注塑充模过程中温度场的数值分析
注塑工艺温度(3篇)
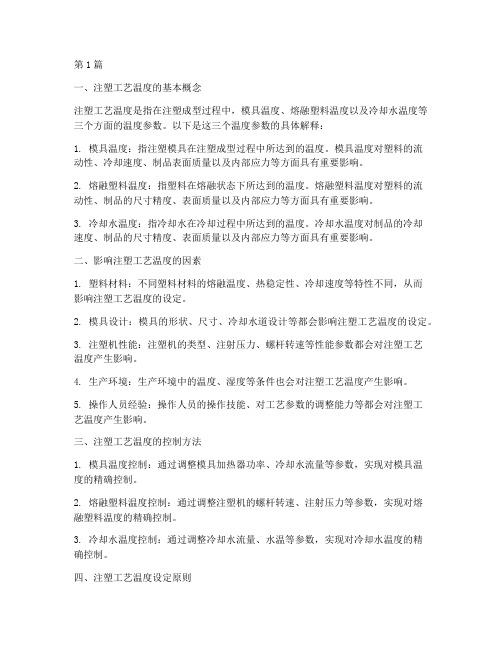
第1篇一、注塑工艺温度的基本概念注塑工艺温度是指在注塑成型过程中,模具温度、熔融塑料温度以及冷却水温度等三个方面的温度参数。
以下是这三个温度参数的具体解释:1. 模具温度:指注塑模具在注塑成型过程中所达到的温度。
模具温度对塑料的流动性、冷却速度、制品表面质量以及内部应力等方面具有重要影响。
2. 熔融塑料温度:指塑料在熔融状态下所达到的温度。
熔融塑料温度对塑料的流动性、制品的尺寸精度、表面质量以及内部应力等方面具有重要影响。
3. 冷却水温度:指冷却水在冷却过程中所达到的温度。
冷却水温度对制品的冷却速度、制品的尺寸精度、表面质量以及内部应力等方面具有重要影响。
二、影响注塑工艺温度的因素1. 塑料材料:不同塑料材料的熔融温度、热稳定性、冷却速度等特性不同,从而影响注塑工艺温度的设定。
2. 模具设计:模具的形状、尺寸、冷却水道设计等都会影响注塑工艺温度的设定。
3. 注塑机性能:注塑机的类型、注射压力、螺杆转速等性能参数都会对注塑工艺温度产生影响。
4. 生产环境:生产环境中的温度、湿度等条件也会对注塑工艺温度产生影响。
5. 操作人员经验:操作人员的操作技能、对工艺参数的调整能力等都会对注塑工艺温度产生影响。
三、注塑工艺温度的控制方法1. 模具温度控制:通过调整模具加热器功率、冷却水流量等参数,实现对模具温度的精确控制。
2. 熔融塑料温度控制:通过调整注塑机的螺杆转速、注射压力等参数,实现对熔融塑料温度的精确控制。
3. 冷却水温度控制:通过调整冷却水流量、水温等参数,实现对冷却水温度的精确控制。
四、注塑工艺温度设定原则1. 确保塑料材料在熔融状态下具有良好的流动性,避免因温度过低导致注塑不良。
2. 在保证制品尺寸精度和表面质量的前提下,尽量提高模具温度,缩短冷却时间。
3. 根据塑料材料的热稳定性,合理设定熔融塑料温度,避免因温度过高导致制品变形或烧焦。
4. 根据制品的形状、尺寸和冷却速度,合理设定冷却水温度,确保制品的尺寸精度和表面质量。
注塑模温度场的数值研究

cl lt tetm eaueds i t na vr u iee t i ead tee et ecnrlo m ea r i i ijc o ac ae h p rtr i r ui t a o sd f n m n h f c v o t ft p rt ew t n net n u e tb o i fr t i o e u h i
F i —ag.F i -n U J ngn U Xa j a oi
( .T eMO e aoa r o caia Mauatr n u mao ,hj n nvr t 1 h E K yLbrt y f o Meh n l n fc eadA t t n Z ei gU i sy c u o i a e i
A s at T r i e e prt ed tb t nO es】 eo jco odcv yud r ol gca nl, o n ay b t c :o e c t m ea r ir ui nt 如c i et nm l ai n e coi h n e bu r r p d th t u si o h fn i t n s d e m n m t dw sue n l i t m eaue e ’jc o l ip pr i acra c i e t c rl l e t h a sdt a ays h t prtrf l i et nm di ts ae ,n cod ne t t r t a e o e o s e e d n i o i nh w h h su u
进行离散化 , 并且只关心模具型腔表面的温度分布, 利 用边界元法 , 求解注塑模冷却问题具有其他方法不可 比的优越性 。在本文中以温度场为主要研究 目标 , 进 行 了数值计算 , 通过数值计算 , 可以掌握各个不同时刻 的温度分布情况 。对温度场进行理论分析, 掌握 温度 分 布 , 生产 上可 以获 得 均 匀 一致 分 布 的温 度 … 。 目 在 前, 已经有 不 少学 者 在这 些 方 面做 了很 多 的工作 。
模具温度场与成型精度分析
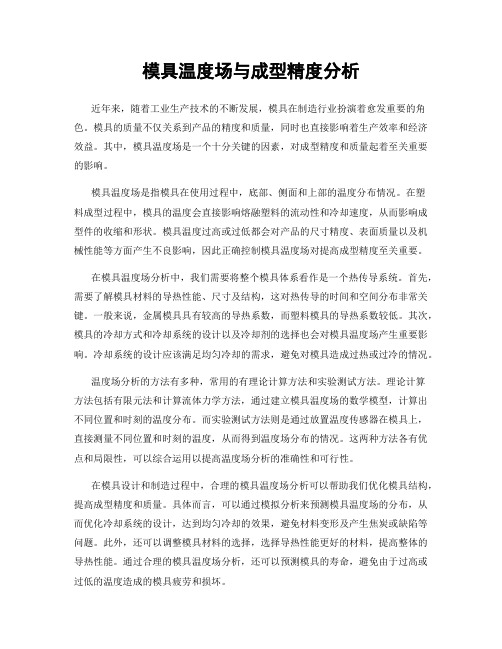
模具温度场与成型精度分析近年来,随着工业生产技术的不断发展,模具在制造行业扮演着愈发重要的角色。
模具的质量不仅关系到产品的精度和质量,同时也直接影响着生产效率和经济效益。
其中,模具温度场是一个十分关键的因素,对成型精度和质量起着至关重要的影响。
模具温度场是指模具在使用过程中,底部、侧面和上部的温度分布情况。
在塑料成型过程中,模具的温度会直接影响熔融塑料的流动性和冷却速度,从而影响成型件的收缩和形状。
模具温度过高或过低都会对产品的尺寸精度、表面质量以及机械性能等方面产生不良影响,因此正确控制模具温度场对提高成型精度至关重要。
在模具温度场分析中,我们需要将整个模具体系看作是一个热传导系统。
首先,需要了解模具材料的导热性能、尺寸及结构,这对热传导的时间和空间分布非常关键。
一般来说,金属模具具有较高的导热系数,而塑料模具的导热系数较低。
其次,模具的冷却方式和冷却系统的设计以及冷却剂的选择也会对模具温度场产生重要影响。
冷却系统的设计应该满足均匀冷却的需求,避免对模具造成过热或过冷的情况。
温度场分析的方法有多种,常用的有理论计算方法和实验测试方法。
理论计算方法包括有限元法和计算流体力学方法,通过建立模具温度场的数学模型,计算出不同位置和时刻的温度分布。
而实验测试方法则是通过放置温度传感器在模具上,直接测量不同位置和时刻的温度,从而得到温度场分布的情况。
这两种方法各有优点和局限性,可以综合运用以提高温度场分析的准确性和可行性。
在模具设计和制造过程中,合理的模具温度场分析可以帮助我们优化模具结构,提高成型精度和质量。
具体而言,可以通过模拟分析来预测模具温度场的分布,从而优化冷却系统的设计,达到均匀冷却的效果,避免材料变形及产生焦炭或缺陷等问题。
此外,还可以调整模具材料的选择,选择导热性能更好的材料,提高整体的导热性能。
通过合理的模具温度场分析,还可以预测模具的寿命,避免由于过高或过低的温度造成的模具疲劳和损坏。
注塑模温度场的试验研究

注塑模温度场的试验研究
近年来,随着科学技术的进步和人们对于技术加工的要求,注塑成型技术得到了快速发展,注塑工艺的管理也变得越来越重要。
注塑模具温度场是注塑过程中控制注塑件成型的重要参数,是判断注塑件合格与否的重要依据。
然而,注塑模具温度场研究还不够深入,对研究温度场的变化对注塑件质量的影响也还不够了解。
为了研究注塑模具温度场的变化对注塑件质量的影响,我们从实验的角度出发,使用先进的测温设备进行注塑模具温度场的实验研究。
首先,我们研究了不同的温度场水平下注塑件的表面质量,即温度场越高,表面质量越好。
其次,我们也对温度场下模具的内部结构进行了检测,结果表明,温度场越高,模具内部结构优化程度越高,效果越好。
此外,还对不同温度场水平下注塑件的力学性能进行了测试,发现温度场越高,注塑件在拉伸力学性能,弯曲力学性能以及疲劳寿命等方面均有显著改善。
综上所述,我们证实了恒定的注塑模具温度场对注塑件的性能有着比较明显的影响,温度场越高,注塑件的表面质量和力学性能均有明显改善。
本试验的研究结果可以为注塑模具的设计提供参考,同时也可以为生产环节提供质量控制手段。
未来,我们还可以进一步研究不同温度场水平下注塑件的表面光泽度,熔体流动性等性能参数,以提供更为精确的注塑模具设计参数。
总之,在研究和优化注塑工艺过程中,注塑模具温度场的研究是十分重要的,本试验的研究结果可以为注塑模具设计提供参考,为注塑工艺的控制和优化提供有益的建议。
铸造模型的温度场有限元分析

铸造模型的温度场有限元分析概述铸造是一种工程制造方法,将液态金属或其他物质浇铸到一个模具中,让其冷却并形成所需形状。
在铸造过程中,温度场是非常重要的因素。
温度场决定了物体的热胀冷缩、形变、质量等方面,因此对温度场进行分析和优化是铸造中非常关键的步骤。
有限元分析是一种数值分析方法,广泛应用于工程领域中的物理模拟和优化。
它通过将复杂的物理系统划分成离散的小单元,然后进行数值计算,求解问题的数值解。
因为铸造模型具有复杂的结构和几何形状,因此需要使用有限元分析方法对其温度场进行建模和分析。
建模铸造模型的温度场建模通常采用有限元法。
首先需要将模型划分为许多小单元,然后对每个小单元进行分析。
对于铸造模型,一般采用三维有限元建模。
建模首先需要构建模型几何结构,通常可以使用CAD软件进行建模,并将建模结果导入有限元分析软件中。
此外,还需要确定材料属性如热传导系数、比热容等物理参数。
这些参数可以通过实验或者文献数据获得。
模型建立后,需要进行网格划分。
网格划分是将模型划分为许多小单元的过程。
划分应该既能保证精度,又不能花费过多的计算资源。
常用的有限元网格包括四面体网格和六面体网格。
求解一旦建立了有限元模型并完成了网格划分,就可以求解铸造模型的温度场了。
求解需要根据材料性质、边界条件和初值条件设置方程组。
为此,通常会考虑以下因素:•材料参数:包括材料的比热容、密度、热传导系数等。
•边界条件:包括模型的外表面或锥度面进行空气自流冷却,穴道内部注射的铸造材料温度,模型的初值等。
•时间步长:需要选用适当的时间步长来求解模型。
通过建立方程组,使用求解器对其进行求解。
有限元分析通常可以获得模型的温度分布、热流量、热应力等结果。
结果分析求解完成后,可以对求解结果进行分析和优化。
通常采用后处理软件进行结果可视化,比如ParaView、Tecplot等软件。
常用的分析方式包括对温度场进行动态展示、温度场的等高线图、热流分布图等。
这些可视化结果可以帮助研究人员更好地了解模型温度分布的规律,并进行优化改进。
注塑成型数值模拟报告
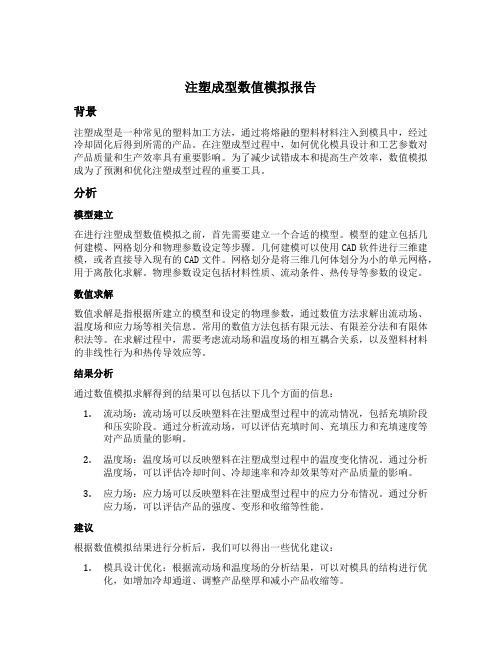
注塑成型数值模拟报告背景注塑成型是一种常见的塑料加工方法,通过将熔融的塑料材料注入到模具中,经过冷却固化后得到所需的产品。
在注塑成型过程中,如何优化模具设计和工艺参数对产品质量和生产效率具有重要影响。
为了减少试错成本和提高生产效率,数值模拟成为了预测和优化注塑成型过程的重要工具。
分析模型建立在进行注塑成型数值模拟之前,首先需要建立一个合适的模型。
模型的建立包括几何建模、网格划分和物理参数设定等步骤。
几何建模可以使用CAD软件进行三维建模,或者直接导入现有的CAD文件。
网格划分是将三维几何体划分为小的单元网格,用于离散化求解。
物理参数设定包括材料性质、流动条件、热传导等参数的设定。
数值求解数值求解是指根据所建立的模型和设定的物理参数,通过数值方法求解出流动场、温度场和应力场等相关信息。
常用的数值方法包括有限元法、有限差分法和有限体积法等。
在求解过程中,需要考虑流动场和温度场的相互耦合关系,以及塑料材料的非线性行为和热传导效应等。
结果分析通过数值模拟求解得到的结果可以包括以下几个方面的信息:1.流动场:流动场可以反映塑料在注塑成型过程中的流动情况,包括充填阶段和压实阶段。
通过分析流动场,可以评估充填时间、充填压力和充填速度等对产品质量的影响。
2.温度场:温度场可以反映塑料在注塑成型过程中的温度变化情况。
通过分析温度场,可以评估冷却时间、冷却速率和冷却效果等对产品质量的影响。
3.应力场:应力场可以反映塑料在注塑成型过程中的应力分布情况。
通过分析应力场,可以评估产品的强度、变形和收缩等性能。
建议根据数值模拟结果进行分析后,我们可以得出一些优化建议:1.模具设计优化:根据流动场和温度场的分析结果,可以对模具的结构进行优化,如增加冷却通道、调整产品壁厚和减小产品收缩等。
2.工艺参数优化:根据流动场和温度场的分析结果,可以对注塑成型过程中的工艺参数进行优化,如调整充填时间、充填压力和冷却时间等。
3.材料选择优化:根据应力场的分析结果,可以对材料的选择进行优化,以满足产品的强度和变形要求。
注塑温度参数

注塑温度参数注塑温度参数是指在注塑过程中所需要控制的温度相关的参数。
这些参数包括熔融温度、熔融区温度、模具温度以及冷却时间等。
正确地控制和调整这些参数对于保证注塑产品的质量和生产效率至关重要。
一、熔融温度1. 熔融温度的定义熔融温度是指将塑料原料加热至其完全熔化所需要的温度。
不同种类的塑料具有不同的熔融温度,因此在注塑过程中需要根据所使用的塑料种类来确定合适的熔融温度。
2. 确定熔融温度的因素确定熔融温度时需要考虑以下因素:- 塑料种类:不同种类的塑料具有不同的熔融点,因此需要根据所使用的塑料种类来确定合适的熔融温度。
- 塑料颜色:某些颜色较深或者添加了颜料的塑料可能需要更高的熔融温度。
- 模具结构:模具结构也会对注塑温度有一定的影响,例如较厚的部分可能需要较高的温度来保证充填完整。
3. 影响熔融温度的因素影响熔融温度的因素主要有以下几个:- 塑料种类:不同种类的塑料具有不同的熔融点,因此需要根据所使用的塑料种类来确定合适的熔融温度。
- 环境温度:环境温度也会对注塑温度有一定的影响,较低的环境温度可能需要增加注塑温度以保证充填完整。
- 模具结构:模具结构也会对注塑温度有一定的影响,例如较厚部分可能需要较高的温度来保证充填完整。
二、熔融区温度1. 熔融区温度的定义熔融区是指在注塑过程中,将固态塑料加热至其完全熔化所经历的区域。
在这个区域内,固态塑料逐渐被加热并转变为流动状态。
2. 确定熔融区温度的因素确定熔融区温度时需要考虑以下因素:- 塑料种类:不同种类的塑料具有不同的熔融温度,因此需要根据所使用的塑料种类来确定合适的熔融区温度。
- 注射速度:较高的注射速度可能需要增加熔融区温度以保证充填完整。
- 模具结构:模具结构也会对熔融区温度有一定的影响,例如较厚部分可能需要较高的温度来保证充填完整。
3. 影响熔融区温度的因素影响熔融区温度的因素主要有以下几个:- 塑料种类:不同种类的塑料具有不同的熔融点,因此需要根据所使用的塑料种类来确定合适的熔融区温度。
注塑成型冷却过程的数值模拟分析
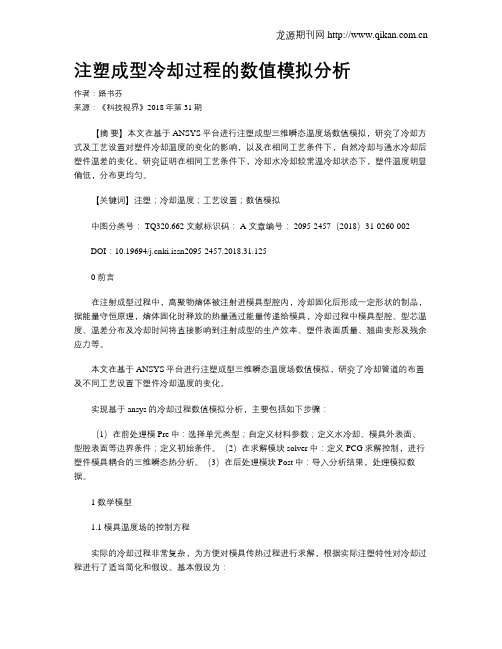
注塑成型冷却过程的数值模拟分析作者:路书芬来源:《科技视界》2018年第31期【摘要】本文在基于ANSYS平台进行注塑成型三维瞬态温度场数值模拟,研究了冷却方式及工艺设置对塑件冷却温度的变化的影响,以及在相同工艺条件下,自然冷却与通水冷却后塑件温差的变化。
研究证明在相同工艺条件下,冷却水冷却较常温冷却状态下,塑件温度明显偏低,分布更均匀。
【关键词】注塑;冷却温度;工艺设置;数值模拟中图分类号: TQ320.662 文献标识码: A 文章编号: 2095-2457(2018)31-0260-002DOI:10.19694/ki.issn2095-2457.2018.31.1250 前言在注射成型过程中,高聚物熔体被注射进模具型腔内,冷却固化后形成一定形状的制品,据能量守恒原理,熔体固化时释放的热量通过能量传递给模具,冷却过程中模具型腔、型芯温度、温差分布及冷却时间将直接影响到注射成型的生产效率、塑件表面质量、翘曲变形及残余应力等。
本文在基于ANSYS平台进行注塑成型三维瞬态温度场数值模拟,研究了冷却管道的布置及不同工艺设置下塑件冷却温度的变化。
实现基于ansys的冷却过程数值模拟分析,主要包括如下步骤:(1)在前处理模Pre中:选择单元类型;自定义材料参数;定义水冷却、模具外表面、型腔表面等边界条件;定义初始条件。
(2)在求解模块solver中:定义PCG求解控制,进行塑件模具耦合的三维瞬态热分析。
(3)在后处理模块Post中:导入分析结果,处理模拟数据。
1 数学模型1.1 模具温度场的控制方程实际的冷却过程非常复杂,为方便对模具传热过程进行求解,根据实际注塑特性对冷却过程进行了适当简化和假设。
基本假设为:(1)模具材料为各向同性材料;(2)成型过程中塑件与模壁完全接触,不考虑接触热;(3)模具与周围的环境的热交换只考虑对流换热,忽略辐射换热。
基于以上基本假设,模具传热简化为一个没有热源的三维瞬态热传导问题,温度场控制方程如下[1]:1.2 塑件传热的数学模型1.2.1 基本假设塑件的实际冷却过程非常复杂,在传热分析过程中,其瞬态温度场分析应该考虑制品内热交换、制品和模具间热交换、模具内热交换、模具和冷却介质间热交换等四个方面[2]。
- 1、下载文档前请自行甄别文档内容的完整性,平台不提供额外的编辑、内容补充、找答案等附加服务。
- 2、"仅部分预览"的文档,不可在线预览部分如存在完整性等问题,可反馈申请退款(可完整预览的文档不适用该条件!)。
- 3、如文档侵犯您的权益,请联系客服反馈,我们会尽快为您处理(人工客服工作时间:9:00-18:30)。
3
=
1
6υ
l
( l) ^ i,j l
( l) 6υ ^ i,j
[∧
( l)
zj ]
2
η
( l)
, j = 2 , 3 , …, N z ( 14)
对每个节点写出上述各式 , 并代入相应的温度控 制方程 , 得到以各计算点的温度为未知量的方程组 [ K ]{ T} = { F} , 该方程组是线性的 , 可以采用松驰法 求解方程 ,从而获得温度场 。 215 凝固层计算 [ 4 ] 在充填阶段 ,热塑料熔体与冷模壁接触 , 若模壁温
=
1
6υ(i ,l)j
l
6
l
υ K ・ Δz 2 3 j
( l) i,j
( 6 ( T N′ , j + 1 , k + 1 - 2 T N′ , j , k + 1 + T N′ , j - 1 , k + 1) )
m =1
( 12)
© 1995-2005 Tsinghua Tongfang Optical Disc Co., Ltd. All rights reserved.
[5 ] 度低于材料的 “不流动” 温度 T nf , 在壁面上就会形成 凝固层 , 凝固层的生长与下面几个因素有关 : 熔体温 度、 模壁温度 、 流动速率和几何体 。 每一个时间步长的凝固层厚度通过给出温度等于 不流动温度的 z 坐标表示 , 有效的型腔厚度通过由原
( 11)
92 T 9z 2
N ,j,k +1
N ,j,k +1
211 瞬态项
温度对时间的导数用向后有限差分近似 [ 1 ] : 9 T TN , j , k + 1 - TN , j , k ( 10) = Δt 9t 式中 N , j , k + 1 — — —N 结点 、 第 j 层和 k + 1 时刻 212 热传导项 若采用隐式向前差分 [ 2 ] : 92 T 1 ( T = - 2 Ti , j , k + 1 + 9z 2 N , j , k + 1 Δ z 2j i , j + 1 , k + 1 T i , j - 1 , k + 1 ) , j = 2 , 3 ……, N z
2001 年 6 月
中 国 塑 料
・ 57 ・
始型腔厚度扣除凝固层获得 。在极端情况下 , 有效型 腔厚度可能为 0 ,导致短射 。
错误必须检查 。因为粘性发热项是非线性源项 , 对整 个分部差分方程的精确数值稳定性分析是比较复杂 的 ; 对流项和粘性发热项的显式处理后的积累误差有 时会引起稳定性问题 , 特别是在浇口和流道等高剪切 区域 。另外 ,除了这些稳定性条件外 , 与瞬态对流扩散 项方程的求解精度有关的还有一条限制 , 如果采用中 心差分处理对流项 ,数值求解有时会出现振荡 , 除非满 足如下严格的条件 , Peclet 数满足 : Pe = ( v x /Δ x + v y / Δ y ) / (α / (Δ z ) 2 ) ≤2/ ( v xΔ t /Δ x + v yΔ t /Δ y ) , 由于主 流道 、 流道 、 浇口区域内的速度相当大 , 这条限制是很 关键的 。为了消除这一严格的条件 , 因而在温度场计 算时采用了上风法技术处理热对流项 [ 3 ] 。
_ _
图1 三角形单元和柱单元的分层
2 能量方程的有限差分求解
熔体的温度在流动平面和沿型腔壁厚方向均发生 变化 。 在流动平面内 , 单元内的温度分布仍采用线性插 [1 ] 值 ,即
3
图2 三角形单元的速度矢量
引入函数 : dot = CN ・ V
( l) υ 于是 ,权函数可定义为 ^ i,j =
3
© 1995-2005 Tsinghua Tongfang Optical Disc Co., Ltd. All rights reserved.
・ 56 ・
注塑充模过程中温度场的数值分析
υ 9T 9u 9 = = = 0 z = 0 9n 9n 9n 式中 h ( t ) — — —t 时刻型腔的厚度 本文采用有限元/ 有限差分混合方法求解压力场 和温度场 , 采用控制体积法跟踪流动前沿 。在采用数 值方法分析前 , 应该将计算区域划分为相应的离散单 元 ,对浇注系统 , 采用一维线单元 , 并沿径向进行差分 网格划分 。对于模具型腔 , 利用中面模型将整个型腔 离散成线性三角形单元 , 并沿厚度方向进行差分网格 划分 [ 1 ] ,如图 1 。
1 数学模型
在注塑充填过程中 , 由于模腔的复杂性及聚合物 熔体流变性质的复杂性 , 再加上移动边界的存在 , 问题 的求解存在着很大的困难 。但由于注塑件通常都是薄 壁件 ,通过引入 Hele - Shaw 近似并给出适当的简化 , 得到最终的控制组压力方程是二维的 , 而温度场控制 仍然保持三维 [ 3 ] 。 本文基于非牛顿流体在非等温下的广义 Hele Shaw 流动的控制 ,采用混合有限元 - 有限差分法求解
9T 9 T υ9 T) 92 T η + u + = k + γ2 9t 9x 9y 9z 2 ( 4) υ— 式中 u 、 — —x 、 y 方向的速度分量 ρ— — — 密度 Cp 、 k— — — 比热容和热传导率 能量方程 :ρ Cp (
p、 T— — — 熔体的压力和温度 x、 y— — — 中面坐标 z— — — 厚度方向 γ— — — 剪切速率
4 算例分析
对一个一模两腔的摩托车内嵌件的模具进行模 拟 ,具体几何模型及离散后的模型如图 3 , 选用 ABS 材 料 ,参数为 :ρ = 896 kg/ m3 , Cp = 1 900 J / kg ・ K, K =
0. 13 W/ m・ K ,cross 粘度模型的 5 个参数为 ( n ,τ3 , B , ) = ( 0. 3496 ,4 855. 3 ,2. 101e - 8 ,15 183. 0 ,0. 0) , T b ,β
方程 ,并采用控制体积法跟踪熔体前沿 。文中对温度 场的计算给出了详细的描述 ,并对所得结果加以讨论 。 111 控制方程 [ 1 ,4 ] υ ) 9 (ρu ) 9 (ρ ( 1) 连续性方程 : + =0 9x 9y 9 p 9 (η 9 u ) ( 2) 运动方程 : =0 9 x 9z 9z υ 9 p 9 (η 9 ) =0 ( 3) 9y 9z 9z
熔体入口温度 230 ℃。
图3 模型几何体及网格划分
在三种状态下对该制件进行分析 : ( 1 ) 充填时间为 4 s 且两侧壁温均为 40 ℃; ( 2) 充填时间为 10 s 且两侧 壁温均为 40 ℃; ( 3 ) 充填时间为 4 s 且两侧壁温均为 100 ℃,在每一个时间步长计算充填区域的压力分布及 温度沿整个型腔的分布 。 三种状态下型腔充满时的最大注射压力分别为 5812 M Pa 、 5116 M Pa 和 4917 M Pa ,温度分布如图 4 所 示 , 由图中可知 , 三种情形的温度场分布趋势大致相 同 ,但由于充模时间及壁温的差异 , 引起制品成型后温 度的高低和分布均匀程度不同 。( 1) 充填时间为 4 s 且 两壁温均为 40 ℃ 时充填结束时的熔体最高体平均温 度和最大温差分别为 22213 ℃ 和 4415 ℃; ( 2 ) 充填时 间为 10 s 且两侧壁温均为 40 ℃ 时充填结束时的熔体 最高 体 平 均 温 度 和 最 大 温 差 分 别 为 21912 ℃和
υ2 9u ) 2 ( 9 ) ( 5) + 9z 9z η— — — 剪切粘度 , 它与压力 、 温度 、 剪切速率有 关 , 这里认为熔体为不可压纯粘性流体 , 采用修正的 Cross 模型 [ 2 ,5 ] : η 0 η= ( 6) η 0γ 1 - n 1+( 3 ) τ γ=
(
T / η 式中 — — 零剪切粘度 ,η 0 — 0 =) Tm
ρ Cp = ( ^ i ,l)j 6υ
l
6υ
l
( l) ^ i,j
∫η d z ・
- h
zj
z
2A
( l)
6 [ ∧(x l) b (ml) + ∧(y l) c (ml) ] ・ T N′ , j , k +1
m =1
( 13)
式中 j = 2 , 3 , …, N z b (ml) , c (ml) — — — 单元面积坐标中的参数 214 粘弹热项 粘弹热项的处理方法同热对流项 ,即 : η γ
_
_
υ(i ,l)j , dot > 0
0 , dot < 0
则差分表示 : 9 T υ9 T u + 9x 9y
3
T
( l)
( x , y , z , t) =
n =1
6
L
( l) m
( x , y)
( l) Tm
( z , t)
( 8)
N , j , k +1
( z , t) — 式中 — —t 时刻单元 l 的第 m 个结点的温 度 厚度方向引入差分格式 , 本文采用均匀差分网格 , ( 9) 即 z j = ( j - 1)Δ z j = 1 , 2 ……N z + 1 Nz — — — 等分网格数
第 15 卷 第6期
2001 年 6 月
中 国 塑 料
CHINA PLASTICS
Vol. 15 ,No. 6 J un. ,2001
注塑充模过程中温度场的数值分析
王利霞 , 申长雨 , 陈静波 , 刘春太
( 郑州大学橡塑模具国家工程研究中心 ,河南 郑州 450002)
摘 要 : 采用有限差分法对注塑过程中充填阶段的温度场的数值分析进行了研究 ,数学模型是基于非牛顿流体在非 等温状态下广义 Hele - Shaw 流动 ,可预测非牛顿流体在任意形状薄壁型腔内流动时的温度场 。对能量方程进行有 限差分近似时 ,能量方程中的瞬态项和热传导项分别采用向后差分和隐式差分 。为保证数值计算过程的稳定性 ,采 用上风法处理对流项 。还讨论了模温和流率对温度分布的影响 。 关 键 词 : 注射成型 ; 数值分析 ; 温度场 中图分类号 : TQ320. 66 + 2 文献标识码 : B 文章编号 :1001O 9278 ( 0001) 06O 0055O 05