冶金含锌粉尘中回收氧化锌的工艺综述
利用含锌工业废渣回收氧化锌

利用含锌工业废渣、 灰制氧化锌的工艺流程 如图 1 所示。
图 1 制备氧化锌的工艺流程
4.1 酸溶含锌废料 取 160kg 废料 (含 Zn24%) 置于 耐 酸 陶 瓷 反
应 缸 中 , 加 清 水 400kg, 在 缓 慢 搅 拌 下 加 入 100kg98%H2SO4, 加 入 速 度 以 不 沸 腾 溢 出 为 限 , 然 后 间 歇 搅 拌 , 使 之 反 应 24h, 保 持 Zn 过 量 。 上清液送下道工序, 下层未反应物与新投入物料 一起继续酸溶; 待未溶物积累一定量后送水泥厂 或砖厂。 4.2 除铁
将除铁后的锌液投入另一大缸或耐酸、 碱水 泥池中, 用硫酸调节 pH.至 4, 投 入 经 活 化 的 锌 屑 2kg (生产中用的是电池厂锌皮下脚料)。 搅拌 1h, 上清液即为精制合格的硫酸锌溶液, 下层不 溶物主要含锌, 可返回酸溶工序。 4.4 制氧化锌
向制得的合格硫酸锌溶液中, 在不断搅拌下 缓 缓 加 入 稀 NH3·H2O 或 稀 NH,HCO3 溶 液 至 pH 为 8.5-10, 停止加料, 并继续搅拌 30min, 自然 澄 清 , 下 层 为 白 色 Zn (OH)2 或 ZnCO3·2Zn (OH) 2·H2 O 沉淀, 用清水漂洗 2 次, 烘 干 、 煅 烧 (若 用 NH3·H2 O 作 沉 淀 剂 , 则 煅 烧 温 度 为 140℃ ; 若用 NH4HCO3 作沉淀剂, 则煅烧温度在 400℃以 上)、 粉碎即得氧化锌产品。 上层清液主要含 (NH4)2 SO4。
作者简介: 王 敏 (1946~), 女, 高级工程师, 主要从事化学分析工作。
第1期
王敏: 利用含锌工业废渣回收氧化锌
· 42 ·
到合格的 ZnSO4 溶液。 3.1.2 废渣的酸溶
锌冶炼渣综合回收有价金属工艺综述与展望

锌冶炼渣综合回收有价金属工艺综述与展望摘要:我国的锌冶炼企业每年均会产生数百万吨渣料,例如炼锌渣和铅烟灰,铅泥等。
该废料中铅、金、银、铟等金属含量较高,具有巨大的回收价值。
近年来有方法研究从锌冶炼渣料中回收铅、金、银、铟等金属。
本文通过对从锌冶炼渣料中回收贵金属工艺的综述,对未来的综合回收工艺进行展望。
关键词:锌冶炼;渣料;综合回收;冶炼工艺引言对国内主流的湿法锌冶炼锌浸出渣处理工艺技术进行简要阐述,并结合某锌冶炼公司具体应用实例对改造效果进行分析。
企业通过积极进行技术升级改造,冶炼渣料中的贵金属综合回收能力大幅提高,经济效益显著增加,市场竞争力得到进一步加强。
同时,企业的技术升级改造也在向更大的深度和广度上发展。
通过生产工艺技术改造实现综合回收,既是一种有效的创效方式,又是企业可持续发展的有效途径,已经得到企业的普遍认同。
文中将对锌冶炼渣料处理工艺技术在实际工程中的应用效果进行重点分析。
1锌冶炼渣料回收贵金属1.1锌冶炼渣料来源锌冶炼工艺分为火法工艺和湿法工艺,火法炼锌过程中,主要的渣料为冶炼炉的炉渣和收尘器中的烟尘,铅、金、银、铟等贵金属大部分分布在炉渣中。
湿法炼锌工艺中,主要的渣料为常规工艺中的浸出渣、硫酸锌溶液的净化渣、电解过程的阳极泥以及回转窑氧化锌浸出渣(铅泥)等;高温沸腾浸出工艺中产生的黄钾铁矾渣、针铁矿渣、赤铁矿渣等。
1.2火法渣料回收有价金属火法炼锌的炉渣,一般通过在浮选的方式回收有价金属,将炉渣通过筛分、球磨后,用水配成矿浆加浮选药剂采用精密浮选机进行浮选,回收渣料中的金、银、铜、锌等有价金属。
烟尘一般通过火法窑炉在处理或通过湿法工艺将贵金属及常规有价金属进行分离富集,再进一步提炼成成品。
1.3湿法渣料回收有价金属在常规湿法炼锌两段浸出过程中,产出的浸出渣一般通过回转窑焙烧后变为氧化锌焙砂,再通过三段浸出分离贵金属及锌。
一段中性浸出将大部分锌浸出至溶液中返回主系统;浸出渣采用低酸浸出,将金属铟浸出至溶液中通过中和置换进行富集,富集后的高铟渣再通过浸出、萃取、反萃、电解等工序产出成品铟锭;酸性浸出渣通过高温高酸浸出,将金、银等贵金属富集至高铅渣中,高铅渣再通过铅冶炼系统或火法窑炉进行处理,进一步分离回收金、银等贵金属。
冶锌废渣次氧化锌的综合利用
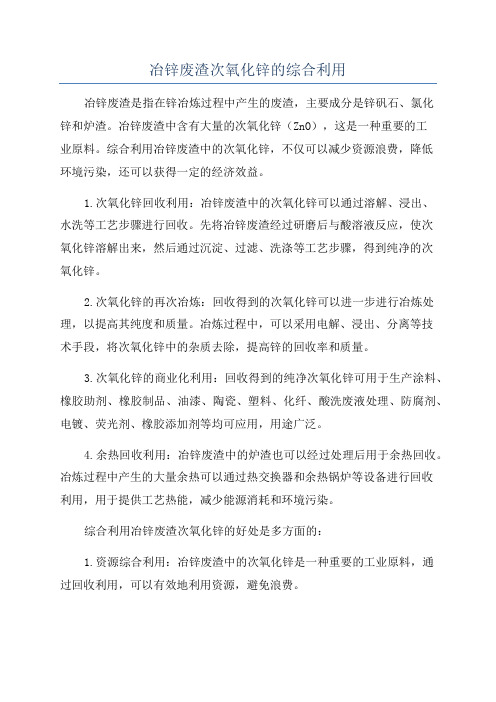
冶锌废渣次氧化锌的综合利用冶锌废渣是指在锌冶炼过程中产生的废渣,主要成分是锌矾石、氯化锌和炉渣。
冶锌废渣中含有大量的次氧化锌(ZnO),这是一种重要的工业原料。
综合利用冶锌废渣中的次氧化锌,不仅可以减少资源浪费,降低环境污染,还可以获得一定的经济效益。
1.次氧化锌回收利用:冶锌废渣中的次氧化锌可以通过溶解、浸出、水洗等工艺步骤进行回收。
先将冶锌废渣经过研磨后与酸溶液反应,使次氧化锌溶解出来,然后通过沉淀、过滤、洗涤等工艺步骤,得到纯净的次氧化锌。
2.次氧化锌的再次冶炼:回收得到的次氧化锌可以进一步进行冶炼处理,以提高其纯度和质量。
冶炼过程中,可以采用电解、浸出、分离等技术手段,将次氧化锌中的杂质去除,提高锌的回收率和质量。
3.次氧化锌的商业化利用:回收得到的纯净次氧化锌可用于生产涂料、橡胶助剂、橡胶制品、油漆、陶瓷、塑料、化纤、酸洗废液处理、防腐剂、电镀、荧光剂、橡胶添加剂等均可应用,用途广泛。
4.余热回收利用:冶锌废渣中的炉渣也可以经过处理后用于余热回收。
冶炼过程中产生的大量余热可以通过热交换器和余热锅炉等设备进行回收利用,用于提供工艺热能,减少能源消耗和环境污染。
综合利用冶锌废渣次氧化锌的好处是多方面的:1.资源综合利用:冶锌废渣中的次氧化锌是一种重要的工业原料,通过回收利用,可以有效地利用资源,避免浪费。
2.减少环境污染:冶锌废渣中的次氧化锌含有有害物质,如果不加以利用或处理,可能会对环境造成污染。
通过综合利用,可以有效地降低环境污染的风险。
3.经济效益:冶锌废渣中的次氧化锌是有一定经济价值的,通过回收利用,可以获得一定的经济效益。
4.能源回收利用:冶锌废渣中产生的余热可以经过处理后用于提供工艺热能,减少能源消耗和环境污染。
综合利用冶锌废渣次氧化锌的主要技术和设备包括研磨设备、溶解设备、沉淀设备、过滤设备、洗涤设备、冶炼设备、热交换器、余热锅炉等。
在实施过程中,需要严格控制工艺参数,优化工艺流程,确保次氧化锌的回收率和质量。
冶锌废渣次氧化锌的综合利用
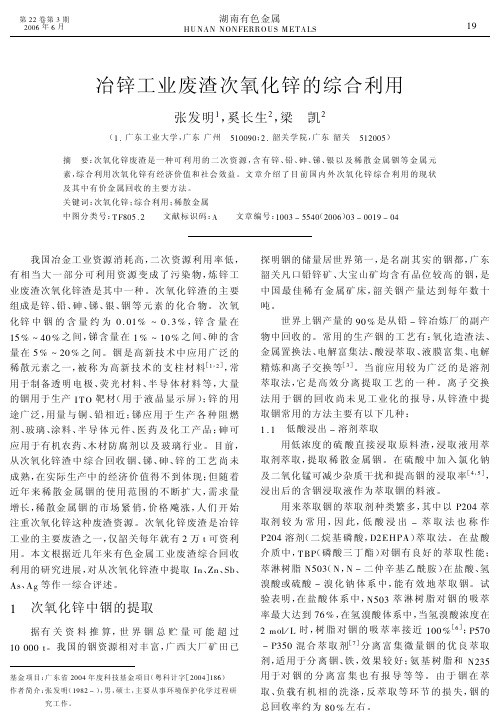
此外,还有 综 合 法 提 铟,采 用 二 段 浸 出(先 中 性 浸出 得 含 铟 渣,再 酸 性 浸 出)和 置 换 等 工 艺,达 到 分 离锌、铅和富 集 铟 的 目 的;氧 化 造 渣 法 提 铟,利 用 铟 对氧的亲和势大大高于铅对氧的亲和势的原理实现 铟和铅等 的 分 离,经 氧 化 造 渣 得 含 铟 浮 渣。 先 中 性 浸 出 除 去 大 部 分 锌,再 用 浓 硫 酸 浸 出,含 铟 的 浸 出 液,直接用锌 置 换;硫 酸 化 焙 烧 水 浸 工 艺 提 铟,原 料 配以 浓 硫 酸 进 行 焙 烧,铟 和 重 金 属 氧 化 物 几 乎 全 部
美国早在七十年代初期就开始用含锌废渣通过 盐 酸 法 来 生 产 氯 化 锌,我 国 从 八 十 年 代 中 后 期 开 始 直接对冶锌废渣、电镀、电池 等行 业 的 锌 浮 渣 来 研 究 生产氯化锌。用含锌废渣生产氯化锌的工艺流程简 单,产品质量较好,是对含锌废渣 综 合 开 发 的 方 法 之 一。
次氧化 锌废 渣另一 重要 用 途 是 制 取 七 水 硫 酸 锌,七水硫酸 锌 作 为 一 种 重 要 工 业 原 料,在 农 业、化 学制造、电 镀、人 造 纤 维、水 处 理、制 造 立 德 粉 和 锌 盐、木材及皮 革 防 腐、骨 胶 澄 清、果 树 防 虫 及 锌 肥 等 方面有广泛用途。我国年产量约 6 万 t,30 % 以上出 口。用次氧化 锌 废 渣 生 产 七 水 硫 酸 锌 工 艺 成 熟,流 程简单,锌的总回收率可达 90 % 以上,每吨产品可获 纯利 300 ~ 400 元。 2 . 3 次氧化锌废渣生产氯化锌[18]
钢铁厂含锌粉尘的处理方法

者低价出售,这样不仅污染环境,而且造成宝贵
资源的浪费。现在越来越多的钢厂已经认识到这
个问题,开始对含锌粉尘进行综合处理,提取金 属锌,既减少污染又节约资源。目前的主要处理
方法有以下:
过于耀眼,将星星直接踢入了黑暗,尽法。高锌和中
锌粉尘可采用湿法直接处理,而低锌粉尘应先富
法、宝钢 BSR 法。
过于耀眼,将星星直接踢入了黑暗,尽管如此,夕年依旧的恋着星
火法处理的优点:1)生产效率较高.设备 占地面积较小;2)多数工艺中的 Zn、Pb 等重金
属的去除彻底,可充分满足环保要求;伴生的铁
碳资源可以得到充分回收;3)在钢厂内部处理
粉尘,其还原剂、能源、动力的消耗较少。
3、湿法-火法联合工艺
目前比较成熟的联合工艺是先火法后湿法
过于耀眼,将星星直接踢入了黑暗,尽管如此,夕年依旧的恋着星
的 MRT(HST)工艺。该工艺先采用转底炉对含锌粉 尘等物料进行直接还原,使铁与锌、铅、镉等分
离,得到的直接还原铁产品可以返回电弧炉循环
利用。
含铅、镉、铜、银等金属的粗氧化锌产品则 送入含热氯化铵的浸出槽中进行浸出,然后对浸
出液进行固、液分离,过滤,得到的滤液进一步
处理,分离回收铅和镉,最后将溶液浓缩、沉淀、
过于耀眼,将星星直接踢入了黑暗,尽管如此,夕年依旧的恋着星
干燥,就可以得到高纯氧化锌。这种联合工艺得 到的产品回收率高,但流程较长,成本比较高。
1cs0f9c9b
集后才能用于湿法处理。
湿法包括酸洗和碱洗。主要流程为:浸出、
净化、沉积和电解。湿法工艺中的溶解是在扩散
过于耀眼,将星星直接踢入了黑暗,尽管如此,夕年依旧的恋着星
控制下进行的,所以要进行高强度搅拌。
一种以工业含锌废渣制取高纯zno的工艺流程

一种以工业含锌废渣制取高纯ZnO的工艺流程1. 导言含锌废渣是炼锌和电解锌过程中产生的一种含有一定量氧化锌的固体废物,其中含有的氧化锌可以被用来制取高纯度的ZnO。
本文将介绍一种利用工业含锌废渣制取高纯ZnO的工艺流程。
2. 工业含锌废渣的性质工业含锌废渣通常含有一定量的氧化锌和其他杂质,其物理性质和化学成分会因不同的生产工艺和原料而有所不同。
在进行制ZnO过程中,需要对废渣的性质进行综合分析,并制定相应的处理工艺。
3. 工艺流程针对工业含锌废渣制取高纯ZnO的工艺流程,一般包括以下几个步骤:步骤一:破碎和粉碎初步处理含锌废渣需要对其进行破碎和粉碎,以提高后续工艺中的反应速率和反应效果。
步骤二:酸洗酸洗是为了去除废渣中的杂质和固相物,使得后续的反应更为纯净。
一般可以选择硫酸、盐酸等强酸进行酸洗,去除其中的铅、铜、铝等杂质。
步骤三:水浸提取在酸洗后,需要对废渣进行水浸提取,将其中的氧化锌溶解出来,形成锌盐溶液。
步骤四:还原和沉淀将水浸提取得到的锌盐溶液进行还原处理,得到石墨烯的粉末,然后通过适当的沉淀工艺,将其中的氧化锌沉淀出来。
这一步骤需要控制沉淀的条件,以保证所得到的ZnO的纯度和颗粒度。
步骤五:焙烧和煅烧最后一步是对得到的氧化锌进行干燥、焙烧和煅烧,形成高纯度ZnO的终产物。
这一步需要控制适当的温度和时间,以确保ZnO的纯度和颗粒度。
4. 工艺优化和环保考虑在进行工业含锌废渣制ZnO的工艺设计和实施过程中,需要充分考虑到工艺的优化和环保要求,以减少能耗和污染排放。
可以通过改进反应条件、节约资源和利用副产物等方式来不断优化工艺流程。
5. 结语利用工业含锌废渣制取高纯ZnO的工艺流程,可以有效地实现含锌废渣的资源化利用,同时得到高附加值的ZnO产品。
在实际生产过程中,需要根据具体的原料情况和生产要求,对工艺流程进行细化和调整,以确保ZnO产品的质量和生产效益。
也需要注意环保和能耗方面的问题,注重可持续发展和循环经济的理念。
含锌除尘灰脱锌工艺的研究进展及展望

含锌除尘灰脱锌工艺的研究进展及展望目录1. 内容描述 (2)1.1 研究背景 (3)1.2 研究意义 (4)1.3 研究内容与目标 (5)2. 含锌除尘灰的特性分析 (5)2.1 含锌除尘灰的来源 (6)2.2 含锌尘及灰的组成与成分 (6)2.3 含锌除尘灰的物理性质与化学性质 (7)3. 现有脱锌工艺的研究进展 (8)3.1 物理脱锌工艺 (11)3.1.1 筛分与洗涤 (12)3.1.2 重力脱锌 (13)3.1.3 浮选脱锌 (14)3.2 化学脱锌工艺 (14)3.2.1 酸浸法 (16)3.2.2 氧化还原脱硫 (17)3.2.3 羧酸盐萃取 (18)3.3 生物脱锌工艺 (19)3.3.1 微生物浸出 (21)3.3.2 酶催化解离 (22)3.4 电化学脱锌工艺 (23)3.4.1 电解法 (24)3.4.2 电化学氧化还原 (25)3.5 组合脱锌工艺 (26)3.5.1 化学与物理联合脱锌 (27)3.5.2 生物技术与化学技术的结合 (28)4. 脱锌工艺存在的问题与挑战 (30)4.1 脱锌效率不高等问题 (31)4.2 环保与能源消耗问题 (32)4.3 成本和经济效益问题 (32)5. 新技术与发展展望 (34)5.1 材料分离技术的最新进展 (35)5.2 环境友好型脱锌新工艺的研究 (36)5.3 智能自动化在脱锌工艺中的应用 (38)5.4 未来脱锌工艺研究的趋势与方向 (39)1. 内容描述本研究旨在全面探讨含锌除尘灰脱锌工艺的研究进展,从当前的技术水平出发,深入分析各种脱锌方法的原理、优缺点及适用条件,并对近年来在该领域取得的重要突破进行综述。
结合具体实例,评估不同脱锌工艺在实际应用中的效果和经济效益。
文章还将展望含锌除尘灰脱锌工艺的未来发展趋势,预测可能出现的新技术、新方法,以及这些新技术将如何进一步推动含锌除尘灰资源化利用的进程。
本文将首先介绍含锌除尘灰的来源及其在工业生产中的重要性,然后系统地回顾和分析现有的脱锌工艺,包括化学法、物理法和生物法等,重点关注每种方法的脱锌机理、操作条件、主要设备以及产生的环境影响等方面。
冶锌废渣次氧化锌的综合利用

冶锌废渣次氧化锌的综合利用冶锌废渣是指在锌冶炼过程中产生的含有锌的固体废弃物。
冶锌废渣的主要成分是氧化锌(ZnO),其中还含有少量的金属锌和其他杂质。
为了充分利用冶锌废渣,降低资源浪费和环境污染,可以通过次氧化锌的综合利用来实现。
次氧化锌是指将冶锌废渣中的氧化锌经过一定的化学或物理处理,得到纯度较高的次氧化锌(ZnO)。
次氧化锌具有很多应用领域,包括橡胶、塑料、橡胶和塑料等材料的添加剂、陶瓷工业的颜料和釉料等。
因此,综合利用冶锌废渣可以为企业带来经济效益和环境效益。
首先,通过化学处理将冶锌废渣中的氧化锌提取出来。
可以采用酸浸法、碱浸法、氧浸法等方法。
其中,酸浸法是最常用的方法,即将冶锌废渣和浓硫酸进行反应,生成硫酸锌,然后通过进一步处理得到次氧化锌。
其次,对得到的次氧化锌进行物理处理,使其纯度更高。
可以采用重力选矿、磁选和浮选等方法。
重力选矿是将次氧化锌和其他杂质按照其比重的大小进行分离;磁选是利用次氧化锌的磁性和其他杂质的非磁性进行分离;浮选是利用次氧化锌和其他杂质的浮力差进行分离。
通过这些物理方法,可以获得高纯度的次氧化锌。
然后,对得到的次氧化锌进行加工,制成适合不同行业的产品。
例如,可以将次氧化锌用作橡胶和塑料的添加剂,改善材料的性能;可以将次氧化锌用作陶瓷工业的颜料和釉料,增加产品的色彩和光泽;还可以将次氧化锌用于制备电子元器件、化妆品等产品。
通过制造不同的产品,可以更好地满足市场需求,提高企业的竞争力。
此外,还可以将冶锌废渣中的金属锌进行回收利用。
可以采用冶金回收的方法,如熔炼、浸出等。
通过回收金属锌,可以减少资源浪费和环境污染。
综上所述,冶锌废渣次氧化锌的综合利用可以实现资源的有效利用和环境的保护。
通过化学和物理处理,可以从冶锌废渣中提取氧化锌,制备高纯度的次氧化锌。
然后,将次氧化锌制成适合不同行业的产品。
同时,可以回收冶锌废渣中的金属锌,减少资源的浪费。
这样,不仅可以为企业带来经济效益,还可以为社会和环境带来积极的影响。
- 1、下载文档前请自行甄别文档内容的完整性,平台不提供额外的编辑、内容补充、找答案等附加服务。
- 2、"仅部分预览"的文档,不可在线预览部分如存在完整性等问题,可反馈申请退款(可完整预览的文档不适用该条件!)。
- 3、如文档侵犯您的权益,请联系客服反馈,我们会尽快为您处理(人工客服工作时间:9:00-18:30)。
冶金含锌粉尘中回收氧化锌的工艺综述
摘要:随着现代化进程的不断推进,钢铁积累不断增加,废钢重铸将逐渐增多,特别是表面镀锌等金属回炉重铸,髙炉粉尘及灰渣中会含有锌元素。
因此,在高
炉粉尘和灰渣中富集、提取氧化锌逐渐成为关键固废资源回收的热点问题。
我国
锌资源储备丰富,分布广泛,品位主要集中在1%-7%之间,品位大于等于6%以
上的已探明锌矿资源量仅全国总量33.3%。
高炉粉尘中回收锌元素对低品位锌矿
的利用也有着重要的借鉴作用。
文章主要针对冶金含锌粉尘中回收氧化锌的工艺
方面进行分析,希望能给相关人士提供重要的参考价值。
关键词:电炉粉尘;回收利用;氧化锌
引言:
传统的含锌电炉粉尘处理工艺中,填埋法虽然处理简单,但并不能利用其中
的金属资源,只是一个暂时无害化的处理。
电炉粉尘循环利用进入生产流程,可
回收其中的铁资源,但由于铅锌的富集,对后续高炉炼铁以及炼钢生产工艺造成
影响,且只能部分循环利用,并不能大规模的处理。
火法处理工艺具有生产效率高,操作简单,脱锌率高,原料适应性强的优点,但其前期设备投资大,能耗大,环境污染严重等问题限制了火法工艺的发展。
湿法处理工艺锌的浸出率低,只能
处理高锌电炉粉尘,锌铁同时浸出导致后续沉铁工序复杂,设备腐蚀严重。
针对
这一现状,文章围绕冶金含锌粉尘中回收氧化锌的工艺进行分析,具有重要的现
实意义。
1.含锌电炉粉尘传统处理方法
1.1填埋法
填埋法有直接填埋法、固化填埋法和玻璃化填埋法。
直接填埋法是指将未经
任何处理的电炉粉尘直接进行填埋处理。
该法仅适用于铅锌含量很低的电炉粉尘,对于铅锌含量高的电炉粉尘,直接填埋法不仅无法回收利用其中的金属资源,造
成资源的浪费,而且成本也高,还会造成地下水污染。
固化填埋法是指先将电炉
粉尘与黏土或者水泥均匀混合后高温固化再进行填埋处理。
此法操作简单,不会
对地下水造成污染,但经过处理的电炉粉尘失去了再次利用的可能,无法再次回
收利用其中的金属资源。
玻璃化填埋法是固化填埋的改进,热稳定性更好,但也
只是一种无害化的处理方式,并不能回收电炉粉尘中的有价金属。
填埋法已经不
适用于当前的资源循环利用模式。
1.2钢铁厂循环利用法
直接将电炉粉尘接配入烧结球团或者炼钢等工序中,进行循环利用。
但由于
锌富集对炼铁炼钢工序带来危害,只能部分选择锌含量较低的电炉粉尘进行循环
利用。
第一,烧结球团处理。
将电炉粉尘作为原料直接配入烧结工艺,回收电炉
粉尘中的铁,但配入的电炉粉尘由于铁品位低,锌含量高,会降低烧结矿的铁品位,同时增加烧结矿的锌含量,对后续的高炉操作带来危害。
电炉粉尘粒度很细,对烧结透气性也有一定影响,采用小球烧结法可以解决粉尘过细带来的烧结性能
变差的问题,目前已在工业生产中得到应用。
球团法处理电炉粉尘有两种处理方式:冷固结球团法和氧化球团法。
冷固结球团法不需要加热,直接将电炉粉尘与
粘结剂混合造球,符合要求的球团配合其他原料直接进高炉。
氧化球团法需要经
过高温加热工序。
造好的生球经过链篦机回转窑焙烧后冷却进高炉。
日本某钢铁
厂按照40%,40%,15%和5%的配比分别配入赤铁矿粉、铁砂、电炉粉尘以及其
他粉尘,成品氧化球团强度2200N/球,含Fe64%,S<0.005%,基本满足高炉生
产的要求,但对配入的电炉粉尘的铅锌含量要求严格,含量过高会影响高炉炼铁
质量。
第二,炼钢处理。
将含锌低的电炉粉尘和一定配比的碳同时喷入转炉或电
炉中,高温下锌被还原挥发进入烟尘系统,锌得到富集,粉尘中的铁氧化物进入
炉渣和钢水得以利用。
德国VELCO公司、美国Armco公司和美国伯利恒钢公司通过此法回收锌铁,回收后的二次粉尘锌含量达到50%,粉尘减少为原来的30%。
电炉粉尘中含有一定的FeO,可以取代废钢作冷却剂。
此法只适合处理铅锌含量
很低且铁含量较高的电炉粉尘,铅锌含量高会降低钢水质量。
2.含锌电炉粉尘处理新技术
2.1微波法
电炉粉尘的碳热还原过程中使用微波技术,升温速度快,可产生局部高温,
降低了还原反应的活化能,加速还原过程的进行。
根据相关学者的研究,使用微
波技术实验室处理电炉粉尘,结果表明在大气条件下脱锌率可达到80%。
这些研
究初步论证了微波处理含锌电炉粉尘的可行性,目前由于前期设备投资大以及实
际操作困难等原因未得到工业应用[1]。
2.2真空冶金技术
电炉粉尘中的铁酸锌具有较高稳定性,难以分解,但在高温下可以被CO还
原至金属锌和金属铁。
电炉粉尘中的Zn、Fe、Pb、Al、Ag、Cu等元素在纯金属状态下的饱和蒸气压不一样,Zn的饱和蒸气压远大于其他金属。
利用这一特性,在
真空中采用含碳球团低温还原的方法可以得到金属锌,而在常压下火法处理电炉
粉尘只能得到氧化锌。
结果表明锌的回收率为83.3%~86.3%,所得锌锭化学成分
能达到国家2#标准。
真空冶金技术处理电炉粉尘具有流程短、环境友好、占地少、成本低、经济效益好等优点,能够实现电炉粉尘的高效、综合处理,符合冶金工
业循环经济的要求。
2.3铝浴熔融法
将含锌电炉粉尘配入煤粉、粘结剂造球,放入铝浴坩埚中高温加热,小球在
高温下迅速熔化,锌被还原挥发后被空气氧化并冷却得到收集。
某些学者对某厂
的电炉粉尘进行铝浴还原实验室研究,铅、锌快速还原成金属铅、锌,锌的沸点
比铅低,以蒸汽形式挥发后经空气氧化冷却得到富集,铅则留在了渣中。
该方法
可得到含ZnO90%的锌产品和含铅15%以上的铅铁渣,脱锌率达90%以上,铅的
富集率在94%以上,基本实现了铅锌分离[2]。
2.4焙烧转化-分离技术
湿法处理电炉粉尘,常压常温浸出只能将氧化锌中的锌浸取出来,并不能浸
取铁酸锌中的锌,导致锌的浸出率低。
采用高压热酸浸出虽然可以将铁酸锌中的
锌也部分浸出,提高锌的浸出率,但铁的浸出率也相应提高,导致后续浸出液中
锌铁分离中除铁程序复杂,增加了生产成本。
国内外对铁酸锌进行了焙烧转化研究。
我国著名学家研究了实验室低温磁化焙烧-磁选法处理含锌电炉粉尘的技术,电炉粉尘中配入合适比例的碳颗粒,在900℃下焙烧30min,焙烧产物采用水冷
的方式冷却,再经过磨矿磁选,得到精矿和尾矿。
结果表明,该技术能有效从电
炉粉尘中提取品位较高的铁精矿,而锌主要被富集到尾矿中。
精矿中铁品位
34.88%,回收率67.22%,尾矿中锌品位9.01%,回收率87.02%。
由于电炉粉尘成
分复杂,在焙烧过程中会形成锌铁固溶体,通过磁选的方法使铁锌分离的效果并
不好,所以此法还处在实验室研究阶段,尚未得到工业化应用。
日本东北大学提
出了一种处理含锌粉尘的新方法—LAMS(。
其原理是将含锌电炉粉尘与氧化钙充
分混匀后在1273K的高温下加热,电炉粉尘中的ZnFe2O4与CaO发生反应。
当
ZnFe2O4和CaO的摩尔比为1:2时,生成ZnO和Ca2Fe2O5。
ZnO、Ca2Fe2O5、ZnFe2O4三种物质分别呈现无磁性,顺磁性和强磁性的特点,利用磁性技术达到分离回收ZnO的目的。
另外,钢厂能直接利用反应产物Ca2Fe2O5脱磷或者直接作为烧结的原料,达到循环利用的目的,该法已在日本得到工业应用[3]。
结论:
简而言之,在含锌电炉粉尘处理的新方法中,微波法和铝浴熔融法虽然脱锌率高,但投资大,成本高,目前还处于实验室研究阶段。
真空冶金技术能够得到金属锌,流程短、占地少、成本低、环境友好,但工业上操作困难。
焙烧转化-分离技术为电炉粉尘的处理提供了新的思路,更具发展前景。
参考文献:
[1]韩龙,杨斌,戴永年,等.真空冶金技术在锌二次资源再生中的应用进展[J].真空,2018,45(2):20-22.
[2]张丙怀,郭兴忠,阳海彬,等.钢铁厂含锌铅粉尘中锌铅分离理论及实践[J].有色金属:冶炼部分,2019(1):7-11.
[3]尹慧超,张建良,陈永星,等.钢铁厂含锌粉尘的低温磁化焙烧试验研究[J].矿产综合利用,2017(3):40-43.。