材料粘接表面处理与胶接
简述粘接前表面处理的作用和常用方法(一)

简述粘接前表面处理的作用和常用方法(一)粘接前表面处理的作用在进行材料或物品的粘接前,必须要进行表面处理,主要作用包括:1.提高粘接强度2.去除污物和表面氧化层3.提高粘接的耐腐蚀性4.减少氧化酸化反应常用方法以下是常用的粘接前表面处理方法:机械方法1.打磨:用砂纸或研磨机器将表面磨平,去除表面污物和氧化层,并提高接触面积,提高粘接强度。
2.喷砂:通过高压喷砂将表面粗糙化,去除表面污物、氧化层,提高接触面积,增加粘接强度。
化学方法1.清洗:用清洗剂和溶剂清洗表面,去除表面污物、油脂及氧化层。
2.融化:使用高温将表面物质融化,包括等离子喷涂、熔化涂层等方法,其优点在于不会破坏表面微观结构。
3.化学改性:使用表面活性剂、偶氮二异丁腈等改性化学试剂来改善表面性质,增加化学键的数量,提高粘接强度。
物理方法1.紫外线照射: 紫外线直接照射表面可以使表面快速清除,并促进表面活性改变,提高粘接质量。
2.等离子体处理:等离子切割和等离子聚合是一种表面处理,其通过改变表面化学和物理性质来增强粘接强度。
结论通过选择恰当的粘接前表面处理方法,可以使得材料间的粘接强度更高,更加耐用。
为了保证材料的质量和数据的精度,合理选择适用的表面处理方法,是非常重要的。
表面处理的注意事项在进行表面处理时,需要注意以下事项:1.不同材料需要不同的表面处理方法不同材料有不同的表面性质,需要选择适合材料的表面处理方法,否则可能导致粘接强度差、粘接不牢或松散等问题。
2.表面处理要耐久表面处理要能够耐受环境的影响,例如氧化、酸化、污染和磨损等因素。
必须选择具有较高的耐久性和高沉积率的方法。
3.表面处理要完整表面处理要完整,没有缺陷和孔洞。
如果表面处理不充分,可能导致粘接强度差、松散或表面裂纹等问题。
4.表面处理应符合操作规程在进行表面处理时,应该遵循规范操作规程,确保安全、精度和效率,并避免操作失误或过度处理等问题。
总结表面处理是材料或物品粘接前必须要完成的重要步骤,其目的主要在于提高粘接强度、去除表面污物和氧化层、提高粘接的耐腐蚀性和减少氧化酸化反应。
粘接材料的加工和施工工艺

粘接材料的加工和施工工艺随着人们对高性能材料的需求越来越高,粘接材料在现代工程领域中的应用越来越广泛。
而对这类材料的加工和施工工艺的熟悉和掌握程度,将直接影响着工程质量和应用效果。
因此,本文将从加工和施工两个方面对粘接材料做一些介绍和分享。
一、粘接材料的加工工艺1.表面处理粘接材料的表面处理非常重要,它直接决定了粘接剂和基材间的附着强度。
一般来说,表面处理要根据基材和粘接材料的特性来具体选择。
例如对于金属基材,表面处理可以采用机械打磨、腐蚀处理等方式,而对于聚合物基材,表面处理则可以采用火热处理、气氛等离子体处理等方式。
2.测量和调配在进行粘接材料的加工过程中,测量和调配是一个不可忽视的环节。
正确的配比和调配能够保证粘接剂的品质和工作性能,从而在后续的工作中提高安全性和效益。
另外,对于一些颜色要求较高的粘接材料,还需要根据需要添加色母来调配颜色。
3.混合混合是将粘接剂和固化剂等配料物料混合均匀的过程。
在混合的过程中,需要严格控制各配比物料的比例和颜色等特性,以确保混合均匀且品质优良。
一般来说,混合过程可以采用手动或者机械化操作,具体的选择要根据实际需要来决定。
4.制备制备即指将混合均匀的粘接材料在特定条件下进行加热、冷却、压力等加工工艺的过程。
在制备过程中,需要对加工条件进行严格控制,以确保粘接材料获得最佳性能的同时保证生产效率。
一般来说,制备过程可以采用手工制备或者机械自动制备。
二、粘接材料的施工工艺1.涂布涂布是指将粘接材料均匀涂布在基材表面的过程。
涂布的精度和均匀性直接决定了粘接剂和基材间的附着力。
因此,在涂布的过程中,需要注意粘接剂的涂布量、厚度和布涂均匀性,同时也要控制涂布温度和湿度等环境因素对涂布质量的影响。
2.压合在涂布完成后,需要对涂布后的基材进行压合,以提高附着力和强度。
压合过程中,要注意控制压合时间和压力的大小,以保证涂布剂和基材能够紧密结合并达到最佳的粘接效果。
3.固化固化是指使涂布的粘接剂在适当的条件下发生固化反应并且形成牢固的连结的过程。
表面处理与胶接强度
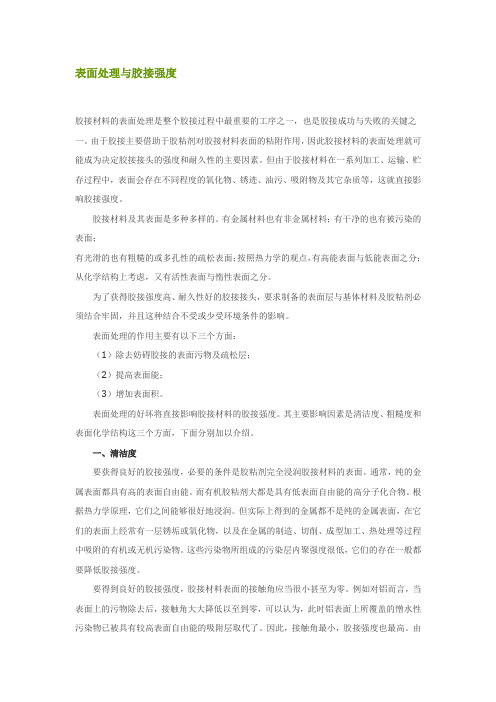
表面处理与胶接强度胶接材料的表面处理是整个胶接过程中最重要的工序之一,也是胶接成功与失败的关键之一。
由于胶接主要借助于胶粘剂对胶接材料表面的粘附作用,因此胶接材料的表面处理就可能成为决定胶接接头的强度和耐久性的主要因素。
但由于胶接材料在一系列加工、运输、贮存过程中,表面会存在不同程度的氧化物、锈迹、油污、吸附物及其它杂质等,这就直接影响胶接强度。
胶接材料及其表面是多种多样的。
有金属材料也有非金属材料;有干净的也有被污染的表面;有光滑的也有粗糙的或多孔性的疏松表面;按照热力学的观点,有高能表面与低能表面之分;从化学结构上考虑,又有活性表面与惰性表面之分。
为了获得胶接强度高、耐久性好的胶接接头,要求制备的表面层与基体材料及胶粘剂必须结合牢固,并且这种结合不受或少受环境条件的影响。
表面处理的作用主要有以下三个方面:(1)除去妨碍胶接的表面污物及疏松层;(2)提高表面能;(3)增加表面积。
表面处理的好坏将直接影响胶接材料的胶接强度。
其主要影响因素是清洁度、粗糙度和表面化学结构这三个方面,下面分别加以介绍。
一、清洁度要获得良好的胶接强度,必要的条件是胶粘剂完全浸润胶接材料的表面。
通常,纯的金属表面都具有高的表面自由能。
而有机胶粘剂大都是具有低表面自由能的高分子化合物。
根据热力学原理,它们之间能够很好地浸润。
但实际上得到的金属都不是纯的金属表面,在它们的表面上经常有一层锈垢或氧化物,以及在金属的制造、切削、成型加工、热处理等过程中吸附的有机或无机污染物。
这些污染物所组成的污染层内聚强度很低,它们的存在一般都要降低胶接强度。
要得到良好的胶接强度,胶接材料表面的接触角应当很小甚至为零。
例如对铝而言,当表面上的污物除去后,接触角大大降低以至到零,可以认为,此时铝表面上所覆盖的憎水性污染物已被具有较高表面自由能的吸附层取代了。
因此,接触角最小,胶接强度也最高。
由此可知,用测定接触角的方法来表示清洁度与胶接强度的关系,作为选择表面处理的最佳条件是有重要参考价值的(见表1)。
粘接物表面处理方法浅谈
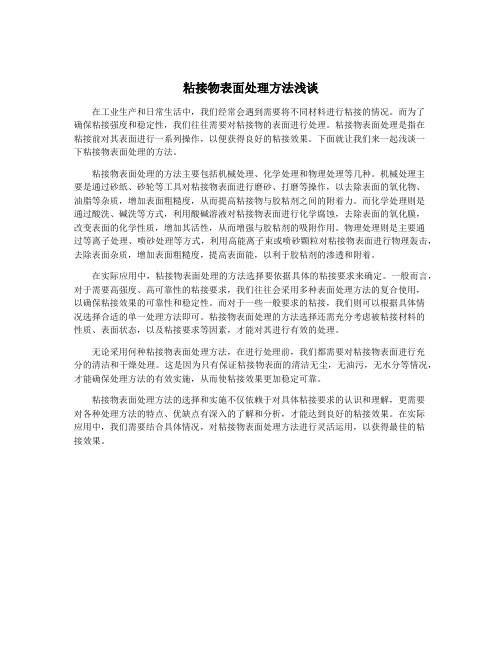
粘接物表面处理方法浅谈在工业生产和日常生活中,我们经常会遇到需要将不同材料进行粘接的情况。
而为了确保粘接强度和稳定性,我们往往需要对粘接物的表面进行处理。
粘接物表面处理是指在粘接前对其表面进行一系列操作,以便获得良好的粘接效果。
下面就让我们来一起浅谈一下粘接物表面处理的方法。
粘接物表面处理的方法主要包括机械处理、化学处理和物理处理等几种。
机械处理主要是通过砂纸、砂轮等工具对粘接物表面进行磨砂、打磨等操作,以去除表面的氧化物、油脂等杂质,增加表面粗糙度,从而提高粘接物与胶粘剂之间的附着力。
而化学处理则是通过酸洗、碱洗等方式,利用酸碱溶液对粘接物表面进行化学腐蚀,去除表面的氧化膜,改变表面的化学性质,增加其活性,从而增强与胶粘剂的吸附作用。
物理处理则是主要通过等离子处理、喷砂处理等方式,利用高能离子束或喷砂颗粒对粘接物表面进行物理轰击,去除表面杂质,增加表面粗糙度,提高表面能,以利于胶粘剂的渗透和附着。
在实际应用中,粘接物表面处理的方法选择要依据具体的粘接要求来确定。
一般而言,对于需要高强度、高可靠性的粘接要求,我们往往会采用多种表面处理方法的复合使用,以确保粘接效果的可靠性和稳定性。
而对于一些一般要求的粘接,我们则可以根据具体情况选择合适的单一处理方法即可。
粘接物表面处理的方法选择还需充分考虑被粘接材料的性质、表面状态,以及粘接要求等因素,才能对其进行有效的处理。
无论采用何种粘接物表面处理方法,在进行处理前,我们都需要对粘接物表面进行充分的清洁和干燥处理。
这是因为只有保证粘接物表面的清洁无尘,无油污,无水分等情况,才能确保处理方法的有效实施,从而使粘接效果更加稳定可靠。
粘接物表面处理方法的选择和实施不仅依赖于对具体粘接要求的认识和理解,更需要对各种处理方法的特点、优缺点有深入的了解和分析,才能达到良好的粘接效果。
在实际应用中,我们需要结合具体情况,对粘接物表面处理方法进行灵活运用,以获得最佳的粘接效果。
各类材质与橡胶黏合表面处理方法
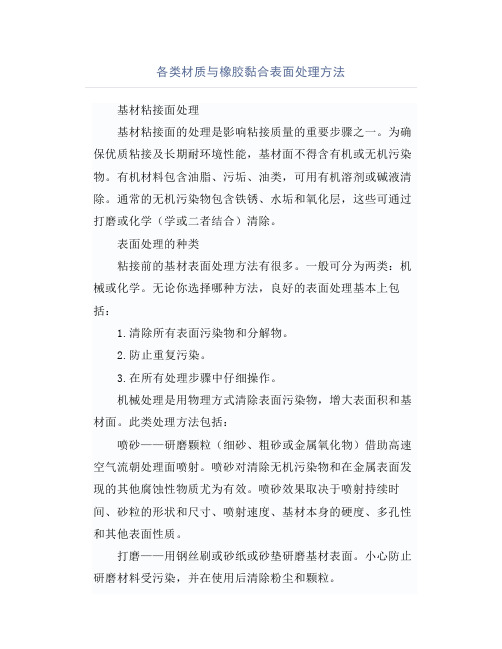
各类材质与橡胶黏合表面处理方法基材粘接面处理基材粘接面的处理是影响粘接质量的重要步骤之一。
为确保优质粘接及长期耐环境性能,基材面不得含有机或无机污染物。
有机材料包含油脂、污垢、油类,可用有机溶剂或碱液清除。
通常的无机污染物包含铁锈、水垢和氧化层,这些可通过打磨或化学(学或二者结合)清除。
表面处理的种类粘接前的基材表面处理方法有很多。
一般可分为两类:机械或化学。
无论你选择哪种方法,良好的表面处理基本上包括:1.清除所有表面污染物和分解物。
2.防止重复污染。
3.在所有处理步骤中仔细操作。
机械处理是用物理方式清除表面污染物,增大表面积和基材面。
此类处理方法包括:喷砂——研磨颗粒(细砂、粗砂或金属氧化物)借助高速空气流朝处理面喷射。
喷砂对清除无机污染物和在金属表面发现的其他腐蚀性物质尤为有效。
喷砂效果取决于喷射持续时间、砂粒的形状和尺寸、喷射速度、基材本身的硬度、多孔性和其他表面性质。
打磨——用钢丝刷或砂纸或砂垫研磨基材表面。
小心防止研磨材料受污染,并在使用后清除粉尘和颗粒。
机加工——如果完全清除油脂,则机加工的表面可能适于粘接。
但若仍有残余油脂杂质,将影响粘接。
另一方面,化学处理方法是利用有机和无机化学品来溶解、松动或消除表面污染。
作业方法包括:蒸汽/溶剂脱脂——利用有机溶剂蒸汽或碱液清洗除去有机污染物或油污。
由于脱脂不能清除残垢或腐蚀物,最好并用金属表面喷砂方法清除。
阳极化处理——氧化铝通过硫酸电解方式沉积在粘接表面形成不封闭薄膜。
钝化锌系磷化处理碱洗铬酸处理化学刻蚀脱脂剂特别注解:虽然三氯乙烯、四氯乙烯仍可用为脱脂溶剂使用,但由于环境和人体健康相关的原因,很多公司已不再使用,并因此已开发出许多不污染环境,能够与粘接系统配用的其他产品,此类产品具有足够的表面清洗效率。
常用的非氯化溶剂脱脂剂包括:水性碱液清洗可用于溶剂型或水剂型胶粘剂不污染环境的石油基溶剂。
通用表面处理以下三步工序是首选机械法表面处理工艺。
粘接工艺分类

粘接工艺分类粘接工艺是一种常用的连接技术,广泛应用于机械、航空航天、汽车、建筑等领域。
根据不同的粘接方式和材料特点,粘接工艺可以分为几种不同的分类。
一、机械粘接工艺机械粘接是利用机械原理将两个或多个零部件连接在一起的粘接方式。
常见的机械粘接工艺包括螺纹连接、铆接、焊接等。
螺纹连接是利用螺纹的相互纠缠来实现连接,常见于各类机械设备中。
铆接是通过铆钉将两个零部件固定在一起,常见于航空航天领域。
焊接是通过熔化两个零部件表面并使其相互融合,形成牢固的连接。
机械粘接工艺具有连接强度高、可靠性好的特点,适用于各类金属和合金材料的连接。
二、化学粘接工艺化学粘接是利用化学反应将两个或多个材料连接在一起的粘接方式。
常见的化学粘接工艺包括胶粘剂粘接、热熔胶粘接等。
胶粘剂粘接是利用胶粘剂在材料表面形成化学键,实现连接。
常见的胶粘剂有环氧树脂、聚氨酯、丙烯酸酯等。
热熔胶粘接是将热熔胶加热至一定温度后涂覆在材料表面,通过冷却固化来实现连接。
化学粘接工艺具有连接面积大、连接强度高的特点,适用于各类材料的连接。
三、热粘接工艺热粘接是利用热能将两个或多个材料连接在一起的粘接方式。
常见的热粘接工艺包括热熔焊接、热板焊接等。
热熔焊接是将材料加热至一定温度后使其熔化,并通过压力使其相互融合,形成连接。
热板焊接是将材料夹在两个热板之间加热,使其熔化并通过压力固化。
热粘接工艺具有连接速度快、连接牢固的特点,适用于各类塑料材料的连接。
四、表面粘接工艺表面粘接是利用表面处理将两个或多个材料连接在一起的粘接方式。
常见的表面粘接工艺包括表面处理、表面活性剂粘接等。
表面处理是通过打磨、除油、除锈等方式将材料表面处理干净,提高粘接强度。
表面活性剂粘接是在材料表面涂覆一层表面活性剂,提高粘接剂的润湿性,使其更好地粘接在材料上。
表面粘接工艺具有连接速度快、连接强度高的特点,适用于各类材料的连接。
总结:粘接工艺是一种重要的连接技术,根据不同的粘接方式和材料特点,可以将其分为机械粘接、化学粘接、热粘接和表面粘接等几种分类。
简述粘接前表面处理的作用和常用方法

简述粘接前表面处理的作用和常用方法
粘接前表面处理是指在进行粘接之前,对粘接表面进行一系列处理,以提高粘接强度和粘接质量。
粘接前表面处理的作用包括清洁表面、增加表面粗糙度、提高粘接剂的附着力、增加粘接面积、去除表面污染物等。
常见的粘接前表面处理方法包括:
1. 清洁:将粘接表面清洁干净,去除油脂、灰尘等杂质,常用
的清洁剂有酒精、溶剂、去污剂等。
2. 去除氧化物:对于金属表面,尤其是氧化性金属表面,需要
去除表面的氧化物层,常用的方法有机械抛光、酸洗等。
3. 增加粗糙度:粘接表面的粗糙度可以增加粘接剂的附着力,
常用的方法有砂纸打磨、喷砂处理等。
4. 表面活化:某些特殊的材料,如聚合物、复合材料等,需要
通过表面活化处理来增加其粘接性能,常用的方法有等离子体处理、火焰处理等。
5. 化学处理:通过使用化学品来改变粘接表面的化学性质,常
用的方法有表面涂覆、表面改性等。
扩展阅读:
粘接前表面处理的目的是为了确保粘接面的清洁和粘接剂的良
好附着。
在粘接过程中,如果表面没有经过适当的处理,可能会导致粘接强度不够,粘接剂容易脱落,从而影响粘接的质量和性能。
除了上述常见的表面处理方法外,还有一些特殊的表面处理方法,
如使用活性化剂、使用特殊的涂层剂等。
这些方法在特定的材料和粘接工艺中有其独特的应用。
此外,粘接前表面处理的效果还受到环境因素的影响,如温度、湿度等。
在选择表面处理方法时,需要根据具体的粘接材料和条件来选择适当的方法。
总之,粘接前表面处理是保证粘接强度和质量的重要步骤,通过合适的处理方法可以有效地改善粘接面的性能,从而确保粘接的可靠性和持久性。
复合材料胶接工艺

复合材料胶接工艺
复合材料胶接工艺是一种常见的连接方法,它利用胶粘剂将两个或多个复合材料部件粘合在一起,形成牢固的接头。
该工艺通常包括以下步骤:
1. 表面处理:对要粘合的复合材料表面进行清洁和处理,以提高胶粘剂的附着力。
2. 涂胶:将胶粘剂均匀地涂敷在一个或多个复合材料表面上。
3. 粘接:将涂有胶粘剂的复合材料部件按要求进行粘接,并施加适当的压力,以确保胶粘剂与复合材料之间的紧密接触。
4. 固化:让胶粘剂在一定的温度和时间条件下固化,形成坚固的接头。
复合材料胶接工艺具有许多优点,如接头强度高、密封性好、耐腐蚀性强、疲劳寿命长等。
它广泛应用于航空航天、汽车、船舶、风能等领域。
复合材料胶接工艺也存在一些挑战,如胶粘剂的选择、表面处理的要求、粘接过程中的温度和压力控制等。
为了获得最佳的粘接效果,需要对这些因素进行仔细考虑和控制。
总之,复合材料胶接工艺是一种重要的复合材料连接技术,它为复合材料结构的设计和制造提供了更多的选择和灵活性。
- 1、下载文档前请自行甄别文档内容的完整性,平台不提供额外的编辑、内容补充、找答案等附加服务。
- 2、"仅部分预览"的文档,不可在线预览部分如存在完整性等问题,可反馈申请退款(可完整预览的文档不适用该条件!)。
- 3、如文档侵犯您的权益,请联系客服反馈,我们会尽快为您处理(人工客服工作时间:9:00-18:30)。
(一)表面特性的影响1、清洁度:金属表面吸附着一层内聚强度低的表面能低的污染层和氧化膜,这将降低胶接强度。
一般地,金属表面干净时,接触很小甚至为零。
材料处理后接触随时间而变化,在空气中易受环境气氛的污染,接触角升高,约5H 后接触角趋于稳定。
表面处理前后的接触角和胶接强度2、粗糙度 被粘材料表面用纱布打磨或喷砂处理,适当地将表面粗化均能提高胶接强度。
糙化过程去除原先存在的表面层。
形成新的表面层(净化),而且喷砂表面比抛光表面有更大的实际胶接面积,表面太粗糙反而会降低胶接强度,因为过于粗糙的表面不能将胶粘剂良好侵润 ,凹处易残面空气对胶接不利。
3、表面化学结构 表面的化学组成与结构对被粘材料的胶接性能、耐久性能、热老化性能等都有重要影响,而表面结构对胶接性能的影响往往是通过改变表面层的内聚强度、厚度、孔隙度、活性和表面能来实现。
用铬酸酸蚀铝表面后,将铝试样侵泡在60oC 蒸馏水中清洗,很容易在表面生成以AL 2O 3.3H 2O 为主的氧化铝水合物,其内聚强度较低,厚度>103A ,使接头出现破坏,强度大大降低,并且能在铝试片表面观察到单晶或粉末状图谱以及虹色干涉现象。
在热自来水中清洗时,填充效率很低,水合物生成较少,其表面看不到虹色或单晶图谱,胶接强度较高。
因此,要得到高剥离强度,铝表面氧化物应该是无水的。
(二)表面处理方法1、溶剂碱液和超声波脱脂法:溶剂脱脂法:常用擦洗法即用无油棉花(脱脂棉)沾溶剂如丙酮、汽油、甲苯等直接擦洗被粘材料表面。
碱液脱脂法:采用热碱液中处理油污表面,如30-55%磷酸钠(Na4P2O7)、10-50% NaOH 、10-6%Na2CO3或30-85%的碱性硅酸盐。
NaOH虽是强碱,由于其润湿性能并不太好,又不易漂洗干净,其效果不如碱性硅酸盐;碱性硅酸盐由 SiO2 和Na2O 混合。
比例为1:2时清洁效果最好;比例为1:1时,适用于铝材的清洁。
超声波脱脂法:一般部件放在功率为20瓦/cm2的超声波中处理20-60秒即可得到足够清洁表面。
2、机械加工:打磨和喷砂砂纸打磨操作简便,但均匀性较差,难以得到相同的重复效果。
喷砂法能迅速简便的清除表面的污物,并产生不同粗糙度的表面。
3、化学腐蚀法:被粘材料经上述处理后须放在酸液或碱液中进行化学腐蚀处理。
这可进一步除去表面上的残留污物,并使表面生成具有良好内聚强度的活化或钝化氧化层,(严格控制水的纯度)。
4、涂底胶法:在处理好的表面上,先涂一层很薄的底胶,以改进胶接性能。
5、等离子体法用等离子体法处理PE、聚丙烯、聚四氟乙烯等难粘材料的胶接强度大大提高,这是因为表面处理后接触角降低,极限表面张力增加,因而改进胶粘剂对其侵润和粘附力。
(三) 各种材料的表面处理与胶接1金属材料1.1、铝合金:按脱脂——碱液处理——铬酸酸蚀处理法。
溶剂脱脂法只能除去铝表面的污物使表层的自然氧化变得干净;碱液法除去油污,又将表层自然氧化膜溶解在碱液中,并形成新的氧化膜;酸蚀法处理能溶解表层的自然氧化膜,并再生成一层致密而坚硬的氧化膜,膜厚为1-3um,内聚强度高,吸附力强,因而胶接性能良好,酸蚀处理后的表面常是在自来水中漂洗干净,并出现一层均匀水膜。
待擦净并在70°C以下烘干。
2Al(OH)3+3H2SO4 → Al2(SO) 4+6H2ONa2CrO7+ H2SO4 → Na2SO4+2CrO3+ H2O2Al+2CrO3 → Al2O3+ Cr2O3美国标准处理H2SO4 ——重铬酸钠溶液配方:Na2CrO7 1 (2.4%)(66-71°C)/10-12分浓H2SO4 10 (22.4%)(66-71°C)/10-12分蒸馏水 30 (73.2%)(66-71°C)/10-12分英国标准处理配方: Cr2O3 5% 或 0 (60-65°C)/30分 Na2CrO7 0 或 7.5% (60-65°C)/30分浓H2SO4 127.3% 或 27.3% 60-65°C)/30分蒸馏水 67.7% 或 65.5% (60-65°C)/30分 1.2、碳钢:在潮湿的空气易氧化生成Fe2O3.n H2O.(1)、溶剂脱脂——在浓HCL1份和H2O1份溶液中室温浸泡5-10min——聚合漂洗干净、擦干——烘干(93°C,10min)(2)、溶液脱脂——在Na2CrO7(4份)、浓H2SO4 (10份)和30份蒸馏水溶液71-77°C下浸泡10min——其余同(1)。
(3)、溶液脱脂——在硫酸酸钠(30份)、洗衣粉(3份)和水(96.7份)中于60-65°C下浸泡5-10min——漂洗干净并在100-105°C烘干。
1.3、不锈钢(1)、脱脂后在100份浓H2SO4 和3份Na2CrO7溶液中于60-65°C下浸泡15min,洗净烘干。
(2)、脱脂后在100份浓HCL、4份H2O2(30%)、20份甲醛(40%)和90份H2O 中于65°C浸泡10分钟。
洗净后放在浓H2SO4 (100份)、Na2CrO7 (10份)和H2O(30份)于65°C下浸泡10min,洗净烘干。
(3)脱脂后在浓HCL(2份),六次甲基四胺(5份),H2O2(1份)和H2O(20份)中于65-70°C浸泡10min,洗净烘干。
1.4、钛合金:(1) 脱脂后在2.7g H2O2(50%)、9.6NaOH和1000mlH2O中室温处理1-2H,洗净烘干。
(2) 脱脂后在841ml浓HCL、63ml浓HF酸和89mlH3PO4中室温浸泡2min,洗净烘干(82-93°C下10-15min)。
选用胶粘剂有环氧、酚醛、聚酰亚胺、聚苯并咪唑等高温胶。
1.5、镁合金:镁合金是很轻的金属,其表面活性大易生成氧化膜。
镁较耐碱,但易与甲酯反应,因此脱脂溶剂只能用丙酮、三氯乙烯等。
(1)、脱脂后在NaOH(80%)中于60-80°C下浸泡5-10min,洗净放在1.8份Ca(NO3) 2、24份铬酸、123份H2O中于室温浸泡5-10min,洗净烘干。
(2)、脱脂后在Cr2O3(17份)、NaNO3(20份)、105份醋酸和100份H2O中于室温浸泡3min,洗净烘干。
选用EPOXY——聚酰胺或EPOXY——橡胶型胶粘剂。
1.6、铜:铜在潮湿环境中易被腐蚀,尤其用乙二胺或DTA固化的环氧胶对铜的腐蚀作用更大。
(1)脱脂后在混合溶液中室温浸泡3min,洗净干燥,立即使用(混合溶液为浓HCL:FeCL3: H2O=50:20:30)(2)脱脂后在溶液HNO3中浸泡约15min,并擦洗至所有腐蚀处消失至净,烘干立即使用。
选用EPOXY、聚酰胺、有机硅、酚醛、氯丁胶和丁腈胶等。
1.7、锌(1)脱脂后在HCL (6%)中于室温浸泡4min,洗净干燥立即使用。
(2)脱脂后在混合溶液中38°C浸泡5min,洗净烘干。
(混合溶液为Na2CrO7:浓H2SO4 :H2O=1:2:8),甲环氧、聚胺酯、有机硅、酚醛等胶接。
2、高分子材料2.1 高分子材料难粘的原因:A 、表面性能很低,难以完全浸润如硅橡胶。
PTFE等。
B 、表面为非极性的,与胶粘剂之间作用力低。
C、表面易吸脂和其他低分子物质,去除困难。
D、热膨胀系数较高,易产生热应力。
E、材料模量低,在界面易发生应力集中。
(选用溶解度参数与被粘材料接近的胶粘剂;表面处理,以便提高胶接强度)2.2 含氟高聚物(聚四氟乙烯PTFE)A、钠——萘——THF溶液腐蚀法。
Rc=18.5dyn/cm将含氟材料表面用细砂纸打磨,丙酮洗涤,晾干于室温的处理液中浸泡1-15min,此时表面产生一层均匀棕色碳化薄膜(厚度约1um)。
取出用丙酮或乙酸洗涤再用水洗净,晾干立即胶接或干燥后存放2-3月内均有良好胶接性能。
处理液配制:在三口瓶中放入升华精萘118-128g,加入去除过氧化物的四氢呋喃100ml。
搅拌溶解后慢慢加入23-30g钠片,反应1-2H,溶液呈现绿色(在干燥的氮气中进行,严防O2和潮气影响)。
处理液须在惰性气体和醋酸密封的干燥容器中可保存三个月之久,严防水汽和空气浸入。
经处理的PTFE用EPOXY——聚酰胺胶胶接,其室温为11mpa以上(PTFE/AL)。
B 熔融的醋酸钾法:在熔融的k+CH3COO-中于320-330°C处理6min,水洗干燥即可。
用有机硅胶、环氧胶、聚氨酯、酚醛——丁腈胶等粘接2.3、聚烷烯烃(聚乙烯和聚丙烯)A、锘酸氧化液配方:Na2CrO7 5 浓H2SO4 8 H2O 100 PE极限表面张力为Rc=31dyn/cm。
PE和PP在66-71°C中浸泡1- 5min或80-85°C处理5-10秒或室温处理1-1.5小时。
用环氧胶胶接时全部是被材料本身内聚破坏。
PS可在Na2CrO7 (10份)和浓H2SO4 (90份)的氧化液中处理3-4min。
B 、等离子体法:处理时间约5秒,胶接强度可提高十倍至数十倍,PP经过处理后,Τ由0.7上升16.8mpa.。
胶接PE:环氧、醋酸乙烯酯——乙烯共聚物、聚氨酯、有机硅等。
胶接PP:环氧——聚酰胺、丁腈胶、聚氨酯等胶。
胶接PS:氯丁胶、氰基丙烯酸醋、聚氨酯、环氧胶等。
表面处理法对PE胶接强度的影响2.4、聚酯和聚碳酸酯聚酯Rc=43dyn/cm,聚酯表面结晶度高,必须降低结晶度和增加极性,可浸泡在20%的NaOH溶液于70-95°C处理10min. 聚酯薄膜(洗涤膜)用有机硅、聚氨酯、线型聚醋、聚酰胺、热熔胶等。
聚碳酸酯脱脂用砂纸打磨,用环氧、聚氨酯、不饱和聚酯等胶。
2.5、聚醚聚甲醛和氯化物聚醚较难胶接,用丙酮脱脂后,在处理液中使表面活化。
Na2CrO7 5 浓H2SO4 8 H2O 100聚甲醛处理条件为室温10-20秒;氯化聚醚为65-71°C下5-10分;聚甲醛用丁腈胶、聚氨酯、环氧和酚醛——丁腈胶氯化聚醚用丁腈胶和氯丁胶粘接。
2.6、聚酰胺(1)细砂纸打磨在表面涂刷间甲酚树脂底胶,用环氧胶接;(2)浸泡在80%苯酚水溶液中刷洗然后用水洗净烘干。
用丁腈胶、聚氨酯、聚酰胺、环氧、酚醛——丁腈胶接。
2.7、赛璐璐、聚甲基丙烯酸甲酯、硬质聚氯乙烯经脱脂砂纸打磨即可赛璐璐用丁腈胶、氯丁胶、热熔胶、聚氨酯等胶;聚甲基丙烯酸甲酯(有机玻璃):丁腈胶、氯丁胶、环氧等;硬质聚氯乙烯:丁腈胶、氯丁胶、白乳胶、聚过氯乙烯、聚氨酯、环氧胶等。
2.8、聚酰亚胺:用丙酮脱脂,在NaOH溶液5%于60-90°C下处理1分钟,胶接扯离强度提高15倍以上,采用环氧胶。