环氧丙烷装置操作规程
环氧丙烷装置操作规程

环氧丙烷装置操作规程一、装置概述环氧丙烷装置是用于生产环氧丙烷的设备,属于化工行业中的重要工艺装置。
本文档旨在规范环氧丙烷装置的操作流程,确保操作安全、高效、稳定。
二、装置安全1.操作人员必须经过相关培训,并且持有相应的操作证书,了解装置的结构、原理、操作流程以及常见故障处理方法。
2.操作前必须检查装置及设备的运行状态,确保设备正常工作,无异常现象。
3.操作人员应佩戴防护设备,包括安全帽、防护服、安全鞋等,并定期进行安全检查。
4.禁止在装置周围堆放杂物,保持通道畅通,防止发生跌倒、碰撞等意外。
三、装置操作流程1. 开车前准备1.打开主控室门禁系统,经允许后进入控制室。
2.检查装置的气、液体位表、压力表、温度表、流量表等仪表是否正常。
3.检查装置的阀门、泵、压缩机等设备是否可靠,并将液位计零点进行调整。
2. 装置启动1.按照操作程序操作前置设备,如泵、压缩机等。
2.按照启动程序,逐个启动设备,等待设备升温、压力上升至正常工作状态。
3.监视相关仪表,确保设备运行状态稳定。
4.启动控制系统,进行仪表校验,确认仪表读数与实际情况一致。
3. 操作规程1.按照生产计划和工艺要求,投入原料,并根据配方控制投料的量和时间。
2.监测各种参数,如温度、压力、流量等,及时调整操作条件,保证产品质量稳定。
3.关注设备运行情况,及时处理异常情况,如泄露、堵塞等,保证装置的正常运行。
4.定期对设备进行巡检和维护,清洗设备、更换易损件,并及时记录维护情况。
5.在操作过程中,严禁随意调整设备的设定值,必须按照工艺要求进行操作。
6.操作结束后,关闭设备,停止装置运行,切断电源,清理工作现场,确保工作环境整洁。
四、事故应急处理1.如果发生设备异常停止或突发事故,首先应立即关闭设备,切断电源,防止事态扩大。
2.操作人员应按照应急预案进行紧急处置,保护人身安全,并确保环境安全。
3.及时报告上级领导和相关维护人员,组织处理事故原因,修复设备,防止再次发生事故。
环氧丙烷生产装置生产工艺知识
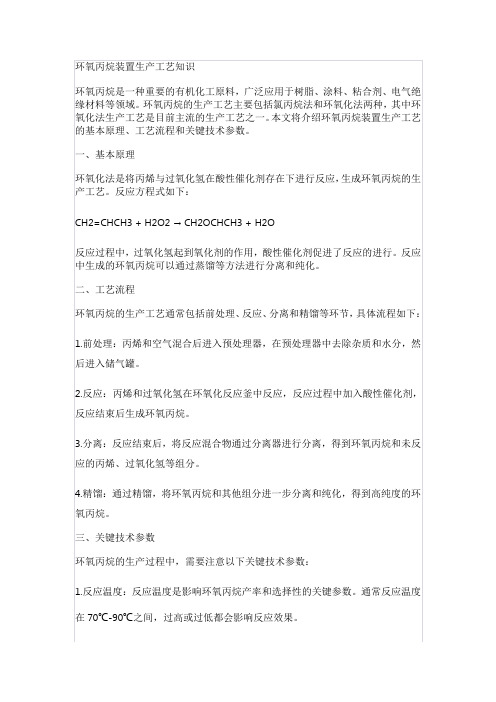
2.酸性催化剂:酸性催化剂种类和使用量的选择对反应效果有很大影响。
常用的酸性催化剂包括硫酸、磷酸等,使用量通常在0.1%-0.5%之间。
3.过氧化氢浓度:过氧化氢的浓度对反应效果也有重要影响。
通常浓度在30%-50%之间,过高或过低都会影响反应效果。
4.反应时间:反应时间也是影响反应效果的重要参数。
反应时间过短,反应不完全,反应时间过长,则会降低产率。
5.分离和纯化技术:分离和纯化环节是保证产品质量的关键步骤,通常采用蒸馏等方法进行分离和纯化,可以得到高纯度的环氧丙烷。
四、装置结构环氧丙烷的生产装置通常包括预处理器、反应釜、分离器、精馏塔、冷却器、储罐等组成部分。
1.预处理器:预处理器用于去除丙烯中的杂质和水分,保证反应混合物的纯度。
2.反应釜:反应釜是进行环氧化反应的核心部件,其中反应混合物在酸性催化剂的作用下进行反应,生成环氧丙烷。
3.分离器:分离器用于分离反应结束后的混合物,将环氧丙烷和未反应的丙烯、过氧化氢等组分分离开来。
4.精馏塔:精馏塔用于进一步分离和纯化环氧丙烷,通常采用多级精馏的方式,可以得到高纯度的产品。
5.冷却器:冷却器用于冷却反应结束后的混合物,保证分离和精馏过程中的安全性。
6.储罐:储罐用于存储生产出来的环氧丙烷。
五、安全措施环氧丙烷的生产过程中,需要注意以下安全措施:1.储气罐、反应釜等容器必须具备一定的压力承受能力和防爆性能,以避免发生意外事故。
2.反应过程中需要加入酸性催化剂和过氧化氢等化学品,操作人员需要严格遵守安全操作规程,防止化学品泄漏和爆炸等事故。
3.反应过程中需要对反应混合物进行冷却,以避免反应器过热引发事故。
4.操作人员需要佩戴防护服、手套、眼镜等防护用品,防止化学品对人体的损害。
5.装置需要配备自动化控制系统和安全监测设备,对反应过程进行实时监测和控制,保证生产过程的安全性。
六、环氧丙烷的应用环氧丙烷是一种重要的有机合成原料,广泛应用于化学、医药、涂料、粘合剂等领域。
环氧丙烷_特性及安全措施
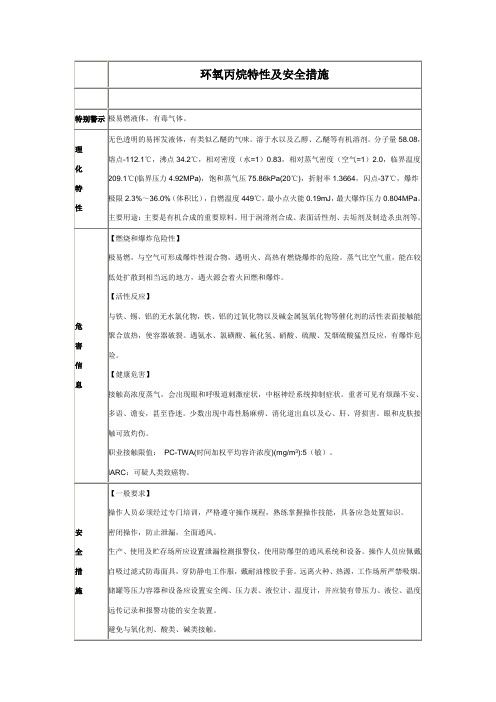
环氧丙烷特性及安全措施特别警示极易燃液体,有毒气体。
理化特性无色透明的易挥发液体,有类似乙醚的气味。
溶于水以及乙醇、乙醚等有机溶剂。
分子量58.08,熔点-112.1℃,沸点34.2℃,相对密度(水=1)0.83,相对蒸气密度(空气=1)2.0,临界温度209.1℃(临界压力4.92MPa),饱和蒸气压75.86kPa(20℃),折射率1.3664,闪点-37℃,爆炸极限2.3%~36.0%(体积比),自燃温度449℃,最小点火能0.19mJ,最大爆炸压力0.804MPa。
主要用途:主要是有机合成的重要原料。
用于润滑剂合成、表面活性剂、去垢剂及制造杀虫剂等。
危害信息【燃烧和爆炸危险性】极易燃,与空气可形成爆炸性混合物,遇明火、高热有燃烧爆炸的危险。
蒸气比空气重,能在较低处扩散到相当远的地方,遇火源会着火回燃和爆炸。
【活性反应】与铁、锡、铝的无水氯化物,铁、铝的过氧化物以及碱金属氢氧化物等催化剂的活性表面接触能聚合放热,使容器破裂。
遇氨水、氯磺酸、氟化氢、硝酸、硫酸、发烟硫酸猛烈反应,有爆炸危险。
【健康危害】接触高浓度蒸气,会出现眼和呼吸道刺激症状,中枢神经系统抑制症状。
重者可见有烦躁不安、多语、谵妄,甚至昏迷。
少数出现中毒性肠麻痹、消化道出血以及心、肝、肾损害。
眼和皮肤接触可致灼伤。
职业接触限值:PC-TWA(时间加权平均容许浓度)(mg/m3):5(敏)。
IARC:可疑人类致癌物。
安全措施【一般要求】操作人员必须经过专门培训,严格遵守操作规程,熟练掌握操作技能,具备应急处置知识。
密闭操作,防止泄漏,全面通风。
生产、使用及贮存场所应设置泄漏检测报警仪,使用防爆型的通风系统和设备。
操作人员应佩戴自吸过滤式防毒面具,穿防静电工作服,戴耐油橡胶手套。
远离火种、热源,工作场所严禁吸烟。
储罐等压力容器和设备应设置安全阀、压力表、液位计、温度计,并应装有带压力、液位、温度远传记录和报警功能的安全装置。
避免与氧化剂、酸类、碱类接触。
环氧丙烷卸车安全操作规程
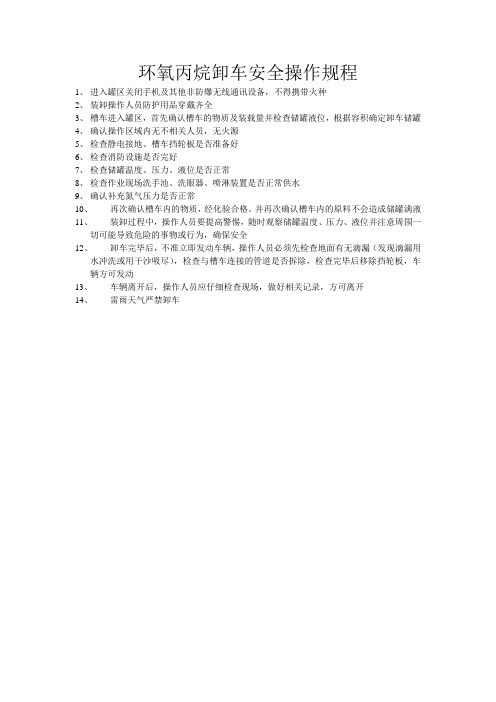
环氧丙烷卸车安全操作规程
1、进入罐区关闭手机及其他非防爆无线通讯设备,不得携带火种
2、装卸操作人员防护用品穿戴齐全
3、槽车进入罐区,首先确认槽车的物质及装载量并检查储罐液位,根据容积确定卸车储罐
4、确认操作区域内无不相关人员,无火源
5、检查静电接地、槽车挡轮板是否准备好
6、检查消防设施是否完好
7、检查储罐温度、压力、液位是否正常
8、检查作业现场洗手池、洗眼器、喷淋装置是否正常供水
9、确认补充氮气压力是否正常
10、再次确认槽车内的物质,经化验合格。
并再次确认槽车内的原料不会造成储罐满液
11、装卸过程中,操作人员要提高警惕,随时观察储罐温度、压力、液位并注意周围一
切可能导致危险的事物或行为,确保安全
12、卸车完毕后,不准立即发动车辆,操作人员必须先检查地面有无滴漏(发现滴漏用
水冲洗或用干沙吸尽),检查与槽车连接的管道是否拆除,检查完毕后移除挡轮板,车辆方可发动
13、车辆离开后,操作人员应仔细检查现场,做好相关记录,方可离开
14、雷雨天气严禁卸车。
环氧丙烷操作规程
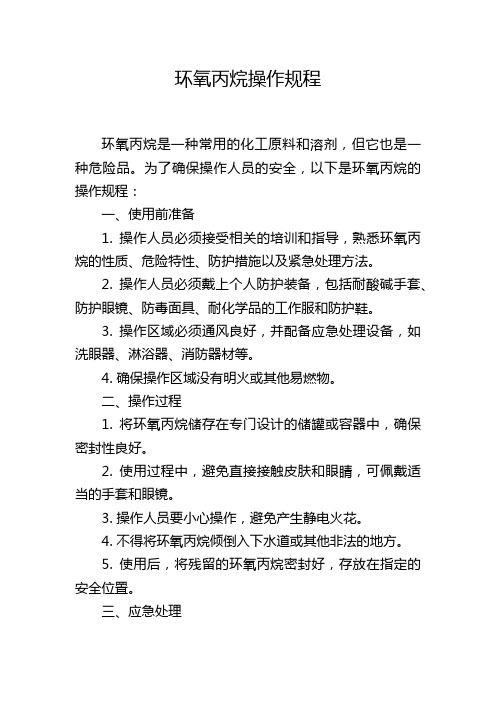
环氧丙烷操作规程环氧丙烷是一种常用的化工原料和溶剂,但它也是一种危险品。
为了确保操作人员的安全,以下是环氧丙烷的操作规程:一、使用前准备1. 操作人员必须接受相关的培训和指导,熟悉环氧丙烷的性质、危险特性、防护措施以及紧急处理方法。
2. 操作人员必须戴上个人防护装备,包括耐酸碱手套、防护眼镜、防毒面具、耐化学品的工作服和防护鞋。
3. 操作区域必须通风良好,并配备应急处理设备,如洗眼器、淋浴器、消防器材等。
4. 确保操作区域没有明火或其他易燃物。
二、操作过程1. 将环氧丙烷储存在专门设计的储罐或容器中,确保密封性良好。
2. 使用过程中,避免直接接触皮肤和眼睛,可佩戴适当的手套和眼镜。
3. 操作人员要小心操作,避免产生静电火花。
4. 不得将环氧丙烷倾倒入下水道或其他非法的地方。
5. 使用后,将残留的环氧丙烷密封好,存放在指定的安全位置。
三、应急处理1. 如果发生泄漏,立即停止工作,迅速将周围人员疏散至安全区域。
2. 尽量阻止泄漏物进入下水道、地下室或密闭空间,避免扩散。
3. 如果泄漏物在可控范围内,使用适当的吸附剂控制泄漏,并将吸附物妥善处置。
如果泄漏较大,立即联系专业的紧急救援人员。
4. 如果有人接触到泄漏物,立即将受污染的衣物脱去,并用大量清水冲洗受影响的部位,然后寻求医疗救治。
5. 在发生火灾时,使用干粉灭火器或二氧化碳灭火器进行灭火,不可使用水灭火。
四、储存与运输1. 环氧丙烷应储存在阴凉干燥、通风良好的仓库中,远离火源和氧化剂。
2. 储存区域应装备完善的泄漏捕获装置和防爆电器设备。
3. 运输过程中,环氧丙烷必须符合相关规范和标准,使用标有危险品标志和标签的运输工具。
4. 在装卸过程中,必须采取防静电措施,避免静电火花引起意外事故。
5. 确保运输容器密封良好,采取防滑和防摔措施,防止破损或泄漏。
总结:环氧丙烷是一种危险品,操作人员在使用过程中必须严格遵守相关的操作规程,如佩戴个人防护装备、保持操作区域通风良好、避免静电火花等。
环氧丙烷装置操作规程
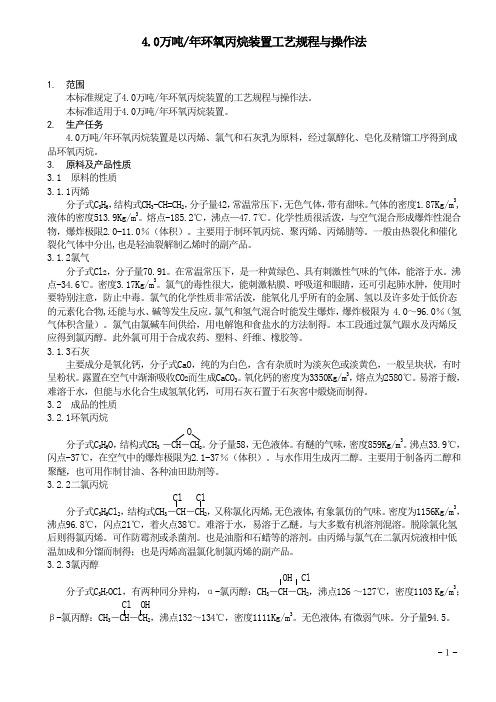
4.0万吨/年环氧丙烷装置工艺规程与操作法1. 范围本标准规定了4.0万吨/年环氧丙烷装置的工艺规程与操作法。
本标准适用于4.0万吨/年环氧丙烷装置。
2. 生产任务4.0万吨/年环氧丙烷装置是以丙烯、氯气和石灰乳为原料,经过氯醇化、皂化及精馏工序得到成品环氧丙烷。
3. 原料及产品性质3.1 原料的性质3.1.1丙烯分子式C3H6,结构式CH3-CH=CH2,分子量42,常温常压下,无色气体,带有甜味。
气体的密度1.87Kg/m3,液体的密度513.9Kg/m3。
熔点-185.2℃,沸点—47.7℃。
化学性质很活泼,与空气混合形成爆炸性混合物,爆炸极限2.0-11.0%(体积)。
主要用于制环氧丙烷、聚丙烯、丙烯腈等。
一般由热裂化和催化裂化气体中分出,也是轻油裂解制乙烯时的副产品。
3.1.2氯气分子式Cl2,分子量70.91。
在常温常压下,是一种黄绿色、具有刺激性气味的气体,能溶于水。
沸点-34.6℃。
密度3.17Kg/m3。
氯气的毒性很大,能刺激粘膜、呼吸道和眼睛,还可引起肺水肿,使用时要特别注意,防止中毒。
氯气的化学性质非常活泼,能氧化几乎所有的金属、氢以及许多处于低价态的元素化合物,还能与水、碱等发生反应。
氯气和氢气混合时能发生爆炸,爆炸极限为 4.0~96.0%(氢气体积含量)。
氯气由氯碱车间供给,用电解饱和食盐水的方法制得。
本工段通过氯气跟水及丙烯反应得到氯丙醇。
此外氯可用于合成农药、塑料、纤维、橡胶等。
3.1.3石灰主要成分是氧化钙,分子式CaO,纯的为白色,含有杂质时为淡灰色或淡黄色,一般呈块状,有时呈粉状。
露置在空气中渐渐吸收CO2而生成CaCO3。
氧化钙的密度为3350Kg/m3,熔点为2580℃。
易溶于酸,难溶于水,但能与水化合生成氢氧化钙,可用石灰石置于石灰窖中煅烧而制得。
3.2 成品的性质3.2.1环氧丙烷O分子式C3H6O,结构式CH3--。
分子量58,无色液体。
有醚的气味,密度859Kg/m3。
环氧丙烷装置培训教材
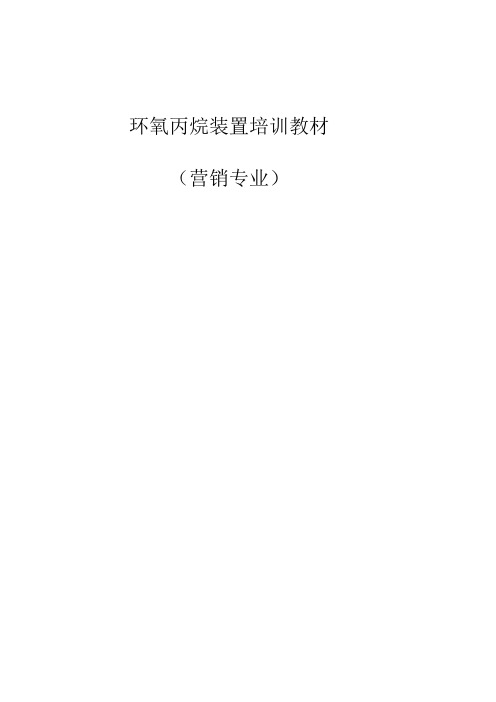
环氧丙烷装置培训教材(营销专业)第一章 生产流程简介1.1前言环氧丙烷是石油化工的重要中间体之一,在丙烯衍生产品中,环氧丙烷目前仅次于聚丙烯和丙烯腈的第三大衍生物。
环氧丙烷(propylene oxide 简称PO )分子式:C 3H 6O ),分子量为58.08。
结构式:H 2CCHCH 3O。
环氧丙烷是生产聚醚、表面活性剂、丙二醇、碳酸丙烯酯、烯丙醇等的主要原料。
我公司环氧丙烷装置采用氯醇法生产技术,连续法生产,年生产时间300天,装置生产能力50000吨/年,该装置的生产工艺比较完善合理,属国际先进水平,产品质量好,收率高,原料单耗低。
1.2装置组成本装置由下列单元组成: 1)环氧丙烷主装置 本系统分六个工序: (1)液氯汽化工序 (2)氯醇化工序 (3)尾气回收工序 (4)皂化精馏工序 (5)石灰乳制备工序 (6)压滤工序 2)丙烯原料罐区3)氯气原料罐区及液氯气化工序 4)石灰库区及石灰乳制备5)尾气回收装置6)产品及中间品罐区7)污水预处理及污水处理装置8)公用工程配套装置循环水、空压制氮站、冷冻站、工艺水站、消防水、锅炉房等9)原料、中控及成品化验室10)物流区及原料材料库区11)综合办公区1.3生产工艺(一)生产方法以丙烯、氯气、水为原料反应生成氯丙醇,氯丙醇再石灰乳发生皂化反应,生成粗环氧丙烷,在皂化过程中,生成的粗环氧丙烷中还含有水及少量氯化副产器(如二氯丙烷、二氯二异丙醚、丙醛等)。
为了生产出符合要求的环氧丙烷产品,需要精馏提纯。
粗环氧丙烷再经过精馏成为成品。
其传统工艺流程如图3-1所示。
图3-1环氧丙烷的传统工艺流程图(二)工艺特点1)本装置采用国际上先进的管式反应器技术,工艺流程简单,安全可靠。
管式氯醇化反应设备是氯气与工艺水在喷射泵中充分预溶,然后与丙烯在管中混合并发生氯醇化反应。
管式反应设备由于采用圆管结构,径向返混激烈,气液接触充分;轴向返混少,近似平推流,反应可按理论等配比进行,氯丙醇选择性高,丙烯和氯气转化率高,因此不需要尾气循环,并节省了能源。
环氧丙烷装置操作规程
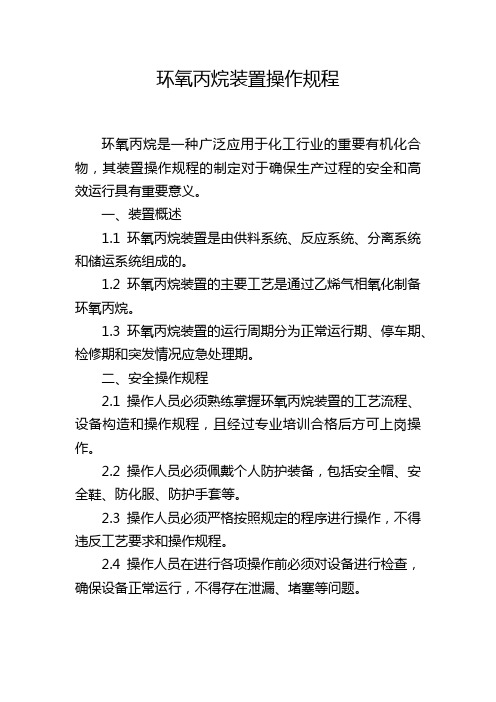
环氧丙烷装置操作规程环氧丙烷是一种广泛应用于化工行业的重要有机化合物,其装置操作规程的制定对于确保生产过程的安全和高效运行具有重要意义。
一、装置概述1.1 环氧丙烷装置是由供料系统、反应系统、分离系统和储运系统组成的。
1.2 环氧丙烷装置的主要工艺是通过乙烯气相氧化制备环氧丙烷。
1.3 环氧丙烷装置的运行周期分为正常运行期、停车期、检修期和突发情况应急处理期。
二、安全操作规程2.1 操作人员必须熟练掌握环氧丙烷装置的工艺流程、设备构造和操作规程,且经过专业培训合格后方可上岗操作。
2.2 操作人员必须佩戴个人防护装备,包括安全帽、安全鞋、防化服、防护手套等。
2.3 操作人员必须严格按照规定的程序进行操作,不得违反工艺要求和操作规程。
2.4 操作人员在进行各项操作前必须对设备进行检查,确保设备正常运行,不得存在泄漏、堵塞等问题。
2.5 操作人员必须熟悉装置的紧急停车程序和应急处理措施,以保证突发情况的快速响应。
三、供料系统操作规程3.1 供料系统主要包括乙烯供料、空气供料和催化剂供料。
操作人员必须按照工艺要求和操作规程控制各个供料系统。
3.2 乙烯供料需确保供应源充足,并在供料前检查供气管道及设备的安全性能。
3.3 空气供料需要定期检查空气压缩机和过滤设备的运行状况,确保供气的质量和安全性。
3.4 催化剂供料需要定期检查和更换催化剂,确保催化剂的活性和稳定性。
四、反应系统操作规程4.1 反应系统主要包括反应釜、冷却器、沉降塔、吸收塔和分离塔等设备,操作人员必须按照工艺要求和操作规程控制反应系统。
4.2 在操作反应釜前,必须确保釜内无残留物,且盖子安装牢固,并定期检查反应釜的安全阀、温度计、压力表等设备。
4.3 冷却器和塔内设备的冷却水和冷却剂必须水质清洁且流量稳定,操作人员需要定期检查冷却系统的性能。
4.4 沉降塔、吸收塔和分离塔等设备的填料和内部管道必须定期清洗和更换,以保证操作效果和设备稳定运行。
- 1、下载文档前请自行甄别文档内容的完整性,平台不提供额外的编辑、内容补充、找答案等附加服务。
- 2、"仅部分预览"的文档,不可在线预览部分如存在完整性等问题,可反馈申请退款(可完整预览的文档不适用该条件!)。
- 3、如文档侵犯您的权益,请联系客服反馈,我们会尽快为您处理(人工客服工作时间:9:00-18:30)。
4.0万吨/年环氧丙烷装置工艺规程与操作法1. 范围本标准规定了4.0万吨/年环氧丙烷装置的工艺规程与操作法。
本标准适用于4.0万吨/年环氧丙烷装置。
2. 生产任务4.0万吨/年环氧丙烷装置是以丙烯、氯气和石灰乳为原料,经过氯醇化、皂化及精馏工序得到成品环氧丙烷。
3. 原料及产品性质3.1 原料的性质3.1.1丙烯分子式C3H6,结构式CH3-CH=CH2,分子量42,常温常压下,无色气体,带有甜味。
气体的密度1.87Kg/m3,液体的密度513.9Kg/m3。
熔点-185.2℃,沸点—47.7℃。
化学性质很活泼,与空气混合形成爆炸性混合物,爆炸极限2.0-11.0%(体积)。
主要用于制环氧丙烷、聚丙烯、丙烯腈等。
一般由热裂化和催化裂化气体中分出,也是轻油裂解制乙烯时的副产品。
3.1.2氯气分子式Cl2,分子量70.91。
在常温常压下,是一种黄绿色、具有刺激性气味的气体,能溶于水。
沸点-34.6℃。
密度3.17Kg/m3。
氯气的毒性很大,能刺激粘膜、呼吸道和眼睛,还可引起肺水肿,使用时要特别注意,防止中毒。
氯气的化学性质非常活泼,能氧化几乎所有的金属、氢以及许多处于低价态的元素化合物,还能与水、碱等发生反应。
氯气和氢气混合时能发生爆炸,爆炸极限为 4.0~96.0%(氢气体积含量)。
氯气由氯碱车间供给,用电解饱和食盐水的方法制得。
本工段通过氯气跟水及丙烯反应得到氯丙醇。
此外氯可用于合成农药、塑料、纤维、橡胶等。
3.1.3石灰主要成分是氧化钙,分子式CaO,纯的为白色,含有杂质时为淡灰色或淡黄色,一般呈块状,有时呈粉状。
露置在空气中渐渐吸收CO2而生成CaCO3。
氧化钙的密度为3350Kg/m3,熔点为2580℃。
易溶于酸,难溶于水,但能与水化合生成氢氧化钙,可用石灰石置于石灰窖中煅烧而制得。
3.2 成品的性质3.2.1环氧丙烷O分子式C3H6O,结构式CH3-CH-CH。
分子量58,无色液体。
有醚的气味,密度859Kg/m3。
沸点33.9℃,2闪点-37℃,在空气中的爆炸极限为2.1-37%(体积)。
与水作用生成丙二醇。
主要用于制备丙二醇和聚醚,也可用作制甘油、各种油田助剂等。
3.2.2二氯丙烷Cl Cl分子式C3H6Cl2,结构式CH3-CH-CH2,又称氯化丙烯,无色液体,有象氯仿的气味。
密度为1156Kg/m3,沸点96.8℃,闪点21℃,着火点38℃。
难溶于水,易溶于乙醚。
与大多数有机溶剂混溶。
脱除氯化氢后则得氯丙烯。
可作防霉剂或杀菌剂。
也是油脂和石蜡等的溶剂。
由丙烯与氯气在二氯丙烷液相中低温加成和分馏而制得;也是丙烯高温氯化制氯丙烯的副产品。
3.2.3氯丙醇OH Cl分子式C3H7OCl,有两种同分异构,α-氯丙醇:CH3-CH-CH2,沸点126 ~127℃,密度1103 Kg/m3;Cl OHβ-氯丙醇:CH3-CH-CH2,沸点132~134℃,密度1111Kg/m3。
无色液体,有微弱气味。
分子量94.5。
-1-Q/BH J GY2.5-2005-2-溶于水、乙醇和乙醚。
性质活泼,由丙烯、氯气、水反应生成,与石灰乳进一步反应生成环氧丙烷。
3.3 副产品的性质3.3.1丙醛分子式C 3H 6O ,结构式CH 3-CH 2-CHO 。
分子量58。
无色易燃液体。
有刺激性。
密度807Kg/m 3,熔点-81℃,沸点47-49℃,溶于水,与乙醇和乙醚混溶。
在紫外光、碘或热的影响下,分解成二氧化碳和乙烷等。
能聚合,用空气、次氯酸盐和重铬酸盐氧化时生成丙酸,用氢还原时生成正丙醇。
与过量甲醛作用生成甲基丙烯醛。
用于制合成树脂、橡胶促进剂和防老剂等,也可用于作抗冻剂、润滑剂和脱水剂。
3.3.2丙二醇OH OH有两种异构体。
较重要的是1,2-丙二醇:CH 3-CH -CH 2,无色粘稠液体。
有吸湿性。
微有辣味。
密度1038Kg/m 3,沸点188.2℃。
与酸反应能生成酯。
与烷基硫酸酯或氯代烃反应能生成醚,是油脂、石腊、树脂、染料和香料等的溶剂。
也可用作抗冻剂、脱水剂等,由环氧丙烷水解而成。
4. 生产原理4.1 反应方程式氯醇化反应方程式Cl 2 + H 2O = HCl + HClO(1) CH 3-CH-CH 2 (90%)CH 3-CH=CH 2 + HClO OH Cl +210KJ/Mol (2) CH 3-CH-CH 2 (10%) Cl OH 氯醇化副反应方程式 Cl 2 + CH 3-CH=CH 2 CH 3-CH-CH 2 Cl Cl CH 3 CH 3 CH 3-CH-CH 2 + Cl 2 + CH 3-CH=CH 2 CH – O - CH (二氯异丙醚) + HCl 2Cl CH 2ClO ClCH 3-CH-CH 2 CH 3-C-CH 2 (氯丙酮)+ H 2OH ClOH Cl O Cl2CH 3-CH-CH 2 + O 2 2CH 3-C-CH 2(氯丙酮)+ 2H 2O皂化反应方程式2HCl + Ca(OH)2 = CaCl 2 + 2H 2O2CH 3-CH-CH 2 + Ca(OH)2 2CH 3-CH - CH 2 + CaCl 2 + 2H 2O +33 KJ/MolOH Cl O2CH 3-CH-CH 2 + Ca(OH)2 2CH 3-CH - CH 2 + CaCl 2 + 2H 2O +33 KJ/MolCl OH O皂化副反应方程式OH Cl2CH 3-CH-CH 2 + Ca(OH)2 2CH 3CH 2CHO + CaCl 2 + 2H 2OCH 3-CH - CH 2 + H 2O CH 3-CH-CH 2O OH OH4.2 影响反应的主要因素4.2.1影响氯醇化反应的因素4.2.1.1反应温度的影响:反应温度过低会降低氯气溶解速度,同时还会导致氯醇液中二氯丙烷液体的积聚,造成二氯丙烷的大量生成,温度过低还会降低主反应的速率;适当提高反应温度可提高反应速率,并可提高主反应的选择性。
通常提高反应温度的主要方法是预热氯醇化反应用水。
4.2.1.2氯醇浓度的影响:反应液中氯醇浓度及氯离子浓度降低有利于氯醇选择性,因此,氯醇化反应必须保持较低的氯丙醇浓度和氯离子浓度。
通常控制氯醇浓度在4%左右。
4.2.1.3气态氯存在对反应的影响:氯气和丙烯气反应生成二氯丙烷,尽量避免氯气和丙烯气用喷射溶氯,接触是提高氯丙醇选择性的一个重要环节,因此,往往采用在进入反应器以前首先溶解氯气,这对减少氯气与丙烯的接触是有利的,一般说来溶氯方法有两种:一是鼓泡溶氯;二是二者都可达到同样的效果。
目前我厂`氯醇化反应器的氯气预溶是采用鼓泡溶解氯气的方式。
4.2.1.4气体线速度对产率的影响:影响反应快慢的主要因素是传质速率,影响传质速率的是比表面积及液相传质系数。
通常对一定的反应介质来说液相传质系数是不变的。
当液体量及性质固定时,反应器设备固定时,则比表面积仅与气含率成正比,而气含率又与气体线速度有关。
气速增加时气含率增加,当气速增加到一定值时气泡汇和,反而使气含率下降,影响传质速率。
因此,在不超过极限的情况下,提高反应器内气体线速度对反应是有利的。
增加气体线速度能增加反应器与循环支管内液体重度差,增加气体的升力,以至增强液体自然循环。
4.2.2影响皂化反应的因素4.2.2.1停留时间与转化率的关系:皂化反应生成的环氧丙烷易水解成丙二醇,因此,皂化反应应选择一个较适宜的停留时间,以免因为停留时间过长环氧丙烷水解为丙二醇,或者停留时间过短反应不完全造成氯丙醇的损失。
4.2.2.2皂化废水碱度对反应的影响:过量的碱可以保证反应的完全和防止逆反应。
但实验证明,废水碱度过高,有利于丙二醇的生成。
因此,适当控制废水碱度,可减少副反应,生产中通常控制皂化废水的PH值在9.0-11。
4.2.2.3温度对产率的影响:温度是影响产率的主要因素。
温度过低造成反应速率的降低,也会造成氯丙醇转化率降低;温度过高则会造成丙二醇的生成,通常皂化反应温度控制在101-105℃。
4.3 精馏原理混合物中不同组分有不同的挥发度,通过精馏塔(填料或多层塔盘)的气液两相逆流接触,同时多次进行部分汽化和部分冷凝的过程中,发生了热量和质量的传递,使混合液得到分离的操作称为精馏。
由于轻组分沸点低,蒸气压高,易挥发,重组分沸点高,蒸气压低,不易挥发,所以,精馏塔越往上轻组分越多,越往下重组分越多。
一般精馏塔可分为三段,上段为精馏段,中段为进料段,下段为提馏段。
塔釜均为间接加热,进料位置通常在塔中部。
塔顶设冷凝器,将冷凝的液体部分或全部回流。
4.4 影响精馏的主要因素4.4.1回流比的影响回流量与出料量之比叫回流比。
回流比过大或过小都会影响精馏操作的经济性和产品的质量,加大回流比,则使塔顶产品中的轻组分浓度增加,但却减小了塔的生产能力,也使塔顶冷量和塔釜热量消耗增大。
在正常操作中,应保持适宜的回流比,在保证产品质量的提下,争取最好的经济效益。
若塔顶产品中重组分含量增加,质量下降,要适当增大回流比,若塔的负荷(进料量)过低,为了保证塔内一定的上升蒸汽速度,也要适当增大回流比。
4.4.2进料组成的影响进料组成的变化直接影响精馏操作,当进料中重组分的浓度增加时,精馏段负荷增加,对于固定了精馏段塔板数的塔来说,将会把重组分带到塔顶,使塔顶产品质量不合格。
若进料组分中轻组分的浓度增加,对于固定了提馏段的塔来说,将造成提馏段的轻组分蒸出不完全,釜液中轻组分的损失加大。
同时,进料组成的变化,还会引起全塔的物料平衡和工艺条件的变化,若组分变轻,则塔顶馏分-3-Q/BH J GY2.5-2005增加,釜液排放量减少,同时全塔温度下降,塔压升高;组分变重,则情况相反。
进料组成变化时,可采用如下措施:a)改进料口:组成变重时,进料口往下改;组成变轻时,进料口往上改。
b)改回流比:组成变重时加大回流比;组成变轻时减小回流比。
c)调节冷剂量和热剂量:根据组成的变化情况,相应调节塔顶冷剂和塔釜热剂量,维持顶、釜的质量不变。
4.4.3温度的影响温度包括进料温度、塔釜温度和塔顶温度。
进料温度对精馏操作的影响是很大的。
总的来说,进料温度降低,将增加塔釜的热负荷,减少塔顶的冷负荷;进料温度升高,情况相反。
当进料温度变化过大时,通常影响整个塔身的温度,从而改变气液平衡组成。
塔釜温度和塔顶温度的变化对精馏操作也有明显影响,釜温低于规定值时,釜液中轻组分的浓度增加,顶部产物量减少;当釜温高于规定值时,就会使塔板上的气相量增加,液相量减少,顶部产物增加,釜液量减少,顶产物重组分增多。
4.4.4进料量的影响进料量变化的范围,不超出塔顶冷凝器和精馏塔再沸器的负荷范围时,只要调节及时得当,对釜温和顶温不会有显著的影响,而只影响塔内蒸气上升速度。