ANSYS优化揭密
ANSYS优化设计步骤解析
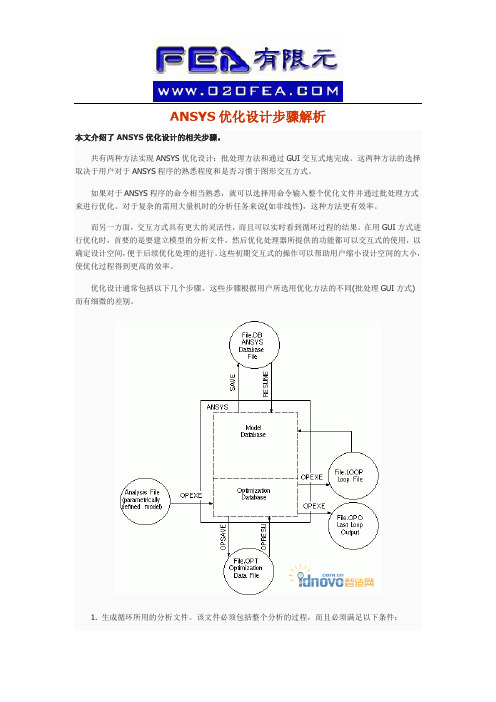
ANSYS优化设计步骤解析本文介绍了ANSYS优化设计的相关步骤。
共有两种方法实现ANSYS优化设计:批处理方法和通过GUI交互式地完成。
这两种方法的选择取决于用户对于ANSYS程序的熟悉程度和是否习惯于图形交互方式。
如果对于ANSYS程序的命令相当熟悉,就可以选择用命令输入整个优化文件并通过批处理方式来进行优化。
对于复杂的需用大量机时的分析任务来说(如非线性),这种方法更有效率。
而另一方面,交互方式具有更大的灵活性,而且可以实时看到循环过程的结果。
在用GUI方式进行优化时,首要的是要建立模型的分析文件,然后优化处理器所提供的功能都可以交互式的使用,以确定设计空间,便于后续优化处理的进行。
这些初期交互式的操作可以帮助用户缩小设计空间的大小,使优化过程得到更高的效率。
优化设计通常包括以下几个步骤,这些步骤根据用户所选用优化方法的不同(批处理GUI方式)而有细微的差别。
1. 生成循环所用的分析文件。
该文件必须包括整个分析的过程,而且必须满足以下条件:a. 参数化建立模型(PREP7)。
b. 求解(SOLUTION)。
c. 提取并指定状态变量和目标函数(POST1/POST26)。
2. 在ANSYS数据库里建立与分析文件中变量相对应的参数。
这一步是标准的做法,但不是必须的(BEGIN或OPT)。
3. 进入OPT,指定分析文件(OPT)。
4. 声明优化变量。
5. 选择优化工具或优化方法。
6. 指定优化循环控制方式。
7. 进行优化分析。
8. 查看设计序列结果(OPT)和后处理(POST1/POST26)。
优化设计步骤的细节在下面列出。
批处理方式和交互方式的区别也同时指出。
第一步:生成分析文件分析文件生成是ANSYS优化设计过程中的关键部分。
ANSYS程序运用分析文件构造循环文件,进行循环分析。
分析文件中可以包括ANSYS提供的任意分析类型(结构,热,电磁等,线性或非线性)。
(注:ANSYS/LS-DYNA的显式分析不能进行优化。
ANSYS高级分析:优化设计(二)
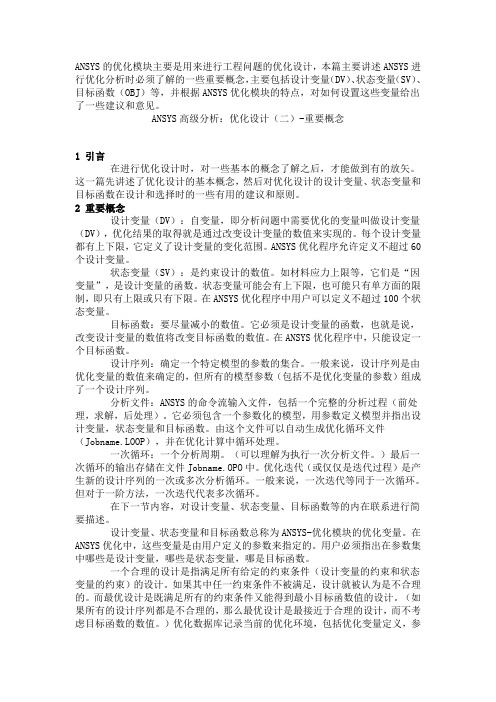
ANSYS的优化模块主要是用来进行工程问题的优化设计,本篇主要讲述ANSYS进行优化分析时必须了解的一些重要概念,主要包括设计变量(DV)、状态变量(SV)、目标函数(OBJ)等,并根据ANSYS优化模块的特点,对如何设置这些变量给出了一些建议和意见。
ANSYS高级分析:优化设计(二)-重要概念1 引言在进行优化设计时,对一些基本的概念了解之后,才能做到有的放矢。
这一篇先讲述了优化设计的基本概念,然后对优化设计的设计变量、状态变量和目标函数在设计和选择时的一些有用的建议和原则。
2 重要概念设计变量(DV):自变量,即分析问题中需要优化的变量叫做设计变量(DV),优化结果的取得就是通过改变设计变量的数值来实现的。
每个设计变量都有上下限,它定义了设计变量的变化范围。
ANSYS优化程序允许定义不超过60个设计变量。
状态变量(SV):是约束设计的数值。
如材料应力上限等,它们是“因变量”,是设计变量的函数。
状态变量可能会有上下限,也可能只有单方面的限制,即只有上限或只有下限。
在ANSYS优化程序中用户可以定义不超过100个状态变量。
目标函数:要尽量减小的数值。
它必须是设计变量的函数,也就是说,改变设计变量的数值将改变目标函数的数值。
在ANSYS优化程序中,只能设定一个目标函数。
设计序列:确定一个特定模型的参数的集合。
一般来说,设计序列是由优化变量的数值来确定的,但所有的模型参数(包括不是优化变量的参数)组成了一个设计序列。
分析文件:ANSYS的命令流输入文件,包括一个完整的分析过程(前处理,求解,后处理)。
它必须包含一个参数化的模型,用参数定义模型并指出设计变量,状态变量和目标函数。
由这个文件可以自动生成优化循环文件(Jobname.LOOP),并在优化计算中循环处理。
一次循环:一个分析周期。
(可以理解为执行一次分析文件。
)最后一次循环的输出存储在文件Jobname.OPO中。
优化迭代(或仅仅是迭代过程)是产生新的设计序列的一次或多次分析循环。
学会使用AnsysWorkbench进行有限元分析和结构优化
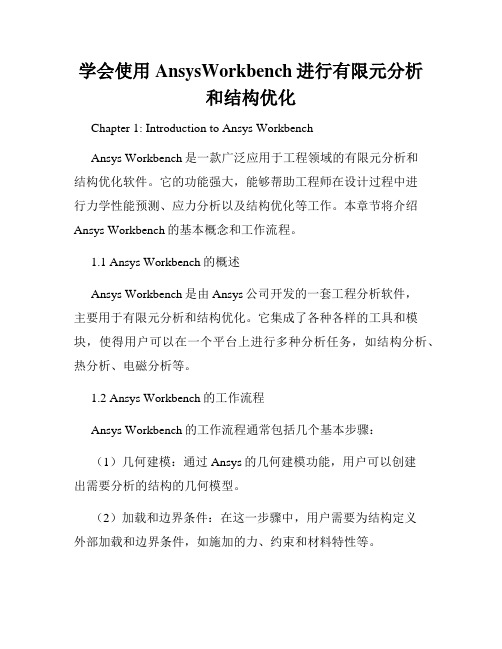
学会使用AnsysWorkbench进行有限元分析和结构优化Chapter 1: Introduction to Ansys WorkbenchAnsys Workbench是一款广泛应用于工程领域的有限元分析和结构优化软件。
它的功能强大,能够帮助工程师在设计过程中进行力学性能预测、应力分析以及结构优化等工作。
本章节将介绍Ansys Workbench的基本概念和工作流程。
1.1 Ansys Workbench的概述Ansys Workbench是由Ansys公司开发的一套工程分析软件,主要用于有限元分析和结构优化。
它集成了各种各样的工具和模块,使得用户可以在一个平台上进行多种分析任务,如结构分析、热分析、电磁分析等。
1.2 Ansys Workbench的工作流程Ansys Workbench的工作流程通常包括几个基本步骤:(1)几何建模:通过Ansys的几何建模功能,用户可以创建出需要分析的结构的几何模型。
(2)加载和边界条件:在这一步骤中,用户需要为结构定义外部加载和边界条件,如施加的力、约束和材料特性等。
(3)网格生成:网格生成是有限元分析的一个关键步骤。
在这一步骤中,Ansys Workbench会将几何模型离散化为有限元网格,以便进行分析计算。
(4)材料属性和模型:用户需要为分析定义合适的材料属性,如弹性模量、泊松比等。
此外,用户还可以选择适合的分析模型,如静力学、动力学等。
(5)求解器设置:在这一步骤中,用户需要选择适当的求解器和设置求解参数,以便进行分析计算。
(6)结果后处理:在完成分析计算后,用户可以对计算结果进行后处理,如产生应力、位移和变形等结果图表。
Chapter 2: Finite Element Analysis with Ansys Workbench本章将介绍如何使用Ansys Workbench进行有限元分析。
我们将通过一个简单的示例,演示有限元分析的基本步骤和方法。
ANSYS优化设计设计优化技术

ANSYS优化设计设计优化技术ANSYS优化设计是一种基于计算机仿真和数值分析的设计优化方法。
它利用ANSYS软件平台上的多物理场问题求解器和优化算法,对设计进行高效、全面的优化。
通过不断迭代求解和更新设计参数,最终达到设计性能的最优化。
ANSYS优化设计涵盖了多个领域的设计问题,例如结构优化、流体优化、电磁优化等。
在结构优化中,可以通过调整材料属性、几何形状和连接方式等设计参数,使结构在承受最大载荷的同时,尽可能地减少重量和成本。
在流体优化中,可以通过调整流体流动的速度、方向和阻力等设计参数,使流体系统的效率和性能得到最大化。
在电磁优化中,可以通过调整电磁场的分布和强度等设计参数,实现电磁设备的最佳性能。
ANSYS优化设计的核心是优化算法。
ANSYS提供了多种优化算法,包括遗传算法、进化算法、粒子群算法等。
这些算法可以根据设计问题的特点和约束条件选择合适的优化策略,并通过不断地试验和调整设计参数,逐步优化设计方案。
优化设计的目标通常是在一定的约束条件下,使设计满足最大化性能、最小化成本或达到特定的指标要求。
使用ANSYS进行优化设计需要以下几个步骤。
首先,确定优化目标和约束条件。
这包括定义设计的性能要求、约束条件、可变参数范围等。
其次,建立数学模型。
将设计问题转化为数学方程组,并确定相关参数之间的关系。
然后,选择合适的优化算法。
根据设计问题的特点和约束条件,选择合适的优化算法进行求解。
最后,进行多次迭代求解。
根据优化算法的要求,通过不断地更新设计参数,逐步接近最优解。
ANSYS优化设计具有以下优势。
首先,通过仿真和数值分析,可以提前发现并解决设计中的问题,减少试错成本。
其次,可以在多个设计方案中比较和选择最优解,提高设计性能。
第三,使用计算机仿真和优化算法,可以大大缩短设计周期,提高设计效率。
最后,ANSYS提供了丰富的优化设计工具和资源,使设计工程师可以更好地应用和掌握优化设计技术。
总之,ANSYS优化设计是一种基于计算机仿真和数值分析的设计优化方法。
基于ANSYS的机械结构强度分析与优化研究

基于ANSYS的机械结构强度分析与优化研究随着现代工程需求的不断增长,对机械结构强度和可靠性的要求也越来越高。
为了满足这一需求,研究人员广泛使用ANSYS软件来进行机械结构的强度分析与优化研究。
本文将介绍基于ANSYS的机械结构强度分析与优化的研究方法和技巧。
一、研究背景和意义机械结构的强度分析是评估其工作状态下可承受的载荷和变形的能力,是确保机械结构安全可靠运行的基础。
而优化设计则是在满足安全性的前提下,设计出更加轻量化和高效的结构,以降低成本和提高性能。
因此,基于ANSYS的机械结构强度分析与优化研究对于工程领域具有重要的意义。
二、ANSYS软件介绍ANSYS是一款广泛应用于工程计算领域的有限元法软件。
它可以模拟和分析各种不同材料和结构类型的力学行为,并提供详细的应力、应变和变形等信息。
利用ANSYS软件,可以进行静力学分析、动力学分析、疲劳分析等多种工程分析。
三、机械结构强度分析流程1. 几何建模:使用ANSYS提供的建模工具,创建机械结构的几何模型。
可以通过绘图、导入CAD文件等方式完成。
2. 材料属性定义:根据实际情况,设置机械结构材料的机械性能参数,包括弹性模量、泊松比、屈服强度等。
3. 网格划分:将几何模型划分成有限元网格,需要注意网格密度和质量的合理选择,以提高计算结果的精度和准确性。
4. 载荷和边界条件定义:根据实际工况对机械结构施加载荷和边界条件。
可以设置静载荷、动载荷、温度载荷等。
5. 强度分析:运行ANSYS计算求解器,进行机械结构的强度分析。
可以获得应力、应变、变形等结果,以评估结构的强度和可靠性。
6. 结果后处理:通过ANSYS的后处理工具,对计算结果进行可视化和分析。
可以生成应力云图、应变曲线等,为结构优化提供依据。
四、机械结构优化方法1. 参数优化:通过改变机械结构的设计参数,如材料厚度、连接方式等,以满足给定的约束条件和性能要求。
2. 拓扑优化:在事先给定的设计空间中,通过修改结构的拓扑形状来实现结构的优化设计。
基于ANSYS的壳体优化

基于ANSYS的壳体优化基于ANSYS的壳体优化壳体优化是一种基于ANSYS的先进技术,用于改进和优化结构的性能和效率。
下面是一步一步的思路,介绍如何利用ANSYS进行壳体优化。
第一步:定义问题在进行壳体优化之前,首先需要明确问题的定义和目标。
例如,我们可能需要优化壳体的强度,减少应力集中区域,或者改善壳体的刚度和振动特性等。
确定问题定义和目标后,我们可以开始进行后续的优化工作。
第二步:建立壳体模型在ANSYS软件中,我们可以使用CAD软件创建壳体的几何模型,或者导入现有的模型。
然后,我们需要将几何模型导入到ANSYS中进行网格划分。
网格划分的质量对后续的计算和分析结果有很大的影响,因此需要仔细选择合适的网格划分方法和参数。
第三步:定义边界条件在进行壳体分析之前,需要定义边界条件。
边界条件包括约束条件和加载条件。
约束条件可以是固定边界、滑动边界或者自由边界等。
加载条件可以是压力、力或温度等。
根据具体问题的要求,我们需要合理地定义边界条件,以模拟真实工作环境。
第四步:进行静态分析一旦模型和边界条件准备好,我们可以进行静态分析。
静态分析是根据给定的边界条件和加载条件,计算壳体的应力和位移分布。
通过观察分析结果,我们可以发现壳体的强度和刚度状况,进而找到可能需要改进的区域。
第五步:进行优化设计在静态分析的基础上,我们可以利用ANSYS的优化功能进行壳体的优化设计。
优化设计的目标是找到最佳的材料分布和几何形状,以满足设计要求。
ANSYS提供了多种优化算法,例如拓扑优化、参数优化和拟合优化等。
我们可以根据具体问题的需求选择合适的优化算法和参数。
第六步:验证和调整优化设计的结果可能需要进行验证和调整。
我们可以利用ANSYS进行二次分析,验证优化设计的性能和效果。
如果结果不符合要求,我们可以对优化参数进行调整,并进行多次优化设计。
这个过程可以迭代进行,直到满足设计要求为止。
最后,通过以上的步骤,我们可以利用基于ANSYS的壳体优化技术,改进和优化壳体的性能和效率。
ANSYS高级分析-优化设计(一)

ANSYS高级分析-优化设计(一)本篇作为ANSYS最常用也是最有用的高级分析技术优化设计技术的开篇,主要从概念上讲述ANSYS优化设计以及在进行ANSYS优化设计分析时通用的基本步骤和考虑方法(本篇所讲述优化分析同样是基于APDL工具,其它优化设计技术具体实现过程随着对优化设计的逐渐深入会逐步描述)。
1 前言优化设计是一种寻找确定最优设计方案的技术。
所谓“最优设计”,指的是一种方案可以满足所有的设计要求,而且所需的支出(如重量,面积,体积,应力,费用等)最小。
也就是说,最优设计方案就是一个最有效率的方案。
设计方案的任何方面都是可以优化的,比如说:尺寸(如厚度),形状(如过渡圆角的大小),支撑位置,制造费用,自然频率,材料特性等。
实际上,因为ANSYS具有专业的和强大的分析能力,具有开放的使用环境,所以所有可以参数化的ANSYS选项都可以作优化设计。
ANSYS参数化设计语言APDL用建立智能分析的手段为用户提供了自动循环的功能,也就是说,程序的输入可设定为根据指定的函数、变量以及选出的分析标准决定输入的形式。
APDL允许复杂的数据输入,使用户实际上对任何设计或分析有控制权。
例如尺寸、材料、载荷、约束位置和网格密度等。
APDL扩展了传统有限元分析之外的能力,并扩展了更高级运算,包括灵敏度研究、零件库参数化建模,设计修改和设计优化。
APDL是一种为ANSYS 二次开发专门设计开发的解释性文本语言,其内容包括参数、数组参数、表达式和函数、分支和循环、重复功能和缩写以及宏和用户程序等。
2 优化设计步骤基于APDL的参数化设计的方法采用ANSYS的批处理方法进行优化的,其主要的优化设计过程通常包括以下几个步骤,这些步骤根据用户所选用优化方法的不同(批处理GUI 方式)而有细微的差别。
生成分析文件:生成分析文件与通常的ANSYS分析并没有很大的不同,唯一的区别就是:优化的分析文件必须是参数化的。
也就是说,必须定义一些参量,至少要把所有的设计变量,状态变量和目标变量定义为参量形式。
ANSYSWorkbench优化设计技术系列讲座(一):设计探索与优化技术概述

ANSYSWorkbench优化设计技术系列讲座(一):设计探索与优化技术概述ANSYS Workbench(以下简称WB)是ANSYS公司开发的仿真应用集成工作平台,ANSYS WB环境提供了参数(Parameter)和设计点(DesignPoint)的管理功能。
集成于WB中的ANSYS DesignXplorer模块(以下简称DX)则提供了强大的设计探索及优化分析功能。
基于WB以及DX的分析结果,设计人员将能够识别影响结构性能的关键变量、确定结构的性能响应同设计变量之间的内在关系、找到满足相关约束条件下的优化设计方案。
WB提供的Parameter Set功能可以实现分析项目中所有参数的管理,参数包括输入参数、输出参数以及用户定义参数等类型。
在Parameter Set管理页面下的“Table of DesignPoints”列表则列出了一系列输入变量的不同取值和对应的输出变量的数值表,即:设计点列表。
WB中的设计点(Design Points),就是一组给定的输入参数取值及其相应的输出参数取值,设计点实际上代表了一种设计方案。
输入参数在其取值范围内变化和组合,可以有很多的设计点,这些设计点就构成成了一个设计空间。
不同设计方案可以通过参数平行轴图来描述。
利用设计点列表可以对设计点进行管理和选择更新设计点,或者选择鼠标右键菜单“Copy inputs to Current”将某个设计点复制到当前设计方案,这样就可以在计算后在后处理程序里用图形查看此设计点的各种响应。
实际上,WB的设计点功能通常是与DX功能结合使用。
集成于WB中的DX提供了更为全面的设计空间探索工具和功能,也是本章将重点介绍的内容。
DX提供的各种分析工具都是基于参数而展开,参数相关性分析用于研究哪些输入变量对输出变量影响最大,基于试验设计的设计点采样和响应面技术可以全方位地揭示输出变量关于输入变量的变化规律,目标驱动优化技术则基于各种优化方法来提供最佳备选设计方案;此外,DX还提供了用于确定输入参数的不确定性(随机性)对输出参数影响的6-sigma分析工具。
- 1、下载文档前请自行甄别文档内容的完整性,平台不提供额外的编辑、内容补充、找答案等附加服务。
- 2、"仅部分预览"的文档,不可在线预览部分如存在完整性等问题,可反馈申请退款(可完整预览的文档不适用该条件!)。
- 3、如文档侵犯您的权益,请联系客服反馈,我们会尽快为您处理(人工客服工作时间:9:00-18:30)。
ANSYS优化揭密1 认识 ANSYS 优化模块1.1 什么时候需要它的帮忙什么是 ANSYS 优化?以普通的水杯为例?圆形底面,上面加盖的那一种。
仔细观察一下,你会发现比较老式的此类水杯有一个共同特点:底面直径=水杯高度。
图 1 水杯的简化模型为什么是这样呢?因为只有满足这个条件,才能在原料耗费最少的情况下使杯子的容积最大:在材料一定的情况下,如果水杯的底面积大,其高度必然就要小;如果高度变大了,底面积又会变小,如何调和这两者之间的矛盾?其实这恰恰就反应了一个完整的优化过程。
在这里,一个水杯的材料是一定的,所要优化的变量就是杯子底面的半径 r 和杯子的高度 h,在 ANSYS 的优化模块里面把这些需要优化的变量叫做设计变量(DV);优化的目标是要使整个水杯的容积最大,这个目标在 ANSYS 的优化过程里叫目标函数(OBJ);再者,对设计变量的优化有一定的限制条件,比如说整个杯子的材料不变,这些限制条件在 ANSYS 的优化模块中用状态变量(SV)来控制。
下面我们就来看看 ANSYS 中怎么通过设定 DV、SV 和 OBJ,并利用优化模块求解以上问题。
首先参数化建立一个分析文件(假设为 volu.inp),水杯初始半径 R=1,高度 H=1(DV)。
由于水杯材料直接和水杯的表面积有关系,这里假设水杯表面积不能大于 100,这样就有 S=2πRH+2πR2<100(SV),水杯的容积为 V=πR2H(OBJ)。
File:volu.inpR=1H=1S=2*3.14*R*H+2*3.14*R*RV=10000/(3.14*R*R*H)然后再建一个优化分析文件(假设为 optvolu.inp),设定优化变量,并求解。
File:optvolu.inp/clear,nostart/input,volu,inp/optopanl,volu,inpopvar,R,dv,1,10,1e-2opvar,H,dv,1,10,1e-2opvar,S,sv,,100,1e-2opvar,V,obj,,,1e-2opkeep,onoptype,subpopsave,optvolu,opt0opexec最后,打开 Ansys,输入“/input,optvolu,in p”,开始优化。
图 2 ANSYS 优化过程图图 3 优化结果 1优化过程结束后,优化的结果如图3:图 3 中带*的 SET22 是最优解,由此可以看出,要想在表面积一定的情况下使水杯容积最大,的确有这样一个规律H=D=2*R。
这个结论可以用求极值的方法演算一下,一定会得到相同的结果(注:原来那些无盖的搪瓷盆有一个规律是H=R,也是为了满足瓷盆容积最大)。
ANSYS的优化模块是用来求解工程分析中的优化例子的,但上面一个例子说明即使这样对于工程毫无关系的纯数学极值问题,也能够轻松求解。
不过在细节处会有一些技巧,后面再仔细分析(其实用 ANSYS 的优化模块完全能解决数学上比较复杂的极值问题,不过有了Matlab、Mathematica之后,就不太经常用ANSYS求解这类问题了)。
1.2 ANSYS 优化设计基础前面的例子,说明了 ANSYS 的基本优化过程。
在这一节中,我们结合这个例子来说明优化模块中的一些概念。
1.2.1 优化模块中的三大变量:设计变量(DV):即自变量。
例子中的 opvar,R,dv,1,10,1e-2 就是用来定义一个设计变量R,其上限为10,下限为1,公差为 10-2(公差和优化过程的收敛有关)。
ANSYS 优化模块中允许定义不超过60个设计变量。
状态变量(SV):用来体现优化的边界条件,是设计变量的函数。
例子里面opvar,S,sv,,100,1e-2 就是定义了一个状态变量 S,它的上限为100,无下限,公差为10-2。
从文件 volu.inp 中可以看到,S=2*3.14*R*H+2*3.14*R*R。
可见,定义这样一个状态变量,即是限制水杯的表面积不大于 100。
在 ANSYS 优化模块中,用户可以定义不超过 100 个状态变量。
目标函数(OBJ):最终的优化目标。
它必须是设计变量的函数,而且只能求其最小值。
volu.inp里面的目标函数为 V=10000/(3.14*R*R*H),为了把求最大体积转化为求最小值,只好对它求倒数了;如果知道目标函数的上限,还可以用一个大数减目标函数的方法来转换(例如 V=X-3.14*R*R *H,其中 X 为较大数,保证 V 值大于 0)。
例子中 opvar,V,obj,,,1e-2 就是定义了一个目标函数 V,它的公差是 10-2。
1.2.2 ANSYS 优化模块中的两种求解模式ANSYS 优化模块的求解有两种运行模式,一种是在 GUI 方式下运行,即在打开 ANSYS的分析界面后进行分析;另一种是 Batch 模式,无需打开 ANSYS分析界面,在后台运行求解。
前面例子的运行过程其实就是一个典型的 GUI 方式体现,它涉及到两个重要的文件:一个是类似 volu.inp 的ANSYS分析文件。
如果是一个工程问题,该文件中应该有参数定义、参数建模、求解、结果提取、目标函数赋值的一个全过程(由于优化求解是一个不断迭代的过程,ANSYS 分析文件其实是包涵了一个完整的循环)。
另一个文件是类似 optvolu.inp 的优化控制文件,即定义三大变量、优化方式、优化控制等的语句。
有人可能会有疑问:既然ANSYS 分析文件包涵了一个完整的循环,但是整个优化过程中是要求设计变量不断改变的,每次循环都有一个参数重定义的过程,不会使设计变量恢复初始值吗?这一点不用担心,正是由于有了另一个优化控制文件,优化过程只在第一次进行完全的参数定义工作,在后续循环中,优化控制文件中声明的设计变量定义将被忽略。
有了这样两个文件,在命令窗口把优化控制文件输入进去(其中的 opanl 命令会自动调用指定的 ANSYS 分析文件),就可以完成整个优化过程。
以上说明的是完全使用命令流的 GUI 方式。
另一种方式是后台运行的 Batch 方式,它只需要一个输入命令流文件(batch文件)。
该文件可以通过把 GUI 方式下 ANSYS 分析文件和优化控制文件合并得到。
不过有几个需要注意的地方:(1)需要把 optanl 语句去掉。
因为在 batch 文件中,不需要提供 ANSYS 分析文件名字,系统默认 batch 文件中/opt 语句以前的所有部分为 ANSYS 分析文件内容;(2)以前为防止在 GUI 方式下的重新定义错误而引入的一些语句,如/cle,nostart,需要去除。
上述例子经过合并、处理,就可以得到 Batch 方式下需要的 batch 文件 batch.inp:File:batch.inpR=1H=1S=2*3.14*R*H+2*3.14*R*RV=10000/(3.14*R*R*H)/optopvar,R,dv,1,10,1e-2opvar,H,dv,1,10,1e-2opvar,S,sv,,100,1e-2opvar,V,obj,,,1e-2opkeep,onoptype,subpopsave,optvolu,opt0opexe假定 batch.inp 在目录 bvolu 下,在 cmd 命令行方式下,进入 bvolu 目录,执行命令:ansys61 -b -j bvolu -p ane3flds -i batch.inp –o output.txt命令中-b 参数指定用 batch 模式求解;-j bvolu 参数指定该求解默认工作名字为bvolu (不指定就默认为file);-p ane3flds 参数指定使用 ANSYS/Multiphysics/LS-DYNA 求解器;-i batch.inp 参数指定输入 batch 文件为 batch.inp;-o output.txt 参数指定把输出导向到output.txt 中,便于查看过程纠错。
运行结束后,可以从 output.txt 文件中看到最优解。
文件 output.txt 中的一部分数据:>>>>>>SOLUTION HAS CONVERGED TO POSSIBLE OPTIMUM<<<<<<(BASED ON DV TOLERANCES BETWEEN FINAL TWO DESIGNS)FINAL V ARIABLES ARESET 22(FEASIBLE)S (SV) 99.997R (DV) 2.2851H (DV) 4.6830V (OBJ) 130.23其结果与用 GUI 方式求解完全一样,生成的 bvolu.opt 文件中也有最优解的信息,同时还能看到求解整个参数的迭代求解过程。
1.2.3 ANSYS 的优化方法和收敛准则例子中优化控制文件里面的优化命令,还有 opkeep,on(用来要求保留最优解的 DB),opexec(执行优化),剩下重要的命令就只有optype了,这个命令指定 ANSYS 优化中使用的优化方法。
优化方法发展到今天可说是形形色色,比较完善了。
虽然 ANSYS 的优化模块中只支持两种优化方法,但是这两种优化方法对绝大多数的工程问题已经足够了。
另外,ANSYS 还有用户优化接口,方便用户使用适合于自己问题的优化方法。
看看例子中的命令“optype,subp”,这里指定的是第一种通用的函数逼进优化方法。
该方法的本质是采用最小二乘逼进,求取一个函数面来拟和解空间,然后再对该函数面求极值。
这是一种普适的优化方法,不容易陷入局部极值点,但优化精度一般不是很高,因此多用做粗优化的手段。
针对第一种优化方法的缺点进行改进,产生了另外一种方法,叫做梯度寻优。
如果说第一种方法是 C0 阶、大范围普适的粗优化方法;那么第二种方法就是C1阶、局部寻优的精优化方法。
一般来说,一个比较负责的问题都需要同时采用两种优化方法:先用函数逼进的第一类方法初步求得最优解基本位置,然后再采用梯度寻优对最优解的位置进行更精确的确定(注:如果用第二类梯度寻优进行优化,不仅时间消耗长,还可能陷入局部最小点,因此通常的问题都建议使用 0 阶函数逼进优化 subp)。
前面讨论了 ANSYS 的两种优化方法。
ANSYS 进行优化计算,都是一个不断迭代的过程,有时候优化的结束条件比优化过程本身更加重要。
下面我们就来谈谈决定优化过程结束的条件:优化准则。
假设 F j、X j 和 F j-1、X j-1 分别为目标函数、设计变量第 j 次迭代和第 j-1 次迭代的结果(Xj 为矢量),F b和X b 分别是当前的最优目标函数和其相应的设计变量值。