KOYO轴承的精度检测及调整
轴承检测仪使用说明

——仅供参考
轴承检查仪用于同步环圆度检测
使用说明
一.结构简图
指示表 2. 指示表紧固螺钉 3. 限位螺钉测力调整螺钉 5. 紧固螺钉 6. 微调螺钉活动测头 8. 固定测头 9. 工作台面活动测头调整螺钉
二.测量时示意图
三.使用说明 1. 调整限位螺钉3,使活动测头7在一定范围内移动.
2. 调整测力调整螺钉(测量内径时旋入,测量外径时旋出),使测量支点产生足够的压力(10±0.3)N 。
1
产品
三个测头都
在内锥上读
3.把齿环安放到工作台面9上,在直径上调整两个固定测头8和活动测头7的位置,
使其三个测头大致在齿环内锥直径上;
4.锁紧固定测头8,将活动测头的调整螺钉10向内移,移动活动测头7与齿环内锥
面接触,锁紧活动测头。
5.松开坚固螺钉5,调整微调螺钉6,使测头与指示表1接触,并使指示表上的指针
7.
得到。
——仅供参考。
造成KOYO轴承早期磨损的多方面原因和简单预防措施

造成KOYO轴承早期磨损的多方面原因和简单预防措施来源:大连轴研科技有限公司 KOYO轴承损伤的例子及其原因和对策,请作为推断轴承损伤原因的资料加以使用损伤状态:KOYO轴承再承受载荷旋转时,内圈、外圈的滚道面或滚动体面由于滚动疲劳而呈现鱼鳞状的剥离现象。
原因:载荷过大。
安装不良(非直线性)力矩载荷异物侵入、进水。
润滑不良、润滑剂不合适轴承游隙不适当。
轴承箱精度不好,KOYO轴承箱的刚性不均轴的挠度大生锈、侵蚀点、擦伤和压引起的发展。
措施:检查载荷的大小及再次研究所使用的KOYO轴承改善安装方法改善密封装置、停机时防锈。
使用适当粘度的润滑剂、改善润滑方法。
检查轴和轴承箱的精度。
检查游隙.损伤状态:呈现出带有轻微磨损的暗面,暗面上由表往里有多条深至5-10m的微小裂缝,并在大范围内发生微小脱落(微小剥离)原因:润滑剂不合适。
异物进入了润滑剂内。
润滑剂不良造成表面粗糙。
配对滚动零件的表面光洁度不好。
措施:选择润滑剂改善密封装置改善配对滚动零件的表面光洁损伤状态:所谓卡伤是由于在滑动面伤产生的部分的微小烧伤汇总而产生的表面损伤。
滑道面、滚动面圆周方向的线状伤痕。
滚子端面的摆线状伤痕靠近滚子端面的轴环面的卡伤。
原因:过大载荷、过大预压。
润滑不良。
异物咬入。
内圈外圈的倾斜、轴的挠度。
轴、KOYO轴承箱的精度不良。
措施:检查载荷的大小。
预压要适当。
改善润滑剂和润滑方法。
检查轴、KOYO轴承箱的精度。
异物侵入,生锈电蚀引起的发展。
润滑不良。
由于滚动体的不规则运动而造成的打滑措施:改善密封装置。
清洗KOYO轴承箱。
充分过滤润滑\要求通常是清洗掉加工液,并作最后的防锈,通常1-3年。
因此,对清洗和防锈的要求更高。
对于使用喷淋设备的客户,储液槽的数量通常达到3个或以上,在清洗槽按规定比例加入低泡的KOYO轴承清洗剂,在漂洗槽加入水基防锈剂进行漂洗。
以上步骤完成后,把产品浸泡在防锈油中浸泡防锈,最终进行防锈包装。
对于使用超声波设备的客户.1.划伤损坏现象:工作表面沿旋转方向发现数根较深的划痕,损伤机理是大颗粒的硬质异粒机械地刻划合金表面,产生原因是:在KOYO轴承润滑间隙中侵入了硬质异粒,主要是由润滑油带入,或因装配时清洁工作不佳而混入。
轴承专用量具检定方法
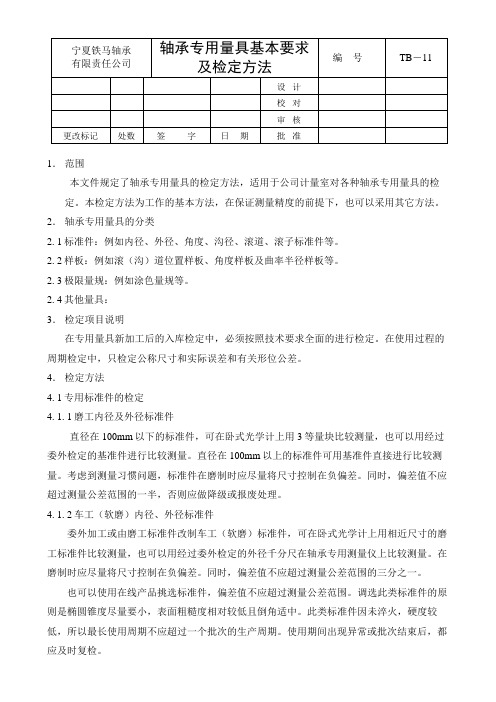
1.范围本文件规定了轴承专用量具的检定方法,适用于公司计量室对各种轴承专用量具的检定。
本检定方法为工作的基本方法,在保证测量精度的前提下,也可以采用其它方法。
2.轴承专用量具的分类2.1标准件:例如内径、外径、角度、沟径、滚道、滚子标准件等。
2.2样板:例如滚(沟)道位置样板、角度样板及曲率半径样板等。
2.3极限量规:例如涂色量规等。
2.4其他量具:3.检定项目说明在专用量具新加工后的入库检定中,必须按照技术要求全面的进行检定。
在使用过程的周期检定中,只检定公称尺寸和实际误差和有关形位公差。
4.检定方法4.1专用标准件的检定4.1.1磨工内径及外径标准件直径在100mm以下的标准件,可在卧式光学计上用3等量块比较测量,也可以用经过委外检定的基准件进行比较测量。
直径在100mm以上的标准件可用基准件直接进行比较测量。
考虑到测量习惯问题,标准件在磨制时应尽量将尺寸控制在负偏差。
同时,偏差值不应超过测量公差范围的一半,否则应做降级或报废处理。
4.1.2车工(软磨)内径、外径标准件委外加工或由磨工标准件改制车工(软磨)标准件,可在卧式光学计上用相近尺寸的磨工标准件比较测量,也可以用经过委外检定的外径千分尺在轴承专用测量仪上比较测量。
在磨制时应尽量将尺寸控制在负偏差。
同时,偏差值不应超过测量公差范围的三分之一。
也可以使用在线产品挑选标准件,偏差值不应超过测量公差范围。
调选此类标准件的原则是椭圆锥度尽量要小,表面粗糙度相对较低且倒角适中。
此类标准件因未淬火,硬度较低,所以最长使用周期不应超过一个批次的生产周期。
使用期间出现异常或批次结束后,都应及时复检。
4.1.3高度块高度块有两个平行的工作面,要求检定平行度和中心长度。
平行度和中心长度用外径千分尺(或立式光学计)进行检定。
检定平行度时,要检五个点(中间一点及四个角各一点),最大差值应不超过平行度的允许误差。
高度块的误差按中心长度决定。
当误差不超过±0.01mm时,在检定证书上不用标示出具体偏差值,只给出合格结论即可。
轴承高速测试方法

轴承高速测试方法全文共四篇示例,供读者参考第一篇示例:轴承是工业生产中常用的一种机械零件,主要用于支撑轴承承受的旋转运动或者直线运动的轴,以降低摩擦。
在工业生产中,轴承的耐用性和高速性能是非常重要的指标。
为了保证轴承的高速性能,需要对轴承进行高速测试。
本文将对轴承高速测试方法进行详细的介绍。
一、轴承高速测试的意义轴承在工业生产中承受的压力和速度都非常大,特别是在高速旋转的情况下,轴承的运行稳定性和耐久性更是受到挑战。
对轴承进行高速测试是非常重要的,可以评估轴承的性能指标,提前发现轴承的潜在问题,避免轴承在高速工作时发生故障,确保生产线的正常运行。
1. 轴承高速旋转校正在进行轴承高速测试之前,首先要对轴承进行高速旋转校正。
通过专用设备对轴承进行高速旋转,检测轴承的旋转速度和噪音等参数,校正轴承的旋转误差,确保轴承的高速性能符合要求。
2. 轴承高速磨损测试在轴承高速测试中,需要对轴承进行高速磨损测试。
通过设定不同的高速旋转条件,观察轴承的磨损情况,检测轴承的磨损程度和耐久性能,评估轴承的高速性能。
轴承高速测试主要应用于工业领域,特别是在航空航天、汽车制造、铁路运输等领域。
在这些领域中,对轴承的高速性能要求非常严格,需要经过严格的高速测试来评估和验证轴承的性能指标,确保轴承在高速工作时的稳定性和耐久性。
轴承高速测试方法是评估和验证轴承高速性能的重要手段,通过对轴承的高速旋转、磨损、温升、噪音和振动等参数进行测试,可以全面评估轴承的高速性能,确保轴承在高速工作时的稳定性和可靠性。
轴承高速测试的应用范围广泛,对工业生产的安全和可靠运行有着重要的意义。
希望本文对您了解轴承高速测试方法有所帮助。
第二篇示例:轴承是机械设备中必不可少的零部件,其主要作用是支撑旋转机械的轴承部件,减少摩擦力,以确保机械设备的稳定运行。
而对于一些高速旋转机械设备来说,轴承的高速性能就显得尤为重要。
轴承的高速测试方法就成为了至关重要的环节。
轴承故障检测、诊断、分析技巧

为了尽可能长时间地以良好状态维持轴承本来的性能,必须保养、检测、检修、以求防事故于未然,确保运转的可靠性,提高生产性、经济性。
对长期运行中的设备来讲,平时的检测跟踪尤为重要,检测项目包括轴承的旋转音、振动、温度、润滑剂的状态等,根据检测结果,设备维护人员可以准确地判断设备的问题点,提早作出预防和解决方案。
一、异常旋转音分析诊断异常旋转音检测分析是采用听诊法对轴承工作状态进行监测的分析方法,常用工具是木柄长螺钉旋具,也可以使用外径为20mm左右的硬塑料管。
相对而言,使用电子听诊器进行监测,更有利于提高监测的可靠性。
轴承处于正常工作状态时,运转平稳、轻快,无停滞现象,发生的声响和谐而无杂音,可听到均匀而连续的“哗哗”声,或者较低的“轰轰”声。
异常声响所反映的轴承故障如下:1、轴承发出均匀而连续的“咝咝”声,这种声音由滚动体在内外圈中旋转而产生,包含有与转速无关的不规则的金属振动声响。
一般表现为轴承内加脂量不足,应进行补充。
若设备停机时间过长,特别是在冬季的低温情况下,轴承运转中有时会发出“咝咝沙沙”的声音,这与轴承径向间隙变小、润滑脂工作针入度变小有关。
应适当调整轴承间隙,更换针入度大一点的新润滑脂。
2、轴承在连续的“哗哗”声中发出均匀的周期性“嗬罗”声,这种声音是由于滚动体和内外圈滚道出现伤痕、沟槽、锈蚀斑而引起的。
声响的周期与轴承的转速成正比。
应对轴承进行更换。
3、轴承发出不规律、不均匀的“嚓嚓”声,这种声音是由于轴承内落入铁屑、砂粒等杂质而引起的。
声响强度较小,与转数没有联系。
应对轴承进行清洗,重新加脂或换油。
4、轴承发出连续而不规则的“沙沙”声,这种声音一般与轴承的内圈与轴配合过松或者外圈与轴承孔配合过松有关系。
声响强度较大时,应对轴承的配合关系进行检查,发现问题及时修理。
二、振动信号分析诊断轴承振动对轴承的损伤很敏感,例如剥落、压痕、锈蚀、裂纹、磨损等都会在轴承及振动测量中反映出来。
所以,通过采用特殊的轴承振动测量器(频率分析器等)可测量出振动的大小,通过频率分布可推断出异常的具体情况。
轴承质量鉴定标准与方法

轴承质量鉴定标准与方法主要包括以下几个方面:
1. 外观检查:检查轴承表面是否有明显的划痕、氧化、锈蚀等缺陷,以及是否有变形、变色等问题。
2. 尺寸测量:测量轴承的外径、内径、宽度等尺寸,与标准尺寸进行比对,判断是否符合要求。
3. 转动灵活度检查:手动转动轴承,观察是否转动灵活,是否有卡滞、异响等现象。
4. 噪音检测:使用专业的噪音检测仪器,对轴承进行噪音测试,判断是否存在异常噪音。
5. 润滑状态检查:检查轴承的润滑状态,包括润滑油的清洁度、黏度等指标,以及是否存在润滑不良的情况。
6. 轴承负荷能力测试:通过加载一定的负荷,测试轴承的承载能力,判断是否符合设计要求。
7. 寿命测试:通过模拟实际使用条件,对轴承进行寿命测试,判断其使用寿命是否符合要求。
轴承质量鉴定标准与方法可以根据不同的轴承类型和应用领域进行具体的调整和细化,以确保轴承的质量符合要求。
轴承测试方法
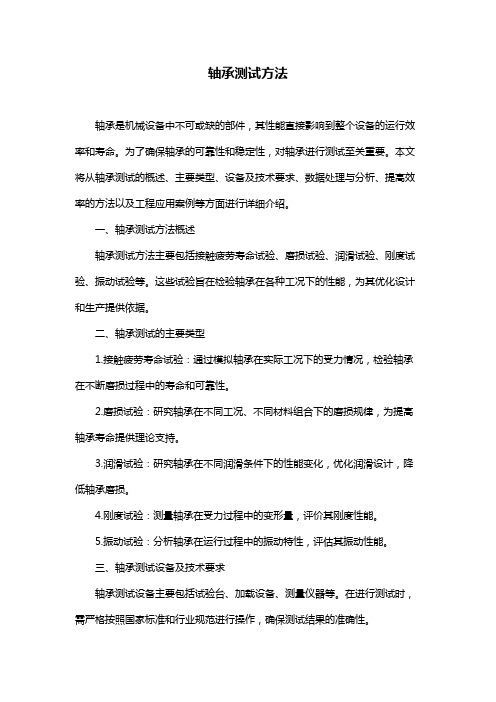
轴承测试方法轴承是机械设备中不可或缺的部件,其性能直接影响到整个设备的运行效率和寿命。
为了确保轴承的可靠性和稳定性,对轴承进行测试至关重要。
本文将从轴承测试的概述、主要类型、设备及技术要求、数据处理与分析、提高效率的方法以及工程应用案例等方面进行详细介绍。
一、轴承测试方法概述轴承测试方法主要包括接触疲劳寿命试验、磨损试验、润滑试验、刚度试验、振动试验等。
这些试验旨在检验轴承在各种工况下的性能,为其优化设计和生产提供依据。
二、轴承测试的主要类型1.接触疲劳寿命试验:通过模拟轴承在实际工况下的受力情况,检验轴承在不断磨损过程中的寿命和可靠性。
2.磨损试验:研究轴承在不同工况、不同材料组合下的磨损规律,为提高轴承寿命提供理论支持。
3.润滑试验:研究轴承在不同润滑条件下的性能变化,优化润滑设计,降低轴承磨损。
4.刚度试验:测量轴承在受力过程中的变形量,评价其刚度性能。
5.振动试验:分析轴承在运行过程中的振动特性,评估其振动性能。
三、轴承测试设备及技术要求轴承测试设备主要包括试验台、加载设备、测量仪器等。
在进行测试时,需严格按照国家标准和行业规范进行操作,确保测试结果的准确性。
四、轴承测试数据的处理与分析轴承测试数据处理与分析是评价轴承性能的关键环节。
通过对测试数据的处理,可以得到轴承在各种工况下的性能指标,如疲劳寿命、磨损量、刚度等。
通过对数据进行分析,可以找出轴承性能与工况、材料、设计等方面的关系,为轴承的优化设计提供依据。
五、提高轴承测试效率的方法1.采用自动化测试技术,减少人工干预,提高测试精度。
2.优化试验方案,缩短试验周期。
3.利用大数据分析技术,提高数据处理与分析效率。
4.加强试验设备的维护和保养,降低故障率。
六、轴承测试在工程应用中的案例分析轴承测试在工程应用中具有广泛的应用,如轴承故障诊断、轴承寿命预测、轴承性能优化等。
通过对实际工程案例的分析,可以发现轴承测试在提高设备运行可靠性、降低维修成本等方面具有重要意义。
轴承外径检测操作作业指导书

页码第1页共2页1.0目的:
确保操作人员能正确的使用测量仪,并保证检测结果的准确性及真实性。
2.0范围:
适用于本公司所有轴承产品的检测。
3.0定义:
用来检测轴承产品的变化量。
4.0程序:
4.1 使用前检测轴仪的外观、测点位置、清洁和磨损程度及测点的灵活性和检测轴仪上所使用的量表是否能正常工作。
4.1.1用相应的标准件校准轴仪:将标准件轻轻放在检测台上,使标准件紧靠辅助撑点,将检测的量表放在相应的检测位置上,按顺时针方向轻轻转动标准件,使量表能够检测到标准件所标定的位置,然后调整轴仪上的微调螺母将量表调到与标准件所指定的对应的数值上。
4.1.2测量:将需要检测的产品按照4.1.1的方法放上,然后顺时针方向旋转,读出量表的最大值和最小值。
4.1.3结果:将所测定数据与工艺卡上的数据进行比对,方行合格的产品,根据不良品处理流程处理不良品。
页码第1页共2页5.0 操作工:负责按照以上的操作流程使用轴仪,检测所需要的项目并负责该量具的日常维护。
5.1.1 计量员:负责该量具的计量管理。
6.0 参照轴仪的使用说明书。
审批/日期编制/日期。
- 1、下载文档前请自行甄别文档内容的完整性,平台不提供额外的编辑、内容补充、找答案等附加服务。
- 2、"仅部分预览"的文档,不可在线预览部分如存在完整性等问题,可反馈申请退款(可完整预览的文档不适用该条件!)。
- 3、如文档侵犯您的权益,请联系客服反馈,我们会尽快为您处理(人工客服工作时间:9:00-18:30)。
KOYO轴承的精度检测及调整
本文源于:
液压机由于其构成件尺寸大、重量重,受铸造、锻造、切削加工、装配等各种工艺条件的限制,所以压机本身的工作精度不可能完全靠机械加工本身来保证,而必须经过组装过程中的调整来达到其各项精度指标。
调整是根据KOYO轴承精度检测的具体要求进行操作的,而精度的保持和稳固则要靠与之相关的预紧和防松手段及措施来保证。
各行各业所使用的液压机,因其用途不同对其工作精度要求也各异,在生产制造中也沿用不同的行业标准。
在同一行业由于生产产品不同,要求的精度也不可能一致。
所以同一行业标准中按不同工作状况又分为若干等级而相对应各精度指标。
工厂生产中由技术部门按生产压机的精度标准编制检验大纲和试车大纲,下发有关部门作为指导性文件,其中规定有关项目和参数的检测方法及相应数据,作为安装调整及检查验收的标准。
一般都包括需在装配KOYO轴承过程中经调整才能达到的精度项目。
如在液压机中对工作台的水平度、柱距偏差、工作台及活动工作台的平面度、立柱与其连接的上下横梁的垂直度、各工作台间的平行度、主油缸在工作行程内与工作台的垂直度、立柱与上下横梁连接的内外螺母贴合面的接触率等。
KOYO轴承精度调整和检测的过程和结果,要经专职人员首肯签章方可通过。
检测调整过程中所需用的工具和工装在生产进行中由对口专业工艺人员设计后按计划编入生产流程。
检验大纲及检测调整操作省略。