汽车保险杠模具结构知识
保险杠模具设计结构原理分析

斜顶中斜顶!
此地方采用斜顶中 斜顶机构!
-7-
详细说明见下图: 斜顶中的推块还有斜顶都是通过此轨迹来实现!
-8-
此推块轨迹
1.30那行程为是大斜顶顶出30时产品不跟着大斜顶方向变形,因为产品侧边有 两斜顶在顶出30时让出了位置,好让产品在下面一段顶出时变形.
2.70那行程是产品变形阶段,变形后前模可以开模;
3.150行程后大斜面中间骨位脱离后,大推块可以后里面运动,同时小推块向外
面运动顶开产品脱离扣位!
-9-
此推块轨迹
-10-
此斜顶轨迹
10 度
-11-
斜顶 (此斜顶采用二次顶出机构)
直顶
此扣位采用直顶中斜顶机构
-12-
侧边扣位采用斜顶机构脱模! 分三个斜顶进行实现!
斜顶
-13-
直顶(在二次顶出机构上面) -14-
-16-
经过第一段顶出后,产品还停留在大 直顶上,还有两段扣位不能够脱模;故 还需要用两个油缸实现二次顶出!从 而使产品从直顶中脱模!
(二次顶出行程为50MM)
二次顶机构 (油缸)
-17-
模具导向机构 导向机构采用两侧方导柱+1圆导柱机构
方导柱 为了不影响机械手取件,故1圆导柱设在地侧方向!
圆导柱 -18-
-1-
产品排位
2450 2750
1000 1500 -2-
模胚厚度
50 100
80 120 734
1785 369
80 -3-
产品两头采用直顶+斜顶 的机构进行脱模! 详细结构见下一页:
-4-
13度 顶出行程170MM,行程为39.2MM
直顶 斜顶
-5-
前保险杠知识点

2 分析前保本体的出模方式:前保本体的模具构造是外饰目前最 复杂的,主要原因是目前对产品外观的高品质要求,基本都需 要做内分型,内分型前后模分模位置在轮眉配合翻边根部,前 模是个倒扣模具,利用两边Y向斜顶拉住倒扣面强行变形,脱出 前模倒扣范围,前模退出,再继续顶出,两侧Y向斜顶走出出模 范围,产品需将倒扣量控制在10mm范围内。避免变形量太大将 产品拉断。其余有与轮眉配合出法向斜顶和与机盖配合Z向斜顶 和一些狗窝卡扣结构小斜顶。 简述保险杠的的安装形式:保险杠在供应商处装成总成,为二 级装配,之后在线下与雷达摄像头前保线束等电器件装成一个 大的集成,然后再总装线上将前保左右安装支架装上翼子板。 然后将保险杠拍进翼子板完成预安装和与定位,之后打好上下 螺栓,目前也有部分车型增加与前防撞梁安装支架。上下螺栓 大部分打在水箱上下横梁上,目前慢慢发展为前端模块。
3
前保知识点
4
保险杠材料:保险杠本体材料绝大部分用改性PP,改性方式基 本为PP+EPDM-TD20,EPDM为橡胶材料,增加PP的柔韧性,在加 EPDM之后,材料的刚度,强度,硬度等力学性能会变差,之后 增加百分之二十的滑石粉调整材料的力学性能至合理均匀状态。 支架材料为POM,具有非常好的强度、刚度、硬度和自带润滑 性。电镀亮条材料为ABS,材料本身具有电极性和可腐蚀性。格 栅很多采用ASA,材料具有非常好的耐候性,非常适合于格栅长 期进风散热的工作环境。
5Leabharlann 6避免卡接结构的擦穿结构:对于回型插片结构卡扣,在卡结结 构两侧做1mm料厚与卡接面平齐,将分型线控制在卡接面上, 既有效的控制了卡接面又避免了模具擦穿。
保险杠周边配合情况:与机盖为运动间隙,一般做到6mm以上; 与翼子板为外观间隙,一般做到0.3mm;与轮眉为外观间隙,一 般为1mm;与防撞梁为安全间隙,推荐法规要求与保险杠蒙皮 75mm。保险杠自身配合间隙:上下本体,上下格栅等大件一般 要求为1mm,最小0.5mm。亮条、雾灯装饰件、拖车钩堵盖等小 件一般为0.5mm,最小为0.3mm。电动车充电口运动间隙为2mm。
保险杠模具设计总结
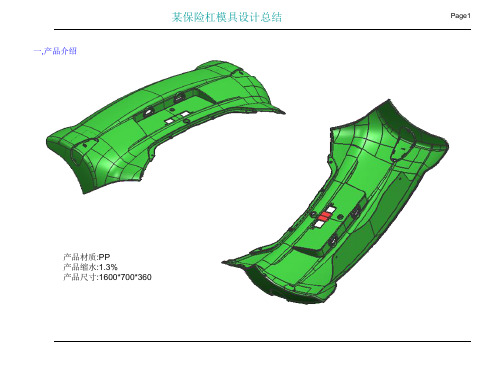
某保险杠模具设计总结
斜顶
顶块 此产品的顶出由6个斜顶+6个顶块组成.
Page11
六,温控系统
某保险杠模具设计总结
1,前模冷却系统
天侧
前模共6组运水
Page12
2,后模冷却系统
某保险杠模具设计总结
天侧
后模共6+6(其中包括斜顶,顶块运水)
Page13
3,斜顶,顶块冷却系统
某保险杠模具设计总结
Page14
A LIFTER 1 A B
C
LIFTER 6 D 行程22.1mm
D
行程9.43mm C
LIFTER 5
后模斜顶结构图PaLeabharlann e6LIFTER 4 25度
LIFTER 3
LIFTER1和LIFTER4,LIFTER2和LIFTER3为镜像关系,以下只描述其中一件. 模具顶出行程为180mm
某保险杠模具设计总结
三,模具结构
某保险杠模具设计总结
Page3
模具结构:4个滑块(两个前模滑块,两个后模滑块),六个斜顶,六个直顶块.
1,前模滑块
某保险杠模具设计总结
此滑块用油缸驱动,滑块行程36mm, 油缸行程需要104mm,实际定购油缸 行程为110mm.
30°
20°
Page4
行程示意图
行程示意图
2,后模滑块
一,产品介绍
某保险杠模具设计总结
Page1
产品材质:PP 产品缩水:1.3% 产品尺寸:1600*700*360
二,热流道系统
某保险杠模具设计总结
流道调节镶件
Page2
此产品采用四点开放式胶口, 利用流道调整镶件调节产品 熔接线,经moldflow和T1试模 验证,基本可以满足客户外观 要求及成型周期(60s)要求.
汽车保险杠模具设计
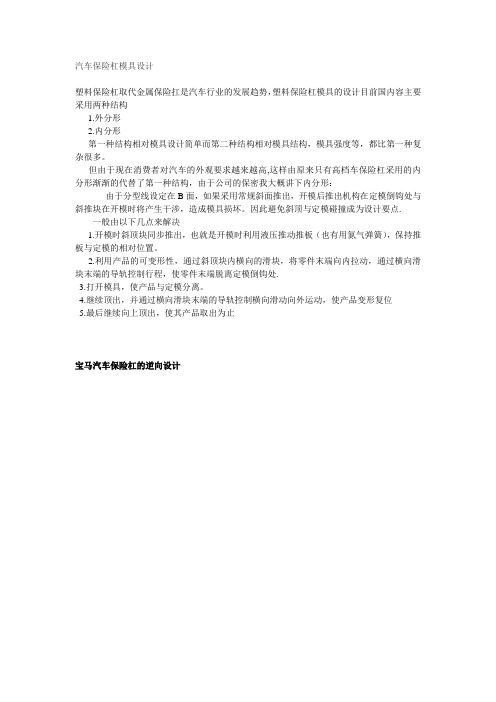
汽车保险杠模具设计
塑料保险杠取代金属保险扛是汽车行业的发展趋势,塑料保险杠模具的设计目前国内容主要采用两种结构
1.外分形
2.内分形
第一种结构相对模具设计简单而第二种结构相对模具结构,模具强度等,都比第一种复杂很多。
但由于现在消费者对汽车的外观要求越来越高,这样由原来只有高档车保险杠采用的内分形渐渐的代替了第一种结构,由于公司的保密我大概讲下内分形:
由于分型线设定在B面,如果采用常规斜面推出,开模后推出机构在定模倒钩处与斜推块在开模时将产生干涉,造成模具损坏。
因此避免斜顶与定模碰撞成为设计要点.
一般由以下几点来解决
1.开模时斜顶块同步推出,也就是开模时利用液压推动推板(也有用氮气弹簧),保持推板与定模的相对位置。
2.利用产品的可变形性,通过斜顶块内横向的滑块,将零件末端向内拉动,通过横向滑块末端的导轨控制行程,使零件末端脱离定模倒钩处.
3.打开模具,使产品与定模分离。
4.继续顶出,并通过横向滑块末端的导轨控制横向滑动向外运动,使产品变形复位
5.最后继续向上顶出,使其产品取出为止
宝马汽车保险杠的逆向设计。
汽车保险杠模具常见机构分析

开发研究汽车保险杠模具常见机构分析杜利静(江苏敏安电动汽车有限公司,江苏南京211102)摘要:本文整理了汽车保险杠模具常见的机构及动作,通过清晰易懂的简易图介绍了多种模具机构及动作,将多种机构不同点进行分析,有利于零件工程师与模具工程师学习多种模具成型特点。
关键词:保险杠模具;外露式分模线;隐藏式分模线保险杠是汽车车身上一种较大的外覆盖零部件,是汽 车前后部的保护装置,是现代汽车结构的重要组成部分。
保 险杠作为汽车重要的被动安全件、外观件,表面质量要求比 较高,周边配合零件多,并且在主要视野区域,对整车的外 观影响很大。
加之保险杠零件大,在保险杠零件设计过程 中,模具设计显得非常重要,常见保险杠图示见图1,文中 以简化图示来讲解,如图2所示。
图1某车型保险杠图2保险杠简化图示1注塑模具的结构注塑模具分为动模和定模2个部分。
开模时,动、定模 在该部分分离,分离的位置叫分型面,在零件上,由于分型 表面能看到比较明显的分模线痕,称为分模线或分型线,分 模线在开模方向上的投影与塑件在该方向上投影的外轮廓 线重合,开模方向也叫拔模方向,在零件设计中,要根据零 件的表面处理及结构成型深度,设计出拔模角度,斜度a则 为拔模角。
滑块是在模具的开模动作中能够按垂直于开合 模方向或与开合模方向成一定角度滑动的模具组件,当产 品结构不能正常脱模的情况下就得使用滑块了。
拔模方向抽芯方向图3模具拔模示意图处理,分型线痕迹也无法避免,且增加了修边工时,不仅不 能保证表面质量,也不利于成本的降低。
图4保险杠配合断面示意图隐藏式分模线是优化安装面位置,将分型线设置在非 可见的B面,如图5所示,保证表面外观质量,减少分模线 处产生飞边的可能性,提升合格率,还能使保险杠与翼子板 配合间隙更小。
可视面(A面)图5调整安装面示意图3 保险杠模具分类由于保险杠及其外观的要求不同,加之考虑模具成本、供应商工艺水平等,保险杠模具分成多种。
汽车保险杠

3.汽车保险杠仿真分析
根据建模方法和功能主要可以分为两类: ① 采用多刚体系统动力学理论对碰撞伤害进 行模拟的软件。 ② 采用显式有限元(FEM)理论进行建模的 软件,比如 LS-DYNA3D、PAM-CRASH、 ABQUES等。
3.汽车保险杠仿真分析
显示非线性有限元是汽车碰撞模拟计算 机中常用的方法之一。目前国内使用较多 的两种软件是LS-DYNA3D和PAM-CRASH。 其中PAM-CRASH在汽车被动安全性领域 分析中的应用是大家公认比较成功的。
现代塑料汽车保险杠通常由热塑性聚碳 酸酯材料制造而成的。
2.保险杠的结构设计
在欧盟ECE法规通常要求设计达到承 受得住时速4km/h的物体撞击、北美洲的 IIHS规范要求承受得住时速8km/h物体撞击。 如果汽车保险杠可以承受时速高达15km/h 的低速碰撞,且除汽车保险杠底座系统外 对车身结构不造成损坏,那对消费者、保 险公司和汽车制造商都具有好处。
Hale Waihona Puke 2.保险杠的结构设计要满足吸能要求,在汽车保险杠底座 安装位置采用挤压变形管或碰撞吸能盒, 或者汽车保险杠具有能量吸收和即时恢复 的回弹能力。
2.保险杠的结构设计
3.汽车保险杠仿真分析
汽车被动安全性计算机仿真方面,目 前具有代表性的几个商品化软件有: • 美国LSTC公司开发的LS-DYNA3D软件; • 荷兰国家应用科学研究院(TNO)开发的 MADYMO软件; • 法国ESI公司开发的PAM-CRASH软件。
汽车保险杠
李升东 2013.12.30
目录
1. 保险杠的作用和结构类型 2. 保险杠结构设计 3. 汽车保险杠仿真分析
1.保险杠的作用和结构类型
1.1 汽车保险杠的作用 • 低速碰撞时保护相关部件的作用 • 事故中行人保护的作用 • 符合空气动力学的要求 • 装饰和美化作用
原创经典详细后保险杠模具设计方案PPT演示文稿

5°
11
前后模开模动作
前模
增加定位,方便修理内 分型线处段差。
• 左图为内分型线脱模方案,而产 品主要是受大斜顶A的行程来变 形,大斜顶A的顶出角度为5°,前 模内分型倒扣距离为2.2MM.根 据分析,斜顶顶出80MM时,行程 为7MM,前模倒扣即可脱离,前后 模完全分开.
后杠产品排位图
TOP
1:根据模具排位图可以确定注塑压力在产品投影面积上所受的力是否在
模具中心上。
1
2:确定模具的模架尺寸
• 运水在主视图的排布,由于PP材料对冷却要求效高,一般需要控制到±5°,
所以我们会根据:1.5D≤A≤2.5D; 2.5D≤B≤3.5D设计运水。
2
• 根据侧视图,我们可以确定各模板的厚度,顶出油缸的安装
斜度c为15°
LB LA
• 由于脱模需要,斜顶B运动方 向为水平14°夹角方向,斜 顶E运动方向为垂直方向,为 避免两斜顶相干涉,所以用 斜度c做让位。
• 斜顶B的顶出角度设计为10°。 SB(斜顶B行程)=TAN 10°XS
(顶出行程) LA= TAN 14°XSB LB= TAN 15°X(LA /SIN14°) • 斜顶E的顶出角度设计为5° SE(斜顶E行程)=TAN 5°XS
此斜度b为25°
SA(斜顶A行程)=TAN 5°XS (顶出行程)
SC(斜顶A行程)=TAN 9°XS (顶出行程)
LA= TAN25°XSA
LC= S8°XSB
LC
LB
LA< LB- LC 由以上推算出两斜顶不会干涉。
7
E B
斜顶A行程( SB)
保险杠模具设计总结

1-2、产品的进胶点位置
最大距离不能超过400mm
2-1、产品分型面的分类
●内外分型面的种类:内分型的产品。
可以从虚线看出有两种不同 的分型,第一种是前模与斜顶 相扣;第二种是前模与斜顶不 相扣,所以结构上也不同。
斜顶 第一种6、模具两头结构与强度要求
斜顶背面角度比 顶出角度小1--2°
50mm
140mm-160mm
140mm
150mm 300--50mm
顶出角度小12 --14 °, 让顶出距离尽可能小。
7、斜顶加推方结构
此处需要预留推 方杆空间
总行程与顶针 板行程相同,弯 曲处行程需要 跟据前模倒扣 量定.原则上行 程越少越好!
前模
推方 后模
斜顶
当产品的变形距离太短的情况需 要产品留在前模取件,可以想像 把推方斜顶去掉,产品的变形弹 性就可以增加!!
4、产品的分型线位置
●产品内分型线位置
内分型就是产品的分型在必需在非外 观可见位置。
5、前模的倒扣量规范
前模内分型倒扣量控制在6mm以内 如果不行请改底部为外分型。
产品底部
容许抗拉应力=抗拉屈服应力/安全系 数;
模胚铸铁属于冲击载荷,安全系数 为15;
FC250的容许抗拉应力=25/15
=1.6[kgf/m㎡]
A
A
截面A处的尺寸为75mmX80mm,单条筋 截面积为6000m㎡;
铸铁FC250的抗拉强度屈服应力为 250MPa,也就是约等于25[kgf/m㎡];
根据拉伸载荷公式:抗拉载荷Pt=容许抗 拉应力X有效截面积
根据以上数据:
单边铸铁的载荷为Pt=2.5X6000
- 1、下载文档前请自行甄别文档内容的完整性,平台不提供额外的编辑、内容补充、找答案等附加服务。
- 2、"仅部分预览"的文档,不可在线预览部分如存在完整性等问题,可反馈申请退款(可完整预览的文档不适用该条件!)。
- 3、如文档侵犯您的权益,请联系客服反馈,我们会尽快为您处理(人工客服工作时间:9:00-18:30)。
主要内容一、保险杠模具基本结构、材料及结构审核二、保险杠产品细节设计对模具的影响三、保险杠产品分型面选取基本原则四、保险杠内分型模具实例讲解五、交流讨论六、培训小结一、保险杠模具基本结构、材料及审核1、基本结构:公司在模具知识方面已经做了很多的相关培训,大家对注射模具知识有了一定的了解,保险杠模具基本结构与其它的注射模具差不多,但由于汽车保险杠产品的特殊性,对模具结构的要求会有所不同,我们可以理解为特殊结构的模具。
2、保险杠模具常用材料:目前市场上模具钢材料比较繁多,有近百个品种,不同的刚材价格差别比较大,我们在模具材料选定时主要从a.经济性、b.硬度、c.抛光性能、d.加工性能、e.耐腐蚀性、f.耐久性等方面来考虑。
主要的模具钢供应商有瑞典一胜百、日本大同、舞钢、龙记(模胚)等。
针对保险杠模具常用的材料有:好的型腔用2738(预硬钢)的材料、型芯用P20(需调质),材料的硬度在28-32HRC;一般都是用P20材料,型芯用S55C钢(需调质),这些钢材都是加工性能都是很好的。
不管是2738、P20、S55C等刚材,都是要进行调质处理,调整后标准硬度在28-32HRC。
当然对模具的使用硬度越高越好,但硬度再高的话将很难加工。
像导柱、导套、耐磨块、锁紧块等零件对其硬度要求要高一些,一般的在55—60HRC。
3、保险杠模具设计图样审核要点:1)装配图审核。
零件的装配关系是否明确、配合代号标注的是否恰当合理、零件标注是否齐全、与明细表中的序号是否对应、有关的说明是否有明显的标记、整个模具的标注化程度如何;2)零件图审核。
零件号、名称、加工数量是否有明显标注、尺寸公差和行位公差标注是否合理齐全。
成型零件容易磨损部位是否预留了修模量。
哪些零件有超高精度要求,这种要求是否合理。
各个零件的材料选择是否合理,热处理要求和表面粗糙度要求是否合理。
3)制图方法审核。
其方法是否正确,是否符合有关规范表中(包括工厂企业的规范标准)、图面表达的几何图形与技术内容是否理解。
4、保险杠模具结构审核要点1)模具的结构和基本参数是否与注射机规格匹配;2)模具是否有合理的合模导向机构;3)分型面选择是否合理,有无产生飞边的可能,制品是否滞留在设有推出机构的动模(定模)一侧;4)模腔的布置与浇注系统设计是否合理。
浇口是否与塑料原料相适应、浇口位置是否恰当,浇口与流道的几何形状机尺寸是否合适、流动比数值是否合理;5)成型零部件结构设计是否合理;6)推出机构与侧抽芯是否合理,是否有干涉或碰撞的风险,脱模板是否会与动模咬死7)排气机构是否合理;8)是否需要温度调节系统,如果需要共热源和冷却方式是否合理,温控元件是否足够,精度等级如何,加热和冷却介质的循环回路是否合理;9)支承零部件结构设计是否合理;10)外形尺寸能否保证安装、紧固方式选侧得是否合理可靠,安装用的螺栓孔是否与注射动、定模固定板上的螺孔位置一致,压板槽附近的固定板上是否有紧固用的螺孔。
二、保险杠产品细节设计对模具的影响好的产品(品质)来源于非常完美的设计,有缺陷的产品设计不仅会降低产品的品质,同时给模具带来复杂的结构和模具加工的难度,生产效率会非常低下,报废率极高,浪费极大。
这就好比我们常说的一个人水平再高,也不可能把一个哑巴培养成歌唱家一样。
因此我倡导我们每一个工程师在平时的工作注重每个设计细节,真正的从设计上提高产品的品质。
2、保险杠强度及安装结构设计。
由于保险杠自身的重量比较重,结构比较特殊,装配、外观要求高,我们可以通过设计一些内部加强支架来保证保险杠的强度。
1、保险杠与自身配合件(大灯、格栅、装饰条、雾灯堵盖、大灯清洗剂堵盖等)有配合要求。
首先建议要求产品的脱模方向一致,前保一般的定义为整车坐标的-X 向,后保为X 向。
与翼子板、前大灯配合目前也有了一些比较成熟的结构。
3、一些小的细节对模具的影响。
A)CNC机加工的刀具路径需要一定圆角过渡,所以在产品设计时尽量避免直角过渡;B)模具薄壁处纵横比不宜过大;C)靠破、插破孔形状不宜太复杂;D)尽量避免侧抽芯分型。
三、保险杠产品分型面选取基本原则1、分型面设置一般原则:1)分型线不得位于明显影响外观的位置;2)开模时不能有死角(倒扣);3)位于模具易加工的位置;4)位于成品后加工容易的位置;5)位于不影响尺寸精度的位置;6)有利于浇注系统、排汽系统、冷却系统的设计;7)能碰穿时,尽量不要用插穿;8)分型面尽量平缓,不要有扭曲面,以便于模具加工;9)对易产生飞边、不宜配模的位置,尽量对产品设计进行检讨;10)装配要求较高的位置,要考虑将来修模的方向。
2、脱模斜度的选定:1)目的是为了方便产品从模具中能顺畅脱出而设置的;2)一般情况下1~3度,不能小于0.5度,在不影响产品外观和配合要求的情况下,角度越大越好(动模脱模斜度比定模大) ;3)插穿时其角度不要小于3度且形状不宜太复杂。
四、保险杠内分型模具实例讲解随着汽车工业的发展,消费者和汽车制造商对汽车,尤其是轿车的外观质量要求越来越高,保险杠作为轿车的主要外饰件,对保险杠的安装配合及其本体上的宽体饰条和镀铬饰条等塑件提出了更高的要求。
一些国外高档轿车如奔驰、宝马等,早在几年前就开始使用内藏式分型线的保险杠及相关塑件,国内汽车厂以大众为代表,自2001年所有的车型均采用内分型线保险杠,上海通用等其他汽车厂商也比较早的推出内分型线保险杠的车型。
我们公司由于没有做具体的要求及供应商水平不高等因数,保险杠内分型模具技术应用的不是很好。
希望通过不断的讨论和学习,把这一技术要求统一起来。
1、分型线外露与内藏的位置如图所示为典型保险杠零件的侧边端部与轮罩饰板相连处造型,A面为外部可视面,内翻边B面是轮罩饰板安装面,基本不可视。
传统模具设计中,为避免倒钩形成,分型面设置在A面与B面过渡圆角R外侧处,处于可视面。
由于模具制造精度及长期使用的磨损,分型线处经常出现错位及飞边,大大影响了制件的美观。
即使经过修边处理,但分型线痕迹无法避免,且增加了修边工时、产品的一致性差,不利于成本的降低。
而内藏式分型线模具将分型线设置在不可见的B 面,因此无论是加工的误差或是长期使用后产生的飞边,都不会影响产品的外观质量,既满足了主机厂的要求,又大大提高了产品的合格率。
2、内藏式分型线模具的结构以内藏分型线保险杠为例,由于分型线设定在B面,如果采用常规斜面推出,开模后推出机构在定模倒钩处与斜推块在开模时将产生干涉,造成模具损坏。
因此避免斜推块与定模碰撞成为设计要点。
解决的方法是:(1)开模时斜推块同步推出,也就是开模时利用液压缸推动推板,保持推板(推块、杆)与定模的相对位置;(2)利用塑件的可变形性,通过斜推块内横向的滑块,将零件末端向内拉动,通过横向滑块末端的导轨控制行程,使零件末端脱离定模倒钩处;(3)打开模具,使塑件与定模分离;(4)继续推出,并通过横向滑块末端的导轨控制横向滑块向外运动,使塑件变形复位。
模具的基本结构如图所示。
推杆5, 通过导轨6 与斜推块2 相连,斜推块2 的运动轨迹又通过导轨7控制。
当模具推板(未画出)推动推杆5,通过导轨6 和7的约束,使斜推块2沿导轨7的方向运动。
滑块3在斜推块2中运动,末端通过变角度导轨8与动模连接。
变角导轨分a、b、c 三段,通过不同角度控制滑块3的运动。
3、模具工作过程通过设定注塑机的抽芯程序,在开模的同时(或者可以设定比开模时间稍早一些)使顶出液压缸开始顶出,并在顶出过程中保持推板与定模相对位置保持不变。
在此过程中,由于横向滑块3 受变角度导轨控制,横向滑块3、塑件和定模块都保持相对静止,而斜推块2则向内运动,将塑件内部空间让出,推出行程至导轨a 段结束时,如图所示。
继续开模,由于变角度导轨b 段角度的改变,横向滑块3向内运动,将塑件通过变形方式向内拉,直到导轨b段结束时,塑件已经完全脱离倒钩段,如图所示。
由于此时塑件倒钩与模具均已分离,但塑件端部顶着定模块,塑件有微量的变形。
模具继续打开,通过导轨C 段的角度变化,推动滑块3,使塑件变形回复到原来状态,并进一步将塑件推出,以利取件,如图所示。
4、内分型模具实例讲解1)、模具打开后产品按要求留在动模上;2)、在动、定模打开的同时,弹簧8的弹力作用于顶针板,通过顶针板的推动,使两端的大斜顶1、滑块3、斜推2(在其底部弹簧的作用下)、共同与前模以同等的速度沿-Z运动,同时大斜顶1、斜推2由于斜导轨的作用下,在-Y方向产生一定位移,保险杠两端随之有相应的变形;3)、斜推2在限位块6的作用下停止运动,斜顶1、外滑块3、前模仍然以同等速度沿-X运动;4)、外滑块3运动到完全脱离斜推2后,弹簧对顶针版的弹力达到极限,大斜顶1停止运动,前模继续打开,同时在斜导柱4的作用下外滑块3沿X方向运动,完全脱离产品。
5)、模具复位。
模具复位的结构主要有油缸复位、注射机复位、弹簧复位、回针杆复位等多种形式。
该模具的是采用回针杆结构实现的,整个模具的复位可以分为三个部分来理解:1、在合模的同时非胶位面先碰上回针9,有回针将顶针板、顶针、直顶块回复到原位(如图1所示);2、两端的大斜顶1在前模的作用下沿斜导槽运动进行复位;3、浅色斜推2在大斜顶1的作用下沿斜导槽运动进行复位;4、外滑块3在外滑块斜导柱4的作用下沿导槽运动进行复位。
6)、机械式安全保护拉钩。
为保证模具在液压机构、弹簧弹力等失效的情况下,模具的机械装置仍然能够保证同步推出,在模具上一定要设计安装安全保护拉钩。
如图所示四、交流讨论五、培训总结一、流道系统和进胶方式选择:流道的选择在模具设计中非常重要,直接影响产品的外观质量和成型精度。
我想我们以后就应该规定保险杠进胶都采用热流道针阀式进胶;二、保险杠模具选材确认:模具钢材料品种较多,导致模具的制造价格差别也比较大,给公司带来一定的不必要的浪费,为此,针对保险杠模具的具体要求,我建议在以后的保险杠模具开发中按照统一的选材标准,即可以保证保险杠的品质又可减少浪费;三、型腔、型腔尺寸设计经验值推荐;四、模具总装图的基本格式推荐;五、技术推广交流:为保证保险杠的外观品质,希望在以后的保险杠产品开发时,要求供应商必须采用内藏分型线模具结构进行进行生产供货。
热流道模具设计制作标准模具总装图基本格式共同进步谢谢。