混炼胶的生产工艺
混炼胶工艺

混炼胶车间工艺总结混炼胶车间工艺简图:密炼→开炼→虑胶→称量包装一密炼工艺备料→复查→分次投料捏合→高温捏合→抽真空→取样送检→冷却捏合,合格出料①备料按照配方单将生胶,白炭黑挑到平台上,分列在捏合机两侧,标识朝外,准备小料一份。
注:原料标识必须朝外,以便复查时清晰。
②复查将所备的原料根据配方单复查一遍,确保无误。
③分次投料捏合第一次投料将所有生胶和硬母料全部投入捏合机,白炭黑和液体小料分次投入。
打开循环水,启动主机开始捏合,至物料抱团良好以后进行下一次投料。
直至所有白炭黑和小料全部投完,物料抱团良好以后,关循环水开蒸汽升温至120℃。
准备高温捏合。
注:1,投料时要防止将纸屑,灰尘等杂质带入缸内污染胶料。
2,刚投完白炭黑启动主机时转速不宜过大(10-15转),捏合5-10分钟以后再将转速调制40转左右。
3,捏合过程中,顶放空阀要打开,循环水阀门打开,蒸汽阀门关闭,真空阀门关闭。
整个吃料过程要保持低温过程。
4,当电动机声音变大,电流表波动较大,温度开始上升时,则物料开始抱团或抱团良好。
即可准备下一次投料。
④高温捏合所有白太黑和小料投完,物料抱团良好以后。
关闭循环水阀,打开放空阀和蒸汽阀门对物料进行升温直至120℃。
保持蒸汽打开,开始高温捏合。
注:1,开蒸汽时,打开放空阀排水,然后关小到看到有蒸汽冒出即可。
升温过程中要保持缸体压力。
⑤抽真空高温捏合结束,物料温度达到150℃左右,放净真空缓冲罐里的积水,开始抽真空。
注:1,抽真空时,关顶放空阀,关蒸汽,开真空阀,开真空泵循环水阀,启动真空泵,开始抽真空。
2,先开真空阀和真空泵循环水阀,再关顶放空阀,最后启动真空泵。
3,调节侧放空阀使真空度达到工艺要求。
4,抽真空过程中每15分钟巡检一次,做好记录。
⑥取样送检抽完真空后,停主机,关放空阀,停真空泵;开顶放空阀直至压力到0;打开缸盖,开机捏合3-5分钟;从3个不同的方向取样约150克送检。
注:1,先停主机,再关放空阀,最后停真空泵,防止缓冲罐内的积水和低分子重新进入缸体,污染胶料。
混炼胶生产工艺

混炼胶生产工艺混炼胶是将天然橡胶或合成橡胶与添加剂等原料混合,经过炼胶机的拉、剪、折等作用,使其成为固态胶料的工艺过程。
混炼胶主要分为两种类型:开炼和封闭式混炼。
开炼是将胶料与添加剂放入开炼机中,通过辊子的旋转和挤压,使胶料与添加剂彻底混合。
开炼机分为两辊机和三辊机,其中三辊机是最常用的。
开炼机中的三个辊子分别是主辊、副辊和辅助辊,通过调整辊子的转速和间距,可以控制胶料的温度、时间和剪切力。
开炼的优点是可以灵活调整添加剂的比例和炼胶温度,适用于生产各种不同性能的橡胶制品。
封闭式混炼是将胶料和添加剂放入封闭式混炼机中,通过高速旋转的螺杆将胶料和添加剂挤压、剪切和折叠,使其混合均匀。
封闭式混炼机具有密闭性好、能耗低、工艺简单等优点,适用于大批量生产相同性能的胶料。
混炼胶的生产工艺主要包括以下几个步骤:1. 胶料准备:将天然橡胶或合成橡胶切碎,并经过清洗、脱水等工艺处理,除去杂质和水分,使其达到生产要求。
2. 添加剂配方:根据橡胶制品的要求,制定合适的添加剂配方,包括硫化剂、活性剂、助剂等。
3. 混合:将胶料和添加剂按照一定比例放入混炼机中,通过机械作用,使其混合均匀。
4. 调温:根据橡胶和添加剂的特性,控制炼胶机的温度,使其达到最佳炼胶温度。
5. 炼胶:开炼或封闭式混炼机通过旋转、挤压、剪切等作用,将胶料和添加剂进行彻底混合,形成固态的胶料。
6. 切割和离心:经过炼胶机的处理,胶料被切割成块状,并通过离心机的旋转,将胶料中的水分去除。
7. 成型:将炼胶后的胶料放入成型机中,进行定型,形成成品。
混炼胶生产工艺的关键是控制炼胶机的温度、时间和剪切力。
温度过高或时间过长会导致胶料老化,性能下降;剪切力过大会使胶料的结构破坏,影响性能。
因此,在生产中需要严格控制这些参数,以获得符合要求的胶料。
炼胶生产工艺规程.doc.
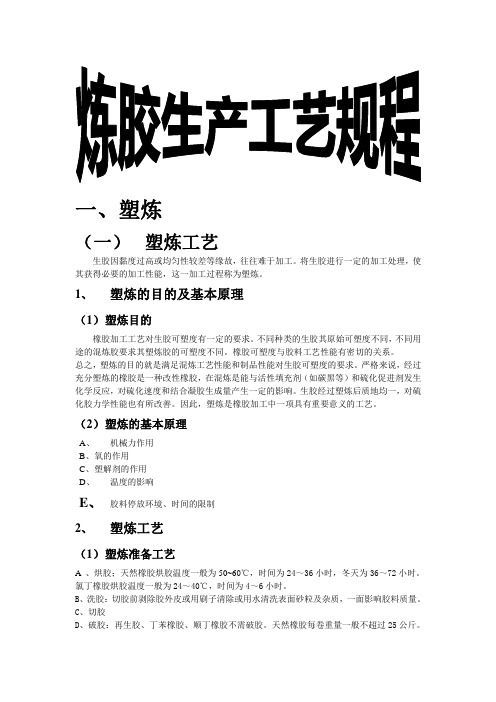
一、塑炼(一)塑炼工艺生胶因黏度过高或均匀性较差等缘故,往往难于加工。
将生胶进行一定的加工处理,使其获得必要的加工性能,这一加工过程称为塑炼。
1、塑炼的目的及基本原理(1)塑炼目的橡胶加工工艺对生胶可塑度有一定的要求。
不同种类的生胶其原始可塑度不同,不同用途的混炼胶要求其塑炼胶的可塑度不同。
橡胶可塑度与胶料工艺性能有密切的关系。
总之,塑炼的目的就是满足混炼工艺性能和制品性能对生胶可塑度的要求。
严格来说,经过充分塑炼的橡胶是一种改性橡胶,在混炼是能与活性填充剂(如碳黑等)和硫化促进剂发生化学反应,对硫化速度和结合凝胶生成量产生一定的影响。
生胶经过塑炼后质地均一,对硫化胶力学性能也有所改善。
因此,塑炼是橡胶加工中一项具有重要意义的工艺。
(2)塑炼的基本原理A、机械力作用B、氧的作用C、塑解剂的作用D、温度的影响E、胶料停放环境、时间的限制2、塑炼工艺(1)塑炼准备工艺A 、烘胶;天然橡胶烘胶温度一般为50~60℃,时间为24~36小时,冬天为36~72小时。
氯丁橡胶烘胶温度一般为24~40℃,时间为4~6小时。
B、洗胶:切胶前剥除胶外皮或用刷子清除或用水清洗表面砂粒及杂质,一面影响胶料质量。
C、切胶D、破胶:再生胶、丁苯橡胶、顺丁橡胶不需破胶。
天然橡胶每卷重量一般不超过25公斤。
胶卷必须注明胶料代号。
(2)开炼机塑炼工艺①开炼机塑炼属于低温塑炼,温度一般在55℃以下,开炼机塑炼关键是降低的温度A、薄通塑炼:将辊距调至1毫米以下,开冷却水使辊筒冷却,将生胶靠大牙轮一端投入,使之通过辊筒间隙,让胶片直接落入胶盘,待辊筒上无堆积胶时,将盘内胶片扭转900重新投入辊隙间,反复8~12次以上,然后切割下片。
生胶下片后要及时冷却,以免降低塑炼效果。
冷却可在隔离剂中进行。
薄通塑炼的特点是冷却效果好(不包辊),不用割刀,对天然胶、合成胶均有效果,尤其是普通丁腈橡胶只有采用薄通法才能获得较好的塑炼效果。
B、包辊塑炼C、爬架子塑炼②影响开炼机塑炼的因素1、辊温辊温越低,塑炼效果越好。
第10章 胶料的混炼
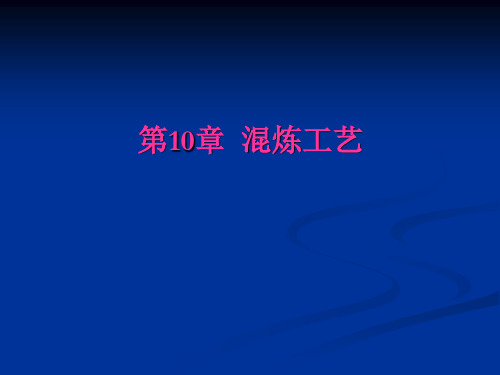
拉伸仪
三.配合剂的分散度检查
目测:借助10倍放大镜或低倍双目显微镜观测胶料表 面,粗略判断胶料的分散程度;
显微镜测定: 定性检验法:只适用于炭黑作填 料的胶料; 定量检验法:利用灯光显微镜、电子显微镜来观察胶 料切片,能真实地反映混炼胶的分散 程度。
四.胶料硫化特性的检查
广泛采用各种类型的 仪器来进行胶料质量的检 验,如硫化仪。能获得有 关混炼胶的相关数据,如 焦烧时间,理论和工艺正 硫化时间等。
炭黑母炼胶中炭黑的最大填充量由炭黑的DBP吸油值决定。 DBP值越高,炭黑的最大填充量越低。
四.称量配合
1、要求称量配合操作做到: 精密、准确、不漏、不错。
2、称量配合的操作方式有两种: (1)手工操作; (2)机械化自动称量配合。
五.常见配合剂的混炼特性
1.硫黄:熔点低,应在混炼的最后阶段在开炼机上 100℃以下加;不能与促进剂一起加。
辊温高有利于吃粉,但分散困难,容易脱辊和焦烧。 前后辊温要有5~10℃的温差: NR:T前>T后;合成胶:T前<T后。 混炼时间:混炼时间过长容易产生过炼和焦烧现象。 辊速和速比:辊速控制在16~18r/min;
速比一般为1:1.1~1:1.2。
二.密炼机混炼工艺
优点: 容量大,时间短,效率高;投料、捏炼、加压和排料操 作易于机械化、自动化,劳动强度低,操作安全性大, 配合剂损失、粉尘飞扬状况得到改善,胶料质量和环境 卫生条件好。 缺点: 混炼时温度较高,对温度敏感的胶料易发生焦烧,需要 对排胶进行补充加工。
§3 混炼胶的质量检查
一.胶料的快检 二.物理机械性能测定 三.配合剂的分散度检查 四.胶料硫化特性的检查
一.胶料的快检
可塑度测定: 威廉氏法、华莱氏法、德弗法, 门尼粘度法。
混炼工艺
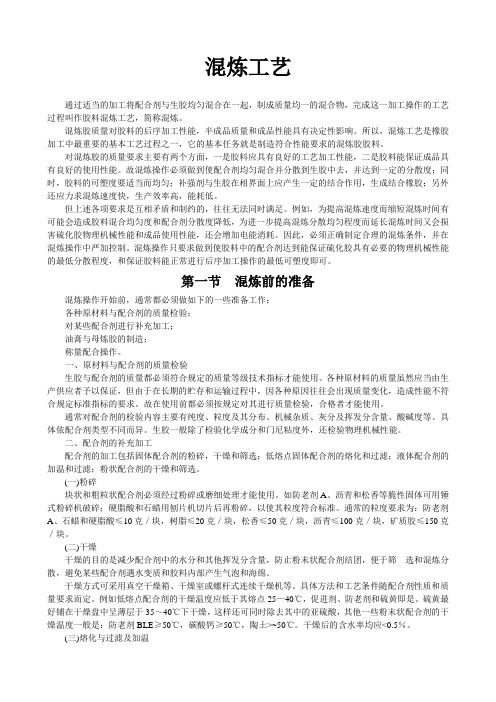
混炼工艺通过适当的加工将配合剂与生胶均匀混合在一起,制成质量均一的混合物,完成这一加工操作的工艺过程叫作胶料混炼工艺,简称混炼。
混炼胶质量对胶料的后序加工性能,半成品质量和成品性能具有决定性影响。
所以,混炼工艺是橡胶加工中最重要的基本工艺过程之一,它的基本任务就是制造符合性能要求的混炼胶胶料。
对混炼胶的质量要求主要有两个方面,一是胶料应具有良好的工艺加工性能,二是胶料能保证成品具有良好的使用性能。
故混炼操作必须做到使配合剂均匀混合并分散到生胶中去,并达到一定的分散度;同时,胶料的可塑度要适当而均匀;补强剂与生胶在相界面上应产生一定的结合作用,生成结合橡胶;另外还应力求混炼速度快,生产效率高,能耗低。
但上述各项要求是互相矛盾和制约的,往往无法同时满足。
例如,为提高混炼速度而缩短混炼时间有可能会造成胶料混合均匀度和配合剂分散度降低,为进一步提高混炼分散均匀程度而延长混炼时间又会损害硫化胶物理机械性能和成品使用性能,还会增加电能消耗。
因此,必须正确制定合理的混炼条件,并在混炼操作中严加控制。
混炼操作只要求做到使胶料中的配合剂达到能保证硫化胶具有必要的物理机械性能的最低分散程度,和保证胶料能正常进行后序加工操作的最低可塑度即可。
第一节混炼前的准备混炼操作开始前,通常都必须做如下的一些准备工作:各种原材料与配合剂的质量检验;对某些配合剂进行补充加工;油膏与母炼胶的制造;称量配合操作。
一、原材料与配合剂的质量检验生胶与配合剂的质量都必须符合规定的质量等级技术指标才能使用。
各种原材料的质量虽然应当由生产供应者予以保证,但由于在长期的贮存和运输过程中,因各种原因往往会出现质量变化,造成性能不符合规定标准指标的要求。
故在使用前都必须按规定对其进行质量检验,合格者才能使用。
通常对配合剂的检验内容主要有纯度、粒度及其分布、机械杂质、灰分及挥发分含量、酸碱度等。
具体依配合剂类型不同而异。
生胶一般除了检验化学成分和门尼粘度外,还检验物理机械性能。
混炼胶混炼工艺最终版本

DF混炼胶生产工艺发布日期:2012年3月12日实施日期:批准人:批准日期:实施日期:文件编号:发放编号:控制状态:持有人:大连巅峰集团2012年3月12日综述混炼胶概念及质量要求通过适当的加工将配合剂与生胶均匀的混合在一起制成质量均一的混合物,完成这一加工操作的工艺过程叫做混炼,混出的胶料叫混炼胶。
对混炼胶质量有两方面要求:一、是胶料应具有良好的物理机械性能。
二、是胶料本身具有良好的工艺加工性能。
为保证混炼胶质量、结合本公司的实际情况特此制订炼胶工艺规程。
炼胶工艺规程包括以下方面:①、生产工艺流程图②、原材料加工工艺③、配料工艺④、切胶工艺⑤、塑胶工艺⑥、混炼工艺⑦、一段,二段混炼胶在每一种胶料中应用⑧、返炼操作方法及要求⑨、不合格胶处理1、生产工艺流程图天然胶合成胶配合剂干燥扒皮加工切胶切胶塑炼检验(可塑度)配合制混炼胶取片检验制片沾浆冷却挂牌存放2、原材料加工工艺2.1 粉碎:固体的石蜡每块不大于50g.石油树脂、古马龙每块不大于50g, 松香每块不大于50g,所用设备为人工锤或万能粉碎机。
2.2筛选:硫磺供应厂家要用自制滚动筛选机筛选标准为100目全过。
2.3 加热过滤:机油加热120℃、时间24H,要求供应厂家要过滤120目×2。
2.4加热:松焦油10月1日到次年5月1次加热100℃以上,时间:24H 2.5干燥:烘干室温度: 50~~60℃。
烘干时间:24H~72H烘干范围: 天然胶 (5月1日-10月1日不烘胶).2.5.1技术要求:(1) 天然胶送加温室前必须将表面泥砂、木屑等杂质清理干净,发霉、发臭、腐烂变质的胶块不得送入车间。
(2) 被加温的生胶不得直接接触暖气片等加热热源,防止局部过热流淌。
(3) 生胶等级不得混杂,胶块不落地。
(4)加温后的生胶按先后顺序使用.2.5.2质量标准:(1) 烘完的生胶应保证内外温度均匀一致, 中心温度不低于25℃(2) 烘完的生胶表面无发霉变臭、无杂物和水迹。
橡胶混炼胶的加工工艺流程
橡胶混炼胶的加工工艺流程1.基本工艺流程伴随现代工业尤其是化学工业的迅猛发展,橡胶制品种类繁多,但其生产工艺过程,却基本相同。
以一般固体橡胶(生胶)为原料的制品,它的生产工艺过程主要包括:原材料准备塑炼混炼成型硫化休整检验2.原材料准备橡胶制品的主要材料有生胶、配合剂、纤维材料和金属材料。
其中生胶为基本材料;配合剂是为了改善橡胶制品的某些性能而加入的辅助材料;纤维材料(棉、麻、毛及各种人造纤维、合成纤维)和金属材料(钢丝、铜丝)是作为橡胶制品的骨架材料,以增强机械强度、限制制品变型。
在原材料准备过程中,配料必须按照配方称量准确。
为了使生胶和配合剂能相互均匀混合,需要对某些材料进行加工:生胶要在60--70℃烘房内烘软后,再切胶、破胶成小块;块状配合剂如石蜡、硬脂酸、松香等要粉碎;粉状配合剂若含有机械杂质或粗粒时需要筛选除去;液态配合剂(松焦油、古马隆)需要加热、熔化、蒸发水分、过滤杂质;配合剂要进行干燥,不然容易结块、混炼时旧不能分散均匀,硫化时产生气泡,从而影响产品质量;3.塑炼生胶富有弹性,缺乏加工时的必需性能(可塑性),因此不便于加工。
为了提高其可塑性,所以要对生胶进行塑炼;这样,在混炼时配合剂就容易均匀分散在生胶中;同时,在压延、成型过程中也有助于提高胶料的渗透性(渗入纤维织品内)和成型流动性。
将生胶的长链分子降解,形成可塑性的过程叫做塑炼。
生胶塑炼的方法有机械塑炼和热塑炼两种。
机械塑炼是在不太高的温度下,通过塑炼机的机械挤压和摩擦力的作用,使长链橡胶分子降解变短,由高弹性状态转变为可塑状态。
热塑炼是向生胶中通入灼热的压缩空气,在热和氧的作用下,使长链分子降解变短,从而获得可塑性。
4.混炼为了适应各种不同的使用条件、获得各种不同的性能,也为了提高橡胶制品的性能和降低成本,必须在生胶中加入不同的配合剂。
混炼就是将塑炼后的生胶与配合剂混合、放在炼胶机中,通过机械拌合作用,使配合剂完全、均匀地分散在生胶中的一种过程。
橡胶混炼工艺
橡胶混炼工艺由于炭黑对硫化速度的影响,硫化胶不同相中交联网构密度必然也不相同,因而形成微观多相交联结构,从而改善硫化胶性能,特别是动态性能。
工艺要点:①混炼的关键是炭黑在胶料中的分散。
为此,先加入炭黑可提高胶料剪切应力,以利于分散;而软化剂必须在炭黑基本分散后加入,以免降低胶料黏度和剪切应力。
②在第一段混炼制备母炼胶时,在部分橡胶中加入全部炭秒度3黑能获得相对高炭黑浓度,提高胶料黏度,增大剪切应力,而有利于配合剂的混入和分散。
例如,在天然橡胶中,炭黑用量从20份增加到50份,剪切应力将提高50%~60%;在丁腈橡胶中,炭黑用量从40份增加到50份,混入时间从18min可降到13min左右。
用此法制备母炼胶,可提高橡胶一炭黑凝胶含量,即使是三元乙丙橡胶也可达40%~50%。
③分段混炼可以使胶料降温,也有利于分散与安全。
④第二段混炼时间不宜过长,否则会破坏胶料中的微观多相结构,对硫化胶性能产生不良影响。
二段混炼的具体操作方法有三种。
其一是合并二段混炼法。
这种方法在合成橡胶或与天然橡胶并用的胶料中应用最普遍。
该操作方法是先用密炼机将天然橡胶与合成橡胶压合成均一的整体,然后按一定加料顺序使配合剂分散均匀,最后排到压片机上进行薄通或翻炼(不加硫黄和超速促进剂),下片后冷却停放。
第二段是把停放冷透的胶料重新在密炼机中进行补充加工,排料至压片机上适当降温后加硫黄及超速促进剂。
若胶炭黑多时,在密炼机中进行二段冷加工时设备负荷太大,很不安全。
这类胶料可在开炼机上进行第二段混炼。
其二是混炼胶并用二段}昆合法。
这种方法是将天然橡胶及合成橡胶先单独制备成母炼胶,然后按配方中天然橡胶与合成橡胶比例在密炼机中充分混合,最后加入硫黄和超速促进剂等。
其三是炭黑母炼胶一段混炼法。
这种方法是将用量大、难混的炭黑先在密炼机中制成母炼胶,经冷却停放(停放时间一般为4~8h),再于密炼机中和其他配合剂一起进行第二段混炼。
这种方法特别适用于快速密炼机混炼,因为快速密炼机对炭黑分散有良好效果,但由于温度高,需配用慢速密炼机进行第二段混炼,以便在低的温度下加入硫化剂。
常用典型橡胶的混炼工艺特点
常用典型橡胶的混炼工艺特点橡胶的混炼就是将各种配合剂借助炼胶机机械力的作用,将各种配合剂均匀地分散在橡胶中,以形成一个以橡胶为介质或者以橡胶与某些能和它相容的配合组分(配合剂、其它聚合物)的混合物为介质,以与橡胶不相容的配合剂(如粉体填料、氧化锌、颜料等)为分散相的多相胶体分散体系的过程。
对混炼工艺的具体技术要求是:配合剂分散均匀,使配合剂特别是炭黑等补强性配合剂达到最好的分散度,以保证胶料性能一致。
混炼后得到的胶料称为“混炼胶”,其质量对进一步加工和制品质量有重要影响。
1·天然橡胶的混炼天然橡胶是生胶塑炼的主要胶种,用开炼机和密炼机进行塑炼均能获得良好效果。
用开炼机塑炼时,通常采用低温(40~50℃)薄通(辊距0.5~1mm)塑炼法和分段塑炼法效果最好。
用密炼机塑炼时,温度宜在155℃以下,时间约在13min 左右。
塑炼时间增加,塑炼胶的可塑性随之增大。
但不要过炼,否则可塑性变得过高而使物理机械性能下降。
天然橡胶塑炼时常加入促进剂M作塑解剂,来提高塑炼效果。
促进剂M对开炼机塑炼和密炼机塑炼都适用。
天然橡胶塑炼后,为使橡胶分子链得到松弛(俗称恢复疲劳)和可塑性均匀,需停放一定时间(4~8h),才能供下道工序使用。
目前国内使用的天然橡胶主要品种有:国产烟片胶和标准胶,进口烟片胶和马来西亚标准胶等。
由于上述胶种的初始门尼粘度不同,欲获得相同的可塑性,所需的塑炼时间当然不同。
其塑炼时间按长短排列的顺序为:进口烟片胶>国产烟片胶>国产标准胶>马来西亚标准胶。
恒粘和低粘标准马来西亚橡胶、充油天然橡胶、轮胎橡胶、易操作橡胶的初始门尼粘度较低(一般小于65),可不经塑炼直接混炼。
天然混炼胶(NR)具有综合性好的物理机械性能,在常温下具有很高的弹性,弹回率可达50%~85%以上。
天然胶还具有较高的机械强度,很好的耐屈挠疲劳性能,滞后损失小,多次变形下生热量低,撕裂强度高,耐磨性和耐寒性良好,以及良好的气密性、防水性、电绝缘性和绝热性。
开炼机混炼工艺和密炼机混炼工艺
开炼机混炼工艺和密炼机混炼工艺
开炼机混炼工艺和密炼机混炼工艺中的混炼的定义:将各类共同剂加入到橡胶中去制成混淆胶。
1. 开炼机混炼工艺
1) 包辊:将生橡胶包于前辊,用3-5分钟有个瞬息的预热过程
2) 吃粉过程:把需要加入的助剂按照一定的顺序加入,加时髦要注意集中胶的体积,少了难于混淆,多了会打滚不容易混炼。
加料顺序:生橡胶→活性剂、加工助剂→硫磺→填充、软化剂、分粉剂→加工助剂→促进剂
3) 翻炼过程:能更好、更快、更匀称的混炼。
刀法:a、斜刀法(八把刀法) b、三角包法 c、打扭操作法 d、捣胶法(走刀法)
4) 开炼机的装胶容量计较公式:V=0.0065*D*L 其中V-体积 D是辊筒的直径(cm) L是辊筒的长度(cm)
5) 辊筒的温度:50-60度
6) 混炼时间:没有具体的规定,看操作员的谙练水平。
2. 密炼机混炼工艺:
1) 一段混炼:一次混炼好,混炼的程序:生橡胶→小料→补强剂→软化剂→排胶→压片机加硫磺、促进剂→下片→冷却停放。
2) 二段混炼:分两段混炼第橡胶生产工艺一段:生橡胶→小料→补强剂→软化剂→排胶→压片→冷却第二段:母胶→硫磺、促进剂→压片→冷却。
- 1、下载文档前请自行甄别文档内容的完整性,平台不提供额外的编辑、内容补充、找答案等附加服务。
- 2、"仅部分预览"的文档,不可在线预览部分如存在完整性等问题,可反馈申请退款(可完整预览的文档不适用该条件!)。
- 3、如文档侵犯您的权益,请联系客服反馈,我们会尽快为您处理(人工客服工作时间:9:00-18:30)。
十四.胶料的混炼
四楼
配料
炭黑斗
二楼
三楼
微机室
胶料秤
一楼
双管气体输送
密炼机
流片机 油管路
炭黑秤
油秤
冷却
十五.胶料的质量保证
• 终炼胶门尼粘度、 焦烧时间检验
十五.胶料的质量保证
• 终炼胶硬度检 验检验
十五.胶料的质量保证
• 终炼胶比 重检验
十五.胶料的质量保证
• 无转子流变仪 检验终炼胶流 变性能
胶料检验、待用
十.炭黑的输送称量系统
• 炭黑气体输送系统 • 炭黑自动称量系统
日 储 斗
十一.油料的输送称量系统
• 油料的输送储存系统
十一.油料的输送称量系统
• 油料的称量系统 • 油料称示意图
十二.细料的称量系统
• 传统的细料联动称量 • 先进的细料自动称量
• 精细的终炼药手动称量
十三.生胶的烘热
• 温度稳定、容量固定的生胶烘胶房
• 温度自控
十四.胶料的混炼
十四.胶料的混炼
• 生胶、药料的称量及加入
十四.胶料的混炼
• 炭黑、油料的自动称量及加入 • 混炼温度的自动控制及排胶
十四.胶料的混炼
• 胶料在压片机通过、 捣合及流片
十四.胶料的混炼
• 胶片的冷却
十四.胶料的混炼
• 胶片的落片
生 胶:用来生产混炼胶的天然胶或合 成胶,也常称为胶料。
硫化胶:生产橡胶成品使,经过硫化后 混炼胶,也作胶料称呼。
四.胶料的组成
五.胶料在轮胎中使用
六.混炼的概念
混炼:将各种配合剂和橡胶,通过炼胶 机制成胶料的工艺过程叫做混炼,俗称 炼胶或打胶。
开放式炼胶机
密闭式炼胶机
七.混炼胶的分类
分类:母炼胶、终炼胶
母炼胶:通常指不加硫磺和促进剂的混 炼胶。根据工艺要求,可分一 段、二段、……多段。
终炼胶:通常指母炼胶加硫磺和促进剂 的混炼胶。
八.胶料混炼设备简介
• 密炼机外观图
• 密炼机结构图
八.胶料混炼设备简介
• 密炼机转子 • 密炼机侧视图
• 密炼机传动系统
八.胶料混炼设备简介
• 密炼机联动系统
九.胶料混炼工序
混炼胶的生产工艺
一.轮胎的概念
轮胎:在各种车辆 或机械上装配的接 地滚动的圆环形弹 性橡胶制品。
二.轮胎的组成
轮
胶料
胎
组
成 骨架材料
纤维 OR 钢丝
三.胶料是俗称
混炼胶:为了提高橡胶制品的使用性能、 改进工艺性能、降低产品性能,必须在 生胶中加入各种配合剂。然后在炼胶机 上将各种配合剂加到橡胶中制成混合胶, 即为混炼胶,俗称胶料。
十五.胶料的质量保证
• 终炼胶物理性能检验
完毕谢谢
原材料
1.1
入库检验
混炼
贮存
1.2
发放运输
炭黑油料
生胶
输送
2.3
烘胶
2.2
图例说明:
主工序 半成品材料
2.4
密炼称量
2.5
混炼与排胶
2.6
出片至收胶
过程 检测点
废品 运输
终炼胶
2.8
胶料快检
YES 停放运输
配合剂 配料
2.1
隔离剂
2.7
配制
NO YES
掺用
技术处理 NO 废品
炼胶前的准备 胶料的混炼