炼胶工艺规程
炼胶生产工艺规程.doc.
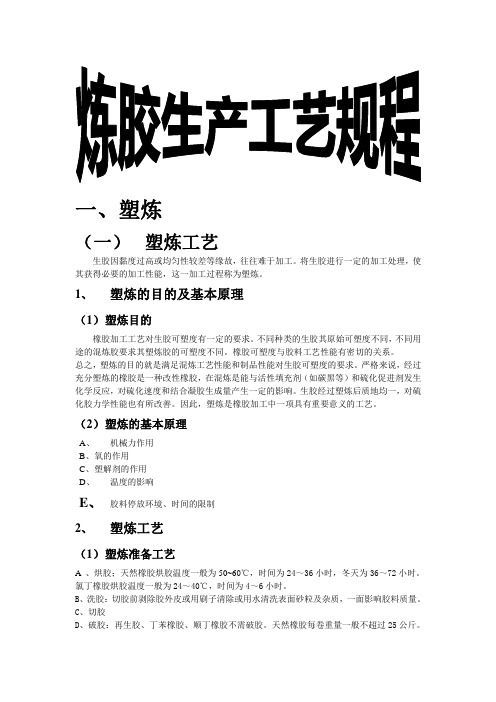
一、塑炼(一)塑炼工艺生胶因黏度过高或均匀性较差等缘故,往往难于加工。
将生胶进行一定的加工处理,使其获得必要的加工性能,这一加工过程称为塑炼。
1、塑炼的目的及基本原理(1)塑炼目的橡胶加工工艺对生胶可塑度有一定的要求。
不同种类的生胶其原始可塑度不同,不同用途的混炼胶要求其塑炼胶的可塑度不同。
橡胶可塑度与胶料工艺性能有密切的关系。
总之,塑炼的目的就是满足混炼工艺性能和制品性能对生胶可塑度的要求。
严格来说,经过充分塑炼的橡胶是一种改性橡胶,在混炼是能与活性填充剂(如碳黑等)和硫化促进剂发生化学反应,对硫化速度和结合凝胶生成量产生一定的影响。
生胶经过塑炼后质地均一,对硫化胶力学性能也有所改善。
因此,塑炼是橡胶加工中一项具有重要意义的工艺。
(2)塑炼的基本原理A、机械力作用B、氧的作用C、塑解剂的作用D、温度的影响E、胶料停放环境、时间的限制2、塑炼工艺(1)塑炼准备工艺A 、烘胶;天然橡胶烘胶温度一般为50~60℃,时间为24~36小时,冬天为36~72小时。
氯丁橡胶烘胶温度一般为24~40℃,时间为4~6小时。
B、洗胶:切胶前剥除胶外皮或用刷子清除或用水清洗表面砂粒及杂质,一面影响胶料质量。
C、切胶D、破胶:再生胶、丁苯橡胶、顺丁橡胶不需破胶。
天然橡胶每卷重量一般不超过25公斤。
胶卷必须注明胶料代号。
(2)开炼机塑炼工艺①开炼机塑炼属于低温塑炼,温度一般在55℃以下,开炼机塑炼关键是降低的温度A、薄通塑炼:将辊距调至1毫米以下,开冷却水使辊筒冷却,将生胶靠大牙轮一端投入,使之通过辊筒间隙,让胶片直接落入胶盘,待辊筒上无堆积胶时,将盘内胶片扭转900重新投入辊隙间,反复8~12次以上,然后切割下片。
生胶下片后要及时冷却,以免降低塑炼效果。
冷却可在隔离剂中进行。
薄通塑炼的特点是冷却效果好(不包辊),不用割刀,对天然胶、合成胶均有效果,尤其是普通丁腈橡胶只有采用薄通法才能获得较好的塑炼效果。
B、包辊塑炼C、爬架子塑炼②影响开炼机塑炼的因素1、辊温辊温越低,塑炼效果越好。
橡胶炼胶工安全操作规程

仅供参考[整理] 安全管理文书
橡胶炼胶工安全操作规程
日期:__________________
单位:__________________
第1 页共3 页
仅供参考[整理]
橡胶炼胶工安全操作规程
1、开车前检查是否有人依靠在机台或运转部位,无人时方可开车。
2、试滚筒温度时手向下与滚筒运转反方向,不准顺滚筒或超过安全线试温。
3、操作人员离开机台时,须将刀子放入鞘内,操作时注意周围人员,防止碰伤。
4、手套严禁扎在手腕部。
5、机器在运转时,不准到机台底下和运转部位附近捡胶片。
6、续胶时,一定将大皮子割成小片,用手拉皮子时,不许超过安全线。
7、推胶时必须将手握成拳形进行,不准超过安全线。
8、楼上发出排胶信号时,楼下操作人员须将滚筒上的存胶全部割下才能回铃,以免发生事故。
9、胶在漏斗堵住时,一定由二楼向下推,不得在楼下伸头往上看或用钩子勾。
10、裁胶时,胶片长度不得超过1.5米。
11、机器在运转过程中,发现胶内有杂质、杂物时,必须停车取出。
12、生产中,不准在运转中坐在药盘上。
停车后不准在滚筒上站立。
13、压塑炼胶时,操作人员应站在侧面,等包辊后才可以割胶,胶头要接上,以免胶皮打伤人。
14保持机床和工作场地的清洁整齐,做好交接班记录。
第 2 页共 3 页
仅供参考[整理] 安全管理文书
整理范文,仅供参考!
日期:__________________
单位:__________________
第3 页共3 页。
炼胶工艺流程
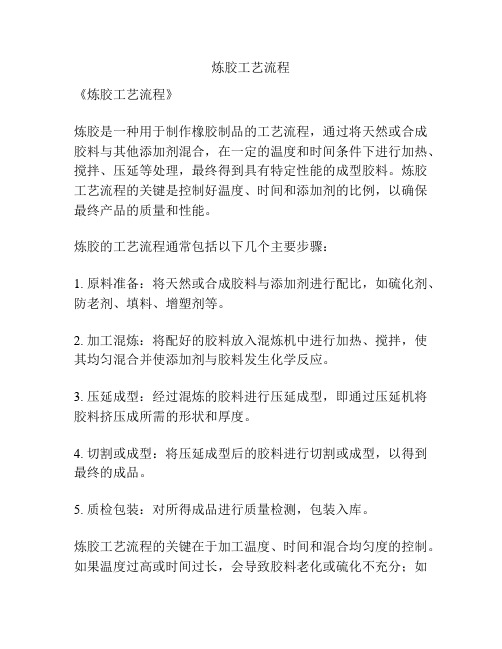
炼胶工艺流程
《炼胶工艺流程》
炼胶是一种用于制作橡胶制品的工艺流程,通过将天然或合成胶料与其他添加剂混合,在一定的温度和时间条件下进行加热、搅拌、压延等处理,最终得到具有特定性能的成型胶料。
炼胶工艺流程的关键是控制好温度、时间和添加剂的比例,以确保最终产品的质量和性能。
炼胶的工艺流程通常包括以下几个主要步骤:
1. 原料准备:将天然或合成胶料与添加剂进行配比,如硫化剂、防老剂、填料、增塑剂等。
2. 加工混炼:将配好的胶料放入混炼机中进行加热、搅拌,使其均匀混合并使添加剂与胶料发生化学反应。
3. 压延成型:经过混炼的胶料进行压延成型,即通过压延机将胶料挤压成所需的形状和厚度。
4. 切割或成型:将压延成型后的胶料进行切割或成型,以得到最终的成品。
5. 质检包装:对所得成品进行质量检测,包装入库。
炼胶工艺流程的关键在于加工温度、时间和混合均匀度的控制。
如果温度过高或时间过长,会导致胶料老化或硫化不充分;如
果混合均匀度不好,会影响到最终产品的性能。
炼胶工艺流程在橡胶制品生产中扮演着重要的角色,通过科学的工艺流程,可以得到质量稳定的橡胶制品。
同时,也需要不断进行工艺改进和技术创新,以适应不同类型和要求的橡胶制品生产。
炼胶工艺规范管理
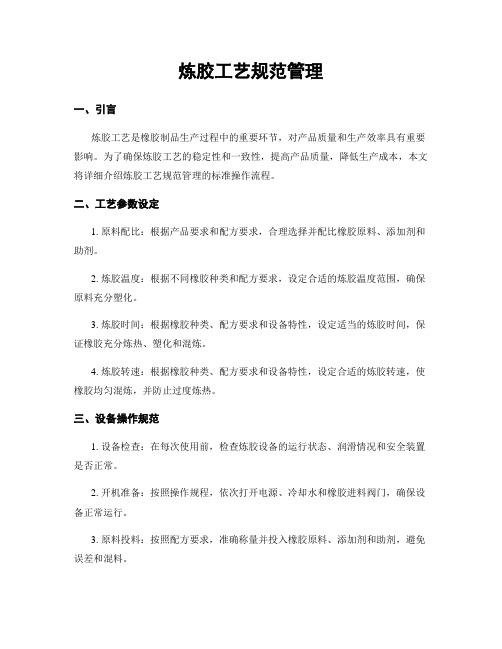
炼胶工艺规范管理一、引言炼胶工艺是橡胶制品生产过程中的重要环节,对产品质量和生产效率具有重要影响。
为了确保炼胶工艺的稳定性和一致性,提高产品质量,降低生产成本,本文将详细介绍炼胶工艺规范管理的标准操作流程。
二、工艺参数设定1. 原料配比:根据产品要求和配方要求,合理选择并配比橡胶原料、添加剂和助剂。
2. 炼胶温度:根据不同橡胶种类和配方要求,设定合适的炼胶温度范围,确保原料充分塑化。
3. 炼胶时间:根据橡胶种类、配方要求和设备特性,设定适当的炼胶时间,保证橡胶充分炼热、塑化和混炼。
4. 炼胶转速:根据橡胶种类、配方要求和设备特性,设定合适的炼胶转速,使橡胶均匀混炼,并防止过度炼热。
三、设备操作规范1. 设备检查:在每次使用前,检查炼胶设备的运行状态、润滑情况和安全装置是否正常。
2. 开机准备:按照操作规程,依次打开电源、冷却水和橡胶进料阀门,确保设备正常运行。
3. 原料投料:按照配方要求,准确称量并投入橡胶原料、添加剂和助剂,避免误差和混料。
4. 温度控制:根据炼胶温度要求,调整加热器的温度设定值,并监控温度变化,及时调整加热功率。
5. 混炼过程:根据炼胶时间和转速要求,启动橡胶混炼机,并根据工艺要求适时调整转速和混炼时间。
6. 检测样品采集:在混炼过程中,定期采集橡胶样品进行质量检测,确保产品符合要求。
7. 停机操作:混炼结束后,先关闭橡胶进料阀门,待橡胶完全排出后再关闭电源和冷却水。
四、质量控制要求1. 原料质量控制:严格按照配方要求选用优质原料,并进行质量检测,确保原料符合要求。
2. 混炼质量控制:通过定期采集样品进行物理性能测试,如硫化速度、硫化度、拉伸强度等,确保混炼质量稳定。
3. 工艺参数记录:每次混炼过程中,记录并保存原料配比、炼胶温度、炼胶时间、炼胶转速等工艺参数,便于追溯和分析。
4. 异常处理:对于混炼过程中出现的异常情况,如温度异常、转速异常等,及时停机并进行排查和处理,确保混炼质量。
炼胶工艺流程
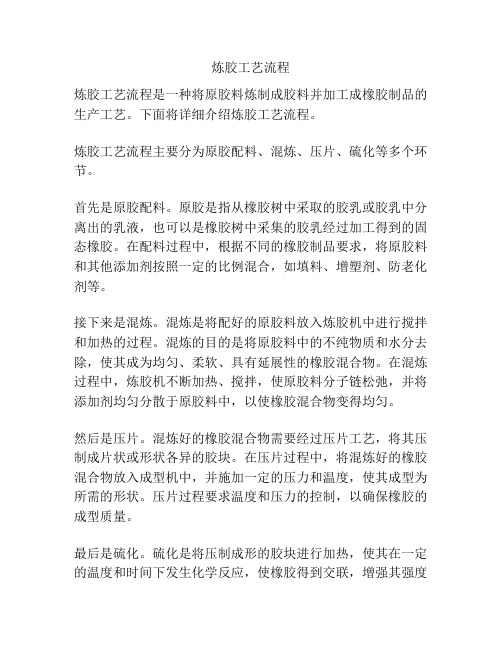
炼胶工艺流程炼胶工艺流程是一种将原胶料炼制成胶料并加工成橡胶制品的生产工艺。
下面将详细介绍炼胶工艺流程。
炼胶工艺流程主要分为原胶配料、混炼、压片、硫化等多个环节。
首先是原胶配料。
原胶是指从橡胶树中采取的胶乳或胶乳中分离出的乳液,也可以是橡胶树中采集的胶乳经过加工得到的固态橡胶。
在配料过程中,根据不同的橡胶制品要求,将原胶料和其他添加剂按照一定的比例混合,如填料、增塑剂、防老化剂等。
接下来是混炼。
混炼是将配好的原胶料放入炼胶机中进行搅拌和加热的过程。
混炼的目的是将原胶料中的不纯物质和水分去除,使其成为均匀、柔软、具有延展性的橡胶混合物。
在混炼过程中,炼胶机不断加热、搅拌,使原胶料分子链松弛,并将添加剂均匀分散于原胶料中,以使橡胶混合物变得均匀。
然后是压片。
混炼好的橡胶混合物需要经过压片工艺,将其压制成片状或形状各异的胶块。
在压片过程中,将混炼好的橡胶混合物放入成型机中,并施加一定的压力和温度,使其成型为所需的形状。
压片过程要求温度和压力的控制,以确保橡胶的成型质量。
最后是硫化。
硫化是将压制成形的胶块进行加热,使其在一定的温度和时间下发生化学反应,使橡胶得到交联,增强其强度和耐磨性。
硫化是一个重要的环节,通过硫化使橡胶制品具备了优良的性能,如耐候性、耐油性、耐磨性等。
以上就是炼胶工艺流程的主要环节。
通过原胶配料、混炼、压片和硫化等过程,将原始的橡胶材料加工成各种形态的橡胶制品。
炼胶工艺流程的每个环节都需要精确的控制温度、压力和时间等参数,以确保橡胶制品的质量和性能。
炼胶工艺的改进和创新对于提高橡胶制品的品质和降低生产成本具有重要意义。
炼胶的流程
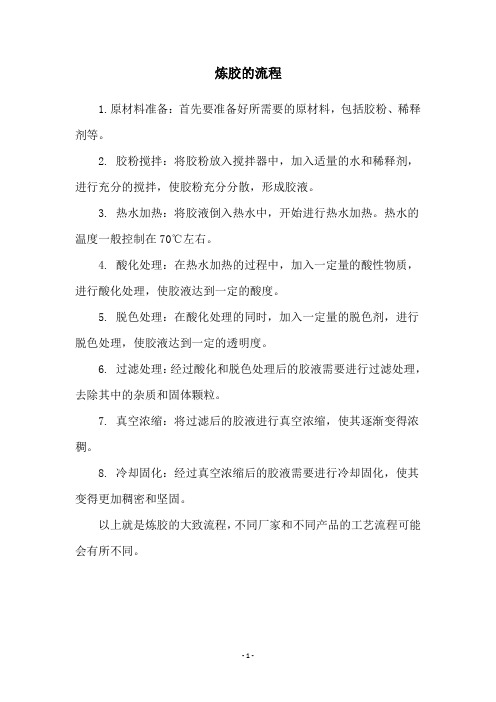
炼胶的流程
1.原材料准备:首先要准备好所需要的原材料,包括胶粉、稀释剂等。
2. 胶粉搅拌:将胶粉放入搅拌器中,加入适量的水和稀释剂,进行充分的搅拌,使胶粉充分分散,形成胶液。
3. 热水加热:将胶液倒入热水中,开始进行热水加热。
热水的温度一般控制在70℃左右。
4. 酸化处理:在热水加热的过程中,加入一定量的酸性物质,进行酸化处理,使胶液达到一定的酸度。
5. 脱色处理:在酸化处理的同时,加入一定量的脱色剂,进行脱色处理,使胶液达到一定的透明度。
6. 过滤处理:经过酸化和脱色处理后的胶液需要进行过滤处理,去除其中的杂质和固体颗粒。
7. 真空浓缩:将过滤后的胶液进行真空浓缩,使其逐渐变得浓稠。
8. 冷却固化:经过真空浓缩后的胶液需要进行冷却固化,使其变得更加稠密和坚固。
以上就是炼胶的大致流程,不同厂家和不同产品的工艺流程可能会有所不同。
- 1 -。
炼胶车间工艺流程图
炼胶车间工艺流程图一、引言炼胶车间是橡胶制品生产过程中的重要环节,其工艺流程图对于保证生产质量、提高生产效率具有重要意义。
本文将详细介绍炼胶车间的工艺流程图,包括原料准备、炼胶操作、成品制备等环节,旨在为炼胶车间的工作人员提供参考。
二、工艺流程图炼胶车间工艺流程图如下所示:1. 原料准备1.1 原料采集:采集橡胶、添加剂、填充剂等原料,并进行质量检验。
1.2 原料称量:按照配方要求,精确称量所需的原料。
1.3 原料混合:将橡胶、添加剂、填充剂等原料放入混合机中,进行均匀混合。
2. 炼胶操作2.1 加热:将混合后的原料放入炼胶机中,加热至一定温度。
2.2 搅拌:通过炼胶机的搅拌装置,使原料充分搅拌,使其达到均匀的胶态。
2.3 加入助剂:根据需要,适量加入硫化剂、促进剂等助剂。
2.4 硫化:将搅拌好的胶料放入硫化机中,进行硫化处理,使其具备弹性和耐磨性。
2.5 冷却:将硫化后的胶料放入冷却机中,降低其温度。
3. 成品制备3.1 制胶:将冷却后的胶料进行切割、压制等工艺,制备成所需的橡胶制品。
3.2 检验:对制备好的橡胶制品进行质量检验,确保其符合标准要求。
3.3 包装:将合格的橡胶制品进行包装,便于储存和运输。
3.4 存储:将包装好的橡胶制品存放在指定的仓库中,确保其质量不受影响。
三、工艺流程图解析1. 原料准备环节:该环节主要包括原料的采集、称量和混合。
通过对原料的质量检验和精确的称量,保证了后续工艺的顺利进行。
2. 炼胶操作环节:该环节是炼胶车间的核心环节,主要包括加热、搅拌、加入助剂、硫化和冷却。
通过加热和搅拌,使原料达到均匀的胶态;加入助剂,提高橡胶制品的性能;硫化处理,使橡胶具备弹性和耐磨性;冷却,降低胶料的温度,为后续制备成品做好准备。
3. 成品制备环节:该环节主要包括制胶、检验、包装和存储。
通过制胶工艺的切割、压制等操作,将炼胶得到的胶料制备成所需的橡胶制品;对制备好的橡胶制品进行质量检验,确保其符合标准要求;将合格的橡胶制品进行包装和存储,确保其质量不受影响。
炼胶生产工艺规程
炼胶生产工艺规程本规程包含工艺流程、主要原材料选择、主要设备选型、加工技术指标和操作要点。
一.工艺流程橡胶软管产品采用天然橡胶和氯丁橡胶经塑炼、混炼、编织(缠绕)硫化成型工艺路线。
具体工序顺序见工艺流程框图。
二.主要原材料选择橡胶软管所用原材料主要有天然橡胶、氯丁胶、钢丝及各种配合剂,其具体质量要求见原材料检验规程。
三.主要设备选型3.1开放式炼胶机型号:XQ 400、XQ 6003.2密炼机四.炼胶加工技术指标和操作要点4.1塑炼4.1.1塑炼前的准备4.1.1.1烘胶切胶:为便于塑炼加工,天然胶和氯丁胶气温较低时在塑炼前需烘胶和切割4.1.1.1.1主要设备半环形烘胶房切胶机磅称4.1.1.1.2技术指标烘、切胶的技术指标见下表操作要点a. 烘胶温度不可过高,以免降低橡胶物理机械性能。
b. 打开生胶包外包装,将胶面杂质清理干净。
c. 开包后的橡胶不可落地或粘染杂质。
d. 胶块切成三角形。
4.1.1.2 破胶用开放式炼胶机破胶,辊距1.5〜2mm应将挡板适当调窄,靠近大牙轮一端加料。
4.1.2塑炼采用的是薄通塑炼方法4.1.2.1主要设备开放式炼胶机4.1.2.1技术指标开炼机塑炼过程技术指标见下表操作要点4.1.2.2.1开炼机塑炼a. 塑炼前需先调整炼胶机前后辊筒温度至规定标准。
b. 调整炼胶机前后辊距0.5〜1mmc. 胶料靠主驱动轮一边连续投入,不得间断,直至投完,直接落盘。
d. 将胶料扭转90°角从新投入,如此连续薄通13〜15次。
d. 打包或打卷,单卷重量不超过10kg.停放不少于8h。
e. 也可切割下片,晾置在专用的栏杆上,待胶温降至常温后,将胶片置于平台上,胶层之间用垫布或钙粉隔离,高度不高于0.5m,停放不少于8h。
f. 放置标签注明品名、塑炼时间及操作人。
4.2混炼4.2.1配料421.1主要设备:网筛、烘箱、容器、磅秤、421.2技术指标配合剂如受潮结块应按下表加工处理原材料称量允许公差如下表操作要点1. 所有材料均应用加盖容器盛装,以防飞撒损失。
第十章 炼胶工艺
2、工艺方法
(1)一段混炼法: 适用:粘度低、填充量少、生热低的胶料,如以NR为主的胶料。 优点:胶料管理方便,节省停放面积。 缺点:可塑度低,不易分散均匀,混炼周期长,易焦烧和过炼。 具体方法: 传统一段混炼法:按顺序加料。采用慢速或变速密炼 分段投胶一段混炼法:分批投加生胶。
因素
(五)塑炼补充工艺
(1)压片或造粒 (2)冷却与干燥 (3)停放 干燥后的胶片按规定堆放质量检验
二、原材料的质量检验
1、生胶的检验 元素组成、杂质含量、门尼黏度、挥发份含量、含水率等。
2、配合剂的检验 固体配合剂的粒度、纯度、酸碱度、吸油值、金属离子含 量、熔点、分解温度、挥发份含量等; 液体配合剂的苯胺点、倾点、闪点、沸点、含水率、挥发份 含量等。
炭黑自动称量与输送系统(示意图)
炭黑自动称量系统
油料自动称量与输送系统 通密炼机
小料自动称量系统(投料口)
小料自动称量系统
胶料称量系统
GK400型密炼机
二棱转子
四棱转子
密炼机控制中心
流片机(开炼机)
胶料输送装置
流片机(辊筒机头螺杆挤出机)
冷却装置
风冷
冷却槽(水冷)
叠放
三、炼胶过程及方法
a-加入配合剂,落下上顶栓; b-上顶栓稳定
c-功率最低值
d-功率二次峰值 e-排料
f—过炼及温度平坦
混炼过程: (1)湿润
混炼时间/min
(2)分散 (3)捏炼
混炼时的容积、功率、温度变化曲线
3、混炼机理
(1)吃粉 开炼机吃粉:返回胶与堆积胶拥挤产生狭缝,配合剂进入 狭缝,被胶料包围。过程慢,时间长。 密炼机吃粉:返回胶与上顶栓的包围。过程快,时间短。 (2)分散 必要条件:①有速比 ②有流道变化 分散过程:胶料和配合剂团块破碎 简单混合 (3)分散均匀 配合剂分散
橡胶炼胶工安全操作规程范本
橡胶炼胶工安全操作规程范本一、前言橡胶炼胶工作是一项重要的化学工艺,工作环境复杂且存在较大的安全风险。
为保障工作人员的人身安全和设备的正常运行,制定本安全操作规程。
本规程适用于橡胶炼胶工作过程中的各项操作,包括原料储存、橡胶炼制、混炼、成型等环节。
二、作业前的准备1. 橡胶炼胶作业必须由熟悉工艺和操作流程的专业人员进行,且需持相关操作证件上岗。
2. 在作业开始前,必须穿戴符合安全标准的防护设备,包括安全帽、防护眼镜、耳塞、耐酸碱手套、防护服等。
3. 检查设备的运行状况和安全装置,并确保其处于正常工作状态。
4. 审阅橡胶炼制工艺流程和物料安全数据表,熟悉各项操作细节和注意事项。
三、操作规范1. 原料储存:(1) 原料应存放在防火、防爆和通风良好的仓库中,禁止将其与可燃物或氧化剂放置在一起。
(2) 储存区域内禁止吸烟、明火和开关电源。
禁止携带火种、易燃物进入储存区域。
(3) 储存的原料必须标明名称、规格、批次和储存日期,及时进行定期检查和清理,确保无漏包、无裂密、无破损。
2. 橡胶炼制:(1) 橡胶炼制作业时,必须按照工艺流程操作,并根据所需的比例和顺序加入原料。
(2) 在投加固体原料时,应小心操作,避免外溢或撒落。
(3) 在液体原料投加时,应使用专用的投料设备或工具,并注意防溅和防止扩散。
(4) 搅拌设备在操作前必须先检查转速、电流等,确保设备正常运行。
(5) 搅拌设备启动后,不得用手插入或取出橡胶或工具,必须采用专用设备。
(6) 禁止向搅拌设备中投放铁器、杂物等可能损坏设备的物品。
3. 混炼:(1) 在混炼过程中,必须戴防护眼镜和防护面罩,避免异物溅入眼睛。
(2) 禁止将混炼橡胶堆积太高,以免发生翻倒事故。
(3) 在混炼过程中,如发现设备异常或异响,应立即停机检查。
(4) 混炼结束后,应关闭设备电源,并进行设备的清洁和维护。
4. 成型:(1) 在成型操作开始前,必须将操作区域清理干净,移除杂物和易燃物。
- 1、下载文档前请自行甄别文档内容的完整性,平台不提供额外的编辑、内容补充、找答案等附加服务。
- 2、"仅部分预览"的文档,不可在线预览部分如存在完整性等问题,可反馈申请退款(可完整预览的文档不适用该条件!)。
- 3、如文档侵犯您的权益,请联系客服反馈,我们会尽快为您处理(人工客服工作时间:9:00-18:30)。
炼胶工艺规程
一、塑炼
1.1用切胶机将天然胶切成3kg左右小块儿,靠驱动齿一侧投入,
不得间断,一次投放容量为10kg ,辊距0.5~1mm辊温45~55℃;
1.2开刀使胶料落盘,这样薄通15~20次;
1.3放厚辊逐片返炼均匀,辊距4-5mm.;
1.4辊温不超过60℃,用手测量,能在辊上放半分钟为宜,总塑炼
时间每辊20~25分钟。
二、轧胶
2.1将塑炼12小时以上的胶上辊回软,辊距4~4.5mm,辊温40~
50℃,时间2~3分钟
2.2加入小料翻炼均匀,时间为4~5分钟,辊温为40~50℃;
2.3加入炭黑的三分之一,待粉料将要吃完时再加入其余碳黑,
辊温50~55℃,时间4-5分钟;
2.4慢慢分次加入软化剂,与落盘碳黑交叉加入。
待料剂将吃完,
两边割刀抽条留少量堆积胶,时间为4-5分钟,辊温为50~
55℃;
2.5加放其余粉剂,待快吃完时加入硫化剂,随即把抽条放入翻
炼均匀。
辊温55~60℃,时间4~5分钟;
2.6放薄辊距打三角包三次,辊温55~60℃,时间6~7分钟;
2.7放厚辊距,取试样检测,然后按规定厚度下片,停放4小时
以上的合格胶片方可进入硫化工序。
2.8无论塑炼、混炼胶料一律不允许落地。