折流板换热性能影响因素 你们的下载是我免费提供的动力
管壳式换热器中折流板的作用
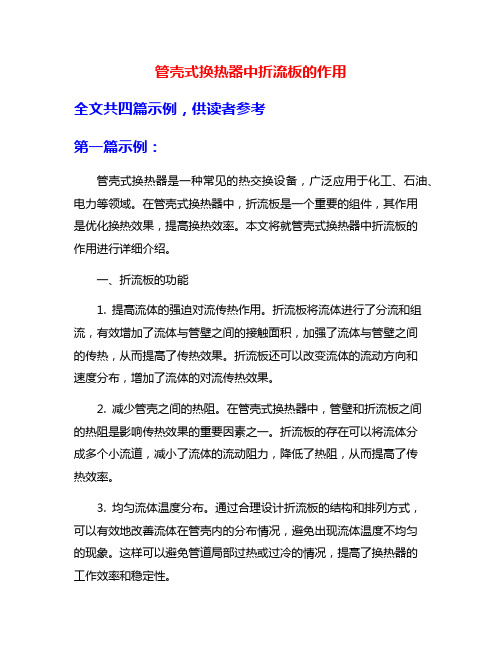
管壳式换热器中折流板的作用全文共四篇示例,供读者参考第一篇示例:管壳式换热器是一种常见的热交换设备,广泛应用于化工、石油、电力等领域。
在管壳式换热器中,折流板是一个重要的组件,其作用是优化换热效果,提高换热效率。
本文将就管壳式换热器中折流板的作用进行详细介绍。
一、折流板的功能1. 提高流体的强迫对流传热作用。
折流板将流体进行了分流和组流,有效增加了流体与管壁之间的接触面积,加强了流体与管壁之间的传热,从而提高了传热效果。
折流板还可以改变流体的流动方向和速度分布,增加了流体的对流传热效果。
2. 减少管壳之间的热阻。
在管壳式换热器中,管壁和折流板之间的热阻是影响传热效果的重要因素之一。
折流板的存在可以将流体分成多个小流道,减小了流体的流动阻力,降低了热阻,从而提高了传热效率。
3. 均匀流体温度分布。
通过合理设计折流板的结构和排列方式,可以有效地改善流体在管壳内的分布情况,避免出现流体温度不均匀的现象。
这样可以避免管道局部过热或过冷的情况,提高了换热器的工作效率和稳定性。
1. 弯曲型折流板。
弯曲型折流板通常采用波纹状或波形状的设计,能够有效地增加传热面积,同时还可以引起流体的湍流运动,增强了传热效果。
2. 梯形折流板。
梯形折流板的结构呈梯形状,能够有效地将流体进行分流和导流,提高了传热效率。
梯形折流板还可以根据需要调整板片的倾角和间距,以适应不同的换热条件。
3. 放置型折流板。
放置型折流板通常安装在换热器的内壳内侧,起到导流和分流的作用,能够有效地提高传热效率。
放置型折流板的结构简单,安装方便,适用于各种规格的换热器。
三、折流板的设计要点1. 考虑流体介质的性质。
在设计折流板时,需要考虑流体的性质,包括流速、温度、压力等因素,以确保折流板的结构能够适应流体的特点,提高传热效率。
2. 合理设计折流板的结构和排列方式。
折流板的结构和排列方式直接影响传热效果,需要根据具体的换热要求和工况条件,合理设计折流板的形状、尺寸和间距,以提高传热效率。
折流板开孔孔径对换热器壳程性能的影响
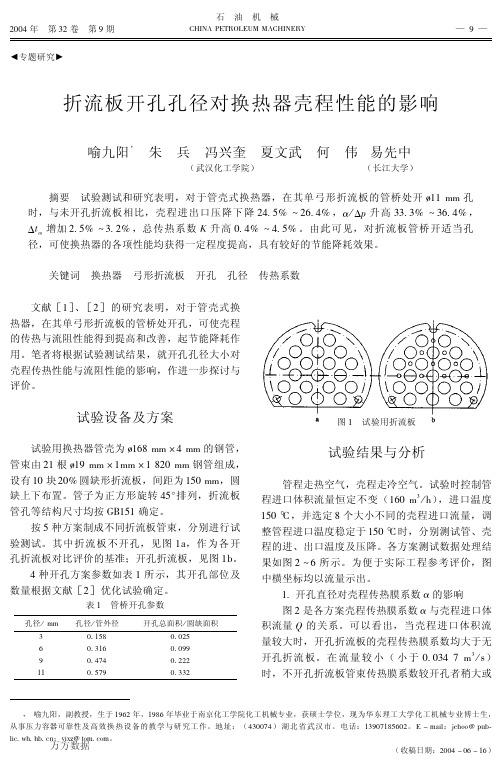
万方数据 图 &$ 频幅响应曲线
[ &] 础设计规范》 ,就可知道与“ 规范” 相比,笔者
结$ 束$ 语
在基础振动分析中使用的方法是不同的,但最终给 出的固有频率和振幅的表达式在实质上是相同的。
参$ 考$ 文$ 献 !$ 倪振华 ) 振动力学 ) 西安:西安交通大学出版社,!./. &$ 89*--(- —.#) 动力机器基础设计规范,!..#
图 *" 对数平均温差 !# $ 与 ! 的关系
*# 开孔直径对总传热系数 % 的影响 图 ’ 是总传热系数 % 与壳程体积流量 ! 的关 系。图示表明,开孔直径为 $ (( 和 ’ (( 时,换 热器 % 值均低于未开孔折流板;而开孔为 %% ((
&--( 年$ 第 ’& 卷$ 第 . 期
喻九阳等:折流板开孔孔径对换热器壳程性能的影响
万方数据
( 收稿日期:%..& I .+ I #+ )
— %/ —
" " " " " "
石" 油" 机" 械
!//) 年" 第 $! 卷" 第 & 期
相当,但相应于该流量的管内流速较小,处于适宜 流速的下限以下,为工业生产非常用流速。故从实 际应用来看,折流板管桥开孔后,不论孔径大小, 对壳程传热性能均有利,且以孔径大者为好。
$ $ $ $ $ $
— !! —
时,! 值在整个流量范围内始终大于未开孔的。这 表明开孔直径足够大时,总传热系数 ! 才能高于 未开孔折流板。 在换热面积相同条件下,若 !" # 和 ! 均得到提 高,无疑会十分有利于提高传热量。前述开孔方案 中,只有最大孔径 !! "",可使 !" # 和 ! 同时得到 提高。
折流板结构对换热器壳程流动和传热性能的影响

通过对比三种板型换热器的传热性能及压力、温度和流速云图,分 析 了 产 生 传 热 性 能 差 异 的 原 因。 研 究 结 果 可 为 管
壳 式 换 热 器 折 流 板 设 计 及 强 化 传 热 性 能 提 供 参 考 ,具 有 一 定 的 工 程 实 际 意 义 。
关键词: 曲面弓形折流板; 球面弓形折流板; 数值模拟; 压力降; 传热
文 章 编 号 :1672���6���952(2018)05���0���072���0���5
投 稿 网 址 :
折流板结构对换热器壳程流动和传热性能的影响
卜英南1,陈祥彬2,张莹莹1,高 磊1
(1.辽宁石油化工大学 机械工程学院,辽宁 抚顺 113001;2.胜宝旺寰球工程有限公司,吉林 吉林 132000)
摘 要: 以弓形折流板为基础,设定相 同 的 工 况 条 件,用 FLUENT 软 件 对 曲 面、球 面 和 弓 形 三 种 折 流 板 型 的
换热器壳程流体的流动和传热性 能 进 行 模 拟,并 对 三 种 板 型 的 管 壳 式 换 热 器 壳 程 压 降 及 换 热 系 数 进 行 比 较 分 析。
中 图 分 类 号 :TQ051.5
文 献 标 志 码 :A
doi:10.3969/ji.ssn.1672���6���952.2018.05.013
InfluenceofBaffleStructureontheFlowand HeatTransfer
PerformanceofShellSideofHeatExchanger
Abstract: Basedonthebowbaffle,thesameworkingconditionsareset.TheFLUENTsoftwareisusedtosimulatetheflow andheattransferperformanceoftheshell,fluidandheattransferofthethreebaffleplatesofcurved,sphericalandarched
管壳式换热器折流板对换热性能影响的数值模拟

江 竹ꎬ等:管壳式换热器折流板对换热性能影响的数值模拟
159
管壳式换热器折流板对换热性能影响的数值模拟
江 竹ꎬ秦 健ꎬ张 辉
( 西华大学 能源与动力工程学院ꎬ四川 成都 610039)
摘要:由于传统弓形折流板换热器设计简单、适应性强被广泛使用于各类生产活动中ꎮ 但是传统弓形换热器的换热性能较差以及壳程
uniform than that of the non - perforated bafflesꎻ the back of the non - perforated baffles is prone to the retention zoneꎬand with
the inlet temperature The increase of the increaseꎻ the jet formed by the open - hole baffle increases the disturbance of the back
of the baffleꎬwhich is beneficial to enhance heat transfer.
Key words: shell - and - tube heat exchangerꎻperforated baffleꎻCFDꎻnumerical simulation
换热器作为一种被广泛应用在化工、石油、动力、食品等产
Heat Transfer Performance Numerical Simulation
Jiang ZhuꎬQin JianꎬZhang Hui
( School of Energy and Power EngineeringꎬXihua UniversityꎬChengdu 610039ꎬChina)
换热器中的管束管板折流板上的小孔
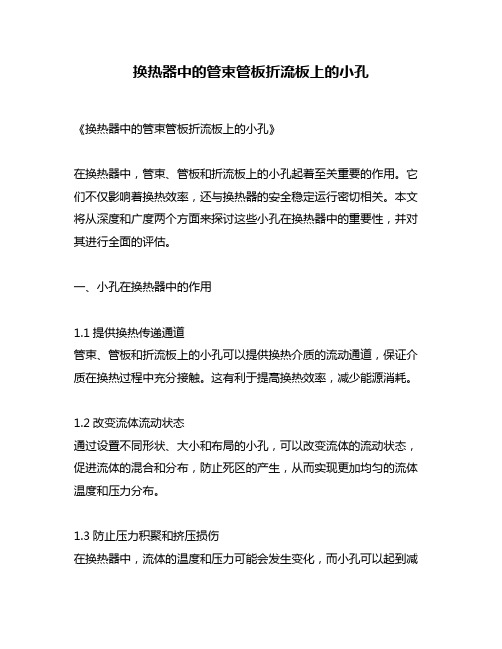
换热器中的管束管板折流板上的小孔《换热器中的管束管板折流板上的小孔》在换热器中,管束、管板和折流板上的小孔起着至关重要的作用。
它们不仅影响着换热效率,还与换热器的安全稳定运行密切相关。
本文将从深度和广度两个方面来探讨这些小孔在换热器中的重要性,并对其进行全面的评估。
一、小孔在换热器中的作用1.1提供换热传递通道管束、管板和折流板上的小孔可以提供换热介质的流动通道,保证介质在换热过程中充分接触。
这有利于提高换热效率,减少能源消耗。
1.2改变流体流动状态通过设置不同形状、大小和布局的小孔,可以改变流体的流动状态,促进流体的混合和分布,防止死区的产生,从而实现更加均匀的流体温度和压力分布。
1.3防止压力积聚和挤压损伤在换热器中,流体的温度和压力可能会发生变化,而小孔可以起到减缓压力积聚、减轻流体挤压损伤的作用,保证换热器的安全稳定运行。
二、小孔的设计原则2.1流体性质在设计小孔时,需要考虑流体的性质,包括粘度、密度、压力等因素,以确保小孔的形状和大小能够适应流体的特性,减小压力损失,避免出现堵塞现象。
2.2换热要求根据换热器的需求,合理设计小孔的分布和密度,确保不同部位的小孔能够满足换热的要求,提高换热效率。
2.3结构强度小孔的设计还需要考虑结构的强度,避免因小孔过大或过多导致管束、管板或折流板的强度不足,甚至出现破裂和泄漏的情况。
三、小孔在实际应用中的挑战与解决方案3.1堵塞问题在换热器运行过程中,小孔可能会受到杂质的堵塞,导致流体通道受阻,影响换热效果。
为此,可以采取定期清洗、使用过滤器等方法来解决堵塞问题。
3.2腐蚀和磨损小孔所处的环境可能存在腐蚀和磨损的因素,影响小孔的形状和大小,进而影响换热效果。
选择耐腐蚀、耐磨损的材料或对小孔进行防腐蚀处理是解决这一问题的关键。
3.3流体过速如果流体速度过快,可能会造成小孔出现振动或压力损失的情况,影响换热器的正常运行。
可以通过设计合理的小孔形状和布局,或者采取降低流速的措施来解决这一问题。
高黏度流体下折流板结构对管壳式换热器传热综合性能的影响
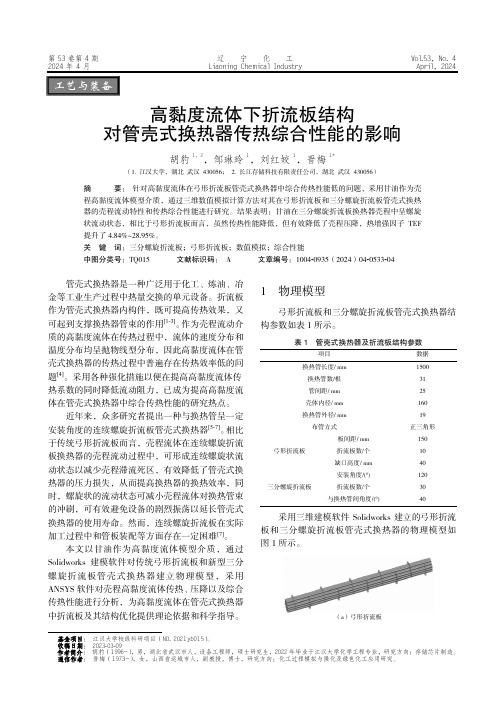
第53卷第4期 辽 宁 化 工 Vol.53,No. 4 2024年4月 Liaoning Chemical Industry April,2024基金项目: 江汉大学校级科研项目(NO. 2021yb015)。
收稿日期: 2023-03-09高黏度流体下折流板结构对管壳式换热器传热综合性能的影响胡豹1,2,邹琳玲1,刘红姣1,晋梅1*(1. 江汉大学,湖北 武汉 430056; 2. 长江存储科技有限责任公司,湖北 武汉 430056)摘 要: 针对高黏度流体在弓形折流板管壳式换热器中综合传热性能低的问题,采用甘油作为壳程高黏度流体模型介质,通过三维数值模拟计算方法对其在弓形折流板和三分螺旋折流板管壳式换热器的壳程流动特性和传热综合性能进行研究。
结果表明:甘油在三分螺旋折流板换热器壳程中呈螺旋状流动状态,相比于弓形折流板而言,虽然传热性能降低,但有效降低了壳程压降,热增强因子TEF 提升了4.84%~28.95%。
关 键 词:三分螺旋折流板;弓形折流板;数值模拟;综合性能中图分类号:TQ015 文献标识码: A 文章编号:1004-0935(2024)04-0533-04管壳式换热器是一种广泛用于化工、炼油、冶金等工业生产过程中热量交换的单元设备。
折流板作为管壳式换热器内构件,既可提高传热效果,又可起到支撑换热器管束的作用[1-3]。
作为壳程流动介质的高黏度流体在传热过程中,流体的速度分布和温度分布均呈抛物线型分布,因此高黏度流体在管壳式换热器的传热过程中普遍存在传热效率低的问题[4]。
采用各种强化措施以便在提高高黏度流体传热系数的同时降低流动阻力,已成为提高高黏度流体在管壳式换热器中综合传热性能的研究热点。
近年来,众多研究者提出一种与换热管呈一定安装角度的连续螺旋折流板管壳式换热器[5-7]。
相比于传统弓形折流板而言,壳程流体在连续螺旋折流板换热器的壳程流动过程中,可形成连续螺旋状流动状态以减少壳程滞流死区,有效降低了管壳式换热器的压力损失,从而提高换热器的换热效率,同时,螺旋状的流动状态可减小壳程流体对换热管束的冲刷,可有效避免设备的剧烈振荡以延长管壳式换热器的使用寿命。
(影响换热器总传热系数的原因

1L: 1、结构;2、介质;3、运行参数2L: 传热系数的大小与冷热流体的性质、换热的操作条件(如流速、温度等)、传热面的结垢状况以及换热器的结构和尺寸等许多因素有关。
对流传热十分复杂,垢层热阻又难以确定,因此传热系数的计算值与实际值往往相差较大。
在设计换热器时,最好有实测值或生产中积累的经验数据作为参考。
3L: 换热器的总传热系数主要与换热管两侧的膜传热系数和换热管的热阻有关,因而换热器的总传热系数与下列参数有关:1.换热管、壳程流体的物性数据(粘度、表面张力、密度等);2.换热管、壳程流体的流速有关;3.换热管的热阻有关。
4L: 在传热基本方程式Q=KAΔtm中,传热量Q是生产任务所规定的,温度差Δtm之值由冷、热流体进、出换热器的始、终温度决定,也是由工艺要求给出的条件,则传热面积A之值与总传热系数K值密切相关,因此,如何合理地确定K值,是设计换热器中的一个重要问题。
目前,总传热系数K值有三个来源:一是选取经验值,即目前生产设备中所用的经过实践证实并总结出来的生产实践数据;二是实验测定K值;三是计算。
在传热计算中,如何合理地确定K值,是设计换热器中的一个重要问题。
而在设计中往往参照在工艺条件相仿、类似设备上所得较为成熟的生产数据作为设计依据。
工业生产用列管式换热器中总传热系数值的大致范围见表4-10列管式换热器中K值大致范围热流体冷流体总传热系数,KW/m2·K水水850~1700轻油水340~910重油水60~280气体水17~280水蒸汽冷凝水1420~4250水蒸汽冷凝气体30~300低沸点烃类蒸汽冷凝(常压)水455~1140高沸点烃类蒸汽冷凝(减压)水60~170水蒸汽冷凝水沸腾2000~4250水蒸汽冷凝轻油沸腾455~1020水蒸汽冷凝重油沸腾140~425总传热系数的计算前述确定K值的方法虽然简单,但往往会因具体条件不完全符合所设计的情况,而影响到设计的可靠性。
所以,还必须对传热过程进行理论上的分析,以了解各种因素对传热过程的影响,从而建立起计算总传热系数K的定量式。
分析影响换热器设计的制约因素并解释其具体影响方式和具体解决方

分析影响换热器设计的制约因素并解释其具体影响方式和
具体解决方
1、环境温度:换热器外部的环境温度直接影响换热器的蒸发或冷凝温度,直接决定换热器管内外的温差,换热器温差越大,则换热能力越大。
2、环境湿度:制冷时室内湿球温度对冷量的影响很大,正常情况下,环境湿度越高,换热器换热效果越好。
3、通风量、风速:一般情况下风量越大、风速越高,换热能力越强,换热效率越高,但同时产生的噪音也越高,所以需要根据性能指标要求合理确定风量。
室外风量选择同样存在换热能力与噪音的矛盾,一般情况下单排换热器迎风面积相对较大,风量较大。
4、压缩机能力:换热器的换热能力与压缩机能力成正比,压缩机排量大,制冷剂在系统中的循环量大,会加快换热器管内制冷剂的流速,提高管内侧换热效率。
但如果用大马拉小车,则成本上升、EER下降,有点得不偿失,一般不提倡,仅适用换热器过小补偿。
- 1、下载文档前请自行甄别文档内容的完整性,平台不提供额外的编辑、内容补充、找答案等附加服务。
- 2、"仅部分预览"的文档,不可在线预览部分如存在完整性等问题,可反馈申请退款(可完整预览的文档不适用该条件!)。
- 3、如文档侵犯您的权益,请联系客服反馈,我们会尽快为您处理(人工客服工作时间:9:00-18:30)。
管壳式换热器由于结构可靠、技术成熟、适用面广,是应用于化工,石油,制冷等行业的一种通用设备.管壳式换热器的研究方法一般有实验研究、理论分析研究与数值模拟研究3种,随着计算机技术的发展,数值模拟已成为主要的研究方法. 最早对壳管式换热器进行数值模拟研究的是英国学者Patankar和Spalding,他们在1974年提出分布阻力、体积多孔度的概念,实现对壳管式换热器壳程流场的数值模拟.多孔介质模型的主要缺点是分布阻力和分布热源的模型和系数要依靠经验来确定,其精度难以保证.建立壳管式换热器实体模型进行模拟计算,能得到比较详细可靠的壳侧流场与温度场.
管壳换热器的折流板数目、位置、缺口高度、换热管的排列方式等影响换热器的壳程管表面换热系数和壳程压降.现有文献大都只研究了某一个方面[1-2],笔者旨在用大型CFD软件FLUENT, 采用数值模拟方法分析和总结折流板间距、弓形折流板缺口高度、进口段折流板与管板的距离等管壳式换热器的结构形式对换热器综合性能的影响.评价不同结构下传热和流动性能的优劣,采用现有文献常用的表面换热系数与压降之比h/Δp, 得到不同结构下h/Δp的变化规律.
1数值模拟及结果分析
1. 1流体动力学控制方程
流体流动受物理守恒定律的支配,包括[3-4]:
质量守恒方程:
1. 2模型验证
笔者建立的换热器数学模型采用与实物模型相一致的几何参数:换热器总长1 940 mm,筒体内径151 mm,折流板直径148 mm,换热管为?19 ×2 mm的管子,正方形排列.根据换热器尺寸用GAMBIT建立模型,由于换热器结构的对称性,可以采用对称性边界条件,建立整体模型的一半,进行网格划分.划分网格时根据折流板的位置将模型分割成多个块,分块划分网格.然后导入FLU- ENT设置与实验相一致的边界条件:换热器壳侧流体介质采用空气,管内的流体为饱和水蒸气,饱和水蒸气不断由锅炉产生,认为管内温度恒定,因此在模拟时可设置管壁温度为恒温.
数值模拟时选用标准κ-ε湍流模型,壁面采用无滑移边界条件[5],近壁面处理采用标准壁面函数法。
采用此壁面函数时,壁面处网格不需要加密,只需要把近壁面的第一个内节点布置在对数分布率成立的区域内,即配置到旺盛湍流区域.当与壁面相邻的控制体积的节点满足y*≥11.225,30<y+<300则流动处于对数率层;网格满足上述要求才能取得较为合理的模拟结果[6].
控制方程采用有限体积法离散,压力速度耦合采用SIMPLE算法,压力插补格式选择Standard格式,其他均采用二阶迎风格式.能量方程收敛精度在10-8以下,其他方程收敛精度在10-3以下,数值模拟结果与实验结果相比较如表1所示.
实验中有污垢等影响,模拟时忽略了这些因素,因此进出口温差和压降都相对实验值小.由表1可以看出模拟值与实验值的误差在工程误差允许范围之内,说明了模型建立和数值计算的正确性.以下采用相同的模拟方法进行数值模拟,读取网格无关解作为本实验数字依据.
1. 3不同结构的数值模拟及分析
1. 3. 1不同折流板间距的影响
进行换热器设计时[7],推荐折流板间距一般不小于壳体内径的1/5,且不小于50 mm,跨度过大也会因流体诱导振动引起换热管不稳定以及流通截面增大造成相同流量下换热系数降低.采用实验模型整体结构参数,间距与壳体内径之比为λ,改变折流板间距,设定缺口高度与壳体内径百分比约为25%,分别在流量为80, 120, 160 m2/h 下,按表2所列的折流
板间距参数,建模进行数值模拟.
模拟结果如图1、2所示,从图中可以看出随着折流板数目的减少,壳程的压降逐渐减小.管表面换热系数h也逐渐减小.随着折流板数目的增多, 壳侧的‘Z’形流动更加接近理想横流,并且相邻两块折流板之间通道面积减小,使流体横掠管束的速度增大,换热系数提高.图3表明相同的流量,随着折流板间距的增加,其综合性能逐渐增加.
1. 3. 2不同缺口高度的影响
进行管壳式换热器设计时,缺口高度宜取0. 2~0. 45倍的壳体内径[7],管壳式换热器整体模型仍然采用上述参数,折流板间距定为97 mm.
只改变折流板缺口高度,流量分别为100, 120, 140 m3/h,缺口高度与壳筒直径Di之比的百分数如表 3.采用与前面相一致的建模和模拟方法分别对上述结构分别进行数值模拟,得到壳程压降和壳侧管表面换热系数随流量的变化趋势如图4、5所示.
从图4中可以看出,同一流量下随着折流板缺口高度的增加,压降减少,趋势越来越缓慢;换热器壳侧管表面换热系数h随着缺口高度的增加而降低,这也是因为随着折流板缺口高度增加时, 壳侧流体流动偏离理想横流流动的程度就越大.
比较在相同折流板间距下,不同的折流板缺口高度下综合性能的变化趋势如图6所示,可以看出综合性能随着缺口高度的增加而增加,趋势越来越缓.
1.3.3不同进口段长度的影响
管壳式换热器因为其结构特点,壳程的流动可以分为进口段、中间段和出口段.中间段的流体从进口翻过第二块折流板后到出口前一块折流板之间,流体流动和传热可视为周期性充分发展状态. 考察进口段对中间周期段的影响,在折流板间距为97mm,缺口高度与壳筒内径比约为25%的结构下,仅改变第一块折流板与管板的距离进行建模和数值模拟,其结构参数如表4所示,通过数值模拟, 结果如图7、8所示.
进出口接管与管板的位置不变,换热器总长度不变,则换热管的有效换热长度没有变,改变第一块折流板与管板的距离,即改变折流板与进出口接管的距离.图7、8表明,不同的进口段长度,换热器壳程压降基本保持不变,改变第一块折流板与管板之间的间距,只是改变了端部区错流管束压降,根据贝尔-台华设计公式,也说明改变间距对压降影响不大.增加折流板与管板的距离,表面换热系数呈下降趋势,是由于进口段温差大,越早进入横向流,表面换热系数就越大.显然其综合性能随着距离的增加是下降的.
2结论
通过对弓形折流板管壳式换热器不同结构参数进行数值模拟,表明折流板换热器壳程的压降和壳程管表面换热系数随着折流板数目的增加而增加,随着折流板缺口高度的增加而减小,而其综合性能随着折流板数目的增加而减小,随着折流板缺口高度的增加而增加;第一块折流板与管板的距离对压降的影响较小,但对表面换热系数影响相对较大.比较不同结构下的综合性能,对弓形折流板换热器的结构优化设计有一定的指导意义.。