所规定加工要求是否合理③零件的选材是否恰当3)零件结构工艺性分析①机械零件的结构,由于使用要求不同而具有各种形状②在分析零件的结构时,不仅要注意各物体表面本身特征,而且要注意这些表面的不同组合③在研究零件结构时,要注意审查零件的结构工艺性4.2选择毛坯类型1)毛坯种类的选择:由材料的力学性能要求,零件结构形状的尺寸大小,零件的生产纲领以及利用新技术,新工艺的可能性决定。
2)确定毛坯的形状和尺寸,确定毛坯形状和尺寸时应注意以下几个问题:①为使加工时工件安装稳定,有些铸件毛坯,需要铸出工艺凸台②为了保证零件加工质量和加工方便,常将一些零件作成一个整体毛坯,加工到一定形状后再切割分离。
4.3选择定位基准按照基准的选择原则,必须选择好各道工序的定位基准。
4.4工艺路线的拟定要解决的主要问题:零件各表面的加工方法和方案的选择,加工阶段的划分,确定工序的分散与集中,加工顺序安排和热处理安排等。
1)加工方法和加工方案的选择选择表面加工方案时,应注意以下几个问题①根据加工表面的技术要求,尽可能采用经济加工精度方案经济加工精度:是指在正常的加工条件下,(包括完好的机床设备、必要的工艺装备、标准的工人技术等级、标准的耗用时间和生产费用)所能达到的加工精度。
机械零件加工工艺规程方案设计
机械零件加工工艺规程方案设计一、引言本文旨在设计机械零件加工的规程方案,以确保加工过程的准确性、安全性和高效性。
二、工艺流程1.制定加工计划:根据零件的要求和材料特性,确定合适的加工方法和设备。
2.准备加工设备和工具:确保加工设备和工具的良好状态,包括刀具、夹具、机床等。
3.检查工件和材料:检查工件和材料是否符合要求,包括尺寸、材质、硬度等。
4.加工前准备:准备加工液、切削液和冷却液,确保加工过程的顺利进行。
5.加工操作:根据加工工艺要求,进行加工操作,包括车削、铣削、磨削等。
6.质量检查:在加工过程中进行定期检查,确保加工质量的合格性。
7.表面处理:根据要求进行表面处理,包括镀铬、喷涂等。
8.检验和验收:对加工完成的零件进行检验,确保其符合要求。
9.清洗和防锈:对加工完成的零件进行清洗和防锈处理,以延长其使用寿命。
10.包装和交付:根据客户要求进行适当的包装,并按时交付给客户。
三、注意事项1.安全第一:加工过程中必须严格遵守安全操作规程,佩戴必要的个人防护装备。
2.设备保养:定期检查和维护加工设备,确保其正常运转。
3.物料管理:加工过程中要注意对材料的储存和保护,防止受潮、受污等。
4.加工参数控制:严格控制加工参数,如切削速度、进给速度和切削深度,以确保加工质量。
5.过程记录:对加工过程中的关键参数和质量数据进行记录,以便追溯和分析。
四、质量控制1.原材料质量控制:进行必要的材料检测,确保其符合零件要求。
2.首件检查:对首件进行全面检查,确保加工程序和工装的准确性。
3.过程控制:加工过程中进行定期检查和检验,纠正加工中的问题,确保加工质量。
4.最终检验:对加工完成的零件进行全面检验,检查尺寸、表面质量和功能性能。
5.不良品处理:对不良品进行分类和处理,如返修、重新加工或报废。
五、工艺改进1.分析问题:对加工过程中出现的问题进行分析,找出问题的原因。
2.制定改进方案:根据问题的原因,制定具体的改进方案,如更换设备、改进工艺参数等。
- 1、下载文档前请自行甄别文档内容的完整性,平台不提供额外的编辑、内容补充、找答案等附加服务。
- 2、"仅部分预览"的文档,不可在线预览部分如存在完整性等问题,可反馈申请退款(可完整预览的文档不适用该条件!)。
- 3、如文档侵犯您的权益,请联系客服反馈,我们会尽快为您处理(人工客服工作时间:9:00-18:30)。
3. 加工阶段的划分
• 粗加工阶段 (Ra 6.4) • 半精加工阶段 (Ra 3.2) • 精加工阶段 (Ra 1.6~0.8) • 光整加工阶段(Ra 0.4~0.01)
4. 定位基准
确定零件上某一点、线、面的位置时所 依据的点、线、面称为基准。
基准分为设计基准和工艺基准。 工艺基准又分为定位基准、测量基准和 装配基准。 在加工中,工件在机床上定位时所用的 基准称为定位基准。
坯料开始加工时,各表面均未加工,故 第一道工序只能以坯料表面定位,这种基准 面称为粗基准;以后的工序中用已加工过的 表面定位,称为精基准。
定位基准为粗基准
定位基准为精基准
机械零件加工工艺的制定
路漫漫其悠远
少壮不努力,老大徒悲伤
1. 毛坯的选择
• 轴杆类零件的毛坯,大多为锻件。 • 盘套类零件的毛坯,根据受力情况及零件
形状,分别采用铸铁件、锻件或冲压件。 • 支座、箱体类零件的毛坯,多为铸铁件。
2. 加工余量
在毛坯加工成零件的过程中,在某加工 表面上切除的金属层的总厚度,称为该表面 的加工总余量;各道工序中切除的那层金属, 称为该工序的工序余量。
5. 各பைடு நூலகம்表面加工方案的选择
(1)外圆表面的加工方案
(2)内孔的加工方案
(3)平面的加工方案
6. 典型零件的加工工艺