PCB流程-图形电镀&蚀刻
pcb-etch

PCB外层电路的蚀刻工艺一.概述目前,印刷电路板(PCB)加工的典型工艺采用"图形电镀法"(Pattern plating)。
即先在板子外层需保留的铜箔部分上,也就是电路的图形部分上预镀一层铅锡抗蚀层,然后用化学方式将其余的铜箔腐蚀掉,称为蚀刻。
图1所示的,为图形电镀后板子横截面的情况。
在图1状态下,印制板的整体厚度是整个加工过程中之最,以后将逐渐减薄,直到阻焊涂覆工艺。
图1的下一道工艺是去膜,即将铜层上铅锡部分以外的感光保护膜剥离掉。
图2表示了去膜后板子的横截面。
接下去的工艺就是蚀刻。
要注意的是,这时的板子上面有两层铜.在外层蚀刻工艺中仅仅有一层铜是必须被全部蚀刻掉的,其余的将形成最终所需要的电路。
这种类型的图形电镀,其特点是镀铜层仅存在于铅锡抗蚀层的下面。
另外一种工艺方法是整个板子上都镀铜,感光膜以外的部分仅仅是锡或铅锡抗蚀层(见图3)。
这种工艺称为“全板镀铜工艺“。
与图形电镀相比,全板镀铜的最大缺点是板面各处都要镀两次铜而且蚀刻时还必须都把它们腐蚀掉。
因此当导线线宽十分精细时将会产生一系列的问题。
同时,侧腐蚀(见图4)会严重影响线条的均匀性。
在印制板外层电路的加工工艺中,还有另外一种方法,就是用感光膜代替金属镀层做抗蚀层。
这种方法非常近似于内层蚀刻工艺,可以参阅内层制作工艺中的蚀刻。
目前,锡或铅锡是最常用的抗蚀层,用在氨性蚀刻剂的蚀刻工艺中.氨性蚀刻剂是普遍使用的化工药液,与锡或铅锡不发生任何化学反应。
氨性蚀刻剂主要是指氨水/氯化氨蚀刻液。
此外,在市场上还可以买到氨水/硫酸氨蚀刻药液。
以硫酸盐为基的蚀刻药液,使用后,其中的铜可以用电解的方法分离出来,因此能够重复使用。
由于它的腐蚀速率较低,一般在实际生产中不多见,但有望用在无氯蚀刻中。
有人试验用硫酸-双氧水做蚀刻剂来腐蚀外层图形。
由于包括经济和废液处理方面等许多原因,这种工艺尚未在商用的意义上被大量采用.更进一步说,硫酸-双氧水,不能用于铅锡抗蚀层的蚀刻,而这种工艺不是PCB外层制作中的主要方法,故决大多数人很少问津。
PCB电镀工艺与流程
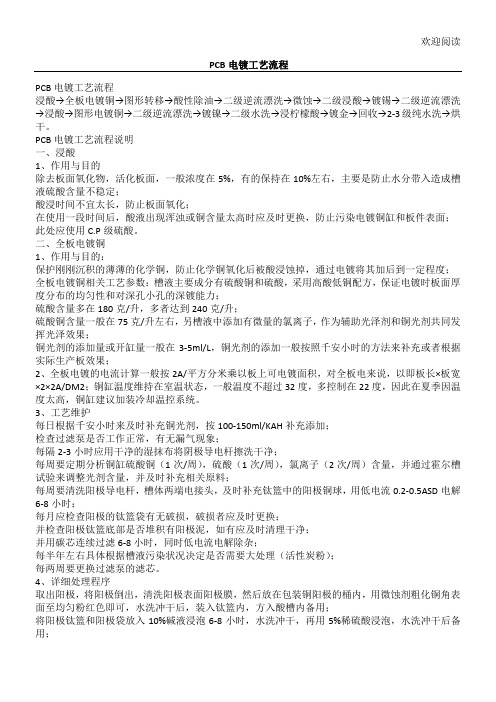
欢迎阅读PCB 电镀工艺流程PCB 电镀工艺流程浸酸→全板电镀铜→图形转移→酸性除油→二级逆流漂洗→微蚀→二级浸酸→镀锡→二级逆流漂洗→浸酸→图形电镀铜→二级逆流漂洗→镀镍→二级水洗→浸柠檬酸→镀金→回收→2-3级纯水洗→烘干。
PCB 电镀工艺流程说明一、浸酸1、作用与目的除去板面氧化物,活化板面,一般浓度在5%,有的保持在10%左右,主要是防止水分带入造成槽 1 2×板宽×2×3每隔2-3电解6-8每月应检查阳极的钛篮袋有无破损,破损者应及时更换;并检查阳极钛篮底部是否堆积有阳极泥,如有应及时清理干净;并用碳芯连续过滤6-8小时,同时低电流电解除杂;每半年左右具体根据槽液污染状况决定是否需要大处理(活性炭粉);每两周要更换过滤泵的滤芯。
4、详细处理程序取出阳极,将阳极倒出,清洗阳极表面阳极膜,然后放在包装铜阳极的桶内,用微蚀剂粗化铜角表面至均匀粉红色即可,水洗冲干后,装入钛篮内,方入酸槽内备用;将阳极钛篮和阳极袋放入10%碱液浸泡6-8小时,水洗冲干,再用5%稀硫酸浸泡,水洗冲干后备用;将槽液转移到备用槽内,加入1-3ml/L的30%的双氧水,开始加温,待温度加到65度左右打开空气搅拌,保温空气搅拌2-4小时;关掉空气搅拌,按3-5克/升将活性碳粉缓慢溶解到槽液中,待溶解彻底后,打开空气搅拌,如此保温2-4小时;关掉空气搅拌,加温,让活性碳粉慢慢沉淀至槽底;待温度降至40度左右,用10um的PP滤芯加助滤粉过滤槽液至清洗干净的工作槽内,打开空气搅拌,放入阳极,挂入电解板,按0.2-0.5ASD电流密度低电流电解6-8小时;经化验分析,调整槽中的硫酸,硫酸铜,氯离子含量至正常操作范围内,根据霍尔槽试验结果补充光剂;待电解板板面颜色均匀后,即可停止电解,然后按1-1.5ASD的电流密度进行电解生膜处理1-2小时,待阳极上生成一层均匀致密附着力良好的黑色磷膜即可;试镀。
图形电镀
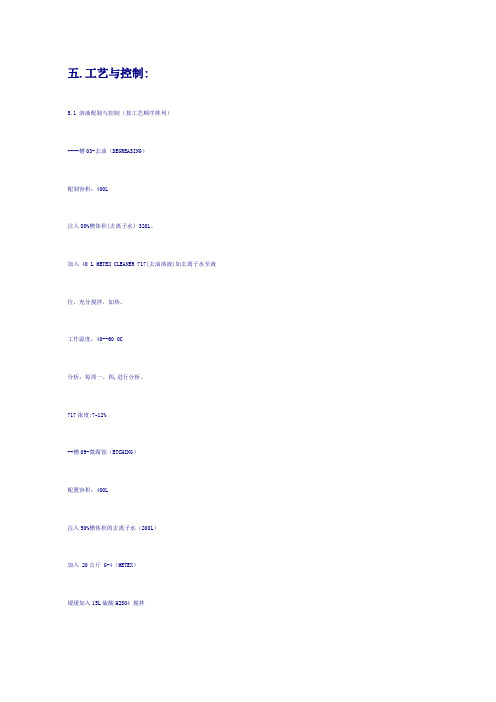
五.工艺与控制:5.1 溶液配制与控制(按工艺顺序排列)----槽03-去油(DEGREASING)配制容积:400L注入80%槽体积(去离子水) 320L。
加入 40 L METEX CLEANER 717(去油溶液)加去离子水至液位,充分搅拌,加热。
工作温度:40--60 0C分析:每周一、四,进行分析。
717浓度:7-12%--槽09-微腐蚀(ETCHING)配置容积:400L注入50%槽体积的去离子水(200L)加入 20公斤 G-4(METEX)缓缓加入15L硫酸H2SO4 搅拌加入去离子水至液位,充分搅拌至充分溶解。
工作温度:20--350C 分析:每天分析一次G-4 浓度:20-70G/LH2SO4 浓度:3%-8% 铜含量<25g/L每次分析后将G-4添加至60g/L H2SO4添加至5%当溶液中铜含量超过25g/L时,更换溶液。
--槽10-浸酸(ACID DIP)配制容积 340L注入50%槽体积(去离子水).加入20L H2SO4 搅拌。
加入去离子水至液面并搅拌每周更换一次。
--11-13 电镀铜(COPPER PLATING)配制容积:2550 L加入CuSO4.5H2O 800 L(METEX)加入1400L 去离子水并搅拌加入250L H2SO4并搅拌溶液组成:CuSO4.5H2O: 60-100 g/lH2SO4: 160-220 g/l工作温度:20-300C电流密度:2-3 A/DM2光亮剂9241为自动添加.(生产时每班检测光亮剂流量)范围: 25-35ML/100AH阴极移动+空气搅拌分析:由实验室每周一,四进行分析.CuSO4.5H2OH2SO4电流密度按工艺要求。
保持循环槽与主槽液面差--14-15 电镀铜(COPPER PLATING)配制容积:1950 L加入CuSO4.5H2O 450 L(METEX)加入1150L 去离子水并搅拌加入200L H2SO4并搅拌电镀工艺同槽11--13--槽07-氟硼酸(ACID DIP)配制容积 340L注入50%槽体积(去离子水).加入30L HBF4 搅拌。
PCB(印刷线路板)工艺流程
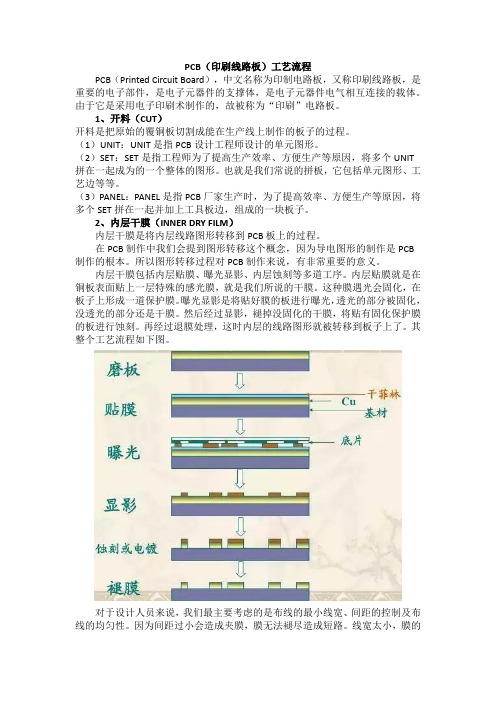
PCB(印刷线路板)工艺流程PCB(Printed Circuit Board),中文名称为印制电路板,又称印刷线路板,是重要的电子部件,是电子元器件的支撑体,是电子元器件电气相互连接的载体。
由于它是采用电子印刷术制作的,故被称为“印刷”电路板。
1、开料(CUT)开料是把原始的覆铜板切割成能在生产线上制作的板子的过程。
(1)UNIT:UNIT是指PCB设计工程师设计的单元图形。
(2)SET:SET是指工程师为了提高生产效率、方便生产等原因,将多个UNIT拼在一起成为的一个整体的图形。
也就是我们常说的拼板,它包括单元图形、工艺边等等。
(3)PANEL:PANEL是指PCB厂家生产时,为了提高效率、方便生产等原因,将多个SET拼在一起并加上工具板边,组成的一块板子。
2、内层干膜(INNER DRY FILM)内层干膜是将内层线路图形转移到PCB板上的过程。
在PCB制作中我们会提到图形转移这个概念,因为导电图形的制作是PCB制作的根本。
所以图形转移过程对PCB制作来说,有非常重要的意义。
内层干膜包括内层贴膜、曝光显影、内层蚀刻等多道工序。
内层贴膜就是在铜板表面贴上一层特殊的感光膜,就是我们所说的干膜。
这种膜遇光会固化,在板子上形成一道保护膜。
曝光显影是将贴好膜的板进行曝光,透光的部分被固化,没透光的部分还是干膜。
然后经过显影,褪掉没固化的干膜,将贴有固化保护膜的板进行蚀刻。
再经过退膜处理,这时内层的线路图形就被转移到板子上了。
其整个工艺流程如下图。
对于设计人员来说,我们最主要考虑的是布线的最小线宽、间距的控制及布线的均匀性。
因为间距过小会造成夹膜,膜无法褪尽造成短路。
线宽太小,膜的附着力不足,造成线路开路。
所以电路设计时的安全间距(包括线与线、线与焊盘、焊盘与焊盘、线与铜面等),都必须考虑生产时的安全间距。
(1)前处理:磨板磨板的主要作用:基本前处理主要是解决表面清洁度和表面粗糙度的问题。
去除氧化,增加铜面粗糙度,便于菲林附着在铜面上。
PCB电镀工艺流程
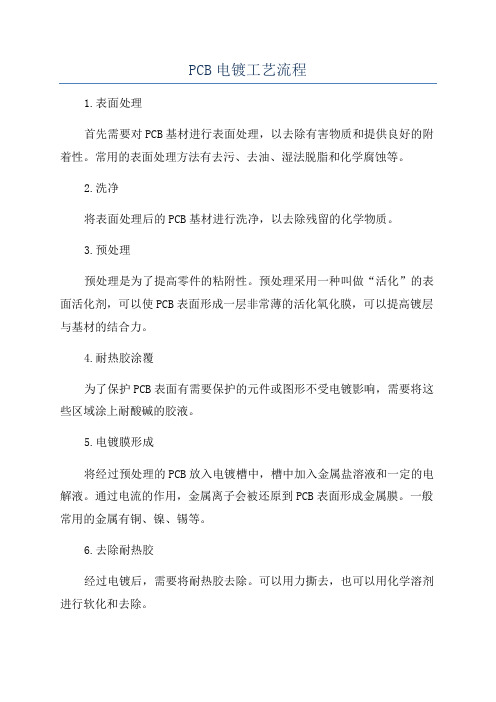
PCB电镀工艺流程1.表面处理首先需要对PCB基材进行表面处理,以去除有害物质和提供良好的附着性。
常用的表面处理方法有去污、去油、湿法脱脂和化学腐蚀等。
2.洗净将表面处理后的PCB基材进行洗净,以去除残留的化学物质。
3.预处理预处理是为了提高零件的粘附性。
预处理采用一种叫做“活化”的表面活化剂,可以使PCB表面形成一层非常薄的活化氧化膜,可以提高镀层与基材的结合力。
4.耐热胶涂覆为了保护PCB表面有需要保护的元件或图形不受电镀影响,需要将这些区域涂上耐酸碱的胶液。
5.电镀膜形成将经过预处理的PCB放入电镀槽中,槽中加入金属盐溶液和一定的电解液。
通过电流的作用,金属离子会被还原到PCB表面形成金属膜。
一般常用的金属有铜、镍、锡等。
6.去除耐热胶经过电镀后,需要将耐热胶去除。
可以用力撕去,也可以用化学溶剂进行软化和去除。
7.硬化经过电镀后,PCB上的金属膜还需要进一步硬化,使其更加坚硬耐磨。
一般采用热处理或用其他技术进行硬化。
8.二次电镀(可选)在硬化后,金属膜的厚度可能还不够,需要进行二次电镀以增加厚度。
常用的二次电镀方法有化学沉积、真空蒸镀等。
9.检查和修复对PCB进行检查,发现电镀层薄或有瑕疵的地方进行修补。
修复可以使用焊锡、导电漆等方法。
10.清洗清洗是为了去除二次电镀或修复过程中残留的化学物质和杂质。
清洗可以使用的方法有水抛光、化学清洗和超声波清洗等。
11.包装进行最后的包装,将电镀后的PCB进行整理、称重,并放入塑料袋或者包装箱中。
以上就是PCB电镀的工艺流程,通过这些步骤可以为PCB提供良好的导电和防腐蚀性能。
PCB生产流程概况

PCB生产流程概况总的来说,线路板的整个生产流程如下:来料(IQC)→开料→(烘板)→钻孔→检查(IQC)→粗磨→沉铜→细磨→线路转移(干菲林/丝印)→电镀→)→FQC)→抽查(FA)→包装下在分各个不同的流程分别叙述。
一.IQCIQC的主要功能是检查来料(原材料、大料或钻孔板)的质量,进行收板、验板,合板的板经过包装,送电镀车间磨板。
板料经过IQC检验合板后,送钻房钻孔。
开料后的板有A板及B板等多种尺寸。
钻房钻孔是将各个孔的位置用座标(X.Y)表示,钻针的直径用D表示,另外还有钻速,钻针的上升下降速度等这一系列的数据输入电脑,然后用电脑将这一系列的数据存储在纸带上打印出纸带。
再用纸带去控制钻孔的上述各种数据,即能钻出符合要求的板。
钻好孔后的板需经过IQC的验收,验收的程序如下:1.核对板块生产编号,钻孔制作资料,测度孔径用试针,红胶片样板,按制作要求检验板料。
2.铜板检查项目:板料、板厚及开料尺寸。
3.对不合品质要求的铜板,应抽出重新加工或作报废处理,不能混淆好次。
4.验收板是发现不合格铜板,应立即向当班主管.班长汇报情况。
IQC钻孔板的检查内容主要是:1.钻歪孔2.物有圆孔3.披锋4.多孔5.少孔6.塞孔7.曝孔8.钻偏9.未钻穿10.刮花铜面11.露纤维12.尺寸不合13.板厚/薄14.铜箔厚度不对15.单双面混乱16.工艺不对17.纤维丝18.孔径超公差19.板面花板二.磨板经过IQC检查后合格的板送去电镀房磨板。
磨板用两种磨板机,一台粗磨,一台细磨,其主要区别在于粗磨是在沉铜之前,而细磨则在沉铜之后进行。
磨板的主要作用在于:粗磨:除去钻孔板表面的垃圾,使铜面光滑,平整。
而细磨则不但要使铜面光滑,平整,还可以除去铜板表面的氧化物。
喷锡板厚在1.5MM 以上的板在磨板前需啤圆周角,因为有很多铜板的外形很粗糙,啤上圆角之后,可以将其区分开,另外,还可以避免划伤板。
判断磨板的质量,主要是要看其表面是否有垃圾,铜面是否光滑平整,有无氧化层及刮花等。
PCB电镀
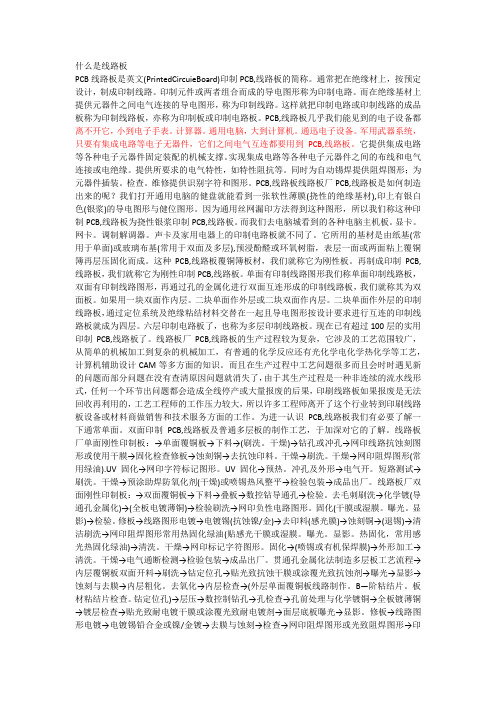
什么是线路板PCB线路板是英文(PrintedCircuieBoard)印制PCB,线路板的简称。
通常把在绝缘材上,按预定设计,制成印制线路。
印制元件或两者组合而成的导电图形称为印制电路。
而在绝缘基材上提供元器件之间电气连接的导电图形,称为印制线路。
这样就把印制电路或印制线路的成品板称为印制线路板,亦称为印制板或印制电路板。
PCB,线路板几乎我们能见到的电子设备都离不开它,小到电子手表。
计算器。
通用电脑,大到计算机。
通迅电子设备。
军用武器系统,只要有集成电路等电子无器件,它们之间电气互连都要用到PCB,线路板。
它提供集成电路等各种电子元器件固定装配的机械支撑。
实现集成电路等各种电子元器件之间的布线和电气连接或电绝缘。
提供所要求的电气特性,如特性阻抗等。
同时为自动锡焊提供阻焊图形;为元器件插装。
检查。
维修提供识别字符和图形。
PCB,线路板线路板厂PCB,线路板是如何制造出来的呢?我们打开通用电脑的健盘就能看到一张软性薄膜(挠性的绝缘基材),印上有银白色(银浆)的导电图形与健位图形。
因为通用丝网漏印方法得到这种图形,所以我们称这种印制PCB,线路板为挠性银浆印制PCB,线路板。
而我们去电脑城看到的各种电脑主机板。
显卡。
网卡。
调制解调器。
声卡及家用电器上的印制电路板就不同了。
它所用的基材是由纸基(常用于单面)或玻璃布基(常用于双面及多层),预浸酚醛或环氧树脂,表层一面或两面粘上覆铜簿再层压固化而成。
这种PCB,线路板覆铜簿板材,我们就称它为刚性板。
再制成印制PCB,线路板,我们就称它为刚性印制PCB,线路板。
单面有印制线路图形我们称单面印制线路板,双面有印制线路图形,再通过孔的金属化进行双面互连形成的印制线路板,我们就称其为双面板。
如果用一块双面作内层。
二块单面作外层或二块双面作内层。
二块单面作外层的印制线路板,通过定位系统及绝缘粘结材料交替在一起且导电图形按设计要求进行互连的印制线路板就成为四层。
六层印制电路板了,也称为多层印制线路板。
pcb图形电镀工艺教材

图形电镀工艺教材一. 图形电镀简介:在平板电镀后,板件经过干膜曝光显影后需要经过图形电镀。
图形电镀的目的在于加大线路和孔内铜厚(主要是孔铜厚度),确保其导电性能和其他物理性能。
根据不同客户不同板件的性能要求,一般孔壁铜厚在0.8mil-1.2mil之间(平板层+图电层),由板件特性决定其平板层和图电层的分配。
一般来说,平板电镀层仅保证可以保护稀薄的沉铜层即可,一般在0.3mil-0.4mil左右,特殊铜厚要求和线路分布不均除外,图形层则保证在0.4-0.6mil,在保证总铜厚的基础上,如果图形分布均匀,比较厚的图形层可以节省铜球耗用和蚀刻成本,提高蚀刻速度,降低蚀刻难度。
反之,如果线宽要求不严,而图形分布不均线路孤立,则可以提高平板层厚度,降低图形电镀层厚度。
图形电镀后是蚀刻流程。
二. 图形电镀基本流程:板件经过贴膜曝光显影后形成一定的线路,图形电镀就是针对干膜没有覆盖的铜面进行选择性加厚。
图形主要流程如下(水洗视条件不同,为一道至两道):进板—除油—水洗—微蚀—水洗—酸浸(硫酸)—电镀铜—水洗—酸浸(氟硼酸)—电镀(铅)锡—水洗—出板—退镀(蚀夹具)—水洗—进板1 .除油:电镀除油流程为酸性除油,主要是除去铜面表面的污物。
因板件经过干膜流程后,不可避免地会在板面带上手印、灰尘、油污等,为使板面洁净,保证平板铜层和图形铜层的层间结合力,必须在电镀前加上清洁板面的流程。
采用酸性环境除油效果比碱性除油差,但避免了碱性物质对有机干膜的攻击,主要成分为硫酸和供应商提供的电镀配套药水(安美特—FR,B图电\C图电\脉冲线;罗门哈斯—LP200,B(II)线;成分均为酸性表面活性剂)。
酸性除油剂的浓度测定是通过测定计算浓硫酸(98%)浓度来相对估算(无法直接测定,而配缸和消耗都是1:1比例),因此在换缸和补充的时候要保证两者要等量添加,以保证测定浓度和实际浓度的一致性。
2. 微蚀:除油的微蚀流程主要作用为去除表面和孔内的氧化层,并将铜层咬蚀出微观上粗糙的界面,以进一步提高图形电镀层和平板层的结合力。
- 1、下载文档前请自行甄别文档内容的完整性,平台不提供额外的编辑、内容补充、找答案等附加服务。
- 2、"仅部分预览"的文档,不可在线预览部分如存在完整性等问题,可反馈申请退款(可完整预览的文档不适用该条件!)。
- 3、如文档侵犯您的权益,请联系客服反馈,我们会尽快为您处理(人工客服工作时间:9:00-18:30)。
图形电镀制程目的
※制程目的
加厚线路及孔内铜厚,使产品达到 客户要求
图形电镀工艺流程
※工艺流程
上板→除油→水洗→微蚀→水洗→ 酸浸→镀铜→水洗→酸浸→镀锡→水 洗→下板→退镀→水洗→上板
图电工序主要工艺参数
流程 主要药水成分 主要工艺参数 作用 除油 Acid Cleaner ACD(ATO) 微蚀 NPS(过硫酸 钠)+H2SO4 酸浸 H2SO4 镀铜 CuSO4、Cl-、 H2SO4、光剂 镀锡 SnSO4、 H2SO4、光剂 操作温度:28-32℃、操作时间:清洁板面 3-5min、浓度:15%-20% 操作温度:24-28 ℃、操作时间: 去除氧化物、粗 1-2min、微蚀速率:0.7化铜面 1.3um/cycle 操作温度:室温、操作时间: 0.5-1min、浓度:7%-12% 去除轻微氧化及 维持药水浓度
退掉干膜
蚀刻 CuCl2 NH4Cl NH4Cl
蚀掉非线路铜层
总酸度:3.8-4.5N 退锡 SS-188(HNO3) 操作温度:20-38 ℃ 速度:2.0-4.0m/min 压力:1.8-2.2bar
退掉抗蚀层-镀 锡层
流程详解
※退膜
退膜制程所使用的化学药液以NaOH为 主,药液浓度在1-3%左右(重量比),槽 液温度在30-50℃左右。 之所以采用NaOH作为退膜药液主要是因 为其对已硬化的干膜有较好的溶解性能, 且价格低廉。
3、操作温度:28-32 ℃ 4、处理时间:3-5min
流程详解
※微蚀(Micro Etch)
1、流程目的:除去铜面上的氧化物,粗化 铜面,提高镀层结合力。 2、主要成分:过硫酸钠、硫酸 3、操作温度:24-28℃ 4、处理时间:1-2min
流程详解
※镀铜预浸(Pre-dip for Cu Plate)
流程详解
※碱性蚀刻
1、组成: 蚀刻液以氯化铜、氯化铵和氨水配成。 2、蚀刻原理: 在氯化铜溶液中加入氨水,发生络合反 应: CuCL2 + 4NH3 → Cu(NH3)4CL2 在蚀刻过程中,板面上的铜被 [Cu(NH3)4]2+络离子氧化,反应如下: Cu(NH3)4CL2 + Cu → 2Cu(NH3)2CL2
蚀刻工艺流程
※工艺流程
退膜→水洗→蚀刻→水洗→退锡 →水洗→烘干
蚀刻工序主要工艺参数
流程 主要药水成分 主要工艺参数 作用
退膜 NaOH
浓度:1.8%-3.0% 操作温度:28-50℃ 速度:2.0-4.0m/min 压力:2.0-2.5bar
比重:1.170-1.190 操作温度:48-52 ℃ 速度:2.0-5.0m/min 压力:1.5-3.3bar
1、流程目的:用稀硫酸除去铜表面的轻微 氧化;维持镀铜缸之酸度,减小镀铜缸成 份的变化。 2、主要成分:硫酸 3、操作温度:室温 4、处理时间:0.5-1min
流程详解
※镀铜(Copper Plate)
1、流程目的:在酸性硫酸铜镀液中,铜离 子不断的得电子被还原为金属铜,沉积在 板面及镀铜孔内,直至达到所需的厚度。 2、主要成分:硫酸、硫酸铜、氯离子、 Brightener 125T-2(R&H)、 Carrier 125-2(R&H) 3、操作温度:22-27℃ 4、处理时间:86min
流程详解
※镀锡预浸(Pre-dip for Tin Plate)
1、流程目的:用稀硫酸除去铜表面的轻微 氧化;维持镀锡缸之酸度,减小镀锡缸各 主要成分变化。 2、主要成分:硫酸 3、操作温度:室温 4、处理时间:0.5-1min
流程详解
※镀锡(Tin Plate)
1、流程目的:在酸性硫酸亚锡镀液中,亚 锡离子不断的得电子被还原为金属锡,沉 积在已经镀铜的板面及孔内,直至达到所 需的厚度。 2、主要成分:硫酸、硫酸亚锡 EC Part A(R&H) EC Part B(R&H) 3、操作温度:18-22℃ 4、处理时间:10m、药水类型: 硝酸型:放热轻微、沉淀较少、不腐蚀 环氧树脂表面、腐蚀铜基体少、板面光 亮。 2、反应原理: 4HON3 + Pb + OX → Pb(NO3) + R R + O2 → OX(氧化剂)
蚀刻线设备
待蚀刻的板
退膜后的板
蚀刻后的板
退锡后的板
流程详解
※夹具退铜(Rack Strip)
1、去除电镀夹具上的镀铜,方便下一循环 的电镀进行。 2、主要成分:硝酸 3、操作温度:室温 4、处理时间:5-8min
图形电镀设备
待图电的板
图电后的板
蚀刻工序
※制程目的
蚀掉非线路铜(底铜和板电层), 获得成品线路图形,使产品达到导通 的基本功能。
操作温度: 22-27℃、镀铜时间: 加厚铜 86min或更长 操作温度: 18-22℃、镀锡时间: 镀锡为碱性蚀刻 10min或更长 提供抗蚀层
退镀 HNO3
操作温度:室温、退镀时间: 5-8min
去除电镀夹具上 的镀铜
流程详解
※除油(Acid Clean)
1、流程目的:清洁铜面,去除上工序的 残膜及人手接触后的指印等油性污垢(使 用酸性溶液,以免使干膜受损)。 2、主要成分:Acid Cleaner ACD(ATO)
流程详解
3、蚀刻药水的再生: Cu(NH3)2CL2为Cu+的络离子,不具有蚀 刻能力,在有过量NH3和CL-的情况下,能很 快地被O2所氧化,生成具有蚀刻能力的 [Cu(NH3)4]2+络离子,反应如下: 2Cu(NH3)2CL2+2NH4CL+2NH3+1/2O2→ 2Cu(NH3)4CL2+H2O