格里森凤凰磨齿机参考点校正方法分析
参考点调整

参考点调整参考点是确定机床坐标原点的基准,而且还是轴的软限位和各种误差补偿生效的条件。
如果采用带绝对值编码器的伺服电机,机床的坐标原点是在机床调试时设定的。
但是由于成本原因,大多数数控机床都采用带增量型编码器的伺服电机。
编码器采用光电原理将角位置进行编码,在编码器输出的位置编码信息中,还有一个零脉冲信号,编码器每转产生一个零脉冲。
当伺服电机安装到机床床身时,伺服电机的位置确定,编码器零脉冲的角位置也就确定了。
由于编码器每转产生一个零脉冲,在坐标轴的整个行程内有很多零脉冲,这些零脉冲之间的距离是相等的,而且每个零脉冲在机床坐标系统的位置是绝对确定的。
为了确定坐标轴的原点,可以利用某一个零脉冲的位置作为基准,这个基准就是坐标轴的参考点。
为了确定参考点的位置,通常在数控机床的坐标轴上配置一个参考点行程开关。
数控机床在开机后,首先要寻找参考点行程开关,在找到参考点行程开关之后,在寻找与参考点行程开关距离最近的一个零脉冲作为该坐标的参考点,根据参考点就可以确定机床的原点了。
所以利用编码器的零脉冲可以准确地定位机床坐标原点。
采用增量式编码器时,必须进行返回参考点的操作,数控系统才能够找到参考点,从而确定机床各轴的原点。
使用绝对值编码器时,初始配置轴之后也要执行参考点调整操作,才能够实现机电系统同步。
所以在数控机床上电之后第一个必要执行的操作就是返回机床各轴的参考点,图5-18所示为参考点配置的一个简单例子。
图5-18 参考点配置的一个简单例子(1)参考点调整概要在840D/810D数控系统中,回参考点的方式可以有通道回参考点,即通道内的轴以规定的次序依次执行回参考点动作;也可以轴回参考点,即每个轴独立回参考点。
执行回参考点操作时,可以带有参考点档块,也可以没有参考点档块。
执行回参考点操作过程中,可以是点动形式,也可以是连续方式。
可以通过机床数据MD来实现这些配置。
λ MD 34110: REFP_CYCLE_NR 通道特定的回参考点;1 至n——确定通道特定回参考点的各轴的起动顺序;0——该机床轴不能由通道指定回参考点功能起动;-1——“NC起动”可以不必要求本轴回参考点。
对格里森弧齿锥齿轮接触区的认识与修正

对格里森弧齿锥齿轮接触区的认识与修正广东梅州齿轮厂李普华(广东省梅州市514016)摘要:阐述了对格里森弧齿锥齿轮接触区的认识,介绍了齿面接触区的基本修正方法,分析了接触区的质量要求以及与啮合噪声等质量之间的关系。
关键词:弧齿锥齿轮接触区修正Recognizing and Correcting the Contact Zone on Gleason Spiral Bevel Gear Li Pu Hua Guangdong Meizhou Gear Factory (Meizhou Guangdong, 514016)Summary: Described the knowledge of contact zone on Gleason spiral bevel gear, introduced the basic correction method of tooth surface contact zone, analyzed the quality relationships between the contact zone and the meshing noise requirements.Key words: spiral bevel gear contact zone correction弧齿锥齿轮和准双曲面齿轮(以下简称为弧齿锥齿轮)具有重迭系数大、承载能力强、运转平稳、噪声低的特点。
随着工业技术的不断进步和发展,对弧齿锥齿轮的传动性能也不断提出更高的要求。
如何提高弧齿锥齿轮的传动性能,降低啮合噪声是一个很复杂的技术问题,这里只是对与弧齿锥齿轮啮合性能密切相关的接触区进行一些分析讨论。
一、对接触区的认识1.接触区就是当齿轮旋转进入啮合直至脱离啮合期间,轮齿相互接触的区域。
它与齿轮的平稳运转,使用寿命和噪声有直接的影响,它是齿轮设计的一个关键特性。
2.接触区主要可分为热前接触区,热后(成品)接触区,安装使用接触区。
磨齿机精度测量与控制技术研究

磨齿机精度测量与控制技术研究随着工业自动化的不断发展,磨齿机在机械加工领域中扮演着重要的角色。
磨齿机的任务是加工各种类型的齿轮,以确保其精度和质量。
而精度测量与控制技术是保证磨齿机性能优越的关键因素之一。
本文将探讨磨齿机精度测量与控制技术的研究进展,并介绍一些常用的方法和工具,以支持精度控制和质量管理。
首先,磨齿机精度测量是确保齿轮工件符合规格要求的关键步骤。
在过去,传统的测量方法主要依赖人工测量,如使用千分尺、游标卡尺等测量工具。
然而,这种方法存在人为误差的可能性,同时也受限于操作人员的技能和经验。
随着科技的进步,磨齿机精度测量与控制技术得到了显著改进。
现代磨齿机上常用的测量方法包括机床内部测量和机床外部测量。
机床内部测量是指在磨齿机加工过程中实时进行测量。
这种方法通过安装传感器和测量仪器在磨齿机上,对工件进行实时测量和反馈控制。
例如,光电测量传感器可以用来监测切削力和切削温度,以便及时调整磨削参数,保持精度和质量。
机床外部测量是指将工件取出磨齿机后进行测量。
这种方法通过使用三维坐标测量机、光学轮廓仪等精密测量设备,对工件进行高精度的尺寸和形状测量。
这些测量设备可以提供更准确的测量结果,同时也可以用来验证磨齿机的性能和精度。
除了精度测量技术,磨齿机精度控制技术也是确保齿轮加工质量的重要方面。
精度控制技术通过监测和调整磨齿机的工作参数,以保持加工过程的稳定性和一致性。
一种常用的精度控制技术是闭环控制系统。
该系统通过将测量结果与预定的规范进行比较,并根据差异调整切削力、加工速度等参数。
这种反馈控制的方式可以及时纠正可能导致工件质量问题的加工偏差。
此外,自动化技术在磨齿机精度控制中也发挥着重要作用。
自动化技术可以实现磨齿机的自动调整和优化,以提高加工效率和工件质量。
例如,采用自动化系统可以实现自动换刀、自动量具校准、自动刀具磨损检测等功能,从而减少操作人员的干预,并提高磨齿机的稳定性和精度。
总之,磨齿机精度测量与控制技术的研究和应用对于保证齿轮加工质量至关重要。
磨齿机数控轴及测头参考点标定

并换算 出 轴 与 c轴 中心坐标 ( 图 5 。 见 ) 用千分垫直接测量 轴距 平尺测量
仪 ,记 录水 平仪 的读 数 。在 轴 端 放 置 一 电 子 水 平
( )标定 z轴 6
仪 ,转动 A轴 ,使 其 上 水 平 仪 的 读 数 与 工 作 台 ( c
轴 )上 平尺水 平 仪 的 读 数 相 等 ,调 整 A轴 角 度 为 0
^
I
I
▲
侧 同样压 一
、 f , 上
…
! i
、 ’
! i
m
丫 上
块 百分 表 ,这 样就 可 以更方 便 的读 出测量
值 比 2 m 大 3m
速而且可靠的测量方法。
为了满足测量要求 ,我们设计了一套检具借 助百 分
面 C 尺寸 ,在 z轴上读数 ,并换算 出 z轴与 c 中 轴
心坐标 ( 见图 6 。 )
参磊 工 ̄n /r j -
WWW. not wo ki r a/ r ng1 0 co 95 . m
兰!
!塑 _ !
Me s rm  ̄ a ue e
.
黪
利 用 百 分 表 测 异 形 板 位 置 尺 寸
. I I J I
彗W 翟 1 .
l -J J I - I IL - I
文\ 千垫 分
— —
J
1
.
【 ! Lபைடு நூலகம்
图 3 标定 轴 图 4 标定 轴
J
定平尺两侧 面 c 、c 及两端面 D 、 c 的位置尺 。 D 与 轴
、
( )标定 轴 3
调 整 z轴位置 ,用千分垫测 出 轴
磨齿机齿形误差分析及调整【干货】
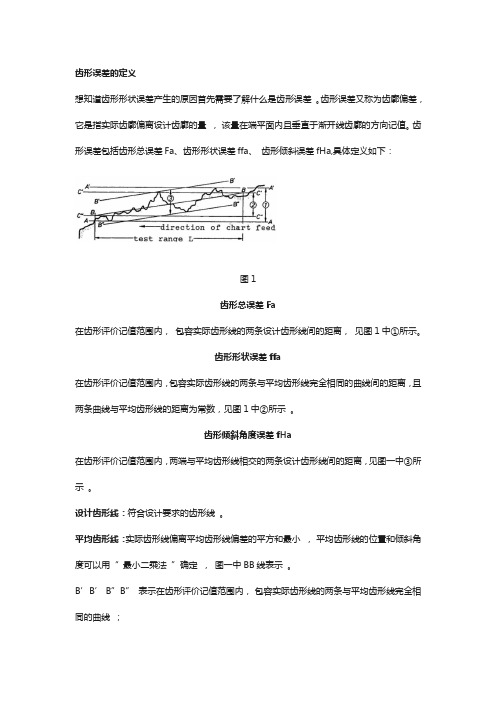
齿形误差的定义想知道齿形形状误差产生的原因首先需要了解什么是齿形误差。
齿形误差又称为齿廓偏差,它是指实际齿廓偏离设计齿廓的量,该量在端平面内且垂直于渐开线齿廓的方向记值。
齿形误差包括齿形总误差Fa、齿形形状误差ffa、齿形倾斜误差fHa,具体定义如下:图1齿形总误差Fa在齿形评价记值范围内,包容实际齿形线的两条设计齿形线间的距离,见图1中①所示。
齿形形状误差ffa在齿形评价记值范围内,包容实际齿形线的两条与平均齿形线完全相同的曲线间的距离,且两条曲线与平均齿形线的距离为常数,见图1中②所示。
齿形倾斜角度误差fHa在齿形评价记值范围内,两端与平均齿形线相交的两条设计齿形线间的距离,见图一中③所示。
设计齿形线:符合设计要求的齿形线。
平均齿形线:实际齿形线偏离平均齿形线偏差的平方和最小,平均齿形线的位置和倾斜角度可以用“最小二乘法”确定,图一中BB线表示。
B’B’B”B”表示在齿形评价记值范围内,包容实际齿形线的两条与平均齿形线完全相同的曲线;C’C’C”C”表示在齿形评价记值范围内,两端与平均齿形线相交的两条设计齿形线;AA A ’A’表示在齿形评价记值范围内,包容实际齿形线的两条设计齿形线。
齿形形状误差分析我公司在实际生产过程中使用的是进口数控成型磨齿机,其采用的是成型法磨削,即把砂轮修整成和工件轮廓相吻合的形状进行磨削。
砂轮的轮廓形状精度决定了齿形形状误差值的大小,通过对齿形形状误差(ffa)定义的理解,齿形的形状误差值来自于齿形波纹的深度,标准设计齿形理论上是一直线,那么在生产过程中实际齿形线上的波纹是如何产生的呢?波纹的大小又受哪些因素的影响呢?我将从以下几个方面去进行分析和探讨:砂轮在成型法磨削中,磨齿机所使用的刀具是砂轮。
砂轮的选用主要取决于齿轮材料的可磨削性及其所要求的表面质量、修整滚轮和可修整砂轮的耐用度及所要求的磨削功率。
砂轮的材质将影响着砂轮的磨削能力,也影响着所磨齿轮齿面的表面特性,其中齿面粗糙度大小决定了齿形波纹度的大小从而影响着齿形的形状误差值。
数控机床参考点回归的方式及常见故障研究_0

数控机床参考点回归的方式及常见故障研究【摘要】参考点的回归对数控机床能否正常准确地运行起着非常重要的作用,同时也关系到零件加工的精度等问题。
本文就数控机床参考点回归方式以及常见故障进行简要探讨。
【关键词】数控机床;参考点回归参考点也就是物理中的参照点,数控机床中的参考点即是针对于机床零点设置的固定位置。
机床启动时,首先应该回归参考点,接着再进行工作。
数控机床在启动时能否准确回归到参考点直接关系到机床在工作中是否能够保证零件加工的精度。
参考点是联系机床坐标系和工件坐标系的重要关系点。
本文通过探讨数控机床参考点回归的必要性,提出了研究此问题的意义,并介绍了数控机床回参考点的方法,还针对数控机床参考点回归的常见故障进行了分析和讨论。
1 参考点回归研究的必要性参考点回归是否准确在机床运行中是不容忽视的环节。
在数控机床上,各坐标轴的正方向是定义好的,因此只要机床原点一旦确定,机床坐标也就确定了。
机床原点往往是由机床厂家在设计机床时就确定了,但这仅仅是机械意义上的,计算机数控系统还是不能识别,即数控系统并不知道以哪一点作为基准对机床工作台的位置进行跟踪、显示等。
为了让系统识别机床原点,以建立机床坐标系,就需要执行同参考点(零点)的操作。
2 回归问题的提出数控机床回参考点的方法,按检测器检测原点信号的方式可分为两种:一种是栅点法,另一种是磁开关法。
在栅点法中,机械本体上安装有减速撞块或减速开关。
检测器随着电机转一圈而产生一个栅点或一个零位脉冲信号,数控系统检测到的第一个栅点或零位信号即为原点。
在磁开关法中,机械本体上安装有磁铁及磁感应原点开关,当磁感应原点开关检测到原点信号后,伺服电机立即停止,该停止点被认作原点。
栅点法的特点是参考点的保持性好,不易出现漂移。
磁开关法的特点是软件及硬件简单,但机床回参考点不稳定,因为参考点的位置会随着伺服电机速度的变化而成比例地漂移。
因此,几乎所有的数控机床都采用栅点法回参考点。
成形磨齿机的尺寸测量与精度校正

成形磨齿机的尺寸测量与精度校正成形磨齿机是一种广泛应用于工业生产中的重要设备,主要用于加工各种类型的齿轮零部件。
在磨齿加工过程中,尺寸测量和精度校正是确保齿轮质量和加工效果的关键环节。
本文将介绍成形磨齿机尺寸测量和精度校正的基本原理及操作技巧。
首先,尺寸测量是保证成形磨齿机加工精度的重要步骤。
尺寸测量可以通过多种方法进行,常用的方法包括测量仪器测量和三坐标测量。
测量仪器测量是一种常见的尺寸测量方法,它可以通过使用千分尺、游标卡尺、光学显微镜等工具来测量齿轮的直径、模数、齿顶高、齿根高等关键尺寸参数。
在进行测量时,需要确保测量仪器的精度和准确性,并注意避免误差的产生。
另一种常用的尺寸测量方法是三坐标测量。
通过使用三坐标测量仪器,可以在三个坐标方向上对齿轮的形状和尺寸进行测量,从而获取更为准确和精细的尺寸数据。
三坐标测量方法可以帮助工作人员更准确地了解并掌握齿轮的实际尺寸情况,为后续的精度校正提供数据支持。
除了尺寸测量,精度校正也是确保成形磨齿机加工精度的重要步骤。
首先,精度校正可以通过调整成形磨齿机的各个部件和参数来实现。
例如,可以通过调整工作台的水平度、切削速度和进给速度等参数,来达到更高的加工精度。
此外,还可以通过更换磨轮、修整磨齿室等方式,来提高磨齿机的加工精度。
同时,还可以通过进行齿轮的磨前磨齿试验来进行精度校正。
在磨前磨齿试验中,工作人员可以在成形磨齿机上进行试验加工,再通过尺寸测量和评估来判断加工结果的精度情况。
通过反复试验和调整,可以不断优化磨齿机的加工参数和工艺流程,从而实现更高的加工精度。
此外,还可以借助先进的数控技术来进行精度校正。
通过数控系统可以实现对成形磨齿机的加工参数及工艺流程进行自动控制和调整,从而提高加工精度和效率。
数控技术的应用,不仅可以提高成形磨齿机的工作精度,还可以提高生产效率和品质稳定性。
需要注意的是,尺寸测量和精度校正是一个复杂而细致的过程,需要工作人员具备丰富的经验和技术知识。
成形磨齿机的径向进给误差分析与补偿

成形磨齿机的径向进给误差分析与补偿成形磨齿机是一种用于加工齿轮的重要设备,其精度和效率对于齿轮的质量影响重大。
在使用成形磨齿机进行齿轮加工时,经常会遇到径向进给误差的问题,这会导致齿轮的几何形状和尺寸不符合要求。
因此,分析和补偿成形磨齿机的径向进给误差是非常必要的。
首先,我们需要了解成形磨齿机的径向进给误差是如何产生的。
成形磨齿机工作时,刀盘在齿轮上分别做渐开线和端面磨削运动,刀盘的径向进给是通过驱动装置实现的。
然而,在实际加工过程中,由于机器零件的制造和装配误差、切齿刀具的磨损和变形等因素影响,径向进给误差就会产生。
其次,针对成形磨齿机的径向进给误差,可以采取以下分析方法。
首先,通过测量齿轮加工后的几何尺寸,可以计算出实际加工误差。
然后,通过对成形磨齿机各个部件和装置的检查和测试,找出可能影响径向进给误差的原因。
比如,检查驱动装置的精度和稳定性,以及刀盘的磨削性能等。
最后,结合实际加工数据和分析结果,对成形磨齿机的径向进给误差进行定量评估和分析。
在分析的基础上,我们可以针对成形磨齿机的径向进给误差,采取一些补偿措施。
首先,可以通过调整驱动装置的参数,如速度、加速度等,来改善径向进给的精度和稳定性。
其次,可以对刀盘磨削参数进行优化,例如切削速度、进给速度等,以减小径向进给误差的影响。
此外,针对机器零件的制造和装配误差,可以进行精确校正和调整,以提高成形磨齿机的加工精度。
除了对成形磨齿机进行分析和补偿,还可以通过一些先进的技术手段来改善加工精度。
例如,可以采用先进的控制系统,实时监测和调整成形磨齿机的径向进给,提高加工精度和稳定性。
另外,可以采用先进的刀具和磨削材料,提高切削效率和加工质量。
此外,还可以结合数控技术,实现自动化操作和优化加工过程。
在实际应用中,成形磨齿机的径向进给误差分析和补偿是一个不断探索和改进的过程。
需要综合考虑机器设备、刀具材料、加工参数等多个因素,通过不断地优化和改进,提高成形磨齿机的加工精度和效率。
- 1、下载文档前请自行甄别文档内容的完整性,平台不提供额外的编辑、内容补充、找答案等附加服务。
- 2、"仅部分预览"的文档,不可在线预览部分如存在完整性等问题,可反馈申请退款(可完整预览的文档不适用该条件!)。
- 3、如文档侵犯您的权益,请联系客服反馈,我们会尽快为您处理(人工客服工作时间:9:00-18:30)。
格里森凤凰磨齿机参考点校正方法分析李劲(中国航发中传机械有限公司,湖南长沙410200)摘要:维修人员经常用到格里森凤凰磨齿机参考点的校正,需要掌握其原理方法并积极实践。
介绍450PG磨齿机和275PG磨齿机的参考点校正方法。
关键词:磨齿机;校正;维修;分析中图分类号:TP271+.7文献标识码:B DOI:10.16621/ki.issn1001-0599.2019.03D.740引言美国格里森凤凰磨齿机是用于螺旋锥齿轮磨削加工的精密数控机床,广泛应用于航天、航空、汽车、减速机等齿轮加工行业,自1992年推出第一代数控凤凰磨齿机以来,以其高精度、高稳定性、可靠性及高效率,在世界齿轮加工领域占据着举足轻重的地位。
中国航发中传机械有限公司作为航空齿轮及减速器的专业化生产厂商,也采购了一系列的格里森凤凰磨齿设备。
在对这些设备的使用和维护过程中,经常碰到一些与各轴参考点校正相关的问题或故障,所谓的参考点校正就是机床参考点的找正(参考点的机械绝对位置与数控系统显示位置吻合一致)。
由于格里森凤凰磨齿机采用的是调整卡参数(由调整卡参数自动生成加工程序)加工,其加工的坐标系是以机床参考点为基准点的,因此当机床发生故障导致参考点数据丢失或参考点发生变化,则机床的坐标系就会丢失或移位,机床本身或其加工出的产品就会出问题,此时必须重新进行参考点校正工作。
1磨齿机工作原理中国航发中传机械有限公司现有的格里森凤凰磨齿机系列有275PG、450PG、800PG、600PG等,都采用FANUC数控系统。
其中,450PG及800PG为第一代凤凰磨齿机,275PG、600PG为第二代凤凰磨齿机。
由于生产的年限不一样,第一代与第二代磨齿机的机械及电气结构有所差别,第一代凤凰磨齿机采用的是工件主轴(A轴)与B轴摆角轴、Z轴一体结构,砂轮主轴C轴、X轴在Y轴立柱上(图1)。
其采用的是增量式光栅尺,其参考点数据不会记忆,每次重新开机后需重新回参考点,回参考点方式为减速开关回零方式。
第二代磨齿机采用的是砂轮主轴(C轴)与B轴摆角轴、Z轴一体,工件主轴(A轴)、X轴在Y轴立柱上(图2)。
其采用的是绝对式光栅尺,参考点数据被系统记忆,只需在第一次调试时设好参考点.正常使用时无需执行回参考点操作。
虽然两代磨齿机在结构上有所区别,但参考点校正的原理基本一致,只是在参数的设定和调整方式上有所不同,下面将以第一代的450PG以及第二代的275PG为代表,分析格里森凤凰磨齿机的参考点校正工作。
2450PG磨齿机参考点校正方法分析450PG磨齿机参考点校正原理:使机床各轴参考点的绝对机械位置坐标值与数控系统显示坐标值吻合。
由于该机床使用的增量式光栅尺,机床参考点在每次开机执行回参考点操作后建立,回参考点的方式为减速开关,当机床执行减速回参考点后,机床在参考点位置的显示坐标值为FANUC系统1240参数/10000(1240参数为发那科系统参考点坐标位置参数),当机床减速开关灵敏度改变或安装位置发生变化后导致参考点发生偏移时,参考点实际绝对机械位置坐标值与其数控系统显示值(即1240参数值/10000)会有差异,因此必须确定参考点的实际绝对机械坐标值后乘以10000并输入新1240参数,通过找正各轴校正点,并记录校正点的绝对机械坐标,同时校正点的显示坐标值与参考点位置显示值(即1240参数/10000)之间的差值为参考点与校正点的绝对机械距离,而参考点的实际绝对机械坐标值=[校正点绝对机械坐标值+参考点显示坐标值(即1240参数值/10000)-校正点显示坐标值],将计算的新值乘以10000后输入1240参数,参考点校正完成。
其具体校正方法如下。
(1)首先必须清楚各轴坐标系的绝对机械位置。
根据450PG 磨齿机床绝对机械坐标的设计,机床B轴转到90°的机械绝对位置时工件主轴(A轴)端面与砂轮主轴(C轴)端面平行,同时图1第一代凤凰磨齿机坐标轴图2第二代凤凰磨齿机坐标轴设备管理与维修2019№3(下)B轴转动到90°,当工件主轴与砂轮主轴同心位置时,X,Y轴的机械绝对坐标为0位置(X,Y轴的绝对机械坐标值零点为B轴在90°时的工件主轴中心位置),同时砂轮主轴端面在Z方向的位置为Z轴的机械绝对坐标0位置。
(2)记录机床各轴的参考点坐标值1240参数,X:543142,Y:998397,B:801040,Z:3971660,方便校正后新的1240参数的计算。
(3)B轴校正。
先将B轴移至肉眼观察90°方向(工件主轴A 轴端面与砂轮主轴C轴端面平行),将表架固定在砂轮主轴上,百分表打在工件主轴端面,移动X轴使得表在工件主轴端面移动,观察百分表的读数情况,依据百分表的读数情况微调B轴坐标位置,直至在工件主轴端面全长移动范围内表的变化<0.01mm,此时B轴为该机床90°校正点的绝对机械位置。
观察机床屏幕上B轴显示的坐标位置值,比如89.9256°,参照记录的B轴1240参数,则参考点的实际绝对机械坐标值={90(校正点绝对机械坐标)+[801040(1240参数值)/10000-89.9256(校正点显示坐标值)]}=80.1784,而新的1240参数为801784。
(4)X,Y轴校正。
保持上述B轴90°位置不变,将X轴、Y轴移动到工件主轴与砂轮主轴用肉眼观察的同心位置,将百分表表座固定在砂轮主轴端面中心,将表打在工件主轴内孔内,旋转砂轮主轴一圈,观察百分表的读数,微调X,Y轴的坐标位置,使得砂轮主轴旋转一圈,百分表的变化<0.01mm,即工件主轴与砂轮主轴同心时,此时X,Y轴校正点位置即为该机床绝对机械坐标0位置。
此时观察机床数控系统显示坐标值,比如,X为0.0230,Y为-2.0000。
参照前面记录的X,Y轴1240参数,X 参考点的绝对机械位置值=[0+(543142/10000-0.0230]为50.2912,则X轴新的1240参数为542912,Y轴参考点的绝对机械位置={0+[998397/10000-(-2.0000)]}为101.8397,Y 轴新的1240参数为1018397。
(5)Z轴校正。
保持B轴90°方向,移动Z轴使工件主轴靠近砂轮主轴,将200mm的块规塞入,移动Z轴当两主轴端面与块规靠近时,微调Z轴,使得块规在两主轴端面上刚好能移动(移动有紧度、无间隙),如前所述砂轮主轴端面在Z方向的位置为Z轴的机械绝对坐标0位置,而此时工件主轴端面与砂轮主轴端面在Z轴正方向的绝对距离为200的块规长度,因此该校正点的Z轴机械绝对位置为200,记录此时Z轴数控系统显示坐标值,如202.3144,参照前面记录的Z轴1240参数,则Z 轴参考点的绝对机械位置值=[200+(397166/10000-202.3144]为394.8516,Z轴新的1240参数为3948516。
3275PG磨齿机参考点校正方法分析275PG磨齿机为第二代产品,采用的是绝对式光栅尺,机床参考点的数据被记忆,机床开关机后无需回参考点。
但当机床光栅尺发生故障导致机床参考点数据丢失时需重新进行参考点校正,其校正原理与450PG磨齿机原理相同,即使机床各轴参考点的绝对机械位置坐标值与其数控系统显示坐标值吻合,校正方法也是找到各轴校正点的绝对机械位置。
由于采用了绝对光栅尺,可任意将某一绝对机械位置设为参考点并将绝对位置坐标值输入1240参数以此坐标建立参考点,所以可以直接将校正点设为机床的参考点。
实际操作中将各轴校正点的绝对机械位置找正,机床各轴停在校正点位置不动,将校正点绝对机械坐标值乘以10000输入1240参数,同时将1815号第4位参数APZ (第4位)改为“0”,关机重启后再改为“1”(此操作为绝对式光栅尺的参考点建立操作,当APZ由“0”变为“1”时,数控系统将机床当前各轴的校正点位置作为参考点,同时数控系统显示的坐标为1240参数/10000(即校正点的绝对机械位置值,此操作只对绝对式光栅尺有效)。
此时,机床校正点即为参考点位置,且实际绝对机械位置坐标与数控系统显示坐标值重合,完成参考点校正工作,其具体校正方法如下。
(1)同样必须先清楚275PG磨齿机各轴的绝对机械坐标位置,由于275PG磨齿机与450PG结构不同,其各轴的机械绝对坐标位置有少许差别,这里需涉及到275PG机床砂轮主轴中枢距离(图3)。
X轴方向中枢距离-81.4347,Z轴方向主轴中枢距离152.3783,X轴中枢距离的数值为B轴在90°位置时砂轮主轴C端面离B轴摆动中心点在X轴方向的偏移距离,Z轴中枢距离数值为B轴在90°位置时砂轮主轴C中心离B轴摆动中心点在Z方向的偏移距离,其正、负号是以偏移方向与机床X,Z 轴的正方向是否一致来确定。
根据275PG磨齿机机床绝对机械坐标的设计,机床B轴90°位置与450PG磨齿机B轴位置相似,也是B轴转到90°时砂轮主轴C端面与工件主轴A端面平行,当B轴在90°位置时,调整Y,Z轴使砂轮主轴与工件主轴同心时,Y轴的绝对机械位置坐标值为0,Z轴的绝对机械位置坐标值为Z轴中枢距离值的绝对值即152.3783(可以理解为该机床Z轴方向设置的绝对机械0位置为B轴摆动中心点)。
而B轴为90°时,砂轮主轴端面在X轴方向的绝对机械位置为X轴中枢距离值的绝对值即81.4347(同理可理解为机床X轴方向绝对机械0位置也为B轴的摆动中心点)。
(2)校正B轴。
校正点找正方法与450PG类似,只不过将表架固定在工件主轴上,将百分表打在砂轮主轴端面(砂轮主轴与B轴一体),将B轴移动到肉眼观察的90°方向(砂轮主轴与工件主轴近似平行),移动Z轴,同时微调B轴,使百分表在砂轮主轴端面移动范围内表变化<0.01mm,此时B轴的位置就为90°校正点的绝对机械位置,将此位置作为B轴参考点位置,将900000输入1240参数,后将1815APZ(第4位)参数改为“0”,关机重启后将1815APZ改为“1”,B轴校准完成(3)校正Y轴和Z轴。
校正点找正方法与450PG类似,只不过由450PG的X轴和Y轴变成Y轴和Z轴,同样保持B轴90°不动,将Y轴、Z轴移动到工件主轴与砂轮主轴用肉眼观察的同心位置,将表架固定在砂轮主轴中心,将表打在工件主轴内孔中,旋转砂轮主轴,观察表的读数,微调Z轴、Y轴,使得百分表图3275PG磨齿机1240参数设备管理与维修2019№3(下)的变化<0.01mm,此时砂轮主轴与工件主轴同心,此时Y轴为校正点绝对机械0位置,Z轴校正点的绝对机械位置值为Z轴中枢距离,即砂轮主轴中心在Z方向与B轴摆动中心点在Z方向的偏移值152.3783,输入Y轴和Z轴1240参数分别为0和1523783,之后将1815Z和Y轴的第四位参数APZ改为“0”,关机重启后改为“1”,Y轴和Z轴参考点校正完成。