环氧丙烷氯化法、共氧化法和直接氧化法技术路线解析
环氧丙烷流程
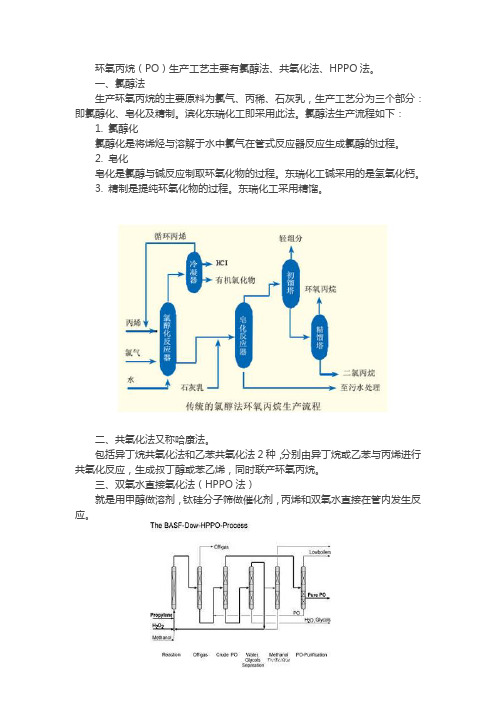
环氧丙烷(PO)生产工艺主要有氯醇法、共氧化法、HPPO法。
一、氯醇法
生产环氧丙烷的主要原料为氯气、丙稀、石灰乳,生产工艺分为三个部分:即氯醇化、皂化及精制。
滨化东瑞化工即采用此法。
氯醇法生产流程如下:
1.氯醇化
氯醇化是将烯烃与溶解于水中氯气在管式反应器反应生成氯醇的过程。
2. 皂化
皂化是氯醇与碱反应制取环氧化物的过程。
东瑞化工碱采用的是氢氧化钙。
3.精制是提纯环氧化物的过程。
东瑞化工采用精馏。
二、共氧化法又称哈康法。
包括异丁烷共氧化法和乙苯共氧化法2种,分别由异丁烷或乙苯与丙烯进行共氧化反应,生成叔丁醇或苯乙烯,同时联产环氧丙烷。
三、双氧水直接氧化法(HPPO法)
就是用甲醇做溶剂,钛硅分子筛做催化剂,丙烯和双氧水直接在管内发生反应。
双氧水与HPPO法集成生产环氧丙烷的技术路线探讨

双氧水与HPPO法集成生产环氧丙烷的技术路线探讨摘要:环氧丙烷(PO)是除聚丙烯和丙烯腈之外的第三大丙烯衍生物,是重要的基本有机化工合成原料,主要用于生产聚醚、丙二醇等。
它也是第四代洗涤剂非离子表面活性剂、油田破乳剂、农药乳化剂等的主要原料。
目前,环氧丙烷的衍生物广泛用于汽车、建筑、食品、烟草、医药及化妆品等多种行业,而且,已生产的下游产品近百种,是精细化工产品的重要原料。
环氧丙烷的生产工艺很多,目前国内外已经工业化生产的主要有氯醇化法、共氧化法以及过氧化氢氧化法(即HPPO法),本文主要对双氧水与HPPO法集成生产环氧丙烷的技术路线进行探讨。
关键词:双氧水与HPPO法环氧丙烷技术路线探讨一、前言环氧丙烷是重要的有机化工原料,在丙烯的衍生物中仅次于聚丙烯和丙烯腈,居第三位。
PO化学性质极其活泼,应用极为广泛。
以PO为原料生产聚醚多元醇进而生产聚氨酯是其最大用途;其次可用于生产聚氨酯弹性体及用途广泛的丙二醇、丙二醇醚等表面活性剂;还可用于生产油田破乳剂、农药乳化剂及润湿剂等。
全称为1,2-环氧丙烷,有氯醇法、共氧化法和直接氧化法(HPPO)三种工业生产工艺。
三种生产工艺的比较:三种工艺路线基本情况从上表可以看出,HPPO法因其运行成本低、节能环保而占据优势,但是高浓度的H2O2无法长距离运输,必须现场配套提供,因此未来的环氧丙烷生产技术路线方向应为双氧水与HPPO法的集成技术。
二、双氧水与HPPO法的集成技术1.技术路线基本情况双氧水直接氧化丙烯制环氧丙烷新技术开发的原位耦合法相比,简化了工艺流程,减少了规划及的损失;与传统工业生产方法相比,工艺简单,环境友好,无联产品问题;在优化的工艺条件下,催化剂循环使用5次以后环氧丙烷相对双氧水的产率仍保持在87%以上,产物分布选择性>99%.新方法在适宜的溶剂体系中,在该研究组开发的新一代反应控制相对转移催化剂作用下,可直接催化双氧水氧化丙烯,高选择性的生成环氧丙烷。
环氧丙烷工艺技术对比

PO/TBA法 反应 方程 及 工艺 流程 简 图 (图 3) (CH ) CH+O2--- ̄(CH,) C·OOH CH CH— CH +(CH ) C·00H—}CH CHCH +(c}{3) COH
异
钛 硅 分 子 筛 催 化 工 业 双 氧 水 和 丙烯 直 接 氧化 生 成 环 氧 丙 烷 ,工 艺 简单 ,反 应 过 程 不 产 生 有 毒 有 害气 体 ,副 产 物 只有 少量 的丙 二醇 单 甲醚 和极 少 量 的 丙 二 醇 ,而 这两 种 产物 可 作 为环 氧 丙烷 高 附加 值 的衍 生 物 回收 ,反 应 中产 生 的水 可 作 为工 艺水 循 环使 用 或 经 一 般 性 处 理 后 排 放 。本 T 艺 摒弃 了 以前 工 艺 的缺 点 ,反 应 条件 温 和 ,并 集 简 易 性 和 安 全性 于一 身 ,并 且 由于 反应 自身 具 有 内在 清 洁 性 ,因 而 不 会 对 环 境产 生 污染 。另 外 ,HPPO技 术 与 其 他 制 备技 术 相 比所 需 配套 设 施少 ,不仅 缩 小 了新 建装 置 的 占 地 面积 ,而且 可大 大减 少开 支 。
第 31卷第 4期 2017年 7月
环氧丙烷工艺技术概况

环氧丙烷工艺技术概况a)氯醇法氯醇法是传统的环氧丙烷工业生产路线,该法自20世纪30年代由美国UCC公司开发并进行工业生产以来,一直是生产环氧丙烷的主要方法。
截止到2009年6月,全球环氧丙烷的总生产能力约810万吨/年,其中氯醇法占33.58%。
氯醇法分为以石灰为皂化原料的传统氯醇法和以电解液(NaOH)为皂化原料的改良氯醇法。
1)传统氯醇法主要专利商:美国Dow Chemical、日本Asahi glass公司、Mitsui Chemicals和Showa denko 公司、意大利Enichem公司等。
主要工艺过程:丙烯、氯气和水按一定配比送入氯醇化反应器中进行反应,未反应的丙烯与反应中产生的HCl及部分的二氯丙烷等自反应器顶部排出,经冷凝除去氯化氢和有机氯化物,丙烯循环回用。
反应器底部得到氯丙醇质量分数为4~5%的盐酸溶液。
将该溶液与过量约10%的石灰乳混合后送入皂化塔中皂化,再经精馏即可得到环氧丙烷。
优点:传统氯醇法具有流程比较短,工艺成熟,操作负荷弹性大,产品选择性好、收率高,生产比较安全,对原料丙烯纯度的要求不高,投资少,无引起市场干扰的联产产品,其产品具有较强的低成本竞争力等优点。
缺点:传统氯醇法存在的最大问题是设备易于腐蚀,在生产过程中产生大量含氯污水(每吨产品约产生45~60吨废水和2.1吨氯化钙)废渣,该废水具有温度、pH值、氯根含量、COD含量和悬浮物含量“五高”的特点,处理成本高,造成严重的环境污染。
世界上大多数发展中国家和地区采用传统氯醇法技术,装置规模都比较小。
例如:俄罗斯、东欧、巴西、印度和中国。
少数发达国家的老装置也在使用该技术(如日本、德国),面临被淘汰。
2)改良氯醇法主要专利商:美国Dow Chemical和意大利Enichem公司。
主要工艺过程:改良氯醇法是用烧碱代替石灰乳,在常压或减压条件下于80~130℃与氯丙醇发生皂化反应。
该法提高了氯丙醇的转化率和环氧丙烷的收率,同时抑制了皂化副反应的发生,提高了环氧丙烷的选择性。
氯醇法与共氧化法生产环氧丙烷的分析对比分析

氯醇法与共氧化法生产环氧丙烷的分析对比分析发表时间:2020-08-27T05:59:30.240Z 来源:《现代电信科技》2020年第6期作者:魏斌[导读] 本文首先分析了环氧丙烷的概况,其次阐述了氯醇法与共氧化法的对比情况,最后对共氧化法与氯醇法的对比情况进行了总结。
魏斌(江苏红宝丽集团股份有限公司江苏南京 210000)摘要:本文首先分析了环氧丙烷的概况,其次阐述了氯醇法与共氧化法的对比情况,最后对共氧化法与氯醇法的对比情况进行了总结。
关键词:氯醇法;共氧化法;生产环氧丙烷1、环氧丙烷的简介环氧丙烷又被称为甲基环氧乙烷,在化工合成中起着重要作用[1]。
环氧丙烷的主要作用就是用于聚醚多元醇、丙二醇的生产,在这之中聚醚多元醇的作用主要是生成聚氨酯,并且应用较为广泛,比如其应用领域主要在家具、保温材质、粘合剂、弹性体等中。
随着我国化工行业的不断发展,其相关领域越来越重视环氧丙烷的生成技术,现在最常见的方法主要有:氯醇法、间接氧化法,其中共氧化法是间接氧化法里面的一种。
2、氯醇法与共氧化法的对比氯醇法在生产环氧丙烷时,在经过丙烯氯醇化、石灰乳皂化和提纯精制的操作流程,如图1所示。
才能得到高质量的环氧丙烷。
氯醇化反应器技术是其最关键性的生产技术,其工艺的应用的主要是陶氏化学的管式反应器。
随着我国科学技术的发展,在生产环氧丙烷的技术方面也得到了相应的提升,我国相关科研人员研发的单管四旋静态混合管式技术,已经研发成功,并在环氧丙烷装置上得到了应用。
其技术的研发不仅减少了化工企业对环境的破坏,还让环氧丙烷装置的选择性得到了一定程度上的提升。
图1:氯醇法的操作流程氯醇法作为出现最早的生产环氧丙烷的工艺技术,其应用的最大优势就是在生产过程中,没有伴生物的生成,并且工艺步骤较少,技术发展成熟度较高,同时它还对生产原料的要求不高,花费的成本也相对较低。
我国出现时间最长的环氧丙烷装置就是氯醇法工艺,并且在全世界的生产量中占有较重的比例,其中对氯醇法生产量贡献最多的区域。
环氧丙烷生产装置生产工艺知识
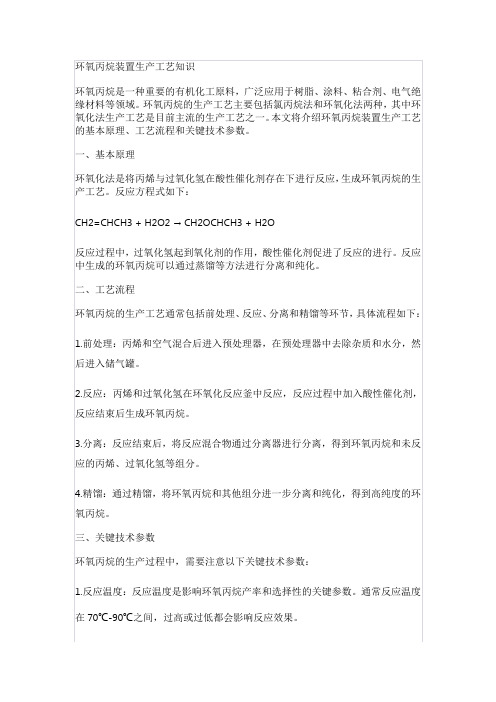
2.酸性催化剂:酸性催化剂种类和使用量的选择对反应效果有很大影响。
常用的酸性催化剂包括硫酸、磷酸等,使用量通常在0.1%-0.5%之间。
3.过氧化氢浓度:过氧化氢的浓度对反应效果也有重要影响。
通常浓度在30%-50%之间,过高或过低都会影响反应效果。
4.反应时间:反应时间也是影响反应效果的重要参数。
反应时间过短,反应不完全,反应时间过长,则会降低产率。
5.分离和纯化技术:分离和纯化环节是保证产品质量的关键步骤,通常采用蒸馏等方法进行分离和纯化,可以得到高纯度的环氧丙烷。
四、装置结构环氧丙烷的生产装置通常包括预处理器、反应釜、分离器、精馏塔、冷却器、储罐等组成部分。
1.预处理器:预处理器用于去除丙烯中的杂质和水分,保证反应混合物的纯度。
2.反应釜:反应釜是进行环氧化反应的核心部件,其中反应混合物在酸性催化剂的作用下进行反应,生成环氧丙烷。
3.分离器:分离器用于分离反应结束后的混合物,将环氧丙烷和未反应的丙烯、过氧化氢等组分分离开来。
4.精馏塔:精馏塔用于进一步分离和纯化环氧丙烷,通常采用多级精馏的方式,可以得到高纯度的产品。
5.冷却器:冷却器用于冷却反应结束后的混合物,保证分离和精馏过程中的安全性。
6.储罐:储罐用于存储生产出来的环氧丙烷。
五、安全措施环氧丙烷的生产过程中,需要注意以下安全措施:1.储气罐、反应釜等容器必须具备一定的压力承受能力和防爆性能,以避免发生意外事故。
2.反应过程中需要加入酸性催化剂和过氧化氢等化学品,操作人员需要严格遵守安全操作规程,防止化学品泄漏和爆炸等事故。
3.反应过程中需要对反应混合物进行冷却,以避免反应器过热引发事故。
4.操作人员需要佩戴防护服、手套、眼镜等防护用品,防止化学品对人体的损害。
5.装置需要配备自动化控制系统和安全监测设备,对反应过程进行实时监测和控制,保证生产过程的安全性。
六、环氧丙烷的应用环氧丙烷是一种重要的有机合成原料,广泛应用于化学、医药、涂料、粘合剂等领域。
环氧丙烷共氧化法

环氧丙烷共氧化法环氧丙烷共氧化法是通过化学反应来制备环氧乙烷和叠氮甲烷的方法。
它是一种绿色环保的方法,其生产过程对环境影响较小,又能够高效地产生所需的产物,因此被广泛应用于工业生产领域。
下面我们来分步骤阐述它的具体过程。
1.催化剂准备在环氧丙烷共氧化法中,使用的催化剂是指定用于此反应的气体协同催化剂。
催化剂制备的第一步是选取合适的催化剂原料。
一般来说,催化剂原料应该有较高的反应活性、良好的稳定性和硬度。
然后按一定比例混合在一起,最后将混合好的材料粉碎和筛选,制得催化剂。
2.反应器设备环氧丙烷共氧化法的反应器设备分为单相和多相两种类型。
单相反应器中,原料以及催化剂均为气态,反应温度较高,反应速度快。
多相反应器中,催化剂与反应物都是液态或固态,整个反应过程需要较长时间,但温度低、能耗少。
3.反应过程将环氧丙烷、氧气和叠氮甲烷按一定比例加入反应器中,同时加入催化剂并将反应器进行预热。
经过一定温度和压力条件下的催化反应,得到所需的产物。
反应完成后,通过分离和净化过程,得到高纯度的环氧乙烷和叠氮甲烷。
4.反应机理环氧丙烷共氧化法是一种氧化还原反应,其机理如下:氧气和叠氮甲烷在催化剂存在下发生氧化还原反应生成高能物质;环氧丙烷与高能物质共同反应,在熵增大的过程中生成环氧乙烷和叠氮甲烷。
整个反应过程中,氧化还原反应提供了反应所需的能量,而催化剂作为反应过程的驱动力,提供了反应所需的条件。
总之,“环氧丙烷共氧化法”作为一种绿色环保的方法,成为了工业生产中制备环氧乙烷和叠氮甲烷常用的方法之一。
在未来的发展中,它将会更好地服务于人类的生产和生活。
环氧丙烷生产工艺
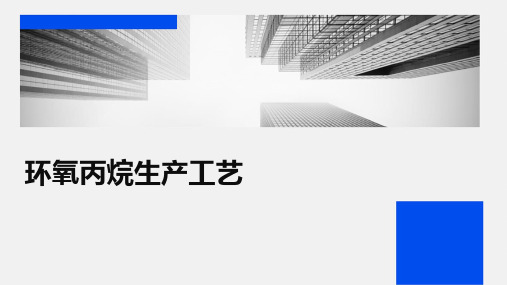
智能化
借助智能化技术实现生产过程 的自动化和信息化,提高生产 管理的效率和精度。
高效化
通过技术进步和设备更新,提 高生产效率和产品质量,降低 能耗和物耗。
多元化原料
开发利用多种原料来源,如生 物质、二氧化碳等,以降低对
传统化石资源的依赖。
THANK YOU
直接氧化法生产工艺
直接氧化法的原理
01
直接氧化法是一种通过直接将丙烯和氧气反应生成环氧丙烷的 方法。
02
该反应通常在高温和催化剂存在的条件下进行,通过自由基反
应机制,丙烯分子被氧气氧化,生成环氧丙烷和水。
催化剂在此过程中起着关键作用,它能降低反应活化能,提高
03
反应速率,并选择性地将丙烯转化为环氧丙烷。
环氧丙烷的沸点为34.2℃,凝 固点为-160.8℃,相对密度为
0.82。
它易溶于水和有机溶剂,具有 较低的蒸气压,因此在大气中
较难挥发。
环氧丙烷的应用
作为生产聚醚和聚氨酯的重要原料,用于制造泡沫塑料 、保温材料、胶粘剂等。
可用于生产润滑油添加剂、表面活性剂等。
在医药、农药、染料等精细化学品合成中用作中间体。 在石油工业中用作萃取剂和溶剂。
缺点
产生大量含盐废水,对环境造成一定 影响;同时,该方法需要使用大量酸 碱,对设备腐蚀严重,维护成本较高 。
03
共氧化法生产工艺
共氧化法的原理
共氧化法是一种利用丙烯和氧气在催化剂存在下,通过氧化反应生成环氧丙烷的方 法。
该反应过程中,丙烯首先被氧化成过氧化氢,然后过氧化氢再与丙烯反应生成环氧 丙烷和水。
环氧丙烷的生产方法
丙烯直接氧化法
01
将丙烯和氧气在催化剂的作用下直接氧化生成环氧丙烷,是最
- 1、下载文档前请自行甄别文档内容的完整性,平台不提供额外的编辑、内容补充、找答案等附加服务。
- 2、"仅部分预览"的文档,不可在线预览部分如存在完整性等问题,可反馈申请退款(可完整预览的文档不适用该条件!)。
- 3、如文档侵犯您的权益,请联系客服反馈,我们会尽快为您处理(人工客服工作时间:9:00-18:30)。
环氧丙烷生产工艺氯醇化法、共氧化法和直接氧化法技术解析万华化学集团股份有限公司(以下简称万华化学)又一具有自主知识产权的高端技术打破国外公司技术垄断,“乙苯共氧化法高效绿色制备环氧丙烷成套技术”项目通过中国石油和化学工业联合会成果鉴定,继百万吨乙烯项目选择丙烷路线之后,将投资32.5亿元,在山东烟台实施该技术成果转化,建设一套年产30万吨环氧丙烷并联产65万吨苯乙烯的世界级规模工业化装置,该装置预计2021年建成投产。
该技术跟其他工艺路线有何不同呢?乙苯共氧化法高效绿色制备环氧丙烷成套技术”项目通过由中国工程院陈建峰院士、蹇锡高院士以及中国科学院李亚栋院士等行业知名专家组成的鉴定,专家委员会认为,该项目成果整体技术进入国际领先行列。
据悉,环氧丙烷是国家重点鼓励发展的高端石化产品,是支撑聚氨酯新材料、精细化工等产业发展非常重要的基础有机化工原料,其生产工艺主要有氯醇化法、共氧化法和直接氧化法。
随着我国精细化工和聚氨酯工业的发展,环氧丙烷产品市场前景日益广阔,但是目前我国环氧丙烷生产主要采用的是氯醇法生产工艺,该工艺存在对设备腐蚀严重、产生的含氯化钙废水严重污染环境等缺点。
乙苯共氧化法环氧丙烷生产技术具有三废少、联产物附加值高、能耗低、经济性好等综合优点,但技术长期被国外公司垄断。
为促进国内环氧丙烷产业技术升级,万华化学数年前就组建团队开始乙苯共氧化法环氧丙烷制造技术自主研究开发,并与浙江大学产学研合作开展小试工艺技术研究。
为突破技术封锁,万华化学的近百名科技人员参与了该项目的研发,并在核心催化剂、反应器关键装备及相关工艺上申请国内外发明专利18件,形成了自主知识产权保护。
同时,万华化学自主设计建成的年产500吨环氧丙烷并联产1100吨苯乙烯工业化试验装置,也一次投料试车成功,并累计实现稳定运行超过90天。
未来,万华化学将投资32.5亿元,在山东烟台实施该技术成果转化,建设一套年产30万吨环氧丙烷并联产65万吨苯乙烯的世界级规模工业化装置,该装置预计2021年建成投产。
环氧丙烷:Propylene oxide 简称POCAS:75-56-9又名氧化丙烯、甲基环氧乙烷是除聚丙烯和丙烯腈以外的第三大丙烯衍生物;重要的基础有机化工原料,主要用于聚醚多元醇的生产,其次用于丙二醇的生产;PO的衍生物产品有近百种,是精细化工产品的重要原料,广泛应用于汽车、建筑及化妆品等行业。
目前国外已工业化生产PO的方法有:氯醇化法、共氧化法和过氧化氢直接氧化法,其中共氧化法又分为乙苯共氧化法和异丁烷共氧化法两种。
以氧气作为氧化剂的直接氧化法也在开发中。
我国在2018年由长岭炼化攻克双氧水法制环氧丙烷成套技术,目前,10万吨/年双氧水法制环氧丙烷工业示范装置标定各项指标均优于设计保证值,产品已成功应用于下游聚醚、丙二醇醚等行业。
1氯醇法氯醇法工艺原理:以丙烯和氯气为原料,首先氯醇化反应后生产氯丙醇,然后氯丙醇经皂化后生成环氧丙烷,最后经静止后得到环氧丙烷产品。
氯醇法生产PO的技术核心是氯醇化反应器技术,目前世界上有代表性的反应器技术为美国陶氏化学(Dow)的管式反应器技术、日本旭硝子公司的管塔型反应器技术、三井东压公司和昭和电工公司的塔式反应器技术。
20世纪80年代末,我国锦化、滨化、大沽等厂家先后引进氯醇法生产工艺,取得了较好的经济效益。
氯醇法具有工艺成熟,丙烯转化率高,投资成本及产品成本较低等优点。
然而其缺点也十分明显:除了环氧丙烷纯度较低,生产过程中产生的“三废”问题以及次氯酸对设备的腐蚀问题也亟待改进和解决。
由于传统氯醇法环氧丙烷生产对于环境的污染过于严重,2000年,美国淘汰了氯醇法工艺。
我国也将氯醇法列入《产业结构调整指导目录2011》限制类条目,新建项目主要考虑共氧化法及直接氧化法,但是早期我国使用该法制备环氧乙烷的企业不在少数。
2共氧化法共氧化法根据原料不同可分为乙苯共氧化法(PO/SM)和异丁烷共氧化法(PO/TBA)。
除PO外,联产苯乙烯和叔丁醇。
环氧丙烷在共氧化法生产中,只是1个产量较少的联产品,每吨环氧丙烷要联产2.2-2.5吨苯乙烯或2.3吨叔丁醇,原料来源和产品销售相互制约因素较大,只有环氧丙烷和联产品市场需求匹配时才能显现出该工艺的优势。
比较适合大型炼化一体化企业生产,装置能力不宜太小。
目前国内应用共氧化法生产PO的企业已有四家(暂不包括仍在试运行的红宝丽),其中两家采用的工艺为PO/SM,另外两家为PO/MTBE。
共氧化法的应用大大减少了废渣废水的产生,并且联产物的销售可以一定程度上降低成本。
然而值得注意的是,共氧化法的工艺通常流程复杂,投资成本大,并且利润常常受联产物市场制约。
PO/SM技术专利商有Lyondell、Shell和Repsol公司,Lyondellhe和Shell,他们主要差别在环氧化反应催化剂上。
Lyondell用钼的配合物溶液为催化剂,反应后需要处理回收利用;Shell 用TiO2 /SiO2 为催化剂,避免了催化剂进入反应生成物的缺点,简化了分离流程,但由于非均相反应体系传热困难,反应器结构复杂,投资增大。
且选择性Shell法98.18%,Lyondellhe法87.14%。
国外均优先选择Shell技术。
PO/TBA技术专利商只有Texaco和Huntsman公司,区别主要在催化剂的使用、产品的分离和PO提纯单元。
2006年中海油与壳牌公司采用Shell技术在广东兴建25万吨/年环氧丙烷装置,打破了我国环氧丙烷生产单纯依赖氯醇法的格局。
2010年中国石化镇海炼化和Lyondell Basell合资建成28.5万吨/年PO/SM装置,也是目前世界上最大的PO/SM生产置。
Huntsman公司先后和烟台万化化学和中石化金陵分公司合资,采用自主研发的异丁烷共氧化法技术,分别在江苏和山东兴建1套24万吨/年的PO/TBA装置,预计2015年投产。
共氧化法PO装置的投产投产,大大降低了氯醇法的产能比例。
3直接氧化法过氧化氢直接氧化法的基本生产原理是在相对比较温和的条件下,丙烯和过氧化氢(H2O2)在甲醇/水混合液中,使用特殊的钛硅催化剂(TS-1)在固定床反应器中发生直接氧化反应的工艺。
这也是目前国内唯一允许产品出口的生产工艺。
1)Degussa-Uhde 和 Dow-BASF的HPPO技术目前国外HPPO工艺分别由赢创工业集团(Degussa)与伍德(Uhde)公司、陶氏化学(Dow)和巴斯夫公司(BASF)联合开发和工业化推广。
2008年7月,韩国SKC公司采用Degussa与Uhde作开发的HPPO技术,在全球首次将HPPO生产工艺运用到商业生产上,该装置生产规模为10万吨/年。
2011年,神华集团引进Degussa与Uhde的HPPO技术,投资25亿元,在吉林建成国内首套且规模最大的HPPO装置,年设计能力30万吨,于2014年7月投运。
BASF与Dow采用自主研发的双氧水制环氧丙烷技术,在比利时建成第一套商业化规模的HPPO装置,年设计生产30万吨,于2008年底投产,显著降低废水排放量和能源消耗。
2011年9月,Dow与SC集团合资在泰国建成的39万吨/年HPPO装置投产。
2)中国石化HPPO技术中国石化石科院、中国石化长岭分公司和湖南长岭石化科技开发有限公司合作开发了钛硅分子筛催化的丙烯与双氧水环氧化合成环氧丙烷技术,在实验室研究、小试和侧线试验的基础上,建立1.0kt/a丙烯与双氧水环氧化制备环氧丙烷的中试装置,进行条件考察试验。
经过两年运行,各项技术指标均符合无污染绿色生产要求,部分指标优于国外同类工艺,2012年,该技术获中国石化总公司审查通过。
2013年1月,中国石化投资约12.8亿元,采用国内自主研发、拥有完全知识产权的双氧水制环氧丙烷技术,在长岭炼化建设一套100 kt/a工业装置。
2014年7月25日,该装置建成中交,同年12月6日投料试车成功。
这项环境友好型清洁生产工艺的开发成功,将使双氧水法工艺(HPPO工艺)取代国内仍大量使用、环境污染严重、技术落后的氯醇法环氧丙烷工艺,对市场、经济、生态环境和社会等方面带来积极影响,被列入2014年全球节能减排十大科技成果之一。
同时也标志着中国石化成为世界上第三家拥有双氧水制环氧丙烷技术的专利商,打破了国外对这一技术的垄断。
2018年12月18日至19日,集团公司2018年度“十条龙”科技攻关工作会议在北京召开。
会上,“十条龙”科技攻关领导小组审议并批准双氧水法制环氧丙烷成套技术等项目“出龙”。
10万吨/年双氧水法制环氧丙烷成套技术由长岭炼化为课题组长单位,中国石化石科院、上海工程公司、湖南长岭石化科技开发公司、青岛安工院联合承担攻关开发。
3)华东理工大学HPPO技术华东理工大学在实验室小试和单管试验的基础上,2007年与天津大沽化工股份有限公司合作建成了国内首套无污染物排放的丙烯恶化双氧水直接环氧化制环氧丙烷的工业试验装置,设计规模了1.50 kt/a,采用TS-1分子筛催化剂,考察装置运行情况及产品性质。
结果表明:连续平稳运行超过4000 h,期间环氧化反应的双氧水转化率达到90%~96 %,环氧丙烷选择性达到90%~92%,产能达到了1.50 kt/a的设计要求,经过精馏纯化,产品的各项性质指标均达到了优级品的要求,实现了环氧丙烷的清洁生产。
为万吨级的丙烯直接环氧化制环氧丙烷装置提供设计依据和参考。
4)中国科学院大连化物所HPPO技术中国科学院大连化物所承担的“反应控制相转移催化丙烯氧化制PO小试研究”于2005年通过了由中石化组织的技术鉴定。
该法在小试中采用了第三代反应控制相转移磷钨酸季铵盐催化剂,用蒽醌法原位生成的H2O2为氧化剂,在70℃、压力小于0.3MPa、丙烯与H2O2摩尔比为3:1的反应条件下,催化丙烯环氧化制PO,PO收率不低于86%(以H2O2计),PO的选择性大于94%(以丙烯计),催化剂质量回收率大于93%。
第三代反应控制相转移磷钨酸季铵盐催化剂可多次循环使用。
2008年8月,通过了由辽宁省科技厅组织的鉴定,实现了环境友好环氧丙烷工艺路线的目标,今后几年有望在在国内得到工业化应用。
以上三大类环氧丙烷制备工艺各有优缺点,用下图直接表示更为直观:未来三年内三种环氧丙烷工艺产能占比预测:以上是关于环氧丙烷的工艺路线情况,近年来,随着聚氨酯市场的发展,作为上游原材料的环氧丙烷也受到关注。
由于国内供应一直存在缺口,进口货源也显得比较重要。
出口方面近年来,体量均较小,且大多只是以我国为中转国通过保税监管场所进行转口。
那么,国内外环氧丙烷的产能情况如何呢?我国环氧丙烷现有总产能约为329.7万吨,产地高度集中,主要分布在华东、东北和华南地区。