固定床催化的操作
固定床气固相催化反应器
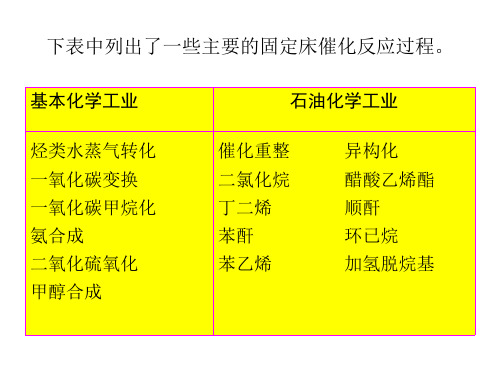
(b)原料气冷激式 Ⅰ
特点:反应器结构简单,便于装 卸催化剂,催化剂床层的温度波动小。
缺点:操作要求较高 应用:适用于放热反应,能做成 大型催化反应器
Ⅱ
x
Ⅲ
平衡温度线
Ⅳ
最佳温度线
大型合成氨厂中的合成反应器,常使用此型
T
(c)非原料气冷激式
冷激用的冷流体如果是非关键组分的反应物, 称为非原料气冷激式。如一氧化碳变换反应器采用 过热水蒸汽冷激。冷激后,平衡温度曲线向着同一 温度下提高平衡转化率的方向移动;最佳温度曲线 也随之变动; 【冷激式反应器的特点】
内冷自热式
催化剂装载在冷管间,与冷管内未反 应气体连续换热,未反应气体经冷管预热 至催化床入口气体温度(高于催化剂的起 始活性温度),故称自热式。
适用于反应热不太大而又在高压下进 行的放热过程。如:中、小型氨合成及甲 醇合成使用此型。
自热式反应器的特点
• 将绝热式和换热式反应器结合起来使用,绝热层 中反应气体借助反应热迅速地升温到理想的反应 温度;然后进入换热段(冷却层)中,反应气体 被冷却而接近最佳温度曲线。自热式反应器只适 用于反应热不太大的放热过程。自热式反应器既 省了外来热源,也可设计出较好的轴向温度分布, 使其更接近于最佳温度分布曲线,因此操作稳定 性更好。但自热式反应器,因其对原料气有热量 反馈,常常会有多重定态现象。开工时,如原料 气不经预热,反应器就会总量处于转化率为零的 低温定态现象。因此对于自热式反应器必须在反 应床层外设置开工加热器。在开工时,必须使原 料气能越过不稳定的定态,当达到转化率高的高 温定态后,再逐步停用开工加热器,使其保持高 温定态反应。
缺点:结构复杂,反应器内催化剂装填量较 少,床层的压降较大,故其不能完全取代 绝热式反应器。
固定床式光催化反应器简易说明
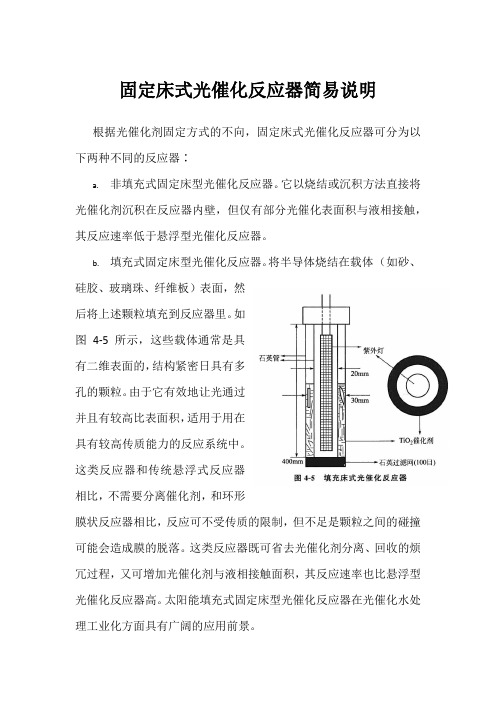
固定床式光催化反应器简易说明根据光催化剂固定方式的不向,固定床式光催化反应器可分为以下两种不同的反应器∶
a.非填充式固定床型光催化反应器。
它以烧结或沉积方法直接将光催化剂沉积在反应器内壁,但仅有部分光催化表面积与液相接触,其反应速率低于悬浮型光催化反应器。
b.填充式固定床型光催化反应器。
将半导体烧结在载体(如砂、硅胶、玻璃珠、纤维板)表面,然
后将上述颗粒填充到反应器里。
如
图4-5 所示,这些载体通常是具
有二维表面的,结构紧密日具有多
孔的颗粒。
由于它有效地让光通过
并且有较高比表面积,适用于用在
具有较高传质能力的反应系统中。
这类反应器和传统悬浮式反应器
相比,不需要分离催化剂,和环形
膜状反应器相比,反应可不受传质的限制,但不足是颗粒之间的碰撞可能会造成膜的脱落。
这类反应器既可省去光催化剂分离、回收的烦冗过程,又可增加光催化剂与液相接触面积,其反应速率也比悬浮型光催化反应器高。
太阳能填充式固定床型光催化反应器在光催化水处理工业化方面具有广阔的应用前景。
固定床气固相催化反应工程

固定床气固相催化反应工程引言固定床气固相催化反应工程是一种重要的化学工程领域,广泛应用于石化、生物质转化和环保领域。
本文将介绍固定床气固相催化反应工程的基本概念、原理及其在实际应用中的重要性。
固定床气固相催化反应工程是指在固定床催化剂上进行的气固相催化反应过程,其特点是催化剂稳定性高,反应产物易于分离,反应条件易于控制。
基本概念固定床气固相催化反应工程是指将气体在固定床催化剂上进行气相催化反应的一种工程化技术。
通常,固定床催化反应器由反应器壳体、催化剂床层、进料装置、催化剂床层和出料装置等组成。
固定床催化剂是反应器中的核心部件,其选择应考虑催化剂的活性、选择性、稳定性和成本等因素。
常用的固定床催化剂包括金属催化剂、金属氧化物催化剂、分子筛催化剂等。
在反应过程中,气体通过催化剂床层与催化剂进行接触,发生催化反应,生成所需的产物。
原理固定床气固相催化反应工程的原理基于气体在催化剂床层中与催化剂发生接触与化学反应的过程。
反应过程可以分为吸附、扩散和反应三个步骤。
首先,气体组分通过物理吸附或化学吸附附着在催化剂表面。
随着反应进行,反应物逐渐被吸附到催化剂表面,形成活性吸附物种。
然后,吸附在催化剂表面上的反应物分子通过表面扩散进入催化剂内部,与催化剂中的活性中心发生反应。
在扩散过程中,反应物分子移动到催化剂内部,并在催化剂孔隙中扩散。
最后,反应物在催化剂内部与催化剂活性中心发生反应,生成所需的产物。
反应产物可以通过物理吸附或化学反应从催化剂表面解吸并释放出来。
应用领域固定床气固相催化反应工程广泛应用于石化、生物质转化和环保领域。
具体应用包括以下几个方面:1.石化领域:固定床气固相催化反应工程在石化行业中广泛应用于合成氨、氢气制备、甲醇制备、乙烯制备等重要化学反应过程中。
通过优化反应条件,提高催化剂的活性和选择性,可以提高反应效率,减少能源消耗和废物排放。
2.生物质转化:固定床气固相催化反应工程在生物质转化领域中起到重要作用。
固定床反应器操作与控制—催化剂基础知识

二、催化剂基本特征
催化剂只改变化学反应的速率,本 身在反应前后没有变化。
基本 特征
催化剂对反应具有选择性
二、催化剂基本特征
不同催化剂的产物
二、催化剂基本特征
催化剂只改变化学反应的速率,本 身在反应前后没有变化。
基本 特征
催化剂对反应具有选择性
催化剂只能加速热力学上可能进行 的化学反应
催化剂对化学反应的平衡状态没影响 对于可逆反应,催化剂在加速正反应 的同时,也能同样程度加速逆反应
固体催化剂的使用-装填和使用
1.催化剂的装填
注
避免催化剂从高处落下造成破损
意
问
题
在填装床层时一定要分布均匀
固体催化剂的使用-催化剂活化
2.催化剂的活化 所用气体
温度、活化气体 的浓度、空速等。
影响因素
氢气、硫化氢、 一氧化碳或氯化 烃等。
活化
使用
活化目的
固体催化剂的使用-催化剂活化
催化剂的活化
又及时排不出去,还会影响到催化剂的力学性能; 3. 还原一般是在工业反应器内进行的,升温过程太快,不容易做到床层温度均匀。
还原时,升温要缓慢,并在温度达到一定程度后要恒温一段时 间,有利于床层温度均匀和床层内的水汽排放。
催化剂的活化
合成氨催化剂的活化
气体中少量的水汽会把a-Fe重新氧化成Fe304
催化剂的制备
2.浸渍法
将制作催化剂的有效成分溶解在水里配成溶 液,然后把抽成真空的多孔载体浸没在溶液 里,使有效组分吸附在载体的内外表面上。
影响因素:活性组分对载体的用量比、载体浸 渍时溶液的浓度、浸渍后干燥速率等。
催化剂的制备
3.混合法
将几种组分用机械混合的方法制 成多组分催化剂。
固定床催化的操作
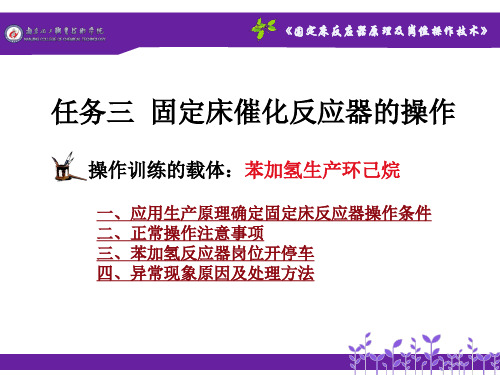
镍系催化剂
活性好,价格便宜 但如耐硫性能差,耐热性差 一般工业使用温度120~180℃ 液苯空速低(一般为0.2~0.8h-) 工业使用寿命短 只能副产低压蒸汽 目前我国镍系苯加氢催化剂主要 用于中小型生产装置;
任务三 固定床催化反应器的操作
一、应用生产原理确定固定床反应器操作条件
(一)反应原料、产物及用途、生产方法 5.生产方法
可逆反应
随温度的升高,总的反应速率提高。因此,对于可逆吸热反应,也应 尽可能在较高温度下进行,这样既有利于提高平衡转化率,又可提高 反应速率。同时,也应考虑一些因素的限制。
例如:天然气的蒸汽转化反应 CH 4 H2O CO H2
是可逆吸热反应,提高温度有利于提高反应速率并提高甲烷的平衡 转化率,但考虑到设备材质等条件限制,一般转化炉内温度小于 800-850℃。
任务三 固定床催化反应器的操作
不可逆反应
由于反应速率常数随温度的升高而升高,因此,无论是放热反应还是 吸热反应,都应该在尽可能高的温度下进行,以获得较大的反应速率, 但在实际生产中,要考虑以下问题: a)温度过高,催化剂活性下降或失活; b)设备材质的选取 c)热能的供应 d)伴有副反应时,会影响反应的选择性
(三)工艺参数的确定与优化 2.反应动力学
任务三 固定床催化反应器的操作
前人在进行苯气相加氢反应动力学的研究时,并没有意识到催化剂颗粒可能并非完全处于气相状态,而是 简单地认为当反应物为气相时得到的动力学就是气相反应动力学。从理论上讲,这种观点确实存在不足, 但从工业应用角度出发,它仍具有一定意义。
《固定床反应器原理及岗位操作技术》
任务三 固定床催化反应器的操作
操作训练的载体:苯加氢生产环己烷
一、应用生产原理确定固定床反应器操作条件 二、正常操作注意事项 三、苯加氢反应器岗位开停车 四、异常现象原因及处理方法
化工反应过程之固定床反应器
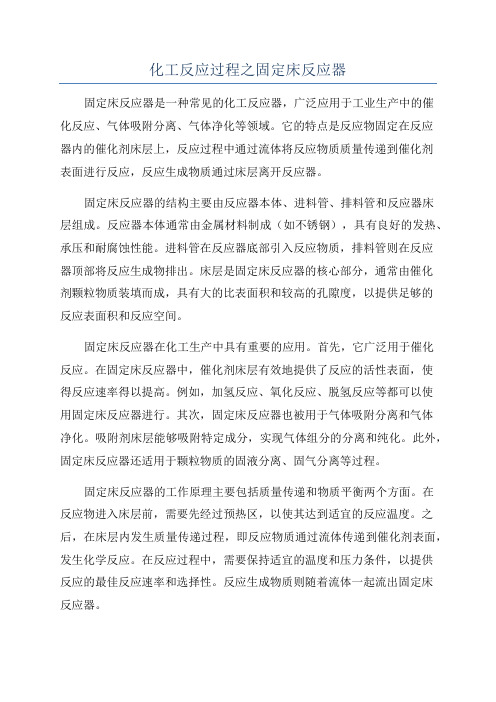
化工反应过程之固定床反应器固定床反应器是一种常见的化工反应器,广泛应用于工业生产中的催化反应、气体吸附分离、气体净化等领域。
它的特点是反应物固定在反应器内的催化剂床层上,反应过程中通过流体将反应物质质量传递到催化剂表面进行反应,反应生成物质通过床层离开反应器。
固定床反应器的结构主要由反应器本体、进料管、排料管和反应器床层组成。
反应器本体通常由金属材料制成(如不锈钢),具有良好的发热、承压和耐腐蚀性能。
进料管在反应器底部引入反应物质,排料管则在反应器顶部将反应生成物排出。
床层是固定床反应器的核心部分,通常由催化剂颗粒物质装填而成,具有大的比表面积和较高的孔隙度,以提供足够的反应表面积和反应空间。
固定床反应器在化工生产中具有重要的应用。
首先,它广泛用于催化反应。
在固定床反应器中,催化剂床层有效地提供了反应的活性表面,使得反应速率得以提高。
例如,加氢反应、氧化反应、脱氢反应等都可以使用固定床反应器进行。
其次,固定床反应器也被用于气体吸附分离和气体净化。
吸附剂床层能够吸附特定成分,实现气体组分的分离和纯化。
此外,固定床反应器还适用于颗粒物质的固液分离、固气分离等过程。
固定床反应器的工作原理主要包括质量传递和物质平衡两个方面。
在反应物进入床层前,需要先经过预热区,以使其达到适宜的反应温度。
之后,在床层内发生质量传递过程,即反应物质通过流体传递到催化剂表面,发生化学反应。
在反应过程中,需要保持适宜的温度和压力条件,以提供反应的最佳反应速率和选择性。
反应生成物质则随着流体一起流出固定床反应器。
固定床反应器的优势在于:一、反应物质与催化剂的接触充分,反应效率高;二、催化剂寿命长,催化剂载体不易破碎;三、床层的填料物质易于更换和维护;四、反应器体积相对较小,能够实现高度效能的连续化生产。
然而,固定床反应器也有一些缺点需要克服。
首先,反应床层在长时间运行后会出现积碳、堵塞等现象,需进行定期清洗和更换床层。
其次,固定床反应器对反应物料的物理性质要求较高,如化学性质、颗粒度等。
固定床反应器操作与控制
4.空速操作原则
在操作过程中,需要进行提温提空速时,应“先 提空速后提温”,而降空速降温时则“先降温后降 空速”。如果违背这个原则,会造成剧烈的加氢裂 化反应,使氢纯度下降,增加催化剂表面的积炭 。在不正常的情况下,应尽量避免空速大幅度下 降,从而引起反应温度超高。
14.2 催化剂器内再生操作
器内再生即是反应物料停止进反应器后, 催化剂保留在反应器内,而将再生介质通过 反应器,进行再生操作。这种再生方式,避 免了催化剂的装卸,缩短了再生时间,是一 种广泛使用的方式。
长期停车:钝化处理—用含少量氧的N2(或水蒸 气)缓慢氧化催化剂,逐步降温——卸出催化剂。
卸出催化剂方法:真空抽出,人工卸出; 更换催化剂的停车:降温、氧化、卸出;
14.1.4 催化剂的使用、失活与再生
14.1.4.1 催化剂的使用 1. 催化剂使用中的变化(活性随时间的变化)
Ⅰ. 诱导期(成熟期) Ⅱ. 稳定期 Ⅲ. 衰老期 2. 注意事项
催化剂使用一段时间后,活性将下降。 活性下降的原因分三类: 结构变化--烧结、粉化、活性组分晶粒长大等。 物理失活--积碳、粉尘、惰性组分吸附等。 化学中毒--原料中的有害物质与催化剂活性组分
发生反应,永久性结合。
解决失活。 2、采用“ 中期活性”设计反应器--反应
化学反应过程与设备
任务14 固定床反应器操作与控制
14.1 催化剂使用
14.1.1运输、贮藏与填装
包装:通常是桶装(内用塑料袋),有金属桶、纤
维板桶。
运输:轻拿轻放,以免破碎。 贮藏:防潮、防污染、防氧化。 装填:保证气流分布均匀、阻力降小——先过筛,
检查支撑箅条、金属支网等状况,顶部用固定栅 条或一层重的惰性物压住——防被吹而移动
精制固定床处理方案
精制汽油固定床再生方案1.固定床退汽油:将固定床入口汽油阀门关闭,利用泄压线串压将床内汽油按正常出流程压空,关闭汽油出口阀,剩余底部汽油接胶管退至地下污油罐,汽油出入口阀门打盲板。
2.打水冲洗:冲洗碱液和汽油,消除异味通过P22102打水,至固定床底部玻璃板起液位后停止补水,开泵打循环4〜6小时,停泵,床内冲压至0.2MPa,将洗床水打至分馏V22203C中,连续置换3〜5次。
直至水样做碱浓度1%左右且汽油量较少后,停止打水冲洗,将床层内残液压空。
3.蒸床:将残留的油气和异味消除将碱液抽出、注入口及泄压线打盲板,固定床R26101注入蒸汽,顶部放空,底部导淋,连续蒸床时间累积24h。
蒸汽不宜过大,根据顶放空情况调整,蒸床完毕后安全阀上游阀及副线打盲板。
4.更换活性炭:开人孔置换通风,配合施工队更换活性炭,检查无异常后封人孔、拆盲板,蒸汽试压试密。
5.催化剂碱液浸渍,循环:(1)催化剂碱液浸渍每2公斤磺化酞菁钴应用10-15%NaOH在25〜50升小桷内预溶解,然后倒入碱液管线入口与碱液充分混合溶解。
所需碱液量直到把固定床催化剂完全浸泡为止。
床层浸渍催化剂磺化酞菁钴用量至少占活性炭床层重量的0.2-0.4%。
(2)催化剂碱液循环打开塔顶放空,关闭塔底排净口,循环流程:R26101→P26102→R26101在床层上浸泡并打循环,保持循环碱液温度45~50度。
碱液循环浸渍至少5-7天。
如果时间允许,可一直循环到进汽油为止。
循环过程中检测碱液浓度,如果低于10%可补加碱液。
挂完催化剂后静止沉降约1天。
充氮气退碱液,将碱液退至V26105中备用。
注意:1.每次操作时应细心、尤其确保操作工艺阀门开关位置要正确,防止互串跑冒。
2.催化剂碱液循环时,禁止固定床抽负压。
催化车间2018.7.4。
第六章固定床催化反应器设计-化学反应工程
第六章气-固相催化反应器设计本章核心内容:本章讨论的气固相催化反应反应器包括固定床反应器和流化床反应器。
在固定床反应器部分,介绍了气固相催化反应器的各种类型和固定床层的流动特性,给出了固定床反应器的两种设计方法:经验或半经验法和数学模型法。
在流化床反应器部分,在对固体颗粒流态化现象和流态化特征参数介绍的基础上,讨论了流化床反应器的分类和工业应用。
6-1 固定床反应器的型式反应器内部填充有固定不动的固体催化剂颗粒或固体反应物的装置,称为固定床反应器。
气态反应物通过床层进行催化反应的反应器,称为气固相固定床催化反应器。
这类反应器除广泛用于多相催化反应外,也用于气固及液固非催化反应,它与流化床反应器相比,具有催化剂不易跑损或磨损,床层流体流动呈平推流,反应速度较快,停留时间可以控制,反应转化率和选择性较高的优点。
工业生产过程使用的固定床催化反应器型式多种多样,主要为了适应不同的传热要求和传热方式,按催化床是否与外界进行热量交换来分,分为绝热式和连续换热式两大类。
另外,按反应器的操作及床层温度分布不同来分,分为绝热式、等温式和非绝热非等温三种类型;按换热方式不同,分为换热式和自热式两种类型;按反应情况来分,分为单段式与多段式两类;按床层内流体流动方向来分,分为轴向流动反应器和径向流动反应器两类;根据催化剂装载在管内或管外、反应器的设备结构特征,也可以对固定床催化反应器进行分类。
图6-1、6-2、6-3分别是轴向流动式、径向流动式和列管式固定床反应器结构示意图。
其中,图6-1和图6-2所示的反应器为绝热式,图6-3所示的反应器为连续换热式。
图6-1 轴向流动式图6-2径向流动式图6-3列管式固固定床反应器固定床反应器定床反应器6-1-1 绝热式固定床反应器绝热式固定床催化反应器有单段与多段之分。
绝热式反应器由于与外界无热交换以及不计入热损失,对于可逆放热反应,依靠本身放出的反应热而使反应气体温度逐步升高;催化床入口气体温度高于催化剂的起始活性温度,而出口气体温度低于催化剂的耐热温度。
固定床反应器操作规程
固定床反应器操作规程《固定床反应器操作规程》一、目的固定床反应器是化工工艺中常用的一种反应器类型,用于催化剂反应或吸附分离等过程。
为了保证固定床反应器的安全操作和稳定运行,制定了本操作规程。
二、操作流程1. 开始操作前,要对固定床反应器进行全面检查,确保设备无漏气、无泄露,并且操作人员已接受了必要的培训。
2. 打开固定床反应器的进料阀门,逐步减小进料流量,保证反应器内的压力稳定并且均匀。
3. 开启反应器的加热或者冷却系统,根据反应条件选择合适的温度,开始反应过程。
4. 在操作中应及时监控反应器内部的温度、压力、流量等参数,根据需要调整操作参数。
5. 反应过程结束后,关闭进料阀门,停止加热或冷却系统,等待反应器内部压力降至安全范围后,进行废气排放处理。
三、安全注意事项1. 操作人员要严格遵守操作规程,严禁在未关闭反应器进料阀门的情况下进行其他操作。
2. 在操作过程中,要定期检查固定床反应器及相关管道的密封情况,发现泄漏要及时处理。
3. 操作人员要了解反应器内介质的性质,以及可能产生的危险情况,如有异味或者异常现象应立即停止操作并报告。
4. 操作人员要穿戴防护装备,如防护眼镜、手套等,以防止意外伤害发生。
四、操作记录每次操作结束后,要对反应器的操作情况进行记录,包括进料流量、操作参数、温度压力变化等,以备日后查阅。
五、紧急处理在发生操作事故或者紧急情况时,操作人员要立即采取相应的应急措施并报告相关部门,确保事故得到及时处理。
六、操作人员的培训所有操作固定床反应器的人员必须接受相关的培训,并且取得相应的操作证书方可参与操作。
以上便是《固定床反应器操作规程》,希望所有操作人员严格遵守,并确保设备的安全运行。
- 1、下载文档前请自行甄别文档内容的完整性,平台不提供额外的编辑、内容补充、找答案等附加服务。
- 2、"仅部分预览"的文档,不可在线预览部分如存在完整性等问题,可反馈申请退款(可完整预览的文档不适用该条件!)。
- 3、如文档侵犯您的权益,请联系客服反馈,我们会尽快为您处理(人工客服工作时间:9:00-18:30)。
(1)严格执行装置下发的工艺指令单; (2)经常巡回检查,发现问题及时汇报处理; (3)V0801A/B新进苯后要勤排水; (4)要求加强控制氢气质量; (5)C0102进口缓冲罐液位、压差、出口温度、电 流要加强监控;
Hale Waihona Puke (6)勤检查P0102出口压力及R0101上室热油量;
二、正常操作注意事项
任务三 固定床催化反应器的操作
任务三 固定床催化反应器的操作
不可逆反应
由于反应速率常数随温度的升高而升高,因此,无论是放热反应还是 吸热反应,都应该在尽可能高的温度下进行,以获得较大的反应速率, 但在实际生产中,要考虑以下问题: a)温度过高,催化剂活性下降或失活; b)设备材质的选取 c)热能的供应 d)伴有副反应时,会影响反应的选择性
三、苯加氢反应器岗位开停车
(一)岗位开车
任务三 固定床催化反应器的操作
1.开车前准备与检查
2.开车程序 (1)投热油系统 (2)系统置换与试漏 (3)加氢系统保压 (4)苯干燥系统 (5)吸附装置 (6)加氢反应和产物处理 (7)庚烷塔T0102开车
三、苯加氢反应器岗位开停车
(二)岗位停车 1. 正常停车 (1)短期停车——系统保温保压 (2)长期停车——系统降温降压 2. 紧急停车 (1)紧急停电、汽、水操作类同 (2)紧急停车按钮
1.原料 苯
2.产物 环己烷
3.产物用途
※生产环己醇、环己酮、聚己内酰胺和聚己二酰己二 胺有机化工原料。
※是纤维素醚、树脂、蜡、沥青和橡胶的优良溶剂。
任务三 固定床催化反应器的操作
一、应用生产原理确定固定床反应器操作条件
(一)反应原料、产物及用途、生产方法
4.催化剂
铂系催化剂
耐硫性能好 中毒后易再生 耐热性能好 工业操作温度可达200~400℃ 可副产中压蒸汽(1.0MPa) 液苯空速可达1.0~2.0h-
任务三 固定床催化反应器的操作
影响加氢过程主要工艺参数有反应温度、压力、空速及氢油比。
(1)反应温度
加氢的平衡常数比较大,反应主要受反应速度制约,提 高温度有利于加快反应速度。
在实际应用中,应根据原料组成和性质及产品要求来选 择适宜的反应温度。 控制反应器
§入口温度为180~200℃ §反应热点温度360~380℃
(三)工艺参数的确定与优化
2.反应动力学
任务三 固定床催化反应器的操作
由此可见,气固相催化反应 过程是个多步骤过程。整个 反应速率取决于最慢的一步, 该步骤就称为速率控制步骤。 当反应过程达到定态时,各 步骤的速率应该相等,且反 应过程的速率等于控制步骤 的速率。
(三)工艺参数的确定与优化 3.苯加氢催化反应器工艺参数的确定
热油循环量FSL01006动作
加大蒸汽量,TSL01003去动作 后,按FT01003复位 重新启动P0101或检查并确认 PSL01001开关动作正确及 备用泵出口阀处于关闭状态 视具体原因重新开车 检查R0101排空情况及上室热 油量是否偏小 重新启动P0102,排气或充油
可逆反应
随温度的升高,总的反应速率提高。因此,对于可逆吸热反应,也应 尽可能在较高温度下进行,这样既有利于提高平衡转化率,又可提高 反应速率。同时,也应考虑一些因素的限制。 例如:天然气的蒸汽转化反应
CH 4 H2O CO H2
是可逆吸热反应,提高温度有利于提高反应速率并提高甲烷的平衡 转化率,但考虑到设备材质等条件限制,一般转化炉内温度小于 800-850℃。
任务三 固定床催化反应器的操作
四、异常现象原因及处理方法
序号 异常现象 原因 原料苯含水量过高 再沸器E0101蒸汽量过小 再沸器E0101或E0102列管漏 D0101分层不佳
任务三 固定床催化反应器的操作
处理方法 苯罐放水 加大蒸汽量 停车检修 D0101勤排水
1
T0101釜 液含 水高
T0101的TSL01003动作 P0101出口压力PSL01001动作 2 停苯加料 C0102停车 R0101上TSH01008(1~12)动作
(7)勤观察反应热点温度及R0102的温差TDI01012 的变化情况; (8)加强控制尾氢排放量,在R0102温差不大情况 下尽量少排; (9)勤检查X0101小泵运行情况; (10)加强控制E0107高温锅炉给水,定期排污, 以防结垢; (11)调整生产负荷,速度要慢; (12)D0103液位现场检查。
(三)工艺参数的确定与优化
2.反应动力学
任务三 固定床催化反应器的操作
前人在进行苯气相加氢反应动力学的研究时,并没有意识到催化剂颗粒可能并非完全处于气相状态,而是 简单地认为当反应物为气相时得到的动力学就是气相反应动力学。从理论上讲,这种观点确实存在不足, 但从工业应用角度出发,它仍具有一定意义。
苯加氢催化剂
镍系催化剂
活性好,价格便宜 但如耐硫性能差,耐热性差
一般工业使用温度120~180℃
液苯空速低(一般为0.2~0.8h-) 工业使用寿命短 只能副产低压蒸汽 目前我国镍系苯加氢催化剂主要 用于中小型生产装置;
工业使用寿命大于5年。
任务三 固定床催化反应器的操作
一、应用生产原理确定固定床反应器操作条件
(一)反应原料、产物及用途、生产方法
5.生产方法
环己烷生产方法
苯加氢法
石油烃馏分的 分馏精制法
工艺气体混合均匀
液相苯加氢
气相苯加氢
转化率、收率均很高 反应激烈,易飞温;
任务三 固定床催化反应器的操作
一、应用生产原理确定固定床反应器操作条件
(二)反应原理及特点
1.原理
苯加氢反应是一个复杂的反应体系。在一定反应条件下, 苯与氢可能发生以下各种反应。
(三)工艺参数的确定与优化
2.反应动力学
任务三 固定床催化反应器的操作
一般而言,气固相催化反应过程经历以下七个步骤,如右图所示。
补充:活性中心
由于化学吸附只能发生于固体表面那些能与 气相分子起反应的原子上,通常把该类原子 称为活性中心,用符号“σ”表示。
①反应组分从流体主体向固体催化剂外表面传递(外扩散过程); ②反应组分从催化剂外表面向催化剂内表面传递(内扩散过程); ③反应组分在催化剂表面的活性中心吸附(吸附过程); ④在催化剂表面上进行化学反应(表面反应过程); ⑤反应产物在催化剂表面上脱附(脱附过程); ⑥反应产物从催化剂内表面向催化剂外表面传递(内扩散过程); ⑦反应产物从催化剂外表面向流体主体传递(外扩散过程)。
(三)工艺参数的确定与优化
任务三 固定床催化反应器的操作
(2)反应压力
★提高氢分压,加快反应速度 ★提高苯的转化率 ★压力提高增加装置的设备投资费用和运行费用 ★对催化剂的机械强度要求也提高
苯加氢气固相催化反应采用铂系催化剂,控制反应器 反应压力为3.1MPa。
(三)工艺参数的确定与优化
(3)反应空速
(二)反应原理及特点
1.原理
任务三 固定床催化反应器的操作
其中,反应(1)为主反应,生成目的产物环己烷; 反应(2)是苯的加氢裂解,最终产物为碳和甲烷; 反应(3)是环己烷的异构化; 反应(4)则是环己烷的裂解反应。 对于苯而言,反应(1)和(2)是平行反应。 尽管反应(1)和(3)均为可逆反应,但前者为放热反应, 后者为吸热反应,这就导致温度对反应的影响各不相 同。
任务三 固定床催化反应器的操作
■空速:单位时间、单位体积(质量)的催化剂所能处理
的原料气的体积流量。
空速的大小反映了反应器的处理能力和反应时间。
■空速越大,处理能力越大 ■原料与催化剂的接触时间则越短 ■相应的反应时间也就越短。
因此,空速的大小最终影响原料的转化率和反应的深度。
苯加氢气固相催化反应:控制液苯空速1.6~1.7h-。
(二)反应原理及特点
2.反应场所
任务三 固定床催化反应器的操作
¤前反应器:列管换热式固定床反应器 ¤后反应器:单段绝热式固定床反应器 3.反应特点
¤强放热反应
¤复杂反应
¤气固催化反应
(三)工艺参数的确定与优化
1.反应热力学
任务三 固定床催化反应器的操作
苯加氢制环己烷的反应是一个放热的、体积减小的可逆反应,因此,低温和高压对该反应 是有利的。 但温度不能太低,分子不能很好活化、反应速率较慢。
(三)工艺参数的确定与优化
(4)反应氢油比 *氢油比:影响反应过程的氢分压。
任务三 固定床催化反应器的操作
*增加氢油比,有利于加氢反应进行 *提高催化剂寿命 *但过高的氢油比将增加装置的操作费用及设备投资
苯加氢气固相催化反应 控制n(H2):n(苯)≥3.8。
二、正常操作注意事项
任务三 固定床催化反应器的操作
《固定床反应器原理及岗位操作技术》
任务三 固定床催化反应器的操作
操作训练的载体:苯加氢生产环己烷
一、应用生产原理确定固定床反应器操作条件 二、正常操作注意事项 三、苯加氢反应器岗位开停车 四、异常现象原因及处理方法
任务三 固定床催化反应器的操作
一、应用生产原理确定固定床反应器操作条件
(一)反应原料、产物及用途、生产方法