冲压模具设计
冲压模具设计全套步骤和流程

冲压模具设计全套步骤和流程1.零件设计:根据产品的功能要求和外观要求,进行零件的设计。
确定零件的几何形状、尺寸和所需的表面质量等。
2.材料选择:根据零件的要求和产品的使用环境,选择合适的材料。
考虑材料的强度、塑性和可加工性等因素。
3.模具结构设计:根据零件的几何形状和加工要求,设计模具的结构。
包括模具的底座、上模、下模、模具导向装置、顶针等部分。
4.模具零件设计:根据模具结构设计的要求,对模具的各个零部件进行设计。
包括模具的滑块、顶出装置、顶出销等。
5.模具总成设计:将各个模具零件组装成一个整体。
进行模具总成的设计,确定各个模具零件的安装位置、尺寸等。
6.模具加工工艺设计:根据模具结构和零件的加工要求,设计模具的加工工艺。
包括模具的加工工艺路线、加工顺序、机床设备等。
7.模具调试和试产:根据模具的设计和加工工艺,进行模具的组装和调试。
包括模具的调试、调整、测试以及初次试产。
根据试产结果,对模具进行优化和改进。
8.模具使用和维护:对模具进行使用和维护。
包括模具的防护、清洁、润滑和定期维护等。
9.模具性能评价:对模具进行性能评价。
包括模具的使用寿命、生产效率、加工精度等方面的评价。
10.模具改进和更新:根据使用中的问题和需求,对模具进行改进和更新。
包括模具的结构改进、材料选择和加工工艺的优化等。
以上是冲压模具设计的全套步骤和流程。
在进行设计的过程中,需要考虑零件的功能要求、材料的选择、模具的结构设计、加工工艺的确定等因素。
通过设计和优化,能够获得满足产品要求的冲压模具,提高生产效率和产品质量。
冲压模具课程设计说明书 2
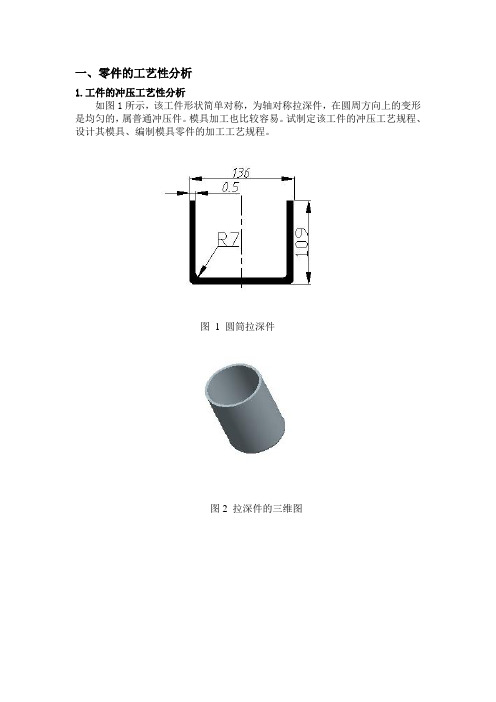
一、零件的工艺性分析1.工件的冲压工艺性分析如图1所示,该工件形状简单对称,为轴对称拉深件,在圆周方向上的变形是均匀的,属普通冲压件。
模具加工也比较容易。
试制定该工件的冲压工艺规程、设计其模具、编制模具零件的加工工艺规程。
图1 圆筒拉深件图2 拉深件的三维图2.工件材料化学成分和机械性能分析(1)材料分析工件的材料为08钢,属于优质碳素结构钢,优质沸腾钢,强度、硬度低,冷变形塑性很好,可深冲压加工,焊接性好。
成分偏析倾向大,时效敏感性大,故冷加工时应采用消除应力热处理或水韧处理,防止冷加工断裂。
08钢的主要机械性能如下:σ(兆帕) 280-390抗拉强度bσ(兆帕) 180屈服强度s抗剪强度(兆帕) 220-310延伸率δ 32%(2)结构分析工件为一窄凸缘筒形件,结构简单,圆角半径为r=7,厚度为t=0.5mm,满足筒形拉深件底部圆角半径大于一倍料厚的要求,因此,零件具有良好的结构工艺性。
(3)精度分析工件上尺寸均为未注公差尺寸,普通拉深即可达到零件的精度要求。
经上述分析,产品的材料性能符合冷冲压加工要求。
在零件工艺性分析的基础上制定其工艺路线如下:零件的生产包括落料、拉深(需计算确定拉深次数)、修边(采用机械加工)等工序,为了提高生产效率,可以考虑工序的复合,经比较决定采用落料与第一次拉深复合。
二、工件的拉深工艺分析及计算1.毛坯尺寸计算(1)计算原则相似原则:拉深前坯料的形状与拉深件断面形状相似;等面积原则:拉深前坯料面积与拉深件面积相等。
(2)计算方法由以上原则可知,旋转体拉深件采用圆形毛坯,其直径按面积相等的原则计算。
计算坯料尺寸时,先将拉深件划分为若干便于计算的简单几何体,分别求出其面积后相加,得拉深件总面积A。
图3 拉深件的坯料计算如图3所示,筒形件坯料尺寸,将圆筒件分成三个部分,每个部分面积分别为:(3)确定零件修边余量由于板料的各向异性和模具间隙不均等因素的影响,拉深后零件的边缘不整齐,甚至出现耳子,需在拉伸后进行修边。
冲压模具设计方法与步骤

冲压模具设计方法与步骤冲压模具是制造行业中常用的一种模具,用于在金属板材上进行冲裁、压制、成形等工艺。
冲压模具的设计是冲压工艺的关键环节之一,合理的设计可以提高产品质量和生产效率。
以下是冲压模具设计的方法与步骤。
一、冲压模具设计方法1.分析产品要求:首先需要仔细分析产品要求,了解产品的形状、尺寸、材质等要求,以及要求的生产效率和成本等因素。
2.选择合适的材料:根据产品的要求选择合适的模具材料,常用的材料有合金工具钢、合金冷作工具钢等。
3.制定冲压工艺:根据产品要求,制定冲压工艺,包括冲剪顺序、成形方式、冲压力、冲头形状等因素。
4.设计模具结构:根据产品要求和冲压工艺,设计模具的结构,包括上模、下模、导向机构等部分。
5.进行模具布局:进行模具布局,合理安排模具零件的形状、位置和尺寸,以确保模具的强度和稳定性。
6.进行模具零件设计:根据模具布局,设计模具的零件,包括冲头、导柱、导套、导向板等部分。
7.进行模具装配:根据模具设计,进行模具的装配,确保各个零件之间的配合和精度。
8.进行模具调试:进行模具调试,调整模具的尺寸和位置,确保模具在冲压过程中的稳定性和精度。
9.进行模具试产:进行模具试产,对模具进行试模和试产,检验产品的质量和模具的性能。
10.进行模具改进:根据试产结果,对模具进行改进和优化,提高模具的性能和生产效率。
二、冲压模具设计步骤1.初步设计:根据产品要求,进行初步的模具设计,包括模具结构和布局。
2.详细设计:对初步设计的模具进行详细设计,包括各个零件的形状、尺寸和材料等。
3.模具制造:根据详细设计,进行模具的制造,包括加工模具零部件和进行模具装配。
4.模具调试:对制造完成的模具进行调试,调整模具的尺寸和位置,确保模具的性能和精度。
5.模具试产:进行模具的试模和试产,检验产品的质量和冲压工艺的可行性。
6.模具改进:根据试产结果,对模具进行改进和优化,提高模具的性能和生产效率。
7.模具验收:对改进后的模具进行验收,确保模具达到产品要求和生产效果。
冲压模具设计

冲压模具设计一、冲压模具设计的步骤1.确定需求:首先要明确冲压件的形状、尺寸和质量要求,以及加工工艺的要求,包括材料选材、工艺流程等。
2.分析冲压过程:了解冲压过程中的受力情况,确定冲压件的受力情况,考虑冲压件的结构和形状。
分析完成后,可以确定模具的结构和工作原理。
3.制定设计方案:设计方案是根据需求和分析决策,形成的模具设计的主要思路,包括模具的结构形式、材料选材、零件加工工艺等。
4.细化设计:在设计方案的基础上,进一步细化设计,包括每个零件的尺寸、形状和工艺要求,确保每个零件都符合设计要求。
5.制作样品:制作模具样品,进行试验和调试,验证设计方案的可行性,确定调整和改进方案。
6.定稿设计:根据试验结果,对设计方案进行调整和优化,形成最终的设计方案。
二、冲压模具设计的关键要点1.良好的受力结构:冲压模具在工作过程中要经受巨大的冲击力和挤压力,因此必须具备良好的受力结构,包括合理的分布受力、合理的受力传递和合理的受力集中。
2.优秀的耐磨材料:冲压模具的工作环境往往十分恶劣,耐磨材料可以大大延长模具的使用寿命,提高生产效率。
3.精密的加工工艺:冲压模具的加工精度直接影响到冲压件的质量,因此必须采用精密的加工工艺,确保模具的精密度和可靠性。
4.优化的结构设计:冲压模具的结构设计要尽可能简单,降低成本,提高生产效率。
同时也要考虑模具的易维护性,方便维修和更换零件。
5.可靠的试验与调试:为了保证冲压模具的质量和可靠性,必须进行全面的试验和调试,包括模具的运行测试、冲压件的检测评价等。
三、结语冲压模具设计是一个复杂而细致的工程,需要综合运用材料学、结构设计、机械加工、模具试验等多方面的知识。
只有具备扎实的理论基础和丰富的实践经验,才能设计出高质量的冲压模具。
希望以上内容对冲压模具设计有所帮助,能够指导相关行业的人士更好地进行冲压模具设计工作。
冲压模具设计是一个复杂的过程,需要设计人员深入且全面地了解冲压工艺、材料特性、机械结构、模具加工工艺等多方面知识,并且需要经验丰富的工程师进行设计。
冲压模具设计的主要内容及步骤

冲压模具设计的主要内容及步骤冲压模具设计是指根据产品的形状、尺寸和工艺要求,设计出适合于冲压成型的模具。
它是冲压工艺的关键环节之一,对于冲压成品的质量、生产效率和成本等方面具有重要影响。
下面将从主要内容和步骤两个方面来详细介绍冲压模具的设计过程。
一、主要内容1.产品分析:了解产品的形状、尺寸、材料以及加工工艺要求等,包括产品的外观和内部结构等方面。
根据产品的特点来确定模具的种类和结构。
2.材料选择:根据冲压工艺要求和模具的使用条件,选择合适的模具材料,包括工作模具和凸模、活塞等配件的材料选择。
3.结构设计:确定模具的分型方式和结构形式,包括模具的基本结构、操作方式、传动方式、冷却系统和脱模系统等。
还需要考虑模具的可拆卸性、装配性以及模具的厚度和尺寸等。
4.零件设计:根据产品的形状和尺寸,设计出模具的主要零件,包括模具座、滑块、压料板、导向套等。
需要考虑模具的刚度和强度等。
5.工艺设计:根据冲压工艺要求,确定模具的工作步骤和工艺参数,包括下料、冲孔、冲凸、整形等工序,并合理安排模具的工作顺序和加工工艺。
6.零件布局:根据结构设计和工艺要求,将各个零件合理布局,包括确定零件之间的相对位置和相互之间的配合关系等。
7.工装设计:根据冲压工艺要求,设计出合适的工装夹具和模板,用于固定和定位工件,保证冲压过程中的精度和稳定性。
二、主要步骤1.产品分析及材料选择:仔细分析产品的形状、尺寸和工艺要求,根据产品的材料选择合适的模具材料。
2.结构设计:根据产品的特点和生产要求,确定模具的结构形式和基本结构,包括模具的分型方式、操作方式、冷却系统和脱模系统等。
3.零件设计:根据产品的形状和尺寸,设计出模具的主要零件,包括模具座、滑块、压料板、导向套等。
4.工艺设计:根据冲压工艺要求,确定模具的工作步骤和工艺参数,合理安排模具的工作顺序和加工工艺。
5.零件布局:将各个零件合理布局,确定零件之间的相对位置和相互之间的配合关系。
冲压模具设计

冲压模具设计1. 引言冲压模具是指用于进行金属冲压工艺的模具,用于在金属工件上施加力量以将其形状改变。
冲压模具设计在制造业中扮演着重要的角色,它直接影响到产品的质量和生产效率。
本文将介绍冲压模具设计的基本概念、设计过程和一些常用的设计原则。
2. 冲压模具设计的基本概念2.1 冲压工艺冲压工艺是指将薄板金属材料经过剪切、冲孔、弯曲等工艺加工,以获得所需形状和尺寸的工件。
冲压工艺具有高效、精确和重复性好等特点,广泛应用于汽车制造、电子设备和机械制造等行业。
2.2 冲压模具冲压模具是用于进行冲压工艺的工具,通常由上模、下模和导向装置等部件组成。
上模和下模通过导向装置进行定位,形成模腔,金属材料在模腔中受力产生变形,从而得到所需形状的工件。
3. 冲压模具设计的过程冲压模具设计通常包括以下几个步骤:3.1 零件分析在进行冲压模具设计之前,需要对待加工的零件进行分析。
分析包括对零件的形状、材料和尺寸等方面进行研究,以确定合适的冲压工艺和模具结构。
3.2 模具结构设计根据零件的形状和要求,设计冲压模具的结构。
模具结构设计包括上模、下模、导向装置、顶出装置等部分的设计,以保证模具具有足够的刚度和稳定性。
3.3 模具零部件设计根据模具结构设计的结果,对各个零部件进行详细设计。
包括绘制各个零部件的草图、确定材料和尺寸,以及进行结构优化和强度计算等工作。
3.4 工艺路线设计根据零件的要求和工艺特点,设计出适合的工艺路线。
包括冲孔位置和尺寸、切削方式、顶出顺序等方面的确定。
3.5 模具制造和试模根据模具设计的结果,进行模具制造和试模工作。
包括制造各个零部件、装配模具、进行调试和试模等过程。
通过试模,检验模具的设计和制造是否符合要求,提出改进和优化的意见。
4. 冲压模具设计的常用原则4.1 简化结构冲压模具的结构尽量简化,以减少制造成本和提高生产效率。
避免使用复杂的零部件和工艺过程,尽量采用标准件或通用部件,方便制造和维护。
冲压工艺及模具设计
冲压工艺及模具设计冲压工艺及模具设计是现代工业制造中常用的一种技术,它通过将金属板材或者其他形状的金属件置于模具中,然后通过冲压机的动作使得金属材料发生塑性变形以得到所需的形状和尺寸。
冲压工艺及模具设计是一门综合性强的工艺技术,以下将介绍其包括冲压工艺流程、模具设计原则、模具结构设计、模具构件选用等相关内容。
一、冲压工艺流程冲压工艺分为单道冲压和多道冲压两种。
单道冲压是指在一个冲压过程中完成产品的全体造型,多道冲压是指通过多次冲压工艺来完成产品的全体造型。
下面将以多道冲压为例介绍冲压工艺流程。
1.材料准备:选择合适的板材材料,进行剪切、铺料等准备工作。
2.模具设计:根据产品的形状和尺寸要求,设计合适的冲压模具。
3.上料:将材料板厚按照模具规格要求剪切成对应尺寸,然后放置在模具上。
4.开模:通过冲压机的动作,使得模具上的凸模与凹模对压,使材料发生塑性变形。
5.去杂及模具保养:在冲压过程中会产生一些杂质,需要及时清理,并对模具进行保养和维护。
二、模具设计原则模具设计是冲压工艺的核心环节,它直接影响着产品的质量和成本。
在进行模具设计时,需要遵循以下原则:1.合理性原则:模具结构要合理,能够满足产品的形状和尺寸要求,并且易于加工和调整。
2.稳定性原则:模具要具有足够的刚性和稳定性,能够承受冲压机的冲击力和振动。
3.高效原则:模具设计要考虑工作效率,设计出能够实现快速冲压的模具结构。
4.经济原则:模具的设计和制造成本要较低,以降低产品的制造成本。
三、模具结构设计模具的结构设计是模具设计的重要环节,它包括模具的整体结构、分段结构、导向结构等。
下面将介绍常用的模具结构设计方法:1.整体结构设计:将模具设计为一个整体结构,具有较好的刚性和稳定性。
2.分段结构设计:根据产品的形状和尺寸要求,将模具分为多个部分,通过连接件进行连接。
3.导向结构设计:模具需要具有良好的导向性,避免材料在冲压过程中发生歪斜和偏移。
4.其他辅助结构设计:模具还需要考虑各种辅助结构,如剪断边缘结构、定位结构、脱模结构等。
冲压模具设计的一般流程
冲压模具设计的一般流程
1.审查产品图纸:首先需要仔细审查产品的工程图纸,了解产品的各
个尺寸要求、工艺要求以及其他相关要求。
2.确定冲压工艺:根据产品的要求,确定适合的冲压工艺,选择冲压
机械设备,确定最佳的冲压工艺参数。
3.设计模具结构:根据产品的工程图纸和冲压工艺要求,设计模具的
结构。
包括上模、下模、保护板、导向机构和顶针等。
4.确定模具尺寸:根据产品的尺寸要求,确定模具的尺寸。
包括上模、下模的尺寸以及模具的总高度。
5.设计冲裁件:在冲压模具中,通常需要设计一些冲裁件,用于切割
产品或者打孔等。
根据产品的要求,设计相应的冲裁件。
6.进行模具分解:将整个模具分解为若干个零部件,根据设计要求,
分布绘制模具的各个零件的图纸。
7.图纸绘制:根据模具的总装图和各个零件的图纸,进行详细的绘制
和标注。
确保各个零件的尺寸和位置准确无误。
8.模具加工:根据图纸,通过数控机床等设备进行各个零件的加工。
包括铣削、车削、磨削等工艺。
9.模具装配:将各个零件按照设计图纸的要求进行装配,完成整个冲
压模具的制作。
10.模具调试:完成模具制作后,进行模具的调试,确保模具能够正
常运行,满足产品的工艺要求。
11.产出产品:经过模具调试后,使用冲压机械设备进行批量生产,产出满足产品要求的冲压件。
12.模具维护和修理:冲压模具在使用过程中,需要进行定期的维护和修理,确保模具长时间稳定运行。
冲压模具毕业设计论文范文
冲压模具毕业设计论文范文冲压模具设计是冲压工艺中重要的一环,合理的模具设计能够提高产品质量、提高生产效率和降低生产成本。
本论文将以冲压模具设计为研究对象,探讨其设计理念和方法,以及在工程实践中的应用。
一、引言随着冲压工艺的广泛应用,冲压模具设计的重要性逐渐凸显。
良好的冲压模具设计能够提高产品的精度和质量,降低产品的成本和生产周期。
因此,冲压模具设计已成为冲压工艺中不可或缺的一部分。
二、冲压模具设计的理念1.综合运用先进技术冲压模具设计应充分利用先进的CAD/CAM/CAE技术,结合数字化模具设计和制造,提高设计效率和精度。
2.优化设计思路通过合理的设计思路,最大限度地降低模具的结构复杂度,减少零部件数量,提高模具的强度和刚度,降低模具重量和成本。
3.标准化设计冲压模具设计应遵循国家和行业的相关标准,确保设计的合理性和安全性。
同时,建立一套适合企业实际情况的标准化设计流程,提高设计的一致性和可操作性。
三、冲压模具设计的方法1.确定工艺参数根据产品的设计要求和冲压工艺的特点,确定冲床的类型和规格,进而确定模具的结构和尺寸。
2.分析产品特点对产品的结构和性能进行分析,确定产品的冲压工艺,包括冲床的振动频率、冲击力大小等参数。
3.设计冲床结构根据冲压工艺的要求和产品特点,设计冲床的结构,包括上模架、下模架、导向装置、传动装置、夹持系统等。
4.设计模具结构根据冲床结构的要求和产品特点,设计模具的结构,包括上模、下模、导向柱、顶针、滑块、模台等。
5.进行模具制造根据模具结构设计的要求,进行模具的加工和制造,包括CAD设计、数控加工、装配等环节。
四、冲压模具设计的工程实践冲压模具设计的工程实践主要包括以下几个方面:模具设计、模具制造、调试和生产。
1.模具设计根据产品的设计要求,进行冲床和模具的结构设计,确定模具的尺寸、材料和加工工艺。
2.模具制造根据设计要求,进行模具的制造和加工,包括材料准备、数控加工、装配和调试等环节。
冲压模具设计方法与步骤
冲压模具设计方法与步骤冲压模具设计是模具设计的一个重要方向,它是指将金属板材通过压力或冲击形成所需的产品形状的一种加工方法。
冲压模具设计方法的主要目标是提高生产效率、降低成本、增加产品质量和提高模具使用寿命。
下面将介绍冲压模具设计的主要步骤。
第一步:确定产品的设计要求在进行冲压模具设计之前,首先需要明确产品的设计要求,包括产品的几何形状、尺寸、材料、数量以及产品的使用环境等。
这些设计要求对模具的结构和功能有较大的影响,所以在设计之前必须充分了解这些要求。
第二步:确定冲压工艺根据产品的设计要求,需要确定适合的冲压工艺,包括冲压的方式(单冲、连冲、复合冲等)、工序的顺序以及冲压过程中需要采取的措施等。
冲压工艺的选择影响着模具的结构和功能,所以在设计之前需要仔细考虑。
第三步:进行产品设计在冲压模具设计中,需要首先进行产品的设计,包括产品的几何形状、尺寸、结构以及功能等方面。
产品的设计需要符合即将进行的冲压工艺的要求,同时还要考虑到产品的使用要求,确保产品的质量和使用寿命。
第四步:进行模具设计在进行冲压模具设计之前,需要对产品进行分析,确定冲压的工艺参数,包括冲压力、冲头尺寸、模具的结构形式以及模具材料等。
模具的设计需要充分考虑产品的形状、尺寸、结构和要求,以确保冲压的稳定性和一致性。
第五步:进行模具结构设计在进行冲压模具设计之前,需要进行模具的结构设计。
模具的结构设计需要考虑到模具的刚度、强度和稳定性等方面。
模具的结构设计还需要进行结构分析,确保模具的可靠性和使用寿命。
第六步:进行模具零件设计在进行冲压模具设计之前,需要进行模具的零件设计。
模具的零件设计需要考虑到模具的精度和加工要求,以及模具的可靠性和使用寿命等方面。
模具的零件设计还需要进行零件的装配分析,确保模具的装配精度和可靠性。
第七步:进行模具加工与调试在完成冲压模具设计之后,需要进行模具的加工与调试。
模具的加工与调试需要按照设计要求进行,包括加工工艺、加工设备、加工工具、加工程序以及加工技术等方面。
- 1、下载文档前请自行甄别文档内容的完整性,平台不提供额外的编辑、内容补充、找答案等附加服务。
- 2、"仅部分预览"的文档,不可在线预览部分如存在完整性等问题,可反馈申请退款(可完整预览的文档不适用该条件!)。
- 3、如文档侵犯您的权益,请联系客服反馈,我们会尽快为您处理(人工客服工作时间:9:00-18:30)。
设计题目:零件图:前 言从几何形状特点看,矩形盒状零件可划分成 2 个长度为 (A-2r) 和 2 个长度为 (B-2r) 的直边加上 4 个半径为 r 的 1/4 圆筒部分。
若将圆角部分和直边部分分开考虑,则圆角部分的变形相当于直径为 2r 、高为 h 的圆筒件的拉深,直边部分的变形相当于弯曲。
但实际上圆角部分和直边部分是联系在一起的整体,因此盒形件的拉深又不完全等同于简单的弯曲和拉深,有其特有的变形特点,这可通过网格试验进行验证。
拉深前,在毛坯的直边部分画出相互垂直的等距平行线网格,在毛坯的圆角部分,画出等角度的径向放射线与等距离的同心圆弧组成的网格。
变形前直边处的横向尺寸是等距的,即321L L L ∆=∆=∆,纵向尺寸也是等距的,拉深后零件表面的网格发生了明显的变化(如图1所示) 。
这些变化主要表现在:图 1⑴直边部位的变形 直边部位的横向尺寸变形后间距逐渐缩小,愈向直边中间部位缩小愈少,纵向尺寸变形后,间距逐渐增大,愈靠近盒形件口部增大愈多,可见,此处的变形不同于纯粹的弯曲。
(2) 圆角部位的变形 拉深后径向放射线变成上部距离宽,下部距离窄的斜线,而并非与底面垂直的等距平行线。
同心圆弧的间距不再相等,而是变大,越向口部越大,且同心圆弧不位于同一水平面内。
因此该处的变形不同于纯粹的拉深。
盒形件拉深有以下变形特点:σ的分布是不均匀的。
在圆角部分最大,直(1) 凸缘变形区内径向拉应力1σ也远小于相应的圆筒形件的拉应力。
边部分最小。
即使在角部,平均拉应力1因此,就危险断面处载荷来说,矩形盒拉深时要小得多;对于相同材料,矩形盒拉深的最大成形相对高度要大于相同半径的圆筒形零件拉深时的最大成形相对高度。
(2) 由于直边和圆角变形区内材料受力情况不同,直边处材料向凹模流动的阻力要远小于圆角处,并且,直边处材料的径向伸长变形小而圆角处材料的径向变形大,使变形区内两处材料的变形量不同,直边处大于圆角处。
由此引起两处位移速度差,因而必然诱发出切应力(图2),以协调直边与圆角处的变形。
图2 盒形件拉深时的应力分布σ的分布也是不均匀的。
从角部到中间直(3)在毛坯外周边上,切向压应力3σ的数值逐渐减小。
通常情况下,起皱都发生在角部,但是起边部位,压应力3皱的趋势要小于拉深相应圆筒形件时的情况。
常用相对圆角半径r/B表示矩形盒的几何形状特征,0<r/B≤0.5,当r/B=0.5时为圆筒形零件。
矩形盒拉深时毛坯变形区的变形分布与相对圆角半径r/B和毛坯形状有关。
相对圆角半径r/B不同,毛坯变形区直边处与圆角处之间的应力应变间的相互影响亦不同。
在实际生产中,应根据矩形盒的相对圆角半斤r/B 和相对高度H/r 来设计毛坯和拉深工艺。
一、拉深工艺分析 1.1 拉深件的材料拉深件材料为304J1是适宜于深拉深的不锈钢。
1.2 拉深件结构零件为带凸缘的盒形件,其中凸缘圆角半径为d r =4mm >1t=1mm ,底部圆角半径为p r =3mm>1t=1mm ,均满足对拉深件的圆角要求。
1.3 拉深件的精度等级零件尺寸工差为自由公差,因此初定公差等级为IT14。
1.4 拉深件工序安排的一般原则(1) 在大批量生产中,在凹、凸模壁厚强度允许的条件下,应采用落科、拉深复合工艺;(2) 当拉深件的尺寸精度要求高或带有小的圆角半径时.应增加整形工序;(3) 修边工序一般安排在整形工序之后;二、毛坯尺寸计算2.1 确定修边余量根据mm B f 85=,33.16485==B B f ,查冲压工艺与模具设计表4-4得到修边余量为:mm 5.3=δ2.2 确定毛坯尺寸由于,39.064/25==Bh,查冲模设计手册得: 当6.0≤Bh时,可按以下步骤求展开图:(1) 直边部分按弯曲件求展开长度(图2-1),即:a f r r h B B l 43.057.020-++-=图2-1⇒ mm l 49.35443.0357.02526485=⨯-⨯++-=(2) 四圆角拼成一带凸缘的圆筒(图2-2),其展开半径为:)(14.0)(86.02202020r r r r r rh R R a a f -++-+=⇒ mm R 36.290=图2-2(3)按求得的l 和0R 得到待修正的展开图后,选用较为简单的修正方法,即做切线修正法,计入修边余量后修正。
展开图的宽度为:)(86.0220a f r r h B K +-++=δ⇒ mm K 98.135= 展开图的长度为:δ22)(86.020+∆-+-+-+=a a f l r r h B B A L⇒ mm L 98.150= (其中a l ∆对于小型工件取2~3mm ,取2.5mm ) 修正后的毛坯展开图如图2-3所示。
图2-3 毛坯图三、拉深次数的确定矩形盒能否一次拉深的成形极限,可以用最大成形相对高度r H /max 表示。
它除受板材的性能影响外,还与零件的几何参数r/B 有关。
r/B 越小,直边部分对圆角部分的影响越大,因此可以获得的最大成形相对高度r H /max 也就越大;反之,r/B 越大,直边部分对圆角部分的影响越小,当r/B=0.5时,方形盒零件变为圆筒形件,最大成形相对高度r H /max 也必然等于圆筒形件的最大成形相对高度。
具体数值参见《冲压工艺与模具设计》表4-17。
当矩形盒的相对厚度t/B<0.01且A/B ≈1时,取表中最小值;当t/B>0.015且A/B ≥2时,取较大值。
由r/B=3/64=0.05,r H /max =25/3=8.3。
由表4-17可知,当0.01≤r/B ≤0.1时,矩形盒一次成型的最大相对高度r H /max 为8~15,因此可知该矩形件可一次拉深成形。
四、冲压力及压力中心的计算4.1 压边力的计算压边力必须适当,如果压边力过大,会增大拉入凹模的拉力,使危险断面拉裂;如果压边力不足,则不能防止凸缘起皱。
实际压边力的大小要根据既不起皱也不被拉裂的原则,并且在试模中加以调整。
设计压边装置时应考虑便于调节压边力,即Ap F Q =⇒ N F Q 38543128483=⨯=(其中单位压边力p 查表4-19得,取3)Q F —压边力(N )A —在压边圈下毛坯的投影面积(2mm ) p —单位压边力(MPa )(其中单位压边力p 查表4-19得,取3) 4.2 拉深力的计算由《冲模设计手册》查得:对于矩形、方形,椭圆形等拉深件,按下式计算拉深力:b KLt P σ=K —系数,一般取0.5~0.8,这里取0.7;L —拉深件断面周长(mm ); t —材料厚度(mm ); b σ—抗拉强度(MPa )⇒ N P 10774452012967.0=⨯⨯⨯= 4.3 总压力的计算总压力为:N P F F Q 14628710774438543=+=+=总4.3 压力中心的计算由于工件为对称件,所以该工件的压力中心为几何中心,即压力中心到短边距离为53mm ,到长边距离为42.5mm 。
五、选择冲压设备在冷冲压生产中,材料、模具、设备是冲压的三要素,而压力机是安装冲模的主要成形设备。
每副冲模只能安装在与其相适应的压力机上才能对板料进行施压 ,冲制出合格的制品零件。
因此在设计冲模时,必须选用合适的压力机。
5.1 压力机的选用方法及原则: (1)冲压设备类型的选择:1.中小型冲裁模、弯曲模、拉深模,应选用单柱、开式压力机;2.批量小,材料较厚的大型冲压件的冲模应选用液压机;3.批量大的自动冲模,应选用高速压力机及多工位压力机;4.对于校平,校形模应选用大吨位的双柱或四柱压力机;5.大中型拉深模应选用闭式拉延压力机;6.多孔电子仪器板件冲裁应选用冲模回转头压力机。
(2)压力机规格的选择:1.压力机的工称压力应大于计算的模具冲压力的1.2~1.3倍;2.压力机的行程应满足制品高度尺寸要求,并保证冲压后制品能顺利地从模具中取出,尤其是弯曲、拉深件;3.压力机的装模高度,应满足:)(10521mm H H H +≥≥-模;4.压力机的工作台尺寸,滑块底面尺寸应满足模具的正确安装尺寸,漏料孔尺寸应大于或能通过制品及废品尺寸;5.压力机的行程次数应符合生产率和材料变形速度的要求;6.压力机的结构应根据工作类别及零件的冲压性质,应具备有特殊装置和夹具,如缓冲器顶出装置,送料或卸料装置等;7.压力机的电动功率应大于冲压所需的功率; 8.压力机应保证使用的方便和安全。
5.2 确定压力机的型号根据压力机的选用方法及原则选用开式曲柄压力机。
由于拉深所需总压力为146.3kN ,压力机的公称压力应为总压力的1.2~1.3倍,则:2.1(=P ~1.3)总F =146.3⨯(1.2~1.3)=175.6~190.2kN根据算的的压力,确定压力机的型号J23—25。
其技术参数如表4-1所示:表5-1 开式曲柄压力机J23—25的技术参数公称压力/kN 250工作台孔尺寸/mm 前后200滑块行程/mm 65 左后290滑块行程次数/1min-55 直径260 最大闭合高度/mm 270垫板尺寸/mm厚度50 闭合高度调节量/mm 55 直径—滑块中心线到机身距离/mm 200模板尺寸/mm直径40 立柱距离/mm 270 深度60工作台尺寸/mm 前后370滑块底面尺寸/mm前后—左右500 左右—机身最大可倾角/(0)30 模柄孔尺寸/mm直径40深度60六、凸模、凹模刃口尺寸计算6.1 确定凸模圆角半径由《模具设计与加工速查手册》可知,凸模尺寸与形状应取为等于盒形零件内表面尺寸与形状。
由于盒形件内底部圆角为3mm,故凸模圆角半径pr取3mm。
而凹模圆角半径ar则按下式确定:=ar(4~10)t =81⨯=8mm6.2 确定凸模与凹模间隙矩形盒零件间隙选择原则:1.矩形盒零件拉深模凸、凹模间隙根据拉深过程中坯料各部位壁厚变化情况而定。
一般直壁部分小些,圆角部分大些。
在选择时,圆角部位应比直壁部位大0.1t左右;2.高矩形盒零件多次拉深时,其前几道工序的凸、凹模间隙可按一般圆筒形零件拉深时确定,而最后一次拉深成形时,按上述原则及下面公式选择适当的间隙值。
盒形件尺寸精度要求较高时:=z (0.9~1.05)t (1) 盒形件尺寸精度要求不高时:=z (1.1~1.3)t (2) 由于矩形件为自由公差,精度要求不高,故按(2)式选择凸、凹模间隙。
即:mm z 2.112.1=⨯=6.3 确定凸模、凹模刃口尺寸及公差由于盒形件只需一次拉深,因此 其凸模、凹模的尺寸及公差应按零件的要求来确定。
(1)当零件要求外形尺寸时:凹模尺寸:d L L d δ+∆-=0)75.0(凸模尺寸:)275.0(p Z L L p δ--∆-=(2)当零件要求内形尺寸时:凸模尺寸:)4.0(p l L p δ-∆+=凹模尺寸:d Z l L d δ++∆+=0)24.0(由零件图尺寸标注方式可知,盒形件要求内形尺寸,因此根据要求内形尺寸时的计算方法求解凸、凹模工作部件的尺寸公差。