压圈冲压模具设计
冲压模具设计方法与步骤

冲压模具设计方法与步骤冲压模具是制造行业中常用的一种模具,用于在金属板材上进行冲裁、压制、成形等工艺。
冲压模具的设计是冲压工艺的关键环节之一,合理的设计可以提高产品质量和生产效率。
以下是冲压模具设计的方法与步骤。
一、冲压模具设计方法1.分析产品要求:首先需要仔细分析产品要求,了解产品的形状、尺寸、材质等要求,以及要求的生产效率和成本等因素。
2.选择合适的材料:根据产品的要求选择合适的模具材料,常用的材料有合金工具钢、合金冷作工具钢等。
3.制定冲压工艺:根据产品要求,制定冲压工艺,包括冲剪顺序、成形方式、冲压力、冲头形状等因素。
4.设计模具结构:根据产品要求和冲压工艺,设计模具的结构,包括上模、下模、导向机构等部分。
5.进行模具布局:进行模具布局,合理安排模具零件的形状、位置和尺寸,以确保模具的强度和稳定性。
6.进行模具零件设计:根据模具布局,设计模具的零件,包括冲头、导柱、导套、导向板等部分。
7.进行模具装配:根据模具设计,进行模具的装配,确保各个零件之间的配合和精度。
8.进行模具调试:进行模具调试,调整模具的尺寸和位置,确保模具在冲压过程中的稳定性和精度。
9.进行模具试产:进行模具试产,对模具进行试模和试产,检验产品的质量和模具的性能。
10.进行模具改进:根据试产结果,对模具进行改进和优化,提高模具的性能和生产效率。
二、冲压模具设计步骤1.初步设计:根据产品要求,进行初步的模具设计,包括模具结构和布局。
2.详细设计:对初步设计的模具进行详细设计,包括各个零件的形状、尺寸和材料等。
3.模具制造:根据详细设计,进行模具的制造,包括加工模具零部件和进行模具装配。
4.模具调试:对制造完成的模具进行调试,调整模具的尺寸和位置,确保模具的性能和精度。
5.模具试产:进行模具的试模和试产,检验产品的质量和冲压工艺的可行性。
6.模具改进:根据试产结果,对模具进行改进和优化,提高模具的性能和生产效率。
7.模具验收:对改进后的模具进行验收,确保模具达到产品要求和生产效果。
压圈冲压模具设计说明书终极版word资料21页

第1章绪论1.1冲压工艺概述1.1.1 冲压工艺简介冲压是塑性加工的基本方法之一,它是利用安装在压力机上的模具,在室温下对材料施加压力使其产生变形或分离,从而获得具有一定形状、尺寸和精度的制件的一种压力加工方法。
因为它主要用于加工板料制件,所以也称板料冲压。
在机械制造中是一种高效率的加工方式。
冲压广泛应用于金属制品各行业中,尤其在汽车、仪表、军工、家用电器等工业中占有极其重要的地位。
冲压工艺有如下特点:1.能冲压出其它加工方法难以加工或无法加工的形状复杂的零件。
比如,从仪器仪表小型零件到汽车覆盖件、纵梁等大型零件,均由冲压加工完成。
2.冲压件质量稳定,尺寸精度高。
由于冲压加工是有模具成型,模具制造精度高、使用寿命长,故冲压件质量稳定,制件互换性好。
尺寸精度一般可达IT10~IT14级,最高可达到IT6级,有的制件不需要在加工,便可满足装配和使用要求。
3.冲压件具有重量轻、强度高、刚性好和表面粗糙度小等特点。
4.冲压加工生产效率极高,没有其它任何一种机械加工方法能与之相比。
比如,汽车覆盖件这样的大型冲压件的生产效率,可达每分钟数件;高速冲压小型制件,可达每分钟上千件。
5.材料利用率高,一般为70%~85%。
因此冲压件能实现少废料或无废料生产。
在某些情况下,边角余料也可充分利用。
6.操作简单,便于组织生产,易于实现机械化和自动化生产。
对操作工人的技术素质要求不高,新工人经短时培训便能上岗操作。
7.冲压的特点是模具制造时间长、制造成本高,故不适宜于单件小批量生产。
另外,冲压生产多采用机械压力机,由于滑块往复运动快,手工操作时,劳动强度大,易发生事故,故必须特别重视安全生产、安全管理以及采取必要的安全技术措施。
8.冲压模设计需要有很强的想象力与创造力,对于模具的设计者和制造者无论在理论、经验、创造力方面都要有很高的要求。
1.1.2 冲压模具的发展近年来,我国冲压模具水平已有很大提高。
大型冲压模具已能生产单套重量达50多吨的模具。
垫圈冲压模具设计工作原理
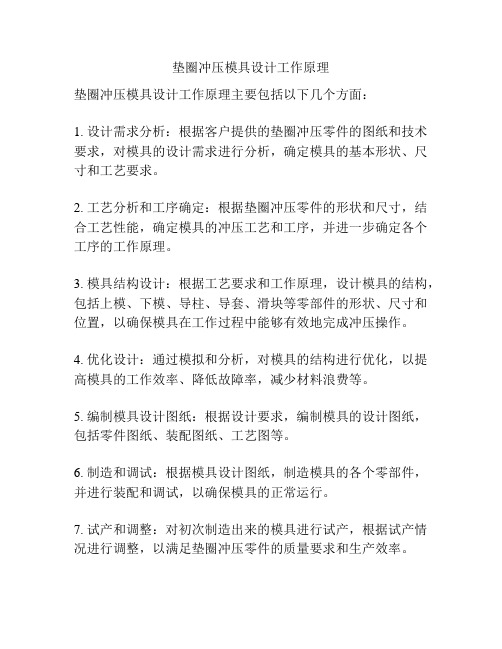
垫圈冲压模具设计工作原理
垫圈冲压模具设计工作原理主要包括以下几个方面:
1. 设计需求分析:根据客户提供的垫圈冲压零件的图纸和技术要求,对模具的设计需求进行分析,确定模具的基本形状、尺寸和工艺要求。
2. 工艺分析和工序确定:根据垫圈冲压零件的形状和尺寸,结合工艺性能,确定模具的冲压工艺和工序,并进一步确定各个工序的工作原理。
3. 模具结构设计:根据工艺要求和工作原理,设计模具的结构,包括上模、下模、导柱、导套、滑块等零部件的形状、尺寸和位置,以确保模具在工作过程中能够有效地完成冲压操作。
4. 优化设计:通过模拟和分析,对模具的结构进行优化,以提高模具的工作效率、降低故障率,减少材料浪费等。
5. 编制模具设计图纸:根据设计要求,编制模具的设计图纸,包括零件图纸、装配图纸、工艺图等。
6. 制造和调试:根据模具设计图纸,制造模具的各个零部件,并进行装配和调试,以确保模具的正常运行。
7. 试产和调整:对初次制造出来的模具进行试产,根据试产情况进行调整,以满足垫圈冲压零件的质量要求和生产效率。
8. 模具维护:定期对模具进行检查和维护,保持模具的工作状态,延长模具的使用寿命。
总结:垫圈冲压模具设计的工作原理是在满足用户需求的基础上,根据工艺要求和工作原理,通过优化设计和调试等一系列工作,最终制造出能够高效稳定地完成冲压操作的模具。
压圈开口环冲压模具设计(含全套CAD图纸)
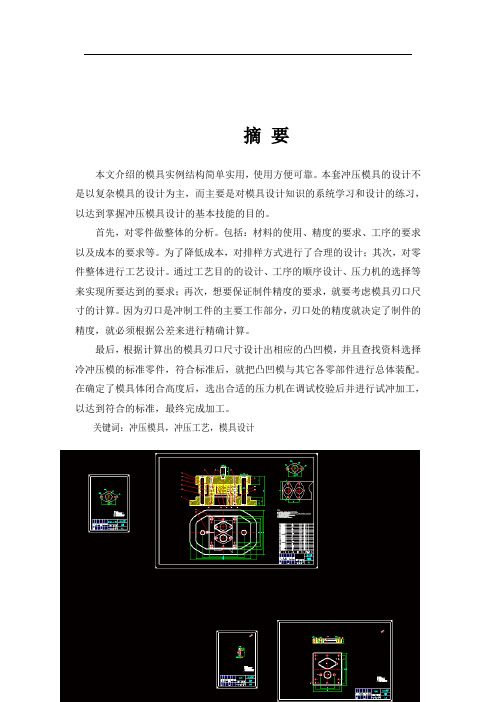
摘要本文介绍的模具实例结构简单实用,使用方便可靠。
本套冲压模具的设计不是以复杂模具的设计为主,而主要是对模具设计知识的系统学习和设计的练习,以达到掌握冲压模具设计的基本技能的目的。
首先,对零件做整体的分析。
包括:材料的使用、精度的要求、工序的要求以及成本的要求等。
为了降低成本,对排样方式进行了合理的设计;其次,对零件整体进行工艺设计。
通过工艺目的的设计、工序的顺序设计、压力机的选择等来实现所要达到的要求;再次,想要保证制件精度的要求,就要考虑模具刃口尺寸的计算。
因为刃口是冲制工件的主要工作部分,刃口处的精度就决定了制件的精度,就必须根据公差来进行精确计算。
最后,根据计算出的模具刃口尺寸设计出相应的凸凹模,并且查找资料选择冷冲压模的标准零件,符合标准后,就把凸凹模与其它各零部件进行总体装配。
在确定了模具体闭合高度后,选出合适的压力机在调试校验后并进行试冲加工,以达到符合的标准,最终完成加工。
关键词:冲压模具,冲压工艺,模具设计AbstractThe topic is the chain plate punching blanking compound mold design and the mold of article described an instance is simple and practical, easy to use and is reliable. This mold is not primarily designed to complex design, but mainly on a systematic study of mold design knowledge and practice, in order to achieve the purpose of master the basic skills of stamping mold design.First of all, do a thorough analysis for the parts, which include the using of the material, the requirement of accuracy and the requirement of working procedure and costs and so on. For declining low cost, proceeded the reasonable design to the row kind method. Secondly, do processing design for the whole parts and the purpose by craft designing and order of the working procedure and by the choice of punching machine. Thirdly, consider the calculation of size of the mould cutting edge in order to meet the need of accuracy. Because the cutting edge is the main working part of the punching processing, the accurate cutting edge guarantees the accurate parts. So you needed to tolerance do accurate calculation.Finally, according to the calculated the size of mold cutting edge design the corresponding punch and mold, and find information on selection criteria for cold stamping parts, meet the standards, put the punch and mold with the other components to the overall assembly. In determining the specific mold closed height, select the appropriate press in the debug and test validation washed after processing, to meet compliance standards, the final completion of the processing chain plate.Keywords:composite modulus, stamping process, mold design , punching blanking目录摘要 (1)Abstract (2)目录 (3)第1章绪论 (5)1.1 我国模具技术的现状及发展趋势 (5)1.2 冲压模的现状与发展趋势 (6)1.3 外国模具工业的发展状况 (7)1.4 课题研究的内容 (8)第2章工艺性分析 (9)2.1 零件的分析 (9)2.1.1 冲压件的尺寸精度 (9)2.1.2 生产批量 (9)2.2 工艺方案分析 (10)2.3 模具间隙的确定 (11)2.4 设备的选择 (12)第3章排样设计 (15)3.1 搭边 (17)3.2 送料进距 (17)3.3 条料宽度 (17)3.4 本章小结 (18)第4章模具总体设计 (19)4.1 模具类型的选择 (19)4.2 定位方式的选择 (19)4.3 卸料﹑出件方式的选择 (20)第5章模具的装配和冲裁模具的试冲 (21)5.1 模具的装配 (21)5.2 冲裁模具的试冲 (22)5.3 装配图 (25)结论与展望 (26)致谢 (27)参考文献 (28)全套图纸加36296518第1章绪论1.1 我国模具技术的现状及发展趋势我国模具工业近年来发展很快。
压圈冲裁模设计

压圈冲裁模设计QQ: 8158623471.1 模具市场发展趋势模具,是工业生产的基础工艺装备,在电子、汽车、电机、电器、仪表、家电和通讯等产品中,60%—80%的零部件都依靠模具成形,模具质量的高低决定着产品质量的高低,因此,模具被称之为“百业之母”。
模具又是“效益放大器”,用模具生产的最终产品的价值,往往是模具自身价值的几十倍、上百倍。
模具生产的工艺水平及科技含量的高低,已成为衡量一个国家科技与产品制造水平的重要标志,它在很大程度上决定着产品的质量、效益、新产品的开发能力,决定着一个国家制造业的国际竞争力。
我国模具工业的技术水平近年来也取得了长足的进步。
大型、精密、复杂、高效和长寿命模具上了一个新台阶。
大型复杂冲模以汽车覆盖件模具为代表,已能生产部分新型轿车的覆盖件模具。
体现高水平制造技术的多工位级进模的覆盖面,已从电机、电器铁芯片模具,扩展到接插件、电子枪零件、空调器散热片等家电零件模具。
在大型塑料模具方面,已能生产48英寸电视的塑壳模具、6.5K g 大容量洗衣机全套塑料模具,以及汽车保险杠、整体仪表板等模具。
在精密塑料模具方面,已能生产照相机塑料模具、多型腔小模数齿轮模具及塑封模具等。
在大型精密复杂压铸模方面,国内已能生产自动扶梯整体踏板压铸模及汽车后桥齿轮箱压铸模。
其他类型的模具,例如子午线轮胎活络模具、铝合金和塑料门窗异型材挤出模等,也都达到了较高的水平,并可替代进口模具。
根据国内和国际模具市场的发展状况,有关专家预测,未来我国的模具经过行业结构调整后,将呈现十大发展趋势:一是模具日趋大型化;二是模具的精度将越来越高;三是多功能复合模具将进一步发展;四是热流道模具在塑料模具中的比重将逐渐提高;五是气辅模具及适应高压注射成型等工艺的模具将有较大发展;六是模具标准化和模具标准件的应用将日渐广泛;七是快速经济模具的前景十分广阔;八是压铸模的比例将不断提高,同时对压铸模的寿命和复杂程度也将提出越来越高的要求;九是塑料模具的比例将不断增大;十是模具技术含量将不断提高,中高档模具比例将不断增大,这也是产品结构调整所导致的模具市场未来走势的变化1.2 冲压模具的现状和技术发展一、现状改革开放以来,随着国民经济的高速发展,市场对模具的需求量不断增长。
支撑圈冲压模具设计
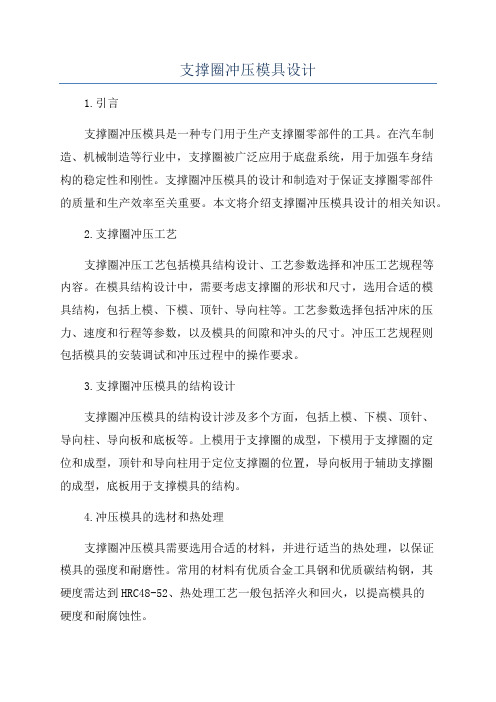
支撑圈冲压模具设计1.引言支撑圈冲压模具是一种专门用于生产支撑圈零部件的工具。
在汽车制造、机械制造等行业中,支撑圈被广泛应用于底盘系统,用于加强车身结构的稳定性和刚性。
支撑圈冲压模具的设计和制造对于保证支撑圈零部件的质量和生产效率至关重要。
本文将介绍支撑圈冲压模具设计的相关知识。
2.支撑圈冲压工艺支撑圈冲压工艺包括模具结构设计、工艺参数选择和冲压工艺规程等内容。
在模具结构设计中,需要考虑支撑圈的形状和尺寸,选用合适的模具结构,包括上模、下模、顶针、导向柱等。
工艺参数选择包括冲床的压力、速度和行程等参数,以及模具的间隙和冲头的尺寸。
冲压工艺规程则包括模具的安装调试和冲压过程中的操作要求。
3.支撑圈冲压模具的结构设计支撑圈冲压模具的结构设计涉及多个方面,包括上模、下模、顶针、导向柱、导向板和底板等。
上模用于支撑圈的成型,下模用于支撑圈的定位和成型,顶针和导向柱用于定位支撑圈的位置,导向板用于辅助支撑圈的成型,底板用于支撑模具的结构。
4.冲压模具的选材和热处理支撑圈冲压模具需要选用合适的材料,并进行适当的热处理,以保证模具的强度和耐磨性。
常用的材料有优质合金工具钢和优质碳结构钢,其硬度需达到HRC48-52、热处理工艺一般包括淬火和回火,以提高模具的硬度和耐腐蚀性。
5.模具的加工和装配支撑圈冲压模具的加工主要包括车削、铣削、磨削和电火花加工等工艺。
加工过程中需要保证模具的尺寸和形状的精度,以及模具表面的光洁度。
模具的装配包括上模、下模、顶针、导向柱和导向板等零部件的装配,以及模具的调试和检验。
6.冲压模具的使用与维护支撑圈冲压模具的使用应按照工艺规程进行,要注意模具的安装和调试,以及冲压过程中的操作规范。
模具的维护包括定期检查、清洁、润滑和更换磨损部件等。
同时,对模具的储存和保养也十分重要,以延长模具的使用寿命。
7.总结支撑圈冲压模具设计是保证支撑圈零部件质量和生产效率的关键环节。
设计者需要综合考虑支撑圈的形状和尺寸,选用合适的材料和热处理工艺,进行精确的加工和装配,以及进行科学的使用和维护。
垫圈冲压模具设计
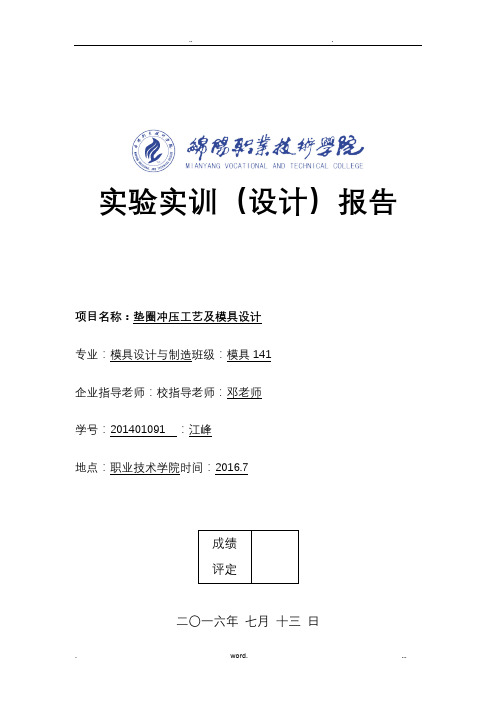
实验实训(设计)报告项目名称:垫圈冲压工艺及模具设计专业:模具设计与制造班级:模具141企业指导老师:校指导老师:邓老师学号:201401091 :江峰地点:职业技术学院时间:2016.7成绩评定二〇一六年七月十三日职业技术学院实验实训(设计)进度检查及成绩评定表摘要本次的课程设计是一个简单的防滑垫圈及其复合模设计,此副模具是采用落料—冲孔两道工序相结合的复合模,本人经查阅相关书籍、资料以及对设计此副模具所要用到的相关公式、数据作出了一个准确的依据。
本次课程设计一共分为两部分,和其他模具的设计一样,第一部是对零件进行工艺分析,接着对工艺方案进行比较,最终确定选用复合模加工制件的工艺方案。
然后画工序图、排样图以及对材料利用率的计算,计算冲压力,选择冲压机。
然后填写冲压工艺规程卡。
第二部分是冲压模具的设计,选择冲模类型以及结构形式,定位方式,卸料方式,模具设计计算(主要计算各类主要零件的外形尺寸),最后确定凸凹模工作部分尺寸。
前言在现代工业生产中,模具是重要的工艺装备之一,它在铸造、锻造、冲压橡胶等生产行业中得到了广泛应用。
由于采用模具进行生产能够提高生产效率,节约原材料,降低成本,并可保证一定的加工质量要求。
所以,汽车、飞机、拖拉机、电器、仪表、玩具等的零部件很多采用模具来加工。
随着科学技术的发展,产品的更新换代加快,对产品质量外观不断提出新要求,对模具质量要求也越来越高。
模具的设计、制造工业部门肩负着为相关企业和部门提供产品的重任。
如果模具设计及制造水平落后,产品质量低劣,制造周期长,必将影响产品的更新换代,使产品失去竞争能力,阻碍生产和经济的发展。
因此,模具设计及制造技术在国民经济中的地位是显而易见的。
金属板料冲压是模具在工业生产中应用广泛的加工形式之一,随着市场竞争日趋加剧,产品质量不断提高,对生产的安全性,操作的方便性等要求也日益提高。
模具作为冲压生产的基本要素,其设计制造技术受到普遍重视。
压圈冲压模具设计说明书

江门职业技术学院毕业设计--压圈冲压模具设计说明书2011届专业学号学生姓名指导教师完成日期 2014年12月24日目录绪论 (4)第1章冲压工艺概述 (4)1.1.1冲压工艺的简介 (4)1.1.2冲压模具的发展 (5)1.2 工艺方案的确定 (6)1.2.1 锡青铜QSn4-4-2.5的性能 (6)1.2.2 方案确定 (6)1.2.3有关设计 (7)第2章复合冲压模具设计与计算 (7)2.1 冲裁件的工艺设计 (7)2.1.1冲裁件的工艺性分析 (7)2.1.2 确定工艺方案及模具形式 (7)2.2凹凸模间隙的选择 (7)2.2.1冲裁间隙的分类 (8)2.2.2 冲裁间隙对冲裁件的影响 (8)2.2.3 间隙对尺寸精度的影响 (8)2.2.4 间隙对冲裁力的影响 (8)2.2.5 间隙对模具寿命的影响 (9)2.2.6 确定合理间隙的理论依据 (9)2.2.7合理间隙的选择 (9)2.3凹凸模制造方法及刃口尺寸的计算 (10)2.3.1 凹凸模的制造方法 (10)2.3.2凹凸模刃口尺寸的计算 (10)2.4排样 (12)2.4.1排样的意义 (12)2.4.2排样的方法 (12)2.4.3搭边、进距计算 (13)2.5冲裁力的计算及选择压力机 (15)2.5.1冲裁力的计算 (15)2.5.2选择压力机 (19)2.6冲裁模主要零件的设计 (20)2.6.1凹模设计 (20)2.6.2 凹凸模设计 (22)2.6.3冲孔凸模的设计 (22)2.6.4定位零件的确定 (23)2.6.5卸料与推料装置 (23)2.6.6模座、导向零件 (24)2.6.7连接与固定零件 (24)致谢 (25)绪论冲压成形作为现代工业中一种十分重要的加工方法,用以生产各种板料零件,具有很多独特的优势,其成形件具有自重轻、刚度大、强度高、互换性好、成本低、生产过程便于实现机械自动化及生产效率高等优点,是一种其它加工方法所不能相比和不可替代的先进制造技术,在制造业中具有很强的竞争力,被广泛应用于汽车、能源、机械、信息、航空航天、国防工业和日常生活的生产之中。
- 1、下载文档前请自行甄别文档内容的完整性,平台不提供额外的编辑、内容补充、找答案等附加服务。
- 2、"仅部分预览"的文档,不可在线预览部分如存在完整性等问题,可反馈申请退款(可完整预览的文档不适用该条件!)。
- 3、如文档侵犯您的权益,请联系客服反馈,我们会尽快为您处理(人工客服工作时间:9:00-18:30)。
压圈冲压模具设计 Company number:【0089WT-8898YT-W8CCB-BUUT-202108】压圈复合模具设计目录(一).冲压件的工艺性分析 (4)(二).确定工艺方案模具机构形式 (4)(三).模具设计计算 (5)(1)排样方式的确定及其计算( 2) 计算凸.凹模刃口尺寸(3)外形落料凸、凹模刃口尺寸的计算(4)冲压力的计算(5)压力中心的计算(四).模具总体设计 (8)(五).模具主要零部件的结构设计 (9)(1)落料凸、凹模的结构设计(2)弹性元件的设计计算(3)模架的设计(六).冲压设备的选择 (12)(七).绘制模具总装图 (13)(八).拆画零件图 (13)(九).参考文献 (14)序言加入WTO后,我国经济将从真正意义上溶入全球经济一体化,中国的市场将不再只属于中国企业。
产品,不仅仅是性能与价格的较量,从外观、实用性到环保,哪一点输给别人那只能堆放在仓库或贱卖,不会创造效益的企业只好关门。
手抄书式的靠机床和操作工来实现工程师设计产品化的老机械制造已成为历史,现代制造业驾驭着微电子和新材料,敲击着键盘,在加工中心与模具组成的流水线上精密的复制着工程师在计算机辅助下设计的从市场捕捉来的最新产品。
进入21世纪,先进制造技术将全面担负起快速、精确的生产更多门类的产品,以保障和提高人类现代化生活的质量。
模具已不仅仅是人类用来浇铸钱币和内燃机壳的砂箱。
今天,它凝聚了各类高技术,能快速精密的直接把材料成型、焊接、装配成零部件、组件或产品,其效率、精度、流线、超微型化、节能、环保,以及产品的性能、外观等,都是传统工艺所无与伦比的。
展望21世纪,无论电子、生物、材料、汽车、家电等哪个行业,不装备由计算机、模具和加工中心砌成的生产线,都不可能在制造业中担纲支柱产业。
模具是现代制造技术的重要装备,其水平标志着一个国家或企业的制造水平和生产能力。
今后一段时期内,我国五大支柱产业的产品质量、批量化成本和包括产业更新在内的技术进步的关键是模具。
现在全球模具总产值早已超过传统机械工业机床与工具类产值的总和。
该零件在汽车,机械,家电,飞机,火车等方面都有广泛的应用。
该零件在生活中到处都可以看到,它具有使两个零件连在一起从而减少之间的磨损。
到处都可以买到,价格便宜,制造简单,方便等。
金属压圈复合模具设计【摘要】:本设计进行了落料、冲孔连续模的设计。
文中简要概述了冲压模具目前的发展状况和趋势。
对产品进行了详细工艺分析和工艺方案的确定。
按照冲压模具设计的一般步骤,计算并设计了本套模具上的主要零部件,如:凸模、凹模、凸模固定板、垫板、凹模固定板、卸料板、导尺、挡料销、导正销等。
模架采用标准模架,选用了合适的冲压设备。
设计中对工作零件和压力机规格均进行了必要的校核计算。
冲孔凹模和落料凹模则采用整体固定板固定。
落料凸模内装有导正销,保证了工件上孔和外形的相对位置准确,提高了加工精度。
如此设计出的结构可确保模具工作运行可靠和冲压产品大批量生产的要求。
关键词:冲压成型落料冲孔一.冲裁件工艺分析1、材料:Q235是普通的碳素钢。
2、工件结构形状:该零件形状简单、对称,是由圆弧和直线组成的。
3、尺寸精度:零件图上所有尺寸均未标注公差,属自由尺寸,可按IT14级确定工件尺寸的公差,经查公差表,各尺寸公差为:φφ20+ 22+ 4+结论:将以上精度与零件的精度要求相比较,该零件的精度要求能够在冲裁加工中得到保证,其他尺寸标注、生产批量等情况,也均符合冲裁的工艺要求,故决定采用冲压方式进行加工。
二.确定工艺方案及模具的结构形状该工件包括落料、冲孔两个基本工序,可有以下三种工艺方案。
方案一:先落料,后冲孔。
采用单工序模生产。
方案二:落料—冲孔复合冲压。
采用复合模生产。
方案三:冲孔—落料级进冲压。
采用级进模生产。
方案一模具结构简单,但需要两道工序两副模具,成本高而生产效率低,难以满足大批量生产要求。
方案二只需一副模具,工件的精度及生产效率都较高,在模具同一位置时可完成数道分离工序的模具,成本低、操作方便、工件精度也能满足要求。
方案三也只需一道模具,生产效率高,但不在同一个位置就可以完成,操作不方便,精度要求不能满足,成本高。
因此从零件加工精度和经济性角度综合考虑,选则方案二是较为合适的,即选择复合模作为本设计的模具方案。
三. 模具设计计算(1)排样方式的确定及其计算设计复合模时,首先要设计条料的排样图,因该零件外形为圆形,可采用有废料排样的直排比较合适,确定其排样方式为直排画出排样图。
最小工艺搭边值a =,a 1=,分别取a =2,a 1=2条料宽度: B =(D+2a )-△B =(42+2*2)-0B = 46mm步距:S =42+2=44mm材料利用率的计算:计算冲压件毛坯的面积:A=π×R 2 =π×212 = 2一个步距的材料利用率:η=%100 BSnA =46×44=﹪ (2)计算总冲压力F 落 = Lt τb =(2πR ×2×450)N=F 冲 = Lt τb =(×10π/180+4+2×)×2 ×450=F 推=n K 推F 孔查表,得 h=6mm 则n=h/t=6mm/2=3K 推=所以,有 F 推=n K 推F 孔=3××=又 F 卸=K 卸F 落查表,得 K 卸=所以,有F 卸=K 卸F 落=×=总冲压力为:F 总=F 落+F 孔+F 推+F 卸=(+++)KN=为了保证冲压力足够,一般冲裁时压力机吨位应比计算的冲F 总′=×F 总=×=(3)压力中心的计算由图可知工件上下对称,将工件冲裁周边分成L 1、L 2、L 3、L 4、L 5基本线段,求出各段长度的重心位置:因工件相对x 轴对称,所以Y c =0, 只需计算X C.L 1=2πr=㎜ X 1=0L 2= X 2=L 3=L 5= X 3=X 5=㎜L 4=4mm X 4=12㎜将以上数据代入压力中心坐标公式X=(L 1 X 1 +L 2 X 2+…+ L 5 X 5 )/ L 1+ L 2+…+ L 5X=[×0+×+×+4×12+×]/+++4+=(4)凹凸模刃口尺寸的计算1)冲孔凹凸模刃口尺寸的计算查表,得间隙值Z min =0.246mm ,Z max =0.360mm 。
由于制件结构简单,精度要求不高,所以采用凹模和凸模分开加工方法制作凸、凹模。
其凸、凹模刃口尺寸计算如下:查表,得φ20mm 凸、凹模制造公差:δ凸 =0.020mm δ凹 =0.025mm校核: Z max -Z min =()㎜=而δ凸+δ凹 =(+)㎜=0.045mm满足 Z max -Z min ≥δ凸+δ凹的条件查表,得:IT14级时标准公差△=㎜,因为>,所以磨损系数X=。
按式() d 凸=[]X∆+min d =(20+×)=0020.026.20-mmD 凹=[]min Z d +凸=025.00246.026.20++)(=025.00506.20+mm 查表,得×4mm 的矩形凸、凹模制造公差:δ凸 =0.020mm δ凹 =0.020mmδ凸+δ凹 =+=满足 Z max -Z min ≥δ凸+δ凹的条件2)外形落料凸、凹模刃口尺寸的计算由于外形形状简单,精度要求不高,所以采用凸模和凹模分开加工的方法制作凸、凹模。
查表,得凸、凹模制作公差δ凸=0.020mm δ凹 =0.030mm校核:Z max -Z min =而δT +δA =满足 Z max -Z min ≥δ凸+δ凹的条件查表,得:IT14级时磨损系数X=,d 凸=[]X∆+min d = d 凹=[]min Z d +凸=+ 四. 模具的总体设计根据上述分析,本零件的冲压包括冲压和落料两个工序,且孔边距较大,可采用倒装复合模,可直接利用压力机的打杆装置进行推件,卸料可靠,便于操作。
工件留在落料凹模空洞中,应在凹模孔设置推件块,卡于凸凹模上的废料可由卸料板推出;而冲孔废料则可以在下模座中开设通槽,使废料从空洞中落下。
由于在该模具中压料是由落料凸模与卸料板一起配合工作来实现的,所以卸料板还应有压料的作用,应选用弹性卸料板卸下条料。
因是大批量生产,采用手动送料方式,从前往后送料。
因该零件采用的是倒装复合模,所以直接用挡料销和导料销即可。
为确保零件的质量及稳定性,选用导柱、导套导向。
由于该零件导向尺寸较小,且精度要求不是太高,所以宜采用后侧导柱模架。
五. 模具主要零部件的结构设计(1)凸模、凹模、凸凹模的结构设计,包括一下几个方面:①落料凸、凹模的结构设计在落料凹模内部,由于要放置推件块,所以凹模刃口应采用直筒形刃口,并查《冲压工艺与模具设计》书中表,取得刃口高度h=6mm,该凹模的结构简单,宜采用整体式。
查《冲压工艺与模具设计》书中表,得k=即凹模高度H=ks=×42mm=凹模壁厚C==×=凹模外形尺寸的确定:凹模外形长度:L=(42+×2)㎜=㎜凹模外形宽度:B=(42+×2)㎜=㎜凹模整体尺寸标准化,取为100mm×100mm×16mm凹模的工艺路线为了增加凸模的强度与刚度,凸模固定板厚度取24mm,因凸模比较长,所以选用带肩的台阶式凸模,凸模长度根据结构上需要来确定。
L= h凸模固定板+h落料凹模=(24+)mm= (取40mm)③凸凹模的结构设计本模具为复合冲裁模,除了冲孔凸模和落料凹模外还有一个凸凹模。
根据整体模具的结构设计需要,凸凹模的结构简图如下图所示:确定凸凹模安排在模架上的位置时,要依据计算的压力中心的数据,使压力中心与模柄中心重合。
校核凸凹模的强度:查《冲压工艺与模具设计》书中表得凸凹模的最小壁厚为,而实际最小壁厚为9mm。
故符合强度要求。
凸凹模的刃口尺寸按落料凹模尺寸配制,并保证双间隙为~.定位方式定位方式采用侧刃加导正销定距的方式。
用侧刃定距时,使侧刃的实际长度和凹模型孔间步距一致,可提高送料精度。
但采用侧刃定距时,送料操作时的人为因素,会产生送料精度不稳定的现象。
对于工位较多的级进模,送料的累积误差,会使送料精度降低,对尺寸精度要求高、形状复杂的冲件尤为明显,因此,在侧刃定距的同时增设导正销的方式,在多工位级进模中得到广泛的应用。
侧刃导正销的定距方式是将侧刃做粗定位,导正销做精定位。
用于导正的导正孔,可以是冲件上的孔,也可在条料上冲出辅助工艺孔。
为保证送料精度,一般应设置两个导正孔,并在第一工位上冲出。
1、侧刃和导正销定距方式时,侧刃、侧刃当块、侧导板和导正销的装配与调整方法,与单独装侧刃、导料销基本相同。