金属切削机床车床说明书
04第四章:金属切削机床

例:CA6140; X6132; X5132 Y3150E; M7120; Z5140
2.专用机床的型号编制
专用机床型号表示方法
专用机床的型号一 般由设计单位代号和设计顺序号组成,其 表示方法为: (△)-△ 例如,北京第一机床厂设计制造的第100种 专用机床为专用铣床,其型号为B1-100。
联系动力源与执行机构之间的传动链。它使执行件获得动力以及一定的速 度和运动方向,其传动比的变化,只影响生产率或表面粗糙度,不影响加工 表面的形状和精度,如下图4-4所示的主运动传动链。
(2)内联系传动链
联系一个执行机构和另一个执行机构之间运 动的传动链。它决定着加工表面的形状和精度, 对执行机构之间的相对运动有严格要求。因此, 内联系传动链的传动比必须准确,不应有摩擦传 动或瞬时传动比变化的传动副(如皮带传动和链 传动),如下图4-4所示的进给运动传动链。
③组、系代号 为了区分机床的结构、布局和所能加工的 零件特征,每类机床可分为“0~9”十个组别。 为了更细的区分机床的结构特征,机床在组下 面又可细分为“0~9”十个系别。同一组、系 的机床,其主要结构及布局形式基本相同。机 床组、系代号用阿拉伯数字表示。机床的类、 组代号的含义见教材P5表2,组、系代号见表 2.3。
图2.8 车削成需要成形运动。 导线(母线1绕轴线O-O旋转的运动轨迹),由轨迹 法形成,需要1个成形运动B1。 形成成形回转表面的成形运动总数是形成母线和导 线所需成形运动的和,即1个成形运动(B1)。
例2 如图2.9所示,用螺 纹60°成形车刀车削三角 螺纹,试分析其母线、导 线的成形方法及所需要的 成形运动,并说明形成该 表面共需要几个成形运动。
图4-4 CA6140车床的传动系统图
3金属切削机床

在规定的工作期间内,保持机床所要求的精度,称之为 精度保持性。影响精度保持性的主要因素是磨损。磨损的影 响因素十分复杂,如结构设计、工艺、材料、热处理、润滑 、防护、使用条件等。
第二节 金属切削机床部件
一、传动系统
1.主传动系统
交流电动机驱动和直流电动机驱动。
分级变速传动和无级变速传动。
电主轴一般工作在两个转速 范围内。在基本转速范围内 (0至额定转速),驱动电机运 行在恒转矩状态,并且功率 随转速呈线性增长。超过了 额定转速,则电机工作在调 磁区以恒功率运行,转矩随 转速增加而下降。
主要特点
③ 在电主轴轴承及润滑方面,高速电主轴轴承已 经普遍采用先进的油汽润滑技术;对于超高速 电主轴采用动、静压液(气)浮轴承 (瑞士IBAG 等)和磁浮轴承,保证主轴的高速使用性能。
2.运动精度
运动精度是指机床空载并以工作速度运动时,主要零部 件的几何位置精度。如高速回转主轴的回转精度。对于高速 精密机床,运动精度是评价机床质量的一个重要指标。它与 结构设计及制造等因素有关。
第一节 概述
3.传动精度
传动精度是指机床传动系各末端执行件之间运动的协 调性和均匀性。影响传动精度的主要因素是传动系统的设 计,传动元件的制造和装配精度。
主要特点
① 在电主轴的低转速大转矩方面,低速段的输出 转矩可以达到300Nm以上,有的更是高达 600Nm(如德国的CYTEC),满足加工中对低速 扭矩的要求;
主要特点
② 在高速方面,用于加工中心电主轴的转速已达 到75000r/min(意大利CAMFIOR),其它用途的 电主轴,已经达到了260000r/min(日本SEIKO SEIKI),满足高速加工需要,提高生产率。
车床教学ppt课件

切削深度
根据工件材料和加工余量,选 择合适的切削深度,确保加工 稳定。
刀具角度
根据加工需求和刀具材料,合 理选择刀具的前角、后角和主 偏角,提高刀具使用寿命和切
削效果。
切削液的使用与注意事项
选择合适的切削液
根据加工需求和材料特性,选择合适的切削 液,如乳化液、切削油等。
定期更换切削液
保持切削液的清洁度,定期更换切削液,防 止细菌和霉菌滋生。
车床教学ppt课件
contents
目录
• 车床简介 • 车床基本操作 • 车床加工工艺 • 车床维护与保养 • 安全操作规程
01 车床简介
车床的定义与种类
总结词
车床是一种金属切削机床,主要用于加工回转体零件。根据用途和加工需求,车床可分为卧式车床、立式车床、 转塔车床等不同类型。
详细描述
车床是一种广泛应用于机械加工行业的机床设备,主要用于对金属或其他材料进行切削、钻孔、攻丝等加工,以 获得所需的几何形状和精度。根据车床主轴的安装方式和加工特点,车床可分为卧式车床、立式车床、转塔车床 等多种类型。
降低生产成本具有重要意义。
车床的发展历程与趋势
总结词
随着科技的进步,车床经历了从传统机械式到数控化 、智能化的转变。未来,车床将朝着高精度、高效率 、自动化和智能化的方向发展。
详细描述
自工业革命以来,车床经历了漫长的发展历程。从最初 的简易机械式车床到现代的数控车床和智能车床,技术 的进步使得车床的加工精度和效率不断提升。未来,随 着科技的不断发展,车床将进一步朝着高精度、高效率 、自动化和智能化的方向发展。智能化车床能够实现自 适应加工和远程监控等功能,提高生产效率和加工质量 。同时,随着工业4.0和智能制造的推进,车床的应用 领域也将不断拓展,为制造业的发展注入新的活力。
金属切削机床课程设计说明书

金属切削机床课程设计说明书课程设计说明书:金属切削机床设计目的:本课程设计旨在帮助学生全面掌握金属切削机床的操作原理、结构组成和常用工艺参数,培养学生对金属切削加工过程的理解和技术能力。
通过理论学习与实践操作相结合,使学生能够独立进行金属切削加工,并能解决常见的加工问题。
一、设计要求:1.熟悉金属切削机床的结构和工作原理,了解其主要组成部分和各部分的功能;2.掌握主轴转速、进给速度、切削深度等工艺参数的选择和调整方法;3.了解常见的切削刀具和刀具材料,并能正确选择和使用;4.掌握数控切削机床的基本编程方法,能够用数控编程实现简单零件的加工操作;5.能够根据图纸要求进行工件夹持和装夹,并进行切削加工;6.熟悉常见切削加工中的安全注意事项、故障排除和维护保养方法。
二、设计内容:1.理论学习:(1)金属切削机床的分类和工作原理;(2)金属切削机床的组成结构及各部分的功能;(3)切削刀具的种类和结构特点;(4)数控切削机床的基本编程方法;(5)切削加工中的安全注意事项及故障排除和维护保养方法。
2.实践操作:(1)金属切削机床的开机准备和操作规程;(2)切削刀具的选择、装夹和调整;(3)常见切削加工工艺参数的选择和调整;(4)根据给定的图纸要求进行零件夹持和装夹;(5)根据给定的工艺参数进行切削加工操作;(6)数控切削机床编程实践。
三、设计方法和步骤:1.理论学习:(1)查阅相关教材、参考书籍和互联网资源,研究金属切削机床的分类和工作原理,整理并了解机床的组成结构及各部分的功能;(2)深入研究不同种类的切削刀具的特点和用途,以及数控切削机床的基本编程方法;(3)分析切削加工中的安全注意事项及常见故障的排除和维护保养方法。
2.实践操作:(1)实地参观金属切削机床,并观察其开机准备和操作规程;(2)根据所学理论知识,选择合适的切削刀具,并进行装夹和调整;(3)调整切削参数,根据给定的工件要求进行切削加工操作;(4)实践数控切削机床的编程操作。
车床主轴箱设计说明书.
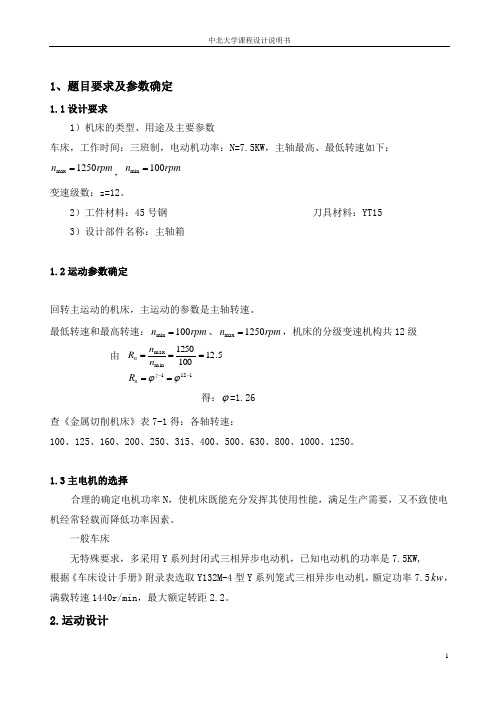
1、题目要求及参数确定1.1设计要求1)机床的类型、用途及主要参数车床,工作时间:三班制,电动机功率:N=7.5KW ,主轴最高、最低转速如下:max 1250n rpm =,min 100n rpm = 变速级数:z=12。
2)工件材料:45号钢 刀具材料:YT15 3)设计部件名称:主轴箱1.2运动参数确定回转主运动的机床,主运动的参数是主轴转速。
最低转速和最高转速:min 100n rpm =、max 1250n rpm =,机床的分级变速机构共12级由得:ϕ=1.26查《金属切削机床》表7-1得:各轴转速:100、125、160、200、250、315、400、500、630、800、1000、1250。
1.3主电机的选择合理的确定电机功率N ,使机床既能充分发挥其使用性能,满足生产需要,又不致使电机经常轻载而降低功率因素。
一般车床无特殊要求,多采用Y 系列封闭式三相异步电动机,已知电动机的功率是7.5KW, 根据《车床设计手册》附录表选取Y132M-4型Y 系列笼式三相异步电动机,额定功率7.5kw ,满载转速1440r/min ,最大额定转距2.2。
2.运动设计5.121001250min max ===n n R n 1121--==ϕϕz n R2.1 传动组的传动副数的确定传动组和传动副数可能的方案有:12=4*3 12=3*4 12=3*2*2 12=2*3*2 12=2*2*3在上列各方案中,前两个有时可以省掉一根轴。
缺点是有一个传动组内有四个传动副。
如果用一个四联滑移齿轮,则会增加轴向尺寸;如果用两个双联滑移齿轮,则操纵机构必须互锁以防止两个滑移齿轮同时啮合。
所以一般少用。
后三个方案中可根据下述原则比较:从电动机到主轴,一般为降速传动。
接近电动机处的零件,转速较高,从而转矩较小,尺寸也就较小。
如使传动副较多的传动组放在接近电动机处,则可使小尺寸的零件多些,大尺寸的零件就可以少些,就省材料了。
金属切削机床第三章 CA6140型卧式车床

8—溜板箱 9—左床腿 10—进给箱 11—交换齿轮变速机构
CA6140型卧式车床的主轴中心线在床身导轨面上的高度(中心高) 约为200mm,所以加工盘类零件的最大工件回转直径为400mm。 当加工轴类零件时,由于工件在滑板上通过,而横向滑板的上平面 位于床身导轨之上,因而刀架滑板上的最大车削直径受到限制,只 有210mm,如图3-3所示。
式中 × × ≈
。
表3-3 CA6140型卧式车床车削模数制螺纹模数表m(mm)
表3-3 CA6140型卧式车床车削模数制螺纹模数表m(mm)
Pha=kPa=k
式中有特殊因子“25.4”,而且英制螺纹的导程参数分母为分段的 等差数列(即每英寸牙数a在分母上),因此在CA6140型卧式车床上 车削英制螺纹时应在传动链中设置抵消特殊因子“25.4”的传动
图3-3 卧式车床的中心高与最大车削直径
CA6140型卧式车床为普通精度级机床,根据卧式车床的精度检验 标准,新机床应达到的工作精度为:
精车外圆的圆度 0.01 mm 0.06mm/300 mm
精车表面的粗糙度 Ra1.6 μm
第一节 机床的传动系统
机床的传动系统由主运动传动链、车削螺纹运 动传动链、纵向和横向进给运动传动链、快速 空程运动传动链组成。
一、主运动传动链
车床的主运动是主轴带动工件的 旋转运动。
u1=×=; u2=×=
u3=×≈; u4=×≈1
其中,u3 ≈u2,所以在中、低转速传动路线中,主轴获得的实际转速 只有2×3(2×2-1)=18级正转转速,即通过两条传动路线主轴可获得 正转转速24级,反转转速12级。
C650车床说明书电气图

绪论车床是机械加工中最广泛的金属切削机床,它可以用于切削各种工件的外圆、内孔、端面、螺纹、螺杆及车削定型表面等。
现代生产机械多采用机械、电气、液压、气动结合的控制技术。
其中电气控制技术起联接中枢作用,应用最为广泛。
电气控制系统是生产机械设备的重要组成部分,是保证J机械设备按生产工艺要求,完成各种运动状态与协调工作,并保证机械设备安全可靠工作以及实现操作自动化。
本设计的主要任务是根据车床的工作情况确定电气设计的技术条件、电力拖动形式的选择、电动机的选择及其他电器元件、电气控制原理图,绘制机电设备的位置图和接线图,最后按要求写出设计报告,绘出设计图样。
第一章车床的运动形式1.1主运动车床的主运动是工件的旋转运动,它是由主轴通过卡盘或顶尖带动工件旋转。
电动机的动力通过主轴箱传给主轴,主轴一般只要单方向的旋转运动,只有在车螺纹时才需要用反转来退刀。
1.2进给运动车床的进给运动是溜板带动刀具作纵向或横向的直线移动,也就是使切削能连续进行下去的运动。
所谓纵向运动是指相对于操作者的左右运动,横向运动是指相对于操作者的前后运动。
车螺纹时要求主轴的旋转速度和进给的移动距离之间保持一定的比例,所以主运动和进给运动要由同一台电动机拖动,主轴箱和车床的溜板箱之间通过齿轮传动来联接,刀架再由溜板箱带动,沿着床身导轨作直线走刀运动。
1.3辅助运动车床的辅助运动包括刀架的快进与快退,尾架的移动与工件的夹紧与松开等。
第二章电力拖动的特点及控制要求2.1电力拖动的特点(1)采用传统的继电器接触器控制系统。
(2)传动方式采用多电动机拖动,即一台设备由多台电动机分别驱动各个工作机构。
这种拖动方式不仅大大简化了生产机械的传动机构,而且控制灵活,为生产机械的自动化提供了有利的条件,现代化机电传动基本上均采用这种拖动形式。
(3)机床主运动和进给运动由主轴电动机M1集中传动,主轴电动机选用三相笼式异步电动机,不进行电气调速,主轴采用齿轮箱进行机械有级调速,由车床主轴箱通过变速箱与主轴电动机的连接来完成(为减小振动,主拖动电动机通过几条传动皮带将动力传递到主轴箱);刀架的给进运动方式有手动和自动两种,在进行螺纹加工时,工作的旋转与刀架的进给速度之间应有严格的比例关系,因此,车床刀架的纵向或横向两个方向进给运动是由主轴箱输出轴依次经挂轮箱、进给箱、光杠传入溜板箱而获得的。
机械制造技术第三章 金属切削机床
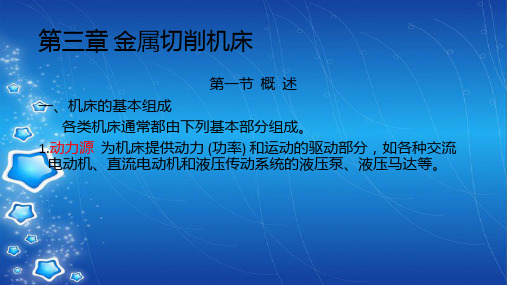
第三章 金属切削机床
上式为深入研究切削过程动力学(机床动刚度和稳定性)提供了基 本概念。
五、机床型号的编制 自学。
第三章 金属切削机床
第二节 金属切削机床部件 一、传动系统
传动系统一般由动力源 (如电动机)、变速装置及执行件 (如主轴、 刀架、工作台),以及开停、换向和制动机构等部分组成。动力源 给执行件提供动力,并使其得到一定的运动速度和方向;变速装 置传递动力以及变换运动速度;
第三章 金属切削机床
3.支承件的材料
支承件常用的材料有铸铁、钢板和型钢、天 然花岗岩、预应力钢筋混凝土凝土等。
近年来,具有优异力学、声学性能的轻质材 料(如多孔材料)的应用研究相当活跃,并已 尝试在高速机床中应用。
轻质材料:增强纤维聚合物基、蜂窝铝、泡沫金 属(含铁、镍、钴等)
第三章 金属切削机床
• 电气伺服进给系统驱动部件 电气伺服进给系统由伺服驱动部件和机械传动部件组成。伺服
驱动部件有步进电机、直流伺服电机、交流伺服电机、直线伺服 电机等。
第三章 金属切削机床
直线伺服电动机是一种能直接将电能转化为直线运动机械能的 电力驱动装置,是适应超高速加工技术发展的需要而出现的一种 新型电动机。
直线伺服电动机传动示意图 —直线滚动导轨 2—床身 3—工作台 4—直流电动机
第三章 金属切削机床
机床刚度相应地分为静刚度及动刚度,后者是抗振性的一部分,习 惯所说刚度一般指静刚度。
如加工系统的动刚度(传递函数的倒数):
Y (s) G(s) Gc (s)Gm (s) 1
式中,Gc (s)为切削过程的传递函数;Gm (s)为机床传递函数。
4.定位精度 定位精度是指机床的定位部件运动到达规定位置的精度。
- 1、下载文档前请自行甄别文档内容的完整性,平台不提供额外的编辑、内容补充、找答案等附加服务。
- 2、"仅部分预览"的文档,不可在线预览部分如存在完整性等问题,可反馈申请退款(可完整预览的文档不适用该条件!)。
- 3、如文档侵犯您的权益,请联系客服反馈,我们会尽快为您处理(人工客服工作时间:9:00-18:30)。
目录1.概述和机床参数确定 (1)1.1机床运动参数的确定 (1)1.2机床动力参数的确定 (1)1.3机床布局 (1)2.主传动系统运动设计 (2)2.1确定变速组传动副数目 (2)2.2确定变速组的扩大顺序 (2)2.3绘制转速图 (3)2.4确定齿轮齿数 (3)2.5确定带轮直径 (3)2.6验算主轴转速误差 (4)2.7绘制传动系统图 (4)3.估算传动件参数确定其结构尺寸 (5)3.1确定传动转速 (5)3.2确定主轴支承轴颈尺寸 (6)3.3估算传动轴直径 (6)3.4估算传动齿轮模数 (6)3.5普通V带的选择和计算 (7)4.结构设计 (8)4.1带轮设计 (8)4.2齿轮块设计 (8)4.3轴承的选择 (9)4.4主轴组件 (9)4.5操纵机构、滑系统设计、封装置设计 (9)4.6主轴箱体设计 (9)4.7主轴换向与制动结构设计 (9)5.传动件验算 (10)5.1齿轮的验算 (10)5.2传动轴的刚度验算 (12)5.3花键键侧压溃应力验算 (16)5.4滚动轴承的验算 (16)5.5主轴组件验算 (17)6. 主轴位置及传动示意图 (20)7.总结……………………………………………………………2 18.参考文献 (22)1.概述1机床课程设计的目的机床课程设计,是在金属切削机床课程之后进行的实践性教学环节。
其目的在于通过机床运动机械变速传动系统的结构设计,使学生在拟定传动和变速的结构的结构方案过程中,得到设计构思,方案分析,结构工艺性,机械制图,零件计算,编写技术文件和查阅技术资料等方面的综合训练,树立正确的设计思想,掌握基本的设计方法,并培养学生具有初步的结构分析,结构设计和计算能力。
轻型车床是根据机械加工业发展需要而设计的一种适应性强,工艺范围广,结构简单,制造成本低的万能型车床。
它被广泛地应用在各种机械加工车间,维修车间。
它能完成多种加工工序;车削内圆柱面,圆锥面,成形回转面,环形槽,端面及内外螺纹,它可以用来钻孔,扩孔,铰孔等加工。
1.1 机床运动参数的确定(1)确定公比φ及Rn已知最低转速n min=160rpm,最高转速n max=2000rpm,变速级数Z=12,则公比:φ= (n max/n min)1/(Z-1) =(2000rpm/160rpm)1/(12-1)≈1.26 转速调整范围: Rn=n max/n min=12.5(2)求出转速系列根据最低转速n min=160rpm,最高转速n max=2000rpm,公比φ=1.26,按《机床课程设计指导书》(陈易新编)表5选出标准转速数列:2000 1600 1250 1000 800 630500 400 315 250 200 1601.2机床动力参数的确定已知电动机功率为N=3kw,根据《金属切削机床课程设计指导书》(陈易新编)附录2选择主电动机为Y100L2-4,其主要技术数据见下表1:表1 Y100L2-4技术参数1.3机床布局确定结构方案1)主轴传动系统采用V 带,齿轮传动。
2)传动型采用集中传动。
3)制动采用式摩擦离合器和带式制动器。
4)变速系统采用多联划移齿轮变速。
5)润滑系统采用飞溅油润滑。
2)布局采用车床常规的布局形式。
机床主要由主轴箱,皮鞍,刀架,尾架,进给箱,溜扳箱,车身等6个部件组成。
主轴的空间位子布局图2 主传动系统运动设计 2.1确定变速组传动副数目实现12级主轴转速变化的传动系统可以写成多种传动副组合: 1)12=34⨯ 2)12=4⨯3 3)12=322⨯⨯ 4)12=223⨯⨯ 5)12=232⨯⨯方案中1)和2)可省一根轴。
但是有一个传动组内有四个变速传动副,会增加轴向尺寸。
这种方案不宜采用。
根据传动副数目分配应“前多后少”的原则,方案3)是可取的。
可以使传动副传动组放在接近电动机处,则可使小尺寸的零件多些,大尺寸的零件少些,这样节省了材料。
2.2确定变速组的扩大顺序12=2×3×2的传动副组合,其传动组的顺序又可有以下六种形式:1) 12=31×23×26 2) 12=31×26×233) 12=32×21×26 4) 12=34×21×225) 12=32×26×21 6) 12=34×22×21选着中间轴的变速范围最小的方案,变速范围小,转速高,转矩较小,传动件的尺寸九可以小些,尽量使扩大组的顺序要与传动顺序一致的原则。
所以选择方案1)较为合理。
结构网图如下:图2变速组扩大顺序2.3绘制转速图图3转速图 2.4确定齿轮齿数利用查表法由《机床课程设计指导书》(陈易新编)表9,求出各传动组齿轮齿数表2 各传动组齿轮齿数2.5确定带轮直径 确定计算功率 kN N j =K-工作情况系数 工作时间一班制 查表得k=1.1 N-主动带轮传动的功率 计算功率为N j =1.2x3=3.6kw根据计算功率和小带轮的转速选用的三角带型号为 A , 查表的小带轮直径推荐植为80mm ,大带轮直径 121121420113.61000n D D D m mn =⨯=⨯=2.6绘制传动系统图图4传动系统图3估算传动件参数确定其结构尺寸3.1确定传动转速表4计算转速图3.2确定主轴支承轴颈尺寸根据《机床课程设计指导书》主轴的驱动功率为3kw 选取前支承轴颈直径为D=70-90, 后支承轴颈直径:6856)85.07.0(12-=-=D D ,选取mm D 602=。
3.3估算传动轴直径表5估算传动轴直径3.4估算传动齿轮模数根据计算公式计算各传动组最小齿轮的模数表6估算齿轮模数3.5普通V 带的选择和计算设计功率 P K P A d =(kw ) 6.332.1p d =⨯=皮带选择的型号为A 型两带轮的中心距mm D D A O ))(26.0(21+-=范围内选择。
中心距过小时,胶带短因而增加胶带的单位时间弯曲次数降低胶带寿命;反之,中心距过大,在带速较高时易引起震动。
①计算胶带速度113.148014205.945/6000060000D n v m sπ⨯⨯===②初定中心距③计算带的基准长度:210()2122()1064.724D D o oL A D D m mA π-=+++=按上式计算所得的值查表选取计算长度L 及作为标记的三角带的内圆长度1250=N L 标准的计算长度为mm Y L L N 1275=+= ④实际中心距A=8=1632.1A=1632.1407.688m m +=为了张紧和装拆胶带的需要,中心距的最小调整范围为A LL h 02.0)01.0(++-0.02L 是为了张紧调节量为22.4 ( h+0.01L) 是为装拆调节量为胶带厚度.⑤定小带轮包角oooAD D 1201801801201≥⨯--=πα求得01175.28oα=合格.⑥带的挠曲次数:100010002 5.94510.616401120m vu L⨯⨯===≤合格⑦带的根数 1c n n Z c j =-o n 单根三角带能传递的功率-1c 小带轮的包角系数3.33.950.930.910.99Z ==⨯⨯取4根三角胶带。
4.结构设计 4.1带轮设计根据V 带计算,选用4根A 型V 带。
由于I 轴安装了摩擦离合器,为了改善它们的工作条件,保证加工精度,采用了卸荷带轮结构。
4.2齿轮块设计116.16~387.2O A m m m m =机床的变速系统采用了滑移齿轮变速机构。
根据各传动组的工作特点,基本组的齿轮采用了销钉联结装配式结构。
第二扩大组,由于传递的转矩较大,则采用了整体式齿轮。
所有滑移出论与传动轴间均采用了花键联结。
从工艺的角度考虑,其他固定齿轮也采用花键联结。
由于主轴直径较大,为了降低加工成本而采用了单键联结。
4.3轴承的选择为了安装方便I轴上传动件的外径均小于箱体左侧支承孔直径并采用0000型向心球轴承为了便于装配和轴承间隙II III IV轴均采用乐2700E型圆锥滚子轴承。
V轴上的齿轮受力小线速度较低采用了衬套式滚动轴承。
滚动轴承均采用E级精度。
4.4主轴组件本铣床为普通精度级的轻型机床,为了简化结构,主轴采用了轴向后端定位的两支承主轴主件。
前轴承采用了318000型双列圆柱滚子轴承,后支承采用了46000型角接触球轴承和8000型单向推力球轴承。
为了保证主轴的回转精度,主轴前后轴承均用压块式防松螺母调整轴承的间隙。
主轴前端采用了圆锥定心结构型式。
前轴承为C级精度,后轴承为D级精度。
4.5操纵机构、滑系统设计、封装置设计为了适应不同的加工状态,主轴的转速经常需要调整。
根据各滑依齿轮变速传动组的特点,分别采用了集中变速操纵机构和单独操纵机构。
主轴箱采用飞溅式润滑。
油面高度为65mm左右,甩油轮浸油深度为10mm左右。
润滑油型号为:HJ30。
I轴轴颈较小,线速度较低,为了保证密封效果,采用了皮碗式接触密封。
而主轴直径大,线速度较高,则采用了非接触式密封。
卸荷皮带轮的润滑采用毛毡式密封,以防止外界杂物进入。
4.6主轴箱体设计箱体外形采取了各面间直角连接方式,使箱体线条简单,明快。
并采用了箱体底面和两个导向块为定位安装面,并用螺钉和压板固定。
安装简单,定位可靠。
4.7制动结构设计本机床属于卧式铣床,适用于机械加工车间和维修车间。
制动器采用了带式制动器,并根据制动器设计原则,将其放置在靠近主轴的较高转速的III 轴上。
为了保证离合器与制动器的联锁运动,采用一个操纵手柄控制。
5. 传动件验算以II 轴为例,验算轴的弯曲刚度,花键的挤压应力,齿轮模数及轴承寿命。
5.1齿轮的验算验算变速箱中齿轮强度应选择相同模数承受载荷最大齿数最小的齿轮进行接触压力和弯曲压力计算,一般对高速传动的齿轮验算齿面接触压力,对低速传动的齿轮验算齿根弯曲压力对硬齿面软齿心渗碳淬火的齿轮要验算齿根弯曲压力。
接触压力的验算公式:][)1(1020813213j js juBnNK K K K u Zmσσ≤±⨯=弯曲应力的验算公式: ][1020823215w js w BYnZm NK K K K σσ≤⨯=表7齿轮验算参数其中寿命系数s K Q n N T s K K K K K =-T K 工作期限系数 oT c T n mK 160=T-齿轮在机床工作期限(s T 的总工作时间h h T 200015000-= ,同一变速组内的齿轮总工作时间可近似地认为pT T s =,P 为该变速组的传动副数。
材料强化系数转速变化系数疲劳曲线指数基准循环次数齿轮的最低转速(-----P n K K m c rpm n 01)稳定工作用量载荷下s K 的极限值s K =1。