电火花细微孔加工方法研究
先进制造—微细电火花加工技术

微机械和微制造的基础——微细电火花加工技术摘要:作为一种实用的微细加工技术,微细电火花加工在加工微细轴、微小孔等小尺度的零件时具有独特的优越性。
本文简略地介绍了微细电火花加工技术的原理,分析了微细电火花加工的特点和优点,研究了微细电火花加工的关键技术,并详细介绍了一种微细电火花加工装置及其应用。
关键词:微细电火花加工原理特点关键技术装置应用0.引言微细加工技术是先进制造技术的重要组成部分,是实现微机械产品的最基本技术,不仅直接影响着尖端技术和国防工业的发展,而且还影响到机械产品的加工精度和加工表面质量,影响产品的国际竞争力。
目前,世界各国都非常重视微细加工技术,将其作为发展先进制造技术中的优先发展内容。
作为微细加工技术的一个重要分支,微细电火花加工技术因其具有设备简单、可控性好、无切削力、适用性强等一系列优点,在微小尺度零件的加工中获得大量应用,受到国内外学者的广泛关注。
1.微细电火花加工的原理及特点1.1微细电火花加工原理电火花加工(Electrical Discharge Machining)是指在绝缘介质中,通过工具电极和工件之间脉冲性火花放电时的电蚀现象对工件材料进行蚀出,以达到一定的形状尺寸和表面粗糙度要求的一种加工方法。
微细电火花加工(micro Electro Discharge Machining,简称micro-EDM)的原理与普通电火花加工并无本质区别。
电火花加工中电极材料的蚀除过程是火花放电时的电场力、磁力、热力、流体动力、电化学及胶体化学等综合作用的过程。
当脉冲电压施加到工具与工件电极之间时,极间介质被击穿并形成一个极为细小的放电通道。
放电通道是由数量大体相等的带正电粒子(正离子)和带负电粒子(电子)以及中性粒子(原子或分子)组成的等离子体。
在极间电场作用下,通道中的正离子与电子高速地向阴极和阳极运动并发生剧烈碰撞,从而在放电通道中产生大量的热;同时,阳极和阴极表面分别受到电子流和离子流的高速冲击,动能也转换为热能,在电极放电点表面产生大量的热,整个放电通道形成一个瞬时热源,其温度可达℃以上。
细孔精密加工技术
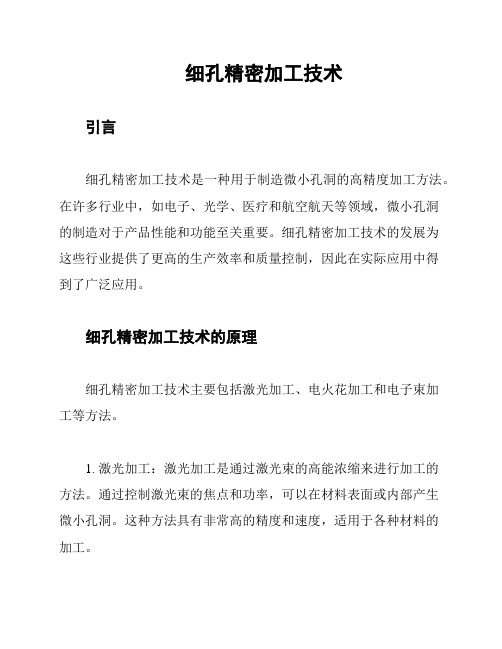
细孔精密加工技术引言细孔精密加工技术是一种用于制造微小孔洞的高精度加工方法。
在许多行业中,如电子、光学、医疗和航空航天等领域,微小孔洞的制造对于产品性能和功能至关重要。
细孔精密加工技术的发展为这些行业提供了更高的生产效率和质量控制,因此在实际应用中得到了广泛应用。
细孔精密加工技术的原理细孔精密加工技术主要包括激光加工、电火花加工和电子束加工等方法。
1. 激光加工:激光加工是通过激光束的高能浓缩来进行加工的方法。
通过控制激光束的焦点和功率,可以在材料表面或内部产生微小孔洞。
这种方法具有非常高的精度和速度,适用于各种材料的加工。
2. 电火花加工:电火花加工是一种利用电热融化材料并通过电火花放电形成孔洞的加工技术。
通过控制电火花的强度和持续时间,可以实现精确的孔洞加工。
这种方法适用于导电材料和非导电材料的加工。
3. 电子束加工:电子束加工是一种利用高速电子束的能量来加工材料的方法。
通过控制电子束的位置和能量,可以在材料表面形成微小孔洞。
这种方法具有非常高的精度和无热影响区域,适用于高硬度和高熔点材料的加工。
细孔精密加工技术的应用细孔精密加工技术在许多行业中都有广泛的应用。
1. 电子行业:细孔精密加工技术在电子行业中用于制造微型零件和半导体器件。
例如,在集成电路的制造过程中,需要对硅片进行微小孔洞的制造,以实现电子元件的连接和通路。
2. 光学行业:细孔精密加工技术在光学行业中用于制造微型透镜和光纤。
透镜的微孔制造可以实现对光束的控制和聚焦,而光纤的微孔则可以实现光信号的传输和调制。
3. 医疗行业:细孔精密加工技术在医疗行业中用于制造医疗器械和植入物。
例如,在人工心脏的制造过程中,需要对心脏泵的外壳进行微小孔洞的制造,以实现血液的循环和氧合。
4. 航空航天行业:细孔精密加工技术在航空航天行业中用于制造航空发动机和火箭发动机的喷嘴。
喷嘴的微孔制造可以实现燃料的喷射和推力的调节,从而实现飞行器的控制和动力。
总结细孔精密加工技术是一种用于制造微小孔洞的高精度加工方法,具有广泛的应用前景。
微细电火花加工技术

微细电火花加工技术微细电火花加工技术是一种高精度加工方法,它通过利用电火花放电的瞬间高温和高压能量,将工件表面的金属材料溶解、熔化、蒸发和喷射等效应,实现对工件进行微细加工的一种技术。
微细电火花加工技术具有加工精度高、表面质量好、加工效率高等优点,在模具制造、航空航天、医疗器械等领域有着广泛的应用。
微细电火花加工技术的原理是利用电火花放电过程中产生的高温等效应来加工工件。
在微细电火花加工过程中,工件和电极通过一个电解液隔开,当施加足够的电压时,电极上会产生高频率的电火花放电。
电火花放电瞬间产生的高温和高压能量会使电解液中的金属离子快速聚集在工件表面,形成微小的气泡,同时气泡瞬间爆破产生的压力将工件表面的金属材料冲击下来。
通过不断重复这个过程,就可以实现对工件表面的微细加工。
微细电火花加工技术的加工精度非常高,可以达到亚微米级别。
这是因为在电火花放电过程中,由于高温和高压能量的局部聚集作用,使得工件表面的金属材料局部熔化和蒸发,从而实现微细加工。
此外,微细电火花加工技术还可以实现对工件表面的复杂形状、小孔和细槽等微细结构的加工,具有很高的灵活性。
微细电火花加工技术的应用非常广泛。
在模具制造领域,微细电火花加工技术可以用于制造高精度的模具零件,如模具芯、模具腔等。
在航空航天领域,微细电火花加工技术可以用于制造航空发动机的涡轮叶片、航天器的结构零件等。
在医疗器械领域,微细电火花加工技术可以用于制造高精度的医疗器械零件,如人工关节、牙科种植体等。
微细电火花加工技术虽然有很多优点,但也存在一些限制。
首先,由于加工过程中电火花放电会产生高温,工件表面容易产生热应力,从而导致表面质量下降。
其次,微细电火花加工技术只适用于导电材料的加工,对于非导电材料的加工效果不佳。
此外,微细电火花加工技术的加工效率相对较低,加工速度较慢。
微细电火花加工技术是一种高精度加工方法,具有广泛的应用前景。
随着科技的不断进步和发展,微细电火花加工技术将会进一步提高加工精度和效率,为各个领域的微细加工需求提供更好的解决方案。
微细电火花加工系统及其工艺技术

微细电火花加工系统及其工艺技术微细电火花加工系统及其工艺技术微细电火花加工技术是针对微小尺寸、高精度、复杂形状的材料制造而研究开发的加工技术。
微细电火花加工系统是实现微细电火花加工技术的关键设备,它是由工作台、工作台运动系统、电极,工作液、供电系统、激光诱导系统、真空抽气系统等部分构成。
微细电火花加工系统可以实现对金属、非金属、半导体材料等的微细加工,具有加工精度高、表面光洁度好、加工速度快等优点。
与传统机械切削加工相比,微细电火花加工在加工难度高、材料硬度高、形状复杂等方面具有明显优势。
微细电火花加工技术在微小材料加工领域有着广泛的应用。
微电子学、生物医学、微机电系统(MEMS)、纳米技术等领域的发展促进了微细电火花加工技术的不断创新。
它在集成电路、微机械器件、微传感器、制造器件等方面得到了广泛应用。
微细电火花加工技术的工艺流程:首先需要准备加工工件和电极。
工件需要固定在工作台上,而电极则需要放在工作液内,与工件相对并保证合适的加工距离。
接下来,启动机器使加工液形成液柱,在构建出微弧隙后,通过加入适量的电采样工作液来增强放电过程。
然后,加工过程中,工作液中的金属粉末、气泡和其他杂质需要时刻保持排出状态。
最后,完成加工之后,需要将工作液中的金属粉末等杂质过滤,方可进行下一次加工。
微细电火花加工技术的优点主要体现在以下几个方面:1. 高加工精度:微细电火花加工系统所加工出来的零件精度可以达到微米级,远高于传统机械加工。
2. 加工形状复杂:微细电火花加工技术可以对任何形状的材料进行加工,即使是非常复杂的形状也能卓有成效。
3. 硬度高材料可加工:对于硬度高材料加工,微细电火花加工技术能够做到很好的克服困难。
4. 具有优秀的表面质量:加工表面光洁,不会出现毛刺和切割留下的凹痕等。
微细电火花加工技术是一项应用非常广泛的技术,未来在精密制造、微电子、医学等领域将有更广泛的应用。
各厂商应加强微细电火花加工技术的创新与发展,为推进智能制造、提高科技竞争力做出更大的贡献。
非磁性材料磁性场辅助微细电火花加工的基础研究
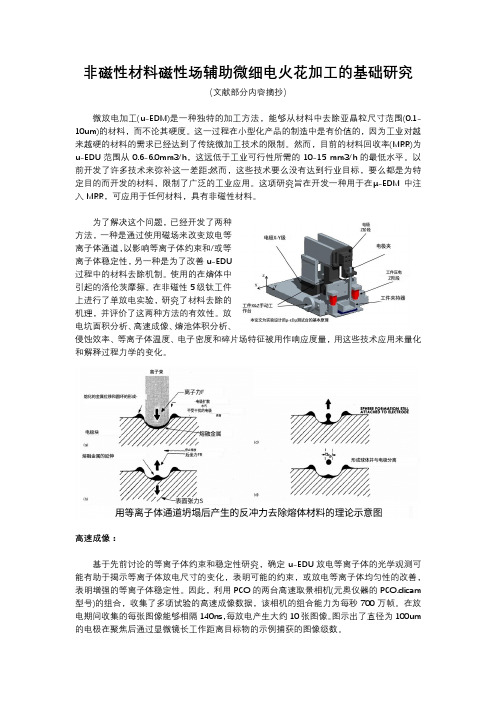
非磁性材料磁性场辅助微细电火花加工的基础研究(文献部分内容摘抄)微放电加工(u-EDM)是一种独特的加工方法,能够从材料中去除亚晶粒尺寸范围(0.1-10um)的材料,而不论其硬度。
这一过程在小型化产品的制造中是有价值的,因为工业对越来越硬的材料的需求已经达到了传统微加工技术的限制。
然而,目前的材料回收率(MRR)为u-EDU范围从0.6-6.0mm3/h,这远低于工业可行性所需的10-15 mm3/h的最低水平。
以前开发了许多技术来弥补这一差距;然而,这些技术要么没有达到行业目标,要么都是为特定目的而开发的材料,限制了广泛的工业应用。
这项研究旨在开发一种用于在μ-EDM中注入MRR,可应用于任何材料,具有非磁性材料。
为了解决这个问题,已经开发了两种方法,一种是通过使用磁场来改变放电等离子体通道,以影响等离子体约束和/或等离子体稳定性,另一种是为了改善u-EDU过程中的材料去除机制。
使用的在熔体中引起的洛伦茨摩擦。
在非磁性5级钛工件上进行了单放电实验,研究了材料去除的机理,并评价了这两种方法的有效性。
放电坑面积分析、高速成像、熔池体积分析、侵蚀效率、等离子体温度、电子密度和碎片场特征被用作响应度量,用这些技术应用来量化和解释过程力学的变化。
高速成像:基于先前讨论的等离子体约束和稳定性研究,确定u-EDU放电等离子体的光学观测可能有助于揭示等离子体放电尺寸的变化,表明可能的约束,或放电等离子体均匀性的改善,表明增强的等离子体稳定性。
因此,利用PCO的两台高速取景相机(元奥仪器的PCO.dicam 型号)的组合,收集了多项试验的高速成像数据,该相机的组合能力为每秒700万帧。
在放电期间收集的每张图像能够相隔140ns,每放电产生大约10张图像。
图示出了直径为100um 的电极在聚焦后通过显微镜长工作距离目标物的示例捕获的图像级数。
空气中u-EDM放电的高速成像示例:使用自定义图像阈值算法处理相机输出的灰度图像,以隔离图像中包含等离子的区域。
微细电火花加工技术
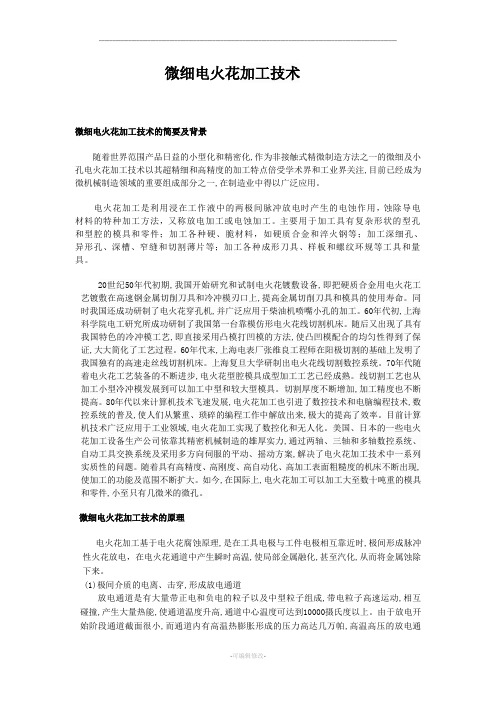
微细电火花加工技术微细电火花加工技术的简要及背景随着世界范围产品日益的小型化和精密化,作为非接触式精微制造方法之一的微细及小孔电火花加工技术以其超精细和高精度的加工特点倍受学术界和工业界关注,目前已经成为微机械制造领域的重要组成部分之一,在制造业中得以广泛应用。
电火花加工是利用浸在工作液中的两极间脉冲放电时产生的电蚀作用,蚀除导电材料的特种加工方法,又称放电加工或电蚀加工。
主要用于加工具有复杂形状的型孔和型腔的模具和零件;加工各种硬、脆材料,如硬质合金和淬火钢等;加工深细孔、异形孔、深槽、窄缝和切割薄片等;加工各种成形刀具、样板和螺纹环规等工具和量具。
20世纪50年代初期,我国开始研究和试制电火花镀敷设备,即把硬质合金用电火花工艺镀敷在高速钢金属切削刀具和冷冲模刃口上,提高金属切削刀具和模具的使用寿命。
同时我国还成功研制了电火花穿孔机,并广泛应用于柴油机喷嘴小孔的加工。
60年代初,上海科学院电工研究所成功研制了我国第一台靠模仿形电火花线切割机床。
随后又出现了具有我国特色的冷冲模工艺,即直接采用凸模打凹模的方法,使凸凹模配合的均匀性得到了保证,大大简化了工艺过程。
60年代末,上海电表厂张维良工程师在阳极切割的基础上发明了我国独有的高速走丝线切割机床。
上海复旦大学研制出电火花线切割数控系统。
70年代随着电火花工艺装备的不断进步,电火花型腔模具成型加工工艺已经成熟。
线切割工艺也从加工小型冷冲模发展到可以加工中型和较大型模具。
切割厚度不断增加,加工精度也不断提高。
80年代以来计算机技术飞速发展,电火花加工也引进了数控技术和电脑编程技术,数控系统的普及,使人们从繁重、琐碎的编程工作中解放出来,极大的提高了效率。
目前计算机技术广泛应用于工业领域,电火花加工实现了数控化和无人化。
美国、日本的一些电火花加工设备生产公司依靠其精密机械制造的雄厚实力,通过两轴、三轴和多轴数控系统、自动工具交换系统及采用多方向伺服的平动、摇动方案,解决了电火花加工技术中一系列实质性的问题。
微细电火花加工技术

微细电火花加工技术微细电火花加工技术的简要及背景随着世界范围产品日益的小型化和精密化,作为非接触式精微制造方法之一的微细及小孔电火花加工技术以其超精细和高精度的加工特点倍受学术界和工业界关注,目前已经成为微机械制造领域的重要组成部分之一,在制造业中得以广泛应用。
电火花加工是利用浸在工作液中的两极间脉冲放电时产生的电蚀作用,蚀除导电材料的特种加工方法,又称放电加工或电蚀加工。
主要用于加工具有复杂形状的型孔和型腔的模具和零件;加工各种硬、脆材料,如硬质合金和淬火钢等;加工深细孔、异形孔、深槽、窄缝和切割薄片等;加工各种成形刀具、样板和螺纹环规等工具和量具。
20世纪50年代初期,我国开始研究和试制电火花镀敷设备,即把硬质合金用电火花工艺镀敷在高速钢金属切削刀具和冷冲模刃口上,提高金属切削刀具和模具的使用寿命。
同时我国还成功研制了电火花穿孔机,并广泛应用于柴油机喷嘴小孔的加工。
60年代初,上海科学院电工研究所成功研制了我国第一台靠模仿形电火花线切割机床。
随后又出现了具有我国特色的冷冲模工艺,即直接采用凸模打凹模的方法,使凸凹模配合的均匀性得到了保证,大大简化了工艺过程。
60年代末,上海电表厂张维良工程师在阳极切割的基础上发明了我国独有的高速走丝线切割机床。
上海复旦大学研制出电火花线切割数控系统。
70年代随着电火花工艺装备的不断进步,电火花型腔模具成型加工工艺已经成熟。
线切割工艺也从加工小型冷冲模发展到可以加工中型和较大型模具。
切割厚度不断增加,加工精度也不断提高。
80年代以来计算机技术飞速发展,电火花加工也引进了数控技术和电脑编程技术,数控系统的普及,使人们从繁重、琐碎的编程工作中解放出来,极大的提高了效率。
目前计算机技术广泛应用于工业领域,电火花加工实现了数控化和无人化。
美国、日本的一些电火花加工设备生产公司依靠其精密机械制造的雄厚实力,通过两轴、三轴和多轴数控系统、自动工具交换系统及采用多方向伺服的平动、摇动方案,解决了电火花加工技术中一系列实质性的问题。
微细电火花加工的实验研究

o 2 0Fm, 法满 足需求 。基 于微细 电 火花精 密 加 .3 i 无 l
工 系 统 I D 一0 针 对 所 需 加 工 的 微 小 孔 , 先 加  ̄ M 5, E 首 工 出 了微 细 工 具 电 极 , 后 在 零 件 上 加 工 出 了 6个 然 均 匀 的微 小 孔 , 径 为 0 1 5mm( 3 。 小 孔 的 边 直 .5 图 ) 缘 均 很 规 整 , 径 一 致 性 也 很 高 , 全 满 足 了 需 求 方 直 完
微 细 电 火 花 加 工 技 术 作 为 一 种 实 现 金 属 零 件 微
小 特 征 精 密 加 工 的 重 要 _ 艺 手 段 , 引 了 国 内 外 众 T 吸 多 学 者 进 行 卓 有 成 效 的研 究 。 微 细 电 火 花 加 工 系统
与实验研究 是其 中重要 的研究 内容 。哈尔滨 工业 大
《 电加工与模具》2 I 年第 2 01 期
工 艺・ 备 装
微 细 电火 花 加 工 的 实 验 研 究
张 勇 斌 ,吉 方 ,刘 广 民 ,张 连 新 ,吴 祉 群
(中 国工程 物理研 究 院机械制 造工艺 研究所 , 四川绵 阳 6 1 0 2 9 0)
摘 要 : 于 新 研 发 的 一 套 微 细 电 火花 精 密加 工 系统 E M一0 在 金 属 材 料 上 进 行 了 一 些 典 型 的 基 D 5, 微 小特 征 精 密 加 工 实验 及 电 火花 放 电 沉 积 实验 。 该 系统 已作 为加 工 特 征 尺 寸 介 于数 十 微 米 到 数 毫
的要 求 。
件, 要求 在 围绕 其 中心 、 直 径 为 1 3 且 . 5mm 的 圆周
上 均 匀 加 工 出 6个 直 径 0 1 'n的 微 小 孔 。 用 微 . 5 DI l
- 1、下载文档前请自行甄别文档内容的完整性,平台不提供额外的编辑、内容补充、找答案等附加服务。
- 2、"仅部分预览"的文档,不可在线预览部分如存在完整性等问题,可反馈申请退款(可完整预览的文档不适用该条件!)。
- 3、如文档侵犯您的权益,请联系客服反馈,我们会尽快为您处理(人工客服工作时间:9:00-18:30)。
电火花细微孔加工方法研究
作者:李存震叶锦华
来源:《科学与财富》2017年第12期
摘要:相对于其他电火花加工操作而言,细微孔的特殊性对加工方法提出了较高的要求。
为了保证细微孔的加工质量,在实际加工处理过程中,应该严格控制各项参数,避免细微孔出现质量问题。
本文从电火花细微孔加工的特点入手,对电火花细微孔加工方法进行分析和研究。
关键词:电火花;细微孔;加工方法
前言:随着工艺技术的不断发展,电火花细微孔加工技术的出现为机械钻削加工带来了新的生机。
就我国目前情况来看,虽然电火花细微孔加工的应用范畴较为广泛,但其加工过程很容易出现质量问题。
对于生产加工厂家而言,这种现象会从一定程度上增加加工过程所需的成本,进而影响最终获利情况。
为了避免出现上述状况,生产厂家应该严格要求加工人员,保证电火花细微孔加工方法、加工操作的准确性。
一、电火花细微孔加工的特点
与常规的电火花加工方式相比,电火花细微孔加工的特点主要包含以下几种:
(一)工具电极细微性特点
电火花细微孔加工属于一种成型加工模式。
在实际加工过程中,工具电极的细微性特点增加了深径孔加工的难度。
如果加工对象孔的深径参数较大时,异常放电现象的出现可能会引发工具电极被烧毁,干扰电火花细微孔加工的顺利进行。
(二)被孔径细微性特点
通常情况下,电火花细微孔的孔径参数处于0.1mm以下。
这种具有细微性特点的孔径参数要求电火花加工过程中每个脉冲的放电能量参数相对较小。
结合我国电火花细微孔的加工经验可知,当每个脉冲的放电能量处于10-6-10-7J范围内时,其所产生的电蚀量能够满足电火花细微孔的深度及电蚀坑直径要求(分别为小于0.1μm和小于1μm)[1]。
(三)被加工孔径细微性特点
在电火花细微孔加工中,被加工孔径也具有明显的细微性特点。
为了满足这一加工要求,电极端面的放电间隙参数应该为1μm[2]。
随着加工孔深度参数的不断增加,加工放电区域工
作也的循环难度也会发生相应增加。
在这种情况下,能够保持稳定状态的放电间隙范围相对较小,所得细微孔加工成果很容易受到相关因素的影响。
此外,电火花细微孔加工过程还具有检验操作难度高、工作液性能特殊等特点。
对于生产加工企业而言,这些特点的存在不利于细微孔加工成本的控制。
为了从电火花细微孔加工中获得更多的经济利润,应该加强高效性、高质量加工方法的研发,更好地满足客户对细微孔的使用要求。
二、电火花细微孔加工方法
这里主要从以下几方面入手,对电火花细微孔加工方法进行分析和研究:
(一)微能脉冲电源方面
这种加工方法的原理在于:在对原材料进行加工的过程中,脉冲通过放电作用使得原材料产生脉冲电蚀量。
脉冲电蚀量参数的大小与电火花细微孔的加工质量有关(二者呈正相关关系)。
微能脉冲电源基于这一原理,为待加工的原材料提供了较小的脉冲电蚀量参数,有效保证了电火花细微孔的加工质量。
相对于传统电源而言,微能脉冲电源的应用优势主要包含以下几种:第一,开关特性优势。
微能脉冲电源将大功率场效应管作为自身的高速开关器件。
在实际应用过程中,微能脉冲电源通过多数载流子导电。
因此,其电火花细微孔加工过程基本不会出现少数载流子的积累效应[3]。
相对于存在积累效应的电源而言,微能脉冲电源的开关特性相关较高。
第二,开关时间优势。
从本质角度来讲,可以将微能脉冲电源内部的大功率场效应管看成一种电压控制元件。
在电火花细微孔加工过程中,这种元件前级部分的驱动电路所需的输入功率参数相对较小。
从这个角度来讲,由于大功率场效应管内部的能量传输时间相对较短,因此,微能脉冲电源开关的时间参数相对较短。
(二)电致伸缩器件方面
电致伸缩器件的应用优势主要在于:当加工环境的直流电压参数低于300V时,这种器件能够保持自身位移始终具有良好的线性[4]。
这种加工方法的加工原理为:在电火花细微孔加工过程中,脉冲电压可以对电致伸缩器件产生一定的激励作用,使得器件内部及表面产生应力波、机械振动波。
当压电换能器与细微孔加工工件之间处于刚性连接状态时,压电换能器的机械振动特性将会通过迁移作用,使得细微孔加工工件同样产生这种特性。
此时,加工材料工件在激振作用下,电火花细微孔加工的工具电机端面包铬工作液、其他相关工件的表面也会出现压力波传播。
这个传播过程可以对电火花细微孔加工过程中的放电条件及工作液循环起到良好的改善作用,进而实现提升加工过程放电脉冲利用率参数的目的。
(三)自适应控制系统方面
从本质角度来讲,电火花细微孔加工难度主要是由其加工过程中较小的放电间隙引发的。
这种加工特点对电极的放电效率提出了较高的要求(灵敏度及放电效率方面)[5]。
为了实现加工目的,利用将自适应系统与伺服控制环结合起来,构成一个完善的控制系统。
在电火花细微孔加工过程中,自适应控制系统可以对加工对象进行精确跟踪。
当伺服控制环开展电火花细微孔加工过程中出现短路状态时,自适应控制系统能够迅速判断将短路这种异常状态判断出来,并切断脉冲电源,通过回退电极的方式将加工过程中的异常放电现象消除。
结论:与常规电火花加工相比,电火花细微孔加工具有明显的工具电极细微性、加工孔径细微性、被加工孔径细微性等特点。
为了降低加工过程中质量问题的发生概率,促进电火花细微孔加工的顺利完成,可以将自适应控制系统、电致伸缩器件、微能脉冲电源等加工方法应用在细微孔加工过程中。
这些加工方法的应用可以对电蚀量产生良好的控制作用,提升放电脉冲的利用率。
因此,生产厂家可以应用这些方式,提高从电火花细微孔加工中获得的经济利润。
参考文献
[1]郑新毅. 深微孔电火花加工关键技术研究[D].大连理工大学,2010.
[2]何小龙. 精密微孔电火花电化学组合加工技术研究[D].哈尔滨工业大学,2012.
[3]殷国强. 电火花加工微孔的深径比理论模型研究[D].大连理工大学,2010.
[4]李伟. 电火花微孔加工中工具电极振动研究[D].大连理工大学,2015.
[5]郭学杰. 微细电火花加工微孔的深径比预测模型研究[D].大连理工大学,2013.。