无氧铜生产工艺流程.
无氧铜生产工艺流程

第四章工艺技术方案4.1工艺技术方案本项目采用的原材料为含铜量99%的电解铜,选用目前国内先进的蓄热式熔化炉和中频炉,用上引法连铸工艺方法生产氧的含量不大于0.02%,杂质总含量不大于0.05%,含铜量99.5%以上无氧铜杆。
4.2工艺流程简述1、生产准备本项目使用的电解铜在江西省内购买。
图4-1项目生产工艺流程图2、上引法连铸工艺流程本项目采用上引法连铸工艺生产无氧铜杆。
上引法连铸铜杆的基本特点是“无氧”,即氧含量在10以下。
上引法与连铸连轧和浸涂法相比,其特点是:1)由于拉扎工艺和铸造工艺不是连续的,拉扎是在常温下进行的,不需要气体保护,钢材也不会被氧化。
因此设备投资小,厂房布置也灵活。
2)单机产量变化范围大,年产量可以从几百吨到几万吨,可供不同规模的厂家选用不同型号的上引机组。
此外,由于连铸机是多头的,可以很容易的通过改变铸造规格(铸杆直径),来改变单位时间的产量,因此其产量可视原材料的供应情况和产品的需求情况来确定,便于组织生产、节约能源。
3)只需更换结晶器和改变石墨模的形状,即可生产铜管、铜排等异型铜材,并可在同一机器上上产不同规格、品种的铜材,灵活机动,这是上引法的中最大特点。
上引法连铸工艺流程:原料通过加料机加入融化炉进行熔化、氧化、扒渣处理后,熔融的铜液经过一段时间的静置还原脱氧并达到一定的温度后,通过有气体保护的流槽经过渡腔(铜液在此进一步还原脱氧、清除渣质),进而平稳的流入中频炉保温静置,铜液的温度由热电偶测量,温度值由仪表显示,温度控制在1150℃±10℃。
连铸机固定于中频保温炉的上方,连铸机铜液在结晶器中快速结晶连续不断地生产出铜杆,最后经双头挠杆机等辅助设备装盘成产品。
⑴加料:原料一般用加料机加入,炉头多加、炉尾少加。
加冷料时要使铜料距炉顶及烟道口有一定距离,以保证燃料燃烧和炉气流动的顺畅。
加料时要保证炉膛有足够高的温度,一般应达到1300℃以上,炉内应保证零压或微负压。
无氧铜生产工艺流程
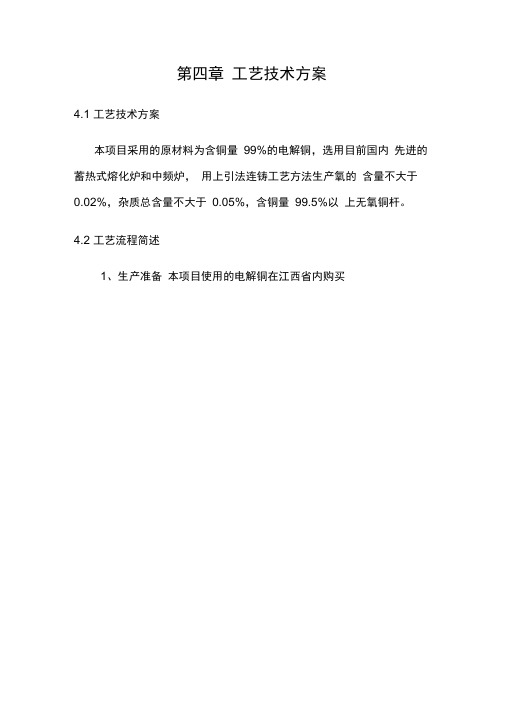
第四章工艺技术方案4.1 工艺技术方案本项目采用的原材料为含铜量99%的电解铜,选用目前国内先进的蓄热式熔化炉和中频炉,用上引法连铸工艺方法生产氧的含量不大于0.02%,杂质总含量不大于0.05%,含铜量99.5%以上无氧铜杆。
4.2 工艺流程简述1、生产准备本项目使用的电解铜在江西省内购买2、上引法连铸工艺流程本项目采用上引法连铸工艺生产无氧铜杆。
上引法连铸铜杆的基氧气烟囱图4-1 项目生产工艺流程图电解铜原料准备合格原料重油烟 1气-喷雾冷却-布袋收尘烟 尘中频炉烟气大气熔剂(副产还原脱氧、保温熔化炉结晶出杆 装盘无氧铜杆(外本特点是“无氧”,即氧含量在10pp m以下。
上引法与连铸连轧和浸涂法相比,其特点是:1)由于拉扎工艺和铸造工艺不是连续的,拉扎是在常温下进行的,不需要气体保护,钢材也不会被氧化。
因此设备投资小,厂房布置也灵活。
2)单机产量变化范围大,年产量可以从几百吨到几万吨,可供不同规模的厂家选用不同型号的上引机组。
此外,由于连铸机是多头的,可以很容易的通过改变铸造规格(铸杆直径),来改变单位时间的产量,因此其产量可视原材料的供应情况和产品的需求情况来确定,便于组织生产、节约能源。
3)只需更换结晶器和改变石墨模的形状,即可生产铜管、铜排等异型铜材,并可在同一机器上上产不同规格、品种的铜材,灵活机动,这是上引法的中最大特点。
上引法连铸工艺流程:原料通过加料机加入融化炉进行熔化、氧化、扒渣处理后,熔融的铜液经过一段时间的静置还原脱氧并达到一定的温度后,通过有CO气体保护的流槽经过渡腔(铜液在此进一步还原脱氧、清除渣质),进而平稳的流入中频炉保温静置,铜液的温度由热电偶测量,温度值由仪表显示,温度控制在1150C 土10C。
连铸机固定于中频保温炉的上方,连铸机铜液在结晶器中快速结晶连续不断地生产出铜杆,最后经双头挠杆机等辅助设备装盘成产品。
⑴加料:原料一般用加料机加入,炉头多加、炉尾少加。
无氧铜杆连铸连轧生产线
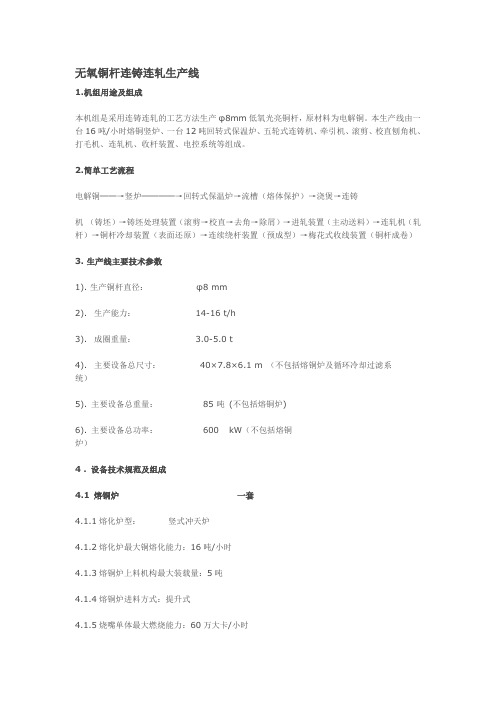
无氧铜杆连铸连轧生产线1.机组用途及组成本机组是采用连铸连轧的工艺方法生产φ8mm低氧光亮铜杆,原材料为电解铜。
本生产线由一台16吨/小时熔铜竖炉、一台12吨回转式保温炉、五轮式连铸机、牵引机、滚剪、校直刨角机、打毛机、连轧机、收杆装置、电控系统等组成。
2.简单工艺流程电解铜──→竖炉────→回转式保温炉→流槽(熔体保护)→浇煲→连铸机(铸坯)→铸坯处理装置(滚剪→校直→去角→除屑)→进轧装置(主动送料)→连轧机(轧杆)→铜杆冷却装置(表面还原)→连续绕杆装置(预成型)→梅花式收线装置(铜杆成卷)3. 生产线主要技术参数1). 生产铜杆直径:φ8 mm2). 生产能力:14-16 t/h3). 成圈重量: 3.0-5.0 t4). 主要设备总尺寸: 40×7.8×6.1 m (不包括熔铜炉及循环冷却过滤系统)5). 主要设备总重量: 85 吨(不包括熔铜炉)6). 主要设备总功率: 600 kW(不包括熔铜炉)4 .设备技术规范及组成4.1熔铜炉一套4.1.1熔化炉型:竖式冲天炉4.1.2熔化炉最大铜熔化能力:16吨/小时4.1.3熔铜炉上料机构最大装载量:5吨4.1.4熔铜炉进料方式:提升式4.1.5烧嘴单体最大燃烧能力:60万大卡/小时4.1.6熔铜炉烧嘴数量:15只4.1.7烧嘴冷却方式:水冷4.1.8烧嘴点火方式:自动4.1.9使用燃料:天然气、液化气、城市煤气4.1.10保温炉炉型:液压回转式4.1.11保温炉有效容量:12吨4.1.12保温炉最高倾力角度:>70º4.1.13烧嘴单体最大燃烧能力:60万大卡/小时4.1.14保温炉烧嘴数量:1只4.1.15燃烧控制方式:比例燃烧,具有保护装置4.1.16燃气阀检漏方式:手动/自动熔铜炉包括冲天式铜熔化炉、回转式保温炉、上下流槽、燃烧控制系统等四大部分。
具有熔化速度快、铜水含氧量低、流量连续可调、铜水温度独立可控、单位铜水燃气消耗量低等特点。
无氧铜生产工艺
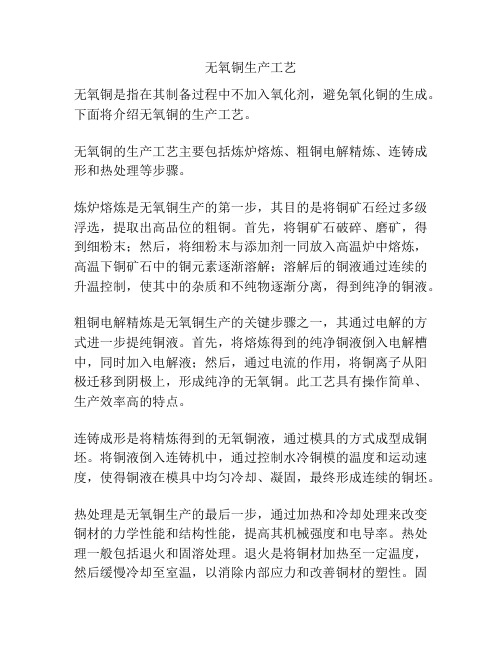
无氧铜生产工艺
无氧铜是指在其制备过程中不加入氧化剂,避免氧化铜的生成。
下面将介绍无氧铜的生产工艺。
无氧铜的生产工艺主要包括炼炉熔炼、粗铜电解精炼、连铸成形和热处理等步骤。
炼炉熔炼是无氧铜生产的第一步,其目的是将铜矿石经过多级浮选,提取出高品位的粗铜。
首先,将铜矿石破碎、磨矿,得到细粉末;然后,将细粉末与添加剂一同放入高温炉中熔炼,高温下铜矿石中的铜元素逐渐溶解;溶解后的铜液通过连续的升温控制,使其中的杂质和不纯物逐渐分离,得到纯净的铜液。
粗铜电解精炼是无氧铜生产的关键步骤之一,其通过电解的方式进一步提纯铜液。
首先,将熔炼得到的纯净铜液倒入电解槽中,同时加入电解液;然后,通过电流的作用,将铜离子从阳极迁移到阴极上,形成纯净的无氧铜。
此工艺具有操作简单、生产效率高的特点。
连铸成形是将精炼得到的无氧铜液,通过模具的方式成型成铜坯。
将铜液倒入连铸机中,通过控制水冷铜模的温度和运动速度,使得铜液在模具中均匀冷却、凝固,最终形成连续的铜坯。
热处理是无氧铜生产的最后一步,通过加热和冷却处理来改变铜材的力学性能和结构性能,提高其机械强度和电导率。
热处理一般包括退火和固溶处理。
退火是将铜材加热至一定温度,然后缓慢冷却至室温,以消除内部应力和改善铜材的塑性。
固
溶处理是将无氧铜加热至固溶温度,然后迅速冷却,以形成均匀的固溶相。
这些热处理工艺可以显著提高无氧铜的性能。
以上就是无氧铜的生产工艺,包括炼炉熔炼、粗铜电解精炼、连铸成形和热处理等步骤。
这些工艺能够制备出高纯度、无氧化铜的产品。
无氧铜杆连铸连轧生产线技术
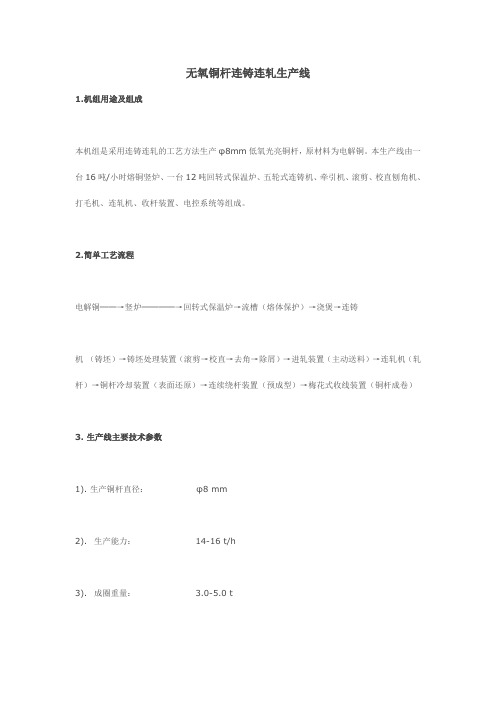
无氧铜杆连铸连轧生产线1.机组用途及组成本机组是采用连铸连轧的工艺方法生产φ8mm低氧光亮铜杆,原材料为电解铜。
本生产线由一台16吨/小时熔铜竖炉、一台12吨回转式保温炉、五轮式连铸机、牵引机、滚剪、校直刨角机、打毛机、连轧机、收杆装置、电控系统等组成。
2.简单工艺流程电解铜──→竖炉────→回转式保温炉→流槽(熔体保护)→浇煲→连铸机(铸坯)→铸坯处理装置(滚剪→校直→去角→除屑)→进轧装置(主动送料)→连轧机(轧杆)→铜杆冷却装置(表面还原)→连续绕杆装置(预成型)→梅花式收线装置(铜杆成卷)3. 生产线主要技术参数1). 生产铜杆直径:φ8 mm2). 生产能力:14-16 t/h3). 成圈重量: 3.0-5.0 t4). 主要设备总尺寸: 40×7.8×6.1 m (不包括熔铜炉及循环冷却过滤系统)5). 主要设备总重量: 85 吨(不包括熔铜炉)6). 主要设备总功率: 600 kW(不包括熔铜炉)4 .设备技术规范及组成4.1熔铜炉一套4.1.1熔化炉型:竖式冲天炉4.1.2熔化炉最大铜熔化能力:16吨/小时4.1.3熔铜炉上料机构最大装载量:5吨4.1.4熔铜炉进料方式:提升式4.1.5烧嘴单体最大燃烧能力:60万大卡/小时4.1.6熔铜炉烧嘴数量:15只4.1.7烧嘴冷却方式:水冷4.1.8烧嘴点火方式:自动4.1.9使用燃料:天然气、液化气、城市煤气4.1.10保温炉炉型:液压回转式4.1.11保温炉有效容量:12吨4.1.12保温炉最高倾力角度:>70º4.1.13烧嘴单体最大燃烧能力:60万大卡/小时4.1.14保温炉烧嘴数量:1只4.1.15燃烧控制方式:比例燃烧,具有保护装置4.1.16燃气阀检漏方式:手动/自动熔铜炉包括冲天式铜熔化炉、回转式保温炉、上下流槽、燃烧控制系统等四大部分。
具有熔化速度快、铜水含氧量低、流量连续可调、铜水温度独立可控、单位铜水燃气消耗量低等特点。
无氧铜杆的生产方法
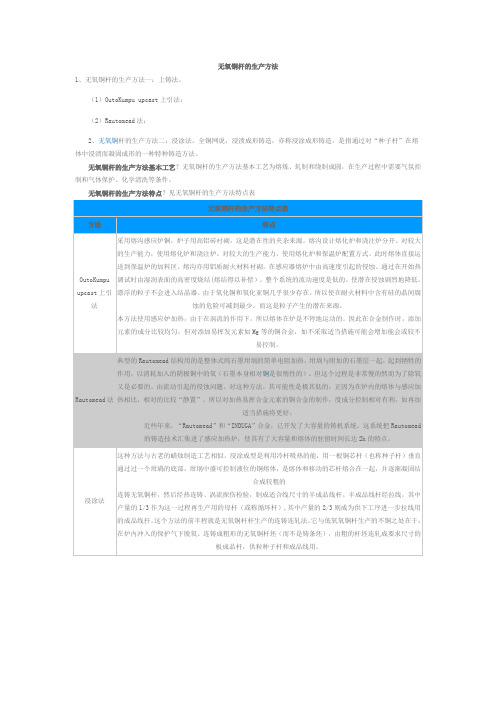
无氧铜杆的生产方法1、无氧铜杆的生产方法一:上铸法。
(1)OutoKumpu upcast上引法:(2)Rautomead法:2、无氧铜杆的生产方法二:浸涂法。
全铜网说,浸渍成形铸造,亦称浸涂成形铸造,是指通过对“种子杆”在熔体中浸渍而凝固成形的一种特种铸造方法。
无氧铜杆的生产方法基本工艺?无氧铜杆的生产方法基本工艺为熔炼、轧制和绕制成圆,在生产过程中需要气氛控制和气体保护、化学清洗等条件。
无氧铜杆的生产方法特点?见无氧铜杆的生产方法特点表Rautomead铸机截面图无氧铜杆的生产方法优势?性能优良,工艺先进,生产效率高并节约能源,不需酸洗。
此外,能减少加工工序,而且铜的损耗率低。
无氧铜杆的生产方法之冶金化学反应?1、阴极铜予处理阶段,阴极铜加入熔化炉前,如在预热炉热(700*c左右)。
此时铜板表面存在的胆矾和碱碳酸铜及水分发生离解和蒸发,其反应式如下CuSO4·5H2O→CuO+SO2↑+H2O↑CuCO3·Cu(OH)2250~270℃→CuCO3+CuO+H2O↑CuCO3560~600℃→CuO+CO2↑H2O(液)→H2O(汽)↑2、阴极铜加入炉内熔化,对浸涂法,铜板加入工频感应熔化炉内,熔体在电磁感应作用下不断运动,铜液中杂质元素间及碳层和保护氨气中的氢元素之间(一般木炭覆盖层厚100~150mm;炉内充入含有2%氢的氮气会发生一系列化学反应,如下4CuO1025℃→2Cu2O+O2↑4Cu+O2≡2Cu2OCu2O+Me←→MeO(造渣)+2Cu(Me—金属杂质)2Cu2O+Cu2S≡6Cu+SO2↑Cu2O+H2≡2Cu+HO2↑Cu2S+H2←→2Cu+H2S↑2Cu2O+C≡4Cu+CO2↑SO2+C≡S+CO2↑2Me+C≡2Me+CO2↑无氧铜杆无氧铜杆的生产方法之生产线参数?下面说的是浸涂法的生产线参数。
1、表格化:现场工艺控制。
现代化生产线的有效管理方法之一,是采取表格化的形式,实行现场工艺控制。
无氧铜管的制造技术介绍
无氧铜管的制造技术介绍无氧铜管,是一种因为其材质优良而被广泛使用的制品。
它主要由纯铜制成,具有良好的导电性和导热性能,同时还具有良好的机械性能和耐腐蚀性能。
本文将介绍无氧铜管的制造技术。
原材料和设备原材料制造无氧铜管所需的原材料主要为铜锭和包覆材料,其中铜锭应该是纯度高达99.99%的无氧铜,包覆材料则包括滑石粉、石棉等。
设备制造无氧铜管需要的设备主要包括铜管生产线和包覆机械。
具体包括铜管生产线,炉子,轧机,冷却设备,检测设备和塑料包装机械等设备。
制造工艺铜管生产线铜管生产线的主要作用是利用原材料铜锭进行铸造、轧制、拉伸等加工过程,最终得到无氧铜管。
铜管生产线可以分为铸造线和轧制生产线两个部分。
铸造线铸造线是将铜锭加热至一定温度,使其变为液态,然后沿着流道注入到模具中,通过冷却,最终形成无氧铜管的过程。
铜管经过铸造后的表面质量相对较差,因此还需要进行轧制或拉伸的过程。
轧制生产线轧制生产线是使铜管经过一系列轧制设备后,逐渐得到所需要的管径、壁厚和长度,以及较好的物理和机械性能。
具体工艺流程包括:到卷——辗轧——减径——水冷——拉伸——颠圆等。
包覆材料和包覆机械包覆材料主要是为了减少制造过程中对铜管的磨损和避免空气中的氧气对无氧铜管的氧化而引入的材料,其成分一般为滑石粉或石棉。
而包覆机械则将铜管表面涂覆上包覆材料,并在后续的工艺中进行处理。
质量控制无氧铜管的质量控制主要包括外观质量、化学成分、物理性能等多个方面。
出厂前还需要对产品进行检测试验,包括焊接性、弯曲性、压力性能等项目。
结论本文介绍了无氧铜管的制造技术,主要包括原材料和设备、制造工艺、质量控制等。
无氧铜管具有良好的导电性和导热性能、机械性能和耐腐蚀性能,可以广泛应用于电力、电子、冷却和加热等领域。
无氧铜和磷脱氧铜
无氧铜和磷脱氧铜一、引言铜是一种广泛应用的金属,具有良好的导电、导热、耐腐蚀等性能。
在铜的生产和应用过程中,常采用不同的方法来改善其性能。
无氧铜和磷脱氧铜是两种常见的铜材料,它们在性能和应用方面有一定的差异。
本文将对无氧铜和磷脱氧铜的性能、制备方法及应用进行介绍。
二、无氧铜1.性能:无氧铜是一种纯度极高的铜材料,其氧含量很低,不超过0.02%。
无氧铜具有优良的导电、导热性能,抗腐蚀性能也较好。
此外,无氧铜的强度和硬度较高,耐磨性好。
2.制备方法:无氧铜的制备方法主要包括真空熔炼、电解精炼和粉末冶金等。
真空熔炼是无氧铜的主要制备方法,通过在真空条件下熔化铜原料,可以有效地去除铜中的氧元素。
3.应用:无氧铜主要应用于电子、电气、通信等领域,如制作电缆、电线、变压器等。
由于其高纯度和优良的性能,无氧铜在高端制造领域具有广泛的应用前景。
三、磷脱氧铜1.性能:磷脱氧铜是一种含磷量较低的铜材料,其磷含量一般在0.02%至0.2%之间。
磷脱氧铜具有良好的导电、导热性能,抗腐蚀性能也较好。
此外,磷脱氧铜的强度和硬度较高,耐磨性好。
2.制备方法:磷脱氧铜的制备方法主要包括熔炼、铸造和挤压等。
在熔炼过程中,通过添加磷元素,可以使铜中的氧元素与磷形成化合物,从而实现脱氧。
3.应用:磷脱氧铜主要应用于电子、电气、通信等领域,如制作电缆、电线、变压器等。
由于其含磷量较低,磷脱氧铜在性能上优于普通铜,因此在高端制造领域具有广泛的应用前景。
四、无氧铜和磷脱氧铜的区别1.纯度:无氧铜的纯度较高,氧含量低于0.02%;而磷脱氧铜的纯度相对较低,磷含量在0.02%至0.2%之间。
2.性能:无氧铜的导电、导热性能略优于磷脱氧铜,但两者的抗腐蚀性能、强度和硬度等性能相差不大。
3.制备方法:无氧铜主要通过真空熔炼等方法制备,而磷脱氧铜主要通过熔炼、铸造和挤压等方法制备。
4.应用:无氧铜和磷脱氧铜在应用领域上有所重叠,但无氧铜更适用于高端制造领域,如电子、电气、通信等;而磷脱氧铜则更适用于一般工业领域。
无氧铜生产新工艺及设备
42资源再生 2009/03T技术echnology无氧铜(OFE)的生产在铜加工行业中是工艺较难掌握、对设备和生产控制要求较高的一种生产工艺。
目前国内还没有自行设计制造大型的无氧铜生产线。
通过对引进无氧铜生产线的学习和研究,对我国铜加工行业的水平提升有深远意义。
一、无氧铜的生产工艺及特点无氧铜是一种高品质的铜,其氧含量少于5×10-6,氢含量低于1×10-6。
生产无氧铜产品需要特别的前提条件:首先,必须用A级的电解铜,要确保其中所含的其他元素在规定的范围之内;其次,电解铜要预热,防止吸附湿气;第三,熔化炉中的液面上覆盖了一层10cm厚的木炭,木炭要经过煅烧,目的是防止液面与空气接触。
因为熔化炉中的气氛通常含少量的氧,且电解铜加料时,加料口是开着的,因此保持熔化炉内气氛呈正压是很重要的。
传统无氧铜生产工艺是采用长流槽内通入一氧化碳,还原铜液中的氧。
这种工艺缺点是设备较多,占地面积大,属于20世纪70年代的技术。
引进的先进无氧铜生产工艺则是使用无氧铜生产新工艺及设备On New Technology and Equipment for Oxygen-Free Copper Production□文/吕 杰摘 要:介绍了引进的无氧铜生产新工艺及设备,叙述了该生产工艺的特点、生产过程和主要设备构造。
关键词:无氧铜;生产工艺;熔化炉;铸造炉A b s t r a c t : T h i s a r t i c l e i n t r o d u c e s t h e n e w t e c h n o l o g y a n d e q u i p m e n t o f o x y g e n -f r e e c o p p e r p r o d u c t i o n b y i l l u s t r a t i n g t h e c h a r a c t e r i s t i c s o f p r o d u c t i o n p r o c e s s a n d m a j o r m e c h a n i c a l c o m p o n e n t s.K e y w o r d s : o x y g e n -f r e e c o p p e r ; p r o d u c t i o n t e c h n o l o g y ; m e l t i n g f u r n a c e ; c a s t i n g f u r n a c e精炼气站,配合在熔化炉和铸造炉底部的透气砖,通过使用一氧化碳达到进一步减少残留氧含量的目的。
无氧铜的生产技术 150509125
无氧铜的生产技术王稳常熟理工学院(215500)摘要:无氧铜是一种高传导性纯铜,它与一般紫铜相比具有纯度高,含氧量少等特点,具有高导电、导热性及良好的抗氢脆性和优良的加工性能、焊接性。
在电气、通讯行业、电真空领域具有特殊而广泛的用途。
关键词:无氧铜生产技术应用Abstract:Oxygen-free copper is a highly conductive copper, copper compared with the general has the advantages of high purity, with low oxygen content characteristics, with high conducyivitythermal conductivity and good resistance to hydrogen embrittlement and excellent processing performance, welding, electrical, communications industry, electric vacuum field with special and a wide range of uses.Key words :Oxygen-free copper production technology application1.前言1.1 无氧铜的基本信息无氧铜是一种高传导性纯铜 ,在化学成分上具有纯度高 ,杂质含量少 ,尤其是含量很低的特点。
因此 ,它具有优良的导电、导热性能 ,导电率可高达102 % IACS ,被广泛用于电子、讯行业。
目前 ,随着我国在微电子和真空电子器件等高科技领域的发展 ,市场对无氧铜材质提出的要求也越来越高。
1.2 无氧铜的分类根据含氧量和杂质含量,无氧铜又分为一号和二号无氧铜。
一号无氧铜纯度达到99.97%,氧含量不大于0.003%,杂质总含量不大于0.03%;二号无氧铜纯度达到99.95%,氧含量不大于0.003%,杂质总含量不大于0.05%。
- 1、下载文档前请自行甄别文档内容的完整性,平台不提供额外的编辑、内容补充、找答案等附加服务。
- 2、"仅部分预览"的文档,不可在线预览部分如存在完整性等问题,可反馈申请退款(可完整预览的文档不适用该条件!)。
- 3、如文档侵犯您的权益,请联系客服反馈,我们会尽快为您处理(人工客服工作时间:9:00-18:30)。
第四章工艺技术方案4.1工艺技术方案本项目采用的原材料为含铜量99%的电解铜,选用目前国内先进的蓄热式熔化炉和中频炉,用上引法连铸工艺方法生产氧的含量不大于0.02%,杂质总含量不大于0.05%,含铜量99.5%以上无氧铜杆。
4.2工艺流程简述1、生产准备本项目使用的电解铜在江西省内购买。
图4-1 项目生产工艺流程图2、上引法连铸工艺流程本项目采用上引法连铸工艺生产无氧铜杆。
上引法连铸铜杆的基本特点是“无氧”,即氧含量在10ppm以下。
上引法与连铸连轧和浸涂法相比,其特点是:1)由于拉扎工艺和铸造工艺不是连续的,拉扎是在常温下进行的,不需要气体保护,钢材也不会被氧化。
因此设备投资小,厂房布置也灵活。
2)单机产量变化范围大,年产量可以从几百吨到几万吨,可供不同规模的厂家选用不同型号的上引机组。
此外,由于连铸机是多头的,可以很容易的通过改变铸造规格(铸杆直径),来改变单位时间的产量,因此其产量可视原材料的供应情况和产品的需求情况来确定,便于组织生产、节约能源。
3)只需更换结晶器和改变石墨模的形状,即可生产铜管、铜排等异型铜材,并可在同一机器上上产不同规格、品种的铜材,灵活机动,这是上引法的中最大特点。
上引法连铸工艺流程:原料通过加料机加入融化炉进行熔化、氧化、扒渣处理后,熔融的铜液经过一段时间的静置还原脱氧并达到一定的温度后,通过有CO气体保护的流槽经过渡腔(铜液在此进一步还原脱氧、清除渣质),进而平稳的流入中频炉保温静置,铜液的温度由热电偶测量,温度值由仪表显示,温度控制在1150℃±10℃。
连铸机固定于中频保温炉的上方,连铸机铜液在结晶器中快速结晶连续不断地生产出铜杆,最后经双头挠杆机等辅助设备装盘成产品。
⑴加料:原料一般用加料机加入,炉头多加、炉尾少加。
加冷料时要使铜料距炉顶及烟道口有一定距离,以保证燃料燃烧和炉气流动的顺畅。
加料时要保证炉膛有足够高的温度,一般应达到1300℃以上,炉内应保证零压或微负压。
⑵熔化:熔化作业系在氧化气氛下进行,一般炉膛温度保持在1300~1400℃以加速冷铜料的熔化,在熔化过程中定期向炉内已熔化的铜液中插入一根风管,鼓入压缩空气剧烈地搅动熔体以加速熔化过程,这时也会有部分杂质熔化,形成炉渣于熔体表面,待熔体大部分熔化完,即可进行氧化操作。
⑶氧化:其要点是增大烟道抽力(-80~-100Pa),提高炉内空气过剩系数(ξ=1.2~1.4),使炉内成氧化性气氛。
用直径为ф18~50mm的钢管2~3根向熔体内鼓入0.3~0.5MPa的压缩空气,进行氧化作业,为减少钢管熔入铜中的消耗,钢管外用耐火材料包裹。
为增加氧的利用率,钢管应尽可能深插,插入角度为45°~60°,插入深度为铜熔体深度的2/3。
氧化期的炉膛温度在1250℃左右,以保证铜液温度为1150℃~1180℃,有利于杂质的氧化。
⑷扒渣:扒渣是将造渣后的杂质通过扒渣过程将其除去,铜面控制是扒渣操作的关键。
铜液面过低,给以后扒渣作业造成困难,床能率低;铜液面过高,易出现侧门、渣口跑铜事故。
为控制好渣含铜,应及时进行扒渣作业,避免干渣转变为稀渣,生产过多的氧化亚铜。
⑸保温静置:熔融的铜液流入中频炉保温静置、还原脱氧并达到一定的温度后,进而处于保温状态,铜液的温度由热电偶测量,温度值由仪表显示,温度控制在1150℃±10℃。
中频保温炉引杆腔铜液表面用焦炭覆盖,覆盖厚度为40-60mm,结晶器周围厚度为80-100mm。
⑹结晶出杆、装盘:连铸机固定于中频保温炉的上方,连铸机铜液在结晶器中快速结晶连续不断地生产出铜杆,最后经双头挠杆机等辅助设备装盘成产品。
1)结晶器准备a.对新的和使用期超过半月的结晶器,进行水压试验,水压为0.5-0.6Mpa,保持15分钟不漏水。
b.装配石墨模:把检验合格的石墨模,旋入结晶器,端面到位。
c.结晶器头部包上8mm厚硅酸铝纤维毯或隔热套,用玻璃纤维带扎紧,端面垫上一层硅酸铝纤维毯圈,然后装护套,在石墨模与护套的缝隙用填料或石棉线填实,以防铜液钻入。
填料配方:耐火粘土95%+水玻璃3%,并合成团。
d.结晶器上口装上石棉盘根,并用装有引锭头的前半节引杆通过,拧紧压套,引锭头端面距石墨模端面5-10mm。
e.结晶器进出水管接上,通少量冷却水,检查管路系统是否畅通,然后放在炉口上预热10分钟以上安装使用。
2)连铸机准备:调整液位跟踪系统的位置,保证结晶器安装后石墨模插入液面的深度为140-160mm。
操作时确认铜液液面离碳化硅保护套上沿距离为30-40mm左右。
3)引杆操作程序:a.结晶器就位,插入铜液,接上后半节引棒,压紧牵引轮,开始引棒。
b.调节冷却水量,¢14.4-¢20mm结晶器进出水温保持在15℃左右。
¢8mm结晶器进出水温保持在6-10℃左右,进水温度最高不能超过35℃,在30℃左右为宜。
c.铜杆引出后,将引棒分节拆下,并通过导轮进入收线系统。
4)铸杆日常操作:a.¢14.4-¢20mm铜杆牵引速度400-700mm/min为宜,¢8mm铜杆牵引速度1800-2800mm/min为宜。
b.经常检查铜杆表面质量,监测冷却水温度,结晶器插入深度,液位跟踪系统工作状况,如遇异常情况,及时排除。
(7)收线1)收线时将引锭头头部切除,将铜杆通过限位装置,穿过并夹紧收线导轮,引入收线框内。
2)经常注意限位装置工作情况,在限位装置失灵情况下,临时利用收线机上的操作按钮进行人工操作,并及时排除故障。
3)收线框装满后,吊出铜杆,挂上产品跟踪卡,标明日期、炉次、生产班组、重量等项。
(8)水系统控制1)水系统供水,¢14.4-¢20mm结晶器水压为0.2-0.3Mpa,水套、线圈为0.18-0.2Mpa。
¢8mm结晶器水压为0.28-0.35Mpa,水套、线圈为0.18-0.2Mpa。
2)水池水温用冷却塔调整,进水温度控制在30±5℃。
3)当临时停电或水泵发生故障,应在一分钟内打开备用水阀门,并关闭原来水阀门,以保证结晶器及水套和线圈的冷却水不间断。
(8)气压控制对新式¢8上引机组,其上引连铸机铸杆压紧、收线机收线、排线,采用气缸压紧。
其气压控制在:连铸机:0.15-0.25Mpa 收线机收线:0.2-0.3Mpa,排线:0.15-0.25Mpa。
(9)安全生产1)操作者应按规定穿戴好劳动防护用品,遵守设备安全操作规程。
2)打开炉盖后不要太靠近炉口,以防一氧化碳气体燃烧时火焰伤人(每次待一氧化碳气体燃烧过后再上去操作)。
3)每班应经常检查机组设备运行是否安全可靠。
4)严禁将潮湿未烘干的工具浸入铜液,以免铜水爆炸造成事故。
5)结晶器安装和取下时,注意防止冷却水进入炉内。
6)发生事故应立即采取措施,并报告有关人员及时处理。
(10)检查铜杆质量就符合GB3952-2008《电工用铜线坯》中无氧铜杆规定。
4、余热回收利用为提高清洁生产水平,贯彻国家关于节能减排的要求,本项目应对熔化炉烟气和中频炉烟气进行余热回收。
一般地,熔化炉出口烟气温度在1000-1200℃,中频炉出口烟气温度在800-1000℃,均具明显的热回收价值。
对没有蒸汽需求的再生铜工厂,通常采用“预热助燃风(纯氧/空气),立足降低本体消耗,节约一次能源”的余热利用方式。
熔化炉烟气余热利用方案:采用两段式换热器进行出炉烟气与入炉助燃风的热交换,降温(降至200℃)后的烟气再进入布袋收尘器。
通过两段式换热器预热入炉助燃风,不但可节省燃料消耗,而且还可缩短熔化炉的操作周期,提高设备利用率。
据统计,两段式换热器可将入炉助燃风预热至400℃左右,节省约20%的燃料消耗和缩短1.5小时的操作周期(一般总时间为18小时)。
中频炉烟气余热利用方案:与熔化炉烟气余热利用方案类似,但因为烟气温度相对较低,通常采用一段管式空气预热器进行烟气与入熔化炉助燃风的热交换。
据统计,经预热器的入熔化炉助燃风温度可达300℃,可节省能源消耗约10%。
4.3主要生产设备方案4.3.1 设备选择的基本原则1、生产性原则:选择生产设备时,注重设备的模块化、标准化、高速化、自动机械化,以提高设备的生产率;2、可靠性原则,设备要求安全可靠,零件的耐用性好、通用性强,设备能够生产高质量产品,要求设备故障率小,准确性高;3、维修性原则,选择可修性、设备的结构简单,零部件模块化设计,零部件通用性强,可迅速拆卸,易于检查,实现标准化和通用化;4、节能性原则,设备要节约能源消耗;5、成套性原则,机器设备要配套,形成整条生产线,尽量选择同一厂家产品;6、环保性原则,设备的噪音和排放的有害物质应达到国家环保限制指标和要求;7、灵活性原则,尽可能做到设备结构紧凑,重量体积小、轻,操作灵活方便,通用性强,可适应工艺相近的产品转换,转换操作简单方便。
4.3.2 主要设备方案本项目采用蓄热式熔化炉作为本项目的主要生产设施,其燃料为重油,该项目原料为电解铜,设备能进一步去除电解铜中的氧和其它杂质,不含硫,因此,选用蓄热式熔化炉处理是可行的,且选择蓄热式熔化炉作为熔炼炉具有适应性强、回收率高等特点,符合《铜冶炼行业准入条件》的要求。
上引法无氧铜杆连铸机组用于生产长度光亮的无氧铜杆。
和传统的铜锭压延生产黑铜杆相比,上引法无氧铜杆新工艺具有工艺技术先进,产品质量很好,单位能耗低,生产品种及规格灵活多样,适应性强,没有三废污染,投资少等特点。
本项目选用主要设备清单见表4-1。
工艺设备优点如下:⑴加料、扒渣方便。
可在炉体侧面靠近平台处设置加料门和渣门,炉料可用加料车方便快速的加入。
炉渣门靠近渣线设置,既可倒渣,也可方便扒渣;⑵热效率高。
炉体紧凑、密闭,氧化管道固定在炉体上,作业时不需要打开炉门操作,热量外泄少,漏入的冷空气少。
在炉体上布置了多块透气砖,通入氮气搅拌,加速了传热传质,缩短操作时间,节省燃料消耗;⑶安全性高。
由于炉体可以转动且氧化、还原管道固定在炉体上,避免了人工持管操作可能发生的安全事故,减少了工人的劳动强度;遇到故障时炉子可迅速转到安全位置,避免“跑铜”事故的发生,操作安全;⑷环保条件好。
炉体密闭性能好,氧化时不需要打开炉门操作,减少了烟气外逸;借助炉体转动可以控制氧化管道的埋入深度,加上透气砖的氮气搅拌作用可提高还原剂的利用率,减少黑烟生成;在炉后设置有完善的烟气处理系统,烟气通过烟罩导入双体结构的二次燃烧室,烧尽可燃物后进余热锅炉回收余热,再进入布袋收尘达标后排放;⑸熔化炉采用富氧助燃的燃烧器。
采用富氧助燃,烟气量仅为空气助燃时的20%,烟气带走的热量少,燃料消耗低,烟气处理系统可大为缩小,减少投资和运行费用。
⑹连铸机是实现上引连铸的主要设备。
它由牵引机构、液位跟踪和结晶器三大部分组成。
牵引机构由交流伺服电机和牵引辊轮等组成,它可实现每分钟0~1000次的间歇运动并通过牵引辊轮将铸杆连续上引出来,每组牵引机构可带动5付牵引辊轮,分别牵引5根铸杆,并通过更换结晶器生产其它规格的铜杆;液位跟踪系统可保证连铸机上结晶器插入铜液的深度相对稳定,确保连铸生产的连续性;结晶器可将液态的铜快速冷却成固态铜并实现热交换,每根结晶器都能单独更换和控制而不影响其它结晶器的正常工作。