金属疲劳应力腐蚀试验及宏观断口分析
综述-铝合金疲劳及断口分析报告
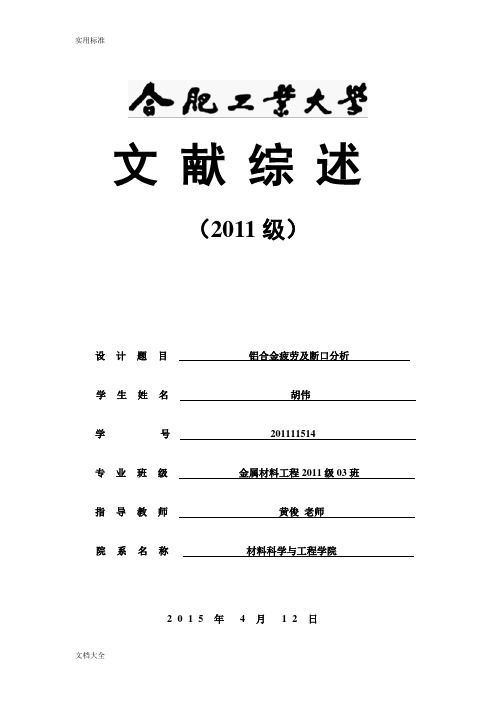
文献综述(2011级)设计题目铝合金疲劳及断口分析学生姓名胡伟学号*********专业班级金属材料工程2011级03班指导教师黄俊老师院系名称材料科学与工程学院2015年4月12日铝合金疲劳及断口分析1 绪论1.1 引言7系铝合金包括Al-Zn-Mg 系和Al-Zn-Mg-Cu 系合金,此类合金具有密度低、比强度高、良好的加工性能及优良的焊接性能等一系列优点。
随着应用在铝合金上的热处理工艺及微合金化技术的不断改进,其力学性能被大幅度强化,综合性能也得到了全面提升。
在航空航天、建筑、车辆、、桥梁、工兵装备和大型压力容器等方面都得到了广泛的应用。
现代工业的飞速发展,对7 系铝合金的强度、韧性以及抗应力腐蚀性能等提出了更高的要求。
但是,存在另外一个现象,在各行各业的领域中,铝合金设备偶尔会出现难以察觉的断裂,在断裂之前很难甚至无法察觉到一点塑性变形。
这种断裂形式,对人身以及财产安全造成了不可挽回的损失。
经过大量实验表明,这些断裂是由于材料的疲劳引起,材料在交变载荷的长期作用下,表面或者内部,尤其是内部会产生微观裂纹。
本文主要研究铝合金疲劳引起的裂纹以及疲劳断口分析,此类研究对于日后的生产安全,有重大意义。
1.2 7系铝合金的发展历史在20世纪20年代,德国的科学家研制出Al-Zn-Mg系合金,由于该合金抗应力腐蚀性能太差,并未得到产业内应用。
在20世纪30年代初一直到二战结束期间,各个国家在研究中发现,Cu元素可以提高铝合金的抗应力腐蚀性能。
在此,开发了大量Al-Zn-Mg 系合金,因此忽视了对Al-Zn-Mg 系合金的研究。
德、美、苏、法等国在Al-Zn-Mg-Cu 系合金基础上成功地开发了7075 、B93 和D。
T。
D683 等合金。
目前正广泛应用在航空航天事业上,但是强度、韧性、抗应力腐蚀性能三者之间未能实现最佳组合状态。
20世纪50年代,德国科学家公布了具有优良焊接性能的合金AlZnMg1 和AlZnMg2,引起了人们对Al-Zn-Mg系合金的重视。
综述-铝合金疲劳及断口分析报告
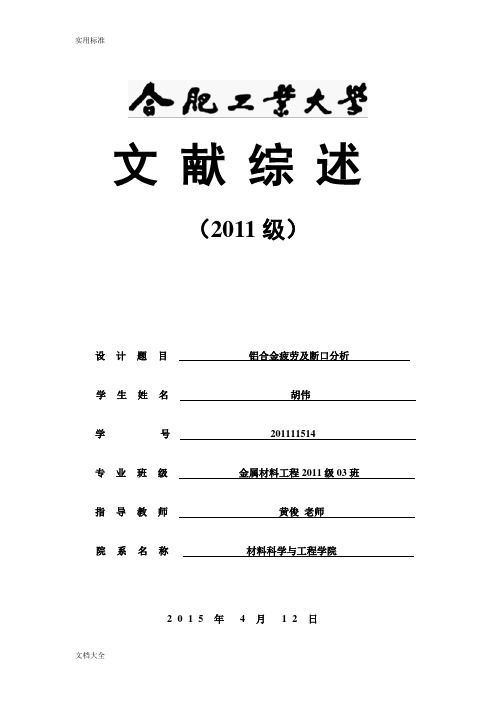
文献综述(2011级)设计题目铝合金疲劳及断口分析学生姓名胡伟学号*********专业班级金属材料工程2011级03班指导教师黄俊老师院系名称材料科学与工程学院2015年4月12日铝合金疲劳及断口分析1 绪论1.1 引言7系铝合金包括Al-Zn-Mg 系和Al-Zn-Mg-Cu 系合金,此类合金具有密度低、比强度高、良好的加工性能及优良的焊接性能等一系列优点。
随着应用在铝合金上的热处理工艺及微合金化技术的不断改进,其力学性能被大幅度强化,综合性能也得到了全面提升。
在航空航天、建筑、车辆、、桥梁、工兵装备和大型压力容器等方面都得到了广泛的应用。
现代工业的飞速发展,对7 系铝合金的强度、韧性以及抗应力腐蚀性能等提出了更高的要求。
但是,存在另外一个现象,在各行各业的领域中,铝合金设备偶尔会出现难以察觉的断裂,在断裂之前很难甚至无法察觉到一点塑性变形。
这种断裂形式,对人身以及财产安全造成了不可挽回的损失。
经过大量实验表明,这些断裂是由于材料的疲劳引起,材料在交变载荷的长期作用下,表面或者内部,尤其是内部会产生微观裂纹。
本文主要研究铝合金疲劳引起的裂纹以及疲劳断口分析,此类研究对于日后的生产安全,有重大意义。
1.2 7系铝合金的发展历史在20世纪20年代,德国的科学家研制出Al-Zn-Mg系合金,由于该合金抗应力腐蚀性能太差,并未得到产业内应用。
在20世纪30年代初一直到二战结束期间,各个国家在研究中发现,Cu元素可以提高铝合金的抗应力腐蚀性能。
在此,开发了大量Al-Zn-Mg 系合金,因此忽视了对Al-Zn-Mg 系合金的研究。
德、美、苏、法等国在Al-Zn-Mg-Cu 系合金基础上成功地开发了7075 、B93 和D。
T。
D683 等合金。
目前正广泛应用在航空航天事业上,但是强度、韧性、抗应力腐蚀性能三者之间未能实现最佳组合状态。
20世纪50年代,德国科学家公布了具有优良焊接性能的合金AlZnMg1 和AlZnMg2,引起了人们对Al-Zn-Mg系合金的重视。
金属疲劳断口的宏现形状特征
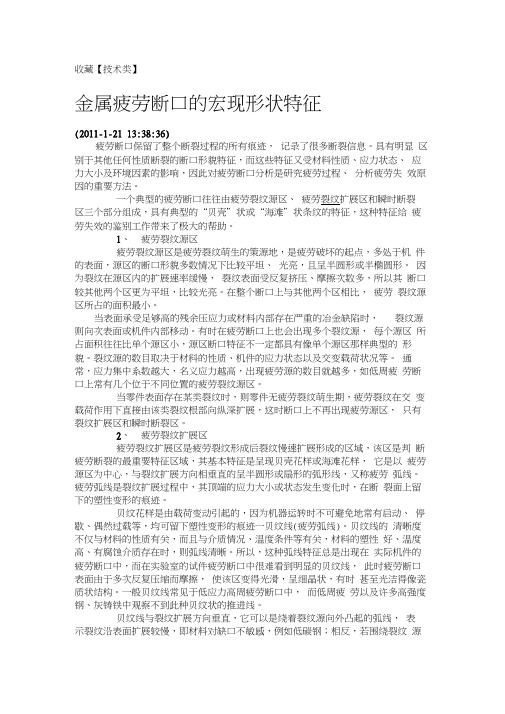
收藏【技术类】金属疲劳断口的宏现形状特征(2011-1-21 13:38:36)疲劳断口保留了整个断裂过程的所有痕迹,记录了很多断裂信息。
具有明显区别于其他任何性质断裂的断口形貌特征,而这些特征又受材料性质、应力状态、应力大小及环境因素的影响,因此对疲劳断口分析是研究疲劳过程、分析疲劳失效原因的重要方法。
一个典型的疲劳断口往往由疲劳裂纹源区、疲劳裂纹扩展区和瞬时断裂区三个部分组成,具有典型的“贝壳”状或“海滩”状条纹的特征,这种特征给疲劳失效的鉴别工作带来了极大的帮助。
1、疲劳裂纹源区疲劳裂纹源区是疲劳裂纹萌生的策源地,是疲劳破坏的起点,多处于机件的表面,源区的断口形貌多数情况下比较平坦、光亮,且呈半圆形或半椭圆形。
因为裂纹在源区内的扩展速率缓慢,裂纹表面受反复挤压、摩擦次数多,所以其断口较其他两个区更为平坦,比较光亮。
在整个断口上与其他两个区相比,疲劳裂纹源区所占的面积最小。
当表面承受足够高的残余压应力或材料内部存在严重的冶金缺陷时,裂纹源则向次表面或机件内部移动。
有时在疲劳断口上也会出现多个裂纹源,每个源区所占面积往往比单个源区小,源区断口特征不一定都具有像单个源区那样典型的形貌。
裂纹源的数目取决于材料的性质、机件的应力状态以及交变载荷状况等。
通常,应力集中系数越大,名义应力越高,出现疲劳源的数目就越多,如低周疲劳断口上常有几个位于不同位置的疲劳裂纹源区。
当零件表面存在某类裂纹时,则零件无疲劳裂纹萌生期,疲劳裂纹在交变载荷作用下直接由该类裂纹根部向纵深扩展,这时断口上不再出现疲劳源区,只有裂纹扩展区和瞬时断裂区。
2、疲劳裂纹扩展区疲劳裂纹扩展区是疲劳裂纹形成后裂纹慢速扩展形成的区域,该区是判断疲劳断裂的最重要特征区域,其基本特征是呈现贝壳花样或海滩花样,它是以疲劳源区为中心,与裂纹扩展方向相垂直的呈半圆形或扇形的弧形线,又称疲劳弧线。
疲劳弧线是裂纹扩展过程中,其顶端的应力大小或状态发生变化时,在断裂面上留下的塑性变形的痕迹。
金属断口分析
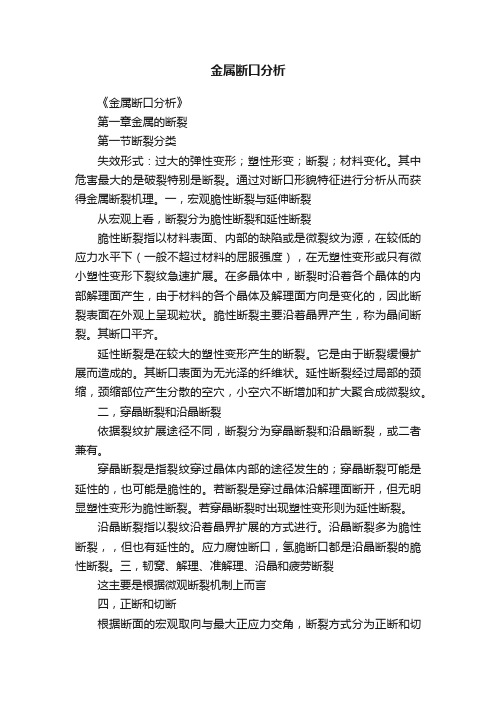
延性断裂为金属材料在过载负荷的作用下,局部发生明显的宏观塑性变形后断裂。延性断裂分两种,一种是韧窝-微孔聚集型断裂;另一种是滑移分类断裂。一些高强度材料其裂缝扩展阻力较小,对裂纹十分敏感,较小的裂纹
即可使其产生宏观脆性的低应力断裂,其断口为韧窝状,断裂机制是微孔聚
集型。
第一节韧窝断口的宏观形貌特征
从宏观上看,断裂分为脆性断裂和延性断裂
脆性断裂指以材料表面、内部的缺陷或是微裂纹为源,在较低的应力水平下(一般不超过材料的屈服强度),在无塑性变形或只有微小塑性变形下裂纹急速扩展。在多晶体中,断裂时沿着各个晶体的内部解理面产生,由于材料的各个晶体及解理面方向是变化的,因此断裂表面在外观上呈现粒状。脆性断裂主要沿着晶界产生,称为晶间断裂。其断口平齐。
此外,高强度马氏体钢纤维区还有环状花样特征。
第二节韧窝断口的微观形貌特征
韧窝断口的微观特征是一些大小不等的圆形或是椭圆形的凹坑(即韧窝)
在韧窝内经常看到夹杂物或是第二相粒子。
凹坑形状有等轴韧窝、剪切韧窝和撕裂韧窝三种,其形状与应力状态。
等轴韧窝是圆形微坑,在拉伸正应力作用下形成的。应力在整个断口表面分布均匀。
2.分叉法
样品断裂中,产生许多分叉,裂纹分叉的方向为裂纹扩展方向,扩展的反方向为裂源位置。
【注】T型法和分叉法是判别脆性断裂的主裂纹和裂纹源
3.变形法
延性断裂的样品,在断裂过程中发生变形后碎成几块,将碎片拼合后变形量大的部位为主裂纹,裂纹源在主裂纹所在的断口上
4.因环境因素引起的断裂的样品,如应力腐蚀、氢脆。裂纹源位于腐蚀或是
延性断裂是在较大的塑性变形产生的断裂。它是由于断裂缓慢扩展而造成的。其断口表面为无光泽的纤维状。延性断裂经过局部的颈缩,颈缩部位产生分散的空穴,小空穴不断增加和扩大聚合成微裂纹。
综述-铝合金疲劳及断口分析

文献综述(2011级)设计题目铝合金疲劳及断口分析学生胡伟学号201111514专业班级金属材料工程2011级03班指导教师黄俊老师院系名称材料科学与工程学院2015年4月12日铝合金疲劳及断口分析1 绪论1.1 引言7系铝合金包括Al-Zn-Mg 系和Al-Zn-Mg-Cu 系合金,此类合金具有密度低、比强度高、良好的加工性能及优良的焊接性能等一系列优点。
随着应用在铝合金上的热处理工艺及微合金化技术的不断改进,其力学性能被大幅度强化,综合性能也得到了全面提升。
在航空航天、建筑、车辆、、桥梁、工兵装备和大型压力容器等方面都得到了广泛的应用。
现代工业的飞速发展,对7 系铝合金的强度、韧性以及抗应力腐蚀性能等提出了更高的要求。
但是,存在另外一个现象,在各行各业的领域中,铝合金设备偶尔会出现难以察觉的断裂,在断裂之前很难甚至无法察觉到一点塑性变形。
这种断裂形式,对人身以及财产安全造成了不可挽回的损失。
经过大量实验表明,这些断裂是由于材料的疲劳引起,材料在交变载荷的长期作用下,表面或者部,尤其是部会产生微观裂纹。
本文主要研究铝合金疲劳引起的裂纹以及疲劳断口分析,此类研究对于日后的生产安全,有重大意义。
1.2 7系铝合金的发展历史在20世纪20年代,德国的科学家研制出Al-Zn-Mg系合金,由于该合金抗应力腐蚀性能太差,并未得到产业应用。
在20世纪30年代初一直到二战结束期间,各个国家在研究中发现,Cu元素可以提高铝合金的抗应力腐蚀性能。
在此,开发了大量Al-Zn-Mg 系合金,因此忽视了对Al-Zn-Mg 系合金的研究。
德、美、、法等国在Al-Zn-Mg-Cu 系合金基础上成功地开发了7075 、B93 和D。
T。
D683 等合金。
目前正广泛应用在航空航天事业上,但是强度、韧性、抗应力腐蚀性能三者之间未能实现最佳组合状态。
20世纪50年代,德国科学家公布了具有优良焊接性能的合金AlZnMg1 和AlZnMg2,引起了人们对Al-Zn-Mg系合金的重视。
金属疲劳破坏机理及断口分析

第三章金属疲劳破坏机理及断口分析一、疲劳宏观断口•1、疲劳断口的特征•疲劳断口宏观来看由两个区域组成:疲劳裂纹产生及扩展区和最后断裂区。
图1、疲劳断裂宏观断口(a)旋转弯曲试样疲劳断口(b)疲劳断口示意图•(1)疲劳裂纹产生及扩展区•由于材料的质量、加工缺陷或结构设计不当等原因,在零件或试样的局部区域造成应力集中,这些区域便是疲劳裂纹核心产生的策源地。
•疲劳裂纹产生后,在交变应力作用下继续扩展长大。
常常留下一条条的同心弧线,叫做前沿线(疲劳线),这些弧线形成了象“贝壳”一样的花样,也称为贝纹区。
断口表面因反复挤压、摩擦,有时光亮得象细瓷断口一样。
•(2)最后断裂区•疲劳裂纹不断扩展,使得零件或试样有效断面逐渐减少,应力不断增加,当应力超过材料的断裂强度时,则发生断裂,形成最后断裂区。
•对于塑性材料,断口为纤维状,呈暗灰色。
•对于脆性材料则是结晶状。
2、影响疲劳断口的因素•(1)试样或零件所受载荷类型。
•(2)试样或零件所受应力的大小。
•(3)应力集中因素。
图2、平板试样拉压疲劳断口形态示意图(a)平板试样;(b)带缺口的平板试样图3、各类疲劳断口形态的示意图二、金属疲劳破坏机理•疲劳裂纹的产生•金属所受交变应力的最大值低于材料的屈服强度,为什么会产生疲劳断裂呢?为了搞清楚金属疲劳断裂的本质,通常是在消除外界应力集中的情况下,研究金属疲劳的微观变化,从而提高疲劳抗力的途径。
图4、静拉伸和交变载荷下的滑移带(a)静拉伸(σ>σ0.2)(b)交变应力(σ=σ-1,N=105次)•从图4可以看出,静拉伸试样表面上到处布满细密的滑移带。
交变载荷下,经过应力循环之后,只有部分晶粒的局部地方出现细滑移带,表现为滑移的不均匀性。
这种滑移的不均匀性通常集中在金属表面、金属的晶界及金属夹杂物等处,并在该处形成疲劳裂纹核心。
•图5低碳钢经过不同循环次数后形成的滑移带。
图5、低碳钢在交变应力下(σ=σ-1)滑移带的发展(a)N=104次;(b)N=2×106次图6、低碳钢(σ=2σ-1)形成的滑移带(a)N=6×104次;(b)电解抛光后留下的“驻留滑移带”图7、交变应力下金属表面形成的“挤出脊”及“挤入沟”•驻留滑移带、挤出脊、挤入沟等,都是金属在交变载荷作用下表面不均匀滑移造成的疲劳裂纹核心策源地。
疲劳断口的宏观形貌特征.
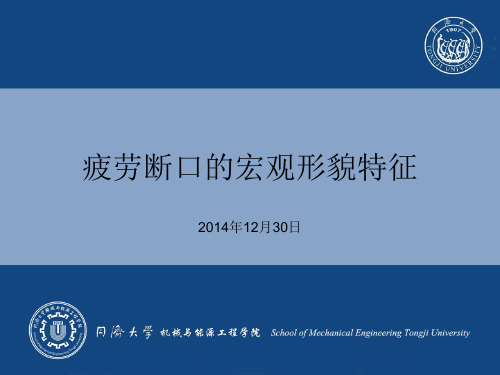
疲劳源位于构件的表面 • o o o
疲劳源位于内部缺陷处
疲劳裂纹萌生的原因: 裂纹构件结构形状不合理:截面突变、拐角、缺口等; 构件表面的晶粒粗大等组织缺陷,或者表面存在切削刀痕或划伤等工艺缺陷; 若在材料的内部存在严重的冶金缺陷如夹渣、疏松时疲劳源也可能在此处产生。
谢谢!
• 为什么要进行疲劳断口分析? 断口总是发生在金属组织中最薄弱的地方,记录着有关 断裂全过程的许多珍贵资料。借助断口可以分析断裂类型、 断裂方式、断裂路径、断裂过程、断裂性质、断裂原因和断 裂机理,所以对断口的观察和研究一直受到重视。 疲劳断口提供了大量信息,由断口可分析裂纹起因、扩 展信息、临界裂纹尺寸、破坏载荷等,是疲劳失效分析的重 要依据。 断口的宏观形貌特征 • 疲劳断口分析的实验基础: 对断口表面的宏观形貌和微观结构特征进行直接观察和 分析。
• 观察方法: 按照观察工具的不同,可以大致分为三类: o 肉眼或者放大镜观察——1~10x o 使用金相显微镜观察——10~1000x o 使用电子显微镜观察——1000x以上
断口的微观结构特征
疲劳断口的观察方法
• 观察工具和能观察到的对象: 肉眼、放大镜 金相显微镜 电子显微镜
观察工具
放大倍数 观察对象
疲劳断口的宏观形貌特征
• 疲劳源 疲劳源区是疲劳裂纹的萌生地,该区一般位于构件的表面或内部缺陷处,可能 一个,也可能多个。
疲劳源位于构件的表面
疲劳源位于内部缺陷处
疲劳源位于构件的表面
在断口上无法明显的看到裂纹萌生的许多细节,但是疲劳断口的整体形貌特征 仍可确定疲劳源的大体位置。
疲劳断口的宏观形貌特征
疲劳断口宏观分析

.1 疲劳断口的形貌特征疲劳断口是指金属材料或零构件在疲劳断裂过程中形成的一种匹配的表面,称断裂面或断口。
分析它的目的在于确定零构件是否属于疲劳破坏?其破坏的原因是什么?从而提出防止事故的措施和方法,为今后的设计、选材以及加工等问题提出改进意见。
对断口的形貌进行分析包括两个方面,即宏观断口分析和微观断口分析。
所谓宏观分析是指用肉眼或20—30倍以下放大镜观察断口的形貌特征。
微观分析是指用光学显微镜或电子显微镜对断口进行分析。
宏观分析不要求专门设备,被观察断口尺寸不受限制,可以观察断件和断口全貌,了解各个方面变化情况,所以说宏观分析是断口分析的基础。
微观分析是用高倍的光学显微镜、c透射电镜,扫描电镜对断口进行分析,能观察断口的精细结构及裂纹形态。
1.1 疲劳断口宏观特征由于零构件经常承受拉、压、弯、扭或复合应力的作用,因载荷类型不同,在宏观断口上表现出的形貌特征也不相同。
(1)弯曲应力作用下的疲劳断口图1-2是在弯曲疲劳载荷作用下的断口示意图。
零件在弯曲疲劳载荷作用下,其表面应力最大,中心应力最小,疲劳源首先在表面形成,然后沿着与最大正应力相垂直方向扩展,到最后瞬断。
图中(a)是单向弯曲疲劳断口,它的疲劳源首先在受拉应力一侧表面形成,瞬断区在疲劳源相对侧,其面积大小由材料抗拉强度和外加载荷的大小来决定。
图中(b)是双向弯曲疲劳断口,由于双向弯曲,试件上下两侧交替承受拉应力作用,故疲劳源在相对两侧面形成,瞬断区在中间。
.页脚...图1-3是轴在旋转弯曲应力作用下的疲劳断口示意图,由于旋转弯曲应力也是表面最大,中心最小,疲劳源也开始于表面,且疲劳源两侧裂纹发展速度较中心快,故贝纹线比较扁平。
最终瞬断区虽然也在疲劳源对面,但总是相对于轴的旋转方向逆偏转一个角度,此种现象称为偏转现象。
因此,从疲劳源与瞬断区的相对位置便能推知轴的旋转方向。
轴上有无应力集中及应力集小,其最终瞬断区的位置是不同的。
若应力集中若应力集中最终瞬断区在疲劳源相对应的一侧。
- 1、下载文档前请自行甄别文档内容的完整性,平台不提供额外的编辑、内容补充、找答案等附加服务。
- 2、"仅部分预览"的文档,不可在线预览部分如存在完整性等问题,可反馈申请退款(可完整预览的文档不适用该条件!)。
- 3、如文档侵犯您的权益,请联系客服反馈,我们会尽快为您处理(人工客服工作时间:9:00-18:30)。
金属疲劳、应力腐蚀试验及宏观断口分析
在足够大的交变应力作用下,由于金属构件外形突变或表面刻痕或内部缺陷等部位,都可能因较大的应力集中引发微观裂纹。
分散的微观裂纹经过集结沟通将形成宏观裂纹。
已形成的宏观裂纹逐渐缓慢地扩展,构件横截面逐步削弱,当达到一定限度时,构件会突然断裂。
金属因交变应力引起的上述失效现象,称为金属的疲劳。
静载下塑性性能很好的材料,当承受交变应力时,往往在应力低于屈服极限没有明显塑性变形的情况下,突然断裂。
疲劳断口(见图1-1)明显地分为三个区域:裂纹源区、较为光滑的裂纹扩展区和较为粗糙的断裂区。
裂纹形成后,交变应力使裂纹的两侧时而张开时而闭合,相互挤压反复研磨,光滑区就是这样形成的。
载荷的间断和大小的变化,在光滑区留下多条裂纹前沿线。
至于粗糙的断裂区,则是最后突然断裂形成的。
统计数据表明,机械零件的失效,约有70%左右是疲劳引起的,而且造成的事故大多数是灾难性的。
因此,通过实验研究金属材料抗疲劳的性能是有实际意义的。
图1-1 疲劳宏观断口
一﹑实验目的
1.了解测定材料疲劳极限的方法。
2.掌握金属材料拉拉疲劳测试的方法。
3.观察疲劳失效现象和断口特征。
4.掌握慢应变速率拉伸试验的方法。
二、实验设备
1.PLD-50KN-250NM 拉扭疲劳试验机。
2.游标卡尺。
3.试验材料S135钻杆钢。
4.PLT-10慢应变速率拉伸试验。
三﹑实验原理及方法
在交变应力的应力循环中,最小应力和最大应力的比值为应力比:
max
min σσ=
r (1-1) 称为循环特征或应力比。
在既定的r 下,若试样的最大应力为max 1σ,经历N 1次循环后,发生疲劳失效,
则N 1称为最大应力r 为时的max 1σ疲劳寿命(简称寿命)。
实验表明,在同一循环特征下,最大应力越大,则寿命越短;随着最大应力的降低,寿命迅速增加。
表示最大应力max σ与寿命N 的关系曲线称为应力-寿命曲线或S-N 曲线。
碳钢的S-N 曲线如图1-2所示。
由图可见,当应力降到某一极限值r σ时,S-N 曲线趋
近于水平线。
即应力不超过r σ时,寿命N 可无限增大。
称为疲劳极限或持久极限。
下标r 表示循环特征。
实验表明,黑色金属试样如经历107次循环仍未失效,则再增加循环次数一般也不会失效。
故可把107
次循环下仍未失效的最大应力作为持久极限r σ。
而把N 0=107称为循环基数。
有色金属的S-N 曲线在N>5×108时往往仍未趋于水平,通常规定一个循环基数N 0,例如取N 0=108,把它对应的最大应力作为“条件”持久极限。
图1-2 疲劳试验S-N 曲线
工程问题中,有时根据零件寿命的要求,在规定的某一循环次数下,测出max σ,并称之为疲劳强度。
它有别于上面定义的疲劳极限。
疲劳试验常采用循环加载,其加载波形如图1-3所示。
图1-3 疲劳应力循环
扭转疲劳试验在PLD-100KN 型拉-拉电液伺服疲劳试验机上进行,扭转疲劳试验时,采用应力控制,加载频率为5Hz ,加载波形为三角波,试验环境为实验室大气。
慢应变速率法是基于在一定的应变速率ε
下,发生应力腐蚀开裂的倾向最大的现象提出来的。
该方法是将试样(一般是光滑试样,但也可用缺口试样或预制裂纹的试样)浸入介质中,以恒定的速率(ε
在410−~810− /s 范围内)将试样拉断,测量断口的断面收缩率。
定义介质影响系数β:
K
S
K
ϕψψβ−= (1-2) 作为断口脆化程度来预测金属的应力腐蚀开裂倾向。
式(1-2)中K ψ和S ψ分别为试样在空气和介质中的断面收缩率。
所以确定β或断口脆化程度都要参照在空气中金属的试验结果。
四﹑实验方法
1.试验标准
本实验参照GB/T 12443-2007《金属材料扭应力疲劳试验方法》和GB 3075-80《金属轴向疲劳试验方法》进行试验。
2.试样
疲劳试样的主要有圆柱形、漏斗形、板状,如图1-4所示。
(a )圆柱形试样 (b )漏斗形试样
(c )板状试样 图1-4 试样形状
3.试验参数的确定 轴向应力由下式求得:
2
r
F πσ=
或 ab F =σ (1-3) 式中,F 为轴向应力,r 为试验件的半径。
试验过程中试验机的夹头以一定的位移速度移动,试样即以慢恒速(t L ∆∆/)拉伸。
由于试验机部分的刚度比试样高的多,所以试样伸长L ∆可用卡头的相应位移来代替。
可按照下式计算:
L L
∆=
ε (1-4) t
L L t L L o ∆∆=
∆∆=⋅
011
ε (1-5) 式中:ε-工程应变;0L -试样标矩长度;⋅
ε-应变速率;t L ∆∆/-夹头的位移速度。
当夹头移动速度保持恒定时,可认为试样的应变速率保持不变。
但严格地说,试样的应变速率应该是
t
L
L ∆∆01,L 为瞬时标矩长度。
事实上,在整个试验过程中L 是一个变量,所以试样的应变速率在整个试
验过程中并不是恒定的量,而是变量。
特别是对韧性金属材料拉伸时,一旦出现颈缩,则在颈缩区的实际应变速率可能会增加一个数量级。
这就有可能使试样的应变速率进入或者偏离临界应变速率范围。
预制裂纹试样裂纹尖端塑性区尺寸如果保持相同,则应变速率也保持在一恒定值。
因此,用预制裂纹试样做慢应变速率试验要比采用普通的光滑试样更为合适、方便。
五﹑试样的制备
1.取样及要求
试验取样部位、取向和方法按有关标准和双方协议。
同一批试样所用材料应为同一牌号和同一炉号,并要求质地均匀没有缺陷。
疲劳强度与试样取料部位﹑锻压方向等有关,并受表面加工﹑热处理等工艺条件的影响较大。
2.机加工
所有的机械加工不允许改变试样的冶金组织或力学性能,且引起的试样表面加工硬化应尽可能小。
磨削精加工较硬材料的试样时,应提供足够的冷却液,确保试样表面不过热。
工作部分与过度圆弧的连接应光滑,不应出现机加工痕迹。
3.表面抛光
抛光后,试样工作部分的表面粗糙度a R 的允许最大值为0.32m m 六、试验过程
1.安装试样
将试样紧固于试验机上,使试样与试验机夹头保持良好同轴。
2.试验参数设置
包括轴向应力幅、平均应力、试验频率 3.测定在一定轴向应力下的疲劳性能 七﹑实验结果处理
1.下列情况实验数据无效:载荷过高致试样弯曲变形过大,造成中途停机;断口有明显夹渣致使寿命偏低。
2.将所得实验数据列表。
材 料 应力比r 应力幅a σ 疲劳寿命f N S135
0.1
444.4
169059
3.观察破坏断口的特征。
S135钻杆钢疲劳断口 S135钻杆钢拉伸断口、
4.结合所学知识区分说明下列断口的特征。
八﹑思考题
1.疲劳试样的有效工作部分为什么要磨削加工,不允许有周向加工刀痕?
2.实验过程中若有明显的振动,对寿命会产生怎样的影响?。