进给系统的机械结构设计
进给系统之机械部件-精选

2020/2/29
装配前的准备工作
(1)装配前进行零件的清洗 ,获得所需的清洁度。 (2)为达到工艺上的装配精度要求 ,对有关零件进行刮削。 (3)对装配工作台面用框式水平仪、平尺对台面的平度、直线
度等进行校 正校平。 (4)某些部件(传动部分)应按图纸要求在装配前进行必要的
内循环
2020/2/29
外循环
滚珠丝杠的螺旋滚道型面
螺旋滚道型面(即滚道法向截形)的形状有多种,常见的截形有单圆弧 型面和双圆弧型面两种。如图3-9所示为螺旋滚道型面的简图,图中钢球 与滚道表面在接触点处的公法线与螺纹轴线的垂线间的夹角称为接触角 α,理想接触角α=45°。
2020/2/29
进给传动导轨
2020/2/29
谢谢观赏
组长:黄伟红 组员:张雪川、沈晓敏、吴达成、曾锦峰
2020/2/29
பைடு நூலகம்
2020/2/29
2020/2/29
电动机与丝杆间的连接
实现进给传动的电动机主要有三种:步进电动 机、直流伺服电动机和流伺服电动机。电动 机与丝杆间的联接主要有三种形式:
1)齿轮传动方式 2)同步带轮传动形式 3)联轴器传动型式
2020/2/29
装配工艺过程 在装配系统图的基础上 ,划分装配工序、规定 工序计划 (包括调整和检验工序) ,并按我所规 定的格式编制工艺过程卡。稳定平台的装内
运转试验 , 试验合格后 ,再投入装配。
2020/2/29
稳定平台装配中的一些具体要求
(1)大多数零部件的装配采用的是互换装配法。 (2)旋转零件 ,如齿轮和啮合间隙等 ,装配时采用调整或修配法。 (3)过盈连接件:如轴承、键、销钉等采用压入法 。轴承的轴向游隙,用垫圈 或锁紧螺母进行调整。 (4)根据测量误差 ,对照装配精度要求以调整法和修配法消除其偏差 。 (5)所有盖板在全部机构调整合格后 ,最后进行紧固、密封 ,电装在机装调整 合格后进行。 (6)装配工人技术水平 ,要求象稳定平台这样复杂的装配 ,需高级工以上的技 术等级 。 (7)环境条件的要求:工作场地 装配间 应有防尘、防振措施。 (8)各部件在总装之间和总装之后 ,均应经过严格检验和必要的试验 ,各工序 件间实行三检 ,严格工艺纪律。
数控车床进给系统设计

数控车床进给系统设计一、进给系统的结构设计1.可靠性高:进给系统的关键零部件应采用优质的材料和加工工艺,以保证系统的稳定性和长寿命。
2.刚性好:进给系统的结构应具备足够的刚度,以保证在高速切削和大负载的工况下,机床能够保持稳定运行。
3.灵活性强:设计时应考虑到不同工件的加工要求,进给系统应能够快速调整和变换,以满足不同工件的加工需求。
二、进给系统的控制方法设计1.PTP控制方式:即点对点控制方式,根据工件形状和切削要求设计程序,实现工件形状的控制和切削路径的规划。
2.直线插补控制方式:通过数学模型进行直线切削路径的插补计算,实现工件形状的控制和切削路径的规划。
3.圆弧插补控制方式:通过数学模型进行圆弧切削路径的插补计算,实现工件形状的控制和切削路径的规划。
三、进给系统的传动方式设计传统数控车床进给系统的传动方式有液压传动和蜗杆传动两种,在设计进给系统时需要选择合适的传动方式,以满足不同加工工况的需求。
1.液压传动:液压传动以其可适应性强、能源利用率高等优点,在高负载和高速切削的工况下表现出较好的性能。
2.蜗杆传动:蜗杆传动以其结构简单、体积小、传动精度高等优点,在精密加工和高速加工的场合得到广泛应用。
四、进给系统的反馈装置设计进给系统的反馈装置是保证机床加工精度的重要组成部分,主要分为位置反馈和力反馈两种。
设计反馈装置时需要考虑以下几个因素:1.精度要求:根据机床加工的精度要求选择合适的反馈装置,以保证加工精度的稳定性。
2.反馈方式:根据加工工况选择合适的反馈方式,如光电编码器、脉冲等。
3.反馈信号的处理:对反馈信号进行合理的滤波和放大处理,以保证控制系统的稳定性和精度。
总之,数控车床进给系统的设计直接影响机床的加工精度和工作效率。
在设计进给系统时应考虑到结构、控制方法、传动方式和反馈装置等方面的因素,以满足不同加工要求。
同时,还需要对系统进行可靠性和稳定性分析,以确保数控车床的长期稳定运行。
7 机床数控技术-第7章 进给系统的机械传动结构-JIN

7.2 齿轮传动副
1.圆柱齿轮传动消除间隙
图示为另一种双片齿轮周 向弹簧错齿消隙结构,两 片薄齿轮1和2套装一起, 每片齿轮各开有两条周向 通槽,在齿轮的端面上装 有短柱3,用来安装弹簧4。 装配时使弹簧4具有足够的 拉力,使两个薄齿轮的左 右面分别与宽齿轮的左右 面贴紧,以消除齿侧间隙。 适合读数装置,不适合驱 动装置。
6.滚珠丝杆副的支承方式 2)一端装止推轴承,另一端装向心深沟球轴承(双推-支承 式)
图7-16( b)一端装止推轴承,另一端装向心球轴承
此种方式可用于丝杠较长的情况。为了减少丝杠热变形的影 响,热源应远离推力轴承一端。
7.3 滚珠丝杠螺母传动装置及支承
6.滚珠丝杆副的支承方式 3)两端装推力轴承(单推—单推式或双推—单推式)
结构简单,工艺性好,承载 能力较高,但径向尺寸较大。应 用最为广泛,也可用于重载传动 系统。
7.3 滚珠丝杠螺母传动装置及支承
7.3.1
2)内循环反向器式
靠螺母上安装的反 向器接通相邻滚道, 使滚珠成单圈循环, 反向器2的数目与滚 珠圈数相等。
丝杠螺母尺寸较小、 结构紧凑,刚度好,滚 珠流通性好,摩擦损失 小,但制造较困难。适 用于高灵敏、高精度的 进给系统,不宜用于重 载传动中。
7.3 滚珠丝杠螺母传动装置及支承
4.滚珠丝杆副间隙的调整 1)双螺母垫片式消隙
调整垫片1的厚度,可使 两螺母2产生相对位移,以 达到消除间隙、产生预紧拉 力之目的。其特点是结构简 单刚度高、预紧可靠,但使 用中调整不方便。
(b)端部加垫片 (a)中间加垫片
7.3 滚珠丝杠螺母传动装置及支承
4.滚珠丝杆副间隙的调整 2)双螺母螺纹式消隙
7.1 概述 7.2 齿轮传动副 7.3 滚珠丝杠螺母传动装置及支承 7.4 数控机床导轨
数控机床原理与结构分析第5章数控机床的进给系统

contents
目录
• 引言 • 数控机床的进给系统原理 • 数控机床的进给系统结构 • 数控机床的进给系统性能分析 • 数控机床的进给系统维护与保养 • 结论
01 引言
数控机床的进给系统概述
数控机床的进给系统是实现切削加工的重要组成部分,它负 责将主轴的旋转运动传递到工作台或刀具上,以完成工件的 加工。
进给系统的热误差分析
热误差产生原因
热误差是由于进给系统在工作过程中受到热源影响,导致机械部件受热变形和温度升高, 从而影响进给系统的运动精度。热误差主要来源于传动元件、轴承、导轨等部件的受热
变形。
热误差补偿技术
为了减小热误差对进给系统性能的影响,可以采用热误差补偿技术。热误差补偿技术包括温 度检测、误差建模和补偿算法等环节,通过实时监测进给系统的温度变化,建立热误差模型
进给系统由电动机、传动装置、丝杠、工作台等组成,通过 控制电动机的旋转运动,经过一系列的传动装置,最终转化 为工作台或刀具的直线运动。
进给系统在数控机床中的重要性
进给系统是数控机床实现高精度、高效率加工的关键因素之一,其性能直接影响 着加工质量和生产效率。
随着现代制造业的发展,对数控机床的加工精度和效率要求越来越高,因此,对 进给系统的性能要求也越来越高。进给系统的性能优劣直接决定了数控机床的性 能和市场竞争力。
,并采用相应的补偿算法对热误差进行补偿,可以有效提高进给系统的运动精度。
05 数控机床的进给系统维护 与保养
进给系统的日常维护
每日检查
01
检查进给系统各部件是否正常,如导轨、丝杠、轴承等,确保
无异常声音和振动。
润滑保养
02
3.1进给伺服系统机械结构

2、滚珠丝杆的支承(图)
一端固定(F)一端自由(o)的支承形式,简 称F-O式(适用于短丝杠及垂直丝扛) 一端固定(F)一端浮动(s)的支承形式,简 称F—S式 (适用于较长丝杠或卧式丝枉) 两端固定的支承形式,简称F—F式 (适
用于长丝杠,以及对刚度相位移精度要求高的 场合 )
3、滚珠丝杠螺母副的预紧
图-滚珠导轨
图-滚柱导轨
图-支撑标准件
常见故障
现象:预警力掌握不当或调整时未达到
要求所造成的滚动导轨在工作中出现的 噪声过大、振动过大;导轨长度不均匀 而预紧力过大所造成的对导轨面的损伤。
措施:将导轨块紧固在可调的楔块或镶
条上。
导轨副的维护
1.间隙调整—保证导轨面之间合理的间隙, 小摩擦力大、磨损,大运动失去准确性和平 稳性、失去导向精度) 2.滚动导轨的预紧—提高刚度、消除间隙 3.导轨的润滑—降低摩擦系数、减少磨损、 防止导轨面锈蚀。 润滑方式:人工加油油杯供油、压力油润滑 润滑油:粘度变化小、润滑性好、油膜刚度
双螺母垫片调隙结构(结构简单,但调整较
费时,调整精度不高 )
双螺母螺纹调隙结构(结构简单) 双螺母齿差调隙结构(结构较为复杂,尺寸
较大,但是调整方便,可获得精确的调整量,预 紧可靠不会松动,适用于高精度传动。)
4、滚珠丝杠螺母副的制动
滚珠丝杠副的传动效率高,但不能 自锁,用在垂直传动或水平放置的高速 大惯量传动中,必须装有制动装置。常 用的制动方法有超越离合器、电磁摩擦 离合器或者使用具有制动装置的伺服驱 动电机。
轴向垫片调整法(图)
特点:调整较复杂,一般要经过几次修 磨才能调整好,且不能自动补偿消除间 隙。工作时只有一个齿轮承载。
XK5040数控铣床主轴箱、进给机构及控制系统设计
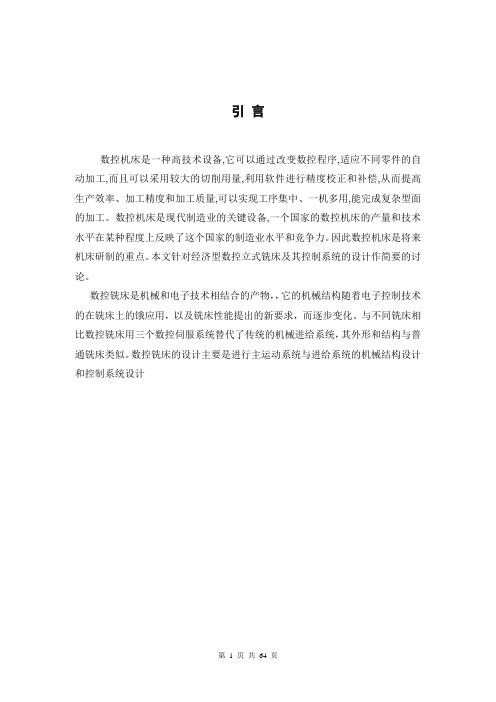
引言数控机床是一种高技术设备,它可以通过改变数控程序,适应不同零件的自动加工,而且可以采用较大的切削用量,利用软件进行精度校正和补偿,从而提高生产效率、加工精度和加工质量,可以实现工序集中、一机多用,能完成复杂型面的加工。
数控机床是现代制造业的关键设备,一个国家的数控机床的产量和技术水平在某种程度上反映了这个国家的制造业水平和竞争力。
因此数控机床是将来机床研制的重点。
本文针对经济型数控立式铣床及其控制系统的设计作简要的讨论。
数控铣床是机械和电子技术相结合的产物,,它的机械结构随着电子控制技术的在铣床上的饿应用,以及铣床性能提出的新要求,而逐步变化。
与不同铣床相比数控铣床用三个数控伺服系统替代了传统的机械进给系统,其外形和结构与普通铣床类似。
数控铣床的设计主要是进行主运动系统与进给系统的机械结构设计和控制系统设计第一章总体设计1.1、铣床简介铣床是一种用途广泛的机床。
它可以加工平面(水平面、垂直面等)、沟槽(键槽、T型槽、燕尾槽等)、多齿零件上齿槽(齿轮、链轮、棘轮、花键轴等)、螺旋形表面(螺纹和螺旋槽)及各种曲面。
此外,它还可以用于加工回转体表面及内孔,以及进行切断工作等。
由于铣床使用旋转的多齿刀具加工工件,同时有数个刀齿参加切削,所以生产效率高,但是,由于铣刀每个刀齿的切削过程是断续的,且每一个的切削厚度又是变化的,这就使切削力相应地发生变化,容易引起机床振动,因此,铣床在结构上要求有较高的刚度和抗振性。
铣床的类型很多,主要类型有:卧式升降台铣床、立式升降台铣床、龙门铣床、工具铣床和各种专门化铣床等。
随着科学技术的进步,数控铣床得到了越来越广泛的应用,它一般分为立式和卧式两种,一般数控铣床是指规格较小的升降台数控铣床,其工作台宽度多在400mm以下,规格较大的数控铣床,例如工作台宽度在500mm以上的,其功能已向加工中心靠近,进而演变成柔性制造单元。
数控铣床多为三坐标、两轴联动的机床,也称两轴半控制,即X、Y、Z三个坐标轴中,任意两个都可以联动。
MJ50数控车床X轴进给系统结构设计
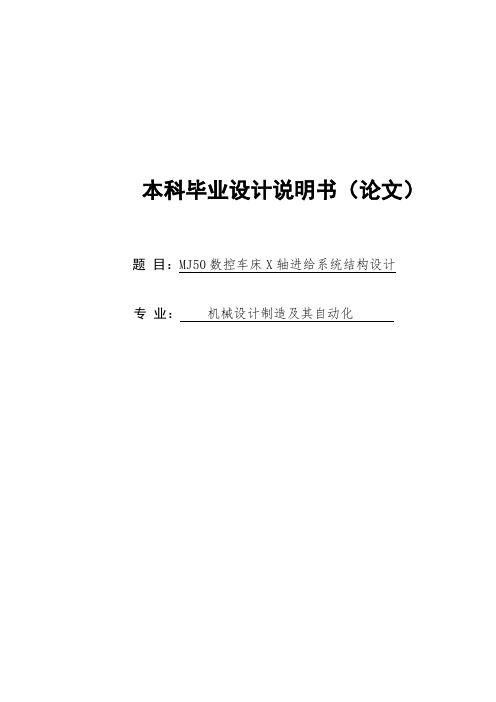
本科毕业设计说明书(论文)题目:MJ50数控车床X轴进给系统结构设计专业:机械设计制造及其自动化毕业设计说明书(论文)中文摘要摘要:本课题对MJ50型数控车床X轴进给系统结构进行了设计,数控车床的进给系统负责接收数控系统发出的脉冲指令,经放大和转换后驱动机床,执行预期的运动。
它的灵敏度和传动精度高,响应速度快且工作稳定,构件刚度高及使用寿命长,故进给系统结构有较高的研究意义。
MJ50是一种经济性数控车床,其X轴的主要结构零件包括伺服电机、滚珠丝杠、同步带、滚珠丝杠支承轴承、滚动导轨和限位挡块。
采用交流伺服电机,能在整个速度区内可实现平滑控制,几乎无振荡;采用低摩擦传动副,如滚动导轨和滚珠丝杠副,传动效率高,定位精度和重复定位精度高且传动有可逆性;采用同步带联接丝杠和电机,结构简单、传动平稳,能缓冲吸振,可以在大的轴间距和多轴间传递动力,结构紧凑,传动效率高。
关键词:进给系统滚珠丝杠导轨毕业设计说明书(论文)英文摘要Title Economical CNC latheAbstractThe subject of MJ50 numerical control lathe X axis feed system structure design, CNC lathe feed system is responsible for receiving CNC system a pulse instruction, after amplification and conversion drive machine, movement is expected to perform. Its sensitivity and transmission accuracy are high, the speed of response and the stability of the work, the stiffness of the component and the long service life, so the structure of the feed system has a higher research significance. MJ50 is a kind of economical numerical control lathe, its main structure parts of X axis include servo motor, ball screw, synchronous belt, ball screw bearing, rolling guide and limit stop block.. By AC servo motor, can realize the smooth control in the whole speed region, almost no oscillation; the low friction transmission pair, such as rolling guideway and ball screw pair, with high transmission efficiency, positioning accuracy and repeatability of positioning accuracy and high transmission is reversible;; low-friction transmission pair, such as rolling guide and ball screw, high transmission efficiency, high positioning accuracy and repeatability of positioning accuracy and reversible drive sex; with belt coupling screw and motor, simple structure, smooth transmission, can buffer the vibration absorption can transfer power between the major axis and multi-axis spacing, compact structure, high transmission efficiency. by synchronous belt connected with the screw rod and the motor, has the advantages of simple structure, stable transmission, buffering, vibration absorption, can be in large shaft distance and multiple shaft to transmit power, compact structure, transmission efficiency is high.Keywords axis feed drive system;ball screw; the guide way目录前言 (1)第一章绪论 (2)1.1 引言 (2)1.2 选题背景与意义 (3)1.3 研究现状 (3)1.3.1国内数控技术发展的现状 (3)1.3.2国外的数控车床发展 (4)第二章总体方案设计 (5)2.1 传动类型的选择 (5)2.2 伺服电机的选择 (6)2.3 电动机与丝杠连接方式的选择 (6)2.4 同步带的选择 (7)2.5 支撑方式及支撑轴承的选择 (7)2.5.1 丝杠有以下四种支撑方式 (7)2.5.2 支承轴承的选择 (8)第三章 X 向进给系统结构设计 (9)3.1 已知技术参数 (9)3.2 滚珠丝杠的设计计算及其选型 (9)3.2.1 主切削力的确定 (9)3.2.2 滚珠丝杠导程的确定 (10)3.2.2.1 确定丝杠的等效转速 (10)3.2.2.2 估算工作台质量以及工作台的承重 (10)3.2.2.3 确定丝杠的等效负载 (10)3.2.2.4 确定最大动载荷 (11)3.2.2.5 丝杠轴向压力选取丝杠底径 (12)3.2.2.6 最大转速限制 (12)3.2.2.7 选择丝杠直径 (12)3.2.2.8 选择滚珠丝杠型号 (12)3.3 伺服电机的计算 (13)3.3.1 电动机转速的确定 (13)3.3.2 理论动态预紧转矩 (13)3.3.3 最大动态摩擦力矩 (13)3.3.4 驱动最大负载所耗转矩 (13)3.3.5 支承轴承所需启动扭矩 (13)3.3.6 驱动滚珠丝杠副所需扭矩 (13)3.3.7 电机的额定转矩 (14)3.4 同步带的设计与计算 (14)3.4.1 确定计算功率 (14)3.4.2 确定带型,节距 (14)3.4.3 小带轮齿数 (15)3.4.4 带轮直径d1,d2的确定 (15)3.4.5 验算带速v (15)3.4.6 确定中心距a及带长Lp (15)3.4.7 计算小带轮的啮合齿数Zm (16)3.4.8计算基本额定功率P0 (16)3.4.9 确定带宽 (17)3.4.10 计算作用在轴上的载荷 (17)3.4.11 带的工作验算 (17)3.5. 轴承及轴承座选型 (17) (18)3.6. 校核 (19)3.6.1 临界压缩负荷 (19)3.6.2 临界转速3.6.3 丝杠拉压振动与扭转振动的固有频率 (20)3.6.4 丝杠扭转刚度 (21)3.6.5 传动精度计算 (21)第四章床身及导轨 (23)4.1 床身的选择 (23)4.2 导轨的选择 (23)4.2.1 导轨的分类 (23)4.2.2 导轨的选择 (24)4.2.3 导轨的间隙调整机构 (26)4.2.4 导轨的润滑 (27)4.2.5 导轨的防护 (27)第五章结论 (29)致谢 (31)参考文献 (33)前言计算机已经普遍成为现代数控技术中最基本的通讯工具,因为计算机具有很强高精密性,操作起来灵活简便,所以在最近这段时间已经越来越赢得广大用户的欢迎[1],数字控制机床简称CNC,每台数控机床上都会装有程序监控装置。
机械制造与自动化专业《数控机床进给系统机械结构》
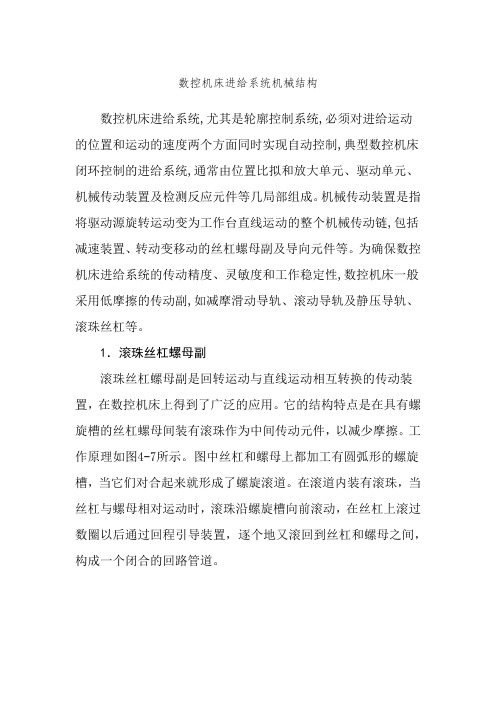
数控机床进给系统机械结构数控机床进给系统,尤其是轮廓控制系统,必须对进给运动的位置和运动的速度两个方面同时实现自动控制,典型数控机床闭环控制的进给系统,通常由位置比拟和放大单元、驱动单元、机械传动装置及检测反应元件等几局部组成。
机械传动装置是指将驱动源旋转运动变为工作台直线运动的整个机械传动链,包括减速装置、转动变移动的丝杠螺母副及导向元件等。
为确保数控机床进给系统的传动精度、灵敏度和工作稳定性,数控机床一般采用低摩擦的传动副,如减摩滑动导轨、滚动导轨及静压导轨、滚珠丝杠等。
1.滚珠丝杠螺母副滚珠丝杠螺母副是回转运动与直线运动相互转换的传动装置,在数控机床上得到了广泛的应用。
它的结构特点是在具有螺旋槽的丝杠螺母间装有滚珠作为中间传动元件,以减少摩擦。
工作原理如图4-7所示。
图中丝杠和螺母上都加工有圆弧形的螺旋槽,当它们对合起来就形成了螺旋滚道。
在滚道内装有滚珠,当丝杠与螺母相对运动时,滚珠沿螺旋槽向前滚动,在丝杠上滚过数圈以后通过回程引导装置,逐个地又滚回到丝杠和螺母之间,构成一个闭合的回路管道。
图4-7 滚珠丝杠副的原理图滚珠丝杠副的优点是摩擦系数小,传动效率高, 可达~,所需传动转矩小;灵敏度高,传动平稳,不易产生爬行,随动精度和定位精度高;磨损小,寿命长,精度保持性好;可通过预紧和间隙消除措施提高轴向刚度和反向精度;运动具有可逆性,不仅可以将旋转运动变为直线运动,也可将直线运动变为旋转运动。
缺点是制造工艺复杂,本钱高,在垂直安装时不能自锁,因而需附加制动机构。
〔1〕滚珠丝杠螺母副的结构滚珠的循环方式有外循环和内循环两种。
滚珠在返回过程中与丝杠脱离接触的为外循环;滚珠在循环过程中与丝杠始终接触的为内循环。
在内、外循环中,滚珠在同一个螺母上只有一个回路管道的叫单循环,有两个回路管道的叫双列循环。
循环中的滚珠叫工作滚珠,工作滚珠所走过的滚道圈数叫工作圈数。
外循环滚珠丝杠副按滚珠循环时的返回方式主要有插管式和螺旋槽式。
- 1、下载文档前请自行甄别文档内容的完整性,平台不提供额外的编辑、内容补充、找答案等附加服务。
- 2、"仅部分预览"的文档,不可在线预览部分如存在完整性等问题,可反馈申请退款(可完整预览的文档不适用该条件!)。
- 3、如文档侵犯您的权益,请联系客服反馈,我们会尽快为您处理(人工客服工作时间:9:00-18:30)。
课程设计(论文)任务书设计题目:进给系统的机械结构设计姓名系别专业班级学号指导老师教研室主任一、基本任务及要求:本课题是以卧式车床C6150为改造对象,以其进给系统的改造设计为主要任务。
主要设计内容包括:进给系统的改造方案拟定(主要技术参数及主要结构方案),步进电机选型,进给系统机械结构的设计计算、部件选型,滚珠丝杆的验算等。
通过设计使大家掌握机械设备机电一体化改造的原理、步骤及内容,熟悉改造过程的有关分析与计算的方法,并达到以下具体要求:1、了解卧式车床的基本结构,工作原理;2、掌握数控机床进给传动系统伺服控制的基本原理,熟悉机械系统中各零件的设计计算方法,内容等;3、根据计算结果,进行进给系统机械结构的设计,画出系统装配图及主要零件图。
4、通过设计说明书的编写训练,使学生掌握工程技术文件的编写。
二、进度安排及完成时间:1、下达设计任务,收集并查阅相关资料,分析、熟悉课题 1天2、拟定进给系统的总体方案,进行必要计算 4天3、进行进给系统机械结构设计,画装配图 6天4、按格式编写设计说明书、制作存储介质(分组刻盘) 3天5、资料汇总,答辩 1天目录第1章绪论 ---------------------------------------------------------------------------------------------------- 1 第2章总体改造方案 ------------------------------------------------------------------------------------------- 22.1 总体方案的拟定 --------------------------------------------------------------------------------------- 2 第3章进给系统机械结构的设计计算 --------------------------------------------------------------------- 33.1 滚珠丝杠的设计计算与选用 ----------------------------------------------------------------------- 33.1.1 滚珠丝杠副的介绍及特点------------------------------------------------------------------ 33.1.2 滚珠丝杠设计与计算----------------------------------------------------------------------- 3 第4章减速齿轮的设计与校核------------------------------------------------------------------------------ 104.1 减速齿轮的设计 -------------------------------------------------------------------------------------- 104.1.1选择齿轮材料及精度等级------------------------------------------------------------------ 104.1.2 按齿面接触疲劳强度设计 ----------------------------------------------------------------- 104.2 减速齿轮的校核 -------------------------------------------------------------------------------------- 114.2.1按齿根弯曲疲劳强度校核------------------------------------------------------------------ 114.2.2验算齿轮得圆周速度V --------------------------------------------------------------------- 12 第5章电机的计算与选择------------------------------------------------------------------------------------ 135.1电机的计算 --------------------------------------------------------------------------------------------- 135.1.1等效转动惯量计算 --------------------------------------------------------------------------- 135.1.2相关力矩及转矩计算 ------------------------------------------------------------------------ 145.2 步进电机的选择 -------------------------------------------------------------------------------------- 155.2.1步进电动机的匹配选择 --------------------------------------------------------------------- 15 第6章自动转位刀架的选用--------------------------------------------------------------------------------- 16 第7章小结------------------------------------------------------------------------------------------------------- 18 参考文献 ----------------------------------------------------------------------------------------------------------- 19 附录 ----------------------------------------------------------------------------------------------------------------- 20 纵向进给传动机构装配图 ------------------------------------------------------------------------------- 20第1章绪论目前, 在我国的机电行业中, 有一些技术含量较低的普通机床还在继续使用,它们普遍的特点是设备陈旧、操作控制复杂、生产效率较低。
随着当今工业设备对精密程度的要求越来越高,对机械加工设备的加工精密程度也要求越来越高,而在中国的机械加工设备的车床中普通车床占了很大比例。
这已经越来越制约着当今工业的发展,形势上要求用生产效率较高, 操作方便的数控机床来替代普通机床。
而数控机床由于价格昂贵,且需要较高技术的加工工人,所以对普通机床进行数控化改造是很有必要的。
本设计是在普通卧式车床C6150的基础上对其进行数控化改造。
企业要在当前市场需求多变, 竞争激烈的环境中生存和发展就需要迅速地更新和开发出新产品, 以最低价格、最好的质量、最短的时间去满足市场需求的不断变化。
而普通机床已不适应多品种、小批量生产要求, 数控机床则综合了数控技术、微电子技术、自动检测技术等先进技术,最适宜加工小批量、高精度、形状复杂、生产周期要求短的零件。
因此,这更强化了对普通机床进行数控化改造的必要性。
C6150车床进给系统的数控化改造主要内容如下:普通车床的X轴和Z轴均由同一电机驱动,走刀运动是经进给箱传动丝杠到溜板箱,获得不同的工件螺距即Z轴运动;走刀运动是经进给箱传动光杆到溜板箱,获得不同的进刀量即Z轴运动和X轴运动。
车床进给系统数控化改造要拆除进给箱总成、溜板箱总成,改用进给伺服(或步进)传动链分别代替。
具体体现为:纵向电机→减速箱(或联轴器)→纵向滚珠丝杠→中拖板,纵向按数控指令获得不同的走刀量和螺距。
改造后整个传动链的传动精度在保证机床刚性的前提下,与滚珠丝杠副的选择和布置结构形式、机床导轨的精度情况等有很大的关系。
第2章总体改造方案2.1 总体方案的拟定伺服驱动系统分开环控制、闭环控制及半闭环控制,根据的各种伺服系统的特点,从加工精度、结构、成本等多方面着手,考虑到C6150数控机床的加工精度要求不高,为了简化结构、降低成本,决定选用直流伺服电机驱动的开环伺服系统。
根据机床的运动精度,改动尽量少,且保证加工精度的要求,运动的平稳。
本车床的纵向进给系统去掉了原来的进给系统的中间传动环节,直接采用了步进电机+减速箱(或联轴器)+滚珠丝杠的传动方案。
拆除原来的进给箱、丝杆等,增加少量的机械附件,就可安装步进电机及滚珠丝杠螺母副。
图2.1 纵向进给传动及控制示意图第3章 进给系统机械结构的设计计算3.1 滚珠丝杠的设计计算与选用3.1.1 滚珠丝杠副的介绍及特点滚珠丝杠副是螺旋传动方式,它的作用是将回旋运动变为直线运动,因此在改造中选用滚珠丝杠副来达到直线运动的目的。
滚珠丝杠副具有如下特点:(1)传动平稳:滚珠丝杠副在工作过程中摩擦阻力小,灵敏度高,而且摩擦系数几乎与运动速度无关,启动摩擦力矩与运动时的摩擦力矩的差别很小。
所以滚珠丝杠副运动平稳,启动时无颤动,低速时无爬行。
(2)传动效率高:滚珠丝杠的传动效率可达85%~98%,为滑动丝杠副的2~4倍。
(3)可预紧,便于消除传动间隙。
(4)定位精度高:由于滚珠丝杆副具有传动效率高,运动平稳,可以预紧等特点,所以滚珠丝杠副在工作中温升较小,无爬行,并可以消除轴向间隙和对丝杠进行预紧拉伸以补偿膨胀,能获得较高的定位精度。
较之以上还有寿命长、温升低、运动摩擦小、磨损小等特点。
3.1.2 滚珠丝杠设计与计算已知条件:工作台重1W =80Kg=800N ,工件及夹具最大重量2W =200N ,工作台最大行程K l =950mm,工作台导轨的摩擦系数为u=0.1,快速进给速度max V =4 m/min,定位精度为 20um/300mm,全行程 25um,重复定位精度为10um,要求寿命为10,000小时。