超细晶化理论及技术与炉外精炼技术
冶金工程技术学科发展简述

冶金工程技术学科发展简述中国科学技术协会,中国金属学会冶金工程技术学科是工程技术学科中的重要学科,它是冶金工业,专门是钢铁工业进展的基础和保证。
现代冶金工程技术学科在我国钢铁工业高速进展中努力创新,支持了钢铁生产流程的优化和符合循环经济差不多原则、符合人类生活可连续进展目标的要求。
我国现代冶金工程技术学科新世纪要紧进展是:提出了可循环钢铁生产流程工艺与装备新理念;利用现有生产装备在优化工艺技术的基础,实践高洁净、高平均性和超细晶理论,经济高效地批量生产高强韧性钢材;大大促进了薄板坯连铸连轧紧凑流程工艺与装备技术的进展。
从总体上能够认为,我国冶金工程技术学科的自主创新能力有了专门大提升,已取得的创新成果中,有许多已达到国际先进或领先水平,成为我国钢铁工业优化与进展的重要标志。
本报告将就冶金工程技术学科新世纪以来进展取得的新进展,与国际先进水平的对比,以后进展的目标、研究方向和重点分不进行论述。
1中国冶金工程技术学科进展的新进展1.1具有较广泛综合性的学科进展新进展要紧有以下3 个方面:1)提出可循环钢铁生产流程工艺与装备新理念,是学科进展最重要的进展之一中国钢铁工业高速进展的同时,提出了新世纪应重点进展如何样的新一代钢铁生产流程的命题。
钢铁工业是流程工业,流程的优化是钢铁工业整体优化的基础和保证。
冶金工程技术学科的专家们研究了钢铁流程功能优化、钢铁生产在循环经济中的作用和责任、环境与能源结构对钢铁生产制约及推动钢铁流程优化的作用等咨询题后,明确提出了钢铁企业要集产品制造、能源转化、社会废弃物再资源化三大功能于一体为要紧内容的新一代钢铁制造流程新理念[1] 。
目前这一理念正在持续完善,把研究衡量其水平的目标体系,在若干现有先进技术、装备基础上,与新开发的工艺、装备及界面技术集成,重新构筑全新流程作为重点,对现有企业的改造和新建钢厂的设计都有专门好的指导意义。
目前这一理念已纳入国家中长期科学和技术进展规划纲要及“十一五”国民经济和社会进展规划纲要。
炉外精炼工:炉外精炼工考试答案
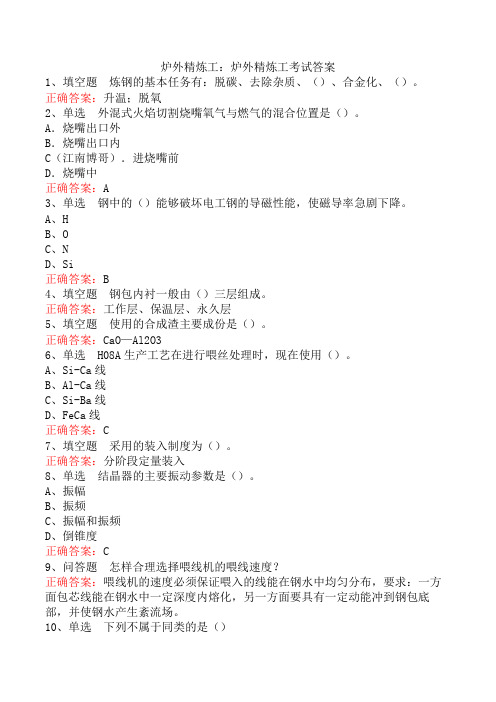
炉外精炼工:炉外精炼工考试答案1、填空题炼钢的基本任务有:脱碳、去除杂质、()、合金化、()。
正确答案:升温;脱氧2、单选外混式火焰切割烧嘴氧气与燃气的混合位置是()。
A.烧嘴出口外B.烧嘴出口内C(江南博哥).进烧嘴前D.烧嘴中正确答案:A3、单选钢中的()能够破坏电工钢的导磁性能,使磁导率急剧下降。
A、HB、OC、ND、Si正确答案:B4、填空题钢包内衬一般由()三层组成。
正确答案:工作层、保温层、永久层5、填空题使用的合成渣主要成份是()。
正确答案:CaO—Al2O36、单选H08A生产工艺在进行喂丝处理时,现在使用()。
A、Si-Ca线B、Al-Ca线C、Si-Ba线D、FeCa线正确答案:C7、填空题采用的装入制度为()。
正确答案:分阶段定量装入8、单选结晶器的主要振动参数是()。
A、振幅B、振频C、振幅和振频D、倒锥度正确答案:C9、问答题怎样合理选择喂线机的喂线速度?正确答案:喂线机的速度必须保证喂入的线能在钢水中均匀分布,要求:一方面包芯线能在钢水中一定深度内熔化,另一方面要具有一定动能冲到钢包底部,并使钢水产生紊流场。
10、单选下列不属于同类的是()A、Fe-Ca包芯线B、Si-Ca包芯线C、Si-Ca-Ba包芯线D、Fe-B包芯线正确答案:D11、单选炉渣粘度的单位为()A、mol/LB、N•s/m2C、t/m3D、J/(mol•K)正确答案:B12、单选精炼使用的Al线其Al含量要求为()A、≥90%B、≥95%C、≥98%D、100%正确答案:C13、问答题钢中碳含量与钢的性能的关系?正确答案:碳主要以碳化物Fe3C形式存在于钢中,是决定钢强度的主要元素,当钢中的碳含量升高时,其硬度、强度均有所提高,而塑性、韧性和冲击韧性降低,冷脆倾向性和时效倾向性也有提高。
随着钢中碳含量的升高,焊接性能显著下降。
14、填空题脱硫速度随碱度CaO/SiO2增加而上升,随SiO2增多而()。
LF精炼全解析

LF精炼全解析LF精炼知识1.炉外精炼发展历程20世纪30-40年代,合成渣洗、真空模铸。
1933年,法国佩兰(R.Perrin)应⽤⾼碱度合成渣,对钢液进⾏“渣洗脱硫”—现代炉外精练技术的萌芽;50年代,⼤功率蒸汽喷射泵技术的突破,发明了钢包提升脱⽓法(DH)及循环脱⽓法(RH)1935年H.Schenck 确定⼤型钢锻件中的⽩点缺陷是由氢引起的-氢脆。
1950年,德国Bochumer Verein (伯施莫尔-威林)真空铸锭。
1953年以来,美国的10万千⽡以上的发电⼚中,都发现了电机轴或叶⽚折损的事故。
1954年,钢包真空脱⽓。
1956年,真空循环脱⽓(DH、RH)。
60-70年代,⾼质量钢种的要求,产⽣了各种精炼⽅法60、70年代是炉外精炼多种⽅法分明的繁荣时期与60年代起纯净钢⽣产概念的提出、连铸⽣产⼯艺稳定和连铸品种扩⼤的强烈要求密切相关此时,炉外精炼正式形成了真空和⾮真空两⼤系列不同功能的系统技术,同时铁⽔预处理技术也得到迅速发展,它和钢⽔精炼技术前后呼应,经济分⼯,形成系统的炉外处理技术体系,使钢铁⽣产流程的优化重组基本完成。
这个时期,还基本奠定了吹氩技术作为各种炉外精炼技术基础的地位和作⽤。
这⼀时期发展的技术:VOD-VAD、ASEA-SKF、RH-OB、LF、喷射冶⾦技术(SL、TN、KTS、KIP)、合⾦包芯线技术、加盖和加浸渍罩的吹氩技术(SAB、CAB、CAS)?80-90年代,连铸的发展,连铸坯对质量的要求及炼钢炉与连铸的衔接,RH-KTB、RH-MFP、RH-OB;RH-IJ(真空深脱磷),RH-PB、WPB(真空深脱硫)、V-KIP、SRP脱磷21世纪,更⾼节奏及超级钢的⽣产。
2.炉外精炼作⽤和地位提⾼冶⾦产品质量,扩⼤钢铁⽣产品种不可缺少的⼿段;是优化冶⾦⽣产⼯艺流程,进⼀步提⾼⽣产效率、节能强耗、降低⽣产成本的有⼒⼿段。
保证炼钢-连铸-连铸坯热送热装和直接轧制⾼温连接优化的必要⼯艺⼿段优化重组的钢铁⽣产⼯艺流程中独⽴的,不可替代的⽣产⼯序图1 取样器⽰意图3. LF 精炼⼯艺优点●精炼功能强,适宜⽣产超低硫、超低氧钢;●具备电弧加热功能,热效率⾼,升温幅度⼤,温度控制精度⾼;●具备搅拌和合⾦化功能,易于实现窄成分控制,提⾼产品的稳定性;●采⽤渣钢精炼⼯艺,精炼成本较低;●设备简单,投资较少。
炉外精炼工(中高级)考试题库(含A.B卷)

炉外精炼工(中高级)考试题库(含A.B卷)A卷:炉外精炼工(高级)题库1、【单项选择题】钢包炉化渣的三要素()。
A、化好渣、化透渣、终渣做粘B、早化渣、化好渣、化透渣C、早化渣、化好渣、均匀升温D、早化渣、化好渣、终渣做粘标准答案:D2、【填空题】引定头的结构形式有()和钩头式。
标准答案:燕尾槽式3、【单项选择题】下列炉外精炼设备不具备真空脱气功能的是()A、LFVB、RHC、DHD、CAS标准答案:D4、【填空题】LF炉短弧操作是指()弧流,()弧压。
标准答案:增大;降低5、【填空题】炼钢的基本任务有:脱碳、去除杂质、()、合金化、()。
标准答案:升温;脱氧6、【单项选择题】关于降低钢中气体的主要措施中描叙不正确的是()A、使用干燥的原材料和耐火材料B、降低与钢液接触的气相中的气体的分压C、在脱气过程中减少钢液的表面积D、利用各种搅拌钢液的方法,提高钢中气体传质系数标准答案:C7、【单项选择题】铸坯内的大颗粒夹杂物一般聚集在内弧的()处。
A、1/2B、1/3C、1/4D、皮下4mm标准答案:C8、【单项选择题】防止LF炉精炼过程钢液增氮的措施有()A、采用短弧操作B、采用长弧操作C、减少渣量D、采用微负压操作标准答案:A9、【单项选择题】钢液吹氩搅拌的作用()。
A、加快钢渣的反应速度B、促进钢液脱氢C、促进夹杂物的上浮D、均匀钢水温度和成分标准答案:B10、【单项选择题】氮对钢的性能的主要影响是()。
A、热脆B、冷脆C、“白点”D、时效硬化标准答案:D11、【单项选择题】LF炉的电极夹持器应选用哪种材质的材料()A、电阻率低、电阻温度系数低B、电阻率高、电阻温度系数低C、电阻率高、电阻温度系数低D、电阻率高、电阻温度系数高标准答案:A12、【单项选择题】铁水中的哪种成分是转炉炼钢的强发热元素()A、SiB、CrC、SD、Mn标准答案:A13、【问答题】为什么精炼后要保证一段弱搅拌时间?标准答案:钢水弱搅拌净化处理技术是指通过弱的氩气搅拌促使夹杂物上浮。
炉外精炼——精选推荐
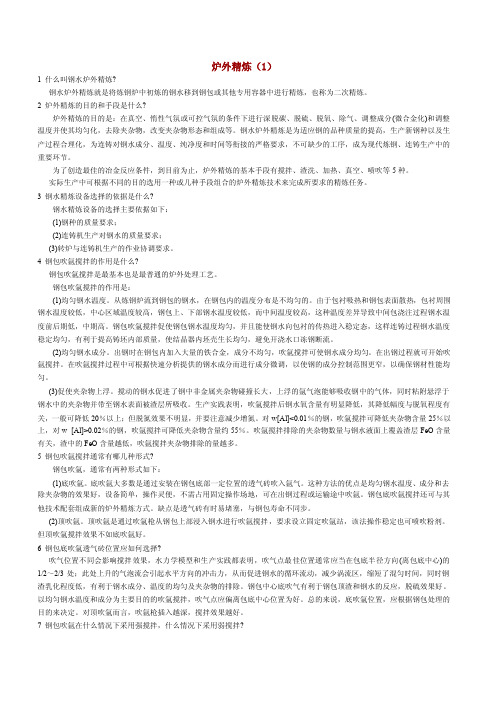
炉外精炼(1)1 什么叫钢水炉外精炼?钢水炉外精炼就是将炼钢炉中初炼的钢水移到钢包或其他专用容器中进行精炼,也称为二次精炼。
2 炉外精炼的目的和手段是什么?炉外精炼的目的是:在真空、惰性气氛或可控气氛的条件下进行深脱碳、脱硫、脱氧、除气、调整成分(微合金化)和调整温度并使其均匀化,去除夹杂物,改变夹杂物形态和组成等。
钢水炉外精炼是为适应钢的品种质量的提高,生产新钢种以及生产过程合理化,为连铸对钢水成分、温度、纯净度和时间等衔接的严格要求,不可缺少的工序,成为现代炼钢、连铸生产中的重要环节。
为了创造最佳的冶金反应条件,到目前为止,炉外精炼的基本手段有搅拌、渣洗、加热、真空、喷吹等5种。
实际生产中可根据不同的目的选用一种或几种手段组合的炉外精炼技术来完成所要求的精炼任务。
3 钢水精炼设备选择的依据是什么?钢水精炼设备的选择主要依据如下:(1)钢种的质量要求;(2)连铸机生产对钢水的质量要求;(3)转炉与连铸机生产的作业协调要求。
4 钢包吹氩搅拌的作用是什么?钢包吹氩搅拌是最基本也是最普通的炉外处理工艺。
钢包吹氩搅拌的作用是:(1)均匀钢水温度。
从炼钢炉流到钢包的钢水,在钢包内的温度分布是不均匀的。
由于包衬吸热和钢包表面散热,包衬周围钢水温度较低,中心区域温度较高,钢包上、下部钢水温度较低,而中间温度较高,这种温度差异导致中间包浇注过程钢水温度前后期低,中期高。
钢包吹氩搅拌促使钢包钢水温度均匀,并且能使钢水向包衬的传热进入稳定态,这样连铸过程钢水温度稳定均匀,有利于提高铸坯内部质量,使结晶器内坯壳生长均匀,避免开浇水口冻钢断流。
(2)均匀钢水成分。
出钢时在钢包内加入大量的铁合金,成分不均匀,吹氩搅拌可使钢水成分均匀。
在出钢过程就可开始吹氩搅拌。
在吹氩搅拌过程中可根据快速分析提供的钢水成分而进行成分微调,以使钢的成分控制范围更窄,以确保钢材性能均匀。
(3)促使夹杂物上浮。
搅动的钢水促进了钢中非金属夹杂物碰撞长大,上浮的氩气泡能够吸收钢中的气体,同时粘附悬浮于钢水中的夹杂物并带至钢水表面被渣层所吸收。
炉外精炼问答题提纲
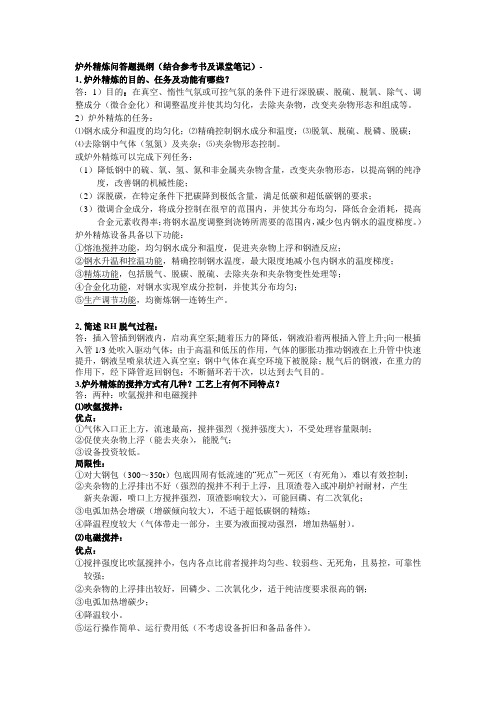
炉外精炼问答题提纲(结合参考书及课堂笔记)-1.炉外精炼的目的、任务及功能有哪些?答:1)目的:在真空、惰性气氛或可控气氛的条件下进行深脱碳、脱硫、脱氧、除气、调整成分(微合金化)和调整温度并使其均匀化,去除夹杂物,改变夹杂物形态和组成等。
2)炉外精炼的任务:⑴钢水成分和温度的均匀化;⑵精确控制钢水成分和温度;⑶脱氧、脱硫、脱磷、脱碳;⑷去除钢中气体(氢氮)及夹杂;⑸夹杂物形态控制。
或炉外精炼可以完成下列任务:(1)降低钢中的硫、氧、氢、氮和非金属夹杂物含量,改变夹杂物形态,以提高钢的纯净度,改善钢的机械性能;(2)深脱碳,在特定条件下把碳降到极低含量,满足低碳和超低碳钢的要求;(3)微调合金成分,将成分控制在很窄的范围内,并使其分布均匀,降低合金消耗,提高合金元素收得率;将钢水温度调整到浇铸所需要的范围内,减少包内钢水的温度梯度。
)炉外精炼设备具备以下功能:①熔池搅拌功能,均匀钢水成分和温度,促进夹杂物上浮和钢渣反应;②钢水升温和控温功能,精确控制钢水温度,最大限度地减小包内钢水的温度梯度;③精炼功能,包括脱气、脱碳、脱硫、去除夹杂和夹杂物变性处理等;④合金化功能,对钢水实现窄成分控制,并使其分布均匀;⑤生产调节功能,均衡炼钢—连铸生产。
2.简述RH脱气过程:答:插入管插到钢液内,启动真空泵;随着压力的降低,钢液沿着两根插入管上升;向一根插入管1/3处吹入驱动气体;由于高温和低压的作用,气体的膨胀功推动钢液在上升管中快速提升,钢液呈喷泉状进入真空室;钢中气体在真空环境下被脱除;脱气后的钢液,在重力的作用下,经下降管返回钢包;不断循环若干次,以达到去气目的。
3.炉外精炼的搅拌方式有几种?工艺上有何不同特点?答:两种:吹氩搅拌和电磁搅拌⑴吹氩搅拌:优点:①气体入口正上方,流速最高,搅拌强烈(搅拌强度大),不受处理容量限制;②促使夹杂物上浮(能去夹杂),能脱气;③设备投资较低。
局限性:①对大钢包(300~350t)包底四周有低流速的“死点”-死区(有死角),难以有效控制;②夹杂物的上浮排出不好(强烈的搅拌不利于上浮,且顶渣卷入或冲刷炉衬耐材,产生新夹杂源,喷口上方搅拌强烈,顶渣影响较大),可能回磷、有二次氧化;③电弧加热会增碳(增碳倾向较大),不适于超低碳钢的精炼;④降温程度较大(气体带走一部分,主要为液面搅动强烈,增加热辐射)。
超细晶钢
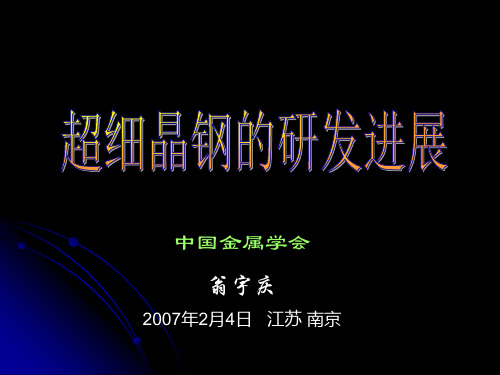
点缺陷(空位)固溶强化 线缺陷(位错)位错强化
超细晶钢 细晶钢
如何形成超细晶的理论和技术?
高洁净度 夹杂物对钢材疲劳强度的影响
在疲劳极限时的强度 (108 周),σw/MPa
1200 1000
S35C,45C,55C,SMn438,443,SCM43 5,440,SCr440,SNC631
C
Si
S
a. 柱状晶发达
81.29
42.51
22.91
b. 等轴晶发达
90.21
71.34
55.98
国际共同开展新一代钢铁材料的研发
1997年日本提出超级钢概念(强度翻番、寿命翻番),随 后各国相继安排了类似目标的科研开发项目。
年份
国别
项目
备注
1997年
日本
“超级钢”基础研究
科技厅,十年项目
1997年
第三阶段:n明显降低,剩余少量形核位置时的转变变缓过程
❖ 临界核心尺寸小
△GD= 50 J/mol
r*= 0.064 µm
DIFT 是一个形核为主的过程
频数 晶粒尺寸( m)
Q235;加热到 900℃;770 ℃
0.3
应变= 0.7;不同时间驰豫;
0.2
0s 晶粒数559
3s 晶粒数679
5s 晶粒数600
→ 相变的自 由能变化
Temperature, C
1100
1050
C-1.50%Mn-0.46%Si steel
1000
950
AD3
900
850
800 750
Ae3
+
700
Ae3 10J/m ol 40J/m ol 70J/m ol 100J/m ol
炉外精炼复习专用资料
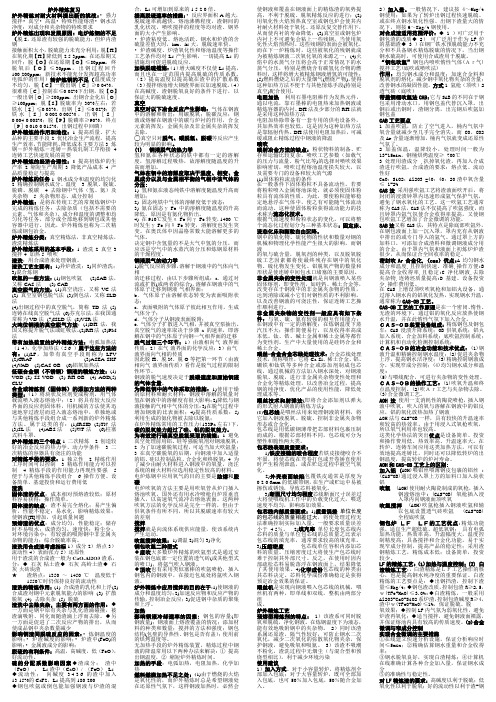
炉外精炼复习炉外精练对耐火材料提出新的挑战:•强力搅拌•真空•高温•特殊性能熔渣•钢水洁净度:对成分和夹杂物的特殊要求炉外精炼出现和发展原因:电炉炼钢的不足(脱S,还原渣有较强的脱硫能力,但炉内渣钢接触面积太小,脱硫能力未充分利用;脱【H】在氧化期【H】降低到2.5-3ppm,在还原期又回升;脱【O】在还原期【O】≤80ppm,终脱氧后【O】≤30ppm,出钢过程回升100-200ppm;新技术不能充分发挥超高功率电弧炉的作用)转炉炼钢的不足(温度成分不均匀,脱【C】一般出钢[C]≥0.04%,很难将[C]控制在≤0.02%下出钢,脱【O】一般出钢[O]≥500ppm,出钢合金化后[O]≥100ppm;脱【S】脱硫率为30%左右;若铁水[S]≤0.03%,出钢[S]≤0.02%;若铁水[S]0.002-0.005%,出钢[S]0.004-0.008%;脱【P】脱磷率≥90%,终点[P]0.010-0.015%,出钢过程中回磷)炉外精炼的作用和地位:1 提高质量、扩大品种的主要手段2 优化冶金生产流程,提高生产效率,节能降耗、降低成本主要方法3 炼钢-炉外精炼-连铸-热装轧制工序衔接4 连铸工艺快速发展的需要炉外精炼的经济合理性:1提高初炼炉的生产率2 缩短生产周期3 降低产品成本4 产品质量稳定与提高炉外精炼的任务1 钢水成分和温度的均匀化2 精确控制钢水成分、温度 3 脱氧、脱硫、脱磷、脱碳 4 去除钢中气体(氢、氮)及夹杂物 5 夹杂物形态、成分控制炉外精炼:是将在传统工艺的常规炼钢炉中完成的精炼任务:去除杂质(包括不需要的元素、气体和夹杂)、成分和温度的调整和均匀化等任务,部分或全部地移到钢包或其他容器中进行。
因此,炉外精炼也称为二次精炼或钢包冶金。
炉外精炼分类:真空精炼法,非真空精炼法,渣洗精炼法炉外精炼采用的基本手段:1 渣洗2 真空3 搅拌4 加热5 喷吹渣洗:用合成渣来处理钢液。
渣洗工艺主要有:1)异炉渣洗;2)同炉渣洗;3)混合炼钢吹氩的一些方法:(1)钢包吹氩(2)SAB法,又称CAS法(3) CAB真空脱气的方法:(1)真空浇注,又称VC法(2) 真空室钢包脱气法(3)倒包法,又称SLD 法(4)出钢过程中的真空脱气,简称TD法(5)连铸在线真空脱气法(6)芬克尔法,在我国通常称为VD法(7)ISLD法(8)VSR法大吨位钢液的真空脱气方法:(1)DH法,我国又称提升脱气法或虹吸法。
- 1、下载文档前请自行甄别文档内容的完整性,平台不提供额外的编辑、内容补充、找答案等附加服务。
- 2、"仅部分预览"的文档,不可在线预览部分如存在完整性等问题,可反馈申请退款(可完整预览的文档不适用该条件!)。
- 3、如文档侵犯您的权益,请联系客服反馈,我们会尽快为您处理(人工客服工作时间:9:00-18:30)。
超细晶化理论及技术是21世纪新一代钢铁材料的重要发展方向。
目前,工业生产和广泛应用的低合金钢的屈服强度约为400MPa,抗拉强度约为500MPa,晶粒尺寸约为lOpm。
长期研究和生产实践表明,具有高强度且有高韧度的钢铁材料是最理想的材料,晶粒细化处理是同时提高材料强度和韧度的最有效途径,因此世界各国研究者力争通过对低合金钢进行细晶化的研究,将低合金钢的屈服强度由目前的400MPa级提高到800MPa级,其核心理论和技术是实现钢材的超细晶(或超细组织)。
1997年4月,日本开始了“新世纪结构材料(或超级钢材料)”为期10年的研究计划,提出生产将现有钢材强度翻番和使用寿命翻番为目标的新一代钢材。
之后韩国在1998年启动了“21世纪高性能结构钢”,我国予1998年末确立启动了“新一代钢铁材料重大基础研究”项目(国家973项目),其目标是将现有的普碳钢和低合金钢的强度和寿命提高1倍,同时不降低钢的综合性能。
东亚相差不到1年,设立相同目标的研究项目带动了欧美各国钢铁界竞相参与和重视。
控制超细晶粒钢的组织而使钢强韧化的观点出发,对现有高强度低合金(HSLA)钢晶粒细化的理论和技术进行了探讨。
探讨高强度低合金钢的晶粒细化理论。
1.高强度低合金钢的晶粒细化理论:2.低合金高强钢最重要的力学性能指标是屈服强度GB和韧脆转变温度T。
对于新一代钢铁材料来说,提高其屈服强度民,降低其韧性转变温度T是研究和开发的重点。
提高钢铁材料强度的方法有:固溶强化、析出相强化、弥散强化、形变强化,细晶强化等。
钢铁材料提高强度的途径主要有4条Ⅲ:通过合金元素和间隙元素原子溶解于基体组织产生周溶强化通过加工变形增加位错密度造成钢材承载时位错运动困难(位错强化)通过晶粒细化使位错穿过晶界受阻产生细晶强化通过第二相(一般为M(C,N),析出相或弥散相)使位错发生弓弯和受阻产生析出强化。
各种强化机制的效果。
其中,细晶强化是唯一能同时提高强度和韧性的方法,其它强化方法得到的显微组织都存在强度提高而韧性下降的缺点。
细晶强化可用传统的Hall-Petch公式描述式中内摩擦力;足为常数,晶粒直径。
同时,晶粒尺寸与材料的塑性和韧性有着密切的关系,Petch根据断裂应力与晶粒直径的关系:α和β为常数,随着晶粒尺寸的逐步变小,屈服强度提高,韧转变温度降低。
研究工作表明:微米、亚微米级的钢铁材料,其强度和晶粒度仍服从Hall-Petch公式。
材料从传统的细晶(10mm或稍大)细化到1mm,其强度可提高l倍以上,并使钢的韧脆转变温度下降到200℃以下,显著地改善了钢的韧性。
Takakic6及其合作者的研究指出,具有低碳贝氏体或针状铁素体的低(微)合金钢若显微组织细化至2mm以下,强度就能翻番。
因此超细晶钢是将目前细晶钢的基体组织细化至微米及亚微米数量级。
微米及亚微米组织的性能特征。
2.分析高强度低合金钢的晶粒细化技术及其研究现状细化晶粒是控制金属材料组织结构的最重要、最基本的方法。
目前,获得细晶粒的方法有利用相变和再结晶的热处理(或形变热处理),钢液超速冷却,机械合金化,超细粒子烧结和非晶体结晶等。
形变热处理对晶粒细化极为有效,已以实验室规模获得了具有小于或等于超细晶组织的成块材料。
下面介绍几种重要的细化晶粒技术。
炉外精炼是把转炉、平炉或电炉中所炼的钢水移到另一个容器中(主要是钢包)进行精炼的过程。
也叫“二次炼钢”或钢包精炼。
炉外精炼把传统的炼钢分为两步。
(1)初炼:在氧化性气氛下进行炉料的熔化、脱磷、脱碳和主合金化。
(2)精炼:在真空、惰性气氛或可控气氛下进行脱氧、脱硫、去除夹杂、夹杂物变性、微调成分、控制钢水温度等。
从60年代以来,各种炉外精炼方法相继出现。
目前,全世界已有500多台炉外精炼设备在钢厂投入工业生产。
炉外精炼在现代化的钢铁生产流程中已成为一个不可缺少的环节。
尤其是炉外精炼与连铸相配合,是保证连铸生产顺行、扩大连铸品种、提高铸坯质量的重要手段。
在炼钢生产流程中,采用转炉(电炉)→炉外精炼→连铸已成为钢厂技术改造的普遍模式。
炉外精炼工艺特点和冶金作用各种炉外精炼方法的工艺各异,共同特点是:(1)有一个理想的精炼气氛,如真空、惰性气体或还原性气体。
(2)采用电磁力、吹惰性气体搅拌钢水。
(3)为补偿精炼过程中的钢水温降损失,采用电弧、等离子、化学法等加热方法。
炉外精炼主要是在钢包内完成的。
总的来说,有以下冶金作用:—钢水温度和成分均匀化。
—微调成分使成品钢的化学成分范围非常窄。
—把钢中硫含量降到非常低(如S<0.005%)。
—降低钢中的氢氮含量(如H<2ppm)。
—改变钢中夹杂物形态和组成。
—去除有害元素。
—调整温度。
钢包精炼方法不同,采用的工艺操作也不相同,所达到的冶金效果也不一样。
要结合生产的钢种、产品质量来选择合适的炉外精炼方法。
选择与连铸相匹配的炉外精炼的要求与连铸相匹配的钢包精炼,在于提高铸坯质量和保证连铸工艺的稳定性。
选择合适的炉外精炼方法是连铸钢水准备、提供合格质量钢水的重要手段。
为此结合产品质量要求,选择钢包精炼设备应满足以下基本要求:(1)调节钢水温度,达到连铸所要求的浇注温度。
(2)提高钢水清洁度,特别是减少钢中大型夹杂物的含量。
(3)降低钢中气体(如氢)含量。
(4)降低有害杂质(如硫、磷)含量。
(5)夹杂物变性作用,改善钢水流动性。
(6)减轻炼钢炉的冶炼负荷,缩短冶炼周期,提高生产率。
(7)钢包精炼炉成为炼钢炉和连铸机之间的一个“缓冲器”,平衡两者之间的生产节奏,有利于提高连铸机的生产率。
炼钢炉与连铸机之间装设了炉外精炼设备,可以达到以下目的:1)为连铸提供合格质量的钢水,改善连铸坯质量;2)协调炼钢与连铸之间的节奏,提高连铸机的生产率。
因此凡是有连铸机的工厂应选择合适的炉外精炼方法来准备钢水。
究竟采用哪种炉外精炼法取决于工厂条件、产品质量等。
应根据产品质量要求,建立不同的生产工艺流程:(1)对于电炉或超高功率电炉相配合连铸机,选择钢包精炼应满足合金比高的产品质量的要求。
如不锈钢可采用电炉—AOD炉一连铸、电炉一VOD炉一连铸,轴承钢采用电炉一钢包炉(如LF、SKF)一连铸。
(2)对于大型转炉相配合的板坯、大方坯、圆坯连铸机,要提供优质钢水,生产高质量的铸坯。
采用转炉一RH一连铸、转炉一RH+KIP一连铸。
生产超低碳(碳小于0.1%)或超低硫(硫小于0.005%)可采用LF炉与真空处理并用,可得到最佳效果。
(3)对于小型转炉,相配合小方坯、矩形坯连铸机,以生产普碳钢为主,一般采用钢包吹氩或辅以钢包喂丝技术,基本上能满足连铸工艺和铸坯质量要求。
与连铸相匹配常用的炉外精炼法有:真空处理(如RH、DH),钢包精炼炉(如LF法、ASEA —SKF法、VOD法等),钢包钙处理(如TN法、KIP法、喂钙丝法等)。
与连铸相配合的RH(或DH)真空处理法的特点RH是目前广泛应用的一种真空处理法。
其设备由真空室与抽气装置组成。
真空室下有吸取钢水的上升管和排出钢水的下降管。
脱气处理时,首先将两根管子插入钢包内钢水面以下150~300mm。
抽真空时钢水在大气压力作用下进入真空室。
同时在上升管内吹入氩气,因钢水内充满氩气泡,液体密度减小而使钢水向上流动进入真空室,而下降管内钢水密度大而下降,返回钢包内。
因此连续反复循环,使钢水在真空室脱气。
RH的作用是脱氢、脱氧、脱碳、减少钢中夹杂物、均匀钢水温度和微调成分等。
RH真空处理法已向多功能方向发展,如RH真空室吹氧以生产超低碳钢(碳小于0.003%),开发了RH—OB、RH—KTB法。
武钢、宝钢均采用转炉一RH一连铸工艺流程生产板坯。
目前,DH真空处理法用得较少。
与连铸相配合的钢包精炼的方法目前广泛采用的钢包精炼法有以下几种: (1)LF钢包精炼炉该法主要特点是:有3根石墨电极,电弧产生在钢包钢水面上的炉渣中,进行“埋弧精炼和加热”。
处理时添加合成渣脱硫,钢包底部吹氩搅拌钢水,可以均匀温度和成分,促使夹杂物上浮排除。
这是一种设备投资省、精炼效果好的炉外精炼法。
LF炉已成为电炉与连铸之间的一个重要设备。
LF炉具有加热功能,可使电炉出钢温度降低120℃。
缩短冶炼时间,提高电炉生产率20%。
经过LF炉处理使连铸钢水温度波动减少到±2℃,有利于连铸生产的稳定性。
我国不少电炉厂建成了电炉一LF炉一连铸以生产方坯、圆坯的生产流程。
(2)VOD炉VOD炉主要用于冶炼低碳不锈钢,在钢包炉内真空条件下吹氧脱碳(脱碳量为0.3~0.6%)。
采用消耗式喷枪或水冷喷枪吹氧。
VOD炉没有热源,一般不用造渣精炼。
上钢三厂已建成电炉一VOD一板坯连铸机流程生产不锈钢,年产量达10万t/年。
与连铸相配合的喷射冶金技术的特点喷射冶金是以压缩气体(如氩气)作为载体,把各类精炼粉剂(如石灰粉、Si-Ca粉等)喷射到钢包深部,利用气体的搅拌作用增加粉剂和钢水的接触面积,从而改善化学反应的动力学条件。
这样可以快速脱硫、脱氧、脱磷、提高合金的收得率和钢的纯净度。
与连铸相配合的钢包喷粉技术主要解决以下问题:(1)改善钢水的可浇性和中间包水口的堵塞。
浇注含铝钢,钢水中Al2O3夹杂呈固态串簇状分布,使钢水发粘是水口堵塞的根源。
在钢包内喷吹Si-Ca粉,使CaO与Al2O3结合成铝酸钙(12CaO·7Al2O3),在钢水中呈液态球形而上浮,解决了水口堵塞。
(2)降低钢水中含硫量。
连铸用于生产石油管线和船板的坯,要求钢中硫小于0.005%,可在钢包喷吹Ca—Si粉、石灰粉来生产低硫钢。
(3)夹杂物变性处理以提高钢的清洁度。
如16Mn钢经喷粉处理后,钢中Al2O3以及MnS夹杂物明显降低,Al2O3降低67%,MnS降低66%。
且夹杂物呈细小均匀分布,有利于钢材力学性能的改善。
目前将喷射冶金和真空处理相结合,是一种有吸引力的炉外精炼技术。
如将LF、VOD、RH 等精炼设备与喷射冶金相结合组成新的精炼工艺,可进一步提高钢水精炼效果。
与连铸相配合的喂线技术的特点向钢水中加钙不仅改善连铸钢水的可浇性,而且可改善钢的质量。
目前向钢水喂钙丝已成为向钢水加钙的有效技术,可取代喷吹Si-Ca粉技术。
以80~300m/min的速度把钙线喂入钢包深部,在1600℃高温下,钙在1~3S内就可熔化,钙滴或钙气泡向上移动时间较长,与钢水更能有效的起反应。
比喷吹Si-Ca粉效果要好。
由于金属钙是非常活泼的元素,在1600℃能很快的气化,所以出钢时若采用通常方法把钙加入钢包,钙蒸发会引起激烈的沸腾喷溅,钙烧损大,效率低。
为此,采用特殊加工方法将CaSi粉或CaSi+A1按比例混合作为芯部材料,外面用0.2mm厚的薄钢带包覆起来,并将粉剂压实,制成6~10mm不同直径的复合包线。
包线可做成圆形或矩形(如12×6mm)。