2000立方米球罐整体热处理方案
球罐热处理方案

球罐热处理方案1. 简介球罐是一种常用的容器,广泛应用于石油、天然气、化工等行业。
为了提高球罐的强度和硬度,常需要进行热处理。
本文将介绍一种针对球罐的热处理方案,以提高其材料的性能。
2. 热处理方案热处理是通过对材料进行加热和冷却来改变其组织结构和性能的过程。
针对球罐的热处理方案主要包括以下几个步骤:2.1 材料准备首先,需要准备好球罐的材料。
常见的球罐材料包括碳钢、合金钢等。
在选择材料时,应根据球罐的具体使用环境和要求来确定。
材料的成分和含碳量等因素将对热处理的效果产生影响。
2.2 加热处理将球罐材料放入坩埚或特定的加热设备中,对材料进行加热处理。
热处理温度和时间应根据材料的具体特性和要求来确定。
一般情况下,球罐材料的加热温度为800℃至1000℃,持续时间为数小时至十几小时。
加热过程中应控制好加热速度和均匀性,以保证热处理效果的一致性。
2.3 针对性处理根据球罐材料的特性和要求,可以在加热的基础上进行针对性处理。
例如,对于碳钢材料,可以通过渗碳、氮化等方式增加其表面硬度。
对于合金钢,可以通过淬火、回火等方式调整其组织结构和机械性能。
2.4 冷却处理在完成加热和针对性处理后,需要对球罐材料进行冷却处理。
冷却速度的选择将对材料的结构和性能产生较大影响。
常用的冷却方式包括水淬、油淬等。
选择合适的冷却方式需要根据具体材料的特性和要求进行。
2.5 检验和评估完成热处理后,需要对球罐材料进行检验和评估,以确保热处理的效果和质量。
常用的方法包括金相显微镜观察、硬度测试、拉伸试验等。
根据检验结果,可以评估材料的性能是否符合要求,并进行必要的调整和改进。
3. 注意事项在进行球罐热处理时,应注意以下几个事项:•确保热处理设备的安全性和稳定性,以避免意外事故的发生。
•控制好加热和冷却过程中的温度和速度,以保证材料的一致性和稳定性。
•严格控制热处理参数,避免超过材料的耐受范围,造成不良效果或材料损坏。
•根据具体要求选择合适的热处理方案和工艺,以获得理想的材料性能。
球罐热处理方案

球罐热处理方案简介球罐热处理是一种将材料加热到一定温度后进行冷却的工艺,目的是改善材料的力学性能和耐磨性。
本文将介绍球罐热处理的原理、步骤以及应用。
原理球罐热处理是通过控制材料的加热温度和冷却速度,改善材料的晶体结构和性能。
常用的球罐热处理方法包括退火、正火和淬火。
•退火:将材料加热到临界温度,然后缓慢冷却至室温。
退火能够消除材料中的应力和晶体缺陷,提高材料的延展性和韧性。
•正火:将材料加热到适当温度,然后迅速冷却。
正火能够提高材料的强度和硬度,但会降低韧性。
•淬火:将材料加热到临界温度,然后迅速冷却。
淬火能够形成马氏体组织,提高材料的硬度和耐磨性,但会降低塑性。
步骤球罐热处理的步骤包括材料准备、加热、冷却和后处理。
1.材料准备:选择合适的材料,并根据要求进行预处理,如去除表面氧化层、清洁等。
2.加热:将材料放入球罐中,加热到所需温度。
加热时需要根据材料的类型和要求确定加热时间和温度曲线。
3.冷却:根据球罐热处理的方法,选择合适的冷却介质和冷却速度,迅速冷却材料。
4.后处理:根据需要进行进一步处理,如清洗、退火等,以达到最终要求。
应用球罐热处理广泛应用于钢铁、铝合金等金属材料的制造和加工过程中,以提高材料的强度、硬度和耐磨性。
钢铁制造在钢铁制造中,球罐热处理可以用于退火、正火和淬火。
•退火:对冷拔、冷轧、焊接等过程中产生的应力进行消除,提高材料的延展性和韧性。
•正火:提高钢材的强度和硬度,适用于需要较高强度的零件制造。
•淬火:形成马氏体组织,提高钢材的硬度和耐磨性,适用于需要耐磨性能的零件制造。
铝合金加工在铝合金加工中,球罐热处理主要用于退火和时效处理。
•退火:消除应力和改善铝合金的可塑性,适用于挤压、拉伸等工艺。
•时效处理:通过加热和冷却控制,使铝合金材料达到最佳强度和耐蚀性能。
注意事项在进行球罐热处理时,需要注意以下几点:1.严格控制加热和冷却过程中的温度和时间,以确保达到所需的材料性能。
2.确保球罐和冷却介质的清洁,以避免污染材料。
热处理方案

热处理方案中石化清江石化有限责任公司2台×2000m3液化气球罐热处理工艺方案二○○○年七月目录1. 编制依据2. 概况3. 热处理方法与工艺4. 流程与装置5. 热处理前准备6. 热处理操作7. 劳动力组合与岗位细则8. 热处理效果评定9. 质量保证措施10. 安全措施11. 机具及材料一览表12. 热工计算13. 附图13.1 2000m3球罐整体热处理工艺流程图(1)13.2 2000m3球罐整体热处理保温图(2)13.3 2000m3球罐整体热处理测点布置图(3)13.4 2000m3球罐整体热处理工艺曲线(4)13.5 2000m3下级板温度补偿电加热器布置图(5)13.6 喷嘴结构示意图(6)13.7 焊接试板固定示意图(7)1. 编制依据及执行规范1.1 编制依据1.1.1 2000m3球罐工艺图1.2 执行规范1.2.1 《球形储罐施工及验收规范》GBJ94-981.2.2 《球形储罐工程施工工艺标准》SHJ512-901.2.3 《钢制球形储罐》GB12337-981.2.4 《钢制压力容器》GB150-981.2.5 《压力容器安全技术监察规程》2. 概况2.1 概况介绍清江石化有限公司2000m3液化气球罐为现场组焊的压力容器,根据施工图的要求为消除球罐组装与焊接的残余应力和变形,改善焊缝及热影响区的组织,减少产生应力腐蚀条件,需现场对这台球进行整体热处理。
2.2 主要技术参数容积 2000m3内径φ15700mm材质 16MnR介质液化石油气壁厚 48mm设计压力 1.75Mpa设计温度50℃容器类别Ⅲ重量 329624kg结构形式混合式3.1. 热处理方法及工艺3.1 热处理方法及原理本球罐采用喷嘴燃油内燃法整体热处理。
原理为:以球罐本身为燃烧室,球外表保温,用O#轻质柴油为燃料,利用装在球罐下部人孔上的油喷嘴为燃烧器,用压缩风将柴油喷入罐内雾化,用液化气点火,使雾化剂燃烧,以对流和辐射方式,使球罐加热到一定的温度,在这一温度下保持一定的时间,球体钢材在不发生相变的情况下,发生塑性变形,从而释放因组装焊接产生的残余应力,同时释放焊缝中的残余氢,细化晶粒,改善金属的综合性能,避免延迟裂纹的产生,达到提高球罐的使用寿命和安全性。
大型球罐整体热处理增效方法

大型球罐整体热处理增效方法摘要:由于大型球罐在企事业单位的普遍应用,基于消除对球罐焊接后产生破坏性应力,本文从球罐热处理的原理及要点,利用数值分析对球罐加装导流装置前后的热处理效果进行比较分析,确定大型球罐整体热处理的增效方法。
关键词:大型球罐热处理数值分析导流装置引言随着化工产业的发展,大型球罐的需用量也随之增大。
然而大型球罐焊接完成后焊缝留有焊接残余应力,有的可达到材料屈服极限,危害极大。
为此大型球罐通常在焊后进行整体热处理[1]以稳定结构尺寸改善焊缝、热影响区的组织,使淬火组织软化,从而改善焊接接头的性能,降低硬度、提髙塑性、断裂韧度及疲劳强度。
工程中,球罐进行整体热处理时,壁面最大温差须控制在一定范围内。
目前对体积> 2000m?的球罐采用内部燃烧加热整体热处理很难达到工艺要求。
文献[2]研究表明,在球罐采用整体热处理时,髙温燃烧产物中的一部分直接由下人孔沿球罐中心轴对称从上人孔排出,对球罐壁面的传热几乎没有作贡献;而另一部分沿中心轴到达上人孔附近后,再沿球罐内壁向下人孔方向流动,同时与壁面发生热交换使壁面温度升高,并损失部分热量,使其向球罐下部流动时与罐壁面的热交换量逐步减少,导致球罐壁面温度从上向下依次降低,从而产生壁面温差。
对体积较大的球罐,上述热处理方法会使其壁面最大温差加大而超过工艺要求的范围。
由此可知,要尽可能消除壁而温差,需加强罐内燃烧产物的循环以及与球罐壁面的对流传热过程,并尽可能降低燃烧产物的直接排出。
通过在球罐内部添加导流板等装置以增加燃烧气流在罐内回转的强度形成良好循环,并使回转气流与壁而发生尽可能多的热量交换减小能量损失,从而降低壁面温差提髙热效率。
一、改进方法在文献[2]的基础上,改进球罐内部喷射燃烧整体热处理,用计算流体力学模型对其内部流场结构进行数值模拟,结果表明,热流控制装置是热处理成功的关键。
温控装置的使用避免了通常情况下整体现场热处理球体上部温度高于下部温度的难点。
球罐安装过程整体热处理具体措施和工艺要求

对球罐的焊接部位进行强度测试,确保焊接质量可 靠。
THANKS
谢谢您的观看
加热速度对球罐的热处理效果也有重要影响,过快的 加热速度可能导致球罐表面与内部温差过大,产生较
大的热应力。
应根据球罐的材料、厚度和热处理工艺要求,合理控 制加热速度,以减小热应力和变形。
对于大型球罐,应采用分段加热的方式,以减小温差 和热应力。
保温时间控制
保温时间是指球罐在达到预定加热温度后保持恒温的时间,其目的是使球 罐内部温度均匀分布,促进材料的充分转变和均匀化。
03
焊后热处理可以采用炉内加热或外部加热的方式,炉内加热具有更好的保温效 果和控制精度。在加热过程中,应严格控制温度和冷却速度,以避免产生新的 裂纹和变形。
03
球罐安装后的热处理
整体热处理
整体热处理是球罐安装后的重要环节,目的是 消除焊接过程中产生的残余应力,提高球罐的 稳定性和耐久性。
整体热处理需要在球罐内部进行,通过加热球 罐整体,使金属材料均匀受热,然后缓慢冷却 ,使金属内部的残余应力得到释放。
预热方法可以采用火焰加热、电加热、红外线加热等。预 热时应特别注意防止局部过热,以免造成球罐材料的脆化 。
焊接过程中的热处理
01
在焊接过程中,为了减小焊接变形和焊接残余应力,需要 进行适当的热处理。
02
根据焊接工艺的要求,可以采用局部热处理或整体热处理 的方式。局部热处理是指在焊接区域附近进行加热,而整
确保热处理方案符合相关标准和规范,并经过审批和备案。
准备热处理设备
根据热处理方案选择合适的热处理设 备,如电加热器、燃气加热器、红外 线加热器等。
对热处理设备进行检查和调试,确保 其性能良好、安全可靠。
2000m3混合式4带球罐方案

球罐施工方案1.概述1.1工程内容:天脊集团100万吨/年硝酸磷钾肥技改工程2000m3单体球罐一台,结构形式为桔瓣式加足球瓣的混合式,材质是16MnR。
1.2 建设单位:天脊集团1.3 设计单位:华泰工程公司1.5工程地址:山西省潞城市2.球罐技术参数及施工依据2.1.球罐技术参数2.2.主体焊接工作量(单台)2.3 编制依据2.3.1执行的主要技术标准、规范(1) GB150-1998《钢制压力容器》(2) GB12337-1998《钢制球形储罐》(3)《压力容器安全技术监察规程》(4) GB50094-98《球形储罐施工及验收规范》(5) JB4708-92《钢制压力容器焊接工艺评定》(6) JB4709-92 《钢制压力容器焊接规程》(7) JB4730-94《压力容器无损检测》2.3.2执行本公司管理文件(1)《质量保证手册》Q/HSG00.05-2000(2)《压力容器含球罐组焊工程质量保证手册》Q/HSA11-98(3)《质量体系程序文件》Q/HSG01-22(4)《安全卫生与环境管理手册》Q/HSG27.01-20013. 施工程序施工程序见附图4.主要施工方法球罐安装采用单片散装法,焊接采用手工电弧焊,焊后要立即进行后热消氢处理,射线检测采用X(或γ)射线透照。
4.1 施工准备4.1.1 对通至球罐安装现场的运输道路和工作区域进行平整。
4.1.2 各种临时管路、水、电、库房、施工临时道路、平台等设施按现场平面布置图的要求进行设置。
4.1.3 对已进场的各种施工机械进行必要的检查、维修试运行。
4.1.4 对施工用的计量器具、样板等工具进行校验,工卡具等加工件全部运抵现场。
4.1.5做好球壳板及其他零部件的开箱检查及验收工作。
4.1.6对施工图、设计文件及制造单位提供的技术文件等认真审核,发现问题及早处理。
4.2. 球壳板检验4.2.1 球罐安装前,对球壳板的曲率、几何尺寸和坡口表面质量进行全面复查。
球罐整体热处理控制工艺规程

球罐整体热处理控制工艺规程1 前言球罐在组装焊接过程中焊缝处会产生较大应力(组装应力,温差应力和组织应力等),焊缝附近存在着淬硬组织和扩散氢,这些都是使球罐产生延迟裂纹和应力腐蚀裂纹的重要因素,从而可能导致球罐早期破损和事故的发生。
对球罐进行焊后整体热处理是消除焊缝应力,释放焊缝中的残余氢,改善和提高焊缝综合机械性能的有效方法,从而极大的提高球罐的安全使用可靠性。
本工艺规程是于本公司现场组焊的球罐整体热处理的通用工艺规程,在实际工程中应根据现场球罐的具体情况制定热处理实施方案。
2 工艺原理燃油内燃法为内热式热处理,它是将球罐作为炉膛,球罐外壁隔热保温,在球罐内部安装燃油燃烧装置,使燃油在球罐内燃烧,以此对球罐加温来达到热处理的目的,燃油内燃法采用了国产GD系列高压多孔喷嘴,使压缩空气与轻柴油在球罐内部雾化点燃后对球罐加热,通过调节压缩空气和燃油流量来控制火焰达到控制温度的目的。
在工程实践中应根据现场球罐的参数进行热工计算,确定喷嘴、空气压缩机、油泵、流量计、供风管道的规格型号。
2.1 施工工艺示意图见“燃油法球罐整体热处理示意图”。
3 热处理前的准备工作热处理工作应在本体焊接工作全部结束后、无损检测结果合格后方可进行,热处理前的准备工作及施工程序应按下列规定进行。
3.1 热处理前的一般规定3.1.1 调整脚手架,以便于保温、热处理操作及防火安全;3.1.2 搭设防雨、防风棚;准备消防灭火设施;3.1.3 松开地脚螺母、调整支柱,使其能自由膨胀位移并保持垂直,安装柱腿热膨胀位移监视装置;3.1.4 断开与球体相连接的平台、过桥、梯子等附件,以确保球体自由膨胀和位移;3.1.5 拆开与热处理无关之球罐接管管口,并用盲板封闭;3.1.6 在防爆区域施工应考虑采取隔离或屏蔽处理等安全措施。
3.2 热处理前准备工作的实施3.2.1 球罐柱腿移动装置安装:卸除地脚螺母后,在基础底板上置入减摩装置或涂上黄油,以减少球罐在热处理过程中膨胀位移的磨擦力。
2000立方米球罐整体热处理方案
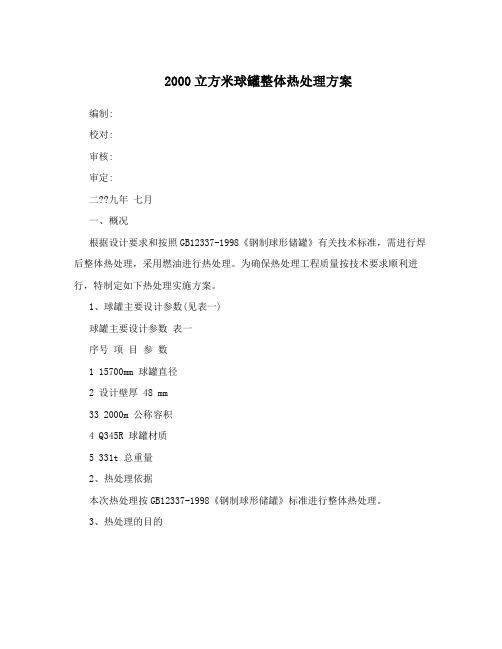
2000立方米球罐整体热处理方案编制:校对:审核:审定:二??九年七月一、概况根据设计要求和按照GB12337-1998《钢制球形储罐》有关技术标准,需进行焊后整体热处理,采用燃油进行热处理。
为确保热处理工程质量按技术要求顺利进行,特制定如下热处理实施方案。
1、球罐主要设计参数(见表一)球罐主要设计参数表一序号项目参数1 15700mm 球罐直径2 设计壁厚 48 mm33 2000m 公称容积4 Q345R 球罐材质5 331t 总重量2、热处理依据本次热处理按GB12337-1998《钢制球形储罐》标准进行整体热处理。
3、热处理的目的为了消除球罐组装与焊接的残余应力,稳定球罐的几何尺寸,改善焊接接头和热影响区的组织和性能,达到降低硬度,提高塑性和韧性的目的,进一步释放焊缝中的有害气体,防止焊缝的氢脆和裂纹的产和生。
二、热处理方法及工艺规范1、热处理方法采用燃油法进行热处理以球罐内部为炉膛,选用0号柴油为燃料,球罐外部用保温材料进行绝热保温,通过鼓风机送风和喷嘴将燃料油喷入并雾化,由电子点火器点燃,随着燃油不断燃烧产生的高温气流在球罐内壁对流传导和火焰热辐射作用,使球罐升温到热处理所需的温度。
2、热处理工艺规范按照GB12337-1998《钢制球形储罐》选择如下热处理工艺参数和工艺曲线:(1)恒温温度 600?25?恒温时间 2h升温速度 50-80?/h(?400?时可不予控制)降温速度 30-50?/h(?400?时可不予控制)升温时的最大温差 ?130?降温时的最大温差 ?130?(2)热处理工艺曲线 (见图一)三、热工计算1、热工计算参数(见表二)热工计算参数表二序号项目参数1 15700mm 球罐内径d2 48mm 球壳板厚度δ3 Q345R 材质4 331t 球壳板重量G5 保温棉厚度δ 80-100mm36 保温棉容量G 65kg/m7 钢材比热C 500?:0.162Kca1/kg .?:600?:0.18Cal/kg . ? 8 钢材导热系数λ1 500?:30.962Kca1/m.h. ?:600?:28Kca1/m.h. ? 9 保温棉导热系数λ0 500?:0.07Kca1/m.h. ?:600?:0.828KCa1/m.h. ?10 保温棉比热λ 0.2Kca1/kg. ?11 环境温度 ? 3512 燃烧油号柴油02、计算热处理耗热量见表三,以下是升温到500?-600?期间,升温速度按50?/h-80?/h时的计算结果。
- 1、下载文档前请自行甄别文档内容的完整性,平台不提供额外的编辑、内容补充、找答案等附加服务。
- 2、"仅部分预览"的文档,不可在线预览部分如存在完整性等问题,可反馈申请退款(可完整预览的文档不适用该条件!)。
- 3、如文档侵犯您的权益,请联系客服反馈,我们会尽快为您处理(人工客服工作时间:9:00-18:30)。
少年易学老难成,一寸光阴不可轻- 百度文库
2000立方米球罐整体热处理方案
编制:
校对:
审核:
审定:
二○○九年七月
一、概况
根据设计要求和按照GB12337-1998《钢制球形储罐》有关技术标准,需进行焊后整体热处理,采用燃油进行热处理。
为确保热处理工程质量按技术要求顺利进行,特制定如下热处理实施方案。
1、球罐主要设计参数(见表一)
球罐主要设计参数表一序号项目参数
1 球罐直径15700mm
2 设计壁厚48 mm
3 公称容积2000m3
4 球罐材质Q345R
5 总重量331t
2、热处理依据
本次热处理按GB12337-1998《钢制球形储罐》标准进行整体热处理。
3、热处理的目的
为了消除球罐组装与焊接的残余应力,稳定球罐的几何尺寸,改善焊接接头和热影响区的组织和性能,达到降低硬度,提高塑性和韧性的目的,进一步释放焊缝中的有害气体,防止焊缝的氢脆和裂纹的产和生。
二、热处理方法及工艺规范
1、热处理方法
采用燃油法进行热处理
以球罐内部为炉膛,选用0号柴油为燃料,球罐外部用保温材料进行绝热保温,通过鼓风机送风和喷嘴将燃料油喷入并雾化,由电子点火器点燃,随着燃油不断燃烧产生的高温气流在球罐内壁对流传导和火焰热辐射作用,使球罐升温到热处理所需的温度。
2、热处理工艺规范
按照GB12337-1998《钢制球形储罐》选择如下热处理工艺参数和工艺曲线:(1)恒温温度600±25℃
恒温时间2h
升温速度50-80℃/h(≤400℃时可不予控制)
降温速度30-50℃/h(≤400℃时可不予控制)
升温时的最大温差≤130℃
降温时的最大温差≤130℃
(2)热处理工艺曲线(见图一)
三、热工计算
1、热工计算参数(见表二)
热工计算参数表二
序号项目参数
1 球罐内径d 15700mm
2 球壳板厚度δ48mm
3 材质Q345R
4 球壳板重量G 331t
5 保温棉厚度δ80-100mm
6 保温棉容量G 65kg/m3
7 钢材比热C 500℃:0.162Kca1/kg .℃:600℃:0.18Cal/kg . ℃
8 钢材导热系数λ1 500℃:30.962Kca1/m.h. ℃:600℃:28Kca1/m.h. ℃
9 保温棉导热系数λ0 500℃:0.07Kca1/m.h. ℃:600℃:0.828KCa1/m.h. ℃
10 保温棉比热λ0.2Kca1/kg. ℃
11 环境温度35℃
12 燃烧油0号柴油
2、计算
热处理耗热量见表三,以下是升温到500℃-600℃期间,升温速度按50℃/h-80℃/h时的计算结果。
速率烟气单位时间耗油量时间单位耗油量10000Kca1/h
℃/h℃BKg/h 流量L/h Q1 Q2 Q3 Q4 Q5 Q6 总耗热量l 65 550 406 484 30.4 30.4 18.56 100.84 24.4 8.8 487
Q2-热壳板与保温层的传热损失
Q3-保温层的蓄热损失
Q4-炉废气带走的热
Q5-燃料化学不完全燃烧损失的热理
Q6-燃料机械不完全燃烧损失的热量
B-燃料油的用量
本次热处理工程采用德国EK9-1000L-R型枪式燃烧器,其燃烧能力产生的热量为11000000kca1由表三可知,球罐热处理时能满足供热要求。
四、热处理现场工艺设计
1、热处理工艺系统
本次热处理工程由供油、燃油、测量、功率控制、柱腿移动组成。
A:燃油系统
燃油系统采用德国EK9-1000L-R型枪式燃烧器,燃烧器与球罐下入孔相接,采用一套微机系统对热处理工程进行智能化控制,以满足工艺要求,燃料采用0号柴油通过油泵送油,经电磁阀控制进入喷嘴喷出,燃烧器鼓风机由底部送风助燃,雾化燃烧油,自动电子点火器点为燃燃油进行燃烧。
B:供油系统
(5)
根据热工计算,本次罐热处理最大耗油量为487L/h,单台热处理耗油量≤4吨,储油罐一次装油量应保证单台球罐热处理全周期所需油量的1.5倍,故应设备容量为6吨的储油罐。
C:温度测量控制系统
温度测量监控系统由热电偶,补偿导线和一套PC-WK型集散控制系统对温度进行智能化测量和控制。
C-1测量点布置
按照GB12337-1998《钢制球形储罐》有关技术标准的要求,本次热处理共设测温点24个,上下半球共7个带,测温点应均匀布置在球壳表面,相邻测温点间距应≤4500mm,距入孔与球壳环缝边缘250mm以内及产品试板上必须设测温点。
详见测温点布置图(图二)
C-2热电偶安装
采用储能式热电偶点焊机,按图二要求将热电偶牢固地点焊在球壳外侧,烟道气和试板应单独另设热电偶。
补偿导线应妥善固定,以防烧毁。
各热电偶型号均为K型镍铬-镍硅,补偿导线采用K型双芯线。
C-3温度监测
温度监测配置两套系统,一套是EH100-24长图自动平衡记录仪1台,共可记录24个测温点,另一套是微机集散型温度监控系统,3秒钟扫描一个测温点巡回检测各测温点的温度,并与设置的热处理工艺曲线进行比较对照。
D:柱腿移动措施
热处理前将罐支柱杆及地脚螺栓全部松开,以保证热处理过程中位移,在每一个柱腿处安装千斤顶一台,并对每个柱腿处设置垂直标准点(径点环向)柱腿移动前在基础板上做出移动量刻度进行移动。
柱腿移动量由公式L=DO×a×t计算,见表四要求。
式中a—材料的线膨胀系数
DO—球罐直径
温度范围℃100 200 300 400 500 600 累计移动量mm 7.6 15.2 19.8 25.4 28 30.6
3、保温方法
球罐保温材料采用超细玻璃纤维毡,总厚度100mm保温棉采φ6和保温钉固定,安装保温棉块时要用14#铁丝在保温钉上交叉绕紧,尤其应注意防止下半球安装的保温棉块下塌脱落。
球罐上的入孔,接管,均应加保温棉,从支柱与球罐连接焊缝的下端算起向下1m长度范围内的支柱需保温。
保温的效果具体由微机每3秒钟巡检上点,每2分钟左右巡查一遍的速度加以监控,能及时发现保温的缺陷发生温差信号告警,提示加以补救。
4、试板与球壳板同步热处理
(7)
在热处理规范中要求试板与球罐的球壳板采用相同工艺进行热处理。
因此规定把试板放在温带以120°间隔放置三块试板力求同步,事实上试板因放在球壳板外侧,靠球壳板温度传导给试板,因此试板必定滞后和低与球壳板的温度。
本次热处理由微机采样方试板附近测温点的温度,把这一温度作为试板的
设定温度,由智能仪表自动加以补温使之保持在±1℃的温差内,做到同步热处理。
五、热处理前的准备工作
1、球罐球体、入孔、接管及预焊件等必须全部焊接完毕,并经外观检察和无损探伤检查合格。
2、所有无损探伤检查工作必须作完。
3、球罐内外表面质量和几何尺寸应检验合格,记录齐全。
4、产品试板焊接检查合格,并经监检人员确认,试板在球壳上固定应牢固。
5、所有原始资料齐全,并经质保系责任人员签字认可,经监检单位和甲方确认。
6、热处理系统装置必须全部安装好,各系统应调试完毕。
7、供电系统经全面检查合格符合要求,并和有关部门联系,确保热处理期间不断电。
8、应掌握气象资料,热处理应避开大风与下雨天气。
9、各岗位人员应齐全到位,并经培训上岗,分工协作。
(8)
10、施工技术方案应向有关人员交底。
六、施工组织
1、人员
郑来林、王浩林等。
2、为确保热处理工作顺利进行,设置岗位和职责范围,详见表五要求:
热处理岗位和职责范围(表五)
序号岗位名称人数责任范围
1 指挥岗 1 负责指挥整个热处理工艺实施和掌握热处理全过程各种情况及各种问题
2 工艺操作岗 2 负责燃烧及供油系统正常进行
3 议表维护岗 1 负责测温系统及燃烧系统仪表正常动行及故障处理
4 电器机械
维护岗
1 负责热处理系统电器,机械设备正常动行及故障处理
5 柱腿移动岗 4 负责柱腿移动(由甲方安排操作人员)
6 保温棉
检查岗
2
检查保温棉完好程度测量外层温度,如属保温棉脱落或外
层温度>60℃应及时补救
7 安全防火岗 1 热处理防火措施落实及过程监控
1、清理现场易燃易爆品及闲置器材,清量工作道路,装好夜间照明,准备足够数量的消防器材。
2、储油罐,液化气瓶,乙炔瓶应离处理点火处20米以外。
3、保证安全送电,各种电缆线布置整齐合理。
4、坚守岗位,尽职尽责,无关人员不得进入热处理施工现场。
5、热处理整个过程中,应有专人24小时全程安全监护。
6、及时掌握天气预报,严禁在5级以上大风或雨雪天气进行热处理作业。
7、设好安全警戒,严禁无关人员进入或通过热处理区域。
8、做好安全应急预案,以备在突发或紧急情况下起动。
八、应急预案
本应急预案是指应当预先考虑到当发生非正常情况时应当采取的措施,以及为采取相应措施时应当预先准备的器材、材料等。