动力电池pack
动力电池PACK生产工艺流程图

动力电池PACK生产工艺流程图
一、背景介绍
电动力电池PACK是用于汽车和其他电动车辆的能源储存单元。
它的
重要性不言而喻,可以说它就像发动机,在电动车辆上担负着转矩输出和
热量回收的重要任务。
经过不断的研发,电池PACK的性能不断提升,具有更高的安全性、
可靠性和能量密度。
有效的管理电池PACK的生产工艺也是提高其品质和
完善它系统的重要环节。
二、电池PACK生产工艺流程
1.材料检验:检查单个电池的规格和质量以及关键零部件的可靠性,
为生产准备好高品质的零部件。
2.电池装配:根据客户的要求以及BOM清单,组装出电池PACK,并
检查电气性能。
3.电池组装:根据客户的要求,组装电池PACK,检查电气连接情况,确保正常密封使用。
4.组装测试:完成电池PACK装配后,将其连接至测试系统,测试各
种功能,如电池容量、充电电流、放电电流等。
5.性能测试:确保电池PACK具有良好的可靠性,测试电池PACK的充
电与放电性能,高温性能,冲击性能,耐久性能等,并记录各项性能数据。
6.包装:将电池PACK进行严格的包装,确保安全运输,有足够的保护。
7.交付:将电池PACK交付给客户,以确保客户收到高性能,高可靠性的电池PACK。
三、优化提升。
动力电池pack生产工艺流程

动力电池pack生产工艺流程动力电池是电动车、混合动力车等新能源汽车的核心部件之一,它以电池单体为基本单元,通过连接、组装、封装等工艺步骤形成能够提供持久动力的电池组。
下面将详细介绍动力电池pack的生产工艺流程。
1.电池单体制备:首先需要准备电池单体。
电池单体制备包含两个主要过程:正负电极材料的制备和电解液的配制。
正负电极材料由锂离子嵌入和脱出能力较好的材料构成,例如三元材料、钴酸锂材料等。
电解液一般由溶剂和锂盐组成。
2.电池单体组装:将制备好的电池单体组装成电池组。
首先将正负电极与一定长度的聚合物隔膜叠放,然后通过热融封或超声波焊接等方式,将电池单体的正负极与隔膜紧密连接起来,形成电池单体组。
3.电池单体测试:对组装好的电池单体进行测试,主要包括容量测试、内阻测试、电压测试等。
如果发现有问题的电池单体,需要进行更换或修复。
4.电池单体匹配:将电池单体按照一定的匹配原则进行分组,确保每个电池组中的电池单体性能相似。
5.电池组设计:在进行电池组设计时需要考虑多方面因素,例如车辆类型、续航里程、功率输出等。
根据设计要求,将匹配好的电池单体进行连接,形成电池组。
6.电池组测试:对组装好的电池组进行全面测试,主要包括能量效率测试、温度特性测试、充放电性能测试等,保证电池组的性能符合设计要求。
7.电池组封装:对测试合格的电池组进行封装。
一般采用金属外壳或塑料外壳进行固化封装,以保护电池组免受外部环境的影响。
8.电池组整合:将封装好的电池组与电池管理系统(BMS)、冷却系统等进行整合,在整车装配阶段完成新能源汽车的生产。
以上就是动力电池pack的生产工艺流程。
在整个生产过程中,需要严格控制每个环节的质量,确保电池组的性能稳定可靠。
此外,还需要对废旧动力电池进行回收处理,实现电池资源的最大化利用和环境友好性。
动力电池是新能源汽车发展的关键,只有不断完善生产工艺,提高电池组的性能和安全性,才能推动新能源汽车行业的健康发展。
动力电池pack工艺
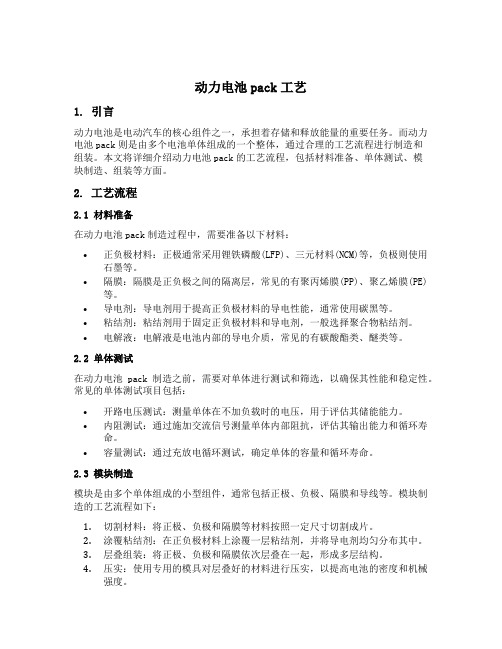
动力电池pack工艺1. 引言动力电池是电动汽车的核心组件之一,承担着存储和释放能量的重要任务。
而动力电池pack则是由多个电池单体组成的一个整体,通过合理的工艺流程进行制造和组装。
本文将详细介绍动力电池pack的工艺流程,包括材料准备、单体测试、模块制造、组装等方面。
2. 工艺流程2.1 材料准备在动力电池pack制造过程中,需要准备以下材料:•正负极材料:正极通常采用锂铁磷酸(LFP)、三元材料(NCM)等,负极则使用石墨等。
•隔膜:隔膜是正负极之间的隔离层,常见的有聚丙烯膜(PP)、聚乙烯膜(PE)等。
•导电剂:导电剂用于提高正负极材料的导电性能,通常使用碳黑等。
•粘结剂:粘结剂用于固定正负极材料和导电剂,一般选择聚合物粘结剂。
•电解液:电解液是电池内部的导电介质,常见的有碳酸酯类、醚类等。
2.2 单体测试在动力电池pack制造之前,需要对单体进行测试和筛选,以确保其性能和稳定性。
常见的单体测试项目包括:•开路电压测试:测量单体在不加负载时的电压,用于评估其储能能力。
•内阻测试:通过施加交流信号测量单体内部阻抗,评估其输出能力和循环寿命。
•容量测试:通过充放电循环测试,确定单体的容量和循环寿命。
2.3 模块制造模块是由多个单体组成的小型组件,通常包括正极、负极、隔膜和导线等。
模块制造的工艺流程如下:1.切割材料:将正极、负极和隔膜等材料按照一定尺寸切割成片。
2.涂覆粘结剂:在正负极材料上涂覆一层粘结剂,并将导电剂均匀分布其中。
3.层叠组装:将正极、负极和隔膜依次层叠在一起,形成多层结构。
4.压实:使用专用的模具对层叠好的材料进行压实,以提高电池的密度和机械强度。
5.切割成片:将压实后的材料切割成小块,即为模块。
2.4 组装组装是将多个模块连接在一起,形成最终的动力电池pack。
组装的主要步骤如下:1.连接器安装:在每个模块上安装连接器,用于连接不同模块之间的导线。
2.模块堆叠:将多个模块按照设计要求堆叠在一起,形成整体结构。
动力电池pack-(22)

❖ 缺点
大容量电池需并联应用 串并联组合设计复杂,组合成本高 串并联组合体积大,影响部分应用
小容量电池串并联与大容量电池的安全性
❖ 突发性安全事故
过充电、过放电、外部短路等可以通过外电路保 护
穿刺、挤压、冲击等外部环境造成的安全问题 单体电池内部短路或电池组内部分短路的自身安
全性问题
❖ 可靠性大部分是由电极的不可靠性(如毛刺等)引起。
电极和隔膜的可靠性仅与其应用面积有关; 同样容量下,小电池并联与大电池电极面积是基本相同的
结论:小电池并联与大电池可靠性相同
❖ 电池制作工艺上,小电池的可靠性与成品率要高于大电池 ❖ 小电池并联在温度、寿命方面比大电池更有优势。
不同组合方式的 ❖ 并联电池容量不能差别太大。
电池串并联组合的可靠性
影响单体电池可靠性的主要因素
❖ 单体电池的可靠性与各部件的可靠性有关:
外壳(r1)、隔膜(r2)、正极组(r3)、负极组(r4)、电解液(r5)等 电池的可靠性=r1×r2×r3×r4×r5
❖ 外壳、电解液等部件的可靠性在电池分选、配组时控制, 可以控制为1
以20Ah锂离子电池为例: ❖ 20Ah (3.6V) 72Wh 259.2KJ ❖ 1 克TNT 4.20KJ ❖ 20Ah锂离子电池的能量 61.7克TNT能量
20Ah锂离子电池仅存储的电能相当于61.7克TNT炸药的能量。 以上计算还未计电解液燃烧所含能量,及正极活性物质分解的能量。
电解液的能量
❖可靠性方面
串联数学模型:
n
Rs(t) Ri (t)
i 1
并联数学模型:
m
Rs(t) 1 1 Ri (t)
i 1
串并联数学模型:
动力电池电芯、模组、PACK基础知识介绍

三、电池PACK
电池PACK爆炸图
谢谢观看
左-圆柱电芯 中-方壳电芯 右-软包电芯
三、电池模组
通过组装单体电芯,通过汇流排将电芯组成不同的串并联,可用电阻焊、超声焊接、超声 铝丝焊及激光焊接。
左-圆柱模组 中-方壳模组 右-软包模组
三、电池PACK
主要包括电池模块、机构系统、电气系统、热管理系统和BMS几个部分。
电池模块:如果把电池PACK比作一个人体,那么模块就是“心脏”,负责储存和释放能量, 为汽车提供动力。 机构系统:主要由电池PACK上盖、托盘、各种金属支架、端板和螺栓组成,可以看作是电 池PACK的“骨骼”,起到支撑、抗机械冲击、机械振动和环境保护(防水防尘)的作用。 电气系统:主要由高压跨接片或高压线束、低压线束和继电器组成。高压线束可以看作是 电池PACK的“大动脉血管”,将动力电池系统心脏的动力不断输送到各个需要的部件中,低 压线束则可以看作电池PACK的“神经网络”,实时传输检测信号和控制信号。 热管理系统:热管理系统主要有4类:风冷、水冷、液冷、相变材料。以水冷系统为例,热 管理系统主要由冷却板,冷却水管、隔热垫和导热垫组成。热管理系统相当于是给电池 PACK装了一个空调。 BMS:Battery management system 电池管理系统,可以看作是电池的“大脑”。BMS的主要 功能包括:电池物理参数实时监测;电池状态估计;在线诊断与预警;充、放电与预充控制 ;均衡管理和热管理等。
动力电池电芯、模组、 PACK基础知识介绍
一、动力电池简介
什么叫PACK电池包?
首先要了解锂电池单体、锂电池模组和锂电 池包的大致区分:
电池单体(cell):组成电池组和电池包的最基 本的元素,一般能提供的电压是3v-4v之间;
动力电池pack (30)

动力电池pack (30)动力电池pack (30)是一种高性能锂离子电池组,由30个单独的锂离子电池单元组成。
这种电池组通常用于电动汽车、混合动力汽车和其他电池存储应用中。
技术规格每个单元的额定电压为3.7伏,容量为不低于2600毫安时(mAh)。
整个电池组的总电压和容量取决于串联和并联的单元数量。
典型的动力电池pack (30)电压为111伏,容量为78安时(Ah)。
这种电池组的优势是高性能和长寿命。
由于其高能量密度和较低的自放电率,它具有长时间的循环寿命和稳定的电压输出。
应用动力电池pack (30)通常被用于需要高性能、长寿命和大容量的应用中。
以下是该电池组可以应用的领域:1. 电动汽车动力电池pack (30)是电动汽车最常用的电池组类型之一。
它的高容量和高功率输出使得电动汽车能够在单次充电时获得更长的行驶里程。
2. 混合动力汽车混合动力汽车通常使用动力电池pack (30)来存储电能,并用来提供动力辅助驱动燃油发动机。
这种电池组的高性能和长寿命使得混合动力汽车具有更高的燃油效率和更低的尾气排放。
3. 电池存储系统动力电池pack (30)也可以被用来构建电池存储系统,以供电网平衡或其他应用。
由于其高能量密度和丰富的容量,该电池组可以有效地存储大量的电能,并在需要时提供给电网或其他电力应用。
动力电池pack (30)是一种高性能和长寿命的锂离子电池组,适用于电动汽车、混合动力汽车和电池存储等应用。
它的高能量密度和丰富的容量使得其能够提供更长的行驶里程和更高的能量存储效率。
动力电池pack生产工艺
动力电池pack生产工艺动力电池 pack 生产工艺动力电池 pack 是电动汽车中的核心组件之一,它由多个动力电池单体组成,并包括电池管理系统和连接器等附件。
动力电池 pack 的生产工艺可以分为以下几个步骤:第一步,电池单体制备。
电池单体是动力电池 pack 的基本组成单元,需要先制备好。
电池单体的制备主要包括正负极锂离子电极的制备、隔膜的湿润、电解质注入和电池单体封装等步骤。
电极的制备包括材料混合、分散、涂覆和烘干等工序。
隔膜的湿润需要将隔膜与电解液接触并吸附一定的液体,以增强电池的电导性能。
电解质注入是将电解液注入到电池单体中,以提供离子导电路径。
最后,电池单体封装是将正负极电极与隔膜叠层后进行封装,以保证电池单体的密封性和安全性。
第二步,电池单体测试和分级。
电池单体制备完成后,需要进行测试和分级,以确保电池单体的质量和性能符合要求。
电池单体测试包括电压、容量、内阻和温度等指标的测试,通过严格的测试流程,筛选出合格的电池单体。
而电池单体分级是根据电压、容量和内阻等参数的不同,将电池单体进行分组,以满足动力电池 pack 对于性能和容量的需求。
第三步,电池 pack 组装。
电池单体测试和分级完成后,可以进行电池 pack 的组装。
电池 pack 的组装包括电池单体的串联和并联,以及配备电池管理系统和连接器等附件。
电池单体的串联是将多个电池单体通过连接片连接在一起,构成电池pack 的电压需求;而电池单体的并联是将多组电池单体串联后再进行并联,以增加 pack 的容量。
此外,电池管理系统是电池 pack 的智能管理核心,它能够监测和控制电池 pack 的状态和性能,以保证电池 pack 的安全和稳定运行。
第四步,电池 pack 测试和调试。
在电池 pack 组装完成后,还需要进行测试和调试,以确保电池 pack 的性能和安全符合要求。
电池 pack 测试主要包括电压、容量、内阻和温度等指标的测试,以验证电池 pack 的性能是否达到设计要求。
动力电池主要零部件介绍
动力电池主要零部件介绍动力电池是电动汽车、混合动力汽车等电动车辆的关键组件之一,负责存储和释放电能以驱动电动机。
一个典型的动力电池系统包含多个主要零部件,以下是这些零部件的简要介绍:1.电池组(Battery Pack):电池组是由若干个电池单体组成的整体。
它负责存储电能,并通过电池管理系统(BMS)进行监控和管理。
电池组的设计和布局取决于车辆的要求,包括电压、能量密度和功率密度等。
2.电池单体(Battery Cell):电池单体是电池组的基本构建块,通常是锂离子电池。
这些电池单体被组装在一起,以形成整个电池组。
电池单体的性能和寿命对整个电池系统的性能至关重要。
3.电池管理系统(Battery Management System,BMS):BMS 是一个电子系统,负责监控和管理电池组中各个电池单体的状态。
它监测电池的电压、温度、充放电状态等参数,以确保电池的安全运行和最大寿命。
4.热管理系统:电池在充放电过程中会产生热量,因此需要一个热管理系统来维持适当的工作温度。
这可能包括液冷或空气冷却系统,以防止电池过热影响性能和寿命。
5.电池电控系统(Battery Control System,BCS):电池电控系统负责控制电池的充放电过程,以满足车辆动力需求。
它与整车控制系统协同工作,确保电池系统的高效运行。
6.电池冷却板:用于散热的散热片或散热板,有助于保持电池的温度在合适的范围内,以提高电池的效率和寿命。
7.高压连接器:电池系统中使用的高压连接器用于连接电池组和电动驱动系统,确保高电压的安全传输。
8.安全系统:包括过电流保护、过温保护、短路保护等,以确保电池在各种条件下都能安全运行。
9.电缆和连接器:用于连接电池组和整车系统的电缆和连接器,传输电能和数据信号。
10.辅助电池:为电池管理系统和其他辅助设备提供电源的小型电池,通常是12V电池。
这些主要零部件共同构成了动力电池系统,其设计和性能直接影响着电动车辆的续航能力、性能和安全性。
动力电池pack包组成分类
动力电池pack包组成分类
根据不同的电池组成和结构特点,动力电池pack包可以分为以下几类:
1. 单体电池组合包(Single Cell Pack):包含多个单体电池,通过连接器或者焊接方式连接在一起,形成一个整体的电池组。
2. 平行组合包(Parallel Pack):将多个相同类型的电池并联连接在一起,增加电池的容量和电流输出能力。
3. 串联组合包(Series Pack):将多个相同类型的电池串联连接在一起,增加电池的电压输出能力。
4. 混合组合包(Mixed Pack):将不同类型的电池按照一定的规则组合在一起,以满足特定的需求,例如同时提供高容量和高电压输出。
5. 模块化组合包(Modular Pack):将电池分成多个模块,每个模块包含多个单体电池,并且具有独立的电子管理系统(BMS)和连接器,以方便维护和更换。
这些分类方式并不是互斥的,实际上,动力电池pack包往往是多种组合方式的综合应用。
不同的电池组合方式可以根据需求选择,以满足不同的功率、能量和安全性要求。
动力电池模组和pack定义
动力电池模组和pack定义动力电池模组和pack定义动力电池是指用于驱动电动汽车的电池,它是电动汽车的核心部件之一。
而动力电池模组和pack则是构成整个动力电池系统的重要组成部分。
一、动力电池模组定义1.1 概念动力电池模组是指将多个单体电池通过串联或并联方式连接在一起,形成一个整体的装置。
1.2 组成一个典型的动力电池模组包括:单体电池、连接器、散热器、保护板等部件。
1.3 功能- 通过对多个单体电池进行串联或并联,实现对整个系统的能量存储和释放管理;- 保护单体电池免受过度放电或充电等异常情况的影响;- 提高整个系统的安全性和稳定性;- 减少整个系统的重量和体积。
二、动力电池pack定义2.1 概念动力电池pack是指将多个动力电池模组通过串联或并联方式连接在一起,形成一个更大的装置。
2.2 组成一个典型的动力电池pack包括:多个动力电池模组、控制器、散热器、保护板等部件。
2.3 功能- 通过对多个动力电池模组进行串联或并联,实现对整个系统的能量存储和释放管理;- 保护动力电池模组免受过度放电或充电等异常情况的影响;- 提高整个系统的安全性和稳定性;- 减少整个系统的重量和体积。
三、动力电池模组和pack的区别3.1 定义动力电池模组是将多个单体电池通过串联或并联方式连接在一起形成一个整体;而动力电池pack是将多个动力电池模组通过串联或并联方式连接在一起形成一个更大的装置。
3.2 组成动力电池模组包括:单体电池、连接器、散热器、保护板等部件;而动力电池pack包括:多个动力电池模组、控制器、散热器、保护板等部件。
3.3 功能两者功能基本相同,都是实现对整个系统的能量存储和释放管理,保护单体电池/动力电池模组免受过度放电或充电等异常情况的影响,提高整个系统的安全性和稳定性,减少整个系统的重量和体积。
四、动力电池模组和pack的应用动力电池模组和pack广泛应用于电动汽车、混合动力汽车、轨道交通等领域。
- 1、下载文档前请自行甄别文档内容的完整性,平台不提供额外的编辑、内容补充、找答案等附加服务。
- 2、"仅部分预览"的文档,不可在线预览部分如存在完整性等问题,可反馈申请退款(可完整预览的文档不适用该条件!)。
- 3、如文档侵犯您的权益,请联系客服反馈,我们会尽快为您处理(人工客服工作时间:9:00-18:30)。
软包装电池组合形式
串并联组合设计注意点
❖ 如何降低电池组合的内阻 ❖ 串联容量的一致性 ❖ 并联内阻的均匀性 ❖ 单体电池电流的均匀性
国内与国外电池及系统设计的差别
1 注重电池与组合、系统整体设计 2 注重应用过程中的均一性设计(温度、电流)
Prius电池结构的改进
均衡的目的和意义
现有的均衡技术
靠性
大容量电池与小容量电池并联特征
大容量电池的特点
❖ 优点
组合方便 指标占优势(体积比能量、质量比能量等) 组合方便,仅需考虑串联组合 应用体积优势
❖ 缺点
工艺复杂,合格率低 内部电流密度、温度的分布均匀性 部分结构电池(如软包装等,引流能力受限)
小容量电池的特点
❖ 优点
电池表面积/体积大,散热性能好 圆柱:比表面积/体积=2*(1/h+1/r),其中,h指高度,r指半 径; 方形电池时,比表面积、体积=2*(1/a+1/b+1/c),a、b、 c分别指电池的长、宽、高)
影响小
❖ 大容量电池
保护措施少 内部问题释放能量大,连锁反应引起周围电池故
障,安全失控
安全性随使用循环变坏
❖ 随着动力电池使用次数的增多,电池的内阻增大, 容量逐渐降低,电池性能逐渐变坏。
❖ 循环后的安全性对热扰动性敏感性更大。 ❖ 电池的安全性是相对的, 一定循环次数之前的电
池安全测试是合格的,而经过一定循环次数后电池 将呈现出不安全因素。
均衡的目的
均衡的目的是补充由于电池自放电等不一 致引起的电池容量的差别,电池实际容量仍 基本保持一致。
➢ 电池自身自放电引起的差别 ➢ 应用中环境不一致引起的自放电差别
均衡电流的大小
❖ 弥补电池自放电引起的差别
假设电池自放电每月最大差别10%,电池组容量500Ah。 充电时间5~8h,均衡时间4h,每次充电后均衡完全,则:
❖最常见的是电池内部为短路、短路等引起的安全性问 题
热量分布均匀性
小电池并联与大电池的安全性比较
电动汽车对电池安全性的要求
❖ 安全性是电动汽车第一指标。 ❖ 电动汽车电池的使用特点: 高速移动、剧烈震动、高温工作、
快速充放电,潜在着撞击、刺伤、短路、跌落、浸水、火烧、 甚至枪击的可能性。 ❖ 因此,电动汽车对动力电池的安全性要求极高,对百万分之一 的非安全概率都会造成极其严重的后果,它意味着大陆年产100 万辆新能源汽车每年都要发生多起安全事故。 ❖ 对锂动力电池科研、生产、使用过程:召回制度、安全隐患对 锂电池企业是致命性的打击。 ❖ 安全、安全、再安全是锂动力电池永久的话题。
安全系数高
❖ 缺点
大容量电池需并联应用 串并联组合设计复杂,组合成本高 串并联组合体积大,影响部分应用
小容量电池串并联与大容量电池的安全性
❖ 突发性安全事故
过充电、过放电、外部短路等可以通过外电路保 护
穿刺、挤压、冲击等外部环境造成的安全问题 单体电池内部短路或电池组内部分短路的自身安
全性问题
❖ 电池组设计电流分布的差异
❖ 不能解决电池实际容量的差别
电池组容量由最低电池容量确定,不可能因为均衡而使 电池组容量超过最低单体容量
❖ 均衡对保护是否有作用
有专门的充放电保护,不能起到作用
❖ 实时均衡或放电均衡是否对电池组容量有作用
放电期间大部分时间电压差别很小,只在最后有作用; 均衡电流有限,作用不明显
❖ 混合动力应用中实时均衡可在一定程度上提高一致 性,延长维护周期
艺简单
,机械强度低
广泛(动力类及消费类)
动力电池
动力电池
电池结构
软包装
圆柱
方形
电池结构
代表性厂家
❖ 圆柱形产品:A123、Valance、力神、CENS、 微宏等
❖ 方形电池:星恒、雷天、洛阳天空、力神、 ATL、国轩等
❖ 软包装:中信国安、万向、双登、丰江等
相对来讲,纯电动汽车用软包装和方形电池居多, 混合电动车用圆柱和方形(金属壳体)居多。
锂离子电池为何可并联应用?
锂离子电池的充电特点
❖ 电压严格限制,受温度等变动影响不大; 超出电压容易受损。
❖ 充电电压单调变化(镍氢电池充电后期 会出现电压下降现象)
❖ 充电效率高,充电过程中基本无副反应
电压V
1.6 1.55
1.5 1.45
1.4 1.35
1.3 1.25
1.2 0
0.1C 0.5C 1C
20
40
60
80 100 120 140 160
%容量
锂电池为何能并联?
❖ 充电为最高电压限制,并联电池电压一致 ❖ 充电、放电电压单方向变化 ❖ 电压限制参数受温度等外界因素影响不大
并联电池的优点
❖ 小电池并联比直接采用大电池安全性更好 ❖ 小电池并联比直接采用大电池的电流通过能力强 ❖ 使用过程中并联电池之间电流可以根据各电池的能
方案2的可靠性 R2=(0.99)100=0.366
结论:1 串联电池数量越多,电池组可靠性越低 2 100只电池串联电池组保证0.9的可靠性,单体电池可靠性需达到0.999 3 单体电池可靠性不独立,则大电池、小电池并串联组合可靠性相同。
单体电池具有独立可靠性的比较
❖ 单体电池可靠性独立(并联电池有1只故障,并不影 响其他电池的应用):
❖可靠性方面
串联数学模型:
n
Rs(t) Ri(t)
i1
并联数学模型:
m
Rs(t)1 1Ri(t)
i1
串并联数学模型:
Rs(t)11n
m
Ri(t)
i1
并串联数学模型:
n
R s(t) 11R i(t)m
i 1
Rs(t)表示系统的可靠度; R=(1,2,3…,n)表示第i个单元的可靠度。
并串联与串并联比较
世界上没有绝对安全的电池
❖ 电池是能量的载体,本质上就存在不安全因素。 ❖ 不同的电化学体系,不同的容量,使用工艺参数,
使用环境,使用程度,都对安全性有较大的影响。 ❖ 所有的安全性均与温度有关:控制温度的重要性。 ❖ 所有电池包括一次电池、各类二次电池,均存在
安全性问题
安全性本质:电池中的能量
方案1的可靠性 若有2只电池或2只以上的电池损坏,则并联组失效(按 容量80%终止假设) R1=(0.99910+ C1090.9999 *0.001)100=0.991
方案2的可靠性 R2=(0.99)100=0.366
结论:1 合理的电池设计和PACK设计可提高电池组的可靠性 2 单体电池可靠性独立,采用小电池并联可大幅度提高电池组可
❖ 可靠性比较
设单个电池的可靠度相同,Ri=0.99,100只电池串联,4只电池并联:
并串联可靠度:0.999999 串并联可靠度:0.8385
❖ 电池管理成本
锂电池需要管理到每只单体 先串联后并联需要增加管理系统成本 先串联后并联的电路无环流处理
单体电池具有独立可靠性的比较
❖ 组合要求:
100只电池串联 两种电池形式
❖ 1:10只10Ah电池并联成100Ah ❖ 2:100Ah单体电池
❖ 假设条件:
电池可靠性仅与电极面积大小有关。 10Ah电池可靠性为0.999,则100Ah电池可靠性约为0.99。
❖ 单体电池可靠性不独立(并联电池有1只故障,则并联组合失效):
方案1的可靠性 R1=(0.99910)100=0.366
❖ 通常控制电池包内温差不超过5℃ ❖ 5℃的差别电池之间衰减速度差别就达30%
控制电池包温差的主要原因之一
微观环境的影响
❖ 电池模块内温度的差异
应用中不能检测到每只电池的温度 模块内不同部位电池的温度差异 模块散热表面与单体电池散热表面的差异
❖ 单体电池内部温度的差异
电池各部位所处环境温度的不一致
❖ 锂离子电池的电解液用量 6mL/AH ❖ 汽油的密度 0.71克/mL ❖ 1 克汽油 42KJ ❖ 1 克TNT 4.183KJ ❖ 1 Ah电池的电解液能量 178.9KJ ❖ 1 Ah电池的电解液能量 42.6克 TNT ❖ 20 Ah电池的电解液能量 832克 TNT
注意:该能量不具备直接爆炸条件
❖ 并联电池的自放电基本一致。 ❖ 并联电池容量不能差别太大。
电池串并联组合的可靠性
影响单体电池可靠性的主要因素
❖ 单体电池的可靠性与各部件的可靠性有关:
外壳(r1)、隔膜(r2)、正极组(r3)、负极组(r4)、电解液(r5)等 电池的可靠性=r1×r2×r3×r4×r5
❖ 外壳、电解液等部件的可靠性在电池分选、配组时控制, 可以控制为1
均衡电流=(50/(30*4))=417mA
每次均衡充电满足4h,均衡电流400~500mA即可。
均衡的研究与发展
❖ 目前通常仅依靠电压或电压差别来考虑均衡 ❖ 如何将电池内阻等参数结合进去 ❖ 放电均衡的高效果实现
电池组的寿命与单体电池寿命为何差异巨大
宏观环境的差异
❖ 实际适用环境温度与试验温度的差异 温度对寿命影响符合Arrhenius公式
新能源汽车 锂离子电池组的设计与应用
目录
❖ 锂离子电池为何可并联应用? ❖ 电池串并联组合的可靠性 ❖ 大容量电池与小容量电池并联特征 ❖ 小电池并联与大电池的安全性比较 ❖ 不同结构的电池特性 ❖ 电池组合形式 ❖ 均衡的目的和意义 ❖ 电池组的寿命与单体电池寿命为何差异巨大? ❖ 纯电动汽车用动力电源系统的设计
电池组合形式
圆柱电池的并串联组合形式
❖ 最常用的方法:并排焊接
问题1:焊接的不可靠性 问题2:导电连接体局部电流密度过大 问题3:一个方向组合,叠层组合难度大 问题4:连接件的锈蚀
改装Prius车电源系统(圆柱锂离子电池)