智能制造中的生产调度算法
智能制造中的AGV系统设计与调度算法研究

智能制造中的AGV系统设计与调度算法研究在智能制造领域中,自动导引车(Automated Guided Vehicle, AGV)系统被广泛应用于物流、仓储和生产线等环节,以提高生产效率、降低人力成本和提高生产质量。
本文针对AGV系统的设计和调度算法展开研究,旨在优化系统的运行效率和资源利用率,以满足智能制造的需求。
一、AGV系统设计在AGV系统的设计中,包括了AGV的基本设计和系统架构的设计两个方面。
1. AGV的基本设计AGV是智能制造中不可或缺的重要组成部分,其基本设计需考虑以下几个关键因素。
首先,需要确定AGV的载荷能力和运行速度。
根据物流和仓储的需求,确定AGV的最大载荷能力,以确保能够承载所需的货物。
同时,根据生产线的需求和工作环境,确定AGV的合适运行速度,以达到高效的运输。
其次,AGV的导航和感知技术至关重要。
AGV需要具备自主感知和导航的能力,以便在复杂的生产环境中进行智能避障和准确导航。
选择合适的传感器和导航系统,并进行合理布局和设计,是关键的技术问题。
最后,对AGV的通信和控制系统进行设计。
AGV系统需要实现与中央控制系统的通信,以便接收任务指令和交互信息。
设计合理的通信和控制系统,可以有效调度和协调AGV的运行,在提高生产效率的同时保证系统安全和稳定性。
2. 系统架构设计除了AGV的基本设计外,系统架构设计是整个AGV系统的关键性任务。
在系统架构设计中,需要考虑以下几个方面。
首先,需要确定AGV的分布和布局。
根据生产线的布局和物流需求,合理安排AGV的数量和位置,以达到整体的运行效果最优化。
其次,系统架构需包括任务分发和调度模块。
任务分发模块负责将任务分发给各个AGV,并进行合理的调度。
调度算法的设计是系统架构设计中的关键任务,可以通过动态规划、遗传算法等方法来实现任务调度。
最后,还需考虑AGV之间的协作和通信。
AGV之间的合作和通信可以实现任务分配的精细化和协调运行,提高系统运行效率。
面向智能制造车间的AGV系统调度算法设计
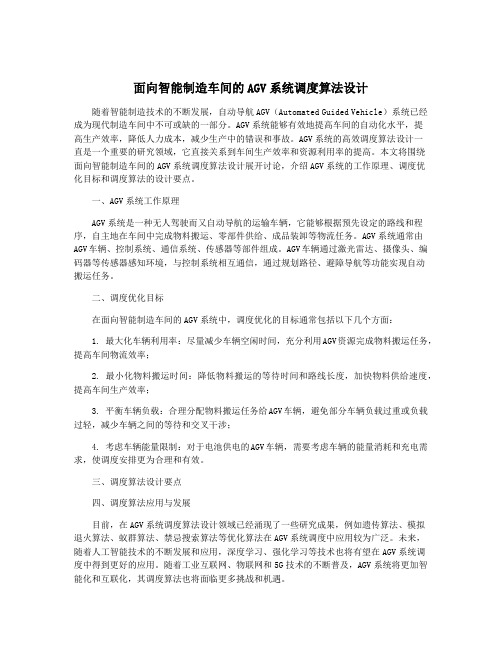
面向智能制造车间的AGV系统调度算法设计随着智能制造技术的不断发展,自动导航AGV(Automated Guided Vehicle)系统已经成为现代制造车间中不可或缺的一部分。
AGV系统能够有效地提高车间的自动化水平,提高生产效率,降低人力成本,减少生产中的错误和事故。
AGV系统的高效调度算法设计一直是一个重要的研究领域,它直接关系到车间生产效率和资源利用率的提高。
本文将围绕面向智能制造车间的AGV系统调度算法设计展开讨论,介绍AGV系统的工作原理、调度优化目标和调度算法的设计要点。
一、AGV系统工作原理AGV系统是一种无人驾驶而又自动导航的运输车辆,它能够根据预先设定的路线和程序,自主地在车间中完成物料搬运、零部件供给、成品装卸等物流任务。
AGV系统通常由AGV车辆、控制系统、通信系统、传感器等部件组成。
AGV车辆通过激光雷达、摄像头、编码器等传感器感知环境,与控制系统相互通信,通过规划路径、避障导航等功能实现自动搬运任务。
二、调度优化目标在面向智能制造车间的AGV系统中,调度优化的目标通常包括以下几个方面:1. 最大化车辆利用率:尽量减少车辆空闲时间,充分利用AGV资源完成物料搬运任务,提高车间物流效率;2. 最小化物料搬运时间:降低物料搬运的等待时间和路线长度,加快物料供给速度,提高车间生产效率;3. 平衡车辆负载:合理分配物料搬运任务给AGV车辆,避免部分车辆负载过重或负载过轻,减少车辆之间的等待和交叉干涉;4. 考虑车辆能量限制:对于电池供电的AGV车辆,需要考虑车辆的能量消耗和充电需求,使调度安排更为合理和有效。
三、调度算法设计要点四、调度算法应用与发展目前,在AGV系统调度算法设计领域已经涌现了一些研究成果,例如遗传算法、模拟退火算法、蚁群算法、禁忌搜索算法等优化算法在AGV系统调度中应用较为广泛。
未来,随着人工智能技术的不断发展和应用,深度学习、强化学习等技术也将有望在AGV系统调度中得到更好的应用。
基于人工智能的智能车间调度优化算法研究

基于人工智能的智能车间调度优化算法研究随着人工智能技术的快速发展,智能制造也越来越受到关注。
智能车间调度是智能制造的关键环节之一,在提高生产效率和降低成本方面起着重要作用。
本文将针对智能车间调度优化算法进行研究,探讨基于人工智能的解决方案。
1. 引言在传统的车间调度中,调度员通常根据经验和手动计算进行决策。
然而,在面对大规模、复杂的生产任务时,传统方法往往效率低下、难以适应实时变化。
基于人工智能的智能车间调度优化算法能够通过自动化和智能化的方式,快速、准确地进行决策,提高车间生产效率和资源利用率。
2. 智能车间调度优化算法的基本原理智能车间调度优化算法的基础是人工智能技术,尤其是深度学习和强化学习。
它通过对车间内生产任务的特征进行分析和学习,在不同的约束条件下找到最优的调度方案。
优化算法的基本原理包括以下几个方面:2.1. 任务特征分析首先,算法需要深入了解车间内各个生产任务的特征,如工艺流程、任务时间、紧急程度等。
这些特征信息将作为模型输入,帮助算法更好地进行决策。
2.2. 规划模型建立基于任务特征分析的基础上,算法需要建立一种合适的规划模型。
常见的模型有松弛的工厂调度问题(Relaxed workshop scheduling problem)和紧迫性工厂调度问题(Urgency-based workshop scheduling problem)等。
2.3. 特征学习与预测利用深度学习技术,算法可以对车间内的任务特征进行学习和预测,并根据预测结果生成车间调度。
2.4. 强化学习与优化强化学习是智能车间调度优化算法中的关键技术之一。
通过建立合适的奖励函数和状态-动作空间,算法能够通过试错的方式不断优化调度方案,逐步达到最优。
3. 实验与结果分析为了验证智能车间调度优化算法的有效性,我们在实际生产环境中进行了一系列实验。
我们选取了一个中型汽车制造工厂作为测试对象,实验结果表明:3.1. 生产效率提高智能车间调度优化算法成功提高了生产效率。
面向智能制造车间的AGV系统调度算法设计
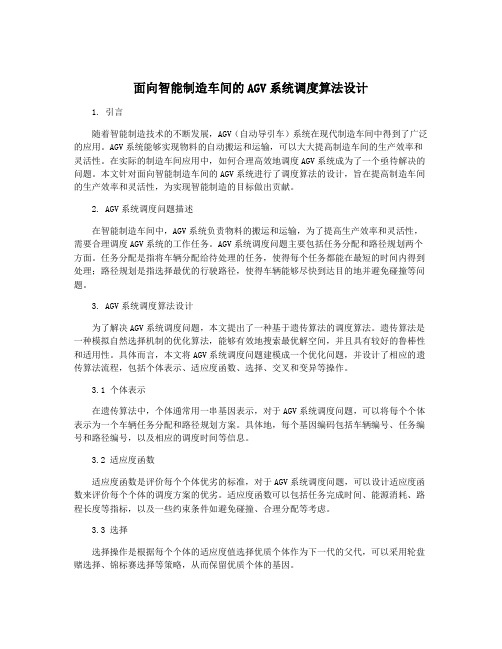
面向智能制造车间的AGV系统调度算法设计1. 引言随着智能制造技术的不断发展,AGV(自动导引车)系统在现代制造车间中得到了广泛的应用。
AGV系统能够实现物料的自动搬运和运输,可以大大提高制造车间的生产效率和灵活性。
在实际的制造车间应用中,如何合理高效地调度AGV系统成为了一个亟待解决的问题。
本文针对面向智能制造车间的AGV系统进行了调度算法的设计,旨在提高制造车间的生产效率和灵活性,为实现智能制造的目标做出贡献。
2. AGV系统调度问题描述在智能制造车间中,AGV系统负责物料的搬运和运输,为了提高生产效率和灵活性,需要合理调度AGV系统的工作任务。
AGV系统调度问题主要包括任务分配和路径规划两个方面。
任务分配是指将车辆分配给待处理的任务,使得每个任务都能在最短的时间内得到处理;路径规划是指选择最优的行驶路径,使得车辆能够尽快到达目的地并避免碰撞等问题。
3. AGV系统调度算法设计为了解决AGV系统调度问题,本文提出了一种基于遗传算法的调度算法。
遗传算法是一种模拟自然选择机制的优化算法,能够有效地搜索最优解空间,并且具有较好的鲁棒性和适用性。
具体而言,本文将AGV系统调度问题建模成一个优化问题,并设计了相应的遗传算法流程,包括个体表示、适应度函数、选择、交叉和变异等操作。
3.1 个体表示在遗传算法中,个体通常用一串基因表示,对于AGV系统调度问题,可以将每个个体表示为一个车辆任务分配和路径规划方案。
具体地,每个基因编码包括车辆编号、任务编号和路径编号,以及相应的调度时间等信息。
3.2 适应度函数适应度函数是评价每个个体优劣的标准,对于AGV系统调度问题,可以设计适应度函数来评价每个个体的调度方案的优劣。
适应度函数可以包括任务完成时间、能源消耗、路程长度等指标,以及一些约束条件如避免碰撞、合理分配等考虑。
3.3 选择选择操作是根据每个个体的适应度值选择优质个体作为下一代的父代,可以采用轮盘赌选择、锦标赛选择等策略,从而保留优质个体的基因。
智能制造系统中的自动调度算法与方法

智能制造系统中的自动调度算法与方法智能制造系统是以人工智能和物联网技术为核心的先进制造模式,旨在提高生产效率、降低成本、提升产品质量和灵活性。
自动调度是智能制造系统中至关重要的环节,能够在生产过程中根据实时情况合理安排任务和资源,实现高效的生产调度和优化。
自动调度算法和方法是实现智能制造系统自动调度的重要工具。
它们通过智能的数据处理和分析,确定最佳的任务分配和资源调度策略,以提高生产效率和降低成本。
下面,将介绍几种常用的自动调度算法和方法。
1. 启发式调度算法启发式调度算法是根据以往的经验和启发规则来决策的。
它通过考虑任务的紧急程度、资源的利用率以及设备间的重要性等因素来进行决策。
此类算法追求快速、高效和合理的任务调度,并能够灵活应对不确定的生产情况。
其中,最常用的启发式调度算法有贪婪算法、遗传算法和模拟退火算法等。
贪婪算法是一种优先级调度算法,其通过对任务和资源进行加权,选择具有最高加权的任务进行调度。
该算法适用于快速解决简单任务调度问题,但可能无法找到全局最佳解。
遗传算法与自然界中的进化过程类似,通过模拟基因的选择、交叉和变异等操作,逐步优化调度结果。
遗传算法具有较好的全局搜索能力和优化性能,适用于复杂问题的解决,但计算复杂度较高。
模拟退火算法则通过模拟金属退火过程来寻找最优解。
它具有较好的局部搜索能力,能够在一定程度上克服贪婪算法的局限性,但在处理大规模问题时计算开销较大。
2. 智能优化算法智能优化算法是一类基于优化理论和人工智能技术的自动调度方法。
常见的智能优化算法包括蚁群算法、粒子群算法和人工神经网络等。
蚁群算法是通过模拟蚁群觅食行为寻求最优调度路径。
蚁群算法具有较强的适应性和鲁棒性,能够很好地解决复杂调度问题,但时间复杂度较高。
粒子群算法则通过模拟鸟群觅食觅食行为进行优化。
粒子群算法能够快速找到较好的解,但与蚁群算法相比,其全局搜索能力稍弱。
人工神经网络是模拟人类神经系统行为的一种优化方法。
智能制造系统中的生产过程优化与资源调度策略研究
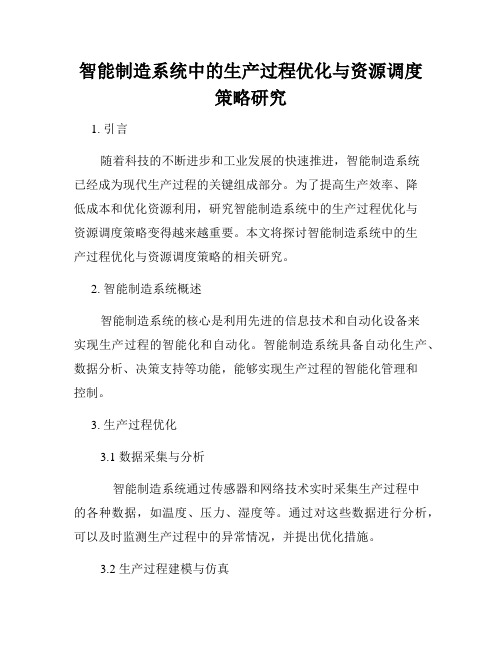
智能制造系统中的生产过程优化与资源调度策略研究1. 引言随着科技的不断进步和工业发展的快速推进,智能制造系统已经成为现代生产过程的关键组成部分。
为了提高生产效率、降低成本和优化资源利用,研究智能制造系统中的生产过程优化与资源调度策略变得越来越重要。
本文将探讨智能制造系统中的生产过程优化与资源调度策略的相关研究。
2. 智能制造系统概述智能制造系统的核心是利用先进的信息技术和自动化设备来实现生产过程的智能化和自动化。
智能制造系统具备自动化生产、数据分析、决策支持等功能,能够实现生产过程的智能化管理和控制。
3. 生产过程优化3.1 数据采集与分析智能制造系统通过传感器和网络技术实时采集生产过程中的各种数据,如温度、压力、湿度等。
通过对这些数据进行分析,可以及时监测生产过程中的异常情况,并提出优化措施。
3.2 生产过程建模与仿真在智能制造系统中,通过对生产过程进行建模和仿真,可以尽可能地模拟真实生产环境,预测生产过程中的问题和瓶颈,并提前采取措施进行优化。
3.3 供应链管理在智能制造系统中,通过对供应链的综合管理,可以优化原材料和零部件的供应,确保生产过程的持续稳定运行。
4. 资源调度策略4.1 生产设备调度生产设备是智能制造系统中的核心要素之一,合理的设备调度可以提高生产效率和保障产品质量。
通过制定合理的生产计划和优化设备调度策略,可以实现生产过程的连续化和高效化。
4.2 人力资源调度在智能制造系统中,通过合理调度人力资源,可以提高生产过程的灵活性和适应性。
通过员工培训和技能认证,提升员工的技术水平和岗位适应能力,实现人力资源的优化配置。
4.3 能源资源调度智能制造系统的运行需要大量的能源支持,通过优化能源的调度策略,可以提高能源利用效率和节约能源成本。
采用可再生能源和优化能源转换装置等措施,可以降低对非可再生能源的依赖程度,减少环境负荷。
5. 应用实例与展望目前,智能制造系统中的生产过程优化与资源调度策略已经在许多领域得到应用。
智能制造中的生产调度优化模型研究
智能制造中的生产调度优化模型研究随着技术的不断发展,智能制造已经成为制造业发展的趋势。
生产调度是智能制造中的一个重要环节,通过对生产过程的分析,确定生产计划和生产调度策略,实现生产过程的优化,提高生产效率和质量。
生产调度优化模型是智能制造中的重要工具,在制定生产计划和生产调度策略时,能够提供科学的依据和支持。
一、智能制造中的生产调度优化模型生产调度是指通过合理的调度安排,实现生产计划的顺利执行和生产过程的高效运作,以达到最大化生产效率和产品质量的目的。
生产调度优化模型是通过对生产过程中的各种因素进行分析和处理,为生产调度提供科学的依据和支持的数学模型。
在智能制造中,生产调度优化模型的建立需要考虑生产过程中的各种因素,包括生产任务、设备状态、作业人员等因素。
同时,还需要考虑到生产过程中的不确定性因素,如设备故障、生产任务变化等,以保证生产调度的高效和稳定。
二、生产调度优化模型的应用生产调度优化模型广泛应用于各种制造业领域,如汽车制造、电子制造、机械制造等。
通过利用生产调度优化模型,企业可以实现生产过程的高效、稳定和可控,从而提高生产效率和产品品质,降低生产成本。
在汽车制造领域,生产调度优化模型应用最为广泛。
随着汽车制造业的快速发展,生产任务的数量和复杂程度不断增加,如何合理安排生产调度成为了企业的头等大事。
通过利用生产调度优化模型,企业可以基于生产任务、设备状态等因素,制定科学合理的生产调度策略,从而保证生产过程的高效、稳定和可控。
三、生产调度优化模型的未来发展随着制造业的快速发展,智能制造、大数据和人工智能等新技术将会对生产调度优化模型的发展带来新的机遇和挑战。
首先,智能制造技术将为生产调度优化模型的发展提供更多的数据支持。
通过采集、分析和利用生产过程中的大数据,可以更准确地把握企业的生产状况,从而实现更加科学合理的生产调度。
其次,人工智能技术的快速发展,将为生产调度优化模型的发展带来更多的可能性。
面向智能制造车间的AGV系统调度算法设计
面向智能制造车间的AGV系统调度算法设计随着智能制造技术的不断发展,AGV(Automated Guided Vehicle)系统在工厂生产车间中的应用越来越广泛。
AGV系统作为智能制造车间的重要组成部分,能够实现物料搬运、工件装配等自动化任务,大大提高了生产效率和产品质量。
在实际的生产过程中,如何有效地调度AGV系统,使其能够高效地完成各项任务,成为了一个亟待解决的问题。
本文将从面向智能制造车间的角度,探讨AGV系统的调度算法设计。
一、智能制造车间的需求分析在智能制造车间中,AGV系统通常需要完成的任务包括物料搬运、工件运输、设备补给等。
这些任务具有一定的复杂性和多样性,需要根据具体的生产情况动态调度AGV系统,以确保生产车间的高效运转。
智能制造车间通常具有多个生产区域,不同区域之间存在物料流动的需求。
AGV系统的调度算法需要考虑不同区域之间的物料运输和协调。
二、AGV系统调度算法设计1. 任务调度分配任务调度分配是AGV系统调度算法的核心部分。
在智能制造车间中,由于生产任务的多样性和复杂性,AGV系统通常需要同时执行多个任务。
如何有效地调度和分配任务,是提高AGV系统运行效率的关键。
在任务调度分配中,可以采用一些经典的调度算法,如最短作业优先、最短剩余处理时间优先等。
还可以结合实际生产情况,采用基于规则的调度策略,根据任务的紧急程度、距离等因素进行动态调度和分配。
2. AGV路径规划AGV路径规划是将任务分配好后,需要确定每个AGV的行驶路径。
在智能制造车间中,由于车间内部存在多个作业区域、设备障碍物等,AGV的路径规划通常需要考虑到多个因素。
为了提高路径规划的精确度和效率,可以采用基于图论的路径规划算法,如Dijkstra 算法、A*算法等。
还可以结合车间实际情况,采用视觉导航、激光雷达等技术,对AGV行驶路径进行实时的动态调整和优化。
3. 车辆协同调度在多AGV系统中,车辆之间的协同调度也是一个关键的问题。
智能制造中的智能生产调度
智能制造中的智能生产调度智能制造被誉为工业的新时代,其带来的生产效率和生产质量的提高给工业带来了革命性的变革。
其中,智能生产调度是智能制造一个重要的组成部分,它的目的是优化生产过程,实现生产线的最高效运转,提高工业生产的生产效率和经济效益。
智能生产调度是指根据生产订单的要求,结合独有的智能计算与智能算法,对工作流程、人员、设备、工具和物料等资源进行策略性规划和调度,以实现生产过程优化的全过程智能决策。
通过智能生产调度的设计和实施,工厂可以实现智能化的生产流程、协同化的管理和优化化的资源调度,从而提高生产和运营的效能和效益。
智能生产调度具有以下特点:1. 强调数据的集中、共享和管理。
智能生产调度必须建立在数据优化和数据管理的基础之上。
只有通过数据的标准化、集成、可视化和共享,才能够提高生产决策的效能和准确度。
数据的存储和管理要充分考虑数据的时效性、准确性和可靠性,保证数据可追溯、真实、可靠。
2. 追求全局最优化目标。
智能生产调度必须追求全局最优。
全局最优是指在考虑各个资源的限制的情况下,最大化生产效率,实现最优生产方案。
全局最优的实现方式需要考虑多个因素,包括生产的瓶颈点、关键节点、设备的运行时序等,通过量化分析,以数据为驱动,实现最优资源调度。
3. 强化智能决策能力。
智能决策是调度系统的重要组成部分。
调度系统利用实时监控生产进程的信息系统和人工智能技术,对已有的制造计划、产品信息等数据进行综合分析,得出最优化的调度方案。
通过大数据处理和分析,以及人工智能的支持,调度系统可以更准确地为生产过程做出决策,使生产效率得到优化,同时可减少生产成本和生产时间。
智能生产调度的实现需要采用多种技术手段:1. 人工智能技术。
利用人工智能技术进行数据挖掘、机器学习、智能规划等操作,提供智能决策和设备自主调度等功能,增强生产过程的智能性。
2. 物联网技术。
物联网技术将生产设备、工具、物料等物理实体与网络相连接,实现设备监控和设备自动化调度,从而提高生产效率和稳定性。
无人工厂智能制造中的生产计划与调度优化
无人工厂智能制造中的生产计划与调度优化随着科技的不断发展和智能制造技术的突破,无人工厂正在逐渐成为制造业的新趋势。
在无人工厂中,人工智能的应用已经实现了生产过程的自动化和智能化,但是为了达到更高效、更灵活的生产模式,生产计划与调度的优化就显得十分重要。
本文将探讨无人工厂智能制造中的生产计划与调度优化策略。
一、生产计划优化在无人工厂中,生产计划的优化是保证生产线平稳运行和高效生产的关键。
通过合理规划和优化生产计划,可以最大程度地提高生产效率,降低生产成本,满足市场需求。
以下是几种常用的生产计划优化策略:1.供需匹配:根据市场需求和生产线的产能,及时调整生产计划,确保供需匹配。
通过实时监测市场需求和库存情况,可以准确预测产品需求量,并根据需求情况灵活调整生产计划。
2.生产线平衡:合理规划生产线的工作负载,避免出现生产线过载或部分工位闲置的情况。
通过分析生产线工序的时间和资源消耗,合理分配任务,提高生产线的利用率和生产效率。
3.材料管理:优化材料库存管理,减少库存成本和材料浪费。
通过精确的材料需求预测和供应链管理,及时补充材料,避免因材料断货或积压造成的生产中断和资金浪费。
二、调度优化调度优化是无人工厂中确保生产任务按时完成的重要环节。
通过合理调度生产任务的执行顺序和资源分配,可以提高生产线的效率和生产能力。
以下是几种常用的调度优化策略:1.任务调度算法:采用合适的任务调度算法,如进程调度算法或遗传算法等,根据任务的优先级和执行时间要求,灵活分配资源和调度任务。
通过优化任务的执行顺序和资源利用率,可以减少等待时间,提高生产效率。
2.自适应调度:利用人工智能和机器学习的技术,建立智能调度系统,根据实时监测的生产数据和环境变化,自动调整生产任务的执行顺序和生产资源的分配,实现自适应调度,提高生产线的适应性和灵活性。
3.协同调度:在无人工厂中,物联网技术的应用使得各个设备和生产线能够实时通信和协同工作。
通过建立协同调度系统,将生产任务和资源分配信息进行实时共享和协调,最大程度地提高生产线的协同效应,实现整体生产效益的最优化。
- 1、下载文档前请自行甄别文档内容的完整性,平台不提供额外的编辑、内容补充、找答案等附加服务。
- 2、"仅部分预览"的文档,不可在线预览部分如存在完整性等问题,可反馈申请退款(可完整预览的文档不适用该条件!)。
- 3、如文档侵犯您的权益,请联系客服反馈,我们会尽快为您处理(人工客服工作时间:9:00-18:30)。
智能制造中的生产调度算法
一、引言
随着科技的不断发展,智能制造成为了未来趋势,旨在提高生
产效率、降低成本。
生产调度是智能制造过程中至关重要的一环,其优化可有效提升生产效率,降低生产成本。
本文将从生产调度
算法方面进行探讨。
二、生产调度算法分类
生产调度算法可以分为静态和动态两种算法。
静态生产调度算法指系统在生产任务开始前安排好生产班次、
生产速率和生产量,并在生产过程中不做任何调整,适用于生产
任务稳定的场景,如批量生产、单品生产等。
动态生产调度算法指系统通过实时监测生产过程中的生产情况,对生产进度、生产速率和生产量进行调整,以适应不同的生产任
务需求,适用于多品种、小批量生产等商业模式,业内称之为“智
能化调度”。
三、静态生产调度算法
静态生产调度可分为先来先服务调度、最短作业优先调度、优先级调度等不同类型。
1. 先来先服务调度
先来先服务调度算法简称 FCFS(First Come, First Served)。
它是最简单、最常见的调度算法之一。
它遵循“先到先处理”的原则,先提交的任务先处理,处理完之后才能处理后来的任务。
优点:算法实现简单,不需要考虑任何优先级和复杂的运算。
缺点:非常不适合对于任务执行时间存在差异的情况,任务之间并没有优先级的规定,会导致长时间的任务会大大影响系统的响应时间。
2. 最短作业优先调度
最短作业优先调度算法简称 SJF(Shortest Job First)。
它根据作业执行的时间长度来选择最短的作业先执行。
优点:可以保证作业平均等待时间最短。
缺点:如果需要计算作业的执行时间,会增加系统的开销。
此外,如果任务的执行时间有变化,会影响后续所有任务的执行时间。
3. 优先级调度
优先级调度算法基于优先级将作业按照优先级排序,在通常情况下优先级越高的任务将会优先执行。
优点:具有较高的响应速度和稳定性,能够有效节约系统资源和时间。
缺点:如果优先级相等,则无法决定先后次序。
四、动态生产调度算法
1. 基于遗传算法的生产调度
基于遗传算法的生产调度算法是将生产调度算法与遗传算法相结合的产物,能够获取未知的状态空间。
它基于染色体母体基因及其生殖操作,运用种群进化的思想,通过适应度函数评估适应度并执行相应的生殖操作。
优点:能够适应动态环境,自适应性好,可以获得较好的生产调度效果。
缺点:运算量大,依赖遗传演化过程。
2. 基于粒子群算法的生产调度
粒子群算法是一种基于群体行为的优化算法。
生产调度用粒子群算法实现,通过不断地优化多个任务之间的关系和任务执行的关系,实现最佳任务执行效果。
优点:可以针对性地优化任务执行顺序,适应性强。
缺点:结果较为复杂,考虑到机器执行顺序较为复杂。
五、结论
不同的生产调度算法适用于不同的场景,优劣之分取决于具体的问题。
在实际应用中,应该根据具体情况选择合适的算法来提高制造效率和节约生产成本。
未来,智能化生产将更加广泛地应用于制造业领域,生产调度算法也将更加智能化和灵活化。